导读
钢材是造船及海洋工程结构建造的主要原材料 , 占据了船体及海洋工程建造成本的 20%-30%。船舶及海洋石油工业的飞速发展对造船及海洋工程用钢提出了迫切需求。
1、背景
进入 21 世纪 , 我国船舶及海洋石油工业迎来了高速增长的新时期 ,2013年我国造船三大指标 ( 造船完工量、新接订单量、手持订单量 ) 分别占世界总量的 41.4%、47.9%、45.0%, 位居世界第一 , 我国已成为世界造船中心。海洋石油工业领域 , 十一五期间我国海上油气开发投入了 1200 亿元 ,2010 年海洋油气产量实现了 500 万 t 油当量。仅根据中海油规划 , 十二五期间将新建5000 万 t 油当量产能。预计“十二五”、“十三五”海洋石油工业投入将分别达到 6700 亿元和 9500 亿元。目前我国船厂能建造国际航运界所需船型的 95%左右 , 包括 17.5 万 t 散货船、30 万 t 超大型油轮 (VLCC)、30 万 t 浮式生产储油船 (FPSO)、14.7 万 m 3 LNG 船等 , 目前已有 9 座 30 万吨级造船坞 , 并在规划 50 万吨级和 100 万吨级船坞。
船舶及海洋石油工业的飞速发展对造船及海洋工程用钢提出了迫切需求。为适应船体高效化的建造需求 , 对船板钢提出了 100-500KJ/cm 的大线能量焊接要求 , 从而实现了船板钢的一次焊接成型 ; 为提高船体运行安全性 , 延长钢材使用寿命 , 对压载舱、货油舱船板钢提出了耐腐蚀的要求 , 提高运行寿命的同时降低了维护成本 ; 大型船体建造提出了 43 号大规格的 D40 球扁钢的需求 ,突破了传统型钢生产开发的极限 ; 自升式海洋平台桩腿构件需要 127-210mm厚高强度特厚板 , 突破了中厚板生产厚度规格极限 ; 油气储运设备提出了超低温用钢铁材料 , 最低使用温度达到 -196℃ , 服役环境极为苛刻。在此基础上 , 根据液化天然气 (LNG)、液化石油气 (LPG)、液化乙烯气 (LEG) 等低温油气的不同使用温度要求 , 研制开发了 9Ni、5Ni 或 3.5Ni 等 Ni 系低温钢。总之 , 高强度、高韧性、易焊接性、良好的耐腐蚀性以及大厚度、大规格化是船舶及海洋工程用钢的发展方向。
但是 , 我国和世界上先进的船舶制造及海洋工程装备设计制造技术相比 ,还存在很大差距。我国船企建造的船舶中 ,60%-70% 主要以低技术含量的散货船为主 , 高技术含量的钻井船及液化天然气船等承接量少。在海洋工程装备领域 , 我国尚处在欧美、新加坡 / 韩国之后的第三阵营 , 在产品设计、高端装备技术与建造方面与国外差距较大。如国外深水钻探最大水深已达 3095m, 我国为 1480m。国外已开发油气田最大水深为 2743m, 我国为 300m, 其中自主开发的装备采油能力不大于 200m 水深 ,与国外有近 10 年的距离。我国南海水深在 500-2000m, 我国目前还不具备在这种海域进行油气勘探和生产的装备技术。为此 , 必须要开发一系列高新技术和产品作为支持 , 而系列高品质船舶及海洋工程用钢的开发是其重要组成部分 , 它将为推进我国船舶工业及海洋石油工业的发展 , 保障我国能源、运输等行业的安全奠定良好的基础。
2、造船及海洋工程用钢的研究进展
钢材是造船及海洋工程结构建造的主要原材料 , 占据了船体及海洋工程建造成本的 20%-30%。涉及的钢材品种主要包括钢板、型钢 ( 船用球扁钢、H 型钢、角钢等 )、铸锻钢以及配套焊接材料等。其中船体建造耗用钢材量约占全船重量的 60% 左右 , 其中板材占88% 左右。
高强度、高韧性是造船和海洋工程用钢的基本要求。早期大型船体结构多采用 235MPa 级以下的钢板 , 随着船体结构的安全性要求的不断提高 , 船用钢板的强度在逐步提高 , 由 235MPa 逐步升级到 315MPa 以及 355MPa, 钢的质量等级也从 A 级提高到 E 级甚至 F 级。
到 20 世纪 90 年代 , 随着船舶的大型化、轻量化和高速化的要求 , 日本和欧洲率先开发出屈服强度为 390MPa 级的TMCP 型高强船板 (YP40K), 主要用在船体受应力比较大的舷侧、舷缘顶板和强力甲板上。目前 , 在大型散装货船和集装箱船中 ,390MPa 级的高强度钢已占主导地位 , 而 TMCP 工艺生产的船体钢的强度级别已经达到 550MPa 级以上 , 在海洋平台等大型海洋结构中获得广泛应用。而海洋工程中自升式钻井平台的桩腿结构 , 如齿条板、半圆板和无缝支撑管等部位 , 均要求屈服强度 690MPa 以上的高强度低合金钢 , 同时对低温冲击韧性的要求也极为苛刻 , 即使在普通工况条件也要求考核 -40℃ (E 级 ) 的低温冲击性能 , 在寒冷或极寒条件下考核 -60℃ (F 级 ) 甚至 -80℃的低温冲击性能。而一些低温油气储运用钢对低温冲击性能的要求更为苛刻 , 如储存 LNG的 9Ni 钢要求考核 -196℃的低温冲击功达到 100J 以上 , 储运 LEG 的 5Ni 钢也要求考核 -120℃冲击功。
焊接性也是船体结构钢关注的重点问题之一。20 世纪 30 年代以前 , 船体结构大都采用铆接或螺栓连接。二战前后 , 焊接技术开始普遍应用在船体结构上 , 对船体钢的焊接性和焊接工艺也提出了越来越高的要求。焊接时 , 钢板的焊接热影响区 HAZ 必须经受高温热循环 , 这很容易引起钢板 HAZ 的组织粗化 , 显着降低 HAZ 的韧性。特别是近几年来 , 为降低建造成本、提高造船的生产率 , 造船厂强烈要求采用大线能量焊接。国外广泛采用 100-500KJ/cm 大线能量焊接。为此 , 各国开发了一系列大线能量焊接船体钢 , 如日本于 20 世纪80 年代初期研制的 YP335 钢、90 年代中期研制的 YP390 钢和目前正在研制的YP460 钢等。目前 , 在海洋工程用钢领域如平台用 E36 等 , 均要求采用大线能量焊接以提高施工建造效率。
近年来 , 船舶及海洋工程结构的耐腐蚀性越来越受到人们的关注 , 国际海事组织 (IMO) 先后通过了压载舱涂层防护标准 (PSPC) 以及货油舱用耐腐蚀钢性能标准 (MSC87), 这使得相关的研究工作变得更加紧迫。在压载舱环境下 ,船板钢经受高温、高湿以及 Cl - 的共同侵蚀 , 尤其在压载舱的潮差部位船板钢发生严重的局部腐蚀。JFE 钢铁公司开发出了可抑制船舶压载舱涂膜劣化的新型高耐腐蚀性压载舱用钢“JFE 一 SIP-BT”。由于找到可抑制涂装后涂膜劣化的元素 , 提高了基于腐蚀生成物的钢材保护性能 , 可将涂膜膨胀及剥离等涂膜的劣化速度减慢到原钢材的一半左右。
新日铁等通过提高钢材的纯净度、添加Ni、Cu、W、Mo 等耐蚀合金元素的方法研制开发的 D36 货油舱用耐腐蚀钢 , 将船体结构的使用寿命从 15 年提高到 25年 , 该钢腐蚀速率约为传统钢的 1/4。
厚度规格也是船体钢技术水平的重要标志之一。虽然一般船体结构中对船体钢厚板规格最多要求到 40mm, 但我国新船体钢标准 GB712-2010 已将规格上限扩大到 100mm, 厚规格船体钢主要用于海洋平台等大型海洋结构中。在自升式钻井平台的桩腿用齿条板 , 其厚度普遍大于 100mm, 目前的主力型号JU2000齿条板一般采用178mm厚钢板。
厚规格船板和平台用钢重要的性能指标之一是抗层状撕裂性能。由于轧制变形量较小以及铸坯偏析的影响 , 厚板厚度方向性能一般显着低于纵、横向性能。
GB5313-2010 对有厚度方向性能要求的钢板进行了规定 , 其中最高级别的 235钢要求断面收缩率≥ 35%。大型船体结构不仅对钢板提出了厚规格要求 , 也对船用型钢提出了厚规格要求。30 万吨级大型船舶舭龙骨部位要求使用 43 号大规格 D40 球扁钢 , 腹板厚度最大达 20mm,是目前研制型钢中强韧性要求最高、截面尺寸最大的型材。型材一般采用孔型轧制生产 , 由于道次变形量低、终轧温度高、轧后无法实现快冷等特点 , 因此大规格高强型钢较钢板技术难度更大。
船舶用钢板应具有良好的止裂特性。近年来 , 散装货船的破损事故和巨型油轮 (VLCC) 的触礁事故不断增多 ,除从设计上进行改进外 , 在造船用钢方面 , 则要求船的碰撞和触礁产生较大塑性变形 (10%) 时 , 造船用钢板必须具有良好的抗脆性裂纹传播的止裂特性。
采用 TMCP 工艺可生产出表层具有超细晶粒组织的钢板 , 厚度方向性能均匀 ,具有良好的阻止脆性裂纹扩展的能力。
这种船板板已成功地用于液化石油气(LPG) 船和散装货船剪切应力最大的部位。随造船工业的发展,船舶对止裂钢板的需求将越来越多。
3、高品质造船及海洋工程用钢开发
3.1 大线能量焊接船板钢及平台用钢
对船板用钢 , 要求采用 200KJ/cm以上大线能量焊接 , 从而实现 18-36mm厚钢板一次焊接成形。采用“氧化物冶金”的技术思路开展了大线能量焊接用钢的研究开发工作。研究开展了Ti处理、Zr 处理、复合 Ti-Mg 处理、复合 Ti-Zr处理对船体钢大线能量焊接性的影响。对试验钢进行 20-200KJ/cm 的焊接热模拟试验 , 焊接热模拟最高加热峰值温度 1350℃。结果表明 ,Ti-Mg、Ti-Zr 复合处理后 , 钢中获得了大量细小的复合含 Ti 氧化物粒子 , 其直径约 1-2μm。比较各种脱氧处理条件下焊接热影响区的低温韧性可以看出,普通未进行任何处理的 C-Mn 钢焊后热影响区的整体低温韧性水平较低 , 其中线能量大于 50KJ/cm 时 , 低温韧性显着降低 , 仅为 10J 左右。经不同合金脱氧处理后 ,模拟焊接粗晶区的低温韧性显着提高。其中经 Ti-Mg 处理 ( 低 Mg) 后 , 粗晶区的低温韧性水平最高 , 各种线能量下的低温冲击功值均在 300J 以上 , 且随线能量的变化不敏感。对比焊接热影响区的组织可看出 ,Al 处理钢中主要得到大量平行排列的侧板条铁素体组织 ,Ti-Mg 复合处理钢中主要得到大量交错排列的晶内铁素体组织。采用 Ti-Mg 复合脱氧处理的方法 , 在工业大生产条件下研制开发了 100-240KJ/cm 大线能量焊接用钢 , 钢板最大厚度为 80mm。
对于海洋平台用 E36 钢 , 由于采用正火态交货 , 无法有效利用 TMCP 及微合金化等技术 , 目前普遍采用 50KJ/cm以下焊接线能量。平台用钢具有以下特点 : 碳含量及碳当量高、厚度规格大(30-100mm)、正火态交货。因此 , 必须在现有平台钢设计基础上通过降低碳含量及碳当量 , 大幅度提高焊接性 , 并采用其他方式弥补强度损失。
通过采用 V-N-Ti 合金设计 , 利用V(CN) 的析出强化弥补钢的强度损失 ,并能大幅度降低钢碳含量和碳氮量。
复合析出的 V-N-Ti 粒子还能起到细化原始奥氏体晶粒 , 并最终提高大线能量焊接热影响区低温韧性的作用。目前 ,工业试制 50mm 以上平台钢可以实现100KJ/cm 以上的大线能量焊接。
3.2 油船货油舱用耐腐蚀钢深入分析
了船板钢在货油舱上甲板、内底板环境下的腐蚀行为 , 研究了提高船板钢耐蚀性的不同技术思路。通过不同的耐蚀合金设计 , 研究了多种合金元素对船板钢在货油舱腐蚀环境下的耐蚀性。三种不同合金元素对腐蚀速率的影响规律。从研究结果可以看出 , 在内底板腐蚀环境下 , 微量合金元素对船板钢的耐蚀性存在显着影响。添加 0.1%以上的 B 和 C 耐蚀合金元素可以使腐蚀速率显着降低到原来的 1/4-1/30 观察腐蚀后的形貌可以看出 , 在 IMO 货油舱内底板腐蚀环境下 , 传统钢表面主要形成大量直径大而深的腐蚀点蚀坑 , 而开发的耐蚀钢表面则出现少量小而浅的点蚀坑,点蚀坑的深度/直径比显着降低。
根据上述结果研制开发的工业钢(NSD32、NSD36) 内底板腐蚀速率均低于 1mm/a 的标准腐蚀速率要求 , 其中 NSD36 钢腐蚀速率最低可以达到 0.38mm/a 的超低水平 , 约为传统钢的 1/13。同时 , 在上甲板腐蚀环境下 , 按照IMO 标准分别进行 21 天、49 天、77 天、98 天的腐蚀试验 , 其试验结果如下 ,从拟合 25 年后的结果来看 , 对比钢腐蚀量达到 9.34mm, 而开发的耐蚀钢仅为 1.512mm, 完全满足 IMO 标准不高于2.0mm 的标准要求。从腐蚀机理来看 ,在干湿交替的腐蚀气体环境下 , 对比钢表面锈层疏松、易剥离 , 锈层多为富硫的腐蚀产物 , 而在耐蚀钢的锈层结构中 , 形成了致密的内锈层 , 其与基体结合强度高 , 有效阻止了腐蚀介质与基体的接触 , 从而在长周期干湿交替腐蚀条件下表现出良好的耐蚀性。
3.3 大规格船用球扁钢
综合利用新型钒氮微合金化设计 +碳氮化钒控制析出轧制工艺 (PCRP), 集成创新开发出高韧性、大规格船用球扁钢品种技术。依靠奥氏体中析出的碳氮化钒促进晶内铁素体形核 , 显着细化了最终的铁素体晶粒尺寸 , 获得显着的细晶强化效果。同时 , 依靠铁素体中弥散析出的碳氮化钒的析出强化作用 , 显着提高钢的强度。利用上述技术思路 , 可在传统孔型轧制条件下研究开发出屈服强 度 355MPa、390MPa、440MPa 级 系 列高韧性船用球扁钢品种。其中研制开发的 D40 极限规格 43 号 ( 边长 430mm、腹板厚 20mm) 热轧船用球扁钢屈服强度高于 410MPa,-40℃冲击功达到 200J。高韧性、高强度、大规格船用球扁钢的开发解决了高韧性舰船用球扁钢品种技术难题 , 满足了我国船体建造的需要。
3.4 高止裂韧性船用钢板
大型集装箱船等在海上航行时 ,受波浪影响会产生弯曲 , 在船体舱口强度甲板上产生较大的应力集中。为了便于装卸货物 , 集装箱船通常采用大的舱口开口设计 , 这就需要集装箱船具有大型商船中最高的纵向强度。从保证船舶安全性 , 防止脆性断裂的产生 , 要求在舱口围板、上甲板等部位使用 51-100mm 的具有高止裂韧性的厚钢。
使 用 新 型 的 TRRP 轧 制 工 艺(Temperature?Reverting?Rolling?Process),可以在厚钢板表层获得超细晶组织 , 与传统 TMCP 工艺相比 , 其特点是在两阶段轧制间将钢板加速冷却到 Ac1 以下 ,出水后钢板内部的热量加热表层 , 表层处在两相区时进行控制轧制 , 在表层得到超细晶组织。厚钢板产生断裂时 , 通常表层不发生脆性断裂 , 而是产生与应力方向垂直面成 45°角的塑性变形 , 能够吸收裂纹传播的能量 , 从而达到阻止裂纹传播的效果 , 有效提高止裂性能 ,表层超细晶钢板就是应用这个原理 , 通过增加剪切唇的形成来提高止裂性。
数值模拟 TRRP 和 TMCP 工艺下钢板内部温度场 , 钢板表面、1/4 处和心部的温度随时间变化如图 4 所示。可以看到 , 空冷时表面到心部的温度差基本不变 , 而水冷回温时 , 表面温度先是迅速降低 , 出水后又被迅速加热到两相区 ,此时精轧变形 , 表层形成超细晶组织。
采用上述工艺开发的高止裂韧性钢板NDT 温度低于 -70℃ ,Kca 止裂韧性满足止裂设计标准要求。
3.5海洋平台特厚齿条钢
随着海洋石油工业的深入开展和钻采难度的加大 , 自升式钻井平台用齿条钢提出了大厚度、高强度、高韧性的发展需求 , 这类产品一般使用调质热处理状态交货。但是 , 随着齿条钢厚度的增加 , 截面厚度方向上组织、性能差异增大 , 提高特厚齿条钢的淬透性成为这类产品开发的难点。研究了不同合金元素复合处理对齿条钢淬透性的影响 , 结果表明 , 采用微 B+ 固 N 元素的复合处理可以在获得良好强韧性的条件下大幅度提高齿条钢的淬透性。同时 , 采用微 Ti处理或稍过量的 Al 处理 , 均可使微量B 的固溶比例达到 50% 以上 , 且偏聚于奥氏体晶界处 , 有效的延缓了高温相变 , 显着提高齿条钢的淬透性。
采取上述合金优化思路 , 工业生产获得了截面均匀的淬透组织和良好力学性能的特厚齿条钢。对于 152mm 厚的齿条钢 , 即使在钢板的心部 , 淬火冷却速率仅为 0.8℃ /s 左右 , 通过上述合金设计和工艺配合 , 也可获得以马氏体 +下贝氏体为主的显微组织 , 开发齿条钢和国内外先进技术相比 , 具有较高的强韧性水平。
3.6 9Ni低温钢
随着 LNG 工业的迅猛发展 ,9Ni 低温钢的研究和开发热度持续升温。LNG储存温度为 -163℃ , 要求 LNG 储罐内壁用 9Ni 钢具有较高的强度、良好的低温韧性和较小的波动。研究发现 , 采用QLT 热处理 ( 在 QT 调质处理中增加一道两相区淬火 ), 可在强度略微降低的情况下 , 显着提高 9Ni 钢的低温韧性 ,同时大大扩展9Ni钢的热处理工艺窗口,提高 9Ni 钢的性能稳定性。
进一步研究显示 ,9Ni 钢的良好低温韧性与其中形成的一定含量的逆转变奥氏体有密切关系。在 9Ni 钢中形成 5%-15% 左右的、热稳定性高的逆转变奥氏体 , 可韧化马氏体基体 , 在受载变形过程中吸收能量,提高相变诱导塑性能力。
在一定范围内 ,9Ni 钢的逆转变奥氏体含量越高 , 低温韧性越好。9Ni 钢逆转变奥氏体的形成和稳定性 , 与 C、Ni、Mn 等奥氏体稳定元素的显着富集具有密切的关系。理论计算和试验结果显示,采用适当的工艺处理,9Ni钢逆转变奥氏体中的 C、Ni、Mn 元素的最高含量可分别达到 0.5%、25% 和 2%左右 , 使热处理过程形成的奥氏体可稳定保持到室温 , 即冷却至液氮温度也不发生转变。逆转变奥氏体的控制技术 ,也是改善和提高 9Ni 钢低温断裂韧性尤其是止裂韧性的关键工艺技术之一。
4、结语
高技术船舶及海洋工程的国产化是建立在高端材料和技术大量依赖进口的基础之上。要实现我国成为世界造船强国的战略目标 , 还有大量关键技术需要突破 , 其中的核心问题之一就是高品质造船及海洋工程用钢的研发和推广应用。
船舶及海洋石油工业的飞速发展给造船及海洋工程用钢提出了高强度、高韧性、大线能最焊接及耐腐蚀性的要求,同时还需要具备大厚度及大尺寸规格的要求。采用 V-N-Ti 复合处理技术 , 开发了 100KJ/cm 以上可大线能量焊接平台钢。采用 Mg-Ti 复合处理技术 , 开发出适合 100-200KJ/cm 的大线能量焊接船体钢 , 其中在 200KJ/cm 的大线能量焊接时 , 焊接热影响区粗晶区 -20℃冲击功高达 350J。通过超纯净度及添加耐蚀合金的方法开发出 NS-D32 及 NS-D36 船板钢 , 下底板腐蚀速率仅为传统钢的 1/130 采用钒氮微合金化 + 碳氮化钒控制析出轧制工艺开发出 43 号极限大规格 D40 球扁钢。采用 TRRP 工艺获得表层细晶粒组织 , 显着提高厚钢板止裂韧性 , 满足集装箱船舱口围等部位止裂设计要求。齿条钢由过去的 100mm、127mm 发展为主力船型用的 178mm, 并逐步增加 210mm 齿条钢的使用 , 个别工况的最大厚度达到 259mm。服役工况也更为苛刻 , 要求的强韧性匹配更高。油气储运设备的大型化趋势也使用户对 Ni 系低温钢安全裕量的考核更加重视。20 万 m 3 和 25 万 m 3 巨型 LNG 储罐的设计和建造促进了超级 9Ni 钢的研究和开发 , 产品厚度达到 50mm 以上 ,在保持强度水平的情况下 ,-196℃冲击功由 150-220J 是高至 250J 以上 ,-163℃ CTOD 值达到 0.3mm 以上。
免责声明:本网站所转载的文字、图片与视频资料版权归原创作者所有,如果涉及侵权,请第一时间联系本网删除。
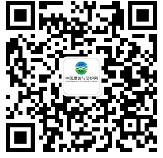
官方微信
《腐蚀与防护网电子期刊》征订启事
- 投稿联系:编辑部
- 电话:010-62316606-806
- 邮箱:fsfhzy666@163.com
- 腐蚀与防护网官方QQ群:140808414