1 前言
2013年,中国国家海洋局发布了《国家海洋事业发展“十二五”规划》。在规划中明确提出:作为发展中的海洋大国,我国在海洋有着广泛的战略利益。随着经济全球化的发展和开放型经济的形成与深化,海洋作为国际贸易与合作交流的纽带作用日益显现,在提供资源保障和拓展发展空间方面的战略地位更为突出。“十二五”期间是我国海洋事业发展的关键时期,未来将向深海和远海发展。着力提升海洋开发、控制和综合管理能力,统筹海洋事业全面发展,是保障国家“走出去”战略实施的重大举措,对于促进沿海地区经济社会发展、国民经济发展方式转变,具有重大的战略意义。以国际海事组织制定的性能标准为主导,世界各国围绕海洋耐蚀钢开展了腐蚀机理、腐蚀过程的研究,其中油船货油舱用耐蚀钢是近 10 年来国际上研究和开发的重要钢铁新品种。在该领域,日本走在世界前列,乌克兰与俄罗斯有其技术特色海洋,中国对海洋耐蚀钢的研究应用相对滞后。随着海洋耐腐蚀钢替代标准不断得到认可,将逐渐取代涂层钢成为海洋腐蚀保护方式的主流。本文重点分析了油船货油舱用耐蚀钢和耐海水腐蚀钢这 2 大类低合金高强度钢的发展现状及需求,不涉及不锈钢、特种合金等钢铁材料。
2 油船货油舱用耐蚀钢
2.1 重大需求分析
进入 21 世纪,中国船舶及海洋石油工业迎来了高速增长期,成为中国国民经济发展的重要支柱。据英国克拉克松研究数据表明,中国已成为世界造船中心。2013 年,中国造船 3 大指标市场份额继续保持世界领先,其中造船完工量、新接订单量、手持订单量分别占世界总量的 40.3%、47.6% 和 45.8%,如表 1 所示。
“十一五”期间,在海洋石油工业领域,中国海上油气开发投入 1200 亿元人民币,建设了 15 个海洋油气田、76 座钻井平台、6 座浮式生产储油船,铺设了 1400km 海底管线,2010 年海洋油气产量实现了 5000 万 t 油当量。根据中海油规划,“十二五”期间将新建5000 万 t 油当量产能。预计“十二五”、“十三五”期间海洋石油工业投入将分别达到 6700 亿元和 9500 亿元人民币,其中海洋工程装备市场投资将达到 2500亿~ 3000 亿元人民币。
根据我国《钢铁工业“十二五”发展规划》对 2015 年关键钢材品种消费预测,未来 5 年,仅船板用钢消费量将从 2010 年的 1300 万 t 提高到 2015 年的1600 万 t,其中油船货油舱用钢量占油船用钢总量的 30% ~ 45%。以建造一艘30万t级的超大型油轮(VLCC) 为例,船体结构总用钢量近 4 万 t,其中油船货油舱部分用钢约 1.7 万 t。据中国船舶工业行业协会对我国目前手持油船订单统计,油船货油舱用钢量每年达 200万 t 左右。如果能推广使用到海洋工程领域,其市场需求将更大。
2.2 油船货油舱用耐蚀钢概况
油船是原油海洋运输的主要工具之一。近年来因货油舱腐蚀造成油船失效事故时有发生,不仅造成巨大的经济损失和安全事故,而且对海洋环境造成严重危害。因此油船货油舱的防腐问题越来越受关注。2006 年以前油船都是单甲板、单底结构,因为货油舱内破损后,油浮在水面上,舱内不至于大量进水,故油船除了在机舱区域内设置双层底以外,货油舱区域一般不设置双层底。
2006 年以后,为了提高海运安全性,防止和减少油轮发生海损事故造成的污染,国际海事组织(IMO)要求大型油轮必须设置双层底或双层船壳。内层为货油舱,用来承载原油。原油尤其是高硫高酸原油对于钢结构货油舱腐蚀影响严重,威胁着油船运营安全。
目前针对油船货油舱腐蚀所采取的防护措施主要有:加注缓蚀剂、采用防腐涂层和耐蚀钢板。其中,加注缓蚀剂过程复杂,长期投资高;防腐涂层使用过程中存在严重的局部腐蚀隐患,每2.5a 就须对油船进行涂层维护和重新涂布,需要耗费高额成本,延长工期,并且货油舱空间封闭,施工环境恶劣,也会一定程度上影响施工质量。表 2 比较了使用涂层和耐蚀钢造船的成本,安全且低成本的防护措施是使用耐蚀钢。
1995 年,国际海事组织对油船货油舱用耐蚀钢提出推荐性要求,并推荐各国进行研究。2010 年 5 月 14 日,国际海事组织海上安全委员会(MSC)第 87 次会议正式通过了《原油油船货油舱防腐保护替代方法性能标准》,并于 2012 年 1 月 1 日生效。2013 年 1 月1 日及以后签订建造合同或 2016 年 1 月1 日及以后交付的所 427 中国材料进展第 33 卷有 5000t 级以上油船必须从货油舱保护涂层和耐蚀钢方案中选择采用一种。该性能标准附件中对耐蚀钢的适用范围、目标寿命、试验程序及性能标准做了规范和要求。标准规定耐蚀钢的目标使用寿命是 25a, 对耐蚀钢的要求是在货油舱顶腐蚀环境中 , 钢材 25a 后估计腐蚀损耗值(ECL)不超过 2mm; 在舱底腐蚀环境中,年均腐蚀速率(C.R ave)不超过 1.0mm/a。两种环境均要求焊缝处放大 1000 倍后,母材和焊缝金属之间不出现阶梯状不连贯表面。
2.3 国内外研究开发现状
2.3.1 日本和韩国
目前走在前列、技术较成熟的国家是日本。早在 1999 年,日本造船协会的 SR242 项目组利用实船测试、实验室模拟等手段对超大型油船(VLCC)进行了为期 3a 的研究,成功揭示了货油舱内的腐蚀状况、腐蚀机理及过程。他们通过实验获得了货油舱内部的腐蚀环境,如图 1 所示。在货油舱顶部,由于原油中的挥发成分、混入的海水、油田盐水的盐分、为防止爆炸而输入的惰性气体(5% O 2 ,13% CO 2 ,0.01% SO 2 ,余量为 N 2 ,体积分数)以及从原油中挥发的 H 2 S 等腐蚀性气体会在油轮货油舱的顶部内表面富集。同时,由于甲板温度在白天和夜晚的交替变化,上甲板内表面湿度大小会发生周期性变化。湿的H 2 S 和 O 2 以及 SO 2 等发生反应,会在上甲板内表面析出单质 S:
4H 2 S+SO 2 +O 2 = 4H 2 O+5S(1)
腐蚀了的钢板表面的铁锈也是催化剂,能加速 SO 2 和 H 2 S 向单质 S 的反应。钢板腐蚀导致新铁锈的生成以及固体 S的析出交替发生,由于固体单质 S 层较脆,容易产生剥离、脱落,如图 1b 所示。货油舱内底板有一层油膜,通过分析发现油膜由原油和混合沉淀物组成,同时包含大量的H 2 S和氯离子( 酸性介质),具有很强的阻抗作用,比焦油环氧树脂涂层的阻抗作用要显著。因此,油膜的存在可以显着增强油船货油舱下底板的耐腐蚀性。但洗舱会造成油膜破损,成为点蚀起源。在破损处会发生化学反应:
阳极(孔内):Fe → Fe 2+ +2e; (2)阴极(孔外):O 2 +2H 2 O+4e → 4OH - (3)随后亚铁离子发生水解,使得孔内的 pH 值大大降低,促进了阳极的进一步溶解。
Fe 2+ +2H 2 O→Fe(OH) 2 +2H + (4)
此外,从上甲板脱落的腐蚀产物S,对底板的点蚀同样有加速作用,如方程式(5)。图 1c 为观察到的货油舱下底板典型局部点蚀照片。
S+2H 2 O→H 2 S+2OH - (5)
通过研究发现,油船货油舱上甲板的腐蚀具有如下特征:① 通过检测分析 4 艘真实油船货油舱顶部空间气体的化学组成发现,在上甲板和原油之间的空间中含有高浓度的 H 2 S,如表 3 所示。②上甲板腐蚀层主要由铁锈和单质 S 组成,其中 60% 是单质 S。③上甲板平均腐蚀速率大于 0.1mm/a,速率较低,腐蚀均匀。而油船货油舱下底板的腐蚀具有如下特征:①在原油和下底板之间贮存有大量的滞留水,通过检测分析 3 艘真实油船货油舱滞留水的化学组成,发现含有高浓度的 Na + 和 Cl- ,约占总质量分数的 10%,如表 4 所示。但是其中不含 Mg、K 等离子,可以确定滞留水并不是海水。但其存在的位置和含有高浓度的 Cl- 会降低货油舱下底板的耐蚀性。②通过水洗、刮擦或酒精擦拭,致密的油膜层由于机械作用或化学溶解而被破坏,导致阻抗明显下降,增加点蚀速率,急剧地减弱了油膜对货油舱下底板的保护。③通过对 6 艘真实油船货油舱中 pH值实地检测,发现货油舱底部点蚀坑内的 pH 值在 0.85 ~ 1.16 之间,显着低于坑外的 pH 值,且点蚀速率随 pH 值的降低显着增加,最大可达 2 ~ 4mm/a。说明点蚀是强酸环境下的腐蚀。④通过观察和测量,发现点蚀坑具有很强的形状性和规律性,整个点蚀坑成等轴状,从点蚀坑的边缘到底部的腐蚀速率相同,以整体同步向外扩展的,点蚀坑越大则点蚀坑越深。表 5 综合比较了油船货油舱上下底板的腐蚀状况。
基于上述研究,日本新日铁、JFE、住友金属 3 大钢铁公司分别开发了新型油船货油舱用耐蚀钢。①新日铁NSGP TM-1 和 NSGP TM-2 。2003 年新日铁公司与 NYK 公司合作首次成功开发了新型耐蚀钢 NSGP TM-1 。表 6 给出了 NSGP TM-1钢的化学成分。从表 6 可知,其所含合金元素较少,成分与传统船用钢 AH32差别不大,完全符合 IACS 标准。模拟油船货油舱下底板点蚀环境的室内全浸腐蚀挂片实验表明,这种钢板及其焊接接头的耐蚀性比传统船板钢 AH32 高,NSGP TM-1 钢的力学性能和现场使用性能与传统船用钢相当甚至更优,且焊接、加工工艺完全相同,建造时无需进行特殊的施工治理。为验证新型耐蚀钢的性能,这 2 家公司于 2004 年将其应用在三菱重工建造的“TAKAMINE”号巨型油船货油舱下底板,该船运营 2.5a 后的考察结果表明,使用 NSGP TM-1 钢的货油舱下底板最大腐蚀孔只有 2.8mm,而采用传统钢板的则为 6.3mm。依据国际惯例,腐蚀孔超过4mm需要重新涂装船体,超过 7mm 则需要焊接维修。因此使用NSGP TM-1 钢的货油舱无需重新涂装,不仅可以省却建造时为防腐而进行的涂装工序,且在检修过程中也无需重新涂装,大大减少维护成本。2007 年,NSGP TM-1钢正式接受订货,截止 2010 年初,其累计发货量已经超过 1 万 t。2008 年,新日铁公司与 NYK 公司又开发了应用于油船货油舱上甲板的耐蚀钢 NSGP TM-2 ,经过 5a 年的实船试验,检测结果表明,NSGP TM-2 钢 5a 平均腐蚀速率小于 0.07mm/a,比传统钢降低了 38%。②住友金属 SMICO R E。2004 年,住友金属开发了 SMICO R E 耐蚀钢,2005 年将其应用于“SANKO BLOSSOM”号油船货油舱上甲板与下底板。经过 2.75a 的实船试验,船坞检查结果表明,与传统钢相比,SMICO R E 钢用于货油舱上甲板时腐蚀速率降低了 40%; 用于货油舱下底板时腐蚀速率降低 40% ~ 80% ,在世界上首次确认了耐蚀钢用于上甲板和下底板都具有优异的耐蚀性。③ JFE 公司 NAC5。JFE 公司于 2004 年开发出一种 NAC5 耐蚀钢。与传统钢相比,将不涂装的 NAC5 用于上甲板,可减少 10%的腐蚀量;将涂装的NAC5用于上甲板,涂层剥离速率降低了 40%,涂层剥离寿命提高 2 倍,上甲板寿命提高 5a 以上。
NAC5 耐蚀钢的化学成分和力学性能见表7。④JFE公司JFE-SIP TM -OT。2008年,日本 JFE 钢铁公司与三井 O.S.K 航运公司共同成功研发了 JFE-SIP TM -OT 高耐蚀厚钢板,并于 2008 年应用于油船货油舱舱顶与舱底。据三井商船称,该耐蚀钢板有以下特点:①抗点蚀性比传统钢板提高 5 倍,甚至可以帮助油船的上甲板耐均匀腐蚀;②与传统船体用钢板具有相同的可焊性和机械性能;③减少传统钢板每 2.5a 的干船坞维护工作。2010 年韩国也开始了油船货油舱用耐蚀钢的研究工作,并且在技术方面已经达到了相关标准的要求。
2.3.2 乌克兰与俄罗斯
钢铁冶金是乌克兰经济中的支柱性产业之一,工业部门齐全,产品产量居世界前列,苏联解体以前曾达到全国人均 1t 钢的水平。乌克兰继承了前苏联惟一的航母制造基地,造船业特别是军舰制造业,具有很高的水平,有能力建造包括航空母舰在内的一切舰艇。黑海造船厂作为前苏联时代惟一的航母建造总装厂,集中了很强的舰船科研和生产力量,曾被誉为“前苏联大型水面舰艇的摇篮”。前苏联几艘航母———“莫斯科”号、“列宁格勒”号、“基辅”号、“明斯克”号、“戈尔什科夫”号、“库兹涅佐夫”号、“乌里扬诺夫斯克”号全部在此建造。乌克兰和俄罗斯的海洋耐蚀钢制造体系不同于日本和欧美,采用低C、低Mn 和微合金化的成分设计,较高的 Cr 含量,Cu,Ni,P 等耐蚀元素较少加入。其核心技术是钢包精炼、中间包精炼、结晶器电磁制动等,达到有效去除钢中低熔点有色金属、非金属等腐蚀性元素和夹杂物。采用结晶器喂钢带等技术有效抑制连铸坯中心偏析和中心疏松,实现铸坯均质化。
2.3.3 中国
由于日本在该领域具有明显的技术优势,正在中国设置专利障碍,并作出各种承诺以维持其技术垄断地位。为了防止国外可能形成的垄断性供应或技术壁垒,2008年中国提出研发船用耐蚀钢。2010 年,国家科技部将“大型油轮货油舱用高品质耐腐蚀钢”列入国家科技支撑计划的重点开发项目,研究高硫、高酸油气环境中,低合金钢在 H 2 S、SO 2 、Cl- 和酸性盐水介质,以及上述各种复杂混合介质条件下的腐蚀规律,开发耐腐蚀合金钢成分体系、生产工艺及相关配套焊接材料,形成油船用耐蚀钢的腐蚀评价体系与标准,解决油气开采、输送和储运过程中的钢铁材料腐蚀问题,形成具有我国自主知识产权的油气开采与储运用耐腐蚀钢生产技术体系和评价标准规范。2012 年,工信部启动了“基于 IMO 标准的船用耐蚀钢应用技术研究”重大科技创新项目。到目前为止,我国油船货油舱用耐蚀钢研究项目已经取得了阶段性研究成果,突破了材料研发的核心技术难关,数家钢铁企业已经进入了工业试制与实船试验阶段。2010年~ 2011 年,鞍钢集团公司陆续开展了两轮 1000t 以上耐蚀钢工业试制,目前已提交船级社认证;2010 年,首钢开始对耐蚀钢进行前期研究,并联合开展腐蚀机理研究,研发油船货油舱腐蚀环境耐蚀钢,到 2012 年上半年已经成功完成 E36 级原油船货油舱用耐蚀钢及相关焊材的开发,并形成了配套的焊接工艺技术,各项性能满足国际海事组织耐蚀钢标准要求及目前的船板规范,具备了进一步开展造船应用研究的条件。2012 年,武钢、宝钢、南钢及湘钢等钢厂相继开发成功油船货油舱用耐蚀钢。武钢经过对高硫高酸油气环境下耐腐蚀钢的腐蚀机理、腐蚀条件、合金元素耐蚀性规律以及钢的洁净度、夹杂物、显微组织对耐蚀性的影响机理等方面的研究,确立了新钢种合金设计方案以及生产工艺,并将实验室研究成果运用到工业试制中,成功实现了油船货油舱用耐蚀钢及其腐蚀试验对比钢的批量试制,钢板性能均满足相关标准要求。南钢与东北大学、北京科技大学、武汉科技大学等高校进行合作,成功研发出高效焊接海洋工程用钢、原油船货油舱用耐蚀钢板 EH36-NS 以及专用焊接材料,并申请了相关专利。中国钢研科技集团有限责任公司钢铁研究总院和国家连铸技术工程研究中心在耐蚀钢成分设计方面亦取得可喜成果,研制的钢板的耐均匀腐蚀和耐局部腐蚀性达到或超过了日本 NAC5 钢板水平。总之,我国船用耐蚀钢国产化项目已建设了符合 IMO 标准的实验装置,突破了材料研发与检测的核心技术难关,国产船用耐蚀钢板各项指标满足 IMO 标准和船级社规范要求,造船工艺性能与传统船板相当,成本增量低于涂层成本,配套的焊接材料、型材、管材等研制工作也已取得初步成果。2014 年 4 月 28 日,中外运长航吴淞船舶工程有限公司启动了大庆 435 号油船改装工程,其改装技术方案由中船集团第七八研究所制订,经中国船级社审定,将采用由鞍钢公司提供的 1100t 船用耐蚀钢对货油舱内底板、上甲板进行改装。同时,将进行耐蚀钢与常规船板的对比使用试验,为后续相关科研工作提供实船数据和工程管理经验。这表明,我国钢企已经掌握了油船货油舱用耐蚀钢的关键制造技术,即将进入批量生产供货阶段。
2.4 问题与差距
长期以来,由于缺乏对大型油船货油舱用耐蚀钢等高品质海洋结构钢材的前瞻性探索,我国对海洋工程高端钢铁材料方面的耐腐蚀机理等研究明显落后于日本等发达国家,造成海洋工程用钢品种规格少、钢材性能差、质量不稳定、使用寿命短等一系列问题;我国耐蚀钢产业集中度低,达不到规模效益,研发、生产难度较大,钢企积极性不高;我国缺乏船用耐蚀钢国家标准和具有检测及认证资质的第三方机构;针对焊缝焊材的耐蚀性问题重视不足。以上问题严重制约了国家重大工程项目的建设和相关产业的发展。
目前,中国船企能建造国际航运界95% 所需船型,包括17.5万t散货轮、30 万 t 超 大 型 油 轮(VLCC)、30 万 t浮式生产储油船(FPSO)、8530 标箱第 6 代集装箱船、14.7 万 m 3 LNG 船、122m 自升式钻井平台 JU2000 等。目前在建 9 座 30 万 t 级造船船坞,并在规划50 万 t 级和 100 万 t 级船坞。但是,在中国船企建造的船舶中,60% ~ 70%以低技术含量的散货船为主,大型油船、高技术含量的钻井船及液化天然气船等承接量少,在先进船舶制造及海洋工程装备设计制造技术、大型油船货油舱用耐蚀钢的研究与开发等方面,才刚刚进入实船验证阶段,与日本等国家相比,还有较大差距。
3 耐海水腐蚀钢
3. 1 重大需求分析
占地球表面积约 71% 的海洋中蕴藏着丰富的资源,随着世界人口的日益增长和陆地资源不断的消耗,未来人类的生存会越来越依赖于海洋,海洋将成为矿产、能源和食品资源的主要供应基地。为此,海洋开发被列为 2l 世纪的重点目标之一。我国享有主权和管辖权的海域面积接近 300 万 km 2 ,但海洋石油和天然气等资源的平均探明率分别只有 12.3% 和 10.9%,远远低于世界73.0% 和 60.5% 的平均水平。随着经济的迅速发展和科学技术水平的提高,我国海洋开发事业有了突飞猛进的发展。由于技术越来越复杂,制造成本越来越高,人们希望海洋装备的使用寿命成倍提高,而耐海水腐蚀材料的开发和应用研究是海洋开发的基础和前提,导致耐海水腐蚀钢材越来越受到人们的重视,用量逐年增加。另外火电厂、核电厂、化工厂和海水淡化工程等项目中也是耐海水腐蚀钢另一个主要应用领域。有报道称,到 2015 年全世界海水淡化能力将增长到 6200 万 m 3 ,所增加的投资预计为 950 亿美元。而中国也是一个水资源贫乏的国家,这个新兴领域对耐海水腐蚀钢的需求必定持续增长。
由于海洋的特定环境对海洋工程材料有很多特殊要求:最主要的是耐海水腐蚀问题;其次是深海下密封壳体结构的强度问题。因此研究高强、轻质、耐海水腐蚀、低成本的材料以及合理的结构设计和选材,已成为海洋工程的关键技术之一。
3. 2 耐海水腐蚀钢的发展概况
海水中含有大量的以 NaCl 为主的盐类,占总含盐量的 88.7%。由于它们易于电离,使海水中的 Cl- 含量增高,达1. 898%(质量分数);同时提高海水电导率,其平均电导率可为 4×10- 2 s/cm,远远超过河水(2×10- 2 s/cm)和雨水(1×10- 2 s/cm)。为此,海水中金属表面难以保持稳定的钝态,易于发生电化学腐蚀,极易发生劣化破坏。目前海洋污染趋于严重,海洋环境更加复杂,从而使得海洋工程用钢材的腐蚀问题更加突出。大型海洋工程结构在海洋环境中的腐蚀一般分为5个区: 大气区、飞溅区、潮差区、全浸区及海泥区。在这些不同的区域,钢材的腐蚀速率是不同的,图 2 是钢桩在海水不同腐蚀区域腐蚀速率示意图。
除了海水区域不同对钢材腐蚀有不同的影响外,就是在一同区域的海洋环境中也含有其他诸多影响因素,如海水的盐度、pH 值、温度、溶解气体(O 2 、CO 2 等)流速、微生物以及污染等,这些因素有时交差作用,造成了海洋环境对钢材腐蚀的一个极其复杂的过程。
目前钢铁材料的防腐蚀方法大致可分为 4 类:①涂层法;②长效法;③阴极保护;④采用本身具有抗腐蚀能力的不锈钢。但大规模使用预防措施所产生的环境污染大、能耗大、投资大,其成本高得难以承受,并且不锈钢的力学性能和焊接性能也很难满足各种工程的需要,因而钢铁材料的腐蚀情况一直没有得到根本的控制。研究表明,通过添加微量合金元素可以在钢材表面形成含有特定结构、具有离子选择特性的致密保护层,使钢材本身具有耐腐蚀性能,并保持优良的综合力学性能及使用性能。
3.3 耐海水腐蚀钢国内外发展现状
国外对耐海水腐蚀钢的研究始于 20世纪 30 年代,其中最为活跃的国家是美国和日本。美国最先开始耐海水腐蚀钢的研究,于 1951 年开发了 Ni-Cu-P系 Mariner 钢, 含 0.5% Ni、0.5%Cu、0.1%P。此类钢在飞溅区的耐海水腐蚀性能较好,为普通碳素钢的 2 ~ 3 倍,但 P 含量偏高(0.08% ~ 0.15%),厚度大于 20 mm 的钢板不适宜焊接。在此基础上,世界各国相继开发了各种系列的耐海水腐蚀钢。如日本针对 Mariner钢 P 含量高、焊接性能差研制了 P 含量≤ 0.03% 的 Mariloy(Cu-Cr-P、Cu-Cr-A1-P、Cu-Cr-Mo)系列低合金耐海水腐蚀钢。Mariloy 系列钢之所以具有好的耐蚀性,主要原因有:①铬、硅共存,促使在腐蚀过程中形成稳定的硫酸盐膜,能阻止在污染海水中细菌的生长,从而减缓了钢的腐蚀;②由于硅、铬、铜在锈层中富集,并直接作用于金属表面,使紧贴基体锈蚀产物变得细小致密,阻碍了海水中溶解氧向钢表面扩散,减缓了钢的腐蚀速率。
中国耐海水腐蚀钢的研究始于 1965年,从300多个钢种中筛选出16个钢种,并于 1978 年进行了耐蚀性能的统一评定。4 年的试验周期表明,Cr-Mo-Al系的 10Cr2MoAl R E 钢耐蚀性能最好。近期宝钢借鉴日本耐海水腐蚀钢成分特点,综合考虑中国近海海水腐蚀介质的环境作用因子,通过优化调整化学成分及采用合理轧制工艺技术,成功开发出Cr-Cu-Mo 系耐海水腐蚀钢种 Q345C-NHY3。该钢种具有优良的力学性能、焊接性能和耐海水腐蚀性能等,能够满足海洋钢结构的制造要求。已经向东海洋山深水港码头二期及三期工程供货约 30t,主要用于加工海底钢管桩。这是国内首次在工程中大批量应用耐海水腐蚀钢,整个工程结束预期应用量达 50 余万 t。
目前国外生产的低合金耐海水腐蚀用钢按成分系列可分为 Ni-Cu-P 系、Cr-Nb 系、Cr-Cu 系、Cr-Al 系、Cr-Cu-Si 系、Cr-Cu-Al 系、Cr-Cu-Mo 系、Cr-Cu-P 系及 Cr-Al-Mo 系等。我国研制的耐海水腐蚀钢试验钢号近 200 种,其中10Cr2MoAl R E、08PV R E、09MnCuPTi、10MnPNb R E、10NiCuAs、10CrMoAl 等已通过鉴定,但尚未推广,在大型固定式和移动式海洋结构件上应用较少。
3.4 问题与差距
我国在耐海水腐蚀钢方面与国外先进国家之间存在较大差距,如表8 所示。我国在海工钢和船用耐蚀钢方面存在以下突出问题:①海工用钢需求有限,科研和生产难度较大。我国主要海工总装制造企业手持各类海工钻井平台不到100 座 / 艘,计划在 3a 内交付。每年交付量在 30 ~ 40 座 / 艘左右,年均用钢量仅为 60 ~ 80 万 t。加之海工用钢的特点为多品种、小批量,达不到规模效益。②对耐海水腐蚀机理的研究不足。
由于各合金元素在不同海洋环境条件下的耐蚀效果不同、各牌号钢种在不同海洋环境条件下的耐蚀性能也有很大的差异,加上因试验方法不同而造成的误差等影响,腐蚀试验结果必然有所不同,而我国缺乏该领域检测与第三方认证机构。特别对我国南海高湿热、强辐射、高 Cl- 海洋环境下的钢铁材料腐蚀问题还未得到研究与验证,腐蚀数据积累不足。③焊缝焊材的耐蚀性问题未得到重视。由于接头各部分在成分和组织上的不均匀性、残余应力以及应力集中等因素的影响,使得接头的耐蚀性往往低于母材,而在整个焊接接头中焊缝是耐腐蚀性最差的部位。
4 对策与建议
随着世界安全和环保意识的提高以及经济全球化引起的物流量增加,强化对船舶与海工装备结构安全性、可靠性、及海上运输高速化、高效化的要求,需进一步提供高性能钢材。如果国内不能生产而大量进口,不但会推高造船行业的建造成本;而且,如果船东青睐这种钢材,而国外不予供货的话,船企接单也将受到影响。因此,需要国家政策引导支持,造船、海工、钢铁、航运等企业以及高校科研院所紧密协同与合作。建议:①加强政策引导和财政支持,加大研发投入。在国家层面制定海洋耐蚀钢的科技发展规划,加大研发投入。同时,改变资金投入机制,让有限的资金集中投放到由企业、高校、研究机构等组成的优势协同创新体。建设我国海洋耐蚀钢 4 大区域中心: 即以环渤海湾(鞍钢、首钢、大连造船、北船重工(青岛)、中国科学院金属研究所、中国科学院海洋研究所、东北大学、北京科技大学、大连理工大学、清华大学等)、长江口(宝钢、南钢、沙钢、沪东中华造船、振华港机、上海交通大学、上海大学、南京工业大学、南京理工大学、浙江大学等)、长江中上游流域(武钢、重钢、攀钢、华菱集团、武船重工、中船重工 719 研究所、武汉科技大学、华中科技大学、武汉大学、武汉理工大学、重庆大学等)和珠江口(宝钢集团湛江基地、武钢集团防城港基地、广州广船国际股份有限公司、广州黄埔造船厂等、华南理工大学、香港科技大学等)为重点的区域中心。②以海洋耐蚀钢的协同研发为切入点,搭建三会一社(中国船舶工业行业协会、中国钢铁协会、中国船东协会、中国船级社)、造船企业、钢铁企业、航运企业、高校科研院所联合参与的“产、学、研、用、检”的工作及信息交流平台,使海洋耐蚀钢的研发从临时协调机制转变为长期合作机制,并尽快落实船用和海工装备耐蚀钢的应用研究和实船考核工作,定期探讨船用耐蚀钢的研发推进工作,规范行业准入和认证管理,建立和完善船用和海工装备耐蚀钢标准体系以及船用和海工装备耐蚀钢加工配送体系。③加强对海洋耐蚀钢,特别是我国南海高湿热、强辐射、高 Cl- 环境下的腐蚀机理研究。建设海洋耐蚀钢的检测机构和第三方认证机构等共同平台。④加强海洋耐蚀钢的焊接性研究与评定,研究开发相配套的焊接材料、焊接工艺。
5 关键技术与核心科学问题
5.1 关键技术
海洋耐蚀钢研究与开发的关键技术包括:中厚板与特厚板的纯净度控制技术(尤其是超低 S 的控制)、腐蚀性夹杂物(MnS 和nCaOmAl 2 O 3 等)控制技术、铸坯中心偏析控制技术、特厚板的轧制技术与工艺、中厚板与特厚板的焊接性评定与焊接工艺、以及配套焊接材料的研究与开发等。
5.2 核心科学问题
海洋耐蚀钢研究与开发的核心科学问题主要包括:
新型易焊接海洋耐蚀钢厚板与特厚板的设计理论与原理,海洋耐蚀钢厚板与特厚板均质化、细晶化、高韧化机理,海洋耐蚀钢厚板与特厚板高效高可靠性焊接冶金原理,海洋工程厚板与特厚板以及焊接接头的耐蚀机理,包括在我国南海高湿热和海洋微生物等特殊环境下的腐蚀机理等。
免责声明:本网站所转载的文字、图片与视频资料版权归原创作者所有,如果涉及侵权,请第一时间联系本网删除。
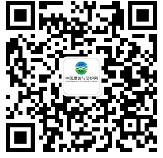
官方微信
《中国腐蚀与防护网电子期刊》征订启事
- 投稿联系:编辑部
- 电话:010-62313558-806
- 邮箱:fsfhzy666@163.com
- 中国腐蚀与防护网官方QQ群:140808414