随着世界工业生产的迅速发展,大量CO2排入大气引发全球气候变暖等一系列问题[1,2]。CO2捕集与储存(carbon capture and storage,CCS)技术被认为是实现全球CO2减排的最有效方式[3~6],CO2的管道输送是CCS技术链中十分重要的一环[7~9]。由于CO2流体的临界参数较低(临界压力为7.38 MPa,临界温度为31.1℃)[10~12],输送过程中温度和压力的变化易导致CO2流体相态的改变[13,14],故CO2管道输送过程中常使CO2维持单一相态输送。根据不同的输送相态(纯CO2相图如图1所示),CO2输送可分为气态、液态、密相态及超临界态输送4种方式[15]。当前世界上绝大多数CO2输送管道建于美国,且输送方式多采用超临界态或密相态输送[16]。超临界态或密相态CO2输送管道的运输效率更高,但一旦发生泄漏等事故,易造成严重环境及安全灾害,而气态CO2输送管道则具有较高的安全性[17,18]。作为CO2的主要排放国家之一,我国对CCS技术给予高度重视,且将CCS技术列入中长期发展规划中。我国CO2输送管道建设起步较晚,尚无成熟的大规模长距离CO2输送管道投入运行,见报道的有齐鲁石化至正理庄油田的75 km CO2输送管道[19]、大庆油田建造的6.5 km CO2-EOR先导性试验CO2输送管道[20]和吉林油田建成的约50 km的CO2驱用管道,以上管道均为气态CO2输送管道[21]。
图1 纯CO2相图
CO2管道在输送过程中发生泄漏是十分严重的事故之一。美国管道安全处(OPS)的统计数据表明,45%的CO2输送管道发生失效是由腐蚀造成的[22],由于CO2输送管道内不可避免地含有水分及其他气体杂质(如SOx、NOx、O2、H2S、N2等)[23,24],且在高压环境下CO2与水的互溶度发生改变,在管内形成具有腐蚀性的溶液,极大地增加了管道发生腐蚀的风险。此外,相比于石油天然气输送管道,CO2输送管道中CO2流体作为主相,与管内其他杂质的交互作用及理化性质随环境发生的变化与油气管道具有显著差异,值得深入探究。目前国内外针对CO2输送管线内腐蚀问题的研究主要集中在超临界相态[25~34],对于含杂质气态CO2输送管道的内腐蚀研究较少。考虑到我国CCS技术的应用现状和发展规划,探明气态CO2输送管道的腐蚀行为及机理,并提出合理的腐蚀速率预测模型,对明确气态CO2输送管道腐蚀规律、规避管道发生腐蚀风险、减小管道运行经济损失,具有十分重要的现实意义。本文针对目前含杂质气态CO2输送管道的内腐蚀研究进行了系统的综述,总结了气态CO2输送管道腐蚀的影响因素,分析了气态CO2输送管道不发生腐蚀临界含水量的确定,归纳了适用于气态CO2输送管道的腐蚀速率预测模型,并针对现有研究的不足提出了当前亟待解决的科学问题和研究展望。
1 气态CO2输送管道腐蚀的影响因素
气态CO2输送管道在低温高压条件下(20~50℃、2~5 MPa)运行,管道内不可避免地存在水分及其他杂质(如SOx、NOx、O2、H2S、N2等),杂质的存在及相互作用是引发管道发生腐蚀的潜在因素。表1[35~45]列出了近年来关于含杂质气态CO2输送管道腐蚀的研究结果,杂质的种类及含量、环境条件(温度、压力等)的变化都会对输送管道的腐蚀行为产生重要影响,但杂质及环境条件对管道腐蚀的作用还需要进一步深入研究。
表1 近年来气态CO2输送管道腐蚀的研究结果[35~45]
1.1 杂质对气态CO2输送管道腐蚀的影响
1.1.1 杂质对互溶度的影响
水是腐蚀发生的根本条件,干燥的CO2不会导致腐蚀发生[46~48],腐蚀环境中水与CO2的互溶度决定了管道金属表面水凝结析出的数量,并决定了金属表面腐蚀溶液中腐蚀物质的浓度,故水与CO2的互溶度计算是腐蚀问题研究的基础。高压环境下,CO2输送管道内存在的杂质对水与CO2的互溶度产生影响,杂质及温度、压力的变化可能导致水相析出,并改变水相的化学组成,引起管线发生腐蚀。Spycher等[49]首先使用简化的H2O-CO2二元体系状态方程初步计算了温度范围为12~100℃、压力范围为0.1~60 MPa条件下水与CO2的互溶度,但当温度、压力较高时计算结果精度不高且计算过程较为依赖现场数据。为了进一步细致研究互溶度随温度、压力的变化,Choi和Ne?i?[37]提出了在不含杂质的情况下水与CO2的互溶度计算模型(如式(1)和(2)所示),其研究认为,当温度范围为15~85℃、压力范围为0.1~30 MPa时,随着压力的升高,水与CO2的互溶度均有所增大,但随着温度的升高,水在CO2中的溶解度有所增大,而CO2在水中的溶解度有所减小。此外,CO2在水中的溶解度远大于水在CO2中溶解度。互溶度计算模型的建立为不同条件下水相析出量的确定提供了参考,并为描述腐蚀的严重程度提供了量化借鉴。
式中,为水在CO2相中的摩尔分数;为CO2在水相中的摩尔分数;P为压力;T为温度;P0为参比压力(0.1 MPa);R为气体常数;、分别为水、CO2的平均摩尔体积;KK分别为水、气相CO2在参比压力下的平衡常数;Φ、Φ分别为水、CO2的逸度系数。
在互溶度计算模型的基础上,Sun等[36]探究了H2S对水与CO2互溶度的影响,指出H2S的加入降低了水在CO2相中的溶解度,并导致溶解于CO2相中的水部分析出,且析出量随加入H2S含量的增大而增大,当溶解水从CO2相中析出成为游离水后,CO2与H2S溶于其中并生成腐蚀性物质(如CO2(aq)、H2CO3、HCO、CO、H2S(aq)、HS-等)导致金属腐蚀加剧,故H2S杂质的存在将加剧管道钢在CO2相中的腐蚀。除H2S外,N2也会影响水在CO2中的溶解度,Foltran等[50]研究认为,N2的存在显著降低了水在CO2中的溶解度,尤其是在10.21 MPa且含10% N2的情况下,水在CO2中的溶解度从4450 × 10-6下降至3400 × 10-6 (下降约30%),这将导致大量游离水析出,极大地增加了管道钢的腐蚀风险。当前针对管内杂质对水与CO2互溶度产生影响的系统研究仍然较少,除H2S、N2外,气态CO2输送管道内可能存在的其他杂质(如SOx、NOx、O2等)也会对水与CO2的互溶度产生影响。此外,杂质对有水相存在的管道发生腐蚀的影响不仅取决于杂质的种类及其在CO2相中的浓度,还取决于其在CO2相与水相间的分配行为,这种分配受到CO2相态、温度、压力及杂质间相互作用等因素的共同影响,故针对CO2-水-杂质体系中水与CO2间及不同物质间的互溶度的测定计算应给予足够重视并进行详尽研究。
1.1.2 杂质对腐蚀行为及腐蚀机理的影响
CO2输送管道内存在的杂质首先会引起CO2流体的相特性发生变化[51] (含杂质CO2的相包线如图2[51]所示),其次,杂质通过与水相反应形成腐蚀性溶液、参与阴阳极电化学反应、改变腐蚀机理、引发局部腐蚀等作用对管道钢腐蚀行为产生影响,当前研究多关注H2S及O2对气态CO2输送管道腐蚀行为及腐蚀机理的影响。H2S通常来源于天然气开采及预燃烧过程,可直接与管道钢发生反应生成产物膜[52] (如式(3)所示),此外,H2S的存在能够改变水分在管道表面的吸附性质,导致管道钢表面生成一层薄水膜,H2S溶于其中并进行水解[33] (如式(4)和(5)所示),参与管道钢腐蚀过程。Zhang等[35]研究表明,在气态H2S/CO2环境中,碳钢的腐蚀速率随CO2分压的升高而有所增大,CO2分压的升高导致系统中腐蚀性物质(如H2CO3、HCO、H+)浓度增大从而导致腐蚀速率增大,但整体上碳钢的腐蚀速率随温度、压力及H2S分压的变化较小,腐蚀速率介于0.6~0.7 mm/a之间,该研究并未对发生此现象的原因及相应的腐蚀机理进行详细地讨论,H2S在气态H2S/CO2腐蚀体系中发挥的作用还需要进一步探究。Sun等[36]研究发现,在水饱和的气态CO2环境(50℃、5 MPa)中,H2S的加入导致碳钢的腐蚀速率增大近3倍,其分析认为H2S主要通过发生阴极反应来参与腐蚀过程并促进腐蚀进行(如式(6)所示),此外,H2S在碳钢表面与基体金属发生反应生成不同类型的硫化铁腐蚀产物(如式(7)所示),如Fe1+xS、Fe1-xS等,腐蚀产物化学成分的不均匀性导致金属表面产物膜保护性能产生差异,从而造成金属表面发生严重的局部腐蚀[53]。除H2S外,SO2也会导致管道钢发生局部腐蚀。Farelas等[54]研究指出,少量SO2即可引起管道发生严重的局部腐蚀,且SO2浓度的增大将加速局部腐蚀。Dugstad等[55]进一步探究了动态条件下SO2引发的局部腐蚀,结果表明即使系统中的含水量远低于该条件下水在CO2中的溶解度,SO2的存在仍会导致管道钢表面发生严重的局部腐蚀,但其并未对SO2引起管道钢发生局部腐蚀的机理进行细致研究。Hua等[29]通过研究也得到了类似的结论,同时,其认为局部腐蚀坑在整个腐蚀过程中的开始、发展、终止等过程亟需进行详尽研究。
图2 含杂质CO2的相包线[51]
管道中O2对腐蚀的影响当前仍存在争议。一方面,O2参与阴极电化学反应(如式(8)所示)且能够抑制FeCO3保护膜的生成(如式(9)和(10)所示),对腐蚀起到促进作用[27];另一方面,O2能够钝化金属并降低金属的均匀腐蚀速率[25,56]。Lin等[41]运用原位电化学测量技术进行了研究,认为在高温高压气态CO2环境中O2与金属发生化学反应生成Fe(OH)3,破坏了金属表面腐蚀产物膜的完整性,导致金属表面发生局部腐蚀且腐蚀速率较大,该研究的实验环境压力虽然为1 MPa,与气态CO2输送管道的实际工作压力有一定差距,但原位电化学测量技术的使用为气态CO2输送环境下管道钢电化学腐蚀原理的研究提供了重要参考。
总体来说,虽然针对H2S及O2对气态CO2输送管道腐蚀行为及腐蚀机理影响的研究已经取得了一些成果,但二者共同存在时管道钢的腐蚀行为特点及腐蚀机理尚不明确。在超临界CO2输送管道腐蚀研究领域,已有众多研究[25,27,57~59]证明多种杂质共同存在时杂质间具有协同竞争效应(如H2S、O2、SO2、NO2等),不同杂质相互作用,通过影响水与CO2的溶解度,参与化学、电化学反应,改变腐蚀产物膜组成及结构等过程影响管道钢的腐蚀行为。此外,SO2、NO2等其他杂质也会对管道钢的腐蚀产生显著影响[27,30,32]。因此,仍需要通过大量且系统的基础实验来探究不同杂质及其相互作用对气态CO2输送管道腐蚀行为及腐蚀机理的影响。
1.2 环境条件对气态CO2输送管道腐蚀的影响
1.2.1 压力的影响
压力能够对管道钢的腐蚀产生显著影响。压力的变化不仅能够影响管道表面腐蚀产物膜的生成过程,还会通过影响CO2与水的互溶度导致体系中腐蚀性物质(如H2CO3)的含量发生变化[60],从而影响腐蚀过程。Choi和Ne?i?[61]认为在CO2分压从4 MPa上升至8 MPa的过程中,虽然在7 MPa左右时CO2的相态从气态转变为超临界态,但在50℃且反应时长为24 h的情况下,碳钢的腐蚀速率并未明显增大。相反,Seiersten等[62]认为当CO2压力从1 MPa上升至5.6 MPa的过程中,在40℃并反应1~2周的情况下,碳钢的腐蚀速率出现了明显下降。二者研究中腐蚀速率数据的不一致可能与实验温度、测试时间、试样表面积与水相体积比、流动条件等因素有关。为了进一步明确气态CO2环境中压力变化对碳钢腐蚀速率的影响,Choi和Ne?i?[37]通过研究发现,腐蚀可以在高压且无游离水生成的水饱和气态CO2环境(50℃,4 MPa、6 MPa)中发生,当温度、压力发生微小变化时CO2中的溶解水便凝析至碳钢表面并迅速被CO2饱和,导致碳钢表面生成FeCO3保护膜,且保护性能随压力的增大而增强。该研究提出了有关管道钢腐蚀的新见解,强调了压力变化对管道钢表面产物膜的作用,且该研究的环境条件与气态CO2输送管道运行工况相接近,为探究压力波动对管道钢内腐蚀的影响提供了参考。但该研究并未考虑杂质存在时压力对管道钢腐蚀行为的影响,研究结论有待进一步充实。
压力的变化也会对水与CO2的互溶度产生影响,导致不同压力下腐蚀性物质的浓度产生差异,从而影响管道钢的腐蚀过程。Zhang等[38]发现,相同温度(50℃)下X65碳钢在超临界CO2环境(9.5 MPa)中的腐蚀速率远大于气态CO2环境(1 MPa),其研究指出当压力接近CO2的临界点时,CO2在水中的溶解度迅速增大,导致超临界环境的水溶液中腐蚀性物质(H2CO3、HCO、CO)浓度较大,相应的阴极反应速率加快,最终导致腐蚀速率明显增大。类似地,Wei等[40]通过计算得知,50℃时气态环境(1 MPa)中水在CO2中的溶解度约为超临界环境(10 MPa)中的4倍,故气态环境中溶解于CO2中的水分较多、凝结析出的水分较少,而超临界环境中则有更多的水凝结聚集于试样表面,此外,超临界环境中碳钢表面的腐蚀性物质(CO2、H2CO3、H+)浓度远大于气态环境,因此,超临界CO2环境中的碳钢腐蚀更加严重。两者的研究均指出压力会对水与CO2的互溶度产生显著影响并最终导致管道钢在不同压力下的腐蚀速率产生明显差异,但二者研究所取压力较为局限,压力变化对含杂质气态CO2输送条件下水与CO2及杂质间互溶度的影响还需进行系统研究。
1.2.2 温度的影响
温度对于管道钢腐蚀的影响主要包括2个方面:一方面,随着系统温度的升高,反应分子获得更多的能量,从而更多的分子越过活化能相互碰撞,导致腐蚀速率有所增大[63];另一方面,温度影响FeCO3的生成过程,温度的升高导致FeCO3成核速率加快,使得管道金属表面的腐蚀防护膜更加完整、致密且具有保护性[64]。上述2种效应共同影响腐蚀速率,即在腐蚀产物膜生成前,高温下金属的腐蚀速率较大,然而当腐蚀产物膜生成后,高温下金属的腐蚀速率反而较小。Zhang等[38]研究指出,在气态CO2环境中,随着温度的上升,X65碳钢的腐蚀速率先增大后减小,而表面的腐蚀产物膜厚度逐渐减小,其分析认为温度越高,FeCO3的过饱和度及沉积速率越大,导致高温时腐蚀产物膜生成更加迅速且更加致密,保护性能更好,故高温时碳钢的腐蚀速率较低。此外,虽然低温时腐蚀产物膜更厚,但其表面的孔状缺陷更多,保护性能较差。该研究阐明了温度通过影响管道钢表面产物膜厚度及结构进而影响管道钢的腐蚀速率,为探明温度对气态CO2输送管道腐蚀行为的影响提供了研究思路。总体上,针对温度对气态CO2输送管道腐蚀行为影响的研究还比较少,温度变化对含杂质气态CO2输送系统中CO2与水的互溶度、管道钢表面产物膜及腐蚀机理等因素的影响还需进行大量基础实验研究。
1.2.3 其他条件的影响
除压力、温度外,其他条件(如暴露角度、腐蚀反应时间、所处介质、流速等)对管道钢的腐蚀行为也会产生不同程度的影响。在气态CO2的输送过程中,由于输送温度及压力的波动,水分将凝结于管壁上,此过程可分为2种[65]:水分在侧壁凝结并在重力的作用下滑落至管底;水分凝结并吸附于管顶,故暴露角度可对管道腐蚀产生明显影响[66]。Wei等[40]研究表明,在气态CO2环境中,液滴可以随机地分布于水平放置的试样表面,但难以附着于垂直的试样表面,只能少量地聚集于垂直试样的底部边缘,故垂直放置的试样腐蚀速率最小,水平放置的试样腐蚀速率较大,该研究为气态CO2输送管道内部不同位置的腐蚀情况判断提供了参考。
腐蚀反应时间的长短对管道钢表面腐蚀产物膜的生成及结构变化产生显著影响,腐蚀产物膜厚度、结构及致密程度等特征决定了管道钢耐腐蚀的程度,即决定了管道钢腐蚀速率的大小[67]。Liu等[42]研究认为,在含饱和水的气态CO2环境中,低合金钢的腐蚀速率随腐蚀反应时间的延长先增大后减小,当反应时间为96 h时,金属表面开始出现FeCO3晶体,且腐蚀速率达到最大值。总体上,腐蚀产物膜在金属表面的覆盖面积随反应时间的延长由小变大,并最终形成一层完整的腐蚀产物膜。该研究为探究气态CO2输送管道内表面腐蚀产物膜随服役时间延长的变化提供了研究思路,但该研究条件较为局限,含杂质条件下反应时间对气态CO2输送管道内表面腐蚀产物膜的影响及对管道钢腐蚀速率的影响有待进一步研究。
管道钢所处介质不同,则腐蚀反应类型及腐蚀机理也不同[68],管道内存在的离子将对管道钢腐蚀电化学过程及腐蚀机理产生影响[69]。Almeida等[39]运用原位电化学测量技术研究指出,在24℃、3 MPa的气态CO2环境中,X65碳钢在CO2饱和盐溶液中的腐蚀速率约为蒸馏水中的3倍,其分析认为盐溶液中的pH值影响了CO2与Fe2+发生反应的类型及过程,从而影响了腐蚀反应的动力学平衡,导致腐蚀速率有所增大。该研究并未对腐蚀反应后金属的表面形貌及腐蚀产物进行分析,但在气态CO2管道内表面腐蚀反应类型及原理研究方面提出了新的见解。Liu等[70]研究了Cl-在管道钢腐蚀过程中发挥的作用,结果表明在气态CO2环境中,N80碳钢的腐蚀速率随Cl-含量的增加先增大后减小,在到达最大值之前,Cl-含量的增加导致腐蚀电流密度有所增大并加快了阳极反应速率,促进了腐蚀进行;然而,在到达最大值之后,Cl-含量的增加显著降低了溶液中CO2的溶解度并降低了H+、H2O、H2CO3、HCO
等物质参与腐蚀反应的可能性,导致腐蚀速率有所降低。该研究阐释了Cl-在管道钢腐蚀过程中对腐蚀电化学反应及腐蚀反应物质参与腐蚀过程的影响,研究过程中电化学测量技术的使用为探究气态CO2管道中杂质离子对管道钢腐蚀行为及电化学腐蚀机理的作用提供了宝贵借鉴。
流动条件的改变将对管道钢表面腐蚀产物膜产生直接影响。流速的变化将导致腐蚀产物膜的结构、致密程度、对金属的保护性能等特性产生明显差异,从而影响管道钢的腐蚀行为[71]。刘丹[72]详尽研究了气态CO2输送条件(60℃、5 MPa)下流速对N80碳钢腐蚀行为及腐蚀机理的影响,指出流动加速了腐蚀反应的传质过程,从而加速了阴极反应进程和腐蚀产物的脱落,导致管道钢的腐蚀速率较静态条件有所增大。此外,流动还能导致管道钢发生局部腐蚀[73],Schmitt和Mueller[74]研究指出,如果流体临界流动强度抑制了保护性腐蚀产物膜的再生,局部腐蚀就会在腐蚀产物膜局部破裂剥落的部位发生。在此基础上,魏亮[75]详尽研究了局部腐蚀过程中腐蚀产物膜在腐蚀坑内的演变过程,认为流动产生壁面剪切力的大小及局部腐蚀坑尺寸的大小决定了局部腐蚀坑内FeCO3保护膜能否再生,从而决定了局部腐蚀是否加剧。虽然当前已初步明确流动对CO2输送管道钢腐蚀产生了一些影响,但针对气态CO2输送环境中流动对管道钢腐蚀造成影响的研究仍鲜有报道,故需要进行大量基础实验研究以明确流动条件下含杂质气态CO2环境中管道钢的腐蚀行为及腐蚀机理,从而为气态CO2输送管道的实际运行提供理论依据。
不同金属材料的耐腐蚀性能也有明显差异[76]。Hassani等[43]研究认为,在60℃、3 MPa的CO2饱和盐溶液中金属的耐腐蚀性由好到差依次为:13Cr钢、5Cr钢、碳钢,腐蚀过程中虽然碳钢及5Cr钢表面生成的腐蚀产物膜较厚,但由于其多孔且附着性较差,导致碳钢及5Cr钢的腐蚀速率仍然较大,而13Cr钢表面生成一层薄而紧实且附着性良好的钝化膜,为13Cr钢提供了良好的防护并显著降低了13Cr钢的腐蚀速率。该研究结合三电极原位电化学测量技术全面探究了气态CO2环境下盐溶液中金属的耐腐蚀性能,为气态CO2输送管道钢选择提供了重要参考。
总体来说,当前有关气态CO2输送条件下管道钢腐蚀的实验及现场数据较少,不同环境条件下含杂质气态CO2输送管道的腐蚀行为及腐蚀机理需要进一步系统研究。
2 气态CO2输送管道临界含水量研究
在CO2的实际管道输送过程中,在输送前需对所输CO2流体进行脱水处理以避免管道内出现游离水导致管道发生腐蚀。美国现存CO2输送管道对于含水量的要求十分严格,要求含水量低于50 × 10-6,即通常被认为是全脱水输送[18]。李玉星等[77]归纳了富CO2输送管道不发生腐蚀的最大含水量与压力、温度的关系(图3[77]),并认为设定最高操作压力下的露点要求并不安全。一般地,对于操作温度高于4℃的纯CO2输送管道,避免发生腐蚀的含水量为(300~500) × 10-6 [78~80]。此外,Visser等[78]基于DYNAMIS规范认为CO2输送管道的含水量上限在(20~630) × 10-6,显然,将CO2输送管道中的含水量降低至很低的数值是不必要且不经济的,故需要根据管道运行的温度、压力及所含杂质来确定一个合理、经济的临界含水量,但当前还不存在针对CO2输送管道最大含水量的国际共识。McGrail等[79]首先探究了22℃、6.25 MPa的气态CO2环境中不同含水率下X70碳钢的腐蚀行为,结果表明,经过72 h的腐蚀反应,在含水率为90%RH (相对湿度)的环境中碳钢表面形成了腐蚀防护膜,然而,在含水率为55%RH的环境中,碳钢经过42 d的反应也并未发生腐蚀,故其认为此条件下的临界含水率介于55%RH与90%RH之间。在此基础上,针对气态CO2输送管道,Jiang等[44]研究表明在游离水相出现前,X65碳钢的均匀腐蚀速率不随相对湿度的增加而变化,但当游离水出现后,均匀腐蚀速率明显增大,如在温度、压力分别为35℃、4 MPa且存在游离水的情况下,X65碳钢发生了严重的均匀腐蚀并出现了局部腐蚀,研究认为气态CO2输送管道不发生腐蚀的临界含水率为80%RH。上述研究为气态CO2输送管道临界含水量的确定提供了参考,但管道内可能存在的其他杂质(如SOx、NOx、O2、H2S、N2等)也会导致管道发生腐蚀,杂质种类及含量的变化将改变水与CO2的互溶度,从而影响水的凝结析出及管内腐蚀物质的浓度。此外,温度、压力的波动也将影响溶于CO2相中水分的析出。总体上,温度、压力及杂质将对气态CO2输送管道临界含水量的确定产生重要影响,然而当前针对含杂质气态CO2输送管道临界含水量的研究仍然较少,故需要对不同条件下含杂质气态CO2输送管道的临界含水量进行大量的系统实验研究,以确定合理的临界含水量,从而保证气态CO2输送管道的经济、安全运行。
图3 富CO2输送管道最大含水量与压力、温度的关系图[77]
3 气态CO2输送管道腐蚀预测模型
基于物理化学过程的腐蚀预测模型的开发是腐蚀科学技术领域的研究热点之一,模型可以帮助工程师判别腐蚀问题,从而做出与腐蚀防护相关的决策[81]。由于腐蚀问题与油气井、管道及其他设备的安全运行密切相关,故腐蚀预测对于油气工业生产尤为重要。CO2腐蚀是油气工业中最常见的腐蚀类型,最早的CO2腐蚀模型由DeWaard与Milliams[48]于1975年提出,随着CO2腐蚀受到越来越多的关注,更多的CO2腐蚀预测模型被提出且被研究者进行了很好的总结归纳[82]。尽管目前有多种CO2腐蚀预测模型[83~85],但其绝大多数仅能应用于CO2分压范围为0~2 MPa的油气生产环境,当模型应用于更高分压的CO2环境时,腐蚀速率预测值大多比实验值高一个数量级[86,87],预测结果并不准确,而产生上述差异的根本原因是高分压CO2环境中水化学及腐蚀机理特性与低分压CO2环境有所不同。随着CCS技术的不断发展,高压CO2输送管道腐蚀预测也得到了广泛关注,当前高压CO2腐蚀预测模型研究已取得一些成果[88,89],其中,可应用于气态CO2输送管道的腐蚀速率预测模型如表2[90~96]所示。
表2 适用于气态CO2输送管道的腐蚀速率预测模型[90~96]
在低压CO2管道腐蚀速率预测模型的基础上,Choi等[97]对模型进行改进并提出了高压CO2环境(0~14 MPa、0~80℃)中低碳钢腐蚀速率预测模型,模型使用Spycher模型[49]及Duan模型[98,99]计算CO2的溶解度,运用H2CO3的Langmuir吸附等温式[100]改进了电化学模型描述,模型计算得到的腐蚀速率与实验数据吻合较好,且为高压气态CO2输送管道腐蚀速率预测提供了模型改进参考。井筒系统(wellbore systems)用于隔离地下流体[101~103],需要在高温、高压、高含盐、高含CO2的CO2封存环境中保持自身的完整性。Han等[104]结合Pitzer基础水化学模型[105]与经典电化学模型[106]提出了应用于井筒系统的低碳钢腐蚀速率预测模型,模型适用的温度范围为0~100℃、CO2分压范围为0.1~100 MPa,该模型计算范围广泛,为气态CO2输送管道腐蚀速率预测提供了借鉴,然而,此模型未考虑金属表面生成的腐蚀产物膜对腐蚀速率的影响。腐蚀产物膜对腐蚀速率及产生局部腐蚀倾向的影响有待于进一步研究。针对CCS过程中的其他环节,也提出了一些腐蚀速率预测模型。Li等[107]建立了CO2封存条件下碳钢的腐蚀速率预测模型,该模型综合了多种子模型以量化相关腐蚀过程对腐蚀速率的作用,模型应用范围广泛,可实现气态CO2输送条件下管道的腐蚀速率预测,但其可靠性与可应用性在很大程度上依赖于现有的研究数据,故需要更广泛的现场及实验数据来验证模型的准确性。总体来说,虽然目前存在的一些腐蚀速率预测模型可应用于气态CO2输送管道,但预测结果的精确程度并不能保证。当前针对气态CO2输送管道腐蚀速率预测模型的研究鲜有报道,气态CO2输送管道内可能存在的多种杂质间的相互作用决定了腐蚀机理的复杂性,导致腐蚀速率预测变得困难,而腐蚀速率预测对于管道的安全运行及完整性管理尤为重要,因此,气态CO2输送管道腐蚀速率预测模型的建立成为一项亟待解决的科学问题。
4 研究展望
目前针对含杂质气态CO2输送管道腐蚀的研究仍然较少,在杂质对腐蚀机理的影响、临界含水量的确定、腐蚀模型的发展等方面仍存在一定的局限性。气态CO2输送环境下管道腐蚀研究亟待解决的科学问题和研究展望如下:
(1) 当前针对含杂质(H2O、N2、O2、NOx、SOx、H2S等)气态CO2环境中水与CO2互溶度的计算研究较少,需进一步探究不同种类杂质对水与CO2互溶度的影响。
(2) 气态CO2输送环境下杂质间的协同竞争作用以及杂质对腐蚀产物膜特征及腐蚀机理的影响需要深入研究。
(3) 动态条件下含杂质气态CO2环境中管道钢的局部腐蚀行为及局部腐蚀机理需要系统研究。
(4) 目前在高压且含微量水的环境中开展原位电化学测试十分困难,亟需确定含杂质气态CO2环境中电化学测试规范以准确解释气态CO2输送管道的腐蚀电化学机理。
(5) 建立含杂质气态CO2输送管道腐蚀产物膜的评价规范并量化腐蚀产物膜的生成、发展过程及对管道钢的保护作用。
(6) 确定保证含杂质气态CO2输送管道不发生腐蚀的临界含水量,为CO2管道输送前的脱水环节提供经济可行的参考。
(7) 当前存在的气态CO2管道腐蚀模型仍然不够精确,需要建立针对含杂质气态CO2输送条件下的管道内腐蚀预测模型,以指导管道安全运行,推动我国CCS技术的发展与应用。
参考文献
1 Hekkert M P, Joosten L A J, Worrell E, et al. Reduction of CO2 emissions by improved management of material and product use: The case of primary packaging [J]. Resour. Conserv. Recy., 2000, 29: 33
2 Wang C L, Li Y X, Teng L, et al. Experimental study on dispersion behavior during the leakage of high pressure CO2 pipelines [J]. Exp. Therm. Fluid Sci., 2019, 105: 77
3 IPCC. Carbon Dioxide Capture and Storage [M]. New York: Cambridge University Press, 2005: 1
4 Czernichowski-Lauriol I, Berenblyum R, Bigi S, et al. CO2 GeoNet actions in Europe for advancing CCUS through global cooperation [J]. Energy Procedia, 2018, 154: 73
5 Bhave A, Taylor R H S, Fennell P, et al. Screening and techno-economic assessment of biomass-based power generation with CCS technologies to meet 2050 CO2 targets [J]. Appl. Energy, 2017, 190: 481
6 Reiner D M. Learning through a portfolio of carbon capture and storage demonstration projects [J]. Nat. Energy, 2016, 1: 15011
7 Gibbins J, Chalmers H. Carbon capture and storage [J]. Energy Policy, 2008, 36: 4317
8 Lilliestam J, Bielicki J M, Patt A G. Comparing carbon capture and storage (CCS) with concentrating solar power (CSP): Potentials, costs, risks, and barriers [J]. Energy Policy, 2012, 47: 447
9 Gale J, Davison J. Transmission of CO2-safety and economic considerations [J]. Energy, 2004, 29: 1319
10 Boot-Handford M E, Abanades J C, Anthony E J, et al. Carbon capture and storage update [J]. Energy Environ. Sci., 2014, 7: 130
11 Kruse H, Tekiela M. Calculating the consequences of a CO2-pipeline rupture [J]. Energy Convers. Manage, 1996, 37: 1013
12 Liu Z G, Gao X H, Li J P, et al. Corrosion behaviour of low-alloy martensite steel exposed to vapour-saturated CO2 and CO2-saturated brine conditions [J]. Electrochim. Acta, 2016, 213: 842
13 Wang C L, Gu S W, Li Y X, et al. Experimental study on foaming characteristics of CO2-crude oil mixture [J]. CIESC J., 2019, 70: 251
13 王财林, 顾帅威, 李玉星等. CO2-原油体系发泡特性实验研究 [J]. 化工学报, 2019, 70: 251
14 Lovseth S W, Skaugen G, Stang H G J, et al. CO2 mix project: Experimental determination of thermo physical properties of CO2-rich mixtures [J]. Energy Procedia, 2013, 37: 2888
15 Vandeginste V, Piessens K. Pipeline design for a least-cost router application for CO2 transport in the CO2 sequestration cycle [J]. Int. J. Greenhouse Gas Control, 2008, 2: 571
16 Barker R, Hua Y, Neville A. Internal corrosion of carbon steel pipelines for dense-phase CO2 transport in carbon capture and storage (CCS)—A review [J]. Int. Mater. Rev., 2017, 62: 1
17 Lone S, Cockerill T, Macchietto S. The techno-economics of a phased approach to developing a UK carbon dioxide pipeline network [J]. J. Pipeline Eng., 2010, 9: 225
18 Sandana D, Hadden M, Race J, et al. Transport of gaseous and dense carbon dioxide in pipelines: is there an internal corrosion risk? [J]. J. Pipeline Eng., 2012, 11: 229
19 Qi G L. Research on CO2 pipeline and liquid separation project of Qilu Petrochemical to Zhenglizhuang oilfield [D]. Qingdao: China University of Petroleum (East China), 2014
19 亓冠玲. 齐鲁二化厂至正理庄油田高89地区CO2输送管道及液化分离工程方案研究 [D]. 青岛: 中国石油大学(华东), 2014
20 Xie S X, Han P H, Qian Y. A pilot test and research on oil displacement by injecting CO2 in eastern Sanan of Daqing oilfield [J]. Oil Gas Recov. Technol., 1997, 4(3): 13
20 谢尚贤, 韩培慧, 钱 昱. 大庆油田萨南东部过渡带注CO2驱油先导性矿场试验研究 [J]. 油气采收率技术, 1997, 4(3): 13
21 Division of Social Development Science and Technology, Ministry of Science and Technology Development, Department of International Cooperation, Ministry of Science and Technology, China Agenda 21 Management Center. Carbon capture, utilization and storage technology development in China [R]. Beijing, 2011
21 科学技术部社会发展科技司, 科学技术部国际合作司, 中国21世纪议程管理中心. 中国碳捕集、利用与封存(CCUS)技术进展报告 [R]. 北京, 2011
22 Johnson K, Holt H, Helle K, et al. Mapping of potential HSE issues related to large-scale capture, transport and storage of CO2 [R]. Horvik: Det Norsk Veritas, 2008
23 Choi Y S, Nesic S, Young D. Effect of impurities on the corrosion behavior of CO2 transmission pipeline steel in supercritical CO2-water environments [J]. Environ. Sci. Technol., 2010, 44: 9233
24 Sim S, Cole I S, Bocher F, et al. Investigating the effect of salt and acid impurities in supercritical CO2 as relevant to the corrosion of carbon capture and storage pipelines [J]. Int. J. Greenhouse Gas Control, 2013, 17: 534
25 Sun C, Sun J B, Wang Y, et al. Synergistic effect of O2, H2S and SO2 impurities on the corrosion behavior of X65 steel in water-saturated supercritical CO2 system [J]. Corros. Sci., 2016, 107: 193
26 Hua Y, Barker R, Neville A. The effect of O2 content on the corrosion behaviour of X65 and 5Cr in water-containing supercritical CO2 environments [J]. Appl. Surf. Sci., 2015, 356: 499
27 Sun J B, Sun C, Wang Y. Effects of O2 and SO2 on water chemistry characteristics and corrosion behavior of X70 pipeline steel in supercritical CO2 transport system [J]. Ind. Eng. Chem. Res., 2018, 57: 2365
28 Xiang Y, Wang Z, Xu C, et al. Impact of SO2 concentration on the corrosion rate of X70 steel and iron in water-saturated supercritical CO2 mixed with SO2 [J]. J. Supercrit. Fluids, 2011, 58: 286
29 Hua Y, Barker R, Neville A. The influence of SO2 on the tolerable water content to avoid pipeline corrosion during the transportation of supercritical CO2 [J]. Int. J. Greenhouse Gas Control, 2015, 37: 412
30 Sun C, Sun J B, Wang Y, et al. Effect of impurity interaction on the corrosion film characteristics and corrosion morphology evolution of X65 steel in water-saturated supercritical CO2 system [J]. Int. J. Greenhouse Gas Control, 2017, 65: 117
31 Hua Y, Jonnalagadda R, Zhang L, et al. Assessment of general and localized corrosion behavior of X65 and 13Cr steels in water-saturated supercritical CO2 environments with SO2/O2 [J]. Int. J. Greenhouse Gas Control, 2017, 64: 126
32 Hua Y, Neville A, Barker R. Corrosion behaviour of X65 steels in water-containing supercritical CO2 environments with NO2/O2 [A]. NACE Corrosion 2018 Conference and Expo. 2018 [C]. Phoenix: National Association of Corrosion Engineers, 2018: 11085
33 Wei L, Pang X L, Gao K W. Effect of small amount of H2S on the corrosion behavior of carbon steel in the dynamic supercritical CO2 environments [J]. Corros. Sci., 2016, 103: 132
34 Yu C, Wang H W, Gao X H. Corrosion behavior of carbon steel with pearlite-ferrite microstructure in water-saturated supercritical H2S/CO2 environment [J]. Int. J. Electrochem. Sci., 2018, 13: 6059
35 Zhang G A, Zeng Y, Guo X P, et al. Electrochemical corrosion behavior of carbon steel under dynamic high pressure H2S/CO2 environment [J]. Corros. Sci., 2012, 65: 37
36 Sun C, Sun J B, Luo J L. Unlocking the impurity-induced pipeline corrosion based on phase behavior of impure CO2 streams [J]. Corros. Sci., 2020, 165: 108367
37 Choi Y S, Ne?i? S. Determining the corrosive potential of CO2 transport pipeline in high pCO2-water environments [J]. Int. J. Greenhouse Gas Control, 2011, 5: 788
38 Zhang Y C, Pang X L, Qu S P, et al. Discussion of the CO2 corrosion mechanism between low partial pressure and supercritical condition [J]. Corros. Sci., 2012, 59: 186
39 Almeida T D C, Bandeira M C E, Moreira R M, et al. New insights on the role of CO2 in the mechanism of carbon steel corrosion [J]. Corros. Sci., 2017, 120: 239
40 Wei L, Pang X L, Zhou M, et al. Effect of exposure angle on the corrosion behavior of X70 steel under supercritical CO2 and gaseous CO2 environments [J]. Corros. Sci., 2017, 121: 57
41 Lin X Q, Liu W, Wu F, et al. Effect of O2 on corrosion of 3Cr steel in high temperature and high pressure CO2-O2 environment [J]. Appl. Surf. Sci., 2015, 329: 104
42 Liu Z G, Gao X H, Du L X, et al. Corrosion behavior of low-alloy steel with martensite/ferrite microstructure at vapor-saturated CO2 and CO2-saturated brine conditions [J]. Appl. Surf. Sci., 2015, 351: 610
43 Hassani S, Vu T N, Rosli N R, et al. Wellbore integrity and corrosion of low alloy and stainless steels in high pressure CO2 geologic storage environments: An experimental study [J]. Int. J. Greenhouse Gas Control, 2014, 23: 30
44 Jiang X, Qu D R, Song X L, et al. Critical water content for corrosion of X65 mild steel in gaseous, liquid and supercritical CO2 stream [J]. Int. J. Greenhouse Gas Control, 2019, 85: 11
45 Jiang X, Qu D R, Song X L, et al. Impact of water content on corrosion behavior of CO2 transportation pipeline [A]. NACE Corrosion 2015 Conference and Expo. 2015 [C]. Dallas: NACE International, 2015: 5844
46 Russick E M, Poulter G A, Adkins C L J, et al. Corrosive effects of supercritical carbon dioxide and cosolvents on metals [J]. J. Supercrit. Fluids, 1996, 9: 43
47 Zhang Y C, Gao K W, Schmitt G. Effect of water on steel corrosion under supercritical CO2 conditions [J]. Mater. Performance, 2011, 50: 62
48 DeWaard C, Milliams D E. Prediction of carbonic acid corrosion in natural gas pipelines [A]. First International Conference on the Internal and External Protection of Pipes [C]. UK: University of Durham, 1975: 28
49 Spycher K, Pruess K, Ennis-King J. CO2-H2O mixtures in the geological sequestration of CO2. I. Assessment and calculation of mutual solubilities from 12 to 1000oC and up to 600 bar [J]. Geochim. Cosmochim. Acta, 2003, 67: 3015
50 Foltran S, Vosper M E, Suleiman N B, et al. Understanding the solubility of water in carbon capture and storage mixtures: An FTIR spectroscopic study of H2O+CO2 +N2 ternary mixtures [J]. Int. J. Greenhouse Gas Control, 2015, 35: 131
51 Gu S W, Teng L, Li Y X, et al. Propagation characteristic of decompression wave for gaseous CO2 in pipeline containing impurities [J]. Petrochem. Technol., 2018, 47: 689
51 顾帅威, 滕 霖, 李玉星等. 含杂质气态CO2管道减压波传播特性 [J]. 石油化工, 2018, 47: 689
52 Zeng Y M, Arafin M, Shi C, et al. Influence of impurity hydrogen sulfide on the corrosion performance of pipeline steels in supercritical carbon dioxide stream [A]. NACE Corrosion 2016 Conference and Expo. 2016 [C]. Vancouver: NACE International, 2016: 7223
53 Wei L, Pang X L, Gao K W. Corrosion of low alloy steel and stainless steel in supercritical CO2/H2O/H2S systems [J]. Corros. Sci., 2016, 111: 637
54 Farelas F, Choi Y S, Nesic S. Corrosion behavior of API 5L X65 carbon steel under supercritical and liquid CO2 phases in the presence of H2O and SO2 [J]. Corrosion, 2013, 69: 243
55 Dugstad A, Halseid M, Morland B. Effect of SO2 and NO2 on corrosion and solid formation in dense phase CO2 pipelines [J]. Energy Procedia, 2013, 37: 2877
56 Tang Y, Guo X P, Zhang G A. Corrosion behaviour of X65 carbon steel in supercritical-CO2 containing H2O and O2 in carbon capture and storage (CCS) technology [J]. Corros. Sci., 2017, 118: 118
57 Sun J B, Sun C, Zhang G A, et al. Effect of O2 and H2S impurities on the corrosion behavior of X65 steel in water-saturated supercritical CO2 system [J]. Corros. Sci., 2016, 107: 31
58 Sun C, Sun J B, Liu S B, et al. Effect of water content on the corrosion behavior of X65 pipeline steel in supercritical CO2-H2O-O2-H2S-SO2 environment as relevant to CCS application [J]. Corros. Sci., 2018, 137: 151
59 Hua Y, Barker R, Neville A. Understanding the influence of SO2 and O2 on the corrosion of carbon steel in water-saturated supercritical CO2 [J]. Corrosion, 2015, 71: 667
60 Xiang Y, Xu M H, Choi Y S. State-of-the-art overview of pipeline steel corrosion in impure dense CO2 for CCS transportation: Mechanisms and models [J]. Corros. Eng. Sci. Technol., 2017, 52: 485
61 Choi Y S, Ne?i? S. Corrosion behavior of carbon steel in supercritical CO2-water environments [A]. NACE Corrosion 2009 Conference and Expo. 2009 [C]. Atlanta: NACE International, 2009: 09256
62 Seiersten M. Materials selection for separation, transportation and disposal of CO2 [A]. NACE Corrosion 2001 Conference and Expo. 2001 [C]. Houston: NACE International, 2001: 01042
63 Tan J, Chan K S. Understanding Advanced Physical Inorganic Chemistry: The Learner's Approach [M]. Singapore: World Scientific Publishing Company, 2010: 1
64 Dugstad A. Fundamental aspects of CO2 metal loss corrosion, part I: mechanism [A]. NACE Corrosion 2006 Conference and Expo. 2006 [C]. San Diego: NACE International, 2006: 6111
65 Zhang Z, Hinkson D, Singer M, et al. A mechanistic model of top-of-the-line corrosion [J]. Corrosion, 2007, 63: 1051
66 Qu S P, Li X, Gao K W, et al. The effect of exposure angle on the corrosion behavior of low-carbon microalloyed steel under CO2 conditions [J]. Corrosion, 2015, 71: 343
67 Zhang J, Wang Z L, Wang Z M, et al. Chemical analysis of the initial corrosion layer on pipeline steels in simulated CO2-enhanced oil recovery brines [J]. Corros. Sci., 2012, 65: 397
68 Tran T, Brown B, Nesic S. Corrosion of mild steel in an aqueous CO2 environment—Basic electrochemical mechanisms revisited [A]. NACE Corrosion 2015 Conference and Expo. 2015 [C]. Dallas: NACE International, 2015: 5671
69 Ma H Y, Yang C, Li G Y, et al. Influence of nitrate and chloride ions on the corrosion of iron [J]. Corrosion., 2003, 59: 1112
70 Liu Q Y, Mao L J, Zhou S W. Effects of chloride content on CO2 corrosion of carbon steel in simulated oil and gas well environments [J]. Corros. Sci., 2014, 84: 165
71 Gao K W, Yu F, Pang X L, et al. Mechanical properties of CO2 corrosion product scales and their relationship to corrosion rates [J]. Corros. Sci., 2008, 50: 2796
72 Liu D. Corrosion behavior of carbon steel under dynamic supercritical CO2 environment [D]. Wuhan: Huazhong University of Science and Technology, 2015
72 刘 丹. 动态条件下碳钢在超临界CO2环境中腐蚀机理研究 [D]. 武汉: 华中科技大学, 2015
73 Nesic S, Wang S H, Cai J Y, et al. Integrated CO2 corrosion-multiphase flow model [A]. SPE International Symposium on Oilfield Corrosion [C]. Aberdeen: Society of Petroleum Engineers, 2004: 87555
74 Schmitt G A, Mueller M. Critical wall shear stresses in CO2 corrosion of carbon steel [A]. NACE Corrosion 1999 Conference [C]. San Antonio: NACE International, 1999: 44
75 Wei L. Study of corrosion mechanism of steels in supercritical CO2 environments [D]. Beijing: University of Science and Technology Beijing, 2016
75 魏 亮. 钢在超临界CO2环境中腐蚀机制的研究 [D]. 北京: 北京科技大学, 2016
76 Pfennig A, Kranzmann A. Effect of CO2 and pressure on the stability of steels with different amounts of chromium in saline water [J]. Corros. Sci., 2012, 65: 441
77 Li Y X, Liu M S, Zhang J. Impacts of gas impurities on the security of CO2 pipelines [J]. Nat. Gas Ind., 2014, 34: 108
77 李玉星, 刘梦诗, 张 建. 气体杂质对CO2管道输送系统安全的影响 [J]. 天然气工业, 2014, 34: 108
78 De Visser E, Hendriks C, Barrio M, et al. DYNAMIS CO2 quality recommendations [J]. Int. J. Greenhouse Gas Control, 2008, 2: 478
79 McGrail B P, Schaef H T, Glezakou V A, et al. Water reactivity in the liquid and supercritical CO2 phase: Has half the story been neglected? [J]. Energy Procedia, 2009, 1: 3415
80 Mohitpour M, Golshan H, Murray A. Pipeline Design & Construction: A Practical Approach [M]. 2nd Ed., New York: American Society of Mechanical Engineers, 2003
81 Ne?i? S. Key issues related to modelling of internal corrosion of oil and gas pipelines—A review [J]. Corros. Sci., 2007, 49: 4308
82 Nyborg R. Overview of CO2 corrosion models for wells and pipelines [A]. NACE Corrosion 2002 Conference and Expo. 2002 [C]. Denver: NACE International, 2002: 2233
83 Nordsveen M, Ne?i? S, Nyborg R, et al. A mechanistic model for carbon dioxide corrosion of mild steel in the presence of protective iron carbonate films—Part 1: Theory and verification [J]. Corrosion, 2003, 59: 443
84 Ne?i? S, Nordsveen M, Nyborg R, et al. A mechanistic model for carbon dioxide corrosion of mild steel in the presence of protective iron carbonate films—Part 2: A numerical experiment [J]. Corrosion, 2003, 59: 489
85 Ne?i? S, Lee K L J. A mechanistic model for carbon dioxide corrosion of mild steel in the presence of protective iron carbonate films—Part 3: Film growth model [J]. Corrosion, 2003, 59: 616
86 Zhang Y, Gao K, Schmitt G, et al. Modeling steel corrosion under supercritical CO2 conditions [J]. Mater. Corros., 2013, 64: 478
87 Kongshaug K O, Seiersten M. Baseline experiments for the modeling of corrosion at high CO2 pressure [A]. NACE Corrosion 2004 Conference and Expo. 2004 [C]. New Orleans: NACE International, 2004: 4630
88 Thomas D C. Carbon Dioxide Capture for Storage in Deep Geologic Formations [M]. 2nd Ed., Amsterdam: Elsevier Science Ltd, 2005: 937
89 Xiang Y, Wang Z, Xu M H, et al. A mechanistic model for pipeline steel corrosion in supercritical CO2-SO2-O2-H2O environments [J]. J. Supercrit. Fluids, 2013, 82: 1
90 Gunaltun Y M. Combining research and field data for beorrosion rate prediction [A]. NACE Corrosion 1996 Conference [C]. Denver: NACE International, 1996: 96027
91 Nesic S, Nordsveen M, Nyborg R, et al. A mechanistic model for CO2 corrosion with protective iron carbonate films [A]. NACE Corrosion 2001 Conference and Expo. 2001 [C]. Houston: NACE International, 2001: 01040
92 Srinivasan S, Kane R D. Prediction of corrosivity of CO2/H2S production environments [A]. NACE Corrosion 1996 Conference [C]. Denver: NACE International, 1996: 11
93 Srinivasan S, Tebbal S. Critical factors in predicting CO2/H2S corrosion in multiphase systems [A]. NACE Corrosion 1998 Conference [C]. San Diego: NACE International, 1998: 38
94 John R C, Jordan K G, Kapusta S D, et al. SweetCor: an information system for the analysis of corrosion of steels by water and carbon dioxide [A]. NACE Corrosion 1998 Conference [C]. San Diego: NACE International, 1998: 20
95 Anderko A M, Young R D. Simulation of CO2/H2S corrosion using thermodynamic and electrochemical models [A]. NACE Corrosion 1999 Conference [C]. San Antonio: NACE International, 1999: 31
96 Anderko A M. Simulation of FeCO3/FeS scale formation using thermodynamic and electrochemical models [A]. NACE Corrosion 2002 Conference [C]. Orlando: NACE International, 2002: 102
97 Choi Y S, Hassani S, Vu T N, et al. Development of a prediction model for high pCO2 corrosion of mild steel [A]. NACE Corrosion 2019 Conference and Expo. 2019 [C]. Nashville: NACE International, 2019: 13157
98 Duan Z H, Sun R. An improved model calculating CO2 solubility in pure water and aqueous NaCl solutions from 273 to 533 K and from 0 to 2000 bar [J]. Chem. Geol., 2003, 193: 257
99 Duan Z H, Sun R, Zhu C, et al. An improved model for the calculation of CO2 solubility in aqueous solutions containing Na+, K+, Ca2+, Mg2+, Cl-, and SO42- [J]. Mar. Chem., 2006, 98: 131
100 Langmuir I. The adsorption of gases on plane surfaces of glass, mica and platinum [J]. J. Am. Chem. Soc., 1918, 40: 1361
101 Carey J W, Wigand M, Chipera S J, et al. Analysis and performance of oil well cement with 30 years of CO2 exposure from the SACROC Unit, West Texas, USA [J]. Int. J. Greenhouse Gas Control, 2007, 1: 75
102 Carey J W, Svec R, Grigg R, et al. Experimental investigation of wellbore integrity and CO2-brine flow along the casing-cement microannulus [J]. Int. J. Greenhouse Gas Control, 2010, 4: 272
103 Crow W, Williams D B, Carey J W, et al. Wellbore integrity analysis of a natural CO2 producer [J]. Energy Procedia, 2009, 1: 3561
104 Han J B, Carey J W, Zhang J S. A coupled electrochemical-geochemical model of corrosion for mild steel in high-pressure CO2-saline environments [J]. Int. J. Greenhouse Gas Control, 2011, 5: 777
105 Pitzer K S. Activity Coefficients in Electrolyte Solutions [M]. 2nd Ed., Boston: CRC Press, 1991: 75
106 Nesic S, Postlethwaite J, Olsen S. An electrochemical model for prediction of corrosion of mild steel in aqueous carbon dioxide solutions [J]. Corrosion, 1996, 52: 280
107 Li Q, Cheng Y F. Modeling of corrosion of steel tubing in CO2 storage [J]. Greenhouse Gas.: Sci. Technol., 2016, 6: 797
免责声明:本网站所转载的文字、图片与视频资料版权归原创作者所有,如果涉及侵权,请第一时间联系本网删除。
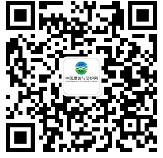
官方微信
《腐蚀与防护网电子期刊》征订启事
- 投稿联系:编辑部
- 电话:010-62316606-806
- 邮箱:fsfhzy666@163.com
- 腐蚀与防护网官方QQ群:140808414