引言
电化学测试技术因具有操作简单、测量耗时短、对材料损害小、测量结果精确和获得腐蚀动力学信息全面等优点,成为腐蚀研究中十分重要的研究手段,但它也存在明显的局限性。电化学测试技术主要检测腐蚀过程中工作电极整体或局部区域的耦合电极电位、电极电流等电学信息,为腐蚀研究提供必要的实验数据,但电化学测试技术尚不能提供电极表面元素成分、结构的相关信息,而且电化学测试技术所提供的电学信息尚无元素选择性。对于多组元材料,电化学测试技术测得的电流是各元素反应的电子得失的总和,不仅包括目标元素反应,还包括其它平行反应,即便是纯金属的电化学腐蚀反应,测量的电信号也是金属阳极反应和 H 2 、O 2 等阴极反应耦合后的结果,很难直接准确提供单一元素、单个阳极或阴极电化学反应的热力学和动力学数据。为此,科技工作者往往借助 X 射线光电子能谱(XPS)、穆斯堡尔谱、椭圆偏振以及二次离子质谱(SIMS)、傅里叶红外光谱(FT-IR)等表面分析技术,移位获得腐蚀电极表面元素成分和结构信息,以弥补电化学测量技术的缺陷,与此同时,电化学测试技术的上述缺陷也催生了各种电化学测试技术与表面分析联用原位测量技术的研制和发展,如电化学测试技术与激光拉曼光谱联用技术使原位捕获电化学腐蚀过程中电极与腐蚀介质界面处不同组元的成分、结构变化成为可能,电化学测量技术与扫描探针测量技术联用使原位捕获电化学腐蚀过程中电极与腐蚀介质界面处的形貌变化成为可能,实现了腐蚀金属电极过程在分子级水平的微观原位研究,大大提高了金属腐蚀理论研究的深度和广度[1-12] 。
尽管如此,上述技术仍无法满足电化学腐蚀理论研究的需要。金属的电化学腐蚀过程涵盖了金属电极、腐蚀介质以及金属电极与腐蚀介质间的界面上电子和离子等物质的化学反应和传输历程,而电化学测试技术仅能追踪到金属电极本体以及金属电极与腐蚀介质界面处的电流、电位等电学信息变化,无法直接提供腐蚀介质本体的成分变化信息。腐蚀介质本体的成分变化信息对深入开展电化学腐蚀理论研究至关重要,若能够建立电化学测量技术与溶液介质成分测试技术联用,该技术将对电化学腐蚀理论研究做出与上述联用技术同等重要的贡献。
在众多的可用于溶液介质成分测量的化学分析技术中,电感耦合等离子体原子发射光谱 / 质谱技术(ICP-AES/MS)是最合适的腐蚀介质化学成分定量分析技术之一。与同类型的化学分析测试技术相比,ICP-AES/MS 技术具有操作简单、样品适用性强、检出限低、多元素同时测定等优点,目前已在金属腐蚀[13,14]溶解[15]以及钝化[16]等问题的研究中得到了很好的应用。若能将电化学测试技术与电感耦合等离子体原子发射光谱 / 质谱技术联用,实现在金属材料发生电化学反应过程中对腐蚀介质中金属电极各合金元素含量变化的实时监测,进而计算出各种合金元素的实时溶解速率,再结合腐蚀介质中各种合金元素的变化规律以及金属腐蚀电极的电化学参数的变化规律,可以更为深入地剖析金属电极的微观腐蚀机制。
1 ICP-AES/MS 测试原理及技术优势
1.ICP-AES测试原理及技术优势
原子发射光谱(AES)法是根据原子的特征发射光谱来研究物质的结构和测定物质的化学成分的一种光谱分析方法。发射光谱通常用直流电弧、低压交流电弧、高压火花源、和电感耦合等离子体(ICP)等光源激发而获得。ICP 是一种通过电磁感应产生的无极放电等离子体,与其它激发光源相比,其工作时所产生的高温(6000~8000K)能够使绝大多数元素在瞬间完成蒸发、原子化、电离和激发的过程,大大缩短了仪器的分析测试时间,此外 ICP 还具有稳定性好,电子密度高等优点,现已成为原子发射光谱(AES)的主要激发源。
ICP-AES 出现于 20 世纪 60 年代,并于 70 年代迅速发展。商品化的 ICP-AES 仪主要由 ICP 发生器和光谱仪两大部分组成。ICP 发生器包括高频电源,进样装置及等离子体矩管。光谱仪包括分光器,检测器及相关的电子数据系统。ICP-AES 进行测定时,液态样品由载气直接引入到雾化器中进行雾化,而固体样品则需要经酸化或萃取转变成溶液才可引入,经雾化后的液态试以气溶胶的形式进入到 ICP 的高温通道中,经去溶剂化、原子化、电离、激发后,最终回到基态并发射出所含元素的特征谱线,样品中的元素含量与其发射的特征谱线的强度值成正比,因此,可根据特征谱线的强度值对试样进行定性定量分析。
ICP-AES 具有的独特性能使其与电化学测试技术联合用于开展金属电化学腐蚀研究成为可能。首先,ICP-AES 仪采用液体进样,可以直接对腐蚀介质的元素成分进行定性和定量分析;其次,ICP-AES 分析速度快,可在 1 分钟内同时完成几十个元素的定量测定,可快速获得电化学控制下腐蚀介质中元素成分的实时数据。除此之外,ICP-AES 不仅能够测定元素周期表中除放射性元素、气体元素以及卤族元素外的绝大多数元素(73 种),而且还具有较高的灵敏度和较低的检出限,对于大多数元素而言,只要其浓度高于 1 ~ 10ppb 就可以有效检出,仪器的动态线性范围也非常宽,其工作曲线的直线范围可达 4 ~ 5 个数量级,可对主、次、痕量元素成分进行同时测定;更重要的是,ICP-AES 的耐盐度高,受腐蚀介质成分限制小,可分析含盐量高达 30% 的盐溶液,而且ICP-AES 受基体干扰小,这得益于等离子体在高温条件下能够破坏所有的分子键并将其转化为原子的特点。但需要指出的是,所有样品一旦进入等离子体中,其分子信息就会丢失,元素的氧化状态和分子形态还需借助其它方式获取。
2.ICP-MS测试原理及技术优势
ICP-MS 是 20 世纪 80 年代发展起来的一种痕量分析技术,它采用独特的接口将 ICP 的高温电离特性与质谱仪的灵敏快速扫描的优点结合在一起,与 ICP-AES 不同,ICP 在 ICP-MS 中是作为高温离子源将样品电离为单电荷离子。ICP-MS 可提供在 3 ~ 250amu 范围内每一个原子质量单位 (amu) 的信息,因此除了痕量元素测定[17]外,ICP-MS 还可用于同位素的测定[18] 。商品化的 ICP-MS 仪由样品引入系统、电感耦合等离子体离子源、离子透镜系统、四级杆质量分析器、检测器等构成。其工作原理是液态样品由载气引入雾化系统经雾化后,以气溶胶的形式进入等离子体中心通道中,在高温和惰性气氛中经过去溶剂化、汽化、解离,最终被电离成带单电荷的正离子,经离子采集系统进入质量分析器,质量分析器根据质荷比进行分离,根据元素质谱峰强度测定样品中相应元素的含量。除了具有与 ICP-AES 相当的优点外,ICP-MS 具有更低的检出限(ppt级)和灵敏度,适于痕量元素的分析。但 ICP-MS 的耐盐量较差 , 要求液体试样的固体含盐量低于 0.2%,因此当测定高盐体系杂质含量时,必须对待测样品进行高倍数的稀释处理,这意味着,将 EC 与 ICP-MS 联用时,还需在二者中间设置一个在线的样品稀释步骤,联用系统更为复杂[19] 。
2 EC-ICP-AES/MS 技 术 特 点及其发展历程
电化学 - 电感耦合等离子体原子发射光谱联用技术(EC-ICP-AES)是由K.Ogle [20] 于 2000 年提出的,借助电化学流动池(electrochemical flow cell)将电化学测试技术与电感耦合等离子体光谱法相连接,实现了金属电极表面电化学反应进行时电解质溶液中各类金属元素含量的实时检测。实验装置包括了流动电解池和电化学控制系统的电化学模块、电感耦合等离子体原子发射光谱测试装置模块和连接上述两大模块的电解液传输系统。测试时,蠕动泵首先以合适的速度将新鲜的电解质溶液不断地输送到电化学流动池中,建立相对稳定的电化学体系;而后利用电化学综合测试系统实现电化学流动电解池中工作电极的电化学参数控制,与此同时,在蠕动泵的推动下流动电解池中的电解质被推送至 ICP-AES 仪中进行目标元素的浓度检测。
若金属工作电极各合金元素在电化学流通池中主要发生如下的电化学反应:
M-----M n+ +ne
假设某一瞬态 t,流动池内工作电极组分 M 的溶解速率为 v M (t),则工作电极组分 M 在流速为 f 的电解液中的浓度 C M (t) 可表示为
(1)
其中,C M (t) 为工作电极组分 M 在流动电解质中的浓度(gmL -1 ),v M (t)为工作电极组分 M 的溶解速率(g s-1 ),f 为电解质的流速(mL s-1 )。将式(1)变形可得到
(2)
其中,电解液流速 f 是电化学流动池的实验参数,是已知量,如不考虑流体在流动池和管线中停留而变宽等因素,则工作电极组分 M 在流动电解质中的浓度 C M (t) 可由位于电化学流动池下游的ICP-AES直接测得,因此,通过式(2)可计算出组分 M 的溶解速率 v M (t)。
假设反应 M → M n+ +ne - 是唯一的反应,并且具有 100% 的法拉第效率,可根据法拉第定律将组分 M 的溶解速率 v M(t) 换算成其等效溶解电流 i M (t),即
(3)
其中,i M (t) 为元素 M 的等效溶解电流(A),n 为 M 的价态,F 为法拉第常数 96500(C mol -1 ),MA 为元素 M 的相对原子质量(g mol -1 )。此时,通过ICP-AES 测试结果计算得到的 M 组分的等效溶解电流应当等于由电化学测试模块测得的法拉第电流。然而,很多情况下却很难确定二者的关系,如元素的价态是未知的或者有其它不可溶的腐蚀产物产生等,因此,用等效溶解电流来表示材料各组分的溶解速率只是为了方便比较光谱数据和电化学数据,并不代表已经知道了该材料的溶解机制[20] 。
在整个 EC-ICP-AES 测试系统中,电化学流动池的设计是决定测试结果可靠性的关键因素之一。目前绝大部分电化学流动池的设计均采用三电极体系,包括工作电极、参比电极和辅助电极。工作时,在工作电极和参比电极之间施加的电压总会伴随着由欧姆降引起的误差,为了减小误差,参比电极都应尽量与工作电极保持接近;辅助电极应置于工作电极的下游,以防止辅助电极上的反应产物干扰工作电极的测定。同时,流动池池体材质的选择也十分重要,尤其是测定痕量元素时,耐蚀性差的池体会污染待测元素进而影响测试结果的准确性,因此池体材质应为不与电解液发生化学反应的惰性材料[21] 。此外,流动池的内部结构、物理容积、电解液体积/ 工作电极面积比例均会对测试结果产生影响[22,23] ,是流动池设计不可忽略的关键要素。作为电化学流动池和 ICP-AES 共同的仪器参数,电解液流速的选择是决定二者能否成功联用的另一重要因素。对于 ICP-AES 而言,增加流速能够增大待测元素在等离子体焰中的浓度,提高发射强度,同时对等离子体焰还有冷却作用,可降低发射背景,提高信噪比。但若流速过大,则会使雾化器的雾化效率变差,即形成大颗粒雾滴,使背景噪音增加,还会使样品消耗量增加。对于 EC-ICP-AES 联用系统而言,由公式(2)可知,当金属电极的溶解速率一定时,电解液的流速越快,其对应的由ICP-AES 测得的浓度值就越小,由此可见联用系统的灵敏度与电解液流速成反比,增加流速会导致联用系统的灵敏度降低;此外,增加电解液流速还会增加流体在电极表面的不均匀性,产生成分梯度,最终影响测试结果的准确性[23] 。除了对联用系统检测性能的影响之外,电解液流速也会在工作电极反应速率和反应机理的研究中起关键作用,特别是当某些电极反应受扩散控制的时候,电解液流速会直接影响工作电极的腐蚀行为。因此电解液流速的合理选择,对提高联用系统的灵敏度,改善联用系统的时间分辨率、提高流体在电极表面的均匀性以及保证测试结果的可靠性非常重要。
近些年,针对不同的测试需求,科技工作者相继设计了各具特色的的电化学流动池。K.Ogle [20] 研究组率先设计了一款三电极体系两腔室结构的流动池,其中的工作电极和辅助电极用多孔膜分隔,形成两个腔室,Ag/AgCl 参比电极置于辅助电极所在腔室。工作时,电解液在蠕动泵(2 ~ 12mL min -1 )的带动下通过进样口进入工作电极所在腔室(<0.2mL),与工作电极的表面(0.52cm 2 )接触并发生反应,随后由出口流出并进入ICP-AES进行元素检测。该流动池的优势是将工作电极与辅助电极分隔,避免了辅助电极上的反应产物对工作电极的测定产生干扰(如,辅助电极析氢反应产生的 OH - 会对工作电极周围的 PH 值产生影响)。K.Ogle 等利用该联用装置研究了在线性扫描伏安法实验中 304 不锈钢中在 2M H 2 SO 4 和 0.1M NaCl 混合介质中铁、铬、镍、锰、钼和铜溶解行为借以验证 EC-ICP-AES在腐蚀研究中的可行性。他们利用该联用装置不仅在腐蚀电位附近测得了铁、铬、镍和锰的塔菲尔斜率,还测得了假设 n=2 时铁、铬、镍、锰、钼的总溶解电流密度,同时利用电化学测试技术获得了不锈钢电极的总的阳极电流密度,并发现二者的值相接近,进而断定 304不锈钢中主要元素的溶解生成了正二价离子。
2019 年,Y.Yan 等[24]设计了一种可用于原位划伤实验的开放式电化学流动池。与 Ogle 的电化学流动池不同,该流动池上端设有开口(8mm×1mm),辅助电极置于工作电极所在腔室,Ag/AgCl 参比电极置于流动池上游的盐桥中。盐桥由纤维素透析膜分隔为上下两部分,Ag/AgCl 参比电极位于盐桥的上半部分,盐桥的下半部分设有通道,该通道与流动池进样口相连。工作时,电解液在蠕动泵的带动下以一定的流速(3mL min -1 )流经该通道,随后进入流动池中与工作电极发生反应。利用该联用系统不但可以原位的对曝露的材料施加机械划伤,还能够实时监测材料在划伤过程中元素的溶解速率变化。Y.Yan等应用该联用装置定量研究了开路电位 下 Mg-Li(-Al-Y-Zr) 合 金 在 0.01MNaCl 中经划伤活化再自愈钝化的动力学行为借以验证了该联用装置的可行性。他们利用该联用装置在不干扰 EC-ICP-AES 在线测定的情况下,对镁锂合金原位实施了机械划伤,同时利用 EC-ICP-AES 装置实时监测了镁锂合金中镁和锂的溶解速率变化,并发现新划伤表面镁和锂的溶解速率明显高于其余未划伤表面的镁和锂的溶解速率,同时在新划痕表面的溶解速率先增加随后在 200s 内消退,由此说明了镁锂合金经划伤溶解后很快又发生了钝化,支持了镁锂合金在水溶液中形成自愈保护膜的理论。
受检出限的限制,ICP-AES 主要用于常量、微量分析,但当元素浓度在ppb 级甚至更低时,ICP-AES 很难满足测试要求,此时,需借助 ICP-MS 进行痕量分析。2007 年,N.Homozava 等[21]设计了一种可用于微区腐蚀研究的流动池。其工作原理是将一个充满电解液(270μL)的毛细管垂直于研究试样的特定位置上,毛细管的下端开口(内径为 600μm)决定了暴露于电解液中的工作电极面积;同时将蠕动泵泵管的一端直接插入毛细管的上端开口中,借助蠕动泵来调节电解液在毛细管中的流量(50μL min -1~ 1000μL min -1 )。 与 同类型的流动池相比,该流动池最大的优势是具有较高的空间分辨率,结合 ICP-MS 的痕量分析能力,能够对电极表面微区进行定位元素分析。但由于 ICP-MS的耐盐度较差,在电解液进入 ICP-MS前,需高倍率稀释,因此该流动池无法直接与 ICP-MS 相连。随后,N.Homozava等[25]对上述流动池进行了改进,增加了流动注射进样以及 ICP-MS 在线稀释技术,弥补了原有装置的不足。2014 年,N.Ott 等[19]又引入了电化学测试技术,将 200μm 的 Ag/AgCl 丝(参比电极)以及 250μm 的铂丝(辅助电极)直接插入毛细管上端开口中,与位于毛细管下端的工作电极构成三电极体系,至此才实现了电化学测试技术与 ICP-MS 真正意义上的联用。
2011 年,S.O.Klemm 等[26]设计了一种 V 型通道电化学流动池。V 型通道的两个分支分别为电解液的进出口通道(通道内径为 400μm,通道总体积为21μL);辅助电极位于入口通道中,Ag/AgCl 参比电极经出口通道的侧面直接插入;V 型通道底部设有开口,用于连通工作电极,开口大小决定了工作电极暴露在电解液中的面积(2.56x10 -3 cm 2 )。工作时,将流动池涂有硅胶的开口直接按压在工作电极表面,构成封闭的电解池,硅胶主要起密封作用以防止电解液泄露。该流动池不但结构简单、易于制作,而且还具更换样品快速、方便的优点。为了验证该联用系统的可行性,S.O.Klemm 利用该联用装置分别测得了纯铜在 1mM 和 10mM HCl 中的溶解速率,并将用 ICP-AES 测得的溶解速率换算成假设 n=1 时的等效溶解电流密度,并与 EC测得的电化学电流密度比较,发现二者的差异与铜的真实价态有很好的相关性。
3 EC-ICP-AES/MS 在金属腐蚀研究中的应用
1.EC-ICP-AES技术在金属腐蚀研究中的应用
⑴金属电极的溶解速率的测定
EC-ICP-AES 在金属腐蚀研究中最直接的应用就是通过测定金属材料中各元素的含量变化,获得金属电极中个合金元素在腐蚀介质中的溶解速率。
M.Serdechnova 等[27]利 用 EC-ICP-AES 分别测得了阴极极化下 AA1199(99.99%Al)和 AA6061 中各元素的溶解速率与时间的关系曲线,研究了阴极铝溶解的化学计量以及其与镁、硅溶出的相互关系。发现高阴极极化电流下 Al的溶解速率与 OH - 的生成速率成线性关系,且 OH - /Al 3+ 的比例为 4.62± 0.22,该比例不受阴极极化电流以及 Si、Mg组分变化的影响,并就此提出了复杂合金中 Al 阴极极化下的溶解速率的简化模型。
Q.Van Overmeere 等[28]用 EC-ICP-AES 原位监测了不同电流密度(1.0mAcm -2 ~10 mA cm -2 )下 0.4mol L -1 磷酸中铝阳极氧化过程中 Al 3+ 的损失速率随时间的变化关系,并根据 Al 在流动池中的停留时间分布,计算出了与电位变化具有相同时间分辨率的 Al 的真实损失速率。研究发现在所研究的电流密度下,根据电位的变化情况可知磷酸中铝阳极氧化过程中 Al 3+ 的损失对应三个不同成膜阶段,分别为阻挡层生长期、多空层形成初期、多孔层形成稳定期;在阻挡层生长阶段 Al 3+ 的损失率最高,而在多孔层形成初期,Al 3+ 的损失速率开始下降,在多孔层稳定形成阶段,Al 3+的损失速率不再继续降低而是稳定在一个恒定值。此外,他们还根据不同成膜阶段 Al 3+ 的损失速率和阳极电流密度,估算出了不同成膜阶段的成膜效率,发现当电流密度从 2.0mA cm -2 增加到10mA cm -2 时,阻挡层生长期间的成膜效率由 0.47 降低到 0.37;在同一电流密度下,多孔层的成膜效率从 0.61 提高到 0.76,1.0mA cm -2 电流密度下的成膜效率表明,当电流密度低于 2.0mAcm -2 时,Al 3+ 的损失机制主要是电场辅助 溶 解(field-assisted dissolution),当电流密度高于 2.0mA cm -2 时,Al 3+的损失机制是阳离子直接喷射(directcation ejection)。
⑵选择性溶解
对于多组分材料而言,因各合金元素化学活性的差异,材料的溶解行为往往具有选择性。通过定性比较溶液中金属离子成分与原金属基体的成分的差异以及定量测量腐蚀介质中合金元素的含量变化规律,可以确定多组分材料选择性溶解行为的特征和溶解规律,进而为剖析多组分材料的腐蚀机制提供必要的实验证据。
K.Ogle 等[30]利用EC-ICP-AES 分别测得了三种金属间化合物中铝、镁、铜和铁随时间和电位变化的溶解速率曲线,并将各元素的溶解速率换算成其对应的等效溶解电流密度。通过比较 Cu/Al、Mg/Al、Fe/Al 的实际溶解比例与在原合金中的成分比例,推断出了各合金元素发生选择性溶解的动力学信息;通过比较总的等效溶解电流密度与电化学电流密度的关系,总的等效溶解电流密度小于电化学电流密度时,表明一部分腐蚀产物参与了成膜过程,间接得到了三种金属间化合物的成膜动力学信息。
⑶表面膜的形成和溶解
材料发生选择性溶解时,一部分金属会优先溶解,而留下惰性的金属或者不可溶的氧化物。在任何一种情况下,金属中的残余物质都将对金属的溶解行为产生影响。尽管联用技术仅是测量溶液中的成分,但可以根据质量守恒定律,通过原金属基体的成分以及溶液中的成分,间接的求得残余物质的量。
P.Zhou 等[31]利用 EC-ICP-AES 研究了纯铜在含氧自来水中的阳极溶解动力学过程,他们首先利用 EC-ICP-AES 测得了恒电流阳极极化下纯铜在含氧自来水中的溶解速率和对应的电化学阳极电流密度。为了便于与下游 ICP-AES 测得的溶解速率数据作比较,他们将阳极电流密度换算成了对应的电子转移速率,通过比较铜的溶解速率与电子转移速率的差异,发现铜的溶解速率明显低于电子转移速率,表明一部分铜溶解生成了不溶铜。为了测得不溶铜的量,P.Zhou等又将含氧自来水更换为除氧柠檬酸盐缓冲溶液,以溶解阳极极化过程中所生成的不溶铜,再利用 EC-ICP-AES 对溶解下来的铜进行测定;最后根据质量 /电荷的平衡关系,计算出可溶铜为 +2价、不溶铜为 +1 价,就此提出了 Cu 的三种可能溶解机制。
2.EC-ICP-MS在金属腐蚀研究中的应用
与 EC-ICP-AES 相 比,EC-ICP-MS的最大优势是检出限低,能够监测溶解速率较低的腐蚀过程,如测定开路电位下的溶解速率或测定有钝化膜覆盖时的溶解速率等,同时还可用于监测溶出量较少的腐蚀过程,如微区腐蚀。
N.Ott 等[19]利 用 EC-ICP-MS 分 别测得了在开路电位和不同恒电位极化下Al-Cr-Feγ 相在 H 2 SO 4 (PH=0) 中的溶解速率,定量研究了 Al-Cr-Feγ 相在酸性介质中的钝化行为。研究发现在开路电位下 Fe、Al、Cr 的溶解速率都很低,表明 Al 膜和 Cr 膜的生成和溶解在一个较低的速率下进行,Cr 的存在提高了表面膜的稳定性;与 Al、Cr 相比,Fe 的溶解速率相对较高,并且 Fe 的溶解速率随时间的变化是恒定的,表明 Fe 透过表面膜直接迁移到氢氧化物 - 溶液界面。研究还发现在 0.18V SCE 和 0.69V SCE电位下,Cr 的溶解速率仍很低,表明 Cr在 Al-Cr-Feγ 相表面发生了富集;在0.18V SCE 电位下,Al 的溶解速率变化不大,但当极化电位升高到 0.69V SCE 时,Al 的溶解速率显著增加,表明高的极化电位降低了表面膜的稳定性从而促进了Al 的溶解;Fe 的溶解速率随着极化电位的升高而降低,表明 Fe 在阳极极化下形成了更稳定的羟基氧化物,由此揭示了Al-Cr-Feγ 相 在 H 2 SO 4 (PH=0) 中 的 成膜和溶解机制。同时,N.Ott 等还利用EC-ICP-AES 实时监测了开路电位下经空气老化处理的 Al-Cr-Feγ 相在 H 2 SO 4(PH=0)中的溶解速率,研究了空气老化对 Al-Cr-Feγ 相钝化行为的影响。研究发现 Cr、Fe 的溶解速率受空气老化的影响不大,但 Al 的溶解速率却显著降低,表明空气老化提高了铝膜的稳定性。
S.O.Klemm 等[32]在电位循环实验中,利用 EC-ICP-MS 测定了不同电位扫描速率下多晶铑在 0.1m H 2 SO 2 中的溶解速率与时间的关系曲线,发现多晶铑的溶解速率曲线的时间分辨率与电位扫描速率有关,在较低的电位扫描速率下,铑的阳极溶解曲线能够较好的与阴极溶解曲线区分开,而在较高的电位扫描速率下,二者却融合在一起,由此提出通过降低电位扫描速率来提高铑的溶解曲线时间分辨率的方法;通过比较不同电位扫描速率下铑的阴阳极溶解速率曲线发现,铑的阴极溶解峰的峰高和面积均高于阳极溶解峰,表明由多晶铑表面氧化物的还原所造成的质量损失高于由氧化物的形成所造成的质量损失,此外铑的阳极溶解峰的出现表明铑的溶解是由表面氧化膜的形成引起的。同时,S.O.Klemm 等还将每一个电位循环下测得的阳极溶解速率曲线和阴极溶解速率曲线的面积进行归一化,从而获得了铑的阳极溶解量和阴极溶解量信息;通过研究扫描电位上限对多晶铑的阴阳极溶解速率以及溶解量的影响发现,多晶铑的阴极溶解量和阳极溶解量的比例和总溶解量均随电位上限的增加而显著增加;通过高扫描电位上限的阳极溶解曲线可知,在铑的阳极溶解峰出现后,铑的溶解速率又出现了增长,表明铑的表面膜的溶解经历峰值后又发生了稳定的阳极溶解,由此为多晶铑表面氧化物稳定溶解提供了清晰的证据。
4 EC-ICP-AES/MS 面临的问题与解决方案
EC-ICP-AES/MS 能够在金属材料发生电化学反应过程中实时监测腐蚀介质中金属电极各合金元素的变化,提供腐蚀介质中元素含量的相关信息,这些信息对于金属腐蚀的研究具有重要意义。然而,EC-ICP-AES/MS 分析方法目前尚处于发展阶段,还存在很多问题需要解决[20] 。
1.流体的均匀性控制
不合理的电化学流动池设计会导致流动池内部不同位置处溶质的扩散速度不同,从而形成浓度梯度,溶质不仅包括金属阳离子的浓度,还包括参与电化学反应的其他物质,比如 Cl - 、H + 、OH - 、O 2 ,酸碱度等。设计中可以通过优化工作电极的面积以及通过在流动池中的位置来减少和避免该类问题的发生。
2.测试信号的同步性控制
对于电化学测试而言,电信号的响应在时间的尺度上即时的,而位于电化学流动池下游的 ICP-AES/MS 的响应信号则会因流体在流动池以及管线中的停留而产生延迟。ICP-AES/MS 的响应信号的延迟时间实际就是产物离子随电解液由电化学流动池、经中间管线、最终流到 ICP-AES/MS 的雾化器中所需的时间,主要与电解液的流速以及流经管线的长度有关。该延迟时间可通过脉冲电流溶解实验获得,即对工作电极(如纯铜)施加一个短暂的(如 0.5s)的阳极脉冲电流,利用 EC-ICP-AES/MS 同时监测电信号和光谱信号随时间的变化,电信号脉冲与光谱信号中第一个数据点的时间差即为 ICP-AES/MS 信号的延迟时间。
3.时间分辨率的匹配性控制
将 EC 与 ICP-AES/MS 联 用, 电 化学测试电信号与 ICP-AES/MS 测试信号的一一对应尤为重要,比如在需要定量比较经下游 ICP-AES 测量获得的元素的溶解速率与经电化学方法获得的金属电极上的极化电流时,两类测试信号的是否具有相同的时间分辨率决定了研究工作的成败[28,29,33] 。工作电极表面元素溶解产生的短暂的瞬时浓度,在流向 ICP-AES/MS 的过程中,会因流体扩散而变宽,导致 ICP-AES 测得的浓度 C M (t)与工作电极表面元素的真实溶解速率v M (t) 之间的卷积积分关系:
(4)
其中,h (t) 为时间停留分布,相当于电化学与光谱测量之间的传递函数。K.Ogle 和 S.Weber 证 明 了 h(t) 可以用近似对数正态分布来拟合:
(5)
其中,β、ω 是对数正态分布的两个时间常数,可通过脉冲电流溶解实验求得。
经过卷积积分模型处理后,光谱数据与电化学数据具有相同的时间分辨率,两类数据可以进行逐点比较。
五、结论与展望
新技术的进步和数据分析手段的完善,促进了元素分析测试技术在金属腐蚀研究领域研究中的广泛应用。EC-ICP-AES/MS 联用技术结合了电化学检测技术的优势与 ICP-AES/MS 的检测限低、动态线性范围宽及多元素同时测定的优点,实时提供金属材料中各元素在电化学反应过程中的溶解信息,这将有助于金属材料的腐蚀行为和腐蚀机理研究的深入,迄今,EC-ICP-AES/MS 在金属腐蚀研究方面已取得了长足的进步,各种新的分析方法已逐步建立并在实际样品的研究中得以应用,随着对金属腐蚀研究的重视度的提高以及分析技术和数据处理方法的不断完善,EC-ICP-AES/MS 的应用前景将更加广阔。
人物简介
于英杰,中国科学院金属研究所分析测试中心工程师,在职博士生。2006 年考入吉林大学高分子材料与工程专业,后赴美国佛罗里达州立大学攻读分析化学专业硕士学位,2012年回国后入职中国科学院金属所,现主要从事化学分析和腐蚀电化学方面的研究工作。
李瑛,博士,中科院金属研究所研究员,博士生导师。1986 年考入吉林大学化学系,毕业后入原中国科学院金属腐蚀与防护研究所师从曹楚南院士攻读硕士和博士学位,曾赴日本原子力研究所、英国国家物理实验室及瑞典皇家工学院开展合作研究。从事腐蚀电化学基础理论研究工作近三十年,在纳米材料电化学腐蚀机制、固态盐膜下的金属在中温含氧水蒸气中的电化学腐蚀规律以及在深海压力交变环境中金属及有机涂层的失效机制、寿命预测及智能涂层的研制等方面开展了大量的研究工作,负责国家自然基金项目、973 项目等十余项,发表 SCI 论文百余篇,受邀参与撰写两部英文专著,曾获辽宁省科学技术一等奖。现任中国腐蚀与防护学会常务理事,腐蚀电化学与测试方法专业委员会主任委员,《中国腐蚀与防护学报》、《腐蚀科学与防护技术》杂志编委。
免责声明:本网站所转载的文字、图片与视频资料版权归原创作者所有,如果涉及侵权,请第一时间联系本网删除。
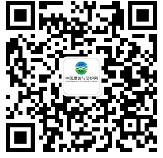
官方微信
《腐蚀与防护网电子期刊》征订启事
- 投稿联系:编辑部
- 电话:010-62316606-806
- 邮箱:fsfhzy666@163.com
- 腐蚀与防护网官方QQ群:140808414