船舶是温室气体排放的重要污染源,随着国际海事组织将温室气体排放纳入国际防止船舶造成污染公约,航运业面临节能减排的压力。开发和应用具有减阻功能的长效防污涂料替代现用防污涂料,对于降低船舶航行阻力,降低燃油消耗和减少“碳排放”具有重要作用。
文| 叶章基 中国船舶重工集团公司第七二五研究所 腐蚀与防护重点实验室
船舶是温室气体排放的重要污染源,随着国际海事组织将温室气体排放纳入国际防止船舶造成污染公约,航运业面临节能减排的压力。开发和应用具有减阻功能的长效防污涂料替代现用防污涂料,对于降低船舶航行阻力,降低燃油消耗和减少“碳排放”具有重要作用。
文| 叶章基 中国船舶重工集团公司第七二五研究所 腐蚀与防护重点实验室
海洋环境是地球上最大的生态系统,生长着大量的海洋生物, 其中有一些喜欢附着在船舶和海洋构筑物表面的海洋生物,称之为污损生物。海洋污损生物附着在船体表面,不仅导致重量增加, 而且增加了船体表面粗糙度,改变了船体表面平滑的流线型结构, 从而导致航速下降和燃油消耗大幅增加;海洋污损生物还容易附着在舵板、海底阀、通海管道、螺旋桨和声纳表面,严重影响船舶机动性能,导致仪器仪表失灵、干扰声纳等。此外,污损生物破坏船体表面的防腐蚀涂层而促进船体腐蚀。腐蚀降低船体结构强度,是造成海难事故原因之一。因此一旦发生污损,则需花费巨额费用用于清除污损生物,修复腐蚀破坏的设备,降低在航率, 缩短了船舶的服役寿命。目前防止海洋生物污损的方法有很多, 涂装防污涂料是船舶最为常用的方法。因此性能优异的防污涂料对于防止海洋生物污损,防止船体表面粗糙度增加,避免燃油消耗增加有十分重要的作用。
近年来,世界各国围绕“碳排放”进行一场经济博弈,各行各业不可避免地加入这场持久的降低“碳排放”的战争中。据了解,船舶也是温室气体排放的重要污染源之一,世界上船舶所排放的二氧化碳已经达到11.2 亿吨,约占全球主要温室气体排放量的4.5%.由于全球航运业的迅猛发展,到2020 年为止,由于燃油消耗增加所导致的大气排放量将飙升38% 至72% 左右。如果船舶不使用防污涂料,船舶的燃油消耗将会增加40%--从现有的年耗燃油3 亿吨增加至4.2 亿吨。据估计,防污涂料的使用为全球航运业每年节省燃油开支约300 亿美元,同时减少3.84 亿吨二氧化碳和360 万吨二氧化硫的排放。自2010 年以来,船舶二氧化碳等温室气体排放已逐步纳入国际防止船舶造成污染公约(MARPOL),在此背景下,研发具有减阻功能的防污涂料替代现用防污涂料,对于降低船舶航行阻力,降低燃油消耗和减少“碳排放”具有重要作用。
减阻防污涂料降阻原理与性能
船舶阻力是船舶最重要的总体性能指标之一,决定了船舶快速性能的优劣,主要包括兴波阻力、粘压阻力和摩擦阻力。兴波阻力和粘压阻力主要和船型有关,通过选用优良的船型,可最大限度地减少这两种阻力。摩擦阻力则主要和湿表面积、物体表面粗糙度、流体介质及介质的湍流分布特性有关。摩擦阻力在船舶等运输工具所受的总阻力中占有很大的比例,对于水面船舶,其表面摩擦阻力约占总阻力的50%.对于减阻技术的研究,早期的研究工作主要是减小表面粗糙度,即表面越光滑阻力越小。60 年代末,科学家发现某些天然树脂、直链高聚物、有机皂等材料可以减少湍流摩擦阻力,对减阻的研究开始向多方面发展,一些新的减阻技术也相继出现,如粘性减阻、仿生沟槽减阻、柔性壁减阻等,部分减阻技术已得到应用。但对于船舶而言,由于体型巨大,目前一些减阻技术如仿生沟槽减阻技术尚难以大面积应用;此外在减阻的同时, 还需保证有长期的防污能力,因此如何将防污技术与减阻技术在同一种涂层产品中应用是富有挑战性的工作。目前实用化防污涂料有两种类型,一类是在漆膜中添加具有防污作用的防污剂,通过防污剂渗出到海水中起到防止海生物附着的作用。另一类是形成特殊表面的漆膜,使漆膜表面不易于附着污损生物,或生物附着不牢, 在航行水流冲刷下污损生物易于脱落。两种类型中第一种是主流技术,在各类运营船舶中占据了90% 以上。第七二五研究所在第一类涂料研究基础上,应用粘性减阻理论,通过高分子改性技术, 在涂料树脂主链上引入疏水性基团,形成侧链疏水性基团排列,提高漆膜光滑性,同时减低漆膜水解后的粗糙度,另外通过接枝合适碳链长度和特定结构的有机酸调节树脂主链的柔韧性和水解性能, 避免侧基增多引发漆膜过脆,并通过树脂合成工艺的进一步优化, 提高树脂的均匀性。在研发的新型具有降阻性能的树脂基础上,添加氧化亚铜、高效防污剂等,通过配方筛选,研发了具有减阻功能的B40-SF 自抛光防污涂料。采用三维视频仪测定新型自抛光防污涂料水解前后表面粗糙度,测试结果表明新型自抛光防污涂料在海水中水解之后可显著降低涂层的表面粗糙度(如图1)。与现在广泛应用的磨蚀型839 防污涂料相比,采用平板模型测定,高流速下减阻性能可达5% 以上,显示出良好的减阻性能(如图2)。
除了具有良好的减阻性能之外,B40-SF 自抛光防污漆不含有机锡、DDT 等国际海事组织禁止使用的有害物质,同时具有良好的防污性能,其主要技术指标如表1 所示:
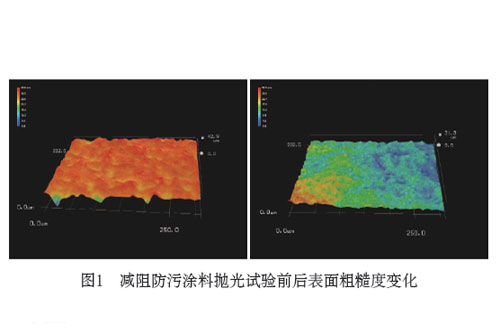
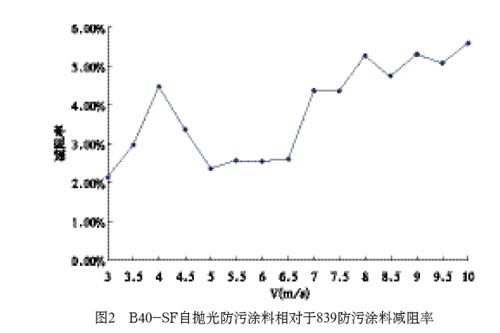
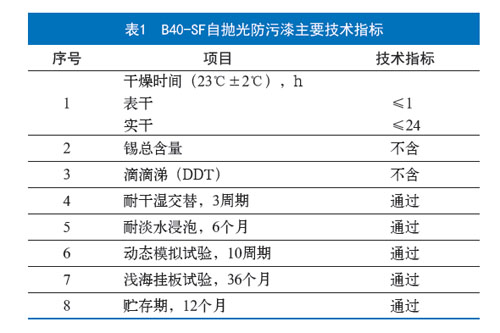
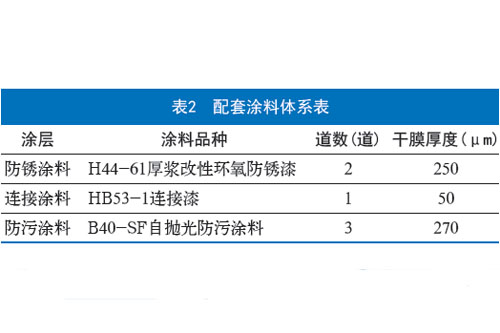
防污涂料体系设计
具有减阻功能的自抛光防污涂料应用于船体水线以下,典型的配套涂料体系一般由船底防锈涂料、连接涂料和防污涂料组成, 如表2 所示,该体系具有3 年防污期效。
B40-SF 自抛光防污涂料施工
B40-SF 自抛光防污涂料施工与普通防污涂料施工工艺相同, 涂料涂装前应保证前道涂层彻底干燥、涂层表面洁净,无油污、水迹、灰尘及其它污染物。如有油污可用洗涤剂清洗,泥浆和生物膜可用擦洗的方法除去。如有漆膜局部破损,需将底面处理, 依次补涂底漆、连接漆至规定厚度。
涂装前应将涂料搅拌均匀,目测无粗颗粒;若有目测可见的粗颗粒,应用80 目筛过滤后再用。涂装工作可在气温-5~40℃, 相对湿度90%以下进行,基材表面温度应高于露点3℃以上。防污涂料可采用刷涂、辊涂、有气喷涂和高压无气喷涂施工。施工中不建议添加稀释剂,必要时,加入量不得超过总涂料量的5%.
采用刷涂和滚涂时不宜较长距离来回刷滚油漆,否则容易起毛,单道的干膜厚度为60μm 左右。采用喷涂作业时应预先在边角处刷涂一道油漆,再进行喷涂,以确保涂膜厚度。高压无气喷涂约90μm.有气喷涂主要工艺参数为出口压力≥ 0.4MPa,喷嘴口径2.0-3.0mm;高压无气喷涂主要工艺参数为出口压力≥ 17MPa,喷嘴口径0.48-0.63mm.施工中应避免长期吸入溶剂或漆雾,皮肤、眼睛不得接触本品,施工中应保持空气流通,涂装现场严禁明火作业。施工完毕后用稀释剂清洗干净器具,切忌用水浸泡。
涂装后应每道测定干膜厚度及检查涂膜外观质量。涂层干燥后,采用涡流测厚仪测定涂层干膜厚度:要求80% 测试点平均干膜厚度不应小于设计干膜厚度,其余20% 测试点最小干膜厚度不应小于设计干膜厚度的80%,每平方米均匀随机检测点数不少于30 个。每道涂层涂装后应目测检查,厚度应均匀,干燥良好,无露底、无针孔、无皱纹、无漏涂、无起泡、无脱落、无分层、无裂缝、无流挂等现象。检查不足之处应予以补涂。
B40-SF 自抛光防污涂料实船应用
B40-SF 自抛光防污涂料在厦门海域进行了实船涂装性能研究。试验结果表明:采用辊涂进行涂装,整体涂装效果良好,漆膜平整,无漆膜弊病存在。经过1 年的实船应用,表明防污涂料防污性能良好。
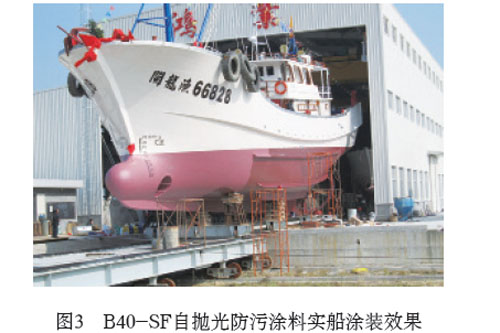
免责声明:本网站所转载的文字、图片与视频资料版权归原创作者所有,如果涉及侵权,请第一时间联系本网删除。
相关文章
无相关信息
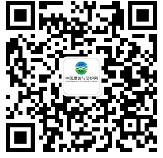
官方微信
《腐蚀与防护网电子期刊》征订启事
- 投稿联系:编辑部
- 电话:010-62316606-806
- 邮箱:fsfhzy666@163.com
- 腐蚀与防护网官方QQ群:140808414
点击排行
PPT新闻
“海洋金属”——钛合金在舰船的
点击数:8135
腐蚀与“海上丝绸之路”
点击数:6475