随着石油、天然气工业的快速发展,由腐蚀造成的经济损失和安全生产问题日益引起人们的关注。在酸性油气田开发环境中,由H2S 引起的局部腐蚀问题越来越突出,特别是由H2S 导致的应力腐蚀开裂(Stress Corrosion Cracking,SCC),使材料发生突然失效,导致极其严重的后果,威胁着油气田生产的安全[1,2]。因此,开发含硫气田极其困难,具有极大的风险性,是石油天然气工业面临的重大难题之一。多年以来,各国石油与腐蚀工作者对酸性油气田开发过程中H2S 应力腐蚀问题进行了大量的研究[3,4],在腐蚀机理、选材以及预防措施等方面取得了一定的进展,并且这些研究成果被成功地应用到了低、中H2S 含量气田的开采中。但是,在高H2S 含量气田的开采过程中,由于苛刻的腐蚀环境,对耐应力腐蚀提出了更高的要求。有关学者提出应向材料选择方面寻求发展,一些具有更高耐蚀性的套管应运而生,如美国SMC 国际镍合金集团公司生产的028、852、G3 等镍基合金套管、日本住友金属工业公司生产的SM22Cr、SM25Cr、SM25CrW 套管以及瑞典Sandvik 公司生产的SAF2205、SAF2207 等双相不锈钢套管。
双相不锈钢(Duplex Stainless Steel, DSS)由于优异的力学性能和耐腐蚀性能,如高强度、良好的韧性、耐应力腐蚀开裂以及耐缝隙腐蚀等,被广泛地应用在了造纸、石油天然气、化工、海洋勘探等重要国防工业领域[5]。双相不锈钢在很多介质中具有很好的耐应力腐蚀性能,尤其是在含有氯盐的工业介质中更加显示出其特有的耐蚀性,但近年来随着原油品质的不断劣化,材料的腐蚀问题也日益加剧,即使是双相不锈钢也会出现SCC 开裂等失效案例[6,7]。面对生产现场苛刻的腐蚀环境,对双相不锈钢耐应力腐蚀提出了更高的要求。2205 双相不锈钢是双相不锈钢中使用量最大的品种,是超低碳奥氏体—铁素体不锈钢,它具有良好的韧性、强度和焊接性,其优良的耐中等氯化物应力腐蚀性能远远超过18-8 型不锈钢,并具有良好的抗点蚀和抗缝隙腐蚀能力,屈服强度是304 型不锈钢的2 倍。该类钢中的含镍量仅为18-8 不锈钢的1/2,解决了世界上工业用镍资源的不足。2205 双相不锈钢制品通常采用焊接方法来实现零部件的连接,但在焊接的过程中由于热循环对其接头组织、力学性能及耐腐蚀性能都有很大影响,这引起了国内外学者的极大关注[8,9]。于兴胜等[10]利用U 形弯曲浸泡实验、慢应变速率拉伸实验、电化学分析等方法对135、318、2205双相不锈钢进行了应力腐蚀开裂实验的研究。结果表明2205 双相不锈钢具有良好的抗H2S 应力腐蚀性能和良好的力学性能。但文中并没有对2205 双相不锈钢具有良好抗H2S 应力腐蚀性能的机理进行分析和讨论。生产中,2205 双相不锈钢在100 ℃以下、含Cl-和 H2S 数百mg/L 的近中性环境中已有成功应用的例子[11],但AVESTA 的双相不锈钢选用说明和设计规范[12]认为其还是存在SCC 和硫化物应力腐蚀开裂(SulfideStress Corrosion Cracking, SSCC)风险。双相不锈钢的应力腐蚀倾向取决于环境因素和材料的冶金状态,至今还没有一个简单的实验方法能评定2205 双相不锈钢在不同含氯等级的环境中发生SCC 的可能性。
C 型环试验[13]是研究材料发生SCC 的一种常用方法。它不但可以准确地判断材料应力腐蚀裂纹的发生、发展以及断裂情况,还可以通过改变施加应力的大小来进一步判断裂纹发展变化以及断裂时间的变化,最重要的是这种方法能够直接判断材料在特定腐蚀环境下是否适用。本研究采用C 型环实验研究了2205 双相不锈钢在NACE 标准A 溶液(5%NaCl+0.5%冰CH3COOH+饱和H2S+蒸馏水)[14]中应力腐蚀行为,通过OM、SEM、EDS和电化学手段分析了材料SCC 萌生、发展及断裂的机理。
1 实 验
参照GB/T 15970.5-1998《金属和合金的应力腐蚀第5 部分:C 型环试样的制备和应用》[15],采用C 型环试验来测试2205 双相不锈钢在H2S 环境下是否发生断裂,其试样尺寸如图1 所示。为了获得 C 型环试样上的预期应力,用公式 (1) 计算挠度D0,用公式 (2) 计算加载后C 型环的最终外径Df。
式中:D 为C 型环加载前外径(mm);Df 为C 型环加载后外径(mm);D0 为挠度(mm);t 为试样厚度(mm);d 为平均直径(mm);S 为施加应力(MPa);E 为弹性模量(MPa);Z 为校正系数上述公式中选取的应力S 应小于材料的弹性极限。对于许多耐蚀合金来说,其弹性极限比规定的屈服强度稍低。本研究中2205 双相不锈钢的弹性模量E=185 GPa,S 取弹性极限605 MPa,D = 31.68 mm,t =1.84 mm,Z = 0.96,经公式(1)计算得D0 = 1.30 mm,Df = 30.38 mm。
图 1 C 型环试样尺寸示意图
C 型环试样的制备:首先加工C 型环试样,用240#砂纸手工打磨试样表面和边缘,打磨方向平行于试样的轴向,测量试样尺寸,然后用丙酮清洗,通过加载螺栓装置对C 型环施加载荷至计算的外径值30.38mm 时,停止拧紧螺母,此时C 型环所受的应力为弹性极限(注意:测量时,外径的测量方向与通过最大应力点的中心线垂直)。
将清洗后的试样放入试验容器,然后让H2S 气体以每分钟几个气泡的速度维持在试验容器和NaOH 溶液中流动,直至试样断裂或达到720 h,试验结束。测试过程中,每120 h 取出试样,清洗干净后在光学显微镜下观察试样应力最集中表面裂纹的变化情况,并拍照记录。如果720 h 内试样断裂,则用扫描电镜观察其断口形貌;如果720 h 内试样没有断裂,同样用扫描电镜观察试样表面应力最集中部位裂纹的形貌,通过电化学方法分析SCC 敏感性区域,对裂纹处和裂纹以外区域的腐蚀产物进行能谱分析,讨论腐蚀机理。
2 结果与讨论
2.1 裂纹发展情况及分析
图2 为每120 h 用光学显微镜观察到的试样表面应力最集中部位的裂纹发展变化情况。从图 2 中可以看出,从开始测试到第360 h,试样表面并没有裂纹产生,而是出现了点蚀现象。从图2b可以看出,从测试开始到第120 h 时,试样表面出现了一些麻点;到第240 h 时,这些细小的麻点逐渐长大,并发展为点蚀坑;到第360 h 时,点蚀坑不断变大,将这个过程看作是点蚀的形成、发展过程。从图2e 可以看出,到第480 h 时,试样表面开始有微裂纹产生;到第600 h 时,裂纹不断扩展,在试样表面可以看到很明显的开裂现象(如图2f 所示),并且有些裂纹是从点蚀处产生的,这也说明了点蚀是不锈钢应力腐蚀的裂纹源,这也证实了点蚀对不锈钢应力腐蚀破裂的危害性。从试验开始到第600 h 试样表面产生了裂纹,说明2205 双相不锈钢耐应力腐蚀的性能还是比较好的,但其到底能否适用于饱和H2S 环境,还要看试验结束(第720 h)时是否断裂。图2g 为第720 h时试样表面形貌。从表面形貌可以看出,第720 h 时点蚀坑的面积在扩大,蚀坑周围不断发生溶解,且裂纹缝隙也逐渐变大,裂纹分布也越来越广,但C 型环试样最终并没有发生断裂,说明2205 双相不锈钢具有良好的抗H2S 应力腐蚀的能力,但试样表面产生了裂纹,这对钢材长期服役是有害的。
图 2 2205 双相不锈钢C 型环试样表面的裂纹发展情况
图 3 C 型环试样应力最集中表面SEM 照片
2.2 表面形貌及分析
为了分析C 型环试样的表面形貌及腐蚀情况,进而分析裂纹形成的机理,将试验后试样受应力最集中的表面进行了扫描电镜分析,观察裂纹的形貌如图3所示。从图3 中可以看出,试样表面裂纹呈散状分布,两侧少,中间多,并且较明显;对于C 型环来说,正是环的最上表面应力最大,这说明应力较集中的地方更容易产生裂纹。从图3 中还可以看出,这种呈散状分布的裂纹在发展过程中受到了阻碍,抑制了裂纹的进一步发展,这种裂纹分布正好是2205 双相不锈钢耐应力腐蚀性较好的原因。在双相不锈钢的特殊相结构中,可能是其中某一相对裂纹的发展起到了阻碍作用。
2.3 能谱分析
图4 为裂纹处和裂纹周围区域元素分布测试结果。对比2 个能谱图可以看出,在裂纹处出现了S 元素,而裂纹周围没有出现S 元素,说明裂纹处含有大量的含硫腐蚀产物。本研究的测试环境为湿H2S 环境,说明H2S 对裂纹的产生起着重要作用。当湿H2S 在裂纹处解离时,其解离后生成的H 原子参与了裂纹的扩展,而S2-则与基体金属发生腐蚀反应。2205 双相不锈钢表面本身有一层钝化膜存在,在该环境下H2S 能够与基体金属发生反应,说明表面的钝化膜遭到了破坏。在该环境下,只可能是Cl-使该处钝化膜发生破坏,使得H2S 在蚀坑解离,生成HS-、S2-及H+,解离后的S2-与暴露的Fe 发生反应,这就是在裂纹内侧检测到S元素的原因。已有研究表明[16],H2S 解离后生成的H原子很容易被吸附到暴露的金属铁表面,通过扩散进入钢中,在局部位置聚集并促进氢气核的形成,当氢压达到2205 双相不锈钢断裂应力时,就会造成氢致开裂的发生。在裂纹周围的部位没有检测到S 元素,说明H2S 在该处还没有与基体金属发生反应,该处继续受到钝化膜的保护。
图4 试验后C 型环试样SEM 照片及EDS 能谱分析
2.4 腐蚀机理分析
材料发生SCC 需要特定的腐蚀环境,这个特定环境可以理解为SCC 临界电位,在不锈钢的阳极极化曲线上有2 个SCC 临界电位区间,称之为活性-钝态过渡区(SCC-1 区域)和钝态-过钝态过渡区(SCC-2 区域),这2 个电位区间称为发生SCC 的敏感性电位区间。当合金材料在某种环境中的腐蚀电位处于该区间时就会发生SCC,否则就不会发生SCC。因此,参照《GB/T 17899-1999 不锈钢点蚀电位测量方法》[17]对2205 双相不锈钢进行了点蚀电位测量,如图5 所示。腐蚀环境为3.5%NaCl 溶液;试样规格为10 mm×10mm,并用环氧树脂封装;温度控制是用85-2 恒温仪保证试验温度在(25±1) ℃范围内;把经过最终打磨(2000#水砂纸)的试样浸于溶液中10 min 后,从开路电位开始以20 mV/min 进行阳极极化,直到电流达到1000 μA/cm2 后,反向进行回扫,使电位向负方向变化,当正扫和反扫曲线相交时结束测试,最后得到一个环状阳极极化曲线,称之为“滞后环”[18]。测试前需持续通入氮气1 h 除氧。
图 5 2205 双相不锈钢点蚀电位测量曲线
从图 5a 中可以看出,2205 双相不锈钢的SCC 敏感性电位区间分别为SCC-1 区域和SCC-2 区域,其对应的临界电位分别为–0.3~ –0.1 V 和1.0~1.2 V。在SCC-1 区域,因临界电位为1 个较负的值,因此在使用过程中钢材表面很容易钝化,钢材要发生SCC 可能集中在SCC-2 区域。而SCC-2 区域电位是一个较正的值,说明要使2205 双相不锈钢发生SCC,则需要一个很高的破钝电位,这就说明钢材能够适应较为苛刻的腐蚀环境,该钢材具有良好的耐应力腐蚀性能。当极化电位达到1.0 V 时,体系钝化膜开始遭到破坏,在1.0~1.2 V 电位区间,钝化膜处于破裂和修复的动态平衡阶段,随着极化电位的继续增大,动态平衡被打破,钝化膜开始损坏,电流密度产生突变,基体金属不再受钝化膜的保护,点蚀也由此产生,因此把点蚀看做是应力腐蚀的起始位置。为了分析2205 双相不锈钢点蚀体系的电化学性能,作了其回扫“滞后环”,如图5b 所示,得到点蚀发生的临界电位Ecr = 1.10 V,点蚀保护电位Epr = 0.98 V。从实验数据可以看出,临界电位和点蚀保护电位并不重合,两者之间的电位差是点蚀发生的孕育期,在此电位区域点蚀可能发生。当电位低于0.98 V 时,金属表面的钝化膜将变得更加稳定,点蚀不会发生,材料得到保护。
结合 EDS 能谱分析以及电化学分析结果,可以认为氢致开裂是2205 双相不锈钢开裂的主要原因。能谱分析在裂纹内检测到S 元素,而在裂纹周围没有检测到S 元素,说明裂纹周围的钝化膜没有被破坏,仍然对金属基体起到保护作用。当腐蚀环境造成点蚀电位达到临界电位时,钝化膜发生破裂,SCC 由此发生。从C 型环裂纹的萌生到发展过程来看,在试验初期试样发生了因Cl-而引起的点蚀,点蚀坑的形成经历了很长一段时间,这与钝化膜的保护作用有关,当点蚀坑发展为蚀孔时,钝化膜遭到完全破坏,此时H2S 会在蚀孔内发生解离,产生S2-、HS-以及H+,与基体金属发生反应,其中H 原子则参与裂纹的萌生与发展,S元素则与Fe 元素发生反应,这就是在裂纹内侧检测到S 元素的原因。
综上所述,当2205 双相不锈钢在临氢环境时,其表面的Cr2O3 钝化膜除了保护基体金属之外,还有阻碍H 原子向基体金属扩散的作用,陈长风等[19]计算了H 原子在Cr2O3 晶格中的扩散系数,结果表明H 原子在氧化膜中的扩散系数非常小,相对于H 原子在基体金属中的扩散系数来说几乎可以忽略不计。这说明在Cr2O3 钝化膜完好的情况下,此钝化膜能够有效地阻止环境H 原子向基体材料内部的扩散,对于防止氢致开裂来说是有益的。但如果Cr2O3 钝化膜遭到破坏,比如点蚀的产生,那么环境H 原子就很容易从点蚀坑进入金属基体,随后H 原子在金属基体内扩散、聚集,最终导致裂纹的产生,这与图2 中C 型环试样表面裂纹的发展变化情况相吻合。
3 结 论
1)2205 双相不锈钢在720 h 内没有发生断裂,说明该钢材具有良好的抗H2S 应力腐蚀的能力。
2)应力较集中的地方更容易产生散状分布的微裂纹,这种裂纹分布说明裂纹在发展过程中受到了阻碍,使得裂纹的发展转向,抑制了裂纹的进一步发展。
3)当试样表面的Cr2O3 钝化膜遇到活性Cl-时,其表面很容易产生点蚀,继而发展为点蚀坑,钝化膜遭到破坏,失去了对基体材料的保护作用。由H2S 解离生成的H 原子很容易从蚀坑位置进入金属基体,随后H 原子在金属基体内扩散、聚集,最终导致裂纹的产生。
4)2205 双相不锈钢应力腐蚀敏感性电位区间为1.0~1.2 V,该区域临界电位是一个较大的正值,说明该钢材耐应力腐蚀性能良好,能在较为苛刻的腐蚀环境中工作。
参考文献
[1] Chasse K R. A Study on the Mechanism of Stress CorrosionCracking of Duplex Stainless Steels in Hot Alkaline-sulfideSolution[D]. Georgia: Georgia Institute of Technology, 2012
[2] Yang Ming (杨明), Ma Xiaoyong (马晓勇), Long Yun (龙云)et al. Corrosion & Protection(腐蚀与防护)[J], 2014, 35(12):1226
[3] Liu Z Y, Dong C F, Li X G et al. Journal of MaterialsScience[J], 2009, 44(16): 4228
[4] Siddiqui R A. Journal of Materials Processing Technology[J],2005, 170(4): 430
[5] Wu Jiu(吴玖 ). Duplex Stainless Steel(双相不锈钢)[M].Beijing: Metallurgical Industry Press, 2000
[6] Lin Hongxian(林红先), Fan Yuguang(樊玉光), Xiong Hui(熊惠) et al. Corrosion & Protection(腐蚀与防护)[J], 2009,30(6): 386
[7] Liu Zhide(刘志德), Huang Liming(黄黎明), Yang Zhongxi(杨仲熙) et al. Nature Gas Industry (天然气工业)[J], 2004,24(12): 122
[8] Geng Shaoning, Sun Junsheng, Guo Lingyu et al. Journal ofManufacturing Processes[J], 2015, 19: 32
[9] Zhang Jianxun(张建勋), Li Qingyan(李庆琰), Li Weiwei(李为卫) et al. Rare Metal Materials and Engineering(稀有金属材料与工程)[J], 2006, 35(11): 1822
[10] Yu Xingsheng(于兴胜), Wang Xiangdong(王向东), MengQingkun(孟庆昆). Oil Field Equipment(石油矿场机械)[J],2007, 36(12): 37
[11] Wu Jiu(吴玖).Petrochemical Corrosion and Protection(石油化工腐蚀与防护)[J], 1999, 16(1): 23
[12] Mats Liljas, G?ran Gemmel. Choice of Specifications andDesign Codes for Duplex Stainless Steels[R]. Sweden: AvestaSheffieId AB and Avesta Sandvick Tube AB, 2000
[13] Yang Fuhe(杨福河). Study on Electrochemical Noise for StressCorrosion Cracking of C Ring Specimen(C 型环试样应力腐蚀开裂的电化学噪声研究)[D]. Tianjin: Tianjin University, 2007
[14] NACE Standard TM0177-2005[S]. 2005
[15] GB/T 15970.5-1998[S]. 1998
[16] Zhang Fengchun(张凤春). First-principles Study on Interactionbetween Fe and H2S, H(金属Fe 与H2S、H 相互作用的第一性原理研究)[D]. Chengdu: Southwest PetroleumUniversity, 2013
[17] GB/T 17899-1999[S]. 1999
[18] Wei Xin(魏欣),Dong Junhua(董君华),Tong Jian(佟键) etal. Acta Metallurgica Sinica(金属学报)[J], 2012, 48(4): 502
[19] Chen Changfeng(陈长风), Yu Haobo(于浩波), Zhen Shuqi(郑树启). Sci China Tech Sci(中国科学: 技术科学)[J], 2011,41(1): 25
免责声明:本网站所转载的文字、图片与视频资料版权归原创作者所有,如果涉及侵权,请第一时间联系本网删除。
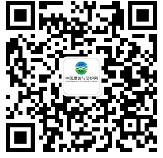
官方微信
《腐蚀与防护网电子期刊》征订启事
- 投稿联系:编辑部
- 电话:010-62316606-806
- 邮箱:fsfhzy666@163.com
- 腐蚀与防护网官方QQ群:140808414