海洋是人类活动的重要组成部分,在战略国防中有着重要地位,是当今国家安全的重要领域。对海洋主权的维护和保障离不开海军舰艇的发展,而高强钢又是海军舰艇发展的重要基础材料,其耐腐蚀性是海军舰艇先进性和安全性的决定性因素之一。因此海军舰艇用高强钢的发展和应用具有重要的意义和价值。
海军舰船,尤其是潜艇在现代战争中具有重要而又特殊的作用,各国海军都非常重视舰船及潜艇的发展,随之而来,高强钢在舰艇中也得到了广泛应用。海军舰艇所处环境复杂、作战及安全性要求极高,舰艇用钢既要有高强度和抗腐蚀性,还要有优良的韧性、焊接性、低磁性、加工性、抗疲劳性及稳定性。
目前,随着细晶及超细晶、析出物及微观组织控制、微合金化、TMCP 等技术的广泛应用,高强钢的各项性能不断提升,为海军舰艇用钢及其耐蚀性的发展打下了坚实的基础。美、欧、俄、日等发达国家和地区舰艇用高强钢的研发、生产及应用较早,规格完善,强度、耐腐蚀性等综合性能及加工工艺为世界先进水平,最高屈服强度已达1100 MPa。我国也在不断加强舰艇用高强钢的研发和应用,但在强度、规格、耐腐蚀性及加工焊接等方面还存在一些的问题,对我国海军舰艇的发展产生了一定的制约,所以对海军舰艇用高强钢及其耐蚀性的研究成为重要课题。
文中对目前国内外舰艇用高强钢的使用现状、腐蚀和焊接问题进行了综述,分析了舰艇用高强钢的发展趋势,为高强钢在我国海军舰艇的应用及防腐蚀工作的发展提供参考。
1 航母及舰船用高强钢现状
目前,舰船尤其是航空母舰使用高强钢的性能状况差异较大,其中由于航母甲板需要承受飞机起降的巨大冲击力以及燃气、爆炸冲击,海洋及其大气腐蚀等极端复杂的服役环境,技术要求最为苛刻,强度、厚度、耐腐蚀性高于一般船体结构钢。
1.1 美国航母及舰船用高强钢
美国航母及舰船用高强钢性能处于世界领先水平,其航母大量采用690 MPa 级高强钢作为甲板用钢,耐腐蚀性能优异,主要用钢分为HY 和HSLA 系列钢。
美国从20 世纪50 年代开始建立HY 系列高强度船体结构钢体系。开发了镍铬钼系的淬火回火高韧性且屈服强度达550 MPa 的HY-80 调质合金钢,用于航母制造,耐腐蚀性能良好。之后在HY-80 钢的基础上,通过改变合金含量及回火温度,研制了屈服强度高于690 MPa 的HY-100 钢,于1966 年用于航母甲板。由于合金成份和含量的优化,其耐腐蚀性能也得到较大的提升,是当前其航母重要部位的主要材料。于20 世纪60 年代中期进一步开发了屈服强度高于896 MPa 的HY-130 钢,但其强度的提升,海洋环境下应力腐蚀的敏感性也相应升高。直到20 世纪80 年代,HY 系列钢仍为美国舰船的主要结构用钢。
20 世纪80 年代后,随着超低碳、超纯净钢冶炼、微合金化及控轧控冷等冶金技术的发展应用,为降低成本、减少焊接工艺和降低腐蚀开裂的发生,美国开始研制不需预热或只需较低温度预热就能焊接的HSLA 系列钢。HSLA 钢的组织为含C 量极低的细晶粒铁素体或珠光体钢,靠低C 微合金化、控轧控冷、沉淀硬化等技术取得了优良的性能。由于其碳含量极低,晶粒被细化,并减少了焊接及其热影响区的影响,其耐腐蚀及腐蚀开裂的性能也得到大幅提升,使船体结构钢的开发及耐腐蚀性能进入了一个新时代。
HSLA-80 钢是美国最早研制成功的新型高强度、高韧性结构钢,不但强韧性达到HY-80 钢的水平,而且焊接性和耐腐蚀性更好。因具有优良的焊接性能,且合金元素含量低,耐腐蚀性好,简化了舰船建造工艺,降低了成本。该型钢基本取代HY-80钢用于建造大型水面舰艇,“尼米兹级”核动力航母的某些结构采用此钢种。HSLA-100 钢是美国为新型航母壳体研制的具有优良焊接工艺的高强钢,其性能已达到HY-100 钢的水平,焊接材料与其相同,厚度可达100 mm,但该钢可在比HY-100 钢更低的焊接预热层间温度下施焊,从而降低建造成本。
HSLA-100 钢已部分代替HY-100 钢用于航母制造,已应用在“斯坦尼斯”号核动力航母。HSLA-115 钢和HSLA-65 钢是美国根据减重及重心降低的要求而研制的,屈服强度分别达785 MPa 和445.9 MPa,其应用在甲板上,不仅降低了航母重心,还显着降低了甲板厚度,从而减轻航母质量,HSLA-115 钢现已在新型航母“福特”号上试用。HSLA-65 钢是低碳含锰钢,不预热既可焊接。从20 世纪90 年代开始,美军对HSLA 钢及其配套材料的耐腐蚀性进行了系统的研究,目前已取得巨大进展。
1.2 英国航母及舰船用高强钢
英国在20 世纪40 年代以前制造舰船壳体主要采用U,X,W 钢。20 世纪50 年代采用了Mn-C 系屈服强度达432 MPa 的调质钢QT28 钢,由于其Mn 元素含量高,易发生应力腐蚀开裂。1958 年至1965 年又广泛采用屈服强度高于550 MPa 的调质钢QT35钢,由于该钢在冶金中出现层状撕裂和应用中腐蚀开裂的问题,被从美国进口的HY-80 代替。之后英军仿造HY-80 钢研发出Q1N 钢,其化学成分与HY-80 相当。20 世纪70 年代以后仿制美国的HY-100 和HY-130 钢,开发出Q2N 和Q3N 钢,此系列钢虽然为仿制美国HY 系列,但其更加注重钢的纯净度,冶炼中严格控制S,P 含量,并在成品强度性能中规定了钢的屈强比上限值,因而对冶炼水平和轧制热处理工艺要求更高,由于其C,S,P 含量控制较好,因而抗腐蚀开裂的性能更优异。此外,在制造水面舰船上英军还大量使用一般碳素钢、A 级钢、B 级钢。为降低成本,充分发挥材料性能,常在一条舰船上根据设计要求使用各种不同强度级别的材料和防腐蚀工艺。目前,英国“无敌”级航母使用的为法国软钢,其屈服强度较低,一般仅用于制造小型垂直起降或者直升飞机航母,耐腐蚀性能较好。
1.3 其他国家航母及舰船用高强钢
俄罗斯、法国等国也在不断开发舰船用高强钢系列。俄罗斯在20 世纪60 年代已形成较完整的AK 系列钢,目前已基本被AB 系列钢所取代,АB系列钢最高强度已达到1175 MPa,耐腐蚀性能极佳。法国在第二次世界大战后开发了60HLES,80HLES,100HLES 等3 代高强钢,“戴高乐”号航母甲板使用的为550 MPa 的HY-80 特种钢。
1.4 中国舰船用高强钢
从20 世纪60 年代初开始,我国不断通过研仿,成功试制了主要舰船用钢,如921,922,923 钢和其配套使用的604,607,608 铸钢及925 锻钢,907,917钢等。自20 世纪60 年代后期开始,自行研制了第一代舰船用钢,锰系无镍铬901,902,903 低合金船体钢和低镍铬的904 等舰艇用钢及配套材料。进入20世纪80 年代,在结构钢及配套材料方面正在逐步形成以强度级别为系列和品种规格较完整的耐蚀可焊钢系列,主要代表有390 MPa 级907A 系列钢、440MPa 级耐海水腐蚀性能和低温性能好的含镍铬945系列钢、590 MPa 级921A 系列钢、785 MPa 级980 系列钢等。我国自行研制的舰船用钢在海军舰艇建造中已得到成功应用,建造了几十种型号的舰船,舰船用钢的研制与耐腐蚀性发展基本满足了不同时期舰船建造的需要,但与国外先进海军舰船用钢及耐腐蚀性能相比还有一定差距。
2 潜艇耐压壳高强钢现状
潜艇在复杂的海洋环境中工作,耐压壳体是由带加强环的圆柱、圆锥和球壳组成,所以其用钢包括不同厚度钢板、型材、铸钢和锻钢。高强度钢的使用使潜艇能够承受其工作深度产生的静压强和在整个服役期内多次下潜和上浮产生的周期性载荷对耐压壳的影响。特别是随着科学技术的发展,为增强战斗力和保障安全性,各国海军都积极研制潜深大、航速快、耐腐蚀、噪音及磁性低的潜艇,而新型高性能钢的应用对其产生了重要的影响。其中,美、俄、日、法和德等国在研制潜艇用钢方面处于领先地位。
潜艇耐压壳使用的金属材料主要有钢和钛合金。由于所用钢的性能差距较大,各种潜艇性能差别很大。普通潜艇,屈服强度在300 MPa 左右,最先进的核潜艇用钢,强度已经高达1100 MPa,比航母用钢还要优良。目前,美、俄、英、法、日、德等国相继研制成一系列的高强度、高韧性、耐腐蚀的耐压壳体结构钢,使潜艇下潜深度从200 m 提高到600 m 左右,俄、美、日等国已采用屈服强度为900~1100MPa 级超高强度钢做为潜艇耐压壳体。
2.1 美国潜艇耐压壳高强钢
美军潜艇的耐压壳主要使用HY系列高强钢及钛合金。已使用HY-80,HY-100,HY-130 和HY-180等高强度、高韧性结构钢,屈服强度分别为550,690,897,1100 MPa,美国潜艇用钢力学性能见表1。
前2 种是潜艇耐压壳体主要用钢,潜艇每年需要这2种钢铸锻件各250 t。20 世纪60 年代前,美海军潜艇耐压壳标准用钢为HY-80 钢,美军“洛杉矶”级潜艇的耐压壳及“伊桑艾伦”级核潜艇的全部耐压壳体使用HY-80 钢。现今强度更高的HY-l00 钢已成为美国海军潜艇耐压壳的标准用钢,美海军“海狼”级潜艇及最新型核潜艇“弗吉尼亚”级的耐压壳都采用HY-l00 钢。20 世纪80 年代用新研制的HY-l30 钢建造深海试验潜艇“海豚”号等潜艇的分段,但其在建造“海狼”号核动力潜艇时产生焊接裂缝而被迫改为HY-100 钢,在对含碳量的控制,焊接材料的改进,耐腐蚀开裂研究及应用经验的积累之上,该钢已用于建造潜艇。HY-180 钢为最新研制的超高强度钢,由于其强度高达1100 MPa,对焊接及耐应力腐蚀开裂提出了更高的要求,目前正在不断的完善中。美军“海崖”号深潜器使用钛合金作耐压壳材料,下潜深度为6100 m,耐腐蚀性能极佳。
2.2 日本潜艇耐压壳高强钢
日本在制造强度较高的特种合金钢方面具有先进技术,潜艇耐压壳体用钢发展处于世界前列,已从NS-30,NS-46,NS-56,NS-63,NS-80,NS90 发展到目前的NS-110 钢,其屈服强度分别为294,451,550,617,780,883 和1080 MPa,日本潜艇用钢力学性能见表2。其中NS-110 钢是目前全球潜艇耐压壳体采用的屈服强度等级最高的可焊接高强钢。
日本潜艇用钢的发展主要采用仿制和自创相结合的方针,20 世纪60 年代初日本潜艇耐压壳材料使用NS-30 和NS-46 钢。此后对国外高强度钢进行了深入研究,包括美国海军使用的高强度潜艇钢,研制成了NS-63(HY-80 改进型),NS-80,NS-90(仿制HY-l00,HY-l30)钢。NS-90 钢用于潜深达2000 m的深海调查船外,NS-63 和NS-80 钢都已分别用于建造“涡潮”、“夕潮”级潜艇的耐压壳,耐腐蚀性能良好。为增加潜艇下潜深度,在美国HY-130 和HY-180 钢的基础上研制了NS-110 钢,将其应用于“春潮”级潜艇的部分耐压壳上,使潜艇潜深达到350 m 左右。新一代“亲潮”级潜艇艇壳全部采用NS-110 超高强度钢,因焊接、腐蚀开裂等问题和设计水平限制,“亲潮”级潜艇潜深只有450 m 左右,该钢为调质钢,焊接工艺相对复杂,目前仍在解决焊接效率低等问题。日本的“深海2000”深潜器使用钛合金作耐压壳材料。
2.3 英国潜艇耐压壳高强钢
英国也是潜艇用钢开发较早的国家。于二战之后研制的QT 系列钢不断应用于潜艇。首先用QT28 来建造潜艇,并于1958 年用QT35 钢建造英国第一艘攻击型核潜艇“无畏号”。QT35 曾大量用于潜艇壳体结构,之后于1969 年开始用Q1N 钢制造潜艇耐压壳体,至今仍用Q1N 钢制造核潜艇壳体,如“特拉法加”号核潜艇。目前新研发的Q2N 和Q3N钢,已用于建造最新设计的核潜艇,英国“机敏”级潜艇计划使用Q2N 作耐压壳材料。英国在潜艇建造过程中所用钢种及性能见表3。
2.4 俄罗斯潜艇耐压壳材料俄罗斯为世界上首先使用钛合金建造潜艇耐压壳的国家,其用钛合金建造潜艇的技术世界领先。
钛合金具有强度高、质量轻、低磁性和耐腐蚀等优点,用其作耐压壳材料可降低潜艇排水量、增大潜深和提高潜艇隐蔽性。俄罗斯先后制造了四级钛合金耐压壳核潜艇,分别为S、M、阿库拉、奥斯卡级,其中奥斯卡级的下潜深度已达1000~1300 m,耐腐蚀性极佳,但钛合金潜艇也存在成本过高的问题。俄罗斯某些潜艇的耐压壳材料采用强度达1175 MPa 的CB-2钢,用其制造的阿库拉级潜艇潜深750 m。
2.5 其他国家潜艇耐压壳高强钢
法国也是世界上采用先进潜艇耐压壳体高强钢的国家。20世纪80年代后期采用屈服强度达980 MPa的100HLES 钢,作为大型核潜艇“凯旋”级的耐压壳体。德国为世界上唯一用低磁钢建造潜艇的国家,212 级潜艇艇体采用一种非磁奥氏体钢制成,不但强度高,而且具有特殊弹性,能防搁浅和碰撞,其低磁钢的屈服强度与HY-80 钢相当。由于其韧性好,因此应力腐蚀开裂敏感性较低。
2.6 中国潜艇耐压壳高强钢
目前,921A,922A,923A 钢及其配套材料是我国最主要的潜艇用钢。最新的核潜艇耐压壳体用钢为980 系钢,具有强度高、韧性高、焊接性好、耐海水腐蚀性优、综合性能优良等特点,但与国外先进水平还有差距。我国7000 m 深海载人潜水器“和谐”号采用钛合金作为耐压壳材料。
3 舰艇用高强钢存在的问题
3.1 舰艇用高强钢腐蚀问题
舰艇在复杂的海洋环境下工作,面临很多严重的腐蚀问题。随舰艇用钢强度的不断提高,尤其是潜艇下潜深度的逐渐增大,压力的不断提升,舰艇的腐蚀问题变得更加复杂化和多样化。
3.1.1 海洋腐蚀问题
舰艇用高强钢长期服役于盐雾、海水等高Cl-的复杂环境,受到海水及海洋生物的作用而产生电化学腐蚀,漆膜易发生皂化、老化等问题,漆膜下金属发生严重腐蚀,不仅降低了材料的力学性能,而且缩短其使用寿命。随着对先进性和安全性要求的不断提高,舰艇用钢耐腐蚀性能的要求也不断提升。现在防止海水腐蚀采用的方法有增加腐蚀裕量、涂层和阴极保护等。
3.1.2 阴极保护影响分析
对舰艇而言,高强度结构钢的应用成为趋势,随性能及安全性要求的不断提高,钢的强度也不断提升。一般情况下,钢强度越高,氢脆破裂敏感性越大。舰艇结构材料主要受电化学腐蚀机制作用,目前采用的阴极保护技术是控制船体结构腐蚀长效且经济的措施之一。在采用阴保的系统中,保护电位过负时,被保护金属表面会产生较强的析氢反应,使氢容易进入金属,晶格应变加大,致使韧性及延展性降低、脆化,在外力下引起氢脆破裂。因此舰艇钢采用阴极保护时,必须严格控制阴极保护电位范围,使舰艇既被有效保护,又避免产生氢脆等不良影响,保证舰艇的安全性。
3.1.3 应力腐蚀问题
随着舰艇用钢强度级别的提高,会导致应力腐蚀等局部腐蚀的敏感性增加,尤其是潜艇随着下潜深度的增加,压力逐步增大,在海水介质作用下可能会发生应力腐蚀开裂。对舰艇而言,材料强度愈高、应力水平越大,应力腐蚀断裂敏感性越高,表面阳极极化行为越明显。应力腐蚀对舰艇的安全性和长期服役产生了极大的不利影响,导致很多危险性事故的发生。德军采用Mn-Cr 系低磁钢建造U1 和U2 潜艇,在使用过程中出现了严重的晶间应力腐蚀开裂;前苏联海军用研制的舰艇低磁钢,建造655 型核潜艇构件,但在海水介质作用下,发生了晶间腐蚀,导致裂纹产生。
3.2 舰艇用高强钢焊接问题
焊接技术的研究与发展对提高舰艇作战性能及安全性具有重大意义。随着舰艇用钢强度、厚度及合金元素的不断提高,对焊接工艺及焊材要求日趋严格,但其焊接易产生氢致裂纹;造成气孔、夹渣、未熔合等焊接缺陷;合金元素增加导致焊接接头过度硬化;因焊后热处理不当引起硬度过高,韧性变低,耐腐蚀性能下降等材料性能裂化;焊接缺陷和焊后材料性能下降引起腐蚀开裂问题;预热及热处理使成本增加等问题也不断呈现。焊接区中的氢含量、拘束应力状态和焊接区微观组织是高强度钢焊接裂纹形成和发展的主要因素。因此加大焊接技术及其配套处理工艺的研究变得尤为重要。目前在满足舰艇性能要求的条件下,高强钢焊缝金属采用低匹配强度技术,降低了建造成本;加强用均热处理和数学模型解决氢致裂缝问题;调整化学成份和热处理工艺,降低或取消焊接预热;通过细化热影响区的晶粒尺寸,减小碳当量,并用TiN,AlN 进行固氮等方法改进焊接热影响区的韧性和耐腐蚀性能。
4 舰艇用高强钢发展趋势
目前从舰艇战斗力、防御性、安全性、环保性等方面考虑,国内外舰艇用钢一直向高强度、厚规格、高的低温韧性、优良的焊接性、良好的抗层状撕裂性的方向发展,潜艇材料更向钛合金钢方向发展。由于舰艇的特殊性,以下方面也成为其重要发展方向。
1)大规格。为满足舰艇大型化、完整化要求,钢板规格不断加大。钢材规格增大,减少了焊接及焊后热处理等过程,降低了建造成本。
2)低磁性。舰艇用钢的低磁性在舰艇的隐蔽性方面发挥了巨大作用,尤其是潜艇用钢的低磁性非常重要,可以提升潜艇的战斗能力和安全性。
3)开发可抑制舰艇涂膜劣化的新型钢板和无需涂装的耐蚀板。开发可抑制舰艇涂膜劣化的新型钢板和无需涂装的耐蚀板对提高舰艇的服役年限,减轻舰艇对环境的影响,并降低舰艇的建造和维修成本有重要作用。
4)开发复合材料。国外正在研究采用复合材料来建造潜艇壳体,并已成为一种趋势。复合材料是由增强纤维和树脂组成的新型材料,目前虽未正式应用,但其具有重量轻、强度高、耐腐蚀、低磁性等优点,可以节省重量,增大下潜深度或提高有效载荷。
5)高耐蚀性。由于大量的腐蚀和腐蚀开裂问题的发生,耐腐蚀性成为高强钢越来越重要的性能,制约着高强钢在舰艇中的应用,目前研究的主要重点是不同组织和元素及其含量对钢耐蚀性的影响,优化和开发材料的腐蚀防护方法,优化冶金和焊接工艺降低腐蚀开裂的可能性。
5 结语
随着各国对海洋权益及安全问题重视程度的不断提高,海军舰艇用高强钢及其耐腐蚀性取得了长足的进步。我国虽然在海军舰艇用高强钢的研发和应用方面取得了一定的成绩,但与欧美等发达国家和地区相比,在钢的强度、焊接性能、耐腐蚀性能等方面都存在一定的差距。在对海军舰艇先进性和安全性要求不断提升的今天,应依托冶金、材料、腐蚀等学科的发展,加强海洋舰艇用高强钢及其耐腐蚀性的研究。
更多关于材料方面、材料腐蚀控制、材料科普等方面的国内外最新动态,我们网站会不断更新。希望大家一直关注中国腐蚀与防护网http://www.ecorr.org
责任编辑:王元
《中国腐蚀与防护网电子期刊》征订启事
投稿联系:编辑部
电话:010-62313558-806
邮箱:fsfhzy666@163.com
中国腐蚀与防护网官方 QQ群:140808414
免责声明:本网站所转载的文字、图片与视频资料版权归原创作者所有,如果涉及侵权,请第一时间联系本网删除。
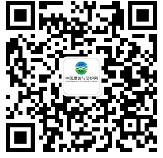
官方微信
《中国腐蚀与防护网电子期刊》征订启事
- 投稿联系:编辑部
- 电话:010-62313558-806
- 邮箱:fsfhzy666@163.com
- 中国腐蚀与防护网官方QQ群:140808414