0 引言
燃气轮机作为一种动力装置,广泛应用于舰船推进、汽车机械、航空航天等领域,其动力来源通常是由叶片从高温高压气体中获取能量,再将其转化为机械功。涡轮叶片是燃气轮机中的重要部件,一般由抗高温氧化、腐蚀能力良好的镍基高温合金制成,作为目前承温能力最高的单晶高温合金其承温能力已接近合金承受温度的理论极限[1-2]。然而随着对发动机推重比和进口温度需求的迅速增加,在工作环境中燃气温度将超过镍基高温合金的熔点250 ℃以上,导致材料更快地产生热疲劳和降解[3-5],因此,人们研究发明了热障涂层(Thermal Barrier Coatings,简 称 TBCs)用 以保护基体免受高温燃气损伤。
热障涂层是通过一定工艺将耐高温陶瓷材料涂覆在基体上的保护层,它的发展始于 20 世纪 50年代,美国国家航空航天局率先提出了热障涂层的概念,并将 CaO-ZrO2/NiCr 应用于火箭飞机的喷气管[6]。随着热障涂层的不断发展,目前用于航空普遍使用的是 6%~8% 氧化钇稳定氧化锆[7-8]。目前,配合使用热障涂层与内部冷却技术,可以使合金表面温度降低 100~300℃,使燃气轮机能够在远远高于高温合金熔点的环境中工作[9]。因此,利用该技术来改善涡轮叶片的基体环境是切实可行的。然而,热障涂层服役环境恶劣,在外物作用、内部生长应力、相变引起的体积膨胀等多方面因素的交叉作用下,极易萌生裂纹,随着服役时长的增加,裂纹也将进一步延伸、扩展,引发剥落并导致最终失效。近年来,国内外学者对热障涂层进行了大量研究及改良,包括制备方法、材料成分、涂层结构等多个方向,此外,为保障航空发动机的质量,节约热端部件的高昂成本,热障涂层的再制造技术,包括涂层裂纹修复以及涂层清洗后再制造也成为了实现航空领域稳定发展的关键。然而截止目前,热障涂层领域仍存在很多问题,尤其是涂层失效,大大影响了航空发动机的使用安全性。
本文从热障涂层的冲蚀、氧化以及热腐蚀三个方面介绍了热障涂层的失效机理,旨在为先进热障涂层的制造提供更多理论基础和设计思路,综述目前应对涂层失效的措施,并对热障涂层的研究和应用前景进行了展望。
1 热障涂层简介
热障涂层通常选用双层结构[10-12],这是热障涂层目前应用最广的结构形式并在航空发动机涡轮叶片上得到了实际应用,如图 1 所示。
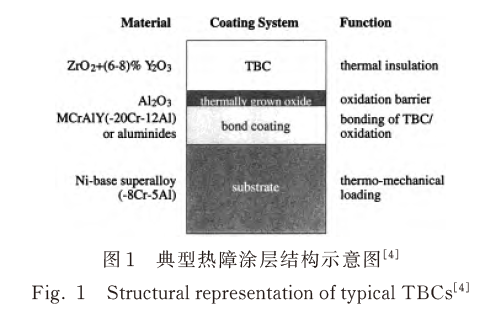
热障涂层的顶部为陶瓷层,应具备的功能有耐蚀、隔 热以及较高的抗热震性。 通常为YSZ(6%~8%)制成的厚度约300μm 的陶瓷层,熔点较高(约2700℃),热导率较低(致密材料在1000 ℃下的热导系数约为 2.3 W·m-1·K-1)[13-16]。
陶瓷层和基体之间存在一层厚度为75~150μm 的粘结层(Bond Coat),目前使用最广的粘结层材料为 MCrAlY,M 为金属 Fe,Ni,Co 或者他们之间的组合[17-20]。Ni+Co 是最常用的组合,Ni+Co基能使基体在具备一定缓和应力能力的同时兼具一定的抗氧化和腐蚀性能。Cr、Ni 可起到固溶强化作用,此外,Al 元素在高温下生成Al2O3,可提供抗氧化性能,Cr 元素可在 Al 氧化后形成氧化物Cr2O3,起到隔绝基体的效果,并提供一定的抗热腐蚀能力,促进 Al2O3 的生成。微量元素Y 的含量很低,一般小于 1%,能够细化晶粒,提高 Al2O3 与基体间结合力,改善涂层的抗热震性[21. 22]。
粘结层 MCrAlY 中主要相组成为 γ(Ni+Co)固溶体和 β-NiAl金属间化合物双相,涡轮叶片工作环境下,温度超过 700 ℃,可能导致粘结层氧化,并在粘结层和陶瓷层间生成厚度为1~10 μm 的热生长 层(Thermally Grown Oxide,简 称 TGO),粘结层内 Al 含量减少,β-NiAl转变为 γ ′(Ni3Al)相。当 涂 层 中 β 相 消 失 时 ,粘结 层 的 抗 氧 化 性降低[23-25]。
2 热障涂层的失效行为
从很大程度上来说,热障涂层的寿命可以决定整个高温零部件的寿命,而热障涂层的失效剥落是热障涂层在航空燃气涡轮发动机中的最大问题,需要以严格的标准频繁检查来确保安全,极大地限制了热障涂层的应用。对其失效机理的研究是为了更有针对性地解决失效原因,提高热障涂层服役寿命,因此通过认识涂层失效的机理并完善其成分结构是先进热障涂层研究中的重要一环。
2.1 冲蚀及外物损伤
燃气轮机涂层表面的物理损伤通常有两种情况,第一种情况源于燃烧形成的碳颗粒或者发动机基体磨损形成的粒子[26],夹杂在气流由于惯性力的作用撞击涂层表面,形成冲蚀,如图 2 所示。第二种情况是由于燃气轮机外界气流中夹杂着杂质或者颗粒[27],如高空中的冰块、砂砾、火山灰等,在惯性力作用下会对整个涡轮叶片造成碰撞,如图3 所示。冲蚀和外物损伤都主要发生在陶瓷层的顶部,可能导致涂层内部柱状晶变形和开裂,甚至热障涂层局部厚度减少,在叶片表面的陶瓷层上产生刻痕或者形变。将造成系统的平衡性以及叶片的气流特性略微降低和退化,当叶片处于旋转或 叶 片 通 过 频 率 状 态 下 时 ,易 造 成 疲 劳 失效[28-29]。有些外物撞击后,产生的残余应力可能致使裂纹扩展到粘结层/金属基体界面,随后裂纹沿着界面横向扩张,使粘结层和陶瓷层部分从基体上剥落,进一步造成涂层的失效。冲蚀的作用深度通常与作用粒子的质量、粒径和速度有关,此外,陶瓷层硬度、弹性模量等力学性能也将会影响作用层深度[26-32]。
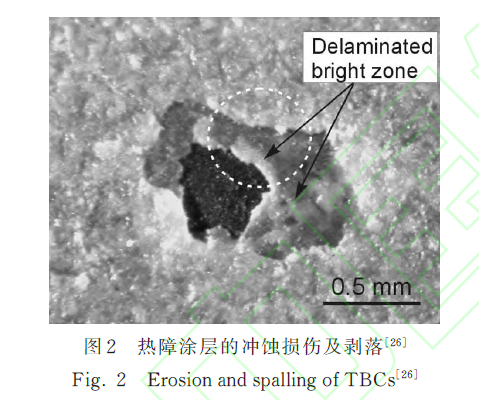
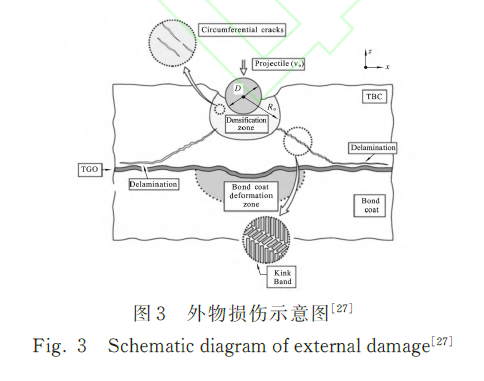
2.2 烧结及氧化行为
通过各种手段沉积后涂层的表层不可避免地存在气孔和裂纹,在 高温服役环境 下(大于 1200 ℃),可能会发生烧结反应,使涂层致密化以及热导率上升。并且由于基体与陶瓷层间的热膨胀系数不匹配,烧结会造成额外应力。当处于逐渐升高的温度下时(约为1200~1400 ℃),顶部陶瓷层沿厚度方向将有明显的线性收缩,在自由表面附近烧结效应更加显著[33]。此外,氧在二氧化锆基的陶瓷层中具有较高的离子扩散率,所以粘结层可能会被氧化,形成TGO。TGO 的氧离子扩散率较低,但铝元素与氧元素的亲合力较强,有向外扩散的趋势,当铝元素的扩散速度小于其反应生成α-Al2O3 相的速度时,Cr 及Ni 元素也将相继被氧化为 Cr2O3、NiO、Ni2Cr2O4 等氧化物,使 TGO 厚度增加,如图 4 所示。大量研究表明[34-37],热生长氧化物内部存在两类应力,即由于氧化物和金属基体间热膨胀系数差异导致的热失配应力和氧化膜生长产生的生长应力。Li M H 等[38]通过观察,认为粘结层发生严重氧化时,氧化层生长较快,粘结层与TGO 界面不规则,不规则的界面将会产生应力集中,并会加速面外应力的累积,从而导致粘结层与 TGO 间界面的开裂。A. Rabiei 等[37]利用短裂纹断裂韧性和测量的缺陷波长等材料属性预测TBC 中的 TGO 临界厚度,认为 TGO 存在一个厚度约为 5 μm 的临界值,低于此临界值时 TGO 不会影响到涂层,高于临界值时,裂纹形态和分层面都发生了明显的变化,并且会出现明显裂缝,如图5所示。
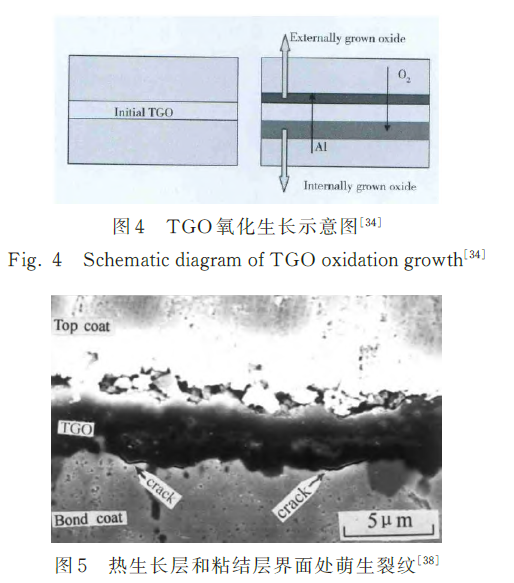
2.3 腐蚀行为
2.3.1 热障涂层在海洋环境下的腐蚀行为
在海洋高湿、高盐雾环境下,体系中存在的大量NaCl,将沿着热障涂层表面的孔隙、裂纹通道持续侵入 MCrAlY 粘结层以及基体,在高温条件下会加速粘结层的氧化从而使热生长层的厚度增加,增大其开裂倾向。即便处于常温条件下,盐雾侵入也会使表层氧化锆晶体挤压变形,产生裂纹的扩展[39-40]。燃料中的含硫物质也是造成燃气轮机腐蚀的一大成因。在 650~750 ℃ 的温度范围内,会发生低温热腐蚀。由于SO3 分压偏高,导致金属氧化物酸性熔解,在 Ni-Cr、Co-Cr、Co-Cr-Al 和 Ni-Cr-Al 合金中形成Na2SO4 和NiSO4 或CoSO4的低熔点混合物,造成点蚀。当处于 850~950 ℃ 较高的温度下,一般会通过形成金属硫化物来提高熔融硫酸盐中Na2O的活性,进而对热生长层产生碱性溶剂腐蚀[41]。当船用燃气轮机接触到工业或森林火灾污染的空气,以及自身燃料中就会产生腐蚀盐类,如V2O5、Na2SO4。这些腐蚀盐类产生以下反应[42-43]。

陶瓷涂层中ZrO2通常以不稳定的四方相(t‘)存在,经式(1)和(2)反应失去稳定组元 Y2O3 后,ZrO2 易于在 1 220 ℃以下发生相变,转换为单斜相(m),当 ZrO2从四方相转化为单斜相时,会伴随着4. 6% 的体积增大[13],这样的体积变化带来的相变应力将会引起裂纹甚至是涂层的剥落。周长海等[44]在 900 ℃下向等离子喷涂 Y2O2-ZrO2热障涂层中添加 V2O5 与 Na2SO4 混合盐,其表面由粗糙,有部分未熔颗粒,且存在微裂纹的层片状涂层转变成为块状、细棒状的 YVO4,从而影响了 Y2O3 的稳定作用,如图 6 所示。
2.3.2 热障涂层在航空领域的腐蚀行为
相对于海洋环境下的燃气轮机而言,航空发动机使用更为为纯净的燃料,含硫量较低,硫化比例少。但仍可能在飞行过程中沉积上其他盐类。
火山活动会使空气中夹杂钙镁铝硅等元素的盐类(CaO-MgO-SiO2-Al2O3简称CMAS)[45-46]。 CMAS 的熔点较低,在 1 190~1 260 ℃间。当其沉积在燃气轮机部件的热障涂层上时,可能会在高温燃气的作用下受热熔化,润湿陶瓷层并渗透进入 TBCs。一方面可能导致不稳定的四方相 t’溶解为单斜相 m 和立方相 c,产生相变应力;另一方面CMAS 渗透进涂层填充孔隙会导致杨氏模量的增加以及应变容限的降低,在高温下陶瓷层与粘结层以及镍基高温合金的热膨胀系数不匹配产生的热应力将会导致涂层失效[47-48]。A.K.Rai 等[47]认为,改变材料结构形貌比改变材料化学性质更加重要,并提出了表层致密化以及将电子束气相沉积制得的柱状结构涂层修改为羽状结构。L.Steinberg 等[46] 制 备 了 不 同 组 分 的火 山 灰 和CMAS,在室温环境中,羽状结构抗外物冲蚀速率明显优于普通涂层,然而在高温条件下一旦预制的火山灰和 CMAS 渗透进涂层内部后,羽状结构涂层和普通涂层的受冲蚀速率分别达到 5.06~5.95 g/kg 和 2.72~3.24 g/kg,即羽状结构涂层与腐蚀盐类作用区域的增加反而会加剧外物对涂层的侵蚀。
3 热障涂层的修复与再制造研究
热障涂层自问世以来,就有大量学者从结构或成分方面对其进行改善,并取得了一定的成果。ChangF 等[49]利用激光在热障涂层表面制备了钉扎结构,经实验证明钉扎结构有助于减轻沉积层的残余应力,并且有助于提高TBC在热循环中的应变耐受性。Liu H 等[50]使用离子镀膜技术在热障涂层表面制备了Pt 层,在 1250 ℃的CMAS 环境下进行腐蚀,在 2 h 以内Pt 层以下涂层保留了结构完整性。徐振华等[51]制备了新型 La(2Zr0. 7Ce0. 3)2O7热障涂层,经 1089 h 恒温氧化后陶瓷层氧化增重低于 8YSZ 涂层。
尽管上述热障涂层的改性在某些方面优于传统的6%~8%TBCs,但始终存在一些问题,如制备工艺复杂,保护周期短或者界面结合较差等。无法避免在长期处于服役环境的情况下出现裂纹甚至剥落,因此目前为止涂层的修复仍是延长服役寿命的关键。现阶段涂层的修复方法通常可分为两类,其一是在制造阶段加入自修复材料,使涂层在高温氧化环境下自发完成修复过程;另一种是在涂层出现裂纹或剥落时,对其进行填充,当出现较大程度的相变或者不可修复的破损时,可将其除去后再使用等离子喷涂(APS)或电子束物理气象沉 积(EB-PVD)等 方法进行热障涂层的再制造。
3.1 自愈合涂层
自愈合涂层是指涂层在受到损伤后具备一定的自修复能力,自愈材料包括金属、聚合物、陶瓷以及它们的复合材料,这些复合材料在受到机械,裂纹扩展后产生自修复机制。损伤自修复的先决条件是产生移动相,通过移动相填充裂纹,修复材料机械性能。
早在 20 世纪 70 年代就有关于自修复材料的报道。F. F. Lange[52]将 SiC 材料热震后发现裂纹,随后进行 1400 ℃恒温氧化,在 10 h 后发现裂纹区域被蓝色SiO2薄膜所填充,自主完成了修复过程。这是由于SiC 在高温下暴露一段时间后,将与进入的氧气形成SiO2 反应,该反应通常发生在 720 ℃左右。形成的硅具有非晶态结构,处于半流体状态,能沿着周围的微裂纹和微孔隙流动。Al2O3 氧化物如果接近TGO 和ZrO2 氧化物,则形成固体复合化合物,如莫来石(3Al2O3·2SiO2)和 ZrSiO4。这个完整的过程被定义为一个自愈过程,其最终产物可作为额外的氧屏障限制其向粘结层的通量,并因此提高了系统的抗氧化性。具体反应如式(3)~式(5)所示。
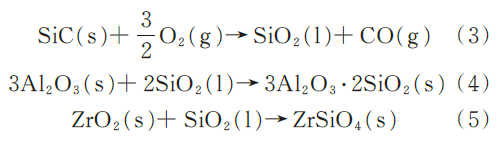
为了提高热障涂层的热循环寿命,K. Portilla-Zea 等[53]使用雾化器在 TBC 粘结层与陶瓷层间制备了一层SiC 纤维层,研究添加 SiC 对YSZ 热障涂层的影响。在 1100 ℃下循环氧化后,保持 190 ℃恒温加热 80 min,随后使用通用试验机进行附着力测试,结果表明,与常规的 YSZ TBCs 相比,增加了SiC 层的TBCs 在循环氧化后能够产生硅类化合物填充微裂纹,并且减少和延缓裂纹的延伸,具有更强的附着力。
研究人员还试图开发新的涂层体系,将其整合至 TBC 自修复涂层中 。Ouyang T 等[54] 在GH4169 基体上制备了 YSZ/SAZ 涂 层(SAZ 由SiC、Al2O3 和YSZ 粉末喷雾干燥获得),经 1 100 ℃等温氧化 20 h 为一个循环,在 20 个循环后 YSZ/SAZ 热障涂层的质量损失仅为YSZ 体系热障涂层的 43. 66%。利用Al2O3 具有较低的氧扩散系数(1400 ℃时约为10-12 cm2/s),进而增强了 TBC 体系的抗氧化性。在过去几十年内,有大量关于其他自修复涂层体系的文献报道[55-58]。
MoSi2 作为近年来热障涂层裂纹自修复的新兴材料 ,具 有与 YSZ 相近的热膨胀系 数(8. 5× 10-6 ℃),在 800 ℃以上,会首先氧化生成 Mo5Si3,然后再进一步氧化生成易于挥发的 MoO3。在热障涂层的工作温度下,与氧气接触并发生反应,生成的MoO3 将会挥发,剩余产物 SiO2体积相较反应前的 MoSi2 要大,导致 SiO2扩张,当涂层在热循环过程中出现裂纹时,SiO2 可能由于体积膨胀进入周边裂纹,从而实现裂缝填充。此外,SiO2 会与陶瓷层中的 ZrO2反应生成 ZrSiO(4锆石),该过程造成体积收缩,使裂纹间隙减小。并且 ZrSiO4 与 ZrO2结合力较好,强度、硬度高,能够对涂层的机械强度进行较好的修复。F. Nozahic 等[59]使用悬浮液等离子喷涂技术将 MoSi2 分散在 8YSZ 中,经火花等离子烧结制备复合材料。研究了该复合材料在 1 000~1 300 ℃温度下的 10 h 循环氧化,在 MoSi 颗粒周围和YSZ 基体晶界附近生成了SiO2 修复裂纹并与ZrO2基体生成ZrSiO4,恢复基体的机械性能,经自修复后的涂层中已无明显裂纹。Z. Derelio‐glu 等[60]在使用 MoSi 颗粒作为裂纹愈合剂的基础上在其中加入了硼合金组元,B 元素在使用温度下能增加 SiO2的流动性,在 SEM 图的观察下,发现SiO2移动了 40 μm,促进了裂纹的填充,如图 7 所示。此外,MoSiB 体系的涂层在抵抗 CMAS 腐蚀方面也被证明是切实有效的[61],熔融 CMAS 会与涂层作用形成CaMoO 和SiO ,相互作用的反应产物改变了CMAS 的组成,产生结晶,有效地固定了CMAS,并抑制了与 MoSiB 基涂层的进一步相互作用。此外,涂层中存在一些裂纹在高温下会被周围流动的硼硅酸盐填充。
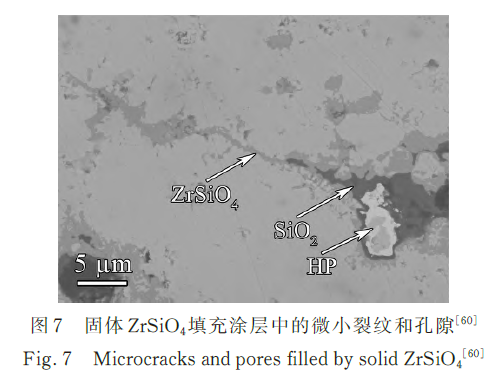
美国宇航局也发布了有关飞机发动机应用的高温轻质自修复复合材料的研究成果[62]。研究了不同添加剂对CrMoSi-SiC 复合涂层的修复情况,在 1600 K 氧化 24 h 后,没有任何添加剂的 CrMo‐ Si-SiC 试样的划痕和孔洞几乎没有变化。但是,添加 5wt. % CrB2 后待修复划痕和孔洞有明显闭合;在 CrMoSi 合金中加入 1wt. % Ge 作为固溶体对修复划痕有效果显著,但对孔的封闭影响较小;当CrMoSi 合金中Y 含量为 0. 1wt. %时,划痕没有得到明显修复;添加 5wt. % ZrSiO4 对修复划痕效果较好,但氧化皮呈层状且易碎。
3.3 热障涂层的再制造方法
航空发动机长期处于高温高压、强腐蚀性的恶劣环境下,当涡轮叶片或其他热端部件长期服役后,热障涂层易出现裂纹、剥落等破损,会导致防护作用逐渐降低甚至失效。由于航空发动机关键零部件制造工艺复杂,生产周期较长,直接更换新部件将造成资源的大量损失。而对缺陷部位进行修复或再制造,能够大幅节约生产成本。因此,燃气轮机叶片热障涂层的修复及再制造是一项关键的航空技术,经济效益好,材料利用率高,具有广阔的工程应用前景。
3.2.1缺陷涂层的修复方法
液体注入等离子体喷涂是一种具有潜力的涂层修复方式,工作原理是通过输送马达抽出溶液,在载气的作用下,经过雾化喷嘴,进入等离子体中,在热等离子体中发生物理、化学反应后,沉积到金属基体上,喷雾的前驱液滴以液态形式冲击基体,形成涂层。Rousseau 等[63]使用了低功率等离子体反应 器(LowPower Plasma Reactor,简 称LPPR)用于修复局部损坏的 TBC。将硝酸盐ZrO(NO3)2 和 Y(NO3)2 前驱体溶液以低功率(240 W)喷入Ar/O2 等离子体放电并转化为氧化物涂层,修复受损试样上的部分裂纹和孔隙,所得涂层的显微结构为层状,具有较高的微米和纳米孔隙度。如图8所示。对受损EB-PVD 涂层,LPPR 涂层也在柱状间隙(图 8 白色箭头)及分层裂纹(图 8 黄色箭头)中展现出了较强的渗透性,与此同时,由于粘结层中的铝元素和等离子放电过程中的氧化剂的交互作用,有约3μm 的新热生长层生成,这种小尺寸的热生长层可以为整个涂层系统提供一定的化学和机械相容性。
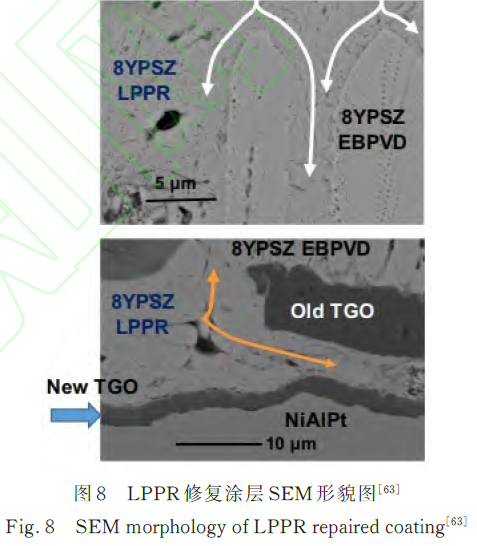
溶胶凝胶法通常用作涂层的制备,且其成本低廉、操作简单,相较其它涂层制备工艺较为灵活,因此可应用于涂层的修复,使用浸渍法可在热障涂层裂纹处填充溶胶-凝胶涂层,涂层质量与溶胶中YSZ 粉末质量分数、热处理温度、浸涂次数等有关[64]。然而浸涂过程的方向性会导致裂纹的不均匀不对称填充,此外,浸涂次数的把控也将大大影响涂层的成型状态,浸涂次数较少会有明显的凝固裂纹,过多则会导致后续沉积效率的降低以及涂层附着力的减弱。因此要得到广泛应用还有待于进一步研究。
3.2.2 失效热障涂层的再制造方法
当热障涂层在服役过程中厚度低于临界尺寸或产生不可修复的破损时,难以修复原有涂层,需要去除并重新涂覆新的涂层。新涂层与原有涂层的制造工艺相同,可使用等离子喷涂、电子束物理气象沉积以及化学气相沉积等多种沉积方法进行新涂层的制造,因此,热障涂层再制造的重点和难点在于完全去除原有涂层的同时不损伤基体。
早期应用于热障涂层陶瓷面层的去除方法有喷砂法、高压水射流法以及卤气反应法等,喷砂法去除陶瓷涂层效率高,成本低,但可控性较差,容易对粘结层甚至基体材料造成损伤。高压水射流去除法通过保持涡流脉冲水射流喷嘴与涡轮工作叶片靶距,将喷嘴沿着涡轮工作叶片的轴向方向逐行往复运动,逐层剥离当前表面的陶瓷层,操作工序简单,无有害物质排放以及环境污染问题,但可控性差,易损伤粘结层和基体。卤气反应法是将热障涂层和含氟粉末混合加热至980~1050℃,持续弱化涂层和基体间的结合,使涂层自发地与基体分离,但设备昂贵,易对涂层及基体均造成损伤。
目前,国内外应用较多的热障涂层去除方法是熔融碱法,熔融碱法的原理是利用金属粘结层与陶瓷层之间的热生长氧化层(主 要成分为 α-Al2O3)容易被碱性溶液腐蚀的原理松动涂层。宫声凯等[65]使用了 KOH 与NaOH 混合溶液,将涂层置于含有上述溶液的坩埚中反应 3~20 min,再将处理后的热障涂层试件进行表面湿吹砂处理,去除部分粘结层。在扫描电镜下观察到陶瓷层已被完全去除,且在电镜分辨精度范围内没有发现钾和钠离子的存在,证明对基体和粘结层是安全的。该方法对设备要求低、工艺简单,并且对试样损害较小。
由于激光技术的进步,激光清洗也逐渐进入了人们的视线,被广泛用于文物、微电子线路板等材料的清洗,是一种新型表面清洁技术。与喷砂法等传统的清洁方法相比,激光清洗具有可控性好、无机械接触、基底损伤小、材料适应性广等优点,且清洗废料为固体粉末,易于回收,是一种绿色清洁的清洗方式[66]。工作原理如图 9 所示[67]。激光直接作用于涂层表面,可通过编程并在远程控制下破坏杂质和基底之间的作用力,随着激光作用时间的增加,待清洗物与基材之间热膨胀系数的差异将在界面处产生压力,清洗物发生屈曲、失稳,从基材表面衍生裂纹,出现机械断裂、振动破碎等现象,最终以喷射的方式从基材表面清除或剥离。清洗阈值与待清洗物的颗粒大小、物化性质以及基体材料有关[67-68]。
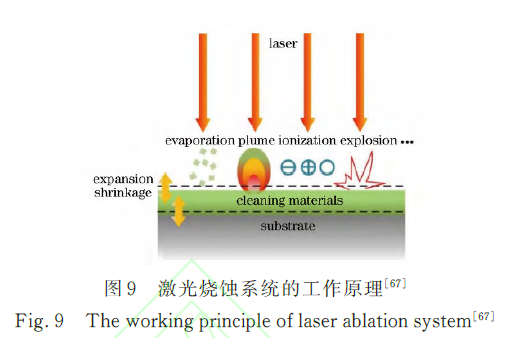
目前,国内外已有科研机构开展了关于激光清洗去除航空发动机零部件表层杂质的理论和试验研究。Zhu 等人采用脉冲固态激光清洗装置对波音系列飞机上的BMS10-11底漆进行清洗[69]。不同激光能量密度清洗下的飞机表面宏观形貌如图 10 所示。研究表明,随着激光能量密度的增大,表面漆料的清洗也更加彻底,激光能量密度达到5J/cm2 时,清洗效最好,且不会降低飞机蒙皮及铆钉孔间的摩擦磨损性能。而当进一步增大能量密度后,将对零部件表面铝层造成损伤。
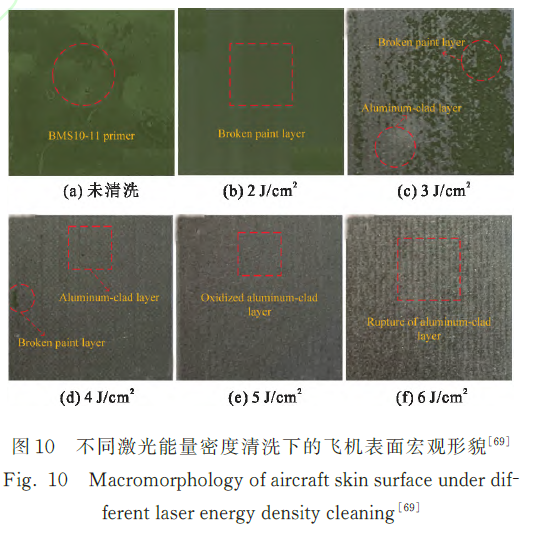
曼彻斯特大学Marimuthu[70]等基于有限元法模拟分析了激光清洗航空发动机零部件热障涂层过程中的瞬态温度场、残余热应力以及材料去除率,并研究了积分通量对涂层和基体烧蚀速率的影响,得 出 TiN、CrTiAlN、WC值,其验证性实验与有限元模拟的结果具有良好的一致性。
4 结语
大量的研究和实践证明了热障涂层是保障燃气轮机高温部件有效运作的关键技术。随着燃气轮机进口温度以及推重比需求的增加,对热障涂层也提出了更高的要求,未来热障涂层的发展主要有以下几个方面。
(1)热障涂层表面裂纹及界面脱粘缺陷的无损检测。通过对涂层显微组织形变大小、裂纹形成与扩展位置、外物损伤程度进行准确的预测与评估,判断涂层的破坏程度,从而界定其失效与否,并及时对产生的磨损、磨蚀现象甚至开始裂纹扩展的涂层进行修复,进而避免陶瓷面层的大面积剥落,显著提升热障涂层的可靠性。
(2)新型热障涂层多因素失效评估及成分、结构优化。稀土氧化物掺杂氧化锆、稀土锆酸盐等新型热障涂层虽已有较多的探索研究,但对其测试分析多数只满足单一环境的使用需求,然而涂层投入实际生产应满足外物磨损、高温氧化、热腐蚀等多元环境的使用需求。此外,粘结层中 Al、Cr、Ni 等元素扩散形成的氧化物热生长层也是引发裂纹和分层的重要成因,而目前对于热障涂层的改性研究主要集中在陶瓷层,因此,需要对粘结层成分优化,探索替换 Al、Cr、Ni 等元素且抗氧化性能较优的粘结层材料。与此同时,相较于传统双层涂层结构,成分分布的梯度化能显著地减少或消除涂层内部界面,缓解涂层内部应力,故开发成本低廉,工艺简单的梯度热障涂层制备方法也将成为未来热障涂层开发探索的方向。
(3)热障涂层自愈合修复新理论及再制造新技术。自愈合材料对涂层的填充具有显著效果,但目前自愈合修复主要针对涂层尺寸修复,对于相变及应力缓解研究较少,因此,应对这一问题进行综合研究,探索自愈合修复新理论。此外,对于现阶段热障涂层的研究,需正视其失效问题,基于现有再制造工艺,开发再制造新技术,为热端部件在航空航天领域的实际使用中提供更可靠的保障。
免责声明:本网站所转载的文字、图片与视频资料版权归原创作者所有,如果涉及侵权,请第一时间联系本网删除。
相关文章
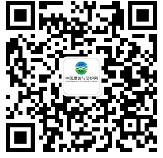
官方微信
《中国腐蚀与防护网电子期刊》征订启事
- 投稿联系:编辑部
- 电话:010-62316606-806
- 邮箱:fsfhzy666@163.com
- 中国腐蚀与防护网官方QQ群:140808414
点击排行
PPT新闻
“海洋金属”——钛合金在舰船的
点击数:7130
腐蚀与“海上丝绸之路”
点击数:5741