0 引言
螺旋桨及其衍生出来的特种推进器[1] 是现代船舶最常用的推进装置,其正常运行对船舶技战水平的发挥具有重要影响。但在行进过程中,空泡腐蚀和海生物污损是影响螺旋桨推进效率而急需解决的两大难题。空泡腐蚀[2?4] 危害主要体现在以下几个方面:高速服役下,空泡持续产生及闭合爆裂,冲击螺旋桨桨叶,造成螺旋桨的振动损伤,以及桨叶受力不均,缩短其机械构件的使用寿命;改变附近水流形态,降低推进效率;空泡破裂产生的持续冲击波,致使形成空蚀坑,破坏基材原有状态,加速对基材的腐蚀破坏及污损;在高速运行中,空蚀噪声是主要的噪声源,对船舶的隐蔽性同样具有极大的威胁。而海生物污损[5?7] 的危害同样不可小觑,污损生物在螺旋桨上的持续累积,增加螺旋桨负重,加大燃油能耗;影响螺旋桨动平衡,降低推进效率,缩短其使用寿命;加速对螺旋桨基材的腐蚀;增加船舶进坞清理和维修的时间及频率,降低在航率。对于螺旋桨的空蚀及污损防护方法中,有机涂层防护是最有效、经济、便捷的方法之一。
本工作采用防腐底漆、弹性缓冲漆、中间连接漆和防污面漆的涂层配套体系应对空泡腐蚀和污损生物粘附问题,实现对螺旋桨的的整体防护,结合实验室性能评价手段与实船应用性能的研究,对螺旋桨防护涂层进行综合性能考察,为我国船舶螺旋桨空泡腐蚀和海生物污损提供完整有效的解决方案。
1 实验
螺旋桨防护涂层由防腐底漆、弹性缓冲漆、中间连接漆和防污面漆组成。螺旋桨防护涂层配套体系及各涂层相关性能指标如表1 所示。
表1 螺旋桨防护涂层组成及相关性能
在螺旋桨防护涂层体系中,各涂层分别发挥着不可替代的作用,并且在充分考虑各涂层的不同功用,有针对性对各涂层进行了相应的膜厚设计。其中防腐底漆需要实现对铜合金基材良好的封闭性、耐海水等介质渗透,从而达到较好的腐蚀防护作用,因此需要具有一定的膜厚,干膜为120μm 为宜。而弹性缓冲漆在螺旋桨防护涂层体系中主要起到缓冲空泡破灭时产生的压力脉动作用,空泡腐蚀对材料的破坏主要来自于空泡溃灭。微射流和冲击波是空泡腐蚀最主要的两种作用机制,或主或次,二者兼而有之。弹性缓冲漆能够有效吸收空泡溃灭时释放的强大能量,实现机械能与热能的转换,因此弹性缓冲漆的厚度不宜太薄。因为有机硅体系的防污面漆其附着力普遍较差,所以在弹性缓冲漆及防污面漆中间引入中间连接漆,实现从弹性缓冲漆到防污面漆的有效过渡,中间连接漆与弹性缓冲漆和防污面漆均具有较好的连接作用。有机硅弹性体防污面漆作为螺旋桨的第一道保护屏障,正面迎击溃灭的空泡,在缓冲空泡溃灭时冲击能的同时,发挥着防止污损生物粘附的作用,较低的表面能及弹性模量使污损生物即使粘附,也附着不牢固,在高速水流剪切作用下轻易脱除。随后本工作对螺旋桨防护涂层体系进行了实验室性能评价及实船考核验证等综合性能的研究。
1.1 表面形貌
采用浩视三维视频显微镜Hirox KH7700 对螺旋桨防护涂层体系进行表面形貌的观察,结合二维形貌及三维立体形貌对涂层表面状态进行全方位的考察。试验过程中,采用KLA Tencor 公司的P?6 探针式台阶测试仪考察涂层表面粗糙度的状况,其中二维粗糙度的扫描长度为5 000 μm,采用400 μm/ s 的扫描速度,施加压力为5 mg。而三维形貌扫描中扫描面积为5 000 μm×5 000 μm,采用4 000 μm/ s 的扫描速度,施加压力同样为5 mg。
1.2 接触角及表面能的测量
静态接触角的测量采用OCA 20 视频光学接触角测量仪(Dataphysics instruments GmbH,Germany) 在室温条件下进行[8] 。对于每个样品,测量三次取平均值。而螺旋桨防护涂层表面能通过将蒸馏水、乙二醇和环己烷的接触角值带入固体表面自由能计算软件获得。
1.3 水动力性能测试
螺旋桨具有异型曲面结构,而水动力性能直接影响到螺旋桨的推进效率,为了考察涂装螺旋桨防护涂层后对螺旋桨水动力性能的影响,在中国船舶工业船舶总体性能试验检测中心进行了涂装螺旋桨防护涂层前后扭矩系数及推力系数的变化情况测试,进一步考察螺旋桨模型涂覆螺旋桨防护涂层前后的水动力性能变化[9] 。
1.4 抗空蚀性能
船舶高速服役下,螺旋桨空蚀现象严重。而空蚀性能评价成为表征涂层性能的重要手段之一。采用超声波振动空蚀仪对抗空蚀性能进行评价,研究中采用符合螺旋桨实际应用工况的对冲方式对螺旋桨防护涂层抗空蚀性能进行考察,试验频率为20 kHz,振幅为25 μm,温度25 ℃,对冲间距2mm,记录样柱的质量随时间的变化[10] 。
1.5 静态防污性能
在青岛中港海洋化工研究院有限公司海上试验站进行螺旋桨防护涂层的静态实海挂板试验,对涂层表面附着生物物种进行归纳总结,研究污损海生物的附着规律,考察螺旋桨防护涂层的静态防污性能[11] 。
1.6 实船应用试验
在实船螺旋桨表面涂覆螺旋桨防护涂层,并及时跟踪记录试验结果。
2 结果与讨论
2.1 表面形貌
螺旋桨防护涂层采用污损释放型防污涂层作为防污面漆,污损释放型防污涂层属于非损耗型防污涂层,具有稳定的化学结构,因此能够在海洋环境下保持性能长期稳定,研究过程中通过与磨蚀损耗型自抛光防污涂层进行表面形貌及表面粗糙度的对比,考察螺旋桨防护涂层表面形貌。表2为螺旋桨防护涂层和自抛光防污涂层在实验室的转鼓型防污涂层动态性能测试装置进行为期1 个月的磨蚀后表面形貌对比。
表2 涂层表面形貌对比
由表2 发现,通过对比磨蚀30 d,随着磨蚀时间的延长,自抛光防污涂层逐渐水解,抛蚀出新的涂层,由明显的沟壑趋向于相对于较平整的状态发展,而性能稳定的螺旋桨防护涂层一直保持表面比较平滑的状态,这与两种涂层的防污机理具有直接的影响。自抛光防污涂层属于水解型的抛光磨蚀型涂层,随着水解行为的持续进行,具有一定凹凸形状的粗糙表面趋向于相对平滑的状态,而表面趋向于平滑的变化与水流体动力学也具有一定的关系。螺旋桨防护涂层为污损释放型防污涂层,为性能稳定的非损耗型涂层,较低的表面能及一定的弹性模量使其具有平滑的表面,而这种平滑的表面能够在较长时间内保持螺旋浆涂层性能稳定性。
基于此,本工作对螺旋桨防护涂层的三维表面形貌进行了观察,如图1 所示。
图1 (a)自抛光防污涂层和(b)螺旋桨防护涂层的三维表面形貌图
从图1 中可以看到,自抛光防污涂层表面具有较明显的尖锐突起,而螺旋桨防护涂层表面相对比较平滑,少有尖锐的粗糙表面的突起。从整体看来,螺旋桨防护涂层具有更加平滑的表面微观形貌。
表面粗糙度也是表面形貌的组成部分,一定形貌的特定结构可以减少污损生物分泌生物胶的浸润及铺展,从而发挥防止污损生物粘附的作用,同样符合水流体动力学的光滑表面还可以发挥减阻的作用。研究中,对螺旋桨防护涂层和自抛光防污涂层进行了表面粗糙度的观察,图2 分别给出两种涂层Ra(算术平均偏差)、Rq(均方根偏差)、Rt(波峰到波谷的最大距离)的数值。
图2 不同涂层粗糙度值对比图
算数平均偏差Ra 值能充分反映涂层表面微观几何形状,其值越大,说明表面越粗糙,相对于自抛光防污涂层的4 343 nm,螺旋桨防护涂层仅为59.66 nm。同样作为可以反映表面微观几何形状的均方根偏差Rq 也具有两个数量级的差距。而对于反映波峰到波谷最大距离的Rt 值同样存在较大的差距,其中自抛光防污涂层Rt 值为18 645 nm,而螺旋桨防护涂层为442.89 nm。表面粗糙度值的测量数值很好地印证了三维视频显微镜所获得两种涂层微观表面形貌观测结果,并且相对于传统自抛光防污涂层来说,螺旋桨防护涂层具有非常出众的平滑表面。平滑的表面能够有效减小污损海生物分泌粘液与涂层的实际接触面积,从而减弱其附着强度,增强其防污性能及脱附性能,同时能够有效降低涂层与海水之间的摩擦阻力,从而赋予涂层优良的减阻性能,对于减少燃油消耗及温室气体的排放具有重要意义。
2.2 接触角及表面能的测量
将涂覆有螺旋桨防护涂层的马口铁板置于水平工作台上,使用注射器将3 μL 的蒸馏水(或其他溶剂)滴于涂层表面。用CCD 视频系统捕获液滴轮廓的数字图像,如图3 所示,并获得接触角测量数值。
对于每个样品,测量三次取平均值。而涂层表面能通过将蒸馏水、乙二醇和环己烷的接触角值带入SCA21 固体表面自由能计算软件获得。其结果如表3 所示。
表3 螺旋桨防护涂层表面能及接触角测量
图3 液滴轮廓数字图像
表面能是评判螺旋桨防护涂层的重要参数,直接影响海洋污损生物在涂层表面的粘附(抵抗海洋生物有机分泌物在涂层表面的浸润和铺展)及脱附情况。拜耳曲线(如图4 所示)阐述了表面能与污损生物的粘附关系,并且经过大量的实验研究表明,当表面能为22~24 mJ·m-2时,污损生物具有相对最少的粘附。而螺旋桨防护涂层的表面能数值显示处于污损生物难以黏附的范围内。
图4 拜耳曲线
2.3 水动力性能测试
实验过程中空泡水筒开展了均流水动力测量试验,利用空泡水筒斜流动力仪对涂层桨进行水动力测量。采用空泡水筒试验,对涂覆螺旋桨防护涂层前后水动力性能进行考察,设定水筒内恒定水流速度为5.34 m/ s,改变螺旋桨模型的转速达到设定的进速比J(0.508~0.908),记录涂装螺旋桨防护涂层与未进行涂层涂装的桨模的推力系数Kt 和扭矩系数Kq。研究过程中,考察一定进速比下,推力系数和扭矩系数的变化,以此研究涂覆螺旋桨防护涂层前后对水动力性能的影响。如图5 所示,在不同进速比条件下,涂装螺旋桨防护涂层与未进行涂层涂装的桨模的推力系数和扭矩系数曲线趋于近似重合的状态,由此表明涂装螺旋桨防护涂层后对水动力性能基本没有影响。
图5 不同进速比下涂装涂层前后桨模推力系数和扭矩系数的关系
2.4 抗空蚀性能
为了更清楚地了解空蚀对螺旋桨铜合金基材的破坏,采用超声波振动空蚀仪对螺旋桨铜合金基材进行了200 min 的空蚀试验,空蚀后铜合金样柱的表面形貌如图6 所示:
图6 空蚀后铜合金基材的表面形貌
从图6 中可以看到经过200 min 空蚀后,铜合金基材具有明显的空蚀坑,并且表面粗糙度急剧增大。同时,实时跟踪铜合金基材空蚀600 min 过程中的失重情况,如图7 所示。
图7 空蚀试验中铜合金基材的失重情况
从图7 中可以看到,200 min 后铜合金基材失重31 mg,400 min 时失重184 mg,而经过600 min 之后,基材失重达351mg。并且随着空蚀时间的延长,空蚀对铜合金基材造成的持续性破坏加剧,基材失重现象日益严重。同时从整个失重曲线中可以看出, 前期失重率小些, 随着铜合金基材表面保护层一旦被破坏,空泡腐蚀造成的基材破坏现象更加严重,从而表现为基材失重率明显增加。同时对于采用的螺旋桨防护涂层进行了抗空蚀性能的研究,图8 为对冲100 h 后,螺旋桨防护涂层表面形貌的变化。观察发现,经过100 h 的对冲空蚀试验后,出现个别的空蚀坑,涂层表面仅有轻微失光现象。
图8 对冲空蚀100 h 后涂层的表面形貌
图9 涂层样柱失重随空蚀时间的变化曲线
试验过程中,对螺旋桨防护涂层进行了对冲空蚀100 h样柱失重情况的跟踪观察,从图9 中可以看到,配套涂层空蚀初期的失重较为明显,之后出现的质量增加是由测量误差所致。100 h 的对冲空蚀后,样柱失重小于5 mg。
2.5 静态防污性能
在青岛中港海上试验站进行了螺旋桨防护涂层静态防污性能的考察,图10 为静态实海挂板32 个月,冲刷前后涂层表面的状态。
图10 螺旋桨防护涂层的静态实海挂板照片
从图10 中可以看到,冲刷前涂层表面已有大量的污损海生物粘附,形成稳定的生物群落,以海藻居多,另有些许海鞘和藤壶。经过海水冲刷后,涂层表面附着的污损海生物可轻易脱落,涂层仍维持良好的表面状态,以右侧最后两块样板配方最优。
2.6 实船应用试验
图11 为某船进坞维护时螺旋桨表面海生物污损情况。从图11 中可以看到,螺旋桨表面附着有大量的藤壶、管虫等污损海生物,已形成重度钙质污损(NSTM 污损等级90?100),已对推进效率产生显著影响。将螺旋桨表面附着的污损海生物清除,并对螺旋桨基材进行表面处理,然后涂装螺旋桨防护涂层。
图11 某船进坞维护时螺旋桨表面海生物污损情况
图12 为螺旋桨防护涂层服役6 个月后的表面状态照片。涂层体系表面未见任何污损海生物,涂层整体仍然非常完整,仅导边处涂层出现小面积区域破损情况,但未出现膜下扩散现象。
图12 螺旋桨防护涂层服役6 个月后的表面状态照片
图13 为螺旋桨防护涂层服役16 个月后的表面状态照片。配套涂层体系整体仍然较为完整,由于该船进坞维护前在港内停泊了2~ 3 个月,涂层表面附着有较多的污损海生物。经过高压水清洗后,涂层表面附着的污损海生物可轻易被冲刷掉。同时可以看到,清洗后水珠难以在涂层表面铺展开,涂层仍维持较低的表面能。导边处涂层出现边缘区域破损现象,但未发生膜下扩散现象,随边处涂层仍然非常完整。由此可见,螺旋桨防护涂层对于抑制海生物附着污损及缓解空蚀危害,维持螺旋桨推进效率具有重要的作用。
图13 螺旋桨防护涂层服役16 个月后的表面状态照片
3 结论
本工作所研制的螺旋桨防护涂层,不含任何防污毒剂,对施工人员健康和海洋环境安全环保;抗空泡腐蚀和防污作用效果明显,整体换装和局部修补方便,对保障螺旋桨推进效率,延长服役寿命具有重要的意义,能够为我国船舶螺旋桨提供一种简便高效的空泡腐蚀和海生物污损解决方案。
参考文献
1 Tom Dinham Peren. Maritime Engineering, 2010, 163(4), 182.
2 Lee Jeung Hoon, Park Hyoung Gil, Kim Jin Hak, et al. Ocean Enginee?ring, 2014, 77, 23.
3 计志也, 陆芳. 船舶性能研究, 1996(4),1.
4 吕秀芬, 王海龙, 谢春生, 等.华东船舶工业学院学报,1997(11),23.
5 David Owen, Yigit Kemal Demirel, Elif Oguz, et al. Ocean Engineering,2018, 159(1), 505.
6 Schultz M P, Bendick J A, Holm E R, et al. Biofouling, 2011, 27(1),87.
7 Michael P. Biofouling, 2007, 23(5), 331.
8 史洪微, 刘福春, 韩恩厚, 等. 中国材料进展,2014(2), 95.
9 王波, 张以良, 熊鹰. 武汉理工大学学报,2015, 39(4),773.
10 陈大融.中国基础科学,2010(6), 3.
11 Emin Korkut, Mehmet Atlar. Ocean Engineering, 2012, 41, 1.
免责声明:本网站所转载的文字、图片与视频资料版权归原创作者所有,如果涉及侵权,请第一时间联系本网删除。
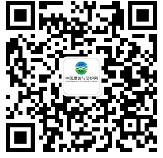
官方微信
《腐蚀与防护网电子期刊》征订启事
- 投稿联系:编辑部
- 电话:010-62316606-806
- 邮箱:fsfhzy666@163.com
- 腐蚀与防护网官方QQ群:140808414