城镇燃气管道是燃气运输的主要工具,其随着社会的快速发展而得到了普及,由于早期的施工工艺和技术标准不健全,导致技术档案资料缺失、对埋地钢制燃气管道管理难度较大,并且在燃气管道运行的过程中,常常会受到各种因素的影响,进而发生故障,如果发生泄漏不能及时发现,发生爆炸事故,将给社会带来巨大危害。
第三方破坏是最主要的因素,与城市和燃气公司管理水平直接相关;腐蚀虽然直接导致的事故较少,但由于腐蚀跟时间有关,如果腐蚀导致泄漏不能及时发现,其导致的后果比第三方破坏更严重。
管道腐蚀最为严重的一般是电化学腐蚀,主要体现方式为在金属管道表面形成腐蚀坑,导致管道变薄,在压力作用下形成裂纹或者鼓包,也可使腐蚀部位的组织发生变化,严重时会引起管道爆裂,使管道的输送能力降低,管道的使用寿命缩短,导致费用增加和意外事故发生。
项目概况
检测项目位于辽宁省盘锦市,该项目主要对其所管辖的部分中压钢质燃气管道进行全面检验。管道全长2.592公里,设计压力0.4MPa,防腐层材料为3LPE,管道无阴极保护系统,2006年6月投入使用,至今已运行14年。
通过前期对所检管道的初步了解,该项目管道运行时间较长,存在很多安全隐患,尤其是架空管道部分,存在防腐层剥离、支架损坏、支架与管道焊接处锈蚀严重、管道变形现象,通过资料审查发现上次全面检验报告设计压力为1.6MPa,与设计资料不符,实际检测发现运行压力在0.6MPa左右波动,存在超压运行现象。并且管道无阴极保护系统,这样很难确定管道的腐蚀情况,因此安全寿命的管道腐蚀检测是本次项目的重点之一。
燃气管道腐蚀检测
1 管道宏观检查
宏观检查主要包括位置与走向检查、泄漏检查、管道沿线地表环境调查、地面标志检查、管道附属设施的检查、穿(跨)越检查。
宏观检查基本符合要求,其中:
1、部分埋地管段缺少地面标志;
2、部分埋地管段埋深不足,埋深最浅处为辽河油田宝石花医院食堂东15米,埋深0.23m;
3、兴油街金河小区南侧院墙外高压开关柜占压;
4、辽河油田油气集输公司院内西侧、螃蟹沟河桥跨越北侧、辽河油田宝石花医院西侧3处出土端防腐层破损,管体存在锈蚀现象;
5、振兴小区院内架空管段防腐层剥离、支架损坏、支架与管道焊接处锈蚀、南侧管段变形。
2 土壤腐蚀环境的检测
土壤中存在着液体、空气、盐分等,尤其是沿海地区,土壤中含盐量、含水量比较高,使土壤成为复杂的电解质,是引起埋地燃气管道外腐蚀的重要因素,土壤的腐蚀性由含盐量、含水量、土壤电阻率、pH值、氧化还原电位等决定,现场主要进行土壤质地测试、土壤电阻率测试、管道自然电位测试、氧化还原电位测试,其它参数通过取样后送实验室分析。对一处土壤进行腐蚀性调查,土壤成分测试结果如下:电阻率44.8Ω。m,pH值8.14,质地为砂土,含水量14.5%,含盐量1.2g/kg,土壤Cl-0.056mg/kg,自然腐蚀电位(vs.CSE)-504mV,氧化还原电位(vs.CSE)115mV,腐蚀性评价得分为13分。
根据GB/T 19285-2014《埋地钢质管道腐蚀防护工程检验》中第4.2对土壤腐蚀性进行评价,土壤腐蚀性评价等级见表1,经评价:土壤腐蚀性为3级(中)。
表1 土壤腐蚀性评价等级
3 防腐层状况的检测
对于早期敷设的钢质燃气管道,由于受到防腐作业水平和材料性能限制,外防腐层形式比较单一并且整体质量不高,通过分析电化学腐蚀原理,可以知道敷设外防腐层是为了增大宏观原电池腐蚀电流回路中的电阻,减小腐蚀电流,从而达到保护管体的目的,外防腐层的整体安装质量、第三方破坏及运行中的自然老化,部分管道外防腐层损耗严重,在一些杂散电流较多的地区,会对燃气管道造成严重腐蚀。
采用交流电压梯度法和电流衰减法对管道进行外防腐层检测,本次检测包括防腐屋破损点检测和防腐层整体质量状况检测。根据GB/T 19285-2014《埋地钢质管道腐蚀防护工程检验》附录K,在不开挖检验情况下对外防腐层状况进行评价,可采用防腐层电阻率(Rg值)、破损点密度(P值)、电流衰减率(Y值)等作为评价指标进行评价,本次检验选取破损点密度(P值)作为评价指标进行评价,评价指标见表2。
表2 外防腐层破损点密度P值(处/100m)分级评价
本次检测的埋地管道总长度2592m,检测出防腐层破损点4处,破损点密度P=0.15,评价结果为2级。
4 管道阴极保护状况的检测
埋地管道腐蚀防护的常规方法是阴极保护法,阴极保护法分为强制电流保护和牺牲阳极保护,强制电流保护法是由外部电源提供保护电流,将埋地钢质燃气管道和外加电流负极相连,来降低管道的腐蚀速率,达到保护管道的目的,牺牲阳极保护法是在埋地钢质燃气管道连接电位更负的金属(锌、镁等)作阳极,与埋地钢质燃气管道在电解质溶液中构成大电池,而使埋地钢质燃气管道阴极极化,达到保护管道的目的。
由于本次检测的管道无阴极保护系统,开挖处管地电位为-0.5040V,管道未受保护,因此评价结果为不合格。
5 杂散电流检测
杂散电流分为交流杂散电流和直流杂散电流,对埋地钢制燃气管道影响最大的是直流杂散电流干扰,使埋地钢质管道防腐层破损处腐蚀速率增大,对于干扰严重的区域(地铁、路面交通系统等),短时间内就可以使埋地钢质燃气管道腐蚀穿孔,造成泄漏,如果不及时发现,将会危害群众生命财产安全。
01 杂散电流交流干扰
本次检测采用万用表、CSE参比电极,利用埋地管道出土端测得管道交流干扰电压最大值为0.0924V,检测结果见表3:
表3 杂散电流交流干扰检测结果(V)
02 杂散电流直流干扰
采用土壤表面电位梯度法测得土壤表面电位梯度为22.98mV/m,杂散电流直流干扰程度为强,检测结果见表4:
表4 杂散电流交流干扰检测结果
6 开挖检测
对检测出的处防腐层破损点进行开挖,验证防腐层间接检测的准确程度,确定管体腐蚀状况,开挖点照片见图1。
图1 破损点现场开挖照片
在开挖条件下对管体腐蚀状况进行调查,采用超声波测厚仪、涂层测厚仪、里氏硬度计、卡尺等工具对管体腐蚀缺陷测量,对焊缝处进行超声波无损检测,同时对腐蚀产物分析,调查腐蚀产生的原因,通过开挖检测发现开挖处防腐层剥落,管体存在局部腐蚀坑,打磨后,采用超声波测厚仪对腐蚀坑进行壁厚检测,实测最小壁厚为2.08mm。
管道检测结果分析
1 埋地钢质管道腐蚀防护系统模糊综合评价
基于宏观检查、土壤腐蚀性、埋地钢制燃气管道外防腐层状况、阴极保护有效性、杂散电流干扰等全面检验基础上,对埋地钢质燃气管道腐蚀防护系统进行模糊综合评价,计算出S=77.94,按照GB/T 19285-2014《埋地钢质管道腐蚀防护工程检验》中附录M埋地钢质管道腐蚀防护系统分级,位于区间70≤Ci<80中,表明该段埋地钢质燃气管道的腐蚀状况综合评价结果为3级。
2 埋地钢质管道剩余寿命预测
依据国家标准进行管体的腐蚀速率以及剩余寿命预测,经计算RL=2.77,在腐蚀速率不增加的情况下,预测管道剩余寿命为2.77年,根据TSG/D 7004-2010《压力管道定期检验规则—公用管道》第29条全面检验周期不能超过预测的管道剩余寿命的一半,因此下次全面检验周期为1年。
3 全面检验结论及建议
① 立即降低使用工作压力;
② 对埋地管道加装阴极保护系统和采取直流排流保护措施,使其得到有效保护;
③ 修复埋地管段防腐层破损点;
④ 对局部减薄处进行修复;
⑤ 对架空管段防腐层剥离、支架损坏、管段变形进行修复;
⑥ 加强日常巡线工作,加强应急抢险队伍及装备的投入工作。
总结
随着人民安全意识的提高,国家和使用单位对埋地钢制燃气管道的安全运行越来越重视,同时随着管道数量逐年增加,使用单位对埋地钢制燃气管道的安全管理形势也是越来越严峻,埋地钢制燃气管道的本体安全显得更为重要,正确检测与评价管道的腐蚀状况,并对含腐蚀缺陷管道进行适用性评价,是管道安全运行的重要保证。
免责声明:本网站所转载的文字、图片与视频资料版权归原创作者所有,如果涉及侵权,请第一时间联系本网删除。
相关文章
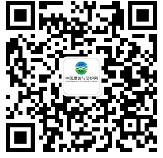
官方微信
《腐蚀与防护网电子期刊》征订启事
- 投稿联系:编辑部
- 电话:010-62316606-806
- 邮箱:fsfhzy666@163.com
- 腐蚀与防护网官方QQ群:140808414
点击排行
PPT新闻
“海洋金属”——钛合金在舰船的
点击数:8148
腐蚀与“海上丝绸之路”
点击数:6486