摘要
作为目前主要的电力供应设备和CO2排放场所,随着“碳达峰-碳中和”目标的提出,燃煤发电锅炉逐渐向零碳/低碳排放的生物质发电锅炉和生物质-燃煤混烧发电锅炉方向发展。燃煤及生物质中含硫、含氯组分的腐蚀及磨损行为对锅炉安全长效运行构成严重威胁,因此,沉积防护涂层成为提高锅炉耐蚀耐磨性能的便捷高效手段。本文综述了目前燃煤锅炉、生物质锅炉及生物质-燃煤混烧锅炉基体材料和防护涂层在高温腐蚀及冲蚀磨损方面的研究成果,针对燃煤及生物质燃烧环境,总结了高温硫酸盐腐蚀及碱金属氯化物腐蚀机理,阐述了生物质-燃煤混烧环境中灰沉积-冲击机制,介绍了目前锅炉基体材料的应用现状,归纳了在腐蚀和磨损不同环境下合金涂层、陶瓷涂层、金属陶瓷涂层的设计原则、制备方法及应用现状。指出了当前锅炉防护研究亟待解决的问题,包括:热腐蚀机理研究不深入,缺乏准确的腐蚀-磨损预测模型,防护涂层种类较少。最后,提出采用材料基因组工程及机器学习方法来加速材料研发,开展腐蚀-磨损机理及多因素耦合模型的研究,同时强调粉末合成设计-涂层结构设计-服役性能评价一体化研究对新型防护涂层研发的重要性。
关键词: 硫腐蚀 ; 氯腐蚀 ; 冲蚀磨损 ; 发电锅炉 ; 防护涂层
随着近几十年全球范围内工业化进程的加快,以化石燃料为基础的能源设施得到前所未有的发展,化石燃料的燃烧已使全球每年CO2排放量超过2.4 × 1010 t,这其中一半的CO2排放量来自电力部门[1~4]。截止2016年,燃煤电厂CO2排放量达到3.0 × 1011 t[5,6],大规模的CO2排放造成碳循环失衡,使得全球生态环境问题日益严重[7]。因此,降低CO2排放被各国提上日程[8,9]。
在电力供应方面,我国大力发展非化石能源,加速能源清洁低碳转型,非化石能源消费比重超过15%,可再生能源每年新增装机占比超过50%[9]。截至2019年底,煤电总装机规模为1.04 × 109 kW,可再生能源发电装机达到7.94 × 108 kW,其中水电装机3.56 × 108 kW,风电装机2.1 × 108 kW,光伏发电装机2.04 × 108 kW,生物质发电装机2.254 × 107 kW,分别同比增长1.1%、14.0%、17.3%和26.6%,在运核电机组规模4.874 × 107 kW[9,10]。煤炭作为我国第一大能源,到2050年仍将占一次能源消费比例的35%[11],降低燃煤供电比例将是今后燃煤发电技术的重点研发方向。生物质能作为全球第四大能源,在燃烧过程中释放的CO2量和生长过程中吸收的CO2量相当,使其成为一种CO2中性燃料。因此,具有碳捕获和存储的生物质能被认为是唯一的大规模CO2负排放技术解决方案[12,13],生物质发电成为现有燃煤电厂潜在的可再生能源替代方案而受到世界范围内的广泛关注[14~16]。燃煤耦合生物质发电作为一项成熟且经济可行的CO2减排技术,其不仅可以减少燃煤电厂含硫、含氮烟气的排放[17,18],也可以在保证发电效率的同时提高燃烧效率[19,20]。据统计,全球在运燃煤耦合生物质发电厂已达230余所,且大多数采用生物质-燃煤混烧发电技术[21],这些耦合燃烧电厂主要分布在欧洲和北美,随着巴黎气候协定的生效,多国制定了零煤发电战略,生物质-燃煤混烧已向大容量机组、高比例混烧方向发展,甚至在英国、丹麦、芬兰、加拿大、美国等国出现了纯生物质燃烧发电电厂[22~24]。
煤炭作为我国的主体能源,燃煤发电在未来相当长一段时间仍将是我国主要的电力供应方式,锅炉作为重要的能量转换及碳源转换设备,其稳定运行将关系到能源转型政策下经济社会的平稳发展。同时,我国生物质资源丰富,大力发展生物质-燃煤混烧及生物质直燃技术将是降低煤电装机量的重要途径,国家能源局已于2017年启动生物质混烧发电试点工作[25],合理发展以农林生物质、生物质成型燃料等为燃料的生物质锅炉的推广使用[9],将是我国能源体系平稳发展和过渡转型的重要桥梁。
“锅炉四管”是锅炉组件中重要的热量交换部件,煤炭、生物质等燃料燃烧过程产生的灰渣使管壁受热面长期遭受积灰腐蚀和冲蚀磨损[26~30],管壁变薄引起的爆管事故导致锅炉停机,对电厂发电效率及经济效益产生巨大影响。对于燃煤锅炉,炉管受热面主要遭受含硫煤燃烧形成的硫化物盐腐蚀,同时也存在一些低品位煤及高碱性煤燃烧产生的钒酸盐、氯化物盐腐蚀[31~33],锅炉运行过程中未完全燃烧的煤灰等颗粒物冲刷炉壁也造成高温冲蚀磨损[34~36]。对于生物质锅炉,农作物秸秆等燃烧形成的碱金属氯化物盐容易沉积在低温管壁上形成积灰腐蚀[37~39],同时也存在飞灰等对管壁的冲刷[40~42]。对于生物质-燃煤混烧锅炉,其在运行过程中产生的含硫、含氯、含钒盐等沉积在管壁上造成热腐蚀,同时煤灰和生物质灰也对管壁造成冲蚀磨损[43,44]。目前锅炉基体材料仍然使用以合金特钢、不锈钢等为主的传统金属材料[45~48],同时也有部分使用镍基和钴基等高温合金材料[49~54]。虽然新型合金材料的开发和使用能够在一定程度上提高锅炉在高温环境中的耐蚀耐磨性能,但高昂的成本和整体性能受限仍只能部分应用。鉴于此,使用表面工程技术在锅炉管壁受热面制备高温防护涂层,不仅大大降低爆管泄露引起的安全事故概率,而且能够因减缓受热面灰渣沉积而提高发电效率,因此降低发电锅炉的碳排放。热喷涂技术作为能源领域常用的表面防护涂层制备方法,其主要包括超音速火焰喷涂、等离子喷涂、爆炸喷涂等,可制备涂层涵盖金属、金属陶瓷及陶瓷材料,可满足发电锅炉不同燃烧温度及环境下的耐蚀耐磨要求[55~58]。同时,热喷涂操作工艺简便、沉积效率高、涂层结合强度高、环境污染小,越来越多的研究开始关注热喷涂涂层在高温含硫、含氯环境下的服役性能,也为推广生物质能应用、促进锅炉碳中和转型奠定基础。
本文综述了目前燃煤锅炉、生物质锅炉及生物质-燃煤混烧锅炉基体材料和防护涂层在高温腐蚀及冲蚀磨损方面的研究成果,首先阐述发电锅炉在高温复杂服役环境下的运行现状和失效机理,其次介绍锅炉基体材料目前的发展及应用状况,再次介绍在腐蚀和磨损等不同环境下涂层材料选择及结构设计,然后介绍锅炉防护用合金涂层、陶瓷涂层、金属陶瓷涂层的研究热点及应用现状,最后对防护涂层在腐蚀、磨损方面的研究进行了简要总结,提出了燃煤锅炉、生物质锅炉防护领域目前亟待解决的问题,并对未来发电锅炉防护涂层的发展趋势进行了展望。
1 发电锅炉材料在复杂服役环境下的失效机理
1.1 燃煤锅炉
1.1.1 运行现状
燃煤电厂作为目前主要的电力供应部门,也是工业碳排放的主要来源。为实现“双碳目标”[59],发展更高效率燃煤火电机组技术成为提效降耗的主要途径,超临界、超超临界锅炉发电技术作为国际上先进的燃煤发电技术受到各国关注。将600 MW发电机组蒸汽参数由600℃、25 MPa提高到700℃、35 MPa,发电机组热效率由43%提高至49%,则每年节约标准煤约1.05 × 105 t,CO2排放量降低约2.9 × 105 t[60,61]。然而,蒸汽参数提高将导致包括水冷壁、过热器、再热器、省煤器在内的“锅炉四管”所承受的温度和压力提高,使得锅炉爆管事故发生率增加。图1[57]为发电锅炉“四管”分布示意图。煤炭中S、V等杂质在燃烧过程中产生SO2、SO3、H2S等含硫烟气,对水冷壁造成高温烟气腐蚀[62],高温下与碱金属元素形成硫酸盐、钒酸盐等,在过热器、再热器管壁上积灰、结渣,形成热腐蚀[63,64],省煤器区域烟气流速高、灰质坚硬会对管壁造成严重磨损[65],这些都对锅炉材料高温强度及耐磨耐蚀性能提出了更高要求。
图1 发电锅炉“四管”分布示意图[57]
1.1.2 硫酸盐腐蚀机制
S是一种强氧化性腐蚀剂,其在高温下主要发生2种类型反应[66]:(1) S与燃气反应产生SO2、H2S等气体,形成金属硫化-氧化;(2) SO2、SO3等与其他碱金属形成熔融硫酸盐热腐蚀。
S在高温环境中与O2结合形成SO2,在SO2分压()达到临界值时,Fe、Cr等金属的硫化速率常数都很高,并且比同等条件下的金属氧化反应更快。Cr的硫化速率比相应的氧化速率快4~5个数量级,大多数含Cr耐热合金在富含SO2气氛中难以形成保护性氧化膜,SO2造成的硫化-氧化过程如下[67,68]:
锅炉燃烧过程中,SO2与其他碱金属反应形成Na2SO4、K2SO4等,沉积在材料表面形成热腐蚀。根据盐膜熔点(melting point,Tm)、露点(dew point,Td)以及盐膜组分的影响将热腐蚀分为2类[66,69]:(1) I型热腐蚀:环境温度介于盐膜熔点和露点之间(750~900℃),盐膜呈液态附着在材料表面,液态盐膜作为离子熔体与金属或合金直接发生电化学机制腐蚀,保护性氧化膜在界面处发生溶解-再沉淀过程;(2) II型热腐蚀:环境温度低于盐膜熔点(600~750℃),盐膜呈固态附着在材料表面,当燃烧过程形成混合盐膜或单一盐膜与材料反应形成其他溶质盐时,盐膜呈共晶体系使得熔点下降,保护性氧化膜发生酸性溶解或活化腐蚀使得热腐蚀过程加速。
燃煤锅炉工作温度通常达到900℃以上,燃烧过程中形成的Na2SO4熔点为884℃,材料表面产生以Na2SO4为主的I型热腐蚀[70];部分组件工作温度低于700℃,材料表面形成Na2SO4-MSO4 (M = Ni、Co等)型共晶体系,使熔点降低,材料发生II型热腐蚀降解[70];同时Na3Fe(SO4)3、K3Fe(SO4)3等也使材料表面发生熔盐热腐蚀降解。部分硫酸盐、焦硫酸盐及共晶盐熔点如表1[63,71]所示。硫酸盐腐蚀过程如下[67]:
表1 部分硫酸盐、焦硫酸盐及共晶盐的熔点[63,71]
材料表面形成的保护性氧化膜,如NiO、Cr2O3、Co3O4、Fe2O3等,与熔盐接触会发生电化学腐蚀溶解失效。熔融Na2SO4的相对酸度/碱度决定了腐蚀产物的热力学平衡浓度及腐蚀反应速率,如式(5)中Na2SO4-Na2O-SO3所示反应,Na2SO4熔盐酸/碱度类似水解离成酸/碱离子的pH测量,Na2SO4熔盐中Na2O作为碱性标识物,SO3作为酸性标识物,酸/碱度计算公式如下[63]:
式中,a为活度系数,为Na2SO4标准Gibbs自由能,R为理想气体常数,T为反应温度。
金属氧化物在熔融Na2SO4中的溶解度和溶解机理取决于
标识的熔盐酸碱度[63],高于8.4为碱性熔体,低于8.4为酸性熔体。文献[72~76]中计算了NiO、Cr2O3、Co3O4、Fe3O4、Al2O3在1200 K纯Na2SO4熔体中的酸/碱度函数,氧化物的碱性溶解如式(14)~(16)所示,酸性溶解如式(17)~(19)所示[63]:
图2[63]为熔融硫酸盐诱导热腐蚀示意图。在热腐蚀初期,燃烧形成的硫酸盐附着在金属基体表面,同时基体材料表面形成保护性氧化膜(图2a[63]);随着热腐蚀进行,硫酸盐熔化成盐膜覆盖在基体表面,阻隔基体与气相接触(图2b[63]);熔融盐膜通过活性部位如缝隙、孔洞、晶界缺陷等处不断渗入并溶解保护性氧化膜,形成金属硫化物或金属硫酸盐(图2c[63]);热腐蚀后期,熔盐同时与基体材料、氧化膜反应形成电化学机制不均匀腐蚀,加速材料失效(图2d[63])。
图2 熔融硫酸盐诱导热腐蚀示意图[63]
燃煤中其他杂质(如V)在燃烧过程中产生酸性V2O5,同时V2O5与Na2SO4形成碱性NaVO3:
Na2SO4-V2O5/Na2SO4-NaVO3形成共晶熔盐[77],低温下加速材料失效。产生的SO3使得熔盐/氧化物界面氧活性降低,使得Cr2O3、Al2O3等氧化物分解,失去保护性。Montero和Galetz[78]也发现,在高Cr、Al含量合金中,Cr、Al与V2O5反应形成CrVO4、AlVO4,使得合金元素被消耗而产生严重内硫化。
1.1.3 磨损机制
燃煤锅炉烟气中含有大量煤灰、飞灰等硬质颗粒,随烟气流动对锅炉受热面造成磨损,其显著特点是磨损区域不均匀,通常只出现在过热器、再热器烟气入口处以及省煤器烟气侧。据统计,因锅炉受热面磨损造成的爆管事故占锅炉运行总事故的45%~50%[65],44%的电厂都受到省煤器磨损问题影响[79]。由于锅炉运行过程中受热面磨损受到燃煤品质和运行参数的影响而具有不确定性,最早由美国电力研究协会(EPRI)提出燃煤锅炉总体磨损性数学模型(式(21)[80]),为描述磨损严重程度提供了量化借鉴。
式中,fE为煤灰总体磨损性,IC为煤的磨损性系数,fBO为锅炉运行因素对总体磨损性的影响系数。
在锅炉总体磨损模型基础上,研究人员提出了不同方法和模型来预测燃煤锅炉磨损特性。Jin等[81]使用浸入边界法进行直接数值模拟,研究了粒子对管道近侧壁和侧壁的碰撞和磨损,粒子Stokes数为0时,粒子为完全示踪剂跟随流体运动,当Stokes数较大时,粒子惯性主导运动,随着Stokes数增大,近侧壁侵蚀更加严重,而侧壁较高的碰撞频率导致较低的侵蚀。Orumbayev等[82]给出了单个球型粒子运动方程并提出粒子群均方速率模型,通过粒子向下运动时的最大均方根速率计算磨损量,当烟气速率达到10 m/s时,粒子向上移动而使磨损率下降10%~15%。除粒子运动对磨损的影响外,不同材料在侵蚀环境下的性能也影响总体磨损率。Singh和Mishra[83]研究了SAE 208、SAE 213-T12和SAE 213-T91的抗冲蚀性能,高硬度和高Cr含量的SAE 213-T12和SAE 213-T91在室温和400℃环境下都具有较好的抗冲蚀性能。Sagayaraj等[84]研究了煤灰粒度、速率、冲击角度对退火和未退火处理的SA210GrA1的侵蚀作用,在相同煤灰粒度和速率情况下,冲击角度为30°时材料磨损率最大,退火处理后材料抗冲蚀性提高。Yun等[85]研究了氧化膜对Alloy 690在蒸汽环境下磨损的影响,随着氧化时间增加,Alloy 690磨损率随表面形成的Cr2O3膜厚度增加而减小。由于燃煤锅炉磨损复杂性,冲蚀-磨损相关研究较少,且模型计算值和实验测定值仍存在差距,磨损机制仍需进行深入研究。
1.2 生物质锅炉
1.2.1 运行现状
目前中国70%的电力由燃煤电厂提供,为实现中国2060年碳中和目标,推广生物质锅炉发电势在必行[86]。生物质作为碳中和能源,根据来源可分为4类:(1) 木质生物质,包括森林残留物(树木、枯叶等)、景观美化残留物(盆栽等)及工业木材残留物(木屑等);(2) 农业生物质,包括农作物秸秆、农业收获残留物、食品工业残留物及草原草甸;(3) 废弃物,包括城市固体废弃物、商业垃圾及建筑垃圾;(4) 粪便,包括畜牧场浆液/粪便和家庭及工业有机废物[29]。生物质锅炉在燃烧过程中,炉内烟气温度可达650~1050℃,锅炉受热面温度可达450~600℃[87],K、Cl等碱金属元素以气相KCl形式存在于烟气中,当气相KCl遇到温度较低的锅炉管受热面时会凝结形成积灰,生物质中其他杂质(如Si、S等)易与KCl形成低温共晶熔体,这些都会造成严重热腐蚀(图3[29]),使锅炉发生爆管泄露事故,同时积灰也使管壁导热性下降,降低电厂发电效率[88,89]。
图3 生物质锅炉管壁积灰腐蚀[29]
1.2.2 KCl熔盐热腐蚀机制
KCl熔点为770℃,高温下容易与金属及合金反应形成熔点较低的金属氯化物(MClx,M = Fe、Cr、Al等)及尖晶石相,从而使共晶温度降低,例如,KCl-FeCl2与KCl-K2CrO4共晶熔点分别为355和650℃[90],共晶熔体使材料表面发生不均匀II型热腐蚀。根据热腐蚀温度不同,目前主流的KCl热腐蚀机制主要分为“电化学机制”过程和“氯活化氧化”过程[91,92]。
当环境温度满足I型热腐蚀条件时,KCl处于熔融态,Cl-可以通过金属或合金表面早期形成的薄且致密的氧化膜向内扩散,与合金成分反应形成MClx,MClx具有较大的平衡蒸气压,容易向氧化层/界面扩散,在界面处与O2反应形成不具有保护性的氧化物颗粒,同时产生Cl2,向内扩散,再次与合金反应形成MClx,使得材料因发生氯腐蚀循环而失效,反应如式(22)~(24)[92]所示。同时熔融态KCl在热力学上也更倾向于与Cr2O3反应,从而使氧化膜失去保护作用[93],反应如式(25)[92]所示。
当环境温度满足II型热腐蚀条件时,热腐蚀初期KCl以固态形式存在,金属或合金热腐蚀速率较低,当合金表面氧化产生的Cr2O3缓慢与KCl反应形成K2CrO4后,KCl-K2CrO4形成低温共晶熔体使热腐蚀过程加速,随着反应进行,KCl-MClx共晶盐进一步加速热腐蚀过程。热腐蚀后期材料同样遭受氯腐蚀循环,材料内部的合金成分被不断消耗而失效。
KCl熔盐诱导的热腐蚀过程示意图如图4所示。在热腐蚀初期,KCl盐膜附着在基体表面,同时基体材料表面氧化形成氧化膜;在热腐蚀中期,若环境温度高于KCl盐膜熔点,KCl熔体中Cl-通过氧化膜晶界及孔隙等缺陷向内扩散,直接与基体材料发生电化学机制腐蚀,形成金属氯化物。若环境温度低于KCl盐膜熔点,KCl与氧化物缓慢反应形成尖晶石相及Cl2,部分Cl2通过氧化膜晶界及孔隙向内扩散发生氯活化氧化,形成金属氯化物,同时KCl盐膜与产生的尖晶石相形成低熔点共晶熔体,Cl-扩散速率比Cl2更高,其与基体材料发生电化学机制腐蚀,使低温热腐蚀过程加速;在热腐蚀后期,金属氯化物向外扩散与O2形成不具保护性的氧化物颗粒,同时释放Cl2,Cl2再次与金属及合金元素反应形成金属氯化物,基体材料发生连续的氯化-氧化过程使金属元素被不断消耗而失效。
图4 KCl熔盐诱导的热腐蚀过程示意图
为了进一步理解生物质腐蚀环境下金属和合金表面氯活化氧化过程,吕泽康等[94]通过量子化学密度泛函理论(density functional theory,DFT)从分子水平研究了FeCl2与O2的反应过程及中间产物,Cl原子从中间体Cl2Fe2O2脱离形成Cl2的过程主要通过迁移过程实现,通过控制反应温度使Cl原子迁移能低于反应能垒,从而降低锅炉过热器腐蚀,这为揭示金属氯化物活性腐蚀过程提供了新思路。
1.3 生物质-燃煤混烧锅炉
1.3.1 运行现状
目前生物质直燃发电技术应用主要集中在农业大省,且高度依赖燃料供应的持续性和经济性,生物质分散、能量密度低、收集运输困难等都直接影响生物质发电运行成本,使得生物质直燃发电综合效率低于30%,又由于生物质锅炉机组及配套设施建造周期较长,生物质直燃发电电厂增速缓慢。燃煤锅炉大容量、高蒸汽参数等优势使得生物质与燃煤混烧发电成为保证电力供应同时低碳排放的便捷途径。国际研究普遍表明,当生物质燃料占总混烧燃料比例低于20%时,只需对燃煤锅炉进行微小改造甚至不需要改造就可以直接进行混烧发电[86,95]。然而,生物质中碱金属与燃煤中S等元素在燃烧时将同时受到2种燃料的共同影响,使得灰质成分变得更加复杂。
1.3.2 腐蚀-磨损机制
生物质-燃煤混烧过程中,灰质在锅炉管壁上主要发生沉积-冲击作用,由此对管壁造成腐蚀-磨损效应。根据颗粒尺寸、浓度、灰质化学成分、局部条件和表面条件,将灰质沉积-冲击分为惯性撞击、热迁移、凝结扩散、化学反应过程,相应的机制如图5[43]所示。惯性撞击取决于粒子跟随气流的惯性力以及粒子自身Stokes数。热迁移过程发生在灰颗粒通过自由流动气体时,由于温度梯度引起的热渗透作用力而影响灰质沉积方向。凝结扩散过程主要针对燃煤、生物质燃烧初期,硫酸盐、碱金属氯化物在低温管壁凝结形成积灰。化学反应过程包括氧化反应、硫化反应、碱金属反应等[29,43]。
图5 生物质-燃煤混烧锅炉受热面灰沉积-冲击机制示意图[43]
2 发电锅炉基体材料的选择及发展
2.1 传统锅炉钢
针对超临界、超超临界锅炉高温高压及腐蚀环境,在传统的20G、12CrMoVG等锅炉钢的基础上[96],研究人员[62,97,98]在钢中添加Ti、W、Cu等合金元素,研制出T24、T92、Super304H等具有良好抗腐蚀和抗高温蠕变性能的钢种。Zhao等[98]研究发现,在H2S环境中T23和T24发生快速的热腐蚀过程,W具有显著的抗H2S腐蚀性。Wright和Dooley[99]研究发现,TP304、TP347等奥氏体不锈钢在高温环境中氧化速率随着Cr含量的升高而减慢,保护性氧化行为缓解了锅炉管表面产物脱落造成的失效。Hussain等[100]研究发现,T92、347HFG、HR3C在不同温度SO2/SO3烟气环境下具有相似的质量损失率,然而在富氧燃烧环境下3种材料质量损失率随着Cr含量升高而降低。不同锅炉钢元素含量及作用见表2[62,96~100]。
传统锅炉钢作为发电锅炉首选基体材料,未来仍将继续发挥其不可替代作用。一般在材料表面形成的氧化性保护膜,对提升材料耐蚀耐磨性能起到重要作用,通过提高锅炉钢中Cr含量同时添加一些有益合金元素(如Ti、W、Cu等)可进一步提高锅炉钢性能及服役寿命。
2.2 高温合金
针对燃煤锅炉和生物质锅炉高硫、高氯腐蚀及磨损环境,锅炉基材除了使用传统锅炉钢,也使用高温合金作为基体材料,部分高温合金成分见表3[101~104]。对于燃煤锅炉,尤其对于高参数超超临界锅炉的过热器及再热器管材,目前国内外较多使用高温合金来保证锅炉管烟气侧具有较好的抗热腐蚀性能[105]。Goyal等[101]研究发现,以Superfer 800H、Superco 605、Superni 75为代表的铁基、钴基、镍基高温合金在Na2SO4 + 60%V2O5 (质量分数)热腐蚀环境下具有不同的增重速率,钴基合金由于表面形成的Co3O4容易产生酸性溶解使得保护性氧化膜无法形成,因此其热腐蚀增重量最大;铁基合金增重次之,其表面形成的Fe2O3与熔盐发生互扩散而产生剥落,腐蚀介质通过裂纹与金属基体接触产生灾难性氧化;镍基合金热腐蚀增重最小,表面形成的Cr2O3与Ni(VO3)2作为扩散屏障降低了腐蚀介质扩散速率,高铬高温合金对于燃煤锅炉硫酸盐腐蚀具有较好保护性。对于生物质锅炉,Israelsson等[106]研究了FeCrAl合金在O2 + H2O + KCl环境中的热腐蚀性能,快速的K2CrO4形成过程使Cr2O3被耗尽,同时触发Fe的快速氧化过程,KCl环境中铁基合金抗热腐蚀能力较弱,高Cr含量合金对于高温Cl腐蚀保护效果不明显。为提高生物质锅炉用高温合金的抗高温氧化及腐蚀性能,一方面研究人员使用前/后处理来提高合金高温性能,如Okoro等[107]研究了预氧化处理对镍基合金热腐蚀性能的影响,发现未处理合金外层形成Ni、Cr氧化物,内层形成Ti、Al氧化物,Cr2O3与KCl反应失去保护性,预氧化处理后合金外层形成TiO2,能有效阻挡KCl向内扩散;另一方面研究人员在高温合金中加入Si、Ni、Nb等成分研究其对高温氧化及腐蚀性能的影响,如Klein等[108]在Co-9Al-9W-B中添加不同含量Ni、Si,结果表明,添加Ni会使得晶界及氧化物层中B消失,阻碍了Al2O3的形成,使得抗氧化性下降,而在氧化物/合金界面、晶界和沉淀物内的含Si相可以进一步提高合金抗氧化性,但有可能降低合金力学性能。Weng等[109]在镍基合金中添加Nb后,合金表面形成致密的Nb2O5,使得抗热腐蚀性能显著提高。Birol[104]发现高温环境下X32CrMoV33锅炉钢的显微硬度下降幅度达到50%,而Inconel 617和Stellite 6的显微硬度下降幅度较小,高温服役环境下高温合金具有更好的力学性能。
表3 锅炉用部分高温合金成分[101~104] (mass fraction / %)
目前高温合金较多使用在超临界、超超临界燃煤锅炉中,镍基合金表现出较好的耐硫酸盐腐蚀性能,钴基合金和铁基合金对于硫酸盐环境防护效果较差。在生物质锅炉高温氯腐蚀环境中,合金中高Cr含量对氯腐蚀防护性能提升不利,适用于生物质锅炉的高温合金还有待深入研究。
3 发电锅炉防护涂层材料及结构设计
为了降低“锅炉四管”等高温部件腐蚀及磨损速率,延长锅炉服役寿命,使用热喷涂技术在锅炉受热面沉积防护涂层,在一定程度上可以防止燃料中S、Cl以及其他沉积物对基材的攻击。本文介绍针对不同服役环境下热喷涂防护涂层材料的选择及结构设计。
3.1 耐热腐蚀涂层设计与制备
3.1.1 涂层成分及结构设计
耐热腐蚀涂层成分及结构设计原则应该满足以下6点要求[110~112]:(1) 涂层本征结构致密,涂层内部孔隙、裂纹等缺陷较少;(2) 涂层在高温环境中表面能够形成热力学稳定的保护相,如Al2O3、Cr2O3、SiO2等保护相以及一些尖晶石相;(3) 形成的保护相能够缓慢生长,使保护性元素在涂层表面处于低消耗水平;(4) 氧化物层、涂层及基体之间热膨胀系数应尽可能接近,减少由于热应力变化引起的涂层与氧化物层剥落;(5) 涂层与基体之间应该具有较高的结合强度,可以通过制备黏结层来实现;(6) 涂层与基体之间应该具有缓慢的相互扩散过程,可以通过设计多层结构引入扩散屏障来实现,或者通过对基材和涂层进行前/后处理来实现。
3.1.2 涂层制备与热腐蚀性能
不同热喷涂技术的主要区别在于火焰温度和粒子飞行速率,2者直接影响粉末熔化程度以及涂层结合强度和孔隙率。锅炉防护领域常用热喷涂技术有电弧喷涂(arc spray,AS)、等离子喷涂(plasma spray,PS)、爆炸喷涂(detonation gun spray,D-gun)、超音速火焰喷涂(high velocity oxygen/air-fuel spray,HVOF/HVAF)以及冷喷涂(cold spray,CS),各技术比较见表4[32,113]。本工作总结了近10年来锅炉防护领域涂层所使用的热喷涂技术,超过40%的防护涂层都使用超音速火焰喷涂技术制备(图6),这是由于在较高的火焰温度和粒子飞行速率条件下,粉末熔化更充分且以较高的速率撞击基材形成高结合强度、低孔隙率的涂层,使其具有更好的服役性能。表5[105,114~123]、表6[124~131]、表7[132~138]分别列举了目前锅炉防护领域常见的合金涂层、陶瓷涂层、金属陶瓷涂层并对其热腐蚀性能进行比较。
表4 锅炉防护领域热喷涂技术比较[32,113]
图6 相关热喷涂技术在锅炉防护领域使用比例
表5 不同合金涂层热腐蚀性能比较[105,114~123]
表6 不同陶瓷涂层热腐蚀性能比较[124~131]
表7 不同金属陶瓷热腐蚀速率比较[132~138]
耐热腐蚀涂层根据保护性氧化膜类型分为Cr2O3形成涂层、Al2O3形成涂层、SiO2形成涂层,致密性氧化膜阻挡了熔盐中S、Cl等向内扩散,同时减少合金元素与熔盐及大气接触,降低合金元素消耗。下面列出了目前较常用的耐蚀性涂层及一些提高涂层耐蚀性的新方法。
(1) Cr2O3形成涂层。NiCr涂层作为目前主要的高温防护涂层,其形成的Cr2O3以及一些尖晶石相能有效阻挡腐蚀介质向内扩散。Wang等[114]及Cheng等[122]发现,在NiCr涂层中提高Cr含量、降低Ni/Cr比可以提高Cr2O3、NiCr2O4膜致密性,进而有效阻挡腐蚀介质的扩散。研究人员[115,116]在FeCrAl、FeCrNiMoSi涂层中添加Al、Mo、Si等元素,促进了Cr2O3的形成,从而提高了涂层耐硫酸盐腐蚀性能。此外,使用不同制备方法也对涂层耐腐蚀性能产生影响,Sundaresan等[139]使用D-gun制备的CoCrAlY、NiCoCrAlY、NiCr涂层比相同条件下使用PS制备的涂层结构更致密、孔隙率更低、显微硬度更高,涂层在热腐蚀环境中具有更短的瞬态氧化阶段,提高了涂层抗热腐蚀性能。
(2) Al2O3形成涂层。NiCrAlY作为最经典的高温防护涂层,其表面形成致密Al2O3氧化膜,可以有效抵挡硫酸盐腐蚀[120]。然而当涂层中有Cr2O3形成时,Cr2O3与氯化物熔盐形成的活化氧化过程会导致表面致密的Al2O3发生严重氯化过程,失去保护性,Cl、O扩散使涂层发生严重内氧化从而使涂层失效[140]。Sadeghimeresht等[123]发现,Al2O3形成涂层相比于Cr2O3形成涂层具有更好的耐KCl熔盐腐蚀性能。同时,Chawla等[117]使用PS技术首先在铁基合金表面制备出TiAl、AlCr涂层,然后将涂层置于650℃ N2环境中氮化3 h,分别得到TiAlN、AlCrN涂层,氮化后涂层孔隙率下降,在硫酸盐环境中,TiAlN表面形成的Al2O3、TiO2相比于AlCrN表面产生的Al2O3、Cr2O3具有更好的抗热腐蚀性。
(3) SiO2形成涂层。NiCrBSi作为代表性的含Si涂层,热腐蚀过程中涂层表面形成热力学稳定的SiO2相,可以有效抵挡硫酸盐的硫化氧化过程[118]。同时,Sadeghimeresht等[92]发现,在KCl腐蚀环境中,NiCrMoSi涂层中形成的SiO2与SiCl4具有缓慢的转化过程,降低了Cl的腐蚀速率。Zhang等[141]在CoCrAlY中添加Si后,促进了Al2O3保护膜的形成,同时涂层中形成的低溶解度CrSi相限制了硫化物的形成,降低了涂层内氧化速率。
陶瓷涂层,如Cr2O3、Al2O3、ZrO2-8Y2O3等,作为优良的抗腐蚀材料,在锅炉领域也具有应用前景。目前陶瓷涂层主要制备方法有PS和D-gun,虽然陶瓷涂层具有优良的抗热腐蚀性能,但其与基体材料结合强度低且热膨胀系数不匹配,导致涂层在高温腐蚀环境中容易发生断裂而失效[124~126]。目前主要通过引入金属黏结层,如NiCr涂层,来提高陶瓷涂层的结合强度[127~129],延长涂层服役寿命。同时,Goyal等[130]及Kumar等[131]使用低能球磨方法在Al2O3、ZrO2-Y2O3中加入碳纳米管(carbon nanotube, CNT),CNT在热腐蚀过程中深入陶瓷裂纹和微孔,大幅度提高涂层耐蚀性能,为陶瓷涂层在锅炉领域的应用提供了新的思路。
除了传统的合金涂层和陶瓷涂层,金属陶瓷涂层兼具合金相的强韧性和陶瓷相的高温稳定性,成为锅炉防护涂层未来重点发展方向。Cr3C2-NiCr作为传统的金属陶瓷涂层已得到广泛应用[132,137],但Cr3C2相在喷涂过程中容易脱C而失去保护性能[142]。因此,目前研究人员开始关注其他合金及氧化物、碳化物、硼化物等添加相对涂层热腐蚀性能的影响。Mudgal等[132]使用球磨法在Cr3C2-NiCr中添加CeO2,在Na2SO4和NaCl腐蚀环境中,CeO2向涂层表面富集形成致密氧化层,由于稀土离子向氧化物晶界的扩散阻塞了合金元素扩散路径,使得涂层合金元素消耗降低,进而降低涂层热腐蚀增重。Ahuja等[133]发现在Cr3C2-NiCr中加入Zr元素,形成钉扎效应,提高了涂层抗热腐蚀性能。Singh等[135]在Ni-20Cr中添加TiC及Re,结果表明,热腐蚀过程中形成了NiTiO3,降低了涂层表面氧化速率,同时Re在涂层中稳定存在,未发生氧化,阻碍了S、O等的内扩散。吴姚莎[138]在NiCrBSi涂层中添加TiB2制备出纳米NiCrBSi-TiB2涂层,热腐蚀过程中形成的TiO2、SiO2相提高了涂层抗热腐蚀性能。本文作者开展了镍基-硼化物金属陶瓷粉末及涂层的制备研究。采用机械球磨及喷雾造粒法成功制备了NiCrBSi-ZrB2粉末,粉末成分均匀、流动性好,并使用HVOF技术制备了NiCrBSi-ZrB2金属陶瓷涂层,所制备涂层结构致密、孔隙率低、结合强度高。粉末及涂层制备方法如图7所示。NiCrBSi-ZrB2涂层热腐蚀及高温磨损性能如图8所示。添加40%ZrB2涂层在700℃、KCl熔盐环境中表现出明显优于传统NiCrBSi涂层的热腐蚀抗性,形成的热腐蚀层外侧为尖晶石相,内侧为非晶态SiO2相,同时涂层/界面侧形成一层连续的富Zr层,SiO2层和富Zr层阻挡了Cl、O内扩散过程,涂层热腐蚀增重明显降低。同时采用球盘摩擦磨损实验测试了涂层700℃高温磨损性能,添加ZrB2后涂层显微硬度明显升高,涂层中形成的CrB相降低了涂层磨损量,添加40%ZrB2涂层表现出优异的耐磨性能。
图7 NiCrBSi-ZrB2金属陶瓷粉末及涂层制备方法示意图
图8 NiCrBSi-ZrB2涂层热腐蚀及高温磨损性能
此外,研究人员通过后处理来改善涂层缺陷,进一步提高涂层耐蚀性能。Chatha等[137]使用封孔、热处理方法提高Cr3C2-NiCr涂层致密性,降低涂层裂纹和孔洞等缺陷对腐蚀介质的输运而提高耐蚀性。Cai等[143]使用大电流脉冲电子束对PS制备的CoCrAlY涂层进行辐照处理,未熔颗粒重新熔化凝固使涂层表面光滑致密化且晶粒细化,诱导处理后表面形成连续致密的Al2O3层并使其在瞬时腐蚀过程中自愈合,提高了涂层的耐腐蚀性能。
3.2 耐冲蚀磨损涂层设计与制备
3.2.1 涂层成分及结构设计
耐冲蚀磨损涂层成分及结构设计原则应该满足以下4点要求[57,144,145]:(1) 涂层具有较高的显微硬度,可以制备陶瓷涂层或在合金涂层中添加陶瓷相来提高涂层显微硬度,如添加氧化物、碳化物、硼化物陶瓷等相;(2) 涂层与基体之间应该具有较高的结合强度,尤其对于陶瓷涂层,可以通过制备金属黏结层来提高结合强度;(3) 涂层在高温环境中表面能形成硬质相或润滑相,降低涂层磨损率;(4) 陶瓷涂层及金属陶瓷涂层应选择兼具高导热系数和高硬度的陶瓷相作为涂层成分,在保证锅炉导热性的同时提高其耐冲蚀磨损性能。
3.2.2 涂层制备与冲蚀磨损性能
锅炉中的磨损问题主要是由硬质灰颗粒以不同角度撞击材料造成的冲蚀磨损,这要求涂层具有较高的显微硬度和结合强度,同时涂层应具有低孔隙率来抵挡含硫、含氯烟气及熔盐的热腐蚀。由于模拟锅炉冲蚀实验的复杂性,涂层材料的冲蚀磨损评价指标尚无统一标准,目前主要通过实验室模拟冲蚀实验和实际锅炉运行环境挂片实验来表征材料的冲蚀磨损性能,实验室条件下涂层冲蚀磨损率(erosion wear rate)为涂层冲蚀磨损质量损失与冲蚀粒子质量之比[146],根据冲蚀环境和冲蚀时长,也采用厚度损失(thickness loss)、体积损失(volume loss)、质量损失(weight loss)来表征涂层耐冲蚀磨损性能。不同涂层冲蚀磨损率比较如表8[146~153]所示。
表8 不同热喷涂涂层冲蚀磨损率比较[146~153]
目前以Cr3C2-NiCr、WC-12Co为代表的碳化物金属陶瓷涂层广泛应用于磨损、腐蚀等侵蚀环境中[154],然而Cr3C2陶瓷在高温下容易脱碳分解,使材料硬度下降[142],制约其在锅炉领域的应用。研究人员也开始关注其他碳化物、氧化物、硼化物陶瓷添加对涂层耐磨性的影响。Bala等[151]在NiCr中添加TiC和Re促进了Cr2O3保护膜的形成,在实际锅炉腐蚀-冲蚀交互作用环境中,致密的Cr2O3膜提高了涂层耐腐蚀-冲蚀性能。Praveen等[146]在NiCrBSi中添加Al2O3提高了涂层显微硬度,同时Al2O3在涂层中起到了钉扎和屏蔽效应,减弱了冲蚀粒子对镍基软质相的剪切作用,使涂层在30°冲蚀角作用下冲蚀磨损率比无涂层保护基材降低2.5倍。Wu等[155]使用高能球磨法在NiCrBSi中添加TiB2陶瓷相制备了纳米结构NiCrBSi-TiB2涂层,球盘摩擦磨损实验结果表明,NiCrBSi-TiB2磨损率比相同条件下NiCrBSi涂层降低1个数量级,纳米涂层高的断裂韧性降低了涂层硬质相和软质相的分离,提高了涂层耐磨性。研究人员也关注了其他合金涂层(如NiCrAlY、Stellite 6等[148,150])及陶瓷涂层(如Al2O3-3TiO2等[153])的耐冲蚀性能,虽然其具有较低的冲蚀磨损率,但合金涂层较低的显微硬度及陶瓷涂层较低的结合强度限制了其在锅炉领域的应用。
4 防护涂层在发电锅炉领域的典型应用
为实现“双碳目标”,在现有燃煤锅炉的基础上,生物质及生物质-燃煤混烧锅炉开始大范围推广应用,这对锅炉材料耐蚀耐磨性能提出了更高的要求。由于新型高温合金研发周期长且整体应用的成本较高,在现有锅炉钢材料上直接应用防护涂层以提高材料高温耐蚀耐磨性能,成为锅炉防护的首选方法。研究人员通过大量模拟实验,在已有的涂层制备、腐蚀及磨损机理研究基础之上,越来越多防护涂层被开发并应用到发电锅炉领域。针对燃煤锅炉、生物质锅炉及生物质-燃煤混烧锅炉不同的服役环境,以下列举了3种锅炉典型防护涂层应用。
4.1 燃煤锅炉
燃煤锅炉烟气温度通常可以达到900℃以上,同时燃煤中硫酸盐腐蚀和颗粒磨损在高温下造成的协同效应更容易导致锅炉管管壁减薄而发生爆管事故。燃煤锅炉不同部位实际运行工况存在较大差异,水冷壁主要受到高温烟气及一些黏结性灰渣造成的热腐蚀,过热器及再热器管壁容易发生熔盐积灰腐蚀,省煤器部位由于烟气流速大且含有较多灰渣等硬质颗粒容易造成冲蚀磨损,因此在不同部位需制备不同防护涂层来提高锅炉服役性能。对于以腐蚀为主的服役环境如水冷壁、过热器、再热器,选择金属涂层作为防护涂层,而对于磨损及冲蚀为主的服役环境如省煤器,主要选择金属陶瓷涂层或陶瓷涂层作为防护涂层。以印度旁遮普省Guru Gobind Singh超级热电厂为例,研究人员已经使用HVOF在燃煤锅炉低温过热器表面沉积NiCrAl涂层,在700℃环境中运行1000 h后涂层表面没有出现明显的结垢和断裂现象[156]。在540℃低温一级过热器表面沉积NiCrAlY涂层,经过1000 h腐蚀-冲蚀后涂层未出现明显减薄,表面形成的高硬度Cr2O3和Al2O3相抵御飞灰冲蚀磨损效果明显[148]。此外,研究人员[134]也将Cr3C2-NiCr-(WC-Co)涂层用于低温过热器中部位置冲蚀-腐蚀的防护,Cr2O3、NiCr2O4及NiWO4使涂层具有较好的服役性能,涂层服役1500 h后仍保持完整结构。我国也在燃煤锅炉防护领域开发出适用于不同煤炭品位的防护涂层,以新疆准东660 MW燃煤锅炉为例,研究人员[157]开发出ZrO2-CeO2-La2O3纳米陶瓷涂层用于准东燃煤锅炉水冷壁热腐蚀防护,锅炉长时间运行后陶瓷涂层能有效降低煤中S、Cl腐蚀介质对基材的侵蚀,减少灰渣在管壁的黏结富集,明显提高了锅炉管服役寿命。NiCrAlY基涂层、ZrO2等陶瓷涂层及Cr3C2-NiCr系列涂层在燃煤锅炉中都显示出优异的耐蚀耐磨性能。
4.2 生物质锅炉
碱金属氯化物腐蚀造成的生物质锅炉材料损失高居三类锅炉之首,尤其是锅炉水冷壁长期遭受高温含Cl腐蚀性气体及KCl熔盐造成的热腐蚀,容易产生爆管等安全事故,而Cr2O3和Al2O3对氯腐蚀抵御效果不明显。自熔性合金涂层(如NiCrBSi涂层)由于其结构均匀致密、结合强度高、不与基体发生互扩散,日本三菱重工业公司成功将NiCrBSi涂层应用于生物质锅炉水冷壁防护,涂层表面形成的SiO2保护层耐氯腐蚀作用明显,锅炉材料从未涂覆涂层的每年减薄1 mm降低到涂覆涂层后的3年减薄0.1~0.2 mm[158],延长了锅炉管壁服役寿命。芬兰皮耶塔尔萨里Alholmens Kraft电厂550 MW 循环流化床锅炉作为世界上最大的生物质锅炉之一,研究人员将NiCr及FeCr涂层用于750℃过热器区域热腐蚀防护,涂层服役5900 h后失效,2种涂层耐氯腐蚀性能都较差,FeCr具有更高的腐蚀速率[159]。总体来看,NiCrBSi基涂层是目前生物质锅炉防护的首选材料。
4.3 生物质-燃煤混烧锅炉
生物质-燃煤混烧发电作为未来生物质发电最具前景的方向,其中,解决生物质-燃煤混烧锅炉腐蚀-冲蚀问题成为该技术推广的关键。CoCrWC (Stellite 6)涂层具有较高的显微硬度和耐腐蚀性能,瑞典奈舍生物质电厂使用Stellite 6涂层作为630℃低温生物质-燃煤混烧锅炉过热器防护涂层,锅炉运行2100 h后依然表现出较好的耐腐蚀-冲蚀性能[160],同时该涂层也应用于860℃高温无烟煤-秸秆混烧锅炉过热器中,锅炉运行1630 h后也表现出优异性能,形成的Cr2O3和CoCr2O4耐腐蚀-冲蚀作用明显[161]。除了金属涂层较常用于生物质-燃煤混烧锅炉防护外,Cr3C2-NiCr涂层在硫酸盐-氯化物盐存在下也表现出较好的耐腐蚀性能,然而高温下碳化物容易分解导致Cr等保护性元素消耗速率加快,不利于涂层长期服役[132]。
总体来看,目前燃煤锅炉及生物质锅炉防护领域广泛采用的涂层以金属涂层及金属陶瓷涂层为主,生物质-燃煤混烧锅炉发展较晚,相应的防护涂层使用较少。为降低碳排放,研发适用于生物质及生物质-燃煤混烧锅炉防护涂层将是未来锅炉防护领域重点发展方向。
5 发电锅炉防护涂层研究展望
随着近年来“碳达峰-碳中和”目标的提出,电力领域以燃煤发电为主的局面开始向燃煤发电、生物质发电、生物质-燃煤混烧发电多极发展的趋势逐渐转变,这也促进了对锅炉高温防护涂层材料及腐蚀-磨损机理的深入研究,发电锅炉防护涂层逐渐从模拟实验转向实际应用。本文就锅炉运行环境下材料腐蚀-磨损机理、锅炉材料发展及防护涂层研究应用现状做了评述。由于锅炉燃烧环境的复杂性,锅炉防护领域仍存在一些问题亟待解决,同时随着材料研究新技术的发展,涂层材料研发也出现一些新方法和新思路。
5.1 存在问题
目前防护涂层热腐蚀及磨损性能评价主要在实验室模拟环境下进行,热腐蚀介质、颗粒侵蚀条件、温度条件、实验时间均与锅炉实际运行环境存在差异,涂层失效机理及材料研发主要有以下3方面的问题:
(1) 热腐蚀机理研究不深入。由于热腐蚀实验周期较长,大多数研究往往集中在基于扫描电镜、能谱和X射线衍射定性表征的腐蚀层成分组成及涂层微观结构和相组成,对涂层不同腐蚀阶段物相动态形成过程未有深入研究。为了更好地了解涂层热腐蚀机理,可以从腐蚀过程的在线表征和腐蚀机制的原子水平分析等方面进行深入研究。
(2) 缺乏精确的腐蚀-磨损预测模型。目前锅炉材料失效模型研究主要通过实验室模拟单一腐蚀或磨损环境来实现,而锅炉材料的失效通常发生在腐蚀-磨损耦合环境中,因此无法通过实验室规模的实验结果来预测涂层实际使用寿命。从目前研究结果来看,缺乏涂层在腐蚀-磨损耦合环境下的评价标准,尤其缺乏对涂层磨损实验及性能的测试规范和评价标准。因此,未来需要建立锅炉燃烧模拟实验平台来准确、有效、全面评估涂层性能。
(3) 应用于含硫、含氯、磨损环境高温防护涂层种类单一,粉末合成设计-涂层结构设计-服役性能评价一体化研究工作开展较少。致密结构和耐蚀元素添加都有助于延长涂层使用寿命,目前研究大部分集中在通过改进技术手段来制备致密涂层结构,或通过在已有涂层体系中添加微量或少量增强相如陶瓷相或稀有金属及氧化物来提高涂层耐蚀耐磨性能。粉末制备工艺研究较少,缺乏从粉末到涂层的一体化研究,导致新型涂层材料研发缓慢。粉末制备作为热喷涂涂层制备的源头,未来应加强粉末材料设计合成工艺与热喷涂涂层材料制备工艺的协同发展。
5.2 发展趋势及展望研究
5.2.1 涂层材料基因工程筛选
材料基因组工程结合薄膜生长原理、合金凝固方程等和高通量快速计算(如密度泛函、第一性原理计算等),通过材料性能数据库建设和构建从原子排列到相组织结构再到材料宏观使用性能的精确脉络关系,为新型耐高温防护涂层的研发提供新思路和新方法[162~164]。已有研究表明,在材料中添加MAX相如Cr2AlC、Ti2AlC等可以大幅度提高材料耐蚀性能[165~167],通过材料基因组工程寻找和设计适用于锅炉服役环境的MAX添加相成为提高锅炉防护涂层高温耐蚀性能的新途径。高熵合金由于其自身微观结构和力学性能的可调节性[168~170],可以通过成分设计来制备满足锅炉使用条件的新型涂层材料。另外,涂层传热性能直接影响锅炉发电效率,然而目前还没有基于理论或物理模型预测得到令人满意的涂层接触传热系数[171,172],通过机器学习方法建立锅炉燃烧环境中腐蚀-磨损-传热多因素影响下的涂层传热模型,为建立防护涂层传热性能评价指标奠定基础。
5.2.2 生物质锅炉发展趋势下的涂层研发
为降低碳排放,生物质发电及生物质-燃煤混烧发电将是未来电力重点发展方向,高装机容量、高热交换效率超临界锅炉发电技术未来也将应用到生物质发电领域,这对生物质锅炉防护涂层在更高温度更高压力下的耐蚀耐磨性能提出了更高要求。目前研究人员对于生物质锅炉耐氯腐蚀涂层已经开展了一些研究性工作,而对于涂层耐冲蚀-磨损性能研究较少,未来研发兼具优良耐氯腐蚀及耐冲蚀-磨损性能涂层将成为生物质锅炉防护涂层发展趋势。目前已有国内外研究人员开始关注锅炉防护涂层高温磨损性能的提升,主要通过粉末合成设计-涂层结构设计-服役性能评价一体化研究来进行相关新材料的研发。例如,Yury等[173]将Y元素通过粉末合金化加入到Cr13Al5B8芯材中并通过AS技术制备得到FeCrBAlY涂层,该涂层耐700℃磨损率相比于FeCrC涂层降低20%;本文作者采用机械球磨、喷雾造粒等方法和HVOF技术分别制备了NiCrBSi-ZrB2金属陶瓷粉末和涂层,金属陶瓷涂层在700℃下的耐磨性能相比于传统NiCrBSi合金涂层提升50%。但是相关研究目前还处于初级阶段,除了继续研发相关涂层体系之外,还需要探索硬质相以及在烧结和喷涂过程中产生的物相对涂层腐蚀及磨损的影响,为研发低成本、耐磨损、优异的耐高温腐蚀以及高热交换效率的工业化应用涂层材料提供重要参考价值。
参考文献
1 Tong D, Zhang Q, Zheng Y X, et al. Committed emissions from existing energy infrastructure jeopardize 1.5oC climate target [J]. Nature, 2019, 572: 373
2 Maurya P K, Mondal S, Kumar V, et al. Roadmap to sustainable carbon-neutral energy and environment: Can we cross the barrier of biomass productivity? [J]. Environ. Sci. Pollut. Res., 2021, 28: 49327
3 Liu Z, Ciais P, Deng Z, et al. Carbon monitor, a near-real-time daily dataset of global CO2 emission from fossil fuel and cement production [J]. Sci. Data, 2020, 7: 392
4 Tong D, Zhang Q, Davis S J, et al. Targeted emission reductions from global super-polluting power plant units [J]. Nat. Sustain., 2018, 1: 59
5 Pfeiffer A, Hepburn C, Vogt-Schilb A, et al. Committed emissions from existing and planned power plants and asset stranding required to meet the Paris Agreement [J]. Environ. Res. Lett., 2018, 13: 054019
6 Edenhofer O, Steckel J C, Jakob M, et al. Reports of coal's terminal decline may be exaggerated [J]. Environ. Res. Lett., 2018, 13: 024019
7 Davis S J, Caldeira K, Matthews H D. Future CO2 emissions and climate change from existing energy infrastructure [J]. Science, 2010, 329: 1330
8 The United Nations. Paris Agreement [EB/OL]. The 21st United Nations Climate Change Conference, Paris, 2015.
9 Ministry of Ecology and Environment of the People's Republic of China. China's policy and action on handling climate change 2020 annual report [EB/OL]. (2021-07-13).
9 中华人民共和国生态环境部. 中国应对气候变化的政策与行动2020年度报告 [EB/OL]. (2021-07-13).
10 Global Energy Interconnection Development and Cooperation Organization. Research on China's “14th five-year plan” for electric power development [R]. Beijing: Global Energy Interconnection Development and Cooperation Organization, 2020
10 全球能源互联网发展合作组织. 中国“十四五”电力发展规划研究 [R]. 北京: 全球能源互联网发展合作组织, 2020
11 The Comprehensive Research Group for Energy Consulting and Research. Strategic research on promoting energy revolution of production and consumption [J]. Strat Study CAE, 2015, 17(9): 11
11 “能源领域咨询研究”综合组. 推动能源生产和消费革命战略研究 [J]. 中国工程科学, 2015, 17(9): 11
12 Zhao X G, Li A. A multi-objective sustainable location model for biomass power plants: Case of China [J]. Energy, 2016, 112: 1184
13 Tan Q L, Wang T R, Zhang Y M, et al. Nonlinear multi-objective optimization model for a biomass direct-fired power generation supply chain using a case study in China [J]. Energy, 2017, 139: 1066
14 Yi Q, Zhao Y J, Huang Y, et al. Life cycle energy-economic-CO2 emissions evaluation of biomass/coal, with and without CO2 capture and storage, in a pulverized fuel combustion power plant in the United Kingdom [J]. Appl. Energy, 2018, 225: 258
15 Goerndt M E, Aguilar F X, Skog K. Drivers of biomass co-firing in U.S. coal-fired power plants [J]. Biomass Bioenergy, 2013, 58: 158
16 Wu C Z, Zhou Z Q, Ma L L, et al. Comparative study on biomass power generation technologies [J]. Renew. Energy Resour., 2008, 26(3): 34
16 吴创之, 周肇秋, 马隆龙等. 生物质发电技术分析比较 [J]. 可再生能源, 2008, 26(3): 34
17 Roni M S, Chowdhury S, Mamun S, et al. Biomass co-firing technology with policies, challenges, and opportunities: A global review [J]. Renew. Sust. Energy Rev., 2017, 78: 1089
18 Mun T Y, Tumsa T Z, Lee U, et al. Performance evaluation of co-firing various kinds of biomass with low rank coals in a 500 MWe coal-fired power plant [J]. Energy, 2016, 115: 954
19 Cebrucean D, Cebrucean V, Ionel I. Modeling and performance analysis of subcritical and supercritical coal-fired power plants with biomass co-firing and CO2 capture [J]. Clean Technol. Environ. Policy, 2020, 22: 153
20 Fogarasi S, Cormos C C. Technico-economic assessment of coal and sawdust co-firing power generation with CO2 capture [J]. J. Clean. Prod., 2015, 103: 140
21 National Energy Administration. The “13th Five-Year Plan” for biomass energy development [EB/OL]. (2016-12-06).
21 国家能源局. 国家能源局关于印发《生物质能发展“十三五”规划》的通知 [EB/OL]. (2016-12-06).
22 Zhang S X, Shi L, Xu Y F, et al. Application of power generation by coupling direct-combustion of biomass, solid waste and coal [J]. Power Syst. Eng., 2021, 37(4): 12
22 张世鑫, 史 磊, 许燕飞等. 煤和生物质、固废直燃耦合发电技术应用 [J]. 电站系统工程, 2021, 37(4): 12
23 Yang W L, Ni Y, Cao S. Progress of biomass direct co-firing for coal-fired boilers [J]. Renew. Energy Resour., 2021, 39: 1007
23 杨卧龙, 倪 煜, 曹 泷. 生物质直接混烧技术在燃煤电站的应用研究进展 [J]. 可再生能源, 2021, 39: 1007
24 Agbor E, Oyedun A O, Zhang X L, et al. Integrated techno-economic and environmental assessments of sixty scenarios for co-firing biomass with coal and natural gas [J]. Appl. Energy, 2016, 169: 433
25 Zhang D W, Fan H D, Zhao B, et al. Development of biomass power generation technology at home and abroad [J]. Huadian Technol., 2021, 43(3): 70
25 张东旺, 范浩东, 赵 冰等. 国内外生物质能源发电技术应用进展 [J]. 华电技术, 2021, 43(3): 70
26 Ma H D, Wang Y G, Zhao Q X, et al. Characteristics of ash deposit and dew point corrosion in biofuel boiler [J]. CIESC J., 2016, 67: 5237
26 马海东, 王云刚, 赵钦新等. 生物质锅炉积灰特性与露点腐蚀 [J]. 化工学报, 2016, 67: 5237
27 Deng J X, Ding Z L, Zhou H M, et al. Performance and wear characteristics of ceramic, cemented carbide, and metal nozzles used in coal-water-slurry boilers [J]. Int. J. Refract. Met. Hard Mater., 2009, 27: 919
28 Nagarajan R, Ambedkar B, Gowrisankar S, et al. Development of predictive model for fly-ash erosion phenomena in coal-burning boilers [J]. Wear, 2009, 267: 122
29 Niu Y Q, Tan H Z, Hui S. Ash-related issues during biomass combustion: Alkali-induced slagging, silicate melt-induced slagging (ash fusion), agglomeration, corrosion, ash utilization, and related countermeasures [J]. Prog. Energy Combust. Sci., 2016, 52: 1
30 Chen H, Pan P Y, Zhao Q X, et al. Coupling mechanism of viscose ash deposition and dewpoint corrosion in industrial coal-fired boiler [J]. CIESC J., 2017, 68: 4774
30 陈 衡, 潘佩媛, 赵钦新等. 燃煤工业锅炉黏性积灰和露点腐蚀耦合机理 [J]. 化工学报, 2017, 68: 4774
31 Xiong X H, Lv Z M, Tan H Z, et al. A typical super-heater tube leakage and high temperature corrosion mechanism investigation in a 260 t/h circulated fluidized boiler [J]. Eng. Fail. Anal., 2020, 109: 104255
32 Zhang X J, Liu H, Chen T Z, et al. Application of coatings to alleviate fireside corrosion on heat transfer tubes during the combustion of low-grade solid fuels: A review [J]. Energy Fuels, 2020, 34: 11752
33 Hu S H, Ni Y G, Yin Q, et al. Research on element migration and ash deposition characteristics of high-alkali coal in horizontal liquid slagging cyclone furnace [J]. Fuel, 2022, 308: 121962
34 Feng Y L, Wei Q, Li H, et al. Summarization of the research on high-temperature erosion test method and mechanisms [J]. Boiler Technol., 2008, 39(4): 62
34 冯艳玲, 魏 琪, 李 辉等. 高温冲蚀磨损测试方法及机理的研究概述 [J]. 锅炉技术, 2008, 39(4): 62
35 Vicenzi J, Villanova D L, Lima M D, et al. HVOF-coatings against high temperature erosion (~300oC) by coal fly ash in thermoelectric power plant [J]. Mater. Des., 2006, 27: 236
36 Pérez M G, Vakkilainen E, Hypp?nen T. Unsteady CFD analysis of Kraft recovery boiler fly-ash trajectories, sticking efficiencies and deposition rates with a mechanistic particle rebound-stick model [J]. Fuel, 2016, 181: 408
37 Dizaji H B, Zeng T, H?lzig H, et al. Ash transformation mechanism during combustion of rice husk and rice straw [J]. Fuel, 2022, 307: 121768
38 Pyyk?nen J, Jokiniemi J. Modelling alkali chloride superheater deposition and its implications [J]. Fuel Process. Technol., 2003, 80: 225
39 Maj I, Kalisz S, Szymajda A, et al. The influence of cow dung and mixed straw ashes on steel corrosion [J]. Renew Energy, 2021, 177: 1198
40 Liu G Q, Li S Q, Yao Q. A JKR-based dynamic model for the impact of micro-particle with a flat surface [J]. Powder Technol., 2011, 207: 215
41 Konstandopoulos A G. Deposit growth dynamics: Particle sticking and scattering phenomena [J]. Powder Technol., 2000, 109: 262
42 Forstner M, Hofmeister G, J?ller M, et al. CFD simulation of ash deposit formation in fixed bed biomass furnaces and boilers [J]. Prog. Comput. Fluid Dynam., 2006, 6: 248
43 Cai Y T, Tay K, Zheng Z M, et al. Modeling of ash formation and deposition processes in coal and biomass fired boilers: A comprehensive review [J]. Appl. Energy, 2018, 230: 1447
44 Doshi V, Vuthaluru H B, Korbee R, et al. Development of a modeling approach to predict ash formation during co-firing of coal and biomass [J]. Fuel Process. Technol., 2009, 90: 1148
45 Mahajan S, Chhibber R. Hot corrosion studies of boiler steels exposed to different molten salt mixtures at 950oC [J]. Eng. Fail. Anal., 2019, 99: 210
46 Mei?ner T M, Grégoire B, Montero X, et al. Long-term corrosion behavior of Cr diffusion coatings on ferritic-martensitic superheater tube material X20CrMoV12-1 under conditions mimicking biomass (co-)firing [J]. Energy Fuels, 2020, 34: 10989
47 Montero X, Ishida A, Rudolphi M, et al. Breakaway corrosion of austenitic steel induced by fireside corrosion [J]. Corros. Sci., 2020, 173: 108765
48 Cao C, Jiang C Y, Lu J T, et al. Corrosion behavior of austenitic stainless steel with different Cr contents in 700oC coal ash/high sulfur flue-gas environment [J]. Acta Metall. Sin., 2022, 58: 67
48 曹 超, 蒋成洋, 鲁金涛等. 不同Cr含量的奥氏体不锈钢在700℃煤灰/高硫烟气环境中的腐蚀行为 [J]. 金属学报, 2022, 58: 67
49 Hagman H, Bostr?m D, Lundberg M, et al. Alloy degradation in a co-firing biomass CFB vortex finder application at 880oC [J]. Corros. Sci., 2019, 150: 136
50 Liu Z D, Chen Z Z, He X K, et al. Systematical innovation of heat resistant materials used for 630~700oC advanced ultra-supercritical (A-USC) fossil fired boilers [J]. Acta Metall. Sin., 2020, 56: 539
50 刘正东, 陈正宗, 何西扣等. 630~700℃超超临界燃煤电站耐热管及其制造技术进展 [J]. 金属学报, 2020, 56: 539
51 Gao B, Wang L, Song X, et al. Effect of pre-oxidation on high temperature oxidation and corrosion behavior of Co-Al-W-based superalloy [J]. Acta Metall. Sin., 2019, 55: 1273
51 高 博, 王 磊, 宋 秀等. 预氧化对Co-Al-W基高温合金高温氧化和热腐蚀行为的影响 [J]. 金属学报, 2019, 55: 1273
52 Mudgal D, Verma P K, Singh S, et al. High temperature degradation of Co based superalloy in incinerator environment [J]. Adv. Mater. Res., 2012, 585: 542
53 Lu J T, Huang J Y, Yang Z, et al. Simulated fireside corrosion behavior of a wrought Ni-Fe-based superalloy for 700oC-class ultra-supercritical power plant applications [J]. J. Mater. Eng. Perform., 2019, 28: 7390
54 Zhou H X, Wang J W, Meng X H, et al. The corrosion mechanism of Fe-based superalloy in molten NaCl-52wt-%MgCl2 at 520oC [J]. Corros. Eng. Sci. Technol., 2017, 52: 261
55 Cheng H S, Liu G, Lei G, et al. Research progress of high temperature corrosion protection coating technology for coal-burning boiler heating surface [J]. Mater. Rep., 2020, 34(): 433
55 程海松, 刘 岗, 雷 刚等. 燃煤锅炉受热面高温腐蚀防护涂层技术研究进展 [J]. 材料导报, 2020, 34(): 433
56 Singh J, Vasudev H, Singh S. Performance of different coating materials against high temperature oxidation in boiler tubes—A review [J]. Mater. Today Proc., 2020, 26: 972
57 Szymański K, Hernas A, Moskal G, et al. Thermally sprayed coatings resistant to erosion and corrosion for power plant boilers—A review [J]. Surf. Coat. Technol., 2015, 268: 153
58 Kumar S, Handa A, Chawla V, et al. Performance of thermal-sprayed coatings to combat hot corrosion of coal-fired boiler tube and effect of process parameters and post-coating heat treatment on coating performance: A review [J]. Surf. Eng., 2021, 37: 833
59 Li H, Liu D, Yao D Y. Analysis and reflection on the development of power system towards the goal of carbon emission peak and carbon neutrality [J]. Proc. CSEE, 2021, 41: 6245
59 李 晖, 刘 栋, 姚丹阳. 面向碳达峰碳中和目标的我国电力系统发展研判 [J]. 中国电机工程学报, 2021, 41: 6245
60 Long H, Huang J J. Development direction analysis of coal-fired power units' design technology during the 13th Five-Year Plan [J]. Power Generat. Technol., 2018, 39: 13
60 龙 辉, 黄晶晶. “十三五”燃煤发电设计技术发展方向分析 [J]. 发电技术, 2018, 39: 13
61 Lu J T, Gu Y F, Yang Z. Coal ash induced corrosion of three candidate materials for superheater boiler tubes of advanced ultra-supercritical power station [J]. Corros. Sci. Protect. Technol., 2014, 26: 205
61 鲁金涛, 谷月峰, 杨 珍. 3种700℃级超超临界燃煤锅炉备选高温合金煤灰腐蚀行为 [J]. 腐蚀科学与防护技术, 2014, 26: 205
62 Li J, Zhou R C, Tang L Y, et al. Research on high temperature fireside corrosion of water wall materials for ultra-supercritical coal fired boiler [J]. Hot Working Technol., 2017, 46(16): 19
62 李 江, 周荣灿, 唐丽英等. 超超临界燃煤锅炉水冷壁材料高温烟气腐蚀研究 [J]. 热加工工艺, 2017, 46(16): 19
63 Hu S S, Finklea H, Liu X B. A review on molten sulfate salts induced hot corrosion [J]. J. Mater. Sci. Technol., 2021, 90: 243
64 Mannava V, Rao A S, Paulose N, et al. Hot corrosion studies on Ni-base superalloy at 650oC under marine-like environment conditions using three salt mixture (Na2SO4 + NaCl + NaVO3) [J]. Corros. Sci., 2016, 105: 109
65 Yan W P, Ma K, Gao Z Y, et al. Erosion of economizer tube bundles in pressurized oxy-fuel coal-fired boiler [J]. J. Xi'an Jiaotong Univ., 2013, 47(3): 53
65 阎维平, 马 凯, 高正阳等. 增压富氧燃煤锅炉省煤器管束磨损研究 [J]. 西安交通大学学报, 2013, 47(3): 53
66 Young D J. High Temperature Oxidation and Corrosion of Metals [M]. Oxford: Elsevier Science, 2008: 361
67 Liang Z Y, Yu M, Zhao Q X. Investigation of fireside corrosion of austenitic heat-resistant steel 10Cr18Ni9Cu3NbN in ultra-supercritical power plants [J]. Eng. Fail. Anal., 2019, 100: 180
68 Syed A U, Simms N J, Oakey J E. Fireside corrosion of superheaters: Effects of air and oxy-firing of coal and biomass [J]. Fuel, 2012, 101: 62
69 Singh G, Bala N, Chawla V, et al. Hot corrosion behavior of HVOF-sprayed carbide based composite coatings for boiler steel in Na2SO4-60%V2O5 environment at 900oC under cyclic conditions [J]. Corros. Sci., 2021, 190: 109666
70 Meier G H. Invited review paper in commemoration of over 50 years of oxidation of metals: Current aspects of deposit-induced corrosion [J]. Oxid. Met., 2021, doi: 10.1007/s11085-020-10015-6
71 Lortrakul P, Trice R W, Trumble K P, et al. Investigation of the mechanisms of Type-II hot corrosion of superalloy CMSX-4 [J]. Corros. Sci., 2014, 80: 408
72 Zhong Y S, Rapp R A. Solubilities of α-Fe2O3 and Fe3O4 in fused Na2SO4 at 1200 K [J]. J. Electrochem. Soc., 1985, 132: 2498
73 Gupta D K, Rapp R A. The solubilities of NiO, Co3O4, and ternary oxides in fused Na2SO4 at 1200 K [J]. J. Electrochem. Soc., 1980, 127: 2194
74 Jose P D, Gupta D K, Rapp R A. Solubility of α-Al2O3 in fused Na2SO4 at 1200 K [J]. J. Electrochem. Soc., 1985, 132: 735
75 Zhang Y S. Solubilities of Cr2O3 in fused Na2SO4 at 1200 K [J]. J. Electrochem. Soc., 1986, 133: 655
76 Rapp R A. Hot corrosion of materials: A fluxing mechanism? [J]. Corros. Sci., 2002, 44: 209
77 Kolta G A, Hewaidy I F, Felix N S. Reactions between sodium sulphate and vanadium pentoxide [J]. Thermochim. Acta, 1972, 4: 151
78 Montero X, Galetz M C. Sulfate-vanadate-induced corrosion of different alloys [J]. Oxid. Met., 2018, 89: 499
79 Zhao Y Y, Chen D L, Chen J, et al. A mathematic model of the whole erosions in coal-fired boilers [J]. Boiler Manuf., 2002, (2): 6
79 赵渝渝, 陈冬林, 陈 荐等. 燃煤锅炉总体磨损性数学模型 [J]. 锅炉制造, 2002, (2): 6
80 Wright I G, Williams D N, Hazard H R, et al. Fireside corrosion and fly ash erosion in boilers: Final report [R]. Palo Alto, CA: Electric Power Research Institute, 1987
81 Jin T, Luo K, Fan J R, et al. Immersed boundary method for simulations of erosion on staggered tube bank by coal ash particles [J]. Powder Technol., 2012, 225: 196
82 Orumbayev R K, Bakhtiyar B T, Umyshev D R, et al. Experimental study of ash wear of heat exchange surfaces of the boiler [J]. Energy, 2021, 215: 119119
83 Singh P K, Mishra S B. Erosion behaviour of boiler component materials at room temperature and 400oC temperature [J]. Mater. Res. Express, 2020, 7: 016538
84 Sagayaraj T A D, Suresh S, Chandrasekar M. Experimental studies on the erosion rate of different heat treated carbon steel economiser tubes of power boilers by fly ash particles [J]. Int. J. Min. Metall. Mater., 2009, 16: 534
85 Yun J Y, Lee H S, Hur D H, et al. Effect of oxidation film on the fretting wear behavior of Alloy 690 steam generator tube mated with SUS 409 [J]. Wear, 2016, 368-369: 344
86 Xing X F, Wang R, Bauer N, et al. Spatially explicit analysis identifies significant potential for bioenergy with carbon capture and storage in China [J]. Nat. Commun., 2021, 12: 3159
87 Gruber T, Schulze K, Scharler R, et al. Investigation of the corrosion behaviour of 13CrMo4-5 for biomass fired boilers with coupled online corrosion and deposit probe measurements [J]. Fuel, 2015, 144: 15
88 Zhou J, Liu Q, Zhong W Q, et al. Migration and transformation law of potassium in the combustion of biomass blended coal [J]. J. Fuel Chem. Technol., 2020, 48: 929
88 周 骏, 刘 倩, 钟文琪等. 生物质混煤燃烧过程中钾的迁移转化规律 [J]. 燃料化学学报, 2020, 48: 929
89 Chen J, Fu P F, Zhang B, et al. Deposition and sintering behavior of alkali metals and chlorine in biomass combustion [J]. J. Eng. Thermophys., 2014, 35: 1453
89 陈 兢, 傅培舫, 张 斌等. 生物质燃烧中碱金属和氯沉积烧结行为分析 [J]. 工程热物理学报, 2014, 35: 1453
90 Lehmusto J, Yrjas P, Skrifvars B J, et al. Detailed studies on the high temperature corrosion reactions between potassium chloride and metallic chromium [J]. Mater. Sci. Forum, 2011, 696: 218
91 Uusitalo M A, Vuoristo P M J, M?ntyl? T A. High temperature corrosion of coatings and boiler steels below chlorine-containing salt deposits [J]. Corros. Sci., 2004, 46: 1311
92 Sadeghimeresht E, Reddy L, Hussain T, et al. Influence of KCl and HCl on high temperature corrosion of HVAF-sprayed NiCrAlY and NiCrMo coatings [J]. Mater. Des., 2018, 148: 17
93 Wang Y B, Tan H Z. Condensation of KCl(g) under varied temperature gradient [J]. Fuel, 2019, 237: 1141
94 Lyu Z K, Long S W, Li G B, et al. Density functional theory study on chlorine corrosion of biomass furnace [J]. CIESC J., 2019, 70: 4370
94 吕泽康, 龙慎伟, 李冠兵等. 生物质锅炉氯腐蚀的密度泛函理论研究 [J]. 化工学报, 2019, 70: 4370
95 Gao J K, Tong Y, Wang S C, et al. The current situation and future development tendency of biomass-coal coupling power generation system [J]. Renew. Energy Resour., 2019, 37: 501
95 高金锴, 佟 瑶, 王树才等. 生物质燃煤耦合发电技术应用现状及未来趋势 [J]. 可再生能源, 2019, 37: 501
96 Jin Q M, Dai G F, Wang Y B, et al. High-temperature corrosion of water-wall tubes in oxy-combustion atmosphere [J]. J. Energy Inst., 2020, 93: 1305
97 Zhang Q, Wang J Q, Chen G H, et al. Microstructures and mechanical properties of T92/Super304H dissimilar steel weld joints [J]. Chin. J. Nonferrous Met., 2013, 23: 396
97 张 祺, 王家庆, 陈国宏等. T92/Super304H异种钢焊接接头的组织结构和力学性能 [J]. 中国有色金属学报, 2013, 23: 396
98 Zhao Q X, Zhang Z X, Cheng D N, et al. High temperature corrosion of water wall materials T23 and T24 in simulated furnace atmospheres [J]. Chin. J. Chem. Eng., 2012, 20: 814
99 Wright I G, Dooley R B. Morphologies of oxide growth and exfoliation in superheater and reheater tubing of steam boiler [J]. Mater. High Temp., 2011, 28: 40
100 Hussain T, Syed A U, Simms N J. Trends in fireside corrosion damage to superheaters in air and oxy-firing of coal/biomass [J]. Fuel, 2013, 113: 787
101 Goyal G, Singh H, Prakash S. Effect of superficially applied ZrO2 inhibitor on the high temperature corrosion performance of some Fe-, Co- and Ni-base superalloys [J]. Appl. Surf. Sci., 2008, 254: 6653
102 Muthu S M, Arivarasu M. Investigations of hot corrosion resistance of HVOF coated Fe based superalloy A-286 in simulated gas turbine environment [J]. Eng. Fail. Anal., 2020, 107: 104224
103 Mudgal D, Singh S, Prakash S. Hot corrosion behavior of some superalloys in a simulated incinerator environment at 900oC [J]. J. Mater. Eng. Perform., 2014, 23: 238
104 Birol Y. High temperature sliding wear behaviour of Inconel 617 and Stellite 6 alloys [J]. Wear, 2010, 269: 664
105 Guo J T. The current situation of application and development of superalloys in the fields of energy industry [J]. Acta Metall. Sin., 2010, 46: 513
105 郭建亭. 高温合金在能源工业领域中的应用现状与发展 [J]. 金属学报, 2010, 46: 513
106 Israelsson N, Unocic K A, Hellstr?m K, et al. A microstructural and kinetic investigation of the KCl-induced corrosion of an FeCrAl alloy at 600oC [J]. Oxid. Met., 2015, 84: 105
107 Okoro S C, Montgomery M, Frandsen F J, et al. Influence of preoxidation on high temperature corrosion of a Ni-based alloy under conditions relevant to biomass firing [J]. Surf. Coat. Technol., 2017, 319: 76
108 Klein L, Killian M S, Virtanen S. The effect of nickel and silicon addition on some oxidation properties of novel Co-based high temperature alloys [J]. Corros. Sci., 2013, 69: 43
109 Weng F, Yu H J, Wan K, et al. The influence of Nb on hot corrosion behavior of Ni-based superalloy at 800oC in a mixture of Na2SO4-NaCl [J]. J. Mater. Res., 2014, 29: 2596
110 Schütze M, Malessa M, Rohr V, et al. Development of coatings for protection in specific high temperature environments [J]. Surf. Coat. Technol., 2006, 201: 3872
111 Trindade V, Christ H J, Krupp U. Grain-size effects on the high-temperature oxidation behaviour of chromium steels [J]. Oxid. Met., 2010, 73: 551
112 Sadeghimeresht E, Markocsan N, Huhtakangas M, et al. Isothermal oxidation of HVAF-sprayed Ni-based chromia, alumina and mixed-oxide scale forming coatings in ambient air [J]. Surf. Coat. Technol., 2017, 316: 10
113 Davis J R. Handbook of Thermal Spray Technology [M]. Materials Park, OH: ASM International, 2004: 54
114 Wang G Y, Liu H, Chen T Z, et al. Comparative investigation on thermal corrosion of alloy coatings in simulated waste incinerator environment [J]. Corros. Sci., 2021, 189: 109592
115 Hussain T, Simms N J, Nicholls J R, et al. Fireside corrosion degradation of HVOF thermal sprayed FeCrAl coating at 700-800oC [J]. Surf. Coat. Technol., 2015, 268: 165
116 Jiang C P, Liu W Q, Wang G, et al. The corrosion behaviours of plasma-sprayed Fe-based amorphous coatings [J]. Surf. Eng., 2018, 34: 634
117 Chawla V, Sidhu B S, Rani A, et al. High-temperature corrosion behavior of some post-plasma-spraying-gas-nitrided metallic coatings on a Fe-based superalloy [J]. Mater. Corros., 2019, 70: 2157
118 Sidhu T S, Prakash S, Agrawal R D. Hot corrosion behaviour of HVOF-sprayed NiCrBSi coatings on Ni- and Fe-based superalloys in Na2SO4-60%V2O5 environment at 900oC [J]. Acta Mater., 2006, 54: 773
119 Mittal R, Singh M, Kumar P. Characterization of detonation gun thermal spray coatings on SA213T91 in simulated boiler environment [J]. Mater. Today Proc., 2019, 18: 4952
120 Singh H, Puri D, Prakash S. Some studies on hot corrosion performance of plasma sprayed coatings on a Fe-based superalloy [J]. Surf. Coat. Technol., 2005, 192: 27
121 Bala N, Singh H, Prakash S. Accelerated hot corrosion studies of cold spray Ni-50Cr coating on boiler steels [J]. Mater. Des., 2010, 31: 244
122 Cheng J, Wu Y P, Chen L Y, et al. Hot corrosion behavior and mechanism of high-velocity arc-sprayed Ni-Cr alloy coatings [J]. J. Therm. Spray Technol., 2019, 28: 1263
123 Sadeghimeresht E, Reddy L, Hussain T, et al. Chlorine-induced high temperature corrosion of HVAF-sprayed Ni-based alumina and chromia forming coatings [J]. Corros. Sci., 2018, 132: 170
124 Goutier F, Valette S, Vardelle A, et al. Behaviour of alumina-coated 304L steel in a waste-to-energy plant [J]. Surf. Coat. Technol., 2011, 205: 4425
125 Singh G, Goyal K, Bhatia R. Hot corrosion studies of plasma-sprayed chromium oxide coatings on boiler tube steel at 850oC in simulated boiler environment [J]. Iran. J. Sci. Technol. Trans. Mech. Eng., 2018, 42: 149
126 Mittal R, Singh H. Evaluation of the behavior of D-gun sprayed coatings on T-11 boiler steel at 900oC temperature [J]. Mater. Today Proc., 2020, 26: 549
127 Rao S, Frederick L, McDonald A. Resistance of nanostructured environmental barrier coatings to the movement of molten salts [J]. J. Therm. Spray Technol., 2012, 21: 887
128 Rani A, Bala N, Gupta C M. Accelerated hot corrosion studies of D-gun-sprayed Cr2O3-50% Al2O3 coating on boiler steel and Fe-based superalloy [J]. Oxid. Met., 2017, 88: 621
129 Katiki K, Yadlapati S, Chidepudi N S, et al. Performance of plasma spray coatings on Inconel 625 in air oxidation and molten salt environment at 800oC [J]. Int. J. Chem. Tech. Res., 2014, 6: 2744
130 Goyal R, Sidhu B S, Chawla V. Hot corrosion performance of plasma-sprayed multiwalled carbon nanotube-Al2O3 composite coatings in a coal-fired boiler at 900oC [J]. J. Mater. Eng. Perform., 2020, 29: 5738
131 Kumar S, Bhatia R, Singh H. Hot corrosion behaviour of CNT-reinforced zirconium yttrium composite coating at elevated temperature [J]. Mater. Today Proc., 2020, 28: 1530
132 Mudgal D, Kumar S, Singh S, et al. Corrosion behavior of bare, Cr3C2-25%(NiCr), and Cr3C2-25%(NiCr) + 0.4%CeO2-coated Superni 600 under molten salt at 900oC [J]. J. Mater. Eng. Perform., 2014, 23: 3805
133 Ahuja L, Mudgal D, Singh S, et al. A comparative study to evaluate the corrosion performance of Zr incorporated Cr3C2-(NiCr) coating at 900oC [J]. Ceram. Int., 2018, 44: 6479
134 Singh H, Kaur M, Prakash S. High-temperature exposure studies of HVOF-sprayed Cr3C2-25(NiCr)/(WC-Co) coating [J]. J. Therm. Spray Technol., 2016, 25: 1192
135 Singh H, Bala N, Kaur N, et al. Effect of additions of TiC and Re on high temperature corrosion performance of cold sprayed Ni-20Cr coatings [J]. Surf. Coat. Technol., 2015, 280: 50
136 Cheng J, Wu Y P, Shen W, et al. A study on hot corrosion performance of high velocity arc-sprayed FeCrNiAlMnB/Cr3C2 coating exposed to Na2SO4 + K2SO4 and Na2SO4 + NaCl [J]. Surf. Coat. Technol., 2020, 397: 126015
137 Chatha S S, Sidhu H S, Sidhu B S. The effects of post-treatment on the hot corrosion behavior of the HVOF-sprayed Cr3C2-NiCr coating [J]. Surf. Coat. Technol., 2012, 206: 4212
138 Wu Y S. Hot corrosion behavior of nanocrystalline NiCrBSi-TiB2 coating in Na2SO4-60%V2O5 molten salt [J]. Hot Work. Technol., 2015, 44(18): 123
138 吴姚莎. 纳米NiCrBSi-TiB2涂层在Na2SO4-60%V2O5熔盐中的热腐蚀行为 [J]. 热加工工艺, 2015, 44(18): 123
139 Sundaresan C, Rajasekaran B, Varalakshmi S, et al. Comparative hot corrosion performance of APS and detonation sprayed CoCrAlY, NiCoCrAlY and NiCr coatings on T91 boiler steel [J]. Corros. Sci., 2021, 189: 109556
140 Hu K, Liu X, Zhang S H, et al. Effect of oxygen-fuel ratio on microstructure and hot corrosion behavior of NiCrAlY coatings in KCl molten salt [J]. Chin. J. Nonferrous Met., 2021, 31: 1545
140 胡 凯, 刘 侠, 张世宏等. 氧燃比对NiCrAlY涂层的微观结构及其在KCl熔盐中热腐蚀行为的影响 [J]. 中国有色金属学报, 2021, 31: 1545
141 Zhang S T, Du K P, Ren X J, et al. Effect of Si on hot corrosion resistance of CoCrAlY coating [J]. Rare Met. Mater. Eng., 2017, 46: 2807
142 Horlock A J, McCartney D G, Shipway P H, et al. Thermally sprayed Ni(Cr)-TiB2 coatings using powder produced by self-propagating high temperature synthesis: Microstructure and abrasive wear behaviour [J]. Mater. Sci. Eng., 2002, A336: 88
143 Cai J, Gao C Z, Lv P, et al. Hot corrosion behaviour of thermally sprayed CoCrAlY coating irradiated by high-current pulsed electron beam [J]. J. Alloys Compd., 2019, 784: 1221
144 Zhu S Y, Cheng J, Qiao Z H, et al. High temperature solid-lubricating materials: A review [J]. Tribol. Int., 2019, 133: 206
145 Meng Y G, Xu J, Jin Z M, et al. A review of recent advances in tribology [J]. Friction, 2020, 8: 221
146 Praveen A S, Sarangan J, Suresh S, et al. Erosion wear behaviour of plasma sprayed NiCrSiB/Al2O3 composite coating [J]. Int. J. Refract. Met. Hard Mater., 2015, 52: 209
147 Baiamonte L, Bj?rklund S, Mulone A, et al. Carbide-laden coatings deposited using a hand-held high-velocity air-fuel (HVAF) spray gun [J]. Surf. Coat. Technol., 2021, 406: 126725
148 Mishra S B, Chandra K, Prakash S. Erosion-corrosion performance of NiCrAlY coating produced by plasma spray process in a coal-fired thermal power plant [J]. Surf. Coat. Technol., 2013, 216: 23
149 Kumar P, Sidhu B S. Characterization and high-temperature erosion behaviour of HVOF thermal spray cermet coatings [J]. J. Mater. Eng. Perform., 2016, 25: 250
150 Singh P K, Mishra S B. Studies on solid particle erosion behaviour of D-gun sprayed WC-Co, Stellite 6 and Stellite 21 coatings on SAE213-T12 boiler steel at 400oC temperature [J]. Surf. Coat. Technol., 2020, 385: 125353
151 Bala N, Singh H, Prakash S. Performance of cold sprayed Ni based coatings in actual boiler environment [J]. Surf. Coat. Technol., 2017, 318: 50
152 Kumar S, Kumar M, Handa A. Erosion corrosion behaviour and mechanical properties of wire arc sprayed Ni-Cr and Ni-Al coating on boiler steels in a real boiler environment [J]. Mater. High Temp., 2020, 37: 370
153 Sapra P K, Singh P K, Prakash S, et al. Performance of Al2O3-3%TiO2 detonation gun coated ferritic steels in coal fired boiler [J]. Int. J. Surf. Sci. Eng., 2009, 3: 145
154 Sidhu H S, Sidhu B S, Prakash S. Mechanical and microstructural properties of HVOF sprayed WC-Co and Cr3C2-NiCr coatings on the boiler tube steels using LPG as the fuel gas [J]. J. Mater. Process. Technol., 2006, 171: 77
155 Wu Y S, Zeng D C, Liu Z W, et al. Microstructure and sliding wear behavior of nanostructured Ni60-TiB2 composite coating sprayed by HVOF technique [J]. Surf. Coat. Technol., 2011, 206: 1102
156 Mahesh R A, Jayaganthan R, Prakash S. Evaluation of hot corrosion behaviour of HVOF sprayed Ni-5Al and NiCrAl coatings in coal fired boiler environment [J]. Surf. Eng., 2010, 26: 413
157 Wang T L, Jia Y H, Wang C Y, et al. Influence of nano ceramic coating on coking characteristics of heating surface of Zhundong coal fired boiler and its engineering application [J/OL]. Therm. Power Generat., 2021. (2021-09-13).
157 王天龙, 贾永会, 汪潮洋等. 纳米陶瓷涂层对燃用准东煤锅炉受热面结焦特性影响研究及工程应用 [J/OL]. 热力发电, 2021. (2021-09-13).
158 Kawahara Y. An overview on corrosion-resistant coating technologies in biomass/waste-to-energy plants in recent decades [J]. Coatings, 2016, 6: 34
159 Oksa M, Mets?joki J, K?rki J. Thermal spray coatings for high-temperature corrosion protection in biomass co-fired boilers [J]. J. Therm. Spray Technol., 2015, 24: 194
160 Hj?rnhede A, Sotkovszki P, Nylund A. Erosion-corrosion of laser and thermally deposited coatings exposed in fluidised bed combustion plants [J]. Mater. Corros., 2006, 57: 307
161 Chi H T, Pans M A, Bai M W, et al. Experimental investigations on the chlorine-induced corrosion of HVOF thermal sprayed Stellite-6 and NiAl coatings with fluidised bed biomass/anthracite combustion systems [J]. Fuel, 2021, 288: 119607
162 Liu X J, Chen Y C, Lu Y, et al. Present research situation and prospect of multi-scale design in novel Co-based superalloys: A review [J]. Acta Metall. Sin., 2020, 56: 1
162 刘兴军, 陈悦超, 卢 勇等. 新型钴基高温合金多尺度设计的研究现状与展望 [J]. 金属学报, 2020, 56: 1
163 Liu Z, Li Y F, Shi D W, et al. The development of cladding materials for the accident tolerant fuel system from the Materials Genome Initiative [J]. Scr. Mater., 2017, 141: 99
164 Xie Y S, Artymowicz D M, Lopes P P, et al. A percolation theory for designing corrosion-resistant alloys [J]. Nat. Mater., 2021, 20: 789
165 Shamsipoor A, Farvizi M, Razavi M, et al. Hot corrosion behavior of Cr2AlC MAX phase and CoNiCrAlY compounds at 950oC in presence of Na2SO4 + V2O5 molten salts [J]. Ceram. Int., 2021, 47: 2347
166 Wang Z Y, Ma G S, Liu L L, et al. High-performance Cr2AlC MAX phase coatings: Oxidation mechanisms in the 900-1100oC temperature range [J]. Corros. Sci., 2020, 167: 108492
167 Richardson P, Cuskelly D, Brandt M, et al. Microstructural analysis of in-situ reacted Ti2AlC MAX phase composite coating by laser cladding [J]. Surf. Coat. Technol., 2020, 385: 125360
168 Li L, Lu J, Liu X Z, et al. AlxCoCrFeNi high entropy alloys with superior hot corrosion resistance to Na2SO4 + 25%NaCl at 900oC [J]. Corros. Sci., 2021, 187: 109479
169 Shang C Y, Axinte E, Sun J, et al. CoCrFeNi(W1 - xMox) high-entropy alloy coatings with excellent mechanical properties and corrosion resistance prepared by mechanical alloying and hot pressing sintering [J]. Mater. Des., 2017, 117: 193
170 Xiao J K, Wu Y Q, Chen J, et al. Microstructure and tribological properties of plasma sprayed FeCoNiCrSiAlx high entropy alloy coatings [J]. Wear, 2020, 448-449: 203209
171 Vu A T, Gulati S, Vogel P A, et al. Machine learning-based predictive modeling of contact heat transfer [J]. Int. J. Heat Mass Transfer, 2021, 174: 121300
172 Zhan T Z, Fang L, Xu Y B. Prediction of thermal boundary resistance by the machine learning method [J]. Sci. Rep., 2017, 7: 7109
173 Yury K, Filiрpov M, Makarov A, et al. Arc-sprayed Fe-based coatings from cored wires for wear and corrosion protection in power engineering [J]. Coatings, 2018, 8: 71
免责声明:本网站所转载的文字、图片与视频资料版权归原创作者所有,如果涉及侵权,请第一时间联系本网删除。
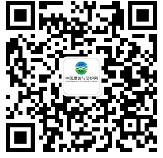
官方微信
《腐蚀与防护网电子期刊》征订启事
- 投稿联系:编辑部
- 电话:010-62316606-806
- 邮箱:fsfhzy666@163.com
- 腐蚀与防护网官方QQ群:140808414