存贮有长寿命极毒组核素的 16MnR 废物包装容器存放在封闭洞室环境中,部分容器填埋在膨润土和混凝土回填结构中。通过现场原位实验和实验室加速实验,利用重量法,XRD,SEM/EDS,电化学阻抗技术和线性极化技术等方法开展了包装容器腐蚀防护和评价研究。通过纳米改性设计了纳米重防腐有机涂层体系,探索了多种满足包装容器长效防腐要求的材料体系和涂装工艺。
一定数量的 16MnR 钢制密封容器存放在封闭洞室环境中,容器中封闭着 239Pu 等长寿命极毒组核素。在可见的将来,利用已有技术把放射性物质移出容器、转移到其它存储空间的技术难度大、成本高,因此把这些容器作为其中放射性废物的包装容器 。国内外大量的研究和工程实践表明,放射性废物处置和暂存均对存贮容器的耐腐蚀性能有较高要求 。前期研究结果表明,包装容器选用的 16MnR 钢材料在存放洞室中的腐蚀比较严重 。为了将地质条件用作防止放射性核素进入人类生存环境的屏障,借鉴高放废物地质处置的多重屏障设计,部分容器被就地填埋处理,填埋过程中,在包装容器与地质体之间填入混凝土和膨润土回填材料 。因此,为了增强包装容器的耐腐蚀性能,借鉴并优化商用重防腐有机涂层进行容器表面防腐,并研究探索将可用于多种介质环境常温下重防腐的 Zn-Al 金属涂层用于进一步提高包装容器的耐腐蚀能力和耐磨性,对防腐涂层与包装容器在填埋条件下的有效寿命进行预估。
实验所用材料和仪器
试 样 包 括 16MnR 裸 钢 试 样 和 6种 带 涂 层 16MnR 钢 试 样, 涂 层 包 括Zn 涂 层、Al 涂 层、Zn/Al 复 合 涂 层(100/300μm 和 300/100μm 两 种 设计)、Zn-Al 合金涂层和纳米有机涂层。裸钢试样和涂层试样基材的尺寸为100mm60mm6mm。纳米有机涂层按照现场采用的涂层设计(如表 1 所示)和涂装工艺进行加工,金属涂层厚度设计为400μm,采用高速电弧喷涂技术加工。
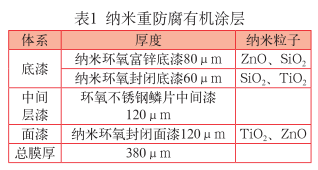
回填材料分别为轻集料混凝土和柯尔碱 200 目膨润土。其中,膨润土压实干密度达到 1.5g/cm 3 ,含水率为26%~28%,轻集料混凝土的配方如表 2所示。
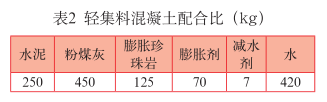
对于材料腐蚀研究,研究人员普遍采用室外现场埋设实验和室内模拟实验相结合的研究方法。现场埋设实验可以较客观地反映实验土壤腐蚀状态,但其实验周期一般较长,需要耗费大量的人力、物力。加速腐蚀实验作为室内模拟实验的重要组成部分,是在全面调查现场环境的基础上,控制实验参数,在较短时间内获取材料腐蚀机理及腐蚀速率的有效方法。
参考 GB 1763 和 GB 1690,利用强化介质法对 16MnR 钢及其防腐涂层在存放洞室中的大气腐蚀行为进行了盐雾加速腐蚀实验研究。为提高腐蚀实验相关性,盐雾腐蚀实验溶液以 5%wtNaCl 溶液为基础,其它离子的浓度按照洞室冷凝水水中离子含量 1:1 配制。
为开展 16MnR 钢材料及其防腐涂层在洞室环境与膨润土和轻集料混凝土的相容性研究,开展了 180d 的填埋环境加速腐蚀实验研究。兼顾相关性和加速比,利用现场回填所用的轻集料混凝土和膨润土,并采用类似的回填工艺制备了埋有试片的混凝土结构件和膨润土结构件,以此实现现场回填环境的模拟,并依据上述腐蚀机理周期性采用“强化介质法 + 干湿交替法”两种方法实现加速腐蚀。包裹块的包裹厚度为 25 ~ 30mm;强化介质溶液以 3.5%wtNaCl 溶液为基础,其它离子的浓度按照洞室现场裂隙水中离子含量 1:1 配制;包裹块浸泡 -干燥周期时间为 168h,其中浸泡时间为72h,干燥时间为 96h。
利用 PARSTAT2273 电化学工作站测试回填材料中涂层试片的线性极化曲线和电化学阻抗谱,并计算极化电阻 Rp和斯特恩 - 盖里常数 B 值。利用 B 值和极化电阻 Rp 计算得到腐蚀电流密度,进而利用法拉第定律计算出腐蚀速率。试样为工作电极,采用石墨电极为辅助电极,饱和甘汞电极为参比电极。
涂层体系设计
与中国科学院金属研究所合作,将经过包覆改性、微胶囊化表面改性的纳米 SiO 2 、TiO 2 和 ZnO 颗粒作为填料分散在在环氧树脂的聚合物结构中,研制出了如表 1 所示的环氧系纳米重防腐有机涂料。一方面,纳米粒子的比表面积大、表面活性大,因此可以提高纳米粒子与环氧基料、涂层与金属基体之间的结合力;另一方面,致密的纳米粒子网络结构能够有效抵抗腐蚀介质的渗透 。为实现纳米有机涂层在 16MnR 钢容器表面的良好涂装,根据涂层的表面质量、硬度及其与 16MnR 基体的结合强度等指标开展工艺优化实验,确定了高压无气喷涂工艺参数:喷涂速率为 40 ~ 50cm/s,喷涂距离为 40 ~ 60cm;空压机输出压力为 0.3 ~ 0.5MPa(压力比为 65:1)和0.4 ~ 0.6MPa(压力比为 32:1)。利用上述工艺得到的涂层硬度≥ 0.5(别尔科维其硬度),其与 16MnR 基体的附着力为 1 级(划圈法)。

与有机涂层相比,合金涂层具有与金属基体更大的结合力、可涂装厚度大(mm 级 ) 等优点,而且其成本较低、工艺周期较短(不需要涂层干燥和固化时间),因此选择以高速电弧喷涂工艺为主要技术特征的 Zn、Al 合金涂层开展研究,以丰富 16MnR 包装容器的表面防腐涂层体系。综合考虑涂层孔隙率、硬度及其与基体的结合强度,采用正交实验方法优化得到了 Zn-Al 合金涂层高速电弧喷涂工艺参数为:喷涂电压 30V、喷涂电流 180A、喷涂距离150mm、喷涂气压 0.7MPa。按照此组参数制备的 Zn-Al 合金涂层,其表面和截面显微组织形貌如图 1 所示,涂层由浅色区富 Zn 相和深色区富 Al 相二相组成,其中富 Al 相呈连续的框架网络,富 Zn相以块状形式存在于富 Al 相的网络包围之中。经性能检测,涂层结合强度为32.5MPa,孔隙率为 2.1%,显微硬度为HV49.45。
纳米有机涂层耐腐蚀性能原位考核研究
在 16MnR 包装容器暂存洞室内经历5a 挂片实验,16MnR 钢裸片表面发生全面腐蚀,部分铁锈脱落,在焊缝两侧热影响区腐蚀严重;采用纳米有机涂层保护的 16MnR 钢试片表面的涂层无可检测到的破坏,没有起泡、剥离、脱层和生锈现象,如图 2 所示。

从经历 4 年挂片实验的试片边缘处剥去部分涂层发现,边缘部分的涂层发生腐蚀,基体没有发现可见腐蚀现象,如图 3 所示。边缘处发生锈蚀是试片制备过程中封边质量不佳造成的。对纳米环氧富锌底漆中的 Zn 粉进行 X 射线衍射分析发现,Zn 粉的相组成为 Zn 和 ZnO,两者的质量比例为Zn:ZnO=89:11,如图 4(a) 所示;收集图 3 中白色粉末进行 X 射线衍射分析发现,其相组成为 Zn、ZnO 和 Zn(OH)2,三者的质量比为:Zn:ZnO:Zn(OH)2=2:46:31,如图 4(b) 所示;对图 3 中的黑灰色部分进行 X 射线衍射分析发现,该部分的相组成为 Zn 和 ZnO,两者的质量比例 Zn:ZnO=92:8,与涂料中原始 Zn 粉的质量组成相当,如图 4(c) 所示。这表明,一方面,经过洞室环境 4年考核,腐蚀性介质并未穿过涂层而造成基体腐蚀,这说明采用的纳米重防腐有机涂层对腐蚀性介质具有较好的机械屏蔽作用;另一方面,尽管因涂层工艺缺陷原因(如封边质量不佳等)会使得腐蚀性介质沿平行于涂层方向传输到达涂层与基体界面,但由于 Zn 粉可通过消耗自身来保护基体,起到了很好的阴极保护作用。

图3 剥离部分涂层的挂片的表观形貌


在 16MnR 包装容器暂存洞室内膨润土和水泥粉中经历 4a 埋片实验,16MnR钢裸片发生显著腐蚀,采用纳米重防腐有机涂层保护的 16MnR 钢试片表面的涂层基本无破坏,没有起泡、剥离、脱层和生锈现象,如图 5 所示。

涂层耐洞室大气腐蚀性能的盐雾腐蚀考核研究
盐雾腐蚀实验过程中,未经防腐处理的 16MnR 钢试片经历 120h 加速腐蚀实验即发生大面积腐蚀,如图 6 所示;采用纳米改性前的商用重防腐环氧有机涂层试片在 3600h 加速实验后表面出现起泡和少量锈斑现象;而采用纳米有机涂层保护的 16MnR 钢试片表面经历4500h基本无破坏,没有可检测的变化,如图 7 所示。根据腐蚀与防护领域的工程经验,以 1000h 加速腐蚀实验相当于海洋大气环境或湿热大气环境现场腐蚀10a 为参考,预估纳米有机涂层可在 45a内保护 16MnR 钢容器在洞室大气环境中不发生腐蚀,超过 30a 的防腐寿命需求。

(左试片涂有纳米复合涂层,右为裸片)
图6 120h加速实验后试片照片

(前试片涂有纳米复合涂层,后为裸片)
图7 4500h加速实验后试片照片
图 8 和图 9 分别给出了 5 种合金涂层的腐蚀累计增重和增重速率随盐雾时间的变化,Zn 涂层和 Zn-Al 合金涂层的增重数据接近,腐蚀速率较高;Al 涂层与两种Zn/Al复合涂层的腐蚀速率较小;Zn-Al 合金涂层 30d 腐蚀增重是 Al 涂层的 1.88 倍,Zn 涂层 30d 的腐蚀增重是Al 涂层的 1.69 倍;Al 合金涂层的累计增重速率随盐雾实验时间显著下降,这是 Al 涂层孔隙率低、结合强度大,其腐蚀产物因充填涂层空隙而形成“钝化膜”,因此其耐腐蚀性能较优。
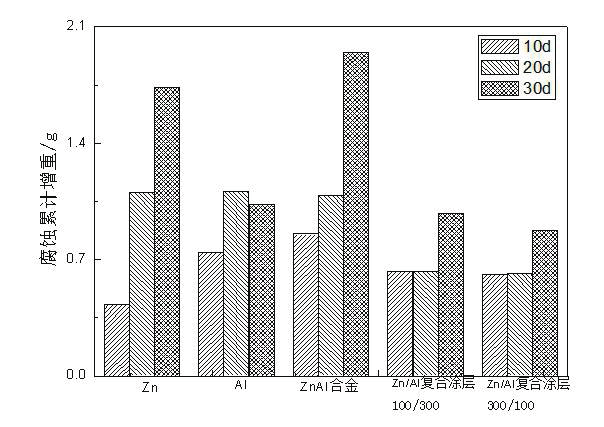
图8 合金涂层的累计增重

图9 合金涂层的累计增重速率
实验时间为 10d、20d、30d 时,纳米有机涂层腐蚀速率分别是 6.40×10-3μm/a、4.22×10-2μm/a 2.62×10-1μm/a。纳米有机涂层在盐雾腐蚀过程中的腐蚀速率较低,而且涂层宏观微观未发生明显变化,仍有较好的屏蔽保护性。Al 涂层靠涂层自身屏蔽作用及阴极保护作用达到保护基体的效果,加速30d 后涂层仍较为致密,且 Al 涂层有一定的钝化自修复作用,因此认为其防护作用优于纳米有机涂层。由于 Zn/Al 复合涂层出现鼓泡,Zn-Al 合金涂层发生明显腐蚀,可认为其对基体的防护效果差于纳米有机涂层。因此,对各涂层在盐雾腐蚀实验过程中的耐蚀性进行排序,由高至低依次为:Al 涂层 > 纳米有机涂层 >Zn/Al-100/300 复合涂层 >Zn/Al-300/100 复合涂层 >Zn-Al 合金涂层 >Zn 涂层。
涂层耐土壤腐蚀性能的加速腐蚀考核研究
经过 180d 模拟膨润土和轻集料混凝土填埋环境的加速腐蚀实验,通过与耐洞室大气腐蚀性能的盐雾腐蚀考核研究类似的评价内容,根据重量法、厚度法、宏观微观观察法和电化学阻抗法的综合分析发现,6 种涂层在膨润土和轻集料混凝土环境中的耐蚀性排序相同,均为 Al 涂层 > 纳米有机涂层 >Zn/Al-300/100 复合涂层>Zn/Al-100/300 复合涂层 >Zn-Al 合金涂层 >Zn 涂层。
对比研究发现,纳米有机涂层显著提高了 16MnR 钢容器在膨润土和轻集料混凝土环境中的耐腐蚀能力,其腐蚀速率在研究范围内降低了 1888 倍和 52倍以上。鉴于纳米有机涂层具有优良的耐腐蚀性能,而且可以利用无气喷涂、空气喷涂和手工刷涂等多种工艺进行涂装,对狭窄空间和深地坑等施工环境也具有较好的适应性,纳米有机涂层已经用于部分 16MnR 放射性废物包装容器的表面防腐。
涂层耐腐蚀寿命预估
研究发现,Al 涂层试样在容器存贮洞室经历 10 个月和 16 个月的挂片实验的大气腐蚀速率分别为 9.32m/a 和3.59m/a,而且 Al 涂层由于生成钝化膜导致其腐蚀速率随腐蚀时间而降低,因此预估 400m 厚的 Al 涂层在存贮洞室有不少于 111a 的耐大气腐蚀寿命,同样超过 30a 的防腐寿命需求。
根据对 Zn 涂层的腐蚀机理分析及腐蚀形貌观察认为,Zn 涂层的腐蚀属于均匀腐蚀,而且其腐蚀产物覆盖于涂层表面产生一定的屏蔽作用,因此认为其腐蚀规律与低合金钢类似。利用电化学线性极化曲线法原位测量得到 Zn 涂层在轻集料混凝土环境模拟腐蚀实验中的腐蚀速率 R,进而计算得到 Zn 涂层的腐蚀深度 C 与时间 t 的关系为:

将 Zn 涂层的腐蚀深度 C=400μm代入 (1) 式计算可得 400μm 厚的 Zn 涂层在轻集料混凝土模拟腐蚀实验过程中的防腐寿命约为 252a。在研究过程中,模拟腐蚀实验混凝土块的包裹厚度(2.5 ~ 3cm)比包装容器的轻集料混凝土层厚度(20cm)大约低 1 个数量级,因此 400μm 厚的 Zn 涂层在真实回填场景中的防腐寿命不低于 252a。而且在研究的 6 种涂层中,Zn 涂层对 16MnR 的防护效果最差,因此可以预估 400μm 厚的6 种涂层在真实回填场景中的防腐寿命均不低于 252a,超过 100a 的防腐寿命要求。
结论和后续考虑
通过 16MnR 放射性废物包装容器的表面腐蚀防护研究,分析了包装容器在封闭洞室环境中大气腐蚀机理和在膨润土、轻集料混凝土填埋环境中的土壤腐蚀机理,针对性设计了纳米有机涂层和 5种合金涂层,开展了模拟封闭洞室环境大气腐蚀的盐雾加速考核实验和模拟膨润土与轻集料混凝土填埋环境的土壤腐蚀加速考核实验。6 种涂层在洞室大气环境、膨润土以及轻集料混凝土填埋环境中耐蚀性排序类似,均为 Al 涂层 > 纳米有机涂层 > 其它 4 种涂层。纳米有机涂层和 Al 涂层在存贮洞室分别有不少于 45a和 111a 的耐大气腐蚀寿命,在填埋环境中的防腐寿命不低于 252a,均显著超过防腐需求。纳米有机涂层已经用于小型16MnR 放射性废物包装容器的表面防腐。
后续将开展 Zn-Al 合金涂层的失效机理研究,明确其在洞室大气和膨润土以及轻集料混凝土填埋环境耐腐蚀性能不佳的原因;针对洞室大气环境和膨润土以及轻集料混凝土填埋环境开展 Al 涂层的封闭涂层体系研究,为最终用于大型16MnR 放射性废物包装容器表面防腐提供支持。
免责声明:本网站所转载的文字、图片与视频资料版权归原创作者所有,如果涉及侵权,请第一时间联系本网删除。
相关文章
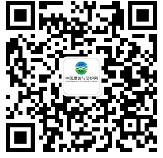
官方微信
《腐蚀与防护网电子期刊》征订启事
- 投稿联系:编辑部
- 电话:010-62316606-806
- 邮箱:fsfhzy666@163.com
- 腐蚀与防护网官方QQ群:140808414
点击排行
PPT新闻
“海洋金属”——钛合金在舰船的
点击数:8135
腐蚀与“海上丝绸之路”
点击数:6475