1 环境障涂层的产生和发展
未来航空发动机正朝着更高推重比和更高热机效率的方向发展,实现此目的最关键的因素就是提高发动机的涡轮端或燃烧室进口温度。但是提高燃气室温度之后会给固有的机械零件带来不利的影响[1-3]。譬如,燃烧室温度的增加会让高压涡轮热端部件的表面温度大幅度提高[4-5]。众所周知,由于硅基非氧化物陶瓷(SiC/Si3N4)具有低密度、高强度、高模量、抗氧化、抗烧蚀、对裂纹不敏感的特点,因而被认为是取代发动机热端部件中镍基高温合金的理想材料[6]。在发达国家,各种SiC陶瓷基复合材料航空发动机的热端部件已经通过技术验证或成功应用。 GE公司已经在LEAP发动机上应用了CMC涡轮罩环,以及在GE9X上应用了CMC涡轮导向叶片和高压涡轮转子叶片,GE [7] 视航空发动机热端部件使用SiC/SiC为重大创新和核心技术。如图1 所示,就是SiC/SiC复合材料(CMC)在航空发动机上的典型应用。由于硅基非氧化物陶瓷自身的不耐高温水氧腐蚀的特性,因此需要施加涂层予以保护,因此环境障涂层(Environmental barrier coatings, EBCs)技术可以作为弥补硅基材料不足的一项重要手段。
图1 SiC/SiC复合材料在航空发动机上的应用[8]
EBCs涂层的功能就是在发动机恶劣环境中对基体材料起到保护作用,阻止或减小发动机环境对高温结构材料性能的影响。 EBCs涂层材料本身必须具备以下几个特点:
(1) 涂层材料应该具有较高的熔点,能够保证涂层材料直接接触外界高温环境而不发生失效。
(2) 涂层材料与基体材料之间应该具有良好的机械结合力,保证涂层体系与基体以及涂层体系内部各层之间不发生剥落。
(3) 涂层材料应具有良好的表面稳定性以及较低的氧渗透能力,以避免其与环境气体发生反应并尽可能抑制氧气与基体材料发生接触。
(4) 涂层材料应与基体材料具有相近的热膨胀系数(CTE)。如果热膨胀系数相差较大,那么在热循环过程中会产生热应力,导致裂纹及分层甚至造成剥落。
(5) 涂层材料在高温条件下尽量不能发生相变。相变通常会导致体积的变化,进而导致涂层开裂甚至剥落。
(6) 涂层材料应该具有较好的化学稳定性和耐腐蚀性,避免生成不稳定相并且能够抵抗发动机恶劣环境的腐蚀。
(7) 涂层要致密、均匀、微孔隙和微裂纹少, 在保证具有抗氧化、耐腐蚀能力的前提下,密度应该尽可能低[9],以达到飞行器减重轻量化需求。
基于以上7 个特点,EBCs的发展大致可以分为4 个阶段:第一代EBCs是以莫来石(Mullite)为主要涂层材料。因为Mullite与硅基陶瓷的热膨胀系数接近,并且化学相容性较好,因此成为了早期EBCs研究的主要对象,但是由于莫来石抗水蒸气能力相对较差,莫来石作为单一环境障涂层显然是不够的;第二代是以莫来石为中间层,YSZ作为表面层的多层结构,但是由于YSZ层和莫来石的热膨胀系数相差太大。第三代EBCs是以莫来石作为中间层,BSAS((1-x)BaO-xSrO-Al2O3-2SiO2, 0≤x<1)作为表层的多层结构涂层,其主要缺点是在1300℃以上,就要与SiO2 发生反应,在1400℃ 以上BSAS涂层就会大量的和水蒸气发生反应然后过早的失效;第四代EBCs的材料研究热点转向了稀土硅酸盐体系[10];在2010 年之后,未来的第五代EBCs将会发展到T/EBCs体系。从性价比的角度而言,第二、三、四代EBCs体系并不是对上一代体系的升级。而是由于在更加严苛的服役条件下产生的下一代EBCs。例如,服役温度在1200℃ 以下的航空器,莫来石/YSZ这一代的EBCs性能很稳定,足以抵抗水蒸气和CMAS的腐蚀,就无需选择加入稀土涂层(如图2)。
图2 环境障涂层选材历史流程图及常见的环境障涂层
图3 直观地体现了EBCs对陶瓷基复合材料温度性能的影响。早期的EBCs由莫来石结合层和钇稳定氧化锆(YSZ) 表面涂层组成。由于莫来石密度低,导热系数低,抗氧化能力强,化学相容性好,热膨胀系数与SiO2 相近,适合成为EBCs的材料。由于莫来石在高温环境下与水蒸气严重腐蚀的缘故,莫来石不能作为顶层涂层。结果表明,钇稳定氧化锆(YSZ)在水蒸气中的稳定性较好。因此,采用等离子喷涂技术将ZrO2-8%Y2O3 喷涂于莫来石层之上。但是由于热膨胀系数(CTE)不匹配,在EBCs系统中产生了热应力, 导致了涂层的失效。因此BSAS和稀土掺杂或改性涂层开始成为研究的方向。
图3 EBCs对陶瓷基复合材料温度性能的影响[13]
文中主要从EBCs的选材和EBCs涂层抗CMAS、水氧腐蚀失效和热冲击失效等国内外相关方面的研究进展进行归纳和总结,并系统阐释了涂层失效机制,并从模拟计算角度概述了相关研究进展,并且为今后的EBCs研究指明方向。
2 EBCs的选材
当前的研究主要集中研究稀土涂层对于CMAS腐蚀和水蒸气腐蚀的防护问题,这涉及到如何选材的问题,目前可用作未来环境障涂层的候选材料主要有莫来石/YSZ、莫来石/BSAS、莫来石/Re2 SiO5、莫来石/Re2 Si2O7。涉及到的体系主要有镱酸盐(Yb)、镥酸盐(Lu)、铪酸盐(Hf)等系列[14]。通过不同的稀土元素掺杂可实现抗腐蚀能力以及热膨胀系数的调控,但目前制备的大多是环境障氧化物块体材料,用作环境障涂层材料相对较少,很多学者通过第一原理的方法对不同稀土掺杂得到的结构的热导率进行了大量的计算,包括电子结构计算、能带计算、声子谱计算,试图寻找有良好的抗CMAS腐蚀和抗水蒸气腐蚀的晶体结构,用作环境障涂层候选材料,同时结合分子动力学对这些结构的热膨胀系数进行了计算。 Zhilin Tian等[15]通过第一性原理计算了β-Y2 Si2O7,γ-Y2 Si2O7,β-Yb2 Si2O7 和 β-Lu2 Si2O7 的弹性势能和导热系数,从而给EBCs的选材提供依据,如图4 所示,反映了模拟得出的最小的晶格导热系数,通过算得最小的晶格导热系数为设计EBCs材料选择提供理论支持。刘金玲[16] 通过第一性原理计算的方法,给出了双稀土硅酸盐材料(Re2 Si2O7)作为EBCs涂层抗水氧腐蚀能力的排布情况。运用密度泛函理论(DFT)的不足是计算的范围尺度较小,这个计算条件和实际工况条件下的情况不相符。不过此结果能为EBCs的选材提供很好的指导作用,并且文中所提出的计算方法可以为今后的EBCs材料对于水蒸气腐蚀行为给出理论上的参考值。虽然现在发表的文献主要以Yb2 Si2O7和Yb2 SiO5 为主,但是国内外学者也对EBCs的选材进行了积极的探索,Wang等[17] 对YPO4 进行了研究,并发现YPO4 在高温条件下水蒸气的腐蚀和熔盐耐腐蚀能力也有很良好的效果。高熵合金也是学者选择材料的热点, Yu Dong等[18]采用溶胶-凝胶法制备了一种新型的高熵材料( Yb0.2Y0.2Lu0.2 Sc0.2Gd0.2)2 Si2O7,长时间暴露在1400℃ 的水蒸气中, 高熵陶瓷(5RE0.2)2 Si2O7 没有发生分解证实了其在水蒸气环境中具有良好的化学稳定性。同时,此材料与Cf/Si复合材料在高温下热膨胀系数与基体也差异较小。这个结果说明,未来高熵陶瓷也可以作为EBCs选材的方向之一。
图4 计算的各向异性最小导热系数[15]
3 等离子喷涂环境障涂层失效的方式
设计EBCs涂层初衷是抵抗高温水蒸气失效,保护碳化硅陶瓷基复合材料。但是由于近年来我国面临空气污染的严峻形势,CMAS失效已经成为我国飞机发动机涡轮叶片失效的主要方式。因此CMAS(CaO-MgO-Al2O3-SiO2)失效和水氧腐蚀失效都变成了EBCs的研究重点。 CMAS失效是指航空器在飞行过程中不可避免地经过风沙聚集或者有火山灰残留的空域。在发动机运转过程中,这些粉尘沉积到叶片上时, 在高温下, 熔融的高温粒子通过涂层表面存在的裂纹和孔隙渗入到环境障涂层内部,冷却形成玻璃态物质造成的表层剥落及层间易开裂问题而使得涂层失效,学者们对CMAS腐蚀进行了全方位的研究。水氧腐蚀失效是由于航空发动机燃料中由于含有大量的水蒸气,基体SiC/CMC表面会生成SiO2 保护膜, SiO2 与水蒸气发生反应,且会随气流的加剧反应加剧。此外,航空器高温部件在服役过程中存在启动、加力、巡航等多种状态,因此需满足能应对热冲击的要求,EBCs涂层抗热震的性能同样值得关注。
3.1 CMAS失效
CMAS失效研究经历了长时间的发展。早期的学者对BSAS涂层与高温冲蚀进行了研究[19-20]。此时,有的学者把其作为连接莫来石层的重点,研究CMAS腐蚀对于莫来石层的影响[21]。现在大多数学者对表层稀土层进行腐蚀研究。甚至有的学者从CMAS的粒子的角度进行研究,发现CMAS粒子越光滑,那么涂层越不容易和CMAS粒子进行反应,这样的研究不能为工艺生产提供帮助。学者们对CMAS腐蚀的研究取得很大进展,但是高于1400℃的情况下,试验所取得数据结果不理想。现在的学者对于CMAS失效机理的研究主要集中于EBCs稀土涂层的部分,归因于Yb元素在水氧腐蚀中的良好表现。
Kendra [19]在2007 年时就已经用BSAS与CMAS进行反应,发现在1300℃下经历1~4 h的腐蚀,CMAS就已经渗入涂层BSAS的内部,如图5,这很明显的说明BSAS-EBCs很容易受到钙镁铝硅酸盐( CMAS) 熔体的攻击,显然仅使用BSAS作为顶层涂层材料是远远不够的。复合涂层中有莫来石层,莫来石结构如图6。 Jang等[21] 以CMAS的条件,对莫来石单独进行腐蚀的模拟,发现了火山灰中的Fe是对莫来石腐蚀的主要元素,但是Na元素对破坏烧结态莫来石起着决定作用。如图7,烧结态莫来石在CMAS腐蚀下经过1400℃ 热处理2 h后的图像。可以从EDS图中很明显发现反应层中存在Na、Mg、Fe、 Si、Al、Ca元素。 Nadia L.Ahlborg等[22]分别研究了Yb2 SiO5(YbMS)和YSi2O7 的表面层在1500℃ 的环境下与CMAS发生反应,发现CMAS与YbMS表面层先和晶界发生反应,并且在高温作用下,由于扩散作用Al、Ca、Mg、Si元素向能量低的晶界进行偏聚。并且发现了Ca2Yb8(SiO4)6O2这个相,这是由于CMAS中的CaO与YbMS反应所生成的。通过研究发现,YSi2O7 表面层与CMAS反应同样存在和YbMS一样的挥发问题。
图5 BSAS/SiC试样在1300℃ 热处理后CMAS的BSE图像[19]
图6 莫来石的晶体结构示意图[9]
图7 烧结态莫来石经1400℃ 热处理2 h后与冰岛VA(试验中的CMAS)反应生成SEM图像和EDS图谱[21]
同时YSi2O7 生成了Ca2Y8(SiO4)6O2。从而导致的涂层失效。 Valerie等[23] 却发现在1400℃ 以上,YSi2O7 作为单独的EBCs材料在抗CMAS方面是无效的,反应式如下:
(1)
关于Ca2Y8(SiO4)6O2 的研究,也有很多学者首先用XRD等测试方法去测得其晶体结构,然后用第一性原理计算的方法计算其热力学的一些性质[24-25]。 F.Stolzenburg等[26] 发现Yb2 SiO5(YbMS) 和Yb2 Si2O7(YbDS) 与CMAS的反应机理不同,通过对比晶体的质量分数在一段时间内的衰退度表征YbDS的反应速度相对较慢。虽然文章中没有给出合理的解释,为什么YbDS比YbMS反应速度相对较慢,但是作者给出了两种推测:反应物的结晶度对速率的影响和反应产物的热力学稳定性的不同。 Hengbei Zhao等[27] 关于YbDS和YbMS与CMAS给出详尽的说明。如图8,在顶层涂层中既有YbDS和YbMS时,由于两者的反应机理不同,CMAS先于YbMS进行反应。如图9,同时也指出了CMAS中的Ca是以非晶相为途径进行扩散,渗入涂层进行反应,反应物通过非晶相为途径扩散到表层,此现象与F.Stolzenburg的观察到的过程是一致的。
图8 CMAS与YbDS顶涂层反应后的BSE图像。磷灰石相首先渗透到SiO2 耗尽(对比度较低的YbMS) 区域的涂层中,并与涂层中未反应的YbDS颗粒混合[27]
图9 设想的CMAS与YbMS和YbDS APS涂层之间的反应机理示意图[27]
关于YbDS与YbMS的相和结构的问题,E.Garcia等[28]解释了YbMS两种形态的转变,结晶促使了晶粒数的增加,高温进而增加了晶体体积,从而使涂层膨胀。涂层的演化动力学,亚稳态和相变对涂层的热力学性能有很大的影响,特别是热导率和热膨胀行为,可以用来获得最合适和稳定的相。并且给出了对于喷涂YbDS与YbMS比较合理的工艺流程。 Fengrui Jiang等[29] 基于反应结晶的腐蚀机理合理解释样品在1200℃下经过4 h的CMAS腐蚀,如图10 所示, 并且阐述了Si-O中的距离比RE-O中的距离短, 因此SiO4 四面体的结构更加稳定,而且RE-O键比Si-O键更容易断裂。因此,在CMAS腐蚀下, RE-O键在高温下容易被破坏。
图10 RE2 SiO5-CMAS系统腐蚀机理的示意图[29]
3.2 水氧腐蚀失效
在高温服役环境中的航空发动机,由于燃料中或者在空气中含有大量的水蒸气,水蒸气和SiC和SiO2 发生反应, 生成容易挥发的Si(OH)4,此物质极容易被航空发动机产生的高速气流带走。使得Cf/SiC直接暴露在高温燃气的环境之中[30]。
在干燥空气或氧气的高温下,硅基非氧化物与氧气反应,形成薄的保护二氧化硅( SiO2) 层, 以防止进一步氧化。然而在燃烧环境中,水蒸气与二氧化硅层形成挥发性氢氧化硅(Si(OH)4), 高温和高的燃烧气体的速度会导致严重的表面退化。
SiC陶瓷与高温水汽的反应公式如下所示:
Si3N4 陶瓷与高温水汽的反应公式如下所示:
针对水氧腐蚀失效问题Fan-Jie Feng等[32] 在莫来石层加入Yb2 SiO5 之后,发现表面致密度变高了,并且随着Yb2 SiO5 含量的增多,表面的气孔率变得越来越小,由此Fan-Jie Feng等得出结论,Yb2 SiO5 有助于抗水蒸气腐蚀。 Bradley T.Richards等[33] 用稀土研究水蒸气失效的机理。如图11,由于涂层受到横向约束,水蒸气腐蚀之后体积的减小导致了多孔的表层。图4( a)展示了这种腐蚀的初始阶段,随着暴露时间的延长, SiO2 挥发所产生的孔隙会一直延伸到涂层之中, 从而扩展成气路的通道。这个通道同时是水蒸气进入和Si(OH)4 溢出的通道。图4(b)显示了水蒸气腐蚀进行到后期的情况。可以很明显得出,在YbDS/Si界面形成热氧化物( TGO) SiO2形成了较大的残余应力。贺世美等[30,34] 在研究YbMS抗水蒸气腐蚀时候发现涂层的失效过程是从未出现裂纹和剥落到部分宏观裂纹在较集中的区域出现并且伴随着涂层向外翘曲,最后边缘部位涂层出现了剥落。这些过程与他在研究BSAS抗水蒸气腐蚀过程是一样的。 YbMS在等离子喷涂之后并没有发生相结构的变化,在恒温氧化之后出现了Al2Yb4O9(单斜相) 和BaO2(四方相)。可以得出由于扩散作用YbMS在高温下与BSAS发生反应,同时YbMS也与水蒸气发生反应的结论。 Nadia Rohbeck等[35] 直接将YbDS喷涂在SiC/CMC之上,在1400℃ 的水蒸气的腐蚀下,即使等离子喷涂涂层含有很高的孔隙率, YbDS层也能很好地有效的保护SiC/CMC基底, 腐蚀仅仅在Si/YbDS界面发生。试验还观察到TGO层的存在,由于TGO是裂纹的集中地,因此黏结性能就会降低,YbDS层会过早的发生剥落。以上两个结果很好的阐述了一个观点:单一的EBCs在保护基体材料能力有限,需要构筑多层结构体系。鲁琳静等[36] 研究发现BSAS涂层在工作温度1250℃、气流条件为50%H2O-50%O2、压力为1.013 ×10 5 Pa进行100 h腐蚀处理, 涂层和复合材料都没有受到明显的腐蚀,经高温热震也没有发生涂层的开裂和剥落。并且与没有加上BSAS涂层经过相同条件下进行对比(如图12)经过100 h的高温水氧腐蚀,Cf/SiC的表面生成了几微米厚的SiO2 层,并且存在大量的微裂纹,这层SiO2 会与高温环境中的水反应生成挥发性的Si(OH)4,使得SiC被进一步的氧化。在图13 中,发现BSAS涂层致密,与基底结合良好, 涂层本身材料没有发生明显的腐蚀。这说明BSAS与基底有良好的热匹配性。这个结果与Lee的结论基本吻合[2]。如图14,可以明显看出在经历工作温度为1300℃的200 h的热循环中, BSAS涂层没有受到明显的破坏,Lee给出了在小于工作温度1300℃,200 h腐蚀的情况下,BSAS涂层与基体能结合良好的范围区间。 Emine Bakan等[37]的试验中以YbDS-YbMS为喷涂顶层,其中阐述了YbDS与H2O(g)反应生成YbMS的结论。因为他们发现,原来致密的YbDS样品表面形成了连续的YbMS层。并且表明在高温水蒸气下,YbMS比YbDS有更加强的挥发性,同时又指出YbMS比YbDS有更好的耐水蒸气腐蚀性[37-38]。该结果为在特定工况条件下EBCs涂层的研究提供参考方向:如失效原因偏向于高速气流,则应该考虑使用YbDS的涂层;同理如水蒸气是失效的主要因素,那么EBCs的选择,则倾向于YbMS涂层。
图11 二氧化硅挥发机理示意图,在暴露的YbDS表面形成YbMS多孔表面层,蒸汽循环后在硅键膜上形成TGO层[33]
图12 Cf /SiC水氧腐蚀形貌(1250℃,50%H2O-50%O2,100 h,1.013 ×10 5 Pa) [36]
图13 Cf /SiC-BSAS水氧腐蚀形貌(1250℃, 50%H2O-50%O2, 100 h, 1.013 ×10 5 Pa) [36]
图14 莫来石/BSAS为涂层制备的SiC在循环水蒸气炉(200 h, 1300℃, 2 h cycle, 90%H2O/O2, 1 atm) [2]
3.3 热冲击失效
当EBCs用于旋转部件时,需要承受可能导致蠕变变形和断裂的大量静态载荷和循环载荷, 这样的环境是先进材料系统所必须经历的最严峻的环境之一。热冲击失效就是飞机发动机用涂层中的一种最常见的失效方式之一。热冲击是指由于急剧加热或冷却,使物体在较短的时间内产生大量的热交换,温度发生剧烈的变化时, 该物体就要产生冲击热应力[39]。针对热冲击失效,Lee等[40]将SiC陶瓷管在1200℃进行淬火实验,系统地对SiC陶瓷管的热冲击性能进行了实验评估。通过对SiC陶瓷管断裂形貌的观察,发现SiC陶瓷有沿晶断裂的特点,且温度梯度越高越容易断裂。 C.V.Cojocaru等[41] 运用材料自修复的思想,对BSAS涂层在1300℃的高温水蒸气环境下进行了循环热考核,以2 h为一个循环考核时间,进行了100 个热循环测试,研究结果发现在高温条件下BSAS涂层能够发生裂纹自修复,试验测试记录了EBCs在高温水蒸气热循环时对应的硬度和弹性模量,这些结果可以为涂层服役行为的模拟计算提供重要的数据支持。 Wang等[42-43]在多孔隙的Si3N4 基体表面喷涂了Y2O3、SiO2、Al2O3 的混合物,从实验的结果发现抗热冲击性能随着烧结温度的升高而提高。 Han等[44]发现YbDS与YbMS混合有很好的抗热冲击性能,并给出失效的原因是因为在热冲击试验过程中产生拉引力,形成裂纹或者是因为在相变过程形成氧化物的体积收缩而导致。作者解释了为什么两种化合物的混合会让抗热冲击能力提升。在热喷涂过程中产生的气泡会让抗热冲击能力的提升。较高的摩尔分数的YbDS会让涂层有更高的断裂韧性和更高的抗裂纹扩展的能力。许振华等[45]同样在1300℃研究了热冲击的行为, 当EBCs涂层由室温急剧加热至1300℃时,涂层内生长的非连续微裂纹,有利于残余应力得到局部释放。然而,涂层长期在1300℃ 的加热环境及反复多次循环快速冷却条件下,涂层内的残余应力不断累积,当应力积累到一定程度时将引起EBCs涂层的微裂纹不断扩展并产生桥联现象,形成宏观裂纹,并最终导致EBCs涂层剥落失效。因此,由于EBCs涂层材料热膨胀系数的差异,涂层内残余应力随着热冲击时间的延长而不断积聚。同时涂层受到的应力也不断增加,二者的交互作用,使EBCs涂层内部出现的裂纹数量越来越多,裂纹宽度也不断增大,从而易于导致EBCs涂层过早剥落失效。这样的失效的过程和3.1 中贺世美等人提到失效的过程相似。许振华同样发现了莫来石中的Al元素由于扩散作用向外进行扩散。
X.F.Zhang [46-47]在研究热冲击的过程中发现用一层致密的铝膜作为过渡层可以很好的抗击热冲击腐蚀。铝与二氧化硅原位反应后,由于氧化铝晶粒中存在氧空位,试样表面呈灰色。在工作温度为1100℃ 热冲击试验55 个循环后的同一试样,除边缘效应导致边缘有一小块散裂区域外,表面无明显裂纹、翘曲和散裂。此外,在热冲击试验中,随着氧的部分消失,灰色表面逐渐变白。这种设计方法很新颖,目前第三代环境障涂层的开发要是寻求能够承受温度更高的顶层材料,但在更高的温度作用下,中间层会与顶层材料发生相互反应[48],如果以Al2O3 作为过渡层既能抵挡热冲击,由于氧化铝已经达到饱和还能使莫来石中Al元素不与基底发生反应。这样的过渡层同样适用于YbMS/YbDS层与莫来石层中,这样就可以防止Al元素和稀土层发生反应从而减缓失效的过程。但是这个实验有弊端,实验温度太低只有1100℃,并且进行热冲击的次数太少,只进行了55 次,更加的可靠的结论还需要未来做实验继续考证。
4 失效控制
通过上述分析失效机制,可以发现CMAS失效主要是由于高温粒子与基体发生化学反应所产生不良的反应物。失效的形式是因为反应物与基体的性能不同导致缺陷(气孔、裂纹、未熔融粒子等)的产生和发展。缺陷的主要表现形式集中表现的是微小的横向裂纹造成的剥落或者是造成的较深纵向裂纹致使复合涂层体系的失效。对于水氧腐蚀和高温热震两种情况, 失效的形式更是由于裂纹的萌生和扩展所导致的。由于裂纹所产生涂层失效是最为常见的失效方式。因此对于裂纹修复的问题值得大家关注。
裂纹的产生不可避免。国内外学者一直努力将EBCs涂层服役的时间延长,让涂层能在更加严苛的环境下服役。如何控制失效是普遍研究的科学问题,针对裂纹的控制,有的学者提出自修复的观点,涂层自修复是在不使用外加补修材料的情况下,在裂纹的初始阶段就对破损的地方进行一定程度的修复,这对延长涂层的时间、保证基材的机械强度等有着十分重要的意义[49]。 Chen [50] 在Y2 Si2O7 加入TiSi2,让裂纹中充斥着TiSi2 阻碍氧气和水蒸气的进入,从而让失效的过程减缓。
Joana Mesquita-Guimars等[51]用有限元有效地模拟出了不同组分的莫来石/YSZ层复合而成的3 种多层涂层体系,计算了中心、边缘和角部的应力分布。该模型有助于识别裂纹的位置;Bradley T.Richards等[52]用有限元模拟的方法计算出了裂纹的能量释放率,结合实验并得出关于裂纹的结论:裂纹大多终止于多孔Si键涂层中的孔隙中,借助孔隙的位置可以改变裂纹的生长方向,从而使裂纹不会形成纵向裂纹; 适当的孔隙还可以解决热膨胀失配的问题,为承受膨胀提供空间,降低弹性模量从而拥有更好的抗应变容限的性能,失效机制汇总表如表1 所示。
针对裂纹的控制,模拟计算能给试验带来很好的辅助。在模拟计算过程中,可以优化BSAS、稀土硅酸盐的成分得到更有利于抗水氧腐蚀的条件。为了让EBCs涂层在高温热震的条件下能服役更长的时间。有限元模拟同时可以优化复合涂层的厚度,得到最小的残余应力值;通过优化界面处的形貌,获得最小的残余应力值也是常用的方法。计算优化出的界面形貌,可以通过合适的加工工艺生产出优化的界面形貌,得到残余应力值小且结合力优异的涂层。在模拟仿真计算过程中,可以引入适当的裂纹,通过裂纹扩展动力学,通过在裂纹尖端处布置气孔等缺陷,钝化裂纹尖端的应力集中,其主要原理是如果裂纹尖端遇到气孔,则气孔能吸收裂纹,致使裂纹停止生长。若裂纹尖端遇到第二相,则裂纹改变裂纹生长方向。由此能发现一些缺陷确实能使裂纹的扩展变缓慢或者改变裂纹的生长方向。
在实际喷涂过程中,可以采用此类方法。在锁定计算过程中可能产生应力集中的地方, 在实际生产中可以适当的改变气体流量、改变路径的工艺方法布置设计的缺陷。再结合原位声发射技术,分析应力集中处是否存在想要布置的气孔或者第二相。通过这样的方式可以延缓裂纹的扩展。但是实际工况条件下,裂纹的萌生不是单独一条的出现,可能是多条裂纹的同时出现,现在的计算模拟仿真只能设置一条裂纹或者设置裂纹与裂纹之间不能发生相互作用的边界条件。未来的计算模拟仿真的研究方向应该向裂纹与裂纹的相互作用方面进行研究与探索。
表1 EBCs典型的失效机制汇总表
失效的控制还有包括其他方面,针对涂层结合力方面,一般来说衬底材料表面粗糙度越大, 衬底材料的表面积越大,机械结合强度越强。借助飞秒激光在SiC/SiC-CMC表面上加工微槽结构,这样的工艺首先不会出现传统的边缘裂纹和纤维拉拔现象;再者EBCs涂层与CMC表面形成了互锁结构[58]。
失效的控制还包括造粒方面,造粒工艺通常有3 种方式: 造粒烧结工艺、粉体造粒工艺、熔融破碎工艺。有的学者还提出粉体造粒工艺对涂层质量的影响,造粒烧结工艺制备粉体具有工艺过程简化、粉体质量好、相稳定性高等优点,更适合于等离子喷涂的要求[12]。在喷涂过程中工艺参数的优化。针对喷涂设备的一系列的工艺改善,都可以对失效进行有效的控制。
5 展望
EBCs涂层虽然已经发展到了第三代,但是还没有完全成熟,发展的方向依然有很多。在标准的指定方面,对于EBCs抗水氧腐蚀目前还没有制定出一套统一完备的国际或国内标准,包括企业自用的标准。在文献中提到的关于水氧腐蚀实验中设定的温度、气压、气体流量、循环次数等一系列的参数设定各异,不能让科研工作者做统一的比较,因此亟待在标准的制定方面得到统一;其次,关于EBCs的高温服役寿命预测方面还没有得到充分的发展,计算机模拟仿真技术可以通过施加时间载荷以及边界条件得到一些参数甚至形成一定规模的数据库,从而可以为寿命的预测提供相应的参考。
在深入理解等离子体喷涂环境障涂层的高温失效机制后,才能够对材料的成分结构及制备工艺方面进行优化。涂层之所以在高温条件下发生失效,归根结底就是涂层本身发生了劣化, 涂层内部或界面发生了损伤。涂层为了抵抗其内部的损伤,必然会释放弹性应变能,表现出裂纹的萌生、扩展和传播,发射弹性应力波,降低其本身的自由能。因此,基于涂层失效机制的涂层成分结构优选及工艺优化同样至关重要。
5.1 EBCs材料结构设计及工艺优化
基于涂层高温失效机制的材料成分结构优选方面,通过结合第一性原理和宏观有限元的模拟设计出新的EBCs涂层,从而拓宽EBCs的材料选择。目前学者大多是以Yb、Lu、Y等稀土元素为主,但是稀土的含量有限。 EBCs的应该向普通元素、聚合物和高熵陶瓷方向发展。 X.F.Zhang [47]发现Al2O3 可以作为EBCs层,可以作为高温下阻碍莫来石中Al和SiC的一道阻隔,可以有效地控制热氧化物(TGO)的扩展,这个可以为涂层的设计提供思路。 Pedro Hern??ndezRodríguez等[59]研究了复合材料聚碳硅烷(PCS) 的相关性能,发现Al的加入会使涂层的疏水性增加。现在的多层涂层中用莫来石,莫来石中含有Al元素,高温下扩散运动在所难免,这个恰巧能使PCS的疏水性能上升。从疏水性角度出发, 可以给未来环境障的防护水蒸气腐蚀一些启发。在涂层的结构设计方面,仿生结构增韧、多层膜结构增韧、优化涂层梯度增韧可以成为高性能EBCs的设计方案。
基于涂层制备工艺创新及优化方面,不能局限于等离子喷涂这一种方法。可以采用等离子和其他方法联合使用,张小锋等[60] 采用等离子喷涂-物理气相沉积技术(PS-PVD)得到的涂层孔隙率低、高致密度且莫来石非晶化的现象不明显,Laura R.Turcerl等[52] 提出了T/EBCs的概念,T/EBCs是在EBCs涂层之上再复合一层TBC涂层材料[61],从而面向高于1 650℃ 的工况环境的新方向,如图15,直观地体现了T/EBCs的构造。黄璇璇等[8] 认为,PS-PVD有可能成为新一代T/EBCs制备的主要方法;Sivakumar Ramasamy等[62]采用基于浆料的浸渍涂覆工艺和烧结工艺;宋涛等[63]采用溶胶凝胶法制备莫来石溶胶, 通过高温煅烧获得莫来石涂层得到的EBCs在研究中相对研究比较少,这些研究都是给工艺创新方面提供了很好的思路。
进一步,在对材料的成分结构及工艺优化完成之后,就要考察涂层全方位的性能,甚至包括涂层室温条件下的性能。室温下性能的好坏一定程度上也会反映涂层的高温性能。涂层的室温力学性能研究方面,同样有很多方法值得进一步探索和发展。 Yuto Aoki等[64]重点研究涂层的分层韧性和涂层结合力。 Yutaro Arai [ 等65] 更进一步地通过剪切加载试验,测定了EBCs体系的分层韧性。传统的方法还有鼓包法、压痕法、屈曲等方法测定涂层的一些机械性能[66-67]。
图15 T/EBCs概念示意图[52]
5.2 EBCs服役性能模拟计算与无损测试表征
随着计算材料科学及无损表征技术的发展, 未来在EBCs的性能研究方面可以采用计算机模拟方法对涂层在极端服役条件下的性能进行评估,对涂层的真实服役寿命进行预测。在模拟计算的同时还可以辅助采用无损表征的手段对涂层的残余应力,内部缺陷进行静态和动态的测量与监测。
计算模拟技术可以为EBCs的发展可以提供温度场、应力值、蠕变、界面优化等方面计算,在研究EBCs的现阶段,文献中所报道的相关计算结果相对比较少,通过有限元或者边界元等一系列的方法,模拟水氧腐蚀、高温粒子冲蚀等一系列的腐蚀情况。为涂层服役性能测试试验的展开提供相对应的参考以及补充。
在无损表征方面, 通过原位声发射技术[68-70]、Micro-CT、中子散射的方法等表征EBCs涂层的裂纹、气孔和夹杂等一系列的缺陷。原位声发射技术通过采用在燃烧器试验台试验过程中同时采集声发射信号的方法。通过对声发射信号的分析,得到了裂纹的扩展规律。为了获得真实有效的反映裂纹扩展和涂层变形的声发射信号,采用了滤波技术来排除燃烧器试验台过程中的噪声干扰。基于有效声发射信号的特征波形,采用快速傅里叶变换(FFT)和小波变换对其幅值和频率的关键分布范围进行分析[71]。声发射技术能较好地检测动态裂纹的扩展,有利于监测涂层裂纹的实时动态扩展信息,从而能更好地预测涂层的服役寿命,已经成为研究EBCs失效过程的非常重要的无损测试表征手段之一。通过对声发射信号的分析,建立EBCs内部裂纹扩展的声发射信号特征参数(能量、幅值、振铃计数、计数率等)与时间之间的关系,同时分析声发射信号特征参数之间的关联,结合裂纹扩展的典型的声发射信号的波形图,运用声发射信号分析方法(快速傅里叶变换,小波(包)分析,神经网络等),建立裂纹扩展的声发射信号特征参数与裂纹扩展模态的动态联系。
Micro-CT在不破坏样品的前提下,获取材料的二维断层序列图。再结合水平集方法拓展到3D空间实现3D图像分割获取材料的三维分析模型,建立了反映涂层实际界面形态和孔隙分布的三维微观结构模型。 Wang等[72] 已经将此技术应用于涂层单轴拉伸损伤和破坏的三维空间演化过程。 A.K.Agrawal等[73]使用Micro-CT对在SiC上使用化学气相沉积的涂层进行孔隙的测定,并指出在未来此技术可以用于研究衬底表面均匀性和微观结构孔隙度对微观结构的影响。
中子散射技术是指中子弹性散射,它可以有效地研究纳米到微米尺度材料的静态结构。中子散射技术有助于研究封闭孔隙,主要是非常小的孔隙(粒内孔隙)。此外,原位中子散射技术提供在高温情况下孔隙微观结构的信息[74]。在TBCs方面有所报导,用于EBCs检测孔隙率相关文献报道的较少。中子散射技术以其无损、深度测量的独特优势被航空公司所青睐。以此评估不同制造和加工制造工艺的有效性。飞机制造商空客公司已使用中子散射技术多年,主要用于研究涂层界面处结构的完整性,分析并评估它们是否适用于未来的飞行器。 Anand Kulkarni等[75]早在2006 年就提出使用中子散射技术去测涂层的孔隙率。 Chris Petorak等[76] 使用中子散射技术确定层间的孔隙和构件内部的微小裂纹。
5.3 基于材料基因工程与机器学习加快EBCs的发展进程
未来对EBCs的研究将借助材料基因组及人工智能,机器学习的思想及研究范式,即通过多尺度计算,高通量试验表征以及数据库,机器学习等手段的相互结合与融合,形成EBCs研究从原子分子层次到宏观连续介质体尺度的自下而上的设计再到全生命周期的考核应用全链条贯通的研究范式。从多尺度计算来看,就微观方面,主要借助第一原理从头算的基本思想,基于密度泛函理论,从原子电子层次筛选有望用作具有更高性能的EBCs材料,从电子结构计算层面, 如能带性质,声子,电子的输运性质,计算弹性模量,剪切模量,导热系数等,结合分子动力学的手段,构造原子之间相互作用的势函数,计算在不同温度点的热膨胀系数和不同温度点的热扩散系数,计算的这些性质都可以作为基本参数存入数据库,从试验上合成这些待筛选的新型EBCs材料,同时结合试验表征的手段,测试材料的性能,存入数据库。利用这些数据库,构造材料的本构,从介观上,构造晶粒模型,计算其在高温烧结过程中的晶粒生长动力学,模拟晶粒生长的热力学与动力学。同时采用宏观有限元模拟的手段,基于连续介质力学模型,计算EBCs在制备过程如等离子体喷涂过程中的残余应力分布及演化规律,对EBCs涂层的各层厚度进行优化,同时对涂层在高温服役过程中的温度场应力场变化进行模拟计算。此外,EBCs涂层通常还服役在CMAS侵蚀,高温水氧腐蚀以及高温循环热冲击等多工况共存的条件,其外部边界条件是一个高度非线性多物理场耦合的环境,因此,需要借助有限元模拟计算的手段计算涂层在此多因素耦合的环境条件下的性能演化行为。包括温度场、应力场的变化,以及裂纹在此服役条件下的动态扩展行为。由于涂层的失效最直接因素就是由于裂纹的萌生,扩展和传播造成的,因此未来EBCs在高温服役条件下裂纹扩展的动态行为研究将是EBCs研究的重要方向之一。通常来说, 模拟涂层内部或界面处的裂纹扩展行为主要手段有扩展有限元法(Extended finite element method, XFEM), 虚拟裂纹闭合技术( Virtual crack closure technique, VCCT) 以及粘聚力单元模型(Cohesive zone model, CZM) 3 种技术。通过对EBCs内部或及界面处的裂纹扩展模拟,构造裂纹扩展的运动学方程,建立裂纹扩展速率da/dt与时间t之间的函数关系,就能够对涂层在高温服役过程中的寿命进行预测。此外,采用原位声发射技术能够对涂层在高温服役过程中的裂纹扩展行为进行实时动态的监测,建立声发射信号参数(如幅值、能量、累计能量、计数率、振铃数、中心频率、峰值频率等)与裂纹扩展行为之间的动态联系。同时可结合采用数字图像相关技术(Digital image correlation, DIC)对涂层在高温承载过程中的应变行为进行监控,通过应变的变化计算,计算涂层的屈曲失效行为。此外,通过Micro-CT技术能够实现整个涂层在三维空间微缺陷(微孔隙和微裂纹)的动态演化行为分析,进一步结合中子衍射技术,能够对涂层各个位置处的应力进行测量计算,对整个涂层的应力分布有较为全面的掌握。基于计算与测量的结果,制定涂层制备工艺参数优化的主攻方向。由于涂层制备工艺参数往往有多个独立或协同变量,因此, 采用机器学习方法,建立参数库集合与涂层性能之间的动态联系,利用大数据技术,聚类分析,神经网络等机器学习算法,实现EBCs制备工艺优化,这些都将是未来EBCs研究与应用的新型研发范式。
参考文献
[1] 刘巧沐,黄顺洲,何爱杰.碳化硅陶瓷基复合材料环境障涂层研究进展[J].材料工程,2018,46(10):1-8.
LIU Q M,HUANG S Z,HE A J.Development on anti-oxi-dation modification of CMC-SiC composites matrix and coat-ing[J].Journal of the Chinese Ceramic Society,2018,46(12):1700-1706(in Chinese).
[2] LEE K N.Current status of environmental barrier coatings for Si-based ceramics [J].Surface & Coatings Technology,2000,133:1-7.
[3] 李其连,崔向中.航空表面涂层技术的应用与发展[J].航空制造技术,2016,14:32-36,46.
LI Q L,CUI X Z.Applications and development trends of a-viation coatings[J].Aeronautical Manufacturing Technology,2016,14:32-36+46(in Chinese).
[4] 刘巧沐,黄顺洲,何爱杰.碳化硅陶瓷基复合材料在航空发动机上的应用需求及挑战[J].材料工程,2019,47(2):1-10.
LIU Q M,HUANG S Z,HE A J.Application requirements and challenges of CMC-SiC composites on aero-engine[J].Journal of Materials Engineering,2019,47(2):1-10(in Chinese).
[5] 黄光宏,王宁,何利民,等.环境障涂层研究进展[J].失效分析与预防,2007(1):59-64.
HUANG G H,WANG N,HE L M,et,al.Development of environmental barrier coatings on Si-based ceramics [J].Failure Analysis and Prevention,2007(1):59-64(in Chi-nese).
[6] 潘牧,南策文.SiC 基材的抗氧化腐蚀涂层的研究现状与方向[J].材料保护,1999(10):1-3.
PAN M,NAN C W.Oxidation barrier coatings on SiC sub-strate[J].Materials Protection,1999(10):1-3(in Chi-nese).
[7] PADTURE N P.Advanced structural ceramics in aerospace propulsion[J].Nature Materials,2016,15:804-809.
[8] 黄璇璇,郭双全,姚改成,等.航空发动机 SiC/SiC 复合材料环境障碍涂层研究进展 [J].航空维修与工程,2017.
HUANG X X,GUO S Q,YAO G C.et al.Research progress of environmental barrier coatings of SiC/SiC composite for aero-engine[J].Aviation Maintenance & Engineering,2017(in Chinese).
[9] 路明辉,冯志海,周延春.硅基非氧化物陶瓷表面环境障涂层的研究进展[J].陶瓷学报,2015,36(2):107-118.
LU M H,FENG Z H,ZHOU Y C.Recent research progress on environmental barrier coatings for non-oxide ceramics[J].Journal of Ceramics,2015,36(2):107-118(in Chinese).
[10] 王岭,焦健,焦春荣.陶瓷基复合材料环境障涂层研究进展[J].航空制造技术,2014(6):50-53.
WANG L,JIAO J,JIAO C R.Research progress of environ-mental barrier coatings for SiC ceramic matrix composites [J].Aeronautical Manufacturing Technology,2014(6):50-53.(in Chinese).
[11] GUIMAR?ES J M,GARCíA E,MIRANZO P,et.al.Mul-lite-YSZ multilayered environmental barrier coatings tested in cycling conditions under water vapor atmosphere[J].Surface & Coatings Technology,2012,209:103-109.
[12] 焦春荣,焦健,陈大明,等.BSAS 喷涂粉体制备工艺及其对涂层性能的影响[J].材料工程,2016,44(8):51-57.
JIAO C R,JIAO J,CHEN D M,et al.Preparation of BSAS powders and its effect on properties of coatings[J].Journal of Materials Engineering,2016,44(8):51-57(in Chinese).
[13] XU Y,HU X X,XU F F,et al.Rare earth silicate environ-mental barrier coatings:Present status and prospective[J].Ceramic International,2017,43(8):5847-5855.
[14] LIU J,ZHANG L T,LIU Q M,et al.Calcium-magnesium-aluminosilicate corrosion behaviors of rare-earth disilicates at 1400 ℃ [J].Journal of the European Ceramic Society,2013,33:3419-3428.
[15] TIAN Z L,ZHENG L Y,ZHAO J L,et al.Exploration of the low thermal conductivities of gamma-Y2 Si2O7,beta-Y2Si2O7,beta-Yb2Si2O7,and beta-Lu2Si2O7as novel envi-ronmental barrier coating candidates[J].Journal of the Eu-ropean Ceramic Society,2016,36(11):2813-2823.
[16] WANG Y G,LIU J L.First-principles investigation on the corrosion resistance of rare earth disilicates in water vapor [J].Journal of the European Ceramic Society,2009,29:2163-2167.
[17] WANG Y G,CHEN X H,LIU W,et al.Exploration of YPO4 as a potential environmental barrier coating[J].Ceram Int,2010,36(2):755-759.
[18] DONG Y,REN K,Lu Y H,et al.High-entropy environ-mental barrier coating for the ceramic matrix composites[J].Journal of the European Ceramic Society,2019,39(7):2574-2579.
[19] GRANT K M,KR?MER S,L?FVANDER J P A,et al.CMAS degradation of environmental barrier coatings [J].Surface & Coatings Technology,2007,202(4-7):653-657.
[20] HARDER B J,Joaquin R R,Jonathan D A,et al.Chemical and mechanical consequences of environmental barrier coat-ing exposure to calcium-magnesium-aluminosilicate [J].Journal of the American Ceramic Society,2011,94:178-185.
[21] JANG B,FENG F J,SUZUTA K,et al.Corrosion behavior of volcanic ash on sintered mullite for environmental barrier coatings [J].Ceramics International,2017,43:1880-1886.
[22] AHLBORG N L,ZHU D M.Calcium-magnesium aluminosil-icate(CMAS)reactions and degradation mechanisms of ad-vanced environmental barrier coatings[J].Surface & Coat-ings Technology,2013,237:79-87.
[23] WIESNER V L,HARDE B J R,BANSAL N P.High-tem-perature interactions of desert sand CMAS glass with yttrium disilicate environmental barrier coating material[J].Ceramic International,2018,44(18):22738-22743.
[24] PENG C,KANG X J,LI G G,et al.Fabrication and lumi-nescence properties of Ca2RE8(O4)6O2:Pb21,Dy 31 (RE5Y,Gd)n one-dimensional phosphors by electrospinning method[J].Journal of the Electrochemical Society,2011,158:J208-J214.
[25] SUN Z H,WANG M Q,YANG Z,et al.Crystal structure and luminescence properties of Bi3 + activated Ca2Y8 (SiO4)6O2 phosphors under near UV excitation[J].Journal of Solid State Chemistry,2016,239:165-169.
[26] STOLZENBURG F,JOHNSON M T,LEE K N,et al.The interaction of calcium-magnesium-alumino silicate with yt-terbium silicate environmental barrier materials[J].Surface & Coatings Technology,2015,284:44-50.
[27] ZHAO H B,RICHARDS B T,Levi C G,et al.Molten sili-cate reactions with plasma sprayed ytterbium silicate coatings [J].Surface & Coatings Technology,2016,288:151-162.
[28] GARCIA E,LEE H,SAMPATH S.Phase and microstruc-ture evolution in plasma sprayed Yb2 Si2O7 coatings [J].Journal of the European Ceramic Society,2019,39:1477-1486.
[29] JIANG F R,CHENG L F,WANG Y G.Hot corrosion of RE2 SiO5 with different cation substitution under calcium-magnesium-aluminosilicate attack [J].Ceram Int,2017,43:9019-9023.
[30] 贺世美,牟仁德,陆峰,等.BSAS 环境障涂层抗水蒸汽性及其失效机理[J].失效分析与预防,2011,6(1):44-49.
HE S M,MU R D,LU F,et al.Vapor resistance and failure mechanism of BSAS environment barrier coatings[J].Failure Analysis and Prevention,2011,6(1):44-49.(in Chi-nese).
[31] 王超,乔瑞庆,吴玉胜,等.Si 基陶瓷表面环境障涂层的研究进展[J].中国陶瓷工业,2017,24(2):28-33.
WANG C,QIAO R Q,WU Y S,et al.Developments of en-vironmental barrier coatings on the Si-based ceramics [J].China Ceramic Industry,2017,24(2):28-33(in Chi-nese).
[32] FENG F J,JANG B K,PARK J Y,et al.Effect of Yb2 SiO5 addition on the physical and mechanical properties of sintered mullite ceramic as an environmental barrier coating material [J].Ceramic International,2016,42(14):15203-15208.
[33] RICHARDS B T,YOUNY K A,FRANCQUEVILLE F D,et al.Response of ytterbium disilicate-silicon environmental barrier coatings to thermal cycling in water vapor[J].Acta Materialia,2016,106:1-14.
[34] 贺世美,熊翔,何利民.新型 Yb2 SiO5 环境障涂层 1400 ℃ 高温氧化行为[J].材料工程,2015,43(4):37-41.
HE S M,XIONG X,HE L M.High temperature oxidation behavior of new Yb2 SiO5 environmental barrier coatings at 1400 ℃ [J].Journal of Materials Engineering,2015,43(4):37-41(in Chinese).
[35] ROHBECK N,MORRELL P,XIAO P.Degradation of ytter-bium disilicate environmental barrier coatings in high temper-ature steam atmosphere[J].Journal of the European Ceramic Society,2019:3153-3163.
[36] 鲁琳静,成来飞,洪智亮,等.Ba0.25 Sr0.75Al2 Si2O8 环境障碍涂层的制备与耐水腐蚀性能研究[J].无机材料学报,2011,26(7):701-706.
LV L J,CHENG L F,HONG Z L,et al.Fabrication and water-vapor corrosion resistance of Ba0.25 Sr0.75Al2 Si2O8 envi-ronmental barrier coating[J].Journal of Inorganic Materials,2011,26(7):701-706(in Chinese).
[37] BAKANA E,SOHNA Y J,KUNZ W,et al.Effect of pro-cessing on high-velocity water vapor recession behavior of Yb-silicate environmental barrier coatings[J].Journal of the Eu-ropean Ceramic Society,2019,39(4):1507-1513.
[38] NGUYENA S T,NAKAYAMAB T,SUEMATSU H,et al.Self-healing behavior and strength recovery of ytterbium disil-icate ceramic reinforced with silicon carbide nanofifiller [J].Journal of the European Ceramic Society,2019,39:3139-3152.
[39] SEO H I,KIM D,LEE K S.Crack healing in mullite-based EBC during thermal shock cycle[J].Coatings,2019(9):585.
[40] LEE Y,MCKRELL T J,KAZIMI M S.Thermal shock frac-ture of silicon carbide and its application to lwr fuel claddingperformance during reflood [J].Nuclear Engineering and Technology,2013,45(6):811-820.
[41] COJOCARU C V,LéVESQUE D,C.MOREAU,et al.Per-formance of thermally sprayed Si/mullite/BSAS environmen-tal barrier coatings exposed to thermal cycling in water vapor environment [J].Surface & Coatings Technology,2013,216:215-223.
[42] WANG C,WANG H J,QIAO R Q,et al.Fabrication and thermal shock resistance of β-Si3N4-based environmental barrier coating on porous Si3N4 ceramic[J].Ceramic Inter-national,2016,42:14222-14227.
[43] WANG C,CHEN M,WANG H J,et al.Fabrication and thermal shock resistance of multilayer Y2Si2O7environmental barrier coating on porous Si3N4 ceramic[J].Journal of the European Ceramic Society,2016,26:689-695.
[44] HAN J,WANG Y F,LIU R J,et al.Thermal shock be-havior of mixed ytterbium disilicates and ytterbium monosili-cates composite environmental barrier coatings[J].Surface & Coatings Technology,2018,352:348-353.
[45] 许振华,何利民,戴建伟,等.新型 La2Zr2O7 环境障涂层的 1300 ℃热冲击行为研究[J].真空,2014,51(3):20-25.
XU Z H,HE L M,DAI J W,et al.Investigation of new La2Zr2O7 environmental barrier coatings on high temperature thermal shock behave at 1300 ℃ [J].Vacuum,2014,51(3):20-25(in Chinese).
[46] 张小锋,周克崧,刘敏,等.大气等离子喷涂环境障涂层镀Al表面改性[J].中国材料进展,2018,37(12):978-984,993.
ZHANG X F,ZHOU K S,LIU M,et al.Al-modified envi-ronmental barrier coating prepared by atmospheric plasma spray[J].Materials China,2018,37(12):978-984,993(in chinese).
[47] ZHANG X F,ZHOU K S,LIU M,et al.Oxidation and ther-mal shock resistant properties of Al-modified environmental barrier coating on SiCf/SiC composites [J].Ceram Int,2017,43(16):13075-13082.
[48] 范金娟,常振东,陶春虎.环境障涂层失效机理研究进展 [J].失效分析与预防,2017,12:386-391.
FAN J J,CHANG Z D,TAO C H.Research progress of fail-ure analysis of EBCs[J].Failure Analysis and Prevention,2017,12:386-391(in Chinese).
[49] WANG L,SHAO F,ZHONG X H,et al.Tailoring of self-healing thermal barrier coatings via finite element method [J].Applied Surface Science,2018,431(60-74).
[50] CHEN Y G,LU Y H,YE Q,et al.A self-healing environ-mental barrier coating:TiSi2-doped Y2Si2O7/barium stronti-um aluminosilicate coating[J].Surface & Coatings Technol-ogy,2016,307:436-440.
[51] MESQUITA G J,GARCIA E,OSENDI M I,et al.Effect of ag-ing on the onset of cracks due to redistribution of residual stres-ses in functionally graded environmental barrier coatings of mul-lite/ZrO2[J].Compos Part B-Eng,2014,61:199-205.
[52] TURCER L R,PADTURE N P.Towards multifunctional thermal environmental barrier coatings(TEBCs)based on rare-earth pyrosilicate solid-solution ceramics [J].Scripta Mater,2018,154:111-117.
[53] LEE K N,ELDRIDGE J I,ROBINSON R C.Residual stres-ses and their effects on the durability of environmental barrier coatings for SiC ceramics[J].J Am Ceram Soc,2005,88:3483-3488.
[54] NASIRI N A,PATRA N,JAYASEELAN D D,et al.Water vapour corrosion of rare earth monosilicates for environmental barrier coating application[J].Ceram Int,2017,43:7393-7400.
[55] AHLBORG N L,ZHU D M.Calcium-magnesium alumino-silicate(CMAS)reactions and degradation mechanisms of advanced environmental barrier coatings[J].Surface & Coat-ings Technology,2013,237:79-87.
[56] TIAN Z L,REN X M,LEI Y M,et al.Corrosion of RE2Si2O7(RE =Y,Yb,and Lu)environmental barrier coat-ing materials by molten calcium-magnesium-alumino-silicate glass at high temperatures [J].Journal of the European Ce-ramic Society,39:4245-4254.
[57] ZHONG X,NIU Y R,LI H,et al.Thermal shock resistance of tri-layer Yb2 SiO5/Yb2 Si2O7 /Si coating for SiC and SiC-matrix composites[J].Journal of the American Ceramic So-ciety,2018,101:4743-4752.
[58] ZHAI Z Y,WANG W J,MEI X S,et,al.Effect of the sur-face microstructure ablated by femtosecond laser on the bond-ing strength of EBCs for SiC/SiC composites [J].Optics Communications,2018,424:137-144.
[59] HERNáNDEZ R P,LóPEZ H E.Polymer derived SiC envi-ronmental barrier coatings with superwetting properties[J].Ceramics International,2017,43(14):11289-11295.
[60] 张小锋,周克崧,刘敏,等.等离子喷涂-物理气相沉积 Si/莫来石/Yb2 SiO5 环境障涂层 [J].无机材料学报,2018,33(3):325-330.
ZHANG X F,ZHOU K S,LIU M,et al.Preparation of Si/Mullite/Yb2 SiO5 environment barrier coating(EBC)by plas-ma spray-physical vapor deposition(PS-PVD)[J].Journal of Inorganic Materials,2018,33(3):325-330(in Chi-nese).
[61] XU J,Sarin V K,Basu S N.Dixit stability of interfaces in hybrid EBC/TBC coatings for Si-based ceramics in corrosive environments[J].International Journal of Refractory Metals and Hard Materials,2015,49:339-349.
[62] RAMASAMY S,TEWARI S N,LEE K N,et al.Slurry based multilayer environmental barrier coatings for silicon carbide and silicon nitride ceramics-I.Processing [J].Surface & Coatings Technology,2010,205(2):258-265.
[63] 宋涛,罗瑞盈.环境障涂层用莫来石涂层材料的制备和表征研究[J].中国陶瓷工业,2017,24(1):1-5.
SONG T,LUO R Y.The preparation and characterization of mullite coating material for environmental barrier coating[J].China Ceramic Industry,2017,24(1):1-5(in Chinese).
[64] AOKI Y,INOUE J,KAGAWA Y,et al.A simple method for measurement of shear delamination toughness in environ-mental barrier coatings[J].Surface & Coatings Technology,2017,321:213-218.
[65] ARAI Y,AOKI Y,KAGAWA Y.Effect of cristobalite for-mation on the delamination resistance of an oxide/Si/(SiC/SiC)environmental barrier coating system after cyclic hightemperature thermal exposure [J].Scripta Mater,2017,139:58-62.
[66] KAKISAWA H,NISHIMURA T.A method for testing the in-terface toughness of ceramic environmental barrier coatings(EBCs)on ceramic matrix composites(CMCs)[J].Jour-nal of the European Ceramic Society,2018,38:655-663.
[67] 杨丽,谭明,周文峰,等.航空发动机涡轮叶片热障涂层冲蚀试验装置的研制[J].装备环境工程,2016,13(3):48-56.
YANG L,TAN M,ZHOU W F,et al.Development of ero-sion equipment for turbine blade with thermal barrier coatings in aeroengine [J].Equipment Environmental Engineering,2016,13(3):48-56(in Chinese).
[68] 史慧扬,李海洋,王召巴,等.基于小波包能量谱的声发射信号处理技术[J].测试技术学报,2019,33(3):201-208.
SHI H Y,LI H Y,WANG Z B,et al.Acoustic emission sig-nal processing technology based on wavelet packet energy spectrum[J].Journal of Test and Measurement Technology,2019,33(3):201-208(in Chinese).
[69] 李雪换,底月兰,王海斗,等.基于声发射技术的热障涂层损伤行为[J].材料导报,2018,32(19):3368-3374.
LI X H,DI Y L,WANG H D,et al.Failure behavior of thermal barrier coatings based on acoustic emission technique [J].Materials Reports,2018,32(19):3368-3374(in Chinese).
[70] 刘战伟,朱文颖,石文雄,等.热障涂层无损检测技术进展[J].航空制造技术,2016(4):43-47.
LIU Z W,ZHU W Y,SHI W X,et al.Progress in the non-destructive testing of thermal barrier coatings[J].Aeronauti-cal Manufacturing Technology,2016(4):43-47(in Chi-nese).
[71] WANG L,MING C,ZHONG X H,et al.Prediction of criti-cal rupture of plasma-sprayed yttria stabilized zirconia thermal barrier coatings under burner rig test via finite element simu-lation and in-situ acoustic emission technique [J].Surface & Coatings Technology,2019,367:58-74.
[72] WANG L,LIU Y B,LI G J,et al.Simulation of damage and failure processes of thermal barrier coatings subjected to a u-niaxial tensile load [J].Materials and Design,2015,86:89-97.
[73] AGRAWAL A K,SARKAR P S,SINGH B,et al.Applica-tion of X-ray micro-CT for micro-structural characterization of APCVD deposited SiC coatings on graphite conduit [J].Ap-plied Radiation and Isotopes,2016,108:133-142.
[74] STRUNZ P,SCHUMACHER G,VA?EN R,et al.In situ small-angle neutron scattering study of La2Zr2O7 and SrZrO3 ceramics for thermal barrier coatings [J].Scripta Mater,2006,55:545-548.
[75] KULKARNI A,GOLAND A,HERMAN H,et al.Advanced neutron and X-ray techniques for insights into the microstruc-ture of EB-PVD thermal barrier coatings[J].Materials Sci-ence and Engineering A,2006,426:43-52.
[76] PETORAK C,ILAVSKY J,WANG H S,et al.Microstruc-tural evolution of 7% Y2O3 -ZrO2 thermal barrier coatings due to stress relaxation at elevated temperatures and the con-comitant changes in thermal conductivity [J].Surface & Coatings Technology,2010,205:57-65.
免责声明:本网站所转载的文字、图片与视频资料版权归原创作者所有,如果涉及侵权,请第一时间联系本网删除。
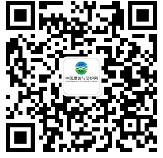
官方微信
《中国腐蚀与防护网电子期刊》征订启事
- 投稿联系:编辑部
- 电话:010-62316606-806
- 邮箱:fsfhzy666@163.com
- 中国腐蚀与防护网官方QQ群:140808414