0 引言
喷涂聚脲弹性体(Spray Polyurea Elastomer,简称SPUA)是近10年来发展起来的一种新型无溶剂、无污染的绿色施工技术。聚脲与传统防腐涂料相比,不仅具有较高的抗冲击性、伸长率和撕裂强度,而且具有优异的耐化学介质性、防水性、耐磨性、防腐蚀性和施工性能。随着国家重点工程建设速度的加快和经济的快速发展需要,聚脲材料已经在混凝土防护工程、铁路交通、化工防腐、水利工程等领域广泛应用。聚脲与其它防腐涂层一样,受到紫外线、腐蚀介质、干湿交替以及外力损伤等因素的影响,涂层会产生老化和破坏,导致涂层防腐蚀性能降低[1]。本文主要研究了聚脲涂层在不同介质中的水解稳定性、涂层耐酸碱性、耐热性以及在户外曝晒过程中涂层力学性能的变化。目的是通过对聚脲材料的性能研究,可以更好地预测出聚脲材料在不同腐蚀环境条件下的使用寿命,并且可以有选择地发挥聚脲的优势,更好地拓展聚脲材料的应用领域。
1 实验部分
1.1 原材料
MDI-50:烟台万华;端氨基聚醚:T5000、D2000美国HUNTSMAN公司; 端羟基聚醚:DL-2000山东蓝星东大;E-100:美国雅宝公司;钛白粉706:杜邦;分散剂、催化剂:市售。
1.2 预聚体的合成
将计量好的端羟基聚醚DL-2000加入至三口烧瓶中,升温至110℃,保温在105~110℃真空除水约2h后,停止抽真空和加热。待物料降温至40~45℃,加入规定量的MDI-50,搅拌均匀,在65℃保温30min后,升温至80℃,在80±2℃保温2h,测量预聚物的NCO含量至规定值后降温出料。
1.3 漆料组分制备
按计量将端氨基聚醚T5000、D2000和扩链剂E-100加入容器中,用高速分散机高速分散均匀,按比例依次加入各种助剂、颜料,高速分散均匀并研磨至细度至合格,制得漆料组分。
1.4 聚脲涂层的制备
采用固瑞克E10HP聚脲喷涂设备进行喷涂,物料温度为65℃,喷涂压力为2000psi。聚脲涂层凝胶时间为10s,表干时间为70s,涂层厚度为2mm。
2 结果与讨论
2.1 聚脲涂层力学性能
将聚脲样片置于温度为23±2℃,湿度为50%条件下养护7天后进行涂层性能测试。测试结果见表1。
表1聚脲涂层力学性能
检测项目 |
测试结果 |
硬度/邵A |
90 |
拉伸强度/MPa |
24.5 |
断裂伸长率/% |
480 |
撕裂强度/N/mm |
65 |
粘结强度/MPa(水泥基材) |
3.0 |
2.2 聚脲涂层耐水解性能
将聚脲样片浸泡于去离子水、10%H2SO4和0.1M/L NaCl溶液中,在50℃试验条件下经一定时间后,检测涂层重量和力学性能变化,根据涂层重量和力学性能变化对涂层耐水解性进行评价,结果见表2。
表2聚脲涂层耐水解性能
介质 |
时间 |
增重% |
烘干后失重% |
拉伸强度/MPa |
断裂伸长率/% |
撕裂强度/N/mm |
空白样 |
—— |
—— |
—— |
24.5 |
480 |
65 |
去离子水 |
30d |
5.3 |
0.34 |
22.3 |
500 |
64.5 |
60d |
4.96 |
0.12 |
21.8 |
492 |
62.4 |
|
100d |
4.7 |
0.13 |
21.6 |
495 |
62.5 |
|
10%H2SO4 |
30d |
2.7 |
0.02 |
23.6 |
487 |
63.4 |
60d |
3.86 |
0.25 |
22.5 |
497 |
62.8 |
|
100d |
4.2 |
0.36 |
22.1 |
493 |
62.2 |
|
0.1M/L NaCl |
30d |
2.75 |
0.32 |
22.5 |
498 |
64.2 |
60d |
2.61 |
0.30 |
21.7 |
487 |
63.1 |
|
100d |
2.5 |
0.26 |
21.5 |
492 |
62.5 |
从表2可以看出,聚脲涂层在不同介质的浸泡试验中,随浸泡时间的增加,样片重量均有一定程度的增长。在去离子水和0.1M/L NaCl溶液中涂层增重趋势是先增后降,在10%H2SO4溶液中呈现逐步增长的趋势,随着浸泡时间的延长,涂层增重逐渐平缓。在力学性能方面,聚脲样片的拉伸强度和撕裂强度有一定程度降低,后期变化很小。涂层经不同介质浸泡后,断裂伸长率均随着浸泡时间的延长,出现增加趋势。原因是由于水分子进入样片中起到增塑作用。实验结果表明,聚脲涂层在长期水溶液浸泡中,其力学性能会保持先降低后稳定的状态,降低幅度很小,涂层吸水率保持相对稳定,证明聚脲涂层的耐水解性良好。
2.3 聚脲涂层耐酸碱性
分别将聚脲样片浸泡于30%磷酸、30%硝酸、30%硫酸、10%硫酸、10%氢氧化钠溶液中,定期测试样片的拉伸强度和撕裂强度,测试结果见图1和图2。
聚脲涂层耐酸碱性可以理解为聚脲材料对水和酸碱溶液的稳定性,它既包括聚脲材料的膨胀过程,同时也包括其与酸碱溶液发生化学反应,导致涂层老化的过程。从图1和图2可以看出,聚脲涂层经过不同浓度酸、碱溶液浸泡后,涂层力学性能均有一定程度的下降,涂层拉伸强度的降低幅度明显高于撕裂强度。弱酸弱碱对聚脲涂层性能影响较低,撕裂强度降低不明显,聚脲涂层在弱酸弱碱溶液中可以保持良好的力学性能。聚脲涂层经10%NaOH溶液浸泡的力学性能,高于涂层经10%H2SO4溶液浸泡后的力学性能,可以证明,聚脲材料耐碱性好于耐酸性。而具有强氧化性的30%硝酸对涂层破坏较为明显,浸泡20天后,涂层力学性能降低明显。
2.4 聚脲涂层耐热性能
将聚脲样片在不同温度条件下进行烘烤,测试涂层力学性能,考察聚脲涂层耐热性能,结果见表3。
表3聚脲涂层不同烘烤温度条件下力学性能
性能 |
23℃×7d |
50℃×7d |
80℃×7d |
120℃×7d |
180℃×2d |
拉伸强度,MP |
25 |
23 |
21.3 |
24 |
— |
断裂伸长率,% |
480 |
476 |
481 |
525 |
— |
撕裂强度,N/mm |
64 |
68 |
76 |
75 |
— |
涂层外观 |
浅灰色 |
无明显变化 |
无明显变化 |
轻微变黄 |
严重变黄、涂层表面析出液体(出现分解现象) |
表3结果显示,聚脲涂层在低于120℃条件下进行烘烤,力学性能保持稳定。随着温度的升高,断裂伸长率和撕裂强度呈现小幅度增长。在180℃烘烤条件下,聚脲涂层有明显收缩、变脆,并出现分解现象,说明内部结构被破坏,力学性能基本丧失。分析原因,聚脲涂层的力学性能是由结构中软链段和硬链度的微相分离决定,软链段由聚醚结构组成,聚醚结构耐热性相对较差(<150℃)。当烘烤温度高于分解温度,醚键会发生断裂,从而导致涂层出现分解[2]。因此可以得出结论,聚脲涂层使用温度在120℃以下,可以保持较稳定的力学性能。
2.5 聚脲涂层耐老化性能
将聚脲涂层样片放在户外曝晒一定时间后,定期对样片性能进行测试,结果见表4。
表4聚脲涂层耐老化性能
性能 |
曝晒前 |
60d |
180d |
270d |
拉伸强度,MPa |
23.5 |
23.2 |
22.9 |
23.1 |
断裂伸长率,% |
520 |
524 |
532 |
540 |
撕裂强度,N/mm |
64.0 |
64.2 |
63.7 |
63.0 |
△E |
— |
3.0 |
6.4 |
7.8 |
光泽,60。 |
75 |
42 |
24 |
18 |
粉化 |
— |
无粉化 |
无粉化 |
无粉化 |
从表4可以看出,经过户外曝晒后,聚脲样片光泽和色差变化明显,表明聚脲样片表层的分子键结构发生了变化,导致聚脲表层性能破坏,出现老化现象[3]。其原因是由于喷涂聚脲弹性体材料所选用的异氰酸酯和胺类扩链剂带有苯环结构,属于芳香族聚脲。芳香族聚脲涂层在紫外线的照射下,易氧化生成醌亚胺结构而出现黄变和失光现象。但随着曝晒时间的延长,聚脲涂层的力学性能保持稳定,并且断裂伸长率呈现小幅度的升高,因此可以判断聚脲涂层的内部结构没有明显的变化。因此,在一些对保色性要求高的场合,芳香族聚脲表面应采用耐候性面漆进行罩面。
3. 结论
⑴聚脲涂层在去离子水、10%H2SO4和0.1M/L NaCl溶液浸泡100天(50℃)后,涂层增重分别为4.7%、4.2%和2.5%,涂层力学性保持基本稳定,表明聚脲材料具有较好的耐水解性。
⑵在不同浓度酸碱溶液浸泡后,聚脲涂层力学性能均有一定下降。弱酸弱碱溶液对聚脲涂层性能影响较小,30%硝酸对涂层力学性能影响较大,说明聚脲涂层不耐强氧化性酸和高浓度酸。
⑶聚脲涂层在低于120℃温度条件下进行烘烤,可以保持稳定的力学性能。当烘烤温度达到180℃时,聚脲材料表面出现分解现象,证明聚脲材料不适合应用于高温环境条件下。
⑷聚脲涂层在户外使用,涂层有失光和变色现象,但涂层力学性能保持稳定,证明聚脲材料内部结构没有发生变化。
更多关于材料方面、材料腐蚀控制、材料科普等方面的国内外最新动态,我们网站会不断更新。希望大家一直关注中国腐蚀与防护网http://www.ecorr.org
责任编辑:王元
投稿联系:编辑部
电话:010-62313558-806
中国腐蚀与防护网官方 QQ群:140808414
免责声明:本网站所转载的文字、图片与视频资料版权归原创作者所有,如果涉及侵权,请第一时间联系本网删除。
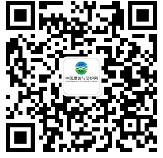
官方微信
《中国腐蚀与防护网电子期刊》征订启事
- 投稿联系:编辑部
- 电话:010-62316606-806
- 邮箱:fsfhzy666@163.com
- 中国腐蚀与防护网官方QQ群:140808414