一、新型超高强度钢及其强韧化设计研究背景
人类社会的进步与材料发展息息相关。当前,钢铁材料仍是最广泛使用的结构材料,为航空航天、先进装备制造、新能源、海洋工程以及先进交通运输等涉及国计民生和国家安全等重大关键领域提供关键材料支撑。近些年来,随着大飞机、高铁和先进核能等重大工程的实施,先进工业、轻型化设计等均对材料强度及综合性能提出了更高的要求。然而,我国作为钢铁大国,在超高强度钢为代表的高端钢铁材料的研发、品控、种类上与国际先进水平存在较大差距,部分关键工业应用领域仍完全依赖进口。在目前严峻的国际政治形势和激烈的国际竞争态势下,研发具有完全自主知识产权的高性能超高强度钢、实现高品质钢材可控制造已迫在眉睫,这对于我国钢铁产业升级、抢占国际科技竞争制高点具有重大意义。
超高强钢一般指屈服强度大于1500 MPa的钢铁材料。由于应用于飞机起落架、喷气发动机主轴、导弹壳体、核工业同位速分离的超高速离心转筒结构及高强紧固件等最具挑战性的工程结构材料领域(如图1所示),超高强度钢除了有极端的超高强度指标要求,还对韧性、疲劳、应力腐蚀、高温以及材料成型性等综合力学性能也提出了更高要求。近年来超高强度钢不仅服役强度不断提升,而且其使用范围正不断拓展到超高层建筑、先进装备制造、高速列车及其它国防装备,高性能、低成本成为其重要的发展方向。
图1 超高强度钢部分用途
自上世纪四十年代以来,超高强度钢强度的提升始终围绕马氏体相变和纳米析出的精细调控而展开。钢铁材料在高温时为面心立方(FCC)奥氏体结构而在相对较低温度时为体心立方结构(BCC)。当冷却速度较快时会发生面心立方向体心立方的连续切变,即马氏体相变,导致材料内部形成极高密度的晶格缺陷。当碳含量较低时,内部缺陷一般由高密度位错组成,造成这种马氏体相本身高的强度和良好的塑性,事实上马氏体相变产生的缺陷贡献了几乎所有超高强度钢一半的强度。高温奥氏体相可固溶高含量的碳以及其它合金元素,在转变为低温体心立方结构的马氏体相时可以形成高过饱和度的过饱和固溶体。通过后续的时效保温,会形成高密度的纳米析出相从而产生显著的时效硬化并获得超高的强度,这是目前多数超高强度钢的强化思路。
据此思路,目前国际上开发出了最具竞争力的两类超高强度钢系列:高Co-Ni二次硬化钢(HY180、AF1410, Aermet 100)和马氏体时效钢(C250-300, T250-300)。虽然合金成分(见表1)及强化相不同,但是强化机理均为半共格析出相与位错的强弹性交互作用,造成超高强度钢大幅度提升强度的同时也导致其它性能,尤其是塑韧性的显著下降,这种矛盾关系在强度突破2000 MPa时更为明显,其均匀塑性几乎为0(见图2)。为保证良好的综合性能,超高强度钢往往需要添加高含量的昂贵合金元素原料(Co、Mo、Ni)保证高体积分数析出,通过超纯净冶炼(极低的N、P、S夹杂含量)以及严苛复杂的热处理工艺控制获得超细组织及晶界调控,这使得超高强度钢成本高昂,进一步优化更为困难,从而极大限制了材料高性能化发展,以及其在工业领域的应用。因此,超高强度下强韧化机制的缺乏、愈发严重的强韧性矛盾以及极高的制备成本是制约超高强度钢发展的关键挑战。
表1 典型超高强度钢的主要合金成分
图2超高强度钢的典型拉伸曲线。
超高强度钢的力学性能主要决定于马氏体基体和时效组织,相关研究主要集中在合金元素作用、多尺度结构设计、先进材料设计方法、析出相调控、析出相与位错交互作用、马氏体板条结构及位错组态控制等方面。近年来通过对强韧化机制的不断探索和新制备技术的应用,各国研制出了系列新的高性能、低成本超高强度钢合金体系,在不同的应用领域表现出良好的应用前景。
二、超高强度钢研究进展及现状
超高强度钢主要包括以300M为代表的低合金钢、高Co-Ni二次硬化钢以及马氏体时效钢,其中低合金超强钢韧性普遍低于其他两类钢种。随着超高强度钢制备技术尤其是高纯净度冶炼的长期发展,传统二次硬化钢以及马氏体时效钢性能优化已渐趋瓶颈。从材料组织角度讲,这两类钢种的强化均依托于纳米析出相在其周围产生的强畸变场与位错的弹性交互作用,但是又不可避免地限制了析出相体积密度以及组织均匀性,造成强度的提升伴随着其他性能的严重下降,往往需要极为复杂严苛的制备工艺和极高的合金含量保证服役性能。近年来,为了突破固有体系的性能限制,逐渐开发了系列共格-半/非共格协同强韧化的新型超高强度钢,表现出良好的应用前景,但是所涉及的协同强韧化机制尚不清楚,也未形成相关设计准则,高成本问题依然严峻。同时为了缩短研发周期,美、法等发达国家开展了材料集成计算技术、材料基因工程等技术加速超高强度钢的发展,但是目前仍主要集中于单一强化体系,在多相协同析出强韧化方面鲜有报道。
2.1 高Co-Ni二次硬化钢
高合金化的马氏体二次硬化钢主要有HY180, AF1410, HP9-4-20和HP9-4-3以及后来推出的Aermet100。这些钢种的成分和热处理制度都非常相似。如图3所示,这些合金经过时效后固溶的C元素主要以细小的M2C结构析出而获得超高强度。研究表明,M2C析出本身对韧性的提升效果非常有限,但是相比于其他马氏体时效钢,M2C析出并不降低固溶在基体中的Ni元素,而Ni元素能明显提升位错交滑移能力,可以缓解微区应力集中、钝化微裂纹等,在宏观上表现为显著提高二次硬化超高强度钢的韧性,因此,在目前研发的超高强度钢中Ni是必不可少的重要元素。
图3 高Co-Ni二次硬化钢M2C相TEM。
HY180是第一个高强高韧的高Co-Ni二次硬化钢,美国通用公司在高Co-Ni 二次硬化钢HY180的基础上研发了AF1410 钢,获得了强度、韧性的进一步提升。AF1410 在最佳时效条件下具有极高的韧性,但强度值并不能达到和最常见的超高强度钢300M 相同的级别。因此,在AF1410 钢的基础上,美国Carpenter公司通过微调合金成分,进一步开发了Aermet100 及Aermet310钢。Aermet100 钢是具有高韧性值的高Co-Ni 二次硬化钢中的典型代表,其具有与300M相当的强度以及接近AF1410 的高韧性,同时具有较高的抗应力腐蚀能力。
从合金成分来看,高Co-Ni二次硬化钢的发展主要体现在三个方面:首先,逐渐增加C及碳化物形成元素并控制其比例,从而增加M2C的平衡体积分数。合适的Cr、Mo比例可降低M2C与基体的错配度从而促进其高密度析出,还能够降低亚稳M2C的粗化速率并避免其他对韧性不利的碳化物析出。其次,提升Co、Ni含量,其中Ni是提高韧性的重要元素。Co能够显著抑制板条马氏体中位错的回复并提升碳的活度,可显著提升M2C借助于位错等缺陷的形核率并细化M2C组织。同时,Co是钢中极少数能够提升Ms点(即马氏体转变起始温度)的合金元素。因此,Co添加能够改善C及其他合金元素含量增加造成的Ms过低、马氏体转变不完全的关键问题。最后,严格控制夹杂含量及种类,夹杂含量越来越低。Aermet100钢的韧性对夹杂物体积分数和平均间距的变化非常敏感,低体积分数及大间距的夹杂能够显著缓解二次裂纹增强的微孔聚合,从而提升断裂韧性。但是,即使当夹杂程度非常低时,断裂时仍会发生包括韧性的微孔聚合、脆性的解离及沿晶断裂,合金本身属性决定了断裂韧性的上限。对于半共格析出组织本身而言,由于高能界面特征其组织结构难以进一步优化。细化晶粒或者调控晶界结构(比如晶界位置形成逆变奥氏体薄膜),成为进一步优化性能的关键,其能够降低韧脆转变温度(尤其是三轴拉应力状态下的),并有效抑制不稳定脆性裂纹的快速扩展。以上是高Co-Ni马氏体钢获得高强度高韧性的重要条件和手段。
对于Aermet100和AF1410的强化机制,研究表明,随时效温度的升高,魏氏渗碳体减少,共格M2C相逐渐形成,引起强度上升并达到强度峰值。在454℃以上时效时,随时效温度的升高,M2C碳化物长大并逐渐失去与基体的共格关系,同时位错密度降低,导致强度下降。该温度下晶界及板条界面处奥氏体的增加也导致了 482℃时效时材料强度下降。因此只有当析出相为M2C、且与基体保持共格关系时才能获得最高的强度。多数研究认为M2C为六方结构,长轴方向沿着BCC,取向关系为[100]M//[100]M2C,[110]M//[001]M2C。M2C中M所占据的点阵位置通过固溶一定量的Cr元素可以有效的降低a轴方向上的错配度从而促进M2C高密度析出。M2C产生的强化效果主要来源于和位错的弹性交互作用,Cr的固溶虽然可以降低M2C与基体的错配度,但是弹性畸变是由晶格错配度和M2C的尺寸共同决定。因此,Cr的添加可细化组织的同时提升材料强度。此外,Aermet 100中相对高的Cr含量还可以降低碳化物的形成温度并加速M2C形成,从而避免过高时效温度导致的逆转变奥氏体增多伴随的强度下降。
Aermet 100钢高的断裂韧性还和一定温度时效后在马氏体板条界面位置处形成的奥氏体薄膜有关。图4所示为马氏体板条界面处形成的薄膜奥氏体组织,Sato等证实马氏体晶界可通过这些逆变奥氏体的塑性变形发生滑动,从而能够有效的钝化裂纹尖端并提高断裂韧性。但是亚稳奥氏体在相变后形成的脆性相会显著降低材料疲劳性能。Ayer等认为由于Aermet100 钢具有较低的Ac1 温度,因此易于形成逆转变奥氏体,同时形成的逆转变奥氏体中富集了大量的Ni、Co、C 元素,使得其Ms 温度较低,从而保持了逆转变奥氏体的稳定性。从热力学平衡角度讲,奥氏体在室温以上可以稳定存在,而Aermet100钢又固溶相对高含量的间隙C元素,由于其远高于置换型溶质元素的扩散系数,相比于其他马氏体时效钢,Aermet100可通过C的快速富集更加容易获得逆转变奥氏体(类似于Q-P钢及超级贝氏体钢中C的配分),因此形成了这种非常独特的纳米析出和奥氏体薄膜组织。此外,通过临界区退火获得热稳定奥氏体可进一步提高Aermet100的断裂韧性。
图4 二次硬化钢中逆转变奥氏体薄层, Austenite layer-薄膜奥氏体
目前,通过制备工艺优化,Aermer100在2GPa强度下的韧性几乎已经达到极致。但是对于强韧化机理的认知仍然由很多争议的地方,比如超过韧化峰值温度后断裂韧性的显著下降,M2C结构及化学成分不明确,薄膜奥氏体稳定性及韧化作用等。从合金化角度讲,沿着HY180、AF1410、Aermet100的设计路线,继续提高碳及M2C的含量提升强度面临着Ms点过低难以获得全马氏体组织、成型性及焊接性能继续恶化的关键问题,因此M2C强化几乎趋近瓶颈,近年来通过协同半共格M2C及共格B2相成为新的发展方向,具体见2.3节。
2.2 马氏体时效钢
马氏体时效钢是指以无碳或微碳的铁镍马氏体为基体,通过合金化Mo、Ti、Co、Al等元素时效时能产生金属间化合物以进行沉淀硬化的超高强度钢,主要包括18Ni为基础的马氏体时效钢以及PH 13-8Mo,PH 17-4等为代表的马氏体时效不锈钢。
相对于马氏体二次硬化钢,马氏体时效钢不仅具有极高的强度和韧性,因其极低的碳含量,低碳板条马氏体室温加工硬化系数极低,使其具有极为优异的热、冷变形能力,包括拉拔、冷轧、弯曲、深冲等大变形冷加工都很容易实现,直接变形可超过90%。同时,相比其他碳增强材料,马氏体时效钢不仅具有焊接性好、淬透性高和变形小的特定,而且不存在脱碳问题。因此,基于其极为优异的成型性、强韧性和高的热稳定性,马氏体时效钢广泛应用于超高压容器、同位素分离用超高速转筒筒体、导弹壳体、发动机转子、飞机起落架及热作模具钢等国民经济重大关键领域和重要国防装备。
马氏体时效钢产生于1960年代初,INCO公司相继开发了1400,1700,1900及2400 MPa级别的Fe-Ni马氏体时效钢,并将其应用于火箭发动机壳体。在该合金体系中,Ni元素一部分固溶于基体保持断裂韧性,一部分形成析出相。Co和Mo是马氏体时效钢中重要的析出控制元素,Co固溶于基体与Mo发生协同作用,促进增强相Ni3Mo在板条内部的高密度析出。不同级别的马氏体时效钢的合金化主要表现在Mo、Ti含量的差别。Ti含量从0.2增加到0.7%时其强度可以从1400 MPa增加到2000 MPa,主要原因是高密度半共格Ni3(Ti, Mo)相的形成(见图5)。基于Ti的显著强化作用,后续又研发了包括T250和T300的系列高Ti无Co马氏体时效钢[43],但是韧性相较于含Co钢有明显下降。无Co高Ti不可避免地引入了粗大Fe2(Mo,Ti)晶界析出(>100 nm)、TiC碳化物(>500 nm)以及含Ti的立方形状夹杂等对韧性极为不利的结构,为保证综合性能对制备工艺提出了更高的要求。
图5 马氏体时效钢中强化相η-Ni3(Ti,Mo)高分辨
马氏体时效钢的强化通常由多种金属间化合物的协同析出所决定,其中主要的强化相与二次硬化钢中的M2C相似,均与基体有明确的共格取向关系,这也是其可以获得高密度、小尺寸组织的主要原因。强化峰值往往也对应与共格界面的保持,即高强度同样源自与位错的弹性交互作用。过时效时共格界面演变为非共格且伴随着逆转变奥氏体的形成,造成强度下降的同时韧性大幅提升。马氏体时效钢的时效行为与二次硬化钢有所差异,主要原因可能与含C和不含C逆变奥氏体不同的转变动力学相关。因此,综合考虑二次硬化钢和马氏体时效钢完全不同的力学性能演化规律,进一步探索纳米析出相和逆转变奥氏体协同控制、以及两者在裂纹扩展过程中的行为及作用,对于发展新一代超高强度钢具有重要意义。
2.3 共格及半/非共格析出协同强化的新型超高强度钢
马氏体时效钢及二次硬化钢两类超高强度钢的发展表明,单纯借助于某一类强化相的超高强度钢几乎达到了性能极限,具有不同属性析出相的协同析出以及其产生的协同强化效应成为超高强度强韧化设计的新方向。协同析出强化具有以下三个优势:一是打破合金体系限制。纯粹的提升某一种析出相的形成元素不仅会造成析出相形成温度过高、低的奥氏体稳定性及初始组织有未溶粗大析出物等问题,而且溶质含量过高时析出相易于粗化、热稳定性较低,通过多种不同类型析出的合金化,可以突破第二相体积分数的限制;二是细化组织。各种析出相在形成过程中会发生协同效应,从而影响析出相的形核长大行为和热稳定性;三是促进均匀塑性流变。不同类型析出相和位错交互作用不同,通过协同作用可以一定程度上避免各自引起的对于塑性流变的不利影响。
研究发现,单纯的依靠共格有序析出强化使得铁素体韧性极低,但是通过协同非共格析出M2C和共格的NiAl和M2C,可以有效避免应变集中,从而保持高强度的同时大幅提升了材料韧性。后来在Aermet100基础上发展了含Co的GE1014,由M2C和NiAl相协同强化,避免了马氏体钢中Ti的不利作用同时提升了M2C组织的热稳定性,从而推动了GE90发动机风扇中间轴的性能提升和更新换代。Delagnes等发现共格NiAl相形成速度快且热稳定性高,不仅保留了马氏体中高密度位错,而且细化了M2C组织并抑制了粗大渗碳体的形成。为避免Ti对抗疲劳及韧性的不利作用,同时又要维持马氏体时效钢的超高强度, Rhoads等在含Co马氏体的基础上去除了Ti,这使得在该钢种中添加0.2 wt.%的C成为可能,进而通过调节Cr,Mo含量研发了Ni3Mo和M2C协同强化的马氏体时效钢,非金属夹杂含量大幅下降,抗疲劳性能得到改善,这种成分设计的调整也使其能够在高达400°C的温度条件下服役成为可能。日本也通过以Al代Ti发展Ni3Mo和NiAl协同强化改善其疲劳性能,研发类似含Co不含Ti的超高强钢应用于汽车无级变速带上。剑桥大学Sun等设计了NiAl和Laves相协同强化的新型马氏体时效钢,使得超高强度钢具有优异的高温力学性能,在500℃ 700 MPa条件下,蠕变寿命超过2000小时。以上结果表明,目前的研究仍然以半共格析出基础上添加少量共格析出为主,半共格析出本身的瓶颈问题仍无法避免。主要问题在于缺乏协同析出组织调控及协同强韧化原理的系统深入研究以及针对于协同析出的合金设计准则。
2.4 多尺度计算模拟与新型耐蚀超高强度钢
相比于低合金钢,超高强度钢合金元素种类多、含量高,且制备工艺复杂,同时对各个尺度下的组织结构均有严格的要求,基于传统试错法的研发方式虽然可以明确简化合金体系背后的物理冶金原理,但是存在周期长、效率低等诸多问题,显然已经不能满足目前新型超高强度钢的研发要求,尤其是复杂合金体系、多相协同强化的情况。高性能钢铁材料的研发模式需要向理性设计转变。
图6 材料基因科技发展历程
Materials Genome Timeline-材料基因工程发展历程;Computational Materials Design-计算材料学;Integrated ComputationalMaterials Engineering-集成计算材料学;Alloys-合金;Polymers-聚合物;Ceramics-陶瓷;Composites-复合材料);Refractory-难熔合金
美国Olson团队率先展开了基于数据库、多尺度材料模拟设计、高通量表征测试的集成计算技术和理性研发模式,搭建了多尺度模拟分析平台,用以综合分析“成分-工艺-性能-工程生产”整个过程对材料性能的影响。图6所示是材料基因工程发展的历程,目前,美国通过集成计算技术先手研发了Ferrium S53 和Ferrium M54两种综合性能优异的新型耐蚀超高强度钢,优化并确定了其在包括铸造-锻造-均匀化-时效整个过程中的工艺参数,最终应用在了飞机起落架、舰艇燃气轮机主轴等美国军事装备上,有效的缩短了钢铁材料的研发周期和成本。Xu等人基于热力学数据库也发展了其他体系高强钢。然而,随着合金体系变得更为复杂但协同析出强韧化的机理尚不明确,对于复杂体系的集成计算技术目前尚未见有详细报道,相信随着基础理论的不断完善,未来基础计算技术必将发挥其独特的魅力。
未完待续。。。。
参考文献从略
免责声明:本网站所转载的文字、图片与视频资料版权归原创作者所有,如果涉及侵权,请第一时间联系本网删除。
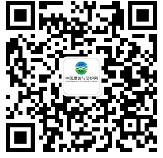
官方微信
《中国腐蚀与防护网电子期刊》征订启事
- 投稿联系:编辑部
- 电话:010-62316606-806
- 邮箱:fsfhzy666@163.com
- 中国腐蚀与防护网官方QQ群:140808414