摘要 非晶合金因其独特的非晶态结构,其腐蚀机制不同于传统晶态合金,是一种很有发展潜力的新型高耐蚀材料。本文综述了非晶合金耐蚀性的研究现状,归纳了合金成分、合金结构、制备工艺、腐蚀介质、表面状态、加载应力以及其他重要因素对非晶合金耐蚀性的影响规律,总结了非晶合金耐蚀性能的改善途径,并对非晶合金耐蚀性研究方面存在的问题和今后的发展趋势进行了探讨和展望。
关键词 非晶合金;耐蚀性;影响因素;改善方法
非晶合金是一种新型材料,又被称为金属玻璃,是由熔融合金急冷从而使金属内部液态结构得以保留,合金内部原子并非周期性排列,而是呈现出短程有序、长程无序的结构状态 [1]。 自 1950 年 Brenner 等[2]利用电沉积法制备出二元非晶合金以来,非晶合金由于高强度、高储弹性[3]、高的耐腐蚀性[4]等优良的物理化学性能,在国防、生物、医疗、军事、建筑等各个领域[5-8]有巨大的应用前景。
腐蚀是金属在服役中最常见的失效形式。金属材料的腐蚀不仅给国民经济带来巨大的损失,同时也会给工程等带来难以预测的安全隐患[9],为了解决这一问题,对于金属腐蚀的控制是当前亟待解决的重要问题之一[10]。
通常情况下,一些金属,如 Al 等,在金属材料表面形成钝化膜,从而使金属具有一定的耐蚀性,但是钝化膜一旦破裂,腐蚀便会立刻发生,从而导致金属失效[11]。传统的合金通常具有优良的力学性能和价格低廉等优势,应用比较广泛,但是在特殊的环境中,耐蚀性往往达不到要求,因此需要重新寻找或者设计一类新型合金,非晶合金由此进入人们的视野。近几年来,对于非晶合金耐蚀性的研究日渐丰富,不断研究非晶合金在各种环境下的腐蚀行为,积累非晶合金的腐蚀数据,对于非晶合金的实际应用具有重要的意义。
本文对非晶合金耐蚀性的最新研究进展进行了综述,通过比较非晶合金和传统合金耐蚀性机理的异同,对于当前影响非晶合金耐蚀性的重要因素进行比较分析,包括非晶合金成分、结构、制备工艺、腐蚀介质、表面状态以及应力状态等,并对改善非晶合金耐蚀性的方法做了系统的归纳总结,对今后非晶合金的研究方向进行展望。
1. 非晶合金耐蚀性能和腐蚀机理
对于传统晶态金属材料的腐蚀研究已经较多,体系也较成熟,按腐蚀形态划分,传统合金腐蚀通常可分为全面腐蚀和局部腐蚀,全面腐蚀研究相对较多,也是比较简单的,但是局部腐蚀包含种类复杂,诸如电偶腐蚀、点(孔)蚀[12]、晶间腐蚀[13]、选择性腐蚀、氢腐蚀、缝隙腐蚀、以及在使用过程中由于受力而引起的腐蚀疲劳、应力腐蚀开裂等。非晶合金具有特殊的结构和多组元特性,其腐蚀机制不同于传统金属材料。由于非晶合金在化学结构方面由单一均匀的固体相所组成,不存在晶界、位错、层错、孪晶等晶体结构中常见的结构缺陷,也不存在成分偏析和第二相析出,这种单一均匀的化学结构使非晶合金不存在晶间腐蚀,且非晶合金中往往含有钝化能力强的元素,使非晶合金材料表面易形成钝化膜,但是也因此使局部腐蚀中点蚀和选择性腐蚀对非晶合金影响较大:(1)非晶合金表面常存在很小的物理缺陷,点蚀常集中在这些很小的区域,使表面钝化膜遭到破坏,材料发生点蚀;(2)非晶合金中元素较为复杂,元素之间存在电位差,使其中的贵金属常常保持稳定,而其他活泼金属易溶解后沉积在材料表面,此时贵金属充当阴极加速腐蚀;(3)在非晶合金应用过程中,难以避免的面临应力的作用,也就存在腐蚀疲劳和应力腐蚀开裂,更会加剧腐蚀,大大降低非晶合金使用寿命。
目前,已有相关研究证实了非晶合金比其相对应的晶态合金耐蚀性良好:在不同 pH 值的 0.6mol/L NaCl 溶液中,Fe68Cr8Mo4Nb4B16 非晶合金腐蚀电流(Icorr)在 10-6-10-7A/cm2 之间,而对应的 Fe68Cr8Mo4Nb4B16 晶态合金则在 10-4-10-5A/cm2[14];非晶合金 Cu52.5Ti30Zr11.5Ni6 在 1M HCl 溶液中 Icorr 为 10-4A/cm2,而对应的 Cu 合金则为 10-3A/cm2[15];非晶合金 Al86Ni6La6Cu2 在0.01M NaCl 溶液中Icorr 为3.64×10-4A/cm2,仅为对应Al 合金和纯Al 的1/2[16]。
图1 展示了不锈钢和非晶合金在3.5%(质量分数)NaCl 溶液、1 mol/L HCl 溶液、及1 mol/L NaOH 溶液中的腐蚀行为图,相比多数不锈钢,非晶合金在对应酸、碱、盐溶液中具有更低的 Icorr 和更高的腐蚀电位(Ecorr),耐蚀性要更好。
图 1 非晶合金(MGs)和常见不锈钢(SSs)在 3.5%NaCl 溶液、1 mol/L HCl 溶液和 1 mol/LNaOH 溶液中的腐蚀行为
综上所述,和对应晶态合金以及传统不锈钢相比,非晶合金耐蚀性更加具有优势,这也使得对于非晶合金耐蚀性的研究具有重要意义。
2.影响非晶合金耐蚀性的因素
非晶合金耐蚀性与非晶合金成分、合金结构、制备工艺、腐蚀介质、表面状态、加载应力均有较大的关系,本文从这几个方面对非晶合金耐蚀性的影响做简单论述。
2.1 非晶合金组成成分的影响
研究表明,合金化可以改变金属材料的耐蚀性能[17, 18],而非晶合金的耐蚀行为与其合金成分也有很大关系,通过微量添加合金元素亦能显著改变非晶合金的耐蚀性能。表 1 总结了典型合金元素对非晶合金耐蚀性影响。合金元素对非晶合金耐蚀性的影响机制主要有以下 3 种:
(1)通过改善合金的非晶形成能力,促进非晶合金结构的均一性,从而提高非晶合金的耐蚀性。Xu 等[19]研究了 B 的加入对非晶合金 Zr66.7-xNi33.3Bx 的耐蚀性能的影响,适量的 B
的加入能够形成多相竞争生长,抑制晶相的析出,从而提高非晶形成能力,进而提高耐蚀性能; Huang 等[20]证实了 Y 的加入也可以提高(Zr55Al10Cu30Ni5)99Yx 在磷酸盐中的耐蚀性能,主要由于 Y 的加入可以参与结晶相的竞争,使液相变得更加稳定,从而提高非晶形成能力,提高抗局部腐蚀的能力。类似地,研究发现 C、B、P 可以提高 Fe-Cr 非晶合金在钝化膜形成之前的活性溶解,以使钝化膜中 Cr 提高,机理虽尚未完全清楚,但对于耐蚀性提升却是显著的[21];Si 可以使钝化膜中含有 SiO2,从而提高耐蚀性能[22, 23]。相关研究表明,也存在一些元素能够破坏非晶成形能力,加速结晶相的析出,加剧电偶腐蚀。Wang 等[24]认为在非晶合金(Mg65Zn30Ca5)100-xMnx 添加 Mn,在模拟体液的腐蚀介质下,会使非晶合金中析出 Mg、 Mn、MgZn 相,非晶形成能力下降,破坏耐蚀性能;周杰等[25]认为 Nd 的过量添加(大于 0.5%)会促进非晶合金中 α-Mg 的析出,从而降低 Mg68-xZn28Ca4Ndx 非晶形成能力。
(2)通过添加抗腐蚀性能较好的合金元素,提高其对应氧化物在钝化膜中的含量,从而提高非晶合金耐蚀性。Nie 等[26]研究发现(Cu37.6Zr46Ag8.4Al8)100-xTix 中 Ti 可以促进钝化膜的快速形成,提高耐蚀性元素如 Zr、Ti、Al 在钝化膜中的含量,可提高非晶合金耐蚀性能;Long等[27]认为 Ni 添加在[(Fe1-xNix)0.75B0.2Si0.05]96Nb4 中对钝化膜的形成有明显的促进作用,且钝化膜中形成的 NiO2 保护性能较好,耐蚀性也有所提高。
(3)这类合金元素的添加并不能直接影响非晶合金的耐蚀性,但是可以通过与合金中主要组成元素的协同作用来改善耐蚀性,如 Zhou 等[28]在研究(Zr46Cu46Al8)100-xCox 耐蚀性时指出, Co 元素的添加主要促进钝化膜中 Zr 和 Al 的富集来促进钝化膜的稳定性,从而改善耐蚀性;Zhang 等[29]认为在 Zr53Co23.5-xAl23.5Agx 中添加 Ag 并未影响钝化膜形成速率,而是通过促进Al2O3 的含量,增强钝化膜的稳定性。但是,值得注意的是,每种元素对于非晶合金耐蚀性的影响并不是一成不变的,在不同情况下,微量元素的影响也会有所不同。首先,同种元素在不同溶液中耐蚀性会稍有差异,如稀土元素 Y,一般认为其对提高耐蚀性有益,但是在 Yu 等[30]对(Zr58Nb3Cu16Ni13Al10)100-xYx的研究中,发现在 H2SO4 溶液中,耐蚀性并不是如预期一般有所改善,而是存在耐蚀性下降的情况,进一步研究发现,Y 可以加剧 Cu 在 H2SO4 溶液中的活性溶解,使耐蚀性降低; Jin 等[31]用Hf 取代Zr55Ti3Cu32Al10 中的Cu,却发现在1 mol/L HCl 中存在点蚀,而在1M H2SO4中发生钝化,这或与腐蚀介质存在一定的关联;此外,微量元素的添加仍需要考虑添加阈值的问题,Xu 等[32]认为随着钝化元素 Cr 的增加会降低非晶形成能力,因此 Cr 的添加对于非晶合金耐蚀性影响存在一阈值。对于给定的合金体系,我们需要在成分设计时尽量减少活泼性金属元素的添加,适当添加钝化能力强的元素,如 Ni、Ti、Cr 等,其表面钝化膜结构致密,可有效延缓合金的腐蚀速率,从而提高耐蚀性能;另外,当电化学势较高的金属达到某一特定含量时,可以使非晶合金整体耐蚀性能有所提高,即n/8 定律,这些都是我们在进行成分设计时需要考虑的因素。
表1 添加合金元素对非晶合金耐蚀性的影响总结
2.2 结构弛豫的影响
非晶合金在低于玻璃化转变温度(Tg)退火时会向更稳定的非晶态转变,降低体系的自由能,这种现象称为非晶合金的结构弛豫。在非晶合金弛豫过程中,往往伴随着非晶合金力学、热学等各种性能的变化,非晶合金拓扑和短程序将发生改变,自由体积发生湮灭,原子堆积更加紧密。非晶合金在服役过程中将不可避免地受热、应力影响,结构弛豫对于耐蚀性的影响研究极其重要。Zhou 等[41]将Zr65Cu17.5Fe10Al7.5 非晶合金在玻璃化温度以下(573K)等温退火 0.5、1.0、2.0 和 4.0h 后,研究其在 3.5%NaCl 溶液中的耐腐蚀性能,电化学曲线如图 2 所示。研究结果表明,该非晶合金经过退火处理后,合金的 Ecorr 较铸态合金有所下降,Icorr 明显增大,但是点蚀电位和钝化区都随着退火时间增加先增加后减少,说明 0.5 和 1.0h 的退火处理使非晶合金表面形成更加致密的钝化膜,从而提高保护能力,合适的退火时间可以提高抗点蚀能力,但是会使抗均匀腐蚀能力变差。这种现象产生的原因是退火弛豫导致非晶内部自由体积减少,化学势减少,减少点蚀的传播,从而提高耐点蚀能力;González 等[42]研究比较了Zr60Cu20Al10Fe5Ti5 非晶合金铸态和退火态的耐腐蚀性,在接近于玻璃化转变温度(648K)和873K 下退火不同时间,退火处理后的样品点蚀电流下降,点蚀电位和钝化区也有所增加,耐蚀性有较大提高。作者分析,退火会使非晶合金自由体积湮没,原子间距离和化学势减少,结构弛豫过程中,金属原子处于低能阶状态,电化学活性降低,使非晶不易发生腐蚀反应,从而使非晶合金耐蚀性得到改善。结构弛豫可以使体系的化学势减少,电化学活性降低,对于非晶合金耐蚀性能改善是有益的。此外,自由体积一般被认为是非晶合金结构上的缺陷,通过适当的退火弛豫可以使自由体积发生湮灭,减少非晶合金结构上的缺陷,有利于提高耐蚀性能[43]。
图2 Zr65Cu17.5Fe10Al7.5 铸态和等温退火不同时间后在3.5%NaCl 溶液中动电位极化曲线[41]
2.3 部分晶化的影响
非晶合金较差的室温塑性严重制约其广泛应用,而当前解决这一问题的常见途径就是引入可变形的塑性第二相,形成非晶复合材料,以提高室温塑性,因此有必要研究部分晶化对于非晶合金耐蚀性的影响。
Poddar 等[44]通过在 650℃退火在 Ni60Nb30Ta10 非晶合金中引入 α-Ni 相,形成非晶复合材料,在 11.5M HNO3 中发现部分结晶的复合材料钝化膜表面缺陷密度增加,且硝酸中氧化物质极易通过钝化膜扩散到晶体相中,引起钝化膜稳定性变差;Hua 等[45]分别在 673K 和 713K 温度下对 Zr68Al8Ni8Cu16 非晶合金热处理,分别引入 10%和 70%的 Zr2Cu、Zr2Ni 晶相,并在 1M HCl 中探究其耐蚀性能,结果发现晶相和基体之间易发生电蚀,从而使复合材料耐蚀性降低。但是,Lin 等[46]通过对 Al86Ni9La5 非晶合金在 503K(开始结晶温度)退火不同时间,从而得到含有不同体积分数 α-Al 相非晶复合材料,其中当 α-Al 相含量为 20%时在 0.01M HCl 中耐蚀性最好,非晶态和纳米晶界面的存在可以促进钝化元素的扩散,加速钝化膜的形成,此外,作者认为初始结晶时处于热力学稳定状态,虽然容易发生局部腐蚀,但是此时热力学稳定性在与局部腐蚀的竞争中处于有利地位,随着晶相体积分数增多,缺陷增加,局部腐蚀慢慢开始占据主导,耐蚀性下降。
以上研究是通过铸态退火从而引入第二相以形成非晶复合材料,通常情况下,我们仍旧可以通过原位反应来制备复合材料。Gu 等[47]通过原位反应和退火分别制备了 Cu47.5Zr47.5Al5非晶复合材料,通过场发射电子扫描显微镜(FESEM)对腐蚀后的样品形貌观察,如图 3所示,可以得出原位生成的复合材料在海水中耐蚀性最好,退火后的材料最差,铸态复合材料中 CuZr 纳米晶从基体中析出,使非晶基体中 Al 含量增高,极易形成含氧化铝的钝化膜,提高耐蚀性,但是退火后,纳米晶体积分数增至 60%,且聚集严重,易在晶界处引入大量缺陷,增加局部腐蚀的倾向;Debnath 等[48]研究表明,Ti45(Zr-Be-Cu-Ni)55-xNbx(x=0,5,10,15 at.%)中晶化相比例在 20%处具有较好的耐蚀性能,随着晶化比例增加,纳米晶粒增多,晶相和非晶相差距较大,非晶合金均质性有所下降,且以晶粒为点蚀的触发点增多,容易引起非晶基体溶解,显然对于耐蚀性是存在不利影响的。部分晶化对于耐蚀性影响较为复杂,影响机理尚不完全清楚,目前普遍认为,对于退火结晶形成的非晶合金复合材料,易在非晶合金基体和晶体界面处引进大量的缺陷,使非晶合金耐蚀性有所降低,但是仍有相关研究表明[46],退火结晶可改善耐蚀性,界面的存在可以促进钝化元素的扩散,加速钝化膜的形成,从而提高非晶合金耐蚀性能。而对于原位反应生成的复合材料,在合适的晶化分数下,会使非晶合金耐蚀性得以提高,但是超过该阈值之后,均质性降低,晶粒增大,缺陷增加,加剧腐蚀,因此可以通过调控晶相分数来改善非晶合金微观结构,进而控制耐蚀性能,但是对于晶相分数的选择相当重要。
(a) (b) 50 μm
图 3 铸态Cu47.5Zr47.5Al5 棒(3 mm) 、铸态棒(5 mm) 和退火态棒(3 mm) 在海水溶液中腐蚀表面的 FESEM 像[47]
2.4 制备工艺的影响
只有当熔融合金以较高的速率冷却时,晶体的形核和长大受到阻碍,金属内部液态结构才得以保留,从而形成非晶合金。因此,非晶合金的制备过程中最重要的是如何做到快速冷却。当前制备非晶合金技术已经比较成熟,常见的非晶合金制备方法包括铜模吸铸法、放电等离子烧结(SPS)、水淬法、单辊熔体旋淬等,不同工艺制备的非晶合金耐蚀性也有所不同[49
铜模吸铸法是目前最常见的制备块体非晶合金的方法。经过此法制备的非晶合金,不易形成气孔,避免了非晶合金的氧化过程,有利于提高耐蚀性,Fan 等[50]以铜模吸铸法成功制备了 Fe41Co7Cr15Mo14C15B6Y2 非晶合金,其在 1M 的H2SO4 溶液中的耐腐蚀性能明显高于不锈钢(SUS 321),和 Ti6Al4V 相接近,具有较好的耐蚀性能;Li 等[51]通过铜模吸铸法成功制备出 Fe65.5Cr4Mo4Ga4P12C5B5.5 非晶合金,发现在相同的腐蚀环境中,耐腐蚀性能明显高于常见合金(如不锈钢,碳化钢和钢),但是铜模内壁上容易形成不均匀晶核,从而使非晶合金表面容易出现腐蚀位点,破坏腐蚀性。Shin 等[52]研究了 SPS 的烧结温度对 Zr65Al10Ni10Cu15 耐蚀性的影响,在 640K 时可以获得最佳的耐蚀性能,而在 620K 时致密化尚未完成,在655K 时,诱导结晶使缺陷密度增加,耐蚀性能相对较差。值得注意的是,虽然烧结温度较低时,致密度较低,孔隙增加,但是烧结温度较高时,非晶态向晶态转变,因此选择合适的SPS 烧结温度至关重要。Ma 等[53]使用水淬法制备出Ni77-x -yMoxCryNb3P14B6非晶合金,探究了非晶合金在 1M NaCl 和 1M HCl 溶液中的腐蚀行为,腐蚀电流数量级均为 10-6A/cm2,耐蚀性远高于不锈钢材料,但水淬法冷却速度有限,所以该方法只适用于制备非晶形成能力较大的合金体系。Uhlenhaut 等[54]以单辊熔体旋淬制备 Mg70Al15Ga15 非晶合金,该非晶合金在中性溶液中腐蚀电流低于 10-6A/cm2,具有较高的耐腐蚀性;Liu 等[55]以不同的圆周转速(R)使用单辊熔体旋淬制备 Al86Ni9La5 非晶合金,使用一定压力对合金进行压缩,当转速较低时,压缩后易引进晶相,破坏耐蚀性,此外该方法还需要保证转速均匀,保证非晶薄膜的均匀性,以避免合金非均质引起耐蚀性降低,因此对单辊的转速要求也非常高。
总而言之,铜模吸铸法可以避免非晶合金在制备过程中产生氧化,却容易在非晶合金表面上形成不均匀晶核,为点蚀提供位点;对于 SPS,我们需要更加注重烧结温度的确定和选择,以保证非晶合金的致密度和减少晶化,使其具有最佳耐蚀性能;水淬法虽然设备简单,操作方便,但是其水冷速度有限,仅适宜 Pd-Ni-Cu-P 和 vit1 等非晶形成能力强的合金制备;单辊熔体旋淬对于单辊的转速要求较高,既需要保证转速合理,又需要保证转速均匀,避免非晶合金的非均质性,各种方法均有优缺点,因此我们需要根据生产需要合理恰当选择。
2.5 腐蚀介质的影响
同一非晶合金在不同腐蚀介质下的腐蚀情况也会有所差异,因此研究非晶合金在不同介质下的腐蚀行为对于非晶合金的应用服役也是至关重要。Padhy 等[56]研究了非晶合金 Zr59Ti3Cu20Al10Ni8 在 1N、6N、11.5N HNO3 和 0.5 mol/L NaCl、1 mol/L NaCl 溶液中的耐腐蚀性,在 HNO3 中经动电位阳极极化测试,随着硝酸浓度的增加,钝化区变窄,钝化膜逐渐溶解,耐蚀性能提高,而在不同浓度 HNO3 和 NaCl 中浸泡不同时间后,可以观察到随着腐蚀介质浓度的增加,非晶合金耐蚀性能均会出现恶化。Ge 等[57]研究了 Zr50.7Ni28Cu9Al12.3 非晶合金及其退火后复合材料在 1 mol/L HC(lpH=0)、0.5 mol/L H2SO(4pH=0.19)和 0.5 mol/LNaCl(pH=6.31)溶液中的耐蚀性,结果如图 4 所示,可以看出腐蚀电位与 pH 值关系并不大,而是与溶液中的成分有较大的关系,Cl-的存在能够引起非晶合金的电蚀,使钝化膜变得不稳定。
图 4 非晶合金 Zr50.7Ni28Cu9Al12.3 在 1M HCl、0.5M H2SO4 和 0.5M NaCl 溶液中 Ecorr 和pH 值的关系[57]
从现有研究结果来看,Ti 基非晶合金在 NaCl 溶液中较 Mg 基合金和 Al 基合金 Icorr 会更低[55, 58-60],耐蚀性能更好;Fe 基、Cr 基、Cu 基非晶合金在 HCl 溶液中耐蚀性要明显比 Zr基非晶合金更差[15, 19, 21, 31, 32, 35];Ca 基非晶合金在人体液环境下耐蚀性极差[40];而非晶合金对于碱的耐蚀性能都较好,Icorr 在 10-1-10μA/cm2 之间[19, 26, 27]。因此我们在选择非晶合金时应该根据腐蚀介质选择不同体系的非晶合金来满足应用的需求。
2.6 表面状态的影响
非晶合金的表面结构和性质也会对合金的耐蚀性产生一定的影响。Wang 等[61]研究了 Zr41Ti14Cu12Ni10Be23 (LM1)和 Zr44Ti11Cu10Ni10Be25 (LM1b)两种非晶合金在 pH=7.4 的腐蚀溶液中表面的润湿性和耐蚀性二者之间的关系,结果显示,在 LM1b 更疏水的情况下,其耐蚀性也要明显高于 LM1;Ma 等[62]也研究了 Pd-Ni-Cu-P 系非晶合金表面疏水性与耐蚀性之间的关系,结果证明非晶合金表面超疏水和耐蚀性有一定联系;而 Gu 等[63]在对非晶合金表面电子逸出功与 Ti-Zr-Be-(Ni-Fe) 系非晶合金耐蚀性能的关系的研究中,使用不同粒径的 SiO2 来控制非晶合金表面粗糙度,结果表明,粗糙度较高的非晶合金样品表面电子活性较低,不利于钝化膜的形成,从而耐蚀性较差,且粗糙度较大的非晶合金样品表面更容易由于化学不均质性引起局部腐蚀,从而造成耐蚀性的下降。
非晶合金表面与腐蚀介质直接相接触,因此研究表面状态对于耐蚀性能相当重要,但是当前研究更多的是探究非晶合金表面润湿性以及粗糙度与耐蚀性之间的关系,方便对于成分相似的非晶合金可以快速预测腐蚀性能[61
2.7 应力的影响
非晶合金性能优越,被认为是一种新型结构材料,在应用过程中非晶合金通常需要承受一定的载荷,如拉伸、压缩和弯曲,因此有必要考察应力状态对非晶合金耐蚀性能的影响。
Li 等[64]研究了 Mg66Zn30Ca3Sr1 非晶合金在循环载荷作用下,在磷酸盐缓冲液(PBS)中的腐蚀疲劳行为,相较于空气中受载,在 PBS 中非晶合金疲劳寿命和疲劳强度都较低。在腐蚀环境中,钝化膜中 Mg(OH)2 与氯离子缓慢反应,从而产生腐蚀区域,而应力集中通常发生在腐蚀区域,使它们成为裂纹萌生源。循环加载条件会使腐蚀速率加快,产生的反复弹性变形也会破坏钝化膜,甚至产生电偶腐蚀和缝隙腐蚀,造成非晶合金局部剥落性断裂,最终粉碎性断裂;断裂的时间与循环应力大小密切相关。总之,非晶合金的疲劳腐蚀对循环应力比较敏感。
Gostin 等[65]以铜模吸铸法制备 Zr52.5Cu17.9Al10Ni14.6Ti5 非晶合金,并通过三点弯曲加载,研究了非晶合金在 0.01mol/LNa2SO4 + 0.01mol/L NaCl 溶液中的应力腐蚀开裂(SCC),研究表明,非晶合金的 SCC 倾向随着外加阳极电位和施加应力的增加而增加。进一步研究发现,裂纹起源于非晶合金边缘缺陷,边缘缺陷诱发点蚀,进而经裂纹扩展形成 SCC。但是裂纹萌生前点蚀过程不受外加应力的影响,应力只影响到裂纹的扩展,这也是与腐蚀疲劳所明显不同的一点。
Liu 等[55]使用单辊熔体旋淬制备 Al86Ni9La5 非晶合金并研究了其在 10 和 15MPa 压应力作用下、在 3.5% NaCl 溶液中的耐腐蚀性,随着压力的增加,耐蚀性会有所下降。在圆周速度为 29.3m/s 时,压缩后引入剪切带,使钝化电流密度增大,从而恶化耐蚀性,但是在其为14.7m/s 时,非晶合金基体中引入自由体积、剪切带和结晶相 Al11La3,阻碍了钝化原子的迁移并降低了钝化膜的形成速率,非晶合金内部缺陷的增加降低了钝化膜稳定性,使耐蚀性有所下降。总而言之,压应力会降低耐蚀性,影响非晶合金的应用。
An 等[66]研究了拉伸对 Cu60Zr30Ti10 非晶合金在 1 mol/L NaCl、1 mol/L HCl 和 0.5 mol/L H2SO4 溶液中的耐蚀性能影响,腐蚀行为都随拉伸发生显著的变化,这与元素的局部分布和应变状态随拉力的变化相关,在该合金体系中,拉伸后使 Zr、Ti 在钝化膜中分布更加均匀,有利于耐蚀性的提高,因此在 H2SO4 中,元素的均匀分布有利于钝化的发生和 Ecorr 的提高,但是拉伸带来的自由体积增加会使钝化区减少,更易发生点蚀,但是在 1M 含 Cl-的溶液中,均匀化分布带来的影响远远小于自由体积增加所带来的负面作用,因此腐蚀电位急剧下降,耐蚀性稍有所降低。
非晶合金受力情况不同,对于耐蚀性的影响也会有所不同。对于腐蚀疲劳和应力腐蚀开裂,均会导致裂纹的萌生和扩展,最终引起材料的失效,在压应力作用下,容易在非晶合金中引入剪切带、结晶相和自由体积,缺陷的增加会降低非晶合金的耐蚀性能;但是在拉应力作用下,我们常常需要考虑由于拉应力引起的元素均匀化分布和自由体积的引入二者之间的平衡关系,需要综合分析来判断对于耐蚀性能的影响。非晶合金在应用过程中不可避免的受载,实际受载情况更是复杂多变,更需要我们对于试验数据不断积累丰富并继续深入研究载荷影响机制。
2.8 其他因素的影响
除了以上指出的非晶合金耐蚀性影响因素外,其他因素如温度、流速、CO2 分压、氧化、退火气氛以及加工工艺也会对耐蚀性产生一定的影响。尚世智等[67]研究了 Zr 基非晶合金 Zr53.5Cu26.5Ni5Al12Ag3 在 25℃和 60℃温度下在不同 NaOH 浓度下的耐腐蚀性,在 NaOH 浓度相同的情况下,浸泡 100h 后,在 60℃下的腐蚀电流密度远远大于 20℃,钝化膜产生了较大的破坏;毕凤琴等[68]采用正交试验研究不同温度、流速、CO2 分压、Cl-浓度对铁基非晶合金涂层 Fe-Cr-Mo-Mn-W-B-C-Si 腐蚀速率的影响,结果表明,温度为 120℃、流速为 1m/s、CO2 分压为 0.5MPa、Cl-浓度为 30g/L 时,腐蚀速率最大,且其中温度影响占据首要地位;Si 等[69]在研究 Cr40Co39Nb7B14 和 Cr50Co29Nb7B14 非晶合金在 HCl 中腐蚀性时指出,增加在氧化环境下的暴露可以加速合金的钝化,以提高耐蚀性能;Li 等[70]研究了 Al86Ni9La5 在H2、空气、Ar 和 N2 不同退火气氛下退火后在 3.5 wt.% NaCl 溶液中的耐蚀性能,由于在 H2 和空气中,H2 和 O2 更容易诱导结晶,促进钝化元素的扩散,更快形成钝化膜,并且纳米微晶结构有利于杂质的均匀分布,为稳定的钝化膜提供均匀的衬底,从而改善耐蚀性;Gebert 等[71]通过对 Zr59Ti3Cu20Al10Ni8 非晶合金进行喷丸处理,虽然非晶合金塑性有所改善,但是对于在 0.01 mol/L Na2SO4 +x mol/L NaCl (x= 0;0.01;0.1)和 6 mol/L HCl 含氯溶液中的抗点蚀能力略微下降,喷丸后形成的机械损伤成为氯离子侵蚀的有利位点,使钝化膜保护作用降低。
3.非晶合金耐蚀性能的改善途径
与传统晶态金属材料相比,非晶合金具有更好的耐蚀性,但非晶合金的耐蚀性能还有进一步提升的空间,此外,部分非晶合金在特定腐蚀介质中的耐蚀性,如 Zr 基非晶合金在含
Cl-腐蚀介质中耐蚀性相对较差[41],因此学者们对非晶合金耐蚀性能的改善开展了大量研究工作。目前较常用的提高耐蚀性的方法有以下几种:
(1)通过微弧氧化、离子注入或者其他表面处理方式来改变非晶合金表面组成或结构。Liu等[72]通过将C 离子注入 Co-Cr-Mo,促进非晶合金表面非晶化,当 C 离子浓度为 1.0×1017/cm2时,非晶合金的 Icorr 从 204.6nA/cm2 降低至 19.2nA/cm2,Ecorr 从-202.8mV 提高至-103.6mV,图 5 也给出腐蚀过后二者形貌的差异,耐蚀性能有极大的改善;Sharma 等[73]研究了 N 离子注入 Zr55Cu30Ni5Al10 非晶合金后的耐蚀性,当 N 离子浓度为 1×1016/cm2 时,由于非晶合金表面 ZrN、ZrO2 的形成,Icorr 从 7.71nA/cm2 降低至 2.13nA/cm2,维钝电流(Ipass)从 3.175μA/cm2降低至 1.257μA/cm2,耐蚀性得到改善;Chen 等[74]在 Mg-Zn-Ca 系非晶合金表面通过微弧氧化制得含 Si 涂层,使得非晶合金 Ecorr 升高 130mV 左右,Icorr 降低两个数量级,耐蚀性得到极大的提升。
图5 Co-Cr-Mo 非晶合金腐蚀试验后注入C 和未处理的表面形貌[72]
(2)降低非晶合金自由体积,提高合金的耐蚀性。Tailleart 等[75]在研究热致弛豫对非晶合金 Al87Co7Ce6 的耐蚀性的影响时,提出热致弛豫使非晶合金内部键长变短,配位数增高,自由体积减少,使耐蚀性能得到改善;Liu 等[76]研究重熔处理对 Gd56Al26Co18 和 Sm56Al26Co18非晶合金耐蚀性的影响时指出, 重熔会使自由体积减少, 使 Gd56Al26Co18 的 Icorr 从 0.2029×10-4A/cm2 降低至 0.1173×10-4A/cm2,Ecorr 从-120.6mV 提高至-113.6mV,Sm56Al26Co18的 Icorr 从 0.7436×10-4A/cm2 降低至 0.6531×10-4A/cm2,Ecorr 从-121.0mV 提高至-112.4mV,耐蚀性均有所提高。
(3)通过退火或者原位合成引入第二相,形成非晶复合材料。Shi 等[77]在研究等温退火对 Zr59Ti6Cu17.5Fe10Al7.5 非晶合金耐蚀性时结果表明,4 h 等温退火可以在非晶合金中引入 Al3Zr2晶相,合金 Ecorr 有所降低,但是 Icorr 由 3.90×10-7A/cm2 降低至 3.55×10-7A/cm2,点蚀电位(Epit)由 0.786V 提高至 0.991V,较铸态合金稍有改善;Yang 等[78]通过原位反应合成含有晶相 β-Ti (Zr, Nb) 的非晶复合材料 Ti42.3Zr29.1Cu6.6Nb6Be16,其中在 HCl 中的 Icorr 为 10-6-10-7A/cm2,在 H2SO4 中的 Icorr 为 10-7-10-8A/cm2,具有较好的耐蚀性能。
(4)在非晶合金中加入钝化能力强的元素或开发新的非晶合金体系,如 Cr 基、Co 基、Ti基等。Li 等[79]研究了使用 Cr 改善 Fe71-xCrxMo3.5Ni5P10C4B4Si2.5 非晶合金耐蚀性,改善结果如图 6 所示,在 3.5wt%的NaCl 溶液中,当 Cr 添加较小量时,如 4%时,Icorr 从 6.48×10-6A/cm2降低至 5.80×10-7A/cm2,Ecorr 由-0.37V 提高至-0.30V。根据合金化对于非晶合金耐蚀性的影响,许多元素对于非晶合金耐蚀性有积极影响,因此可以选择适当的元素开发新的非晶合金体系,如 Cr、Co、Ti 等。相关研究[66]已经证明,Ti 的加入可以改善 Cu-Zr 系非晶合金在 HCl 中的耐蚀性,Cu60Zr30Ti10 非晶合金在 1M HCl 中 Icorr 为 2.7×10-5A/cm2,Ecorr 为-83.6mV,而研究[80]的 Ti 基非晶合金如 Zr30.88Ti33.57Cu7Ni5.39Be23.16 在 1M HCl 中 Icorr 为 5.2×10-7A/cm2, Ti 基非晶合金耐蚀 性能明显 更加优异 ; Xu 等 [32] 研究 了 Cr 基非晶 合金 CrxFe56-xCo7Mo14C15B6Y2 (x = 15, 30, 45 at.%) 在 1M HCl 溶液的耐蚀性,随着 x 的增大,Ecorr分别为 0.048V、0.066V、0.074V,Icorr 在 10-3-10-4A/cm2 之间,耐蚀性逐渐改善,但是相对应的 Fe 基非晶合金在 HCl 中耐蚀性相对较差,研究表明,非晶合金 Fe43Cr16Mo16(C, B, P)25在 1M HCl 中 Icorr 在 10-1-10-2A/cm2 之间[21],较 Cr 基非晶合金耐蚀性有所差异。
图 6 室温下 3.5 wt.% NaCl 溶液中动电位极化曲线[79]
4.总结与展望
非晶合金因其内部不存在晶界、位错等结构缺陷,具有优于传统晶态合金材料的耐蚀性能[81]。目前,学者们研究了 Fe 基、Zr 基、Ti 基、Cr 基、Mg 基、Al 基、Co 基、Cu
基等非晶合金在酸、碱、盐等常见腐蚀介质中的腐蚀行为,初步揭示了合金成分、结构弛豫、部分结晶、制备工艺、腐蚀介质、表面状态、应力等因素对非晶合金耐蚀性能的影响规律,提出了改变非晶合金表面组成或结构、降低非晶合金自由体积、形成非晶复合材料和加入钝化能力强的元素或开发新的非晶合金体系等提高非晶合金耐蚀性能的措施与方法。自非晶合金被研究以来,目前已开发出超过 80 种非晶合金体系、约 20000 种非晶合金成分。因此,在继续研发具有高耐蚀性能的新型非晶合金的同时,需要不断积累非晶合金的耐蚀性能数据,深入研究非晶合金腐蚀机制。由于非晶合金是一类亚稳材料,在其制备、成形过程中常常伴随有晶化的问题,因此有必要系统研究部分晶化对非晶合金耐蚀性能的影响。此外,非晶合金实际服役环境下腐蚀介质较为复杂(如海水、体液等等),且腐蚀往往与热、应力、辐照等因素耦合,对其耐蚀性能提出了更高的要求。因此,开展非晶合金实际服役条件下的耐蚀性研究,实现非晶合金耐蚀性与其它性能(如室温塑韧性)的综合优化,对促进非晶合金作为耐蚀材料获得广泛应用具有重要意义,仍需要研究人员的不断努力。
参考文献
1] Wang W H. The elastic properties, elastic models and elastic perspectives of metallic glasses[J]. Progress in Materials Science. 2012,57(3): 487-656.
[2] Brenner A, Couch D E, Williams E K. Electrodeposition of alloys[J]. Journal of Research of the National Bureau of Standards. 1950(44): 109-122.
[3] Greer A L, Sun Y H. Stored energy in metallic glasses due to strains within the elastic limit[J]. Philosophical Magazine. 2016, 16(96):1643-1663.
[4] Li H, Pang S, Liu Y, et al. Biodegradable Mg-Zn-Ca-Sr bulk metallic glasses with enhanced corrosion performance for biomedical applications[J]. Materials & Design. 2015, 67: 9-19.
[5]Han C, Wei Y, Zhang H, et al. Corrosion Resistance and Electrochemical Behaviour of Amorphous Ni84.9Cr7.4Si4.2Fe3.5 Alloy in Alkaline and Acidic Solutions[J]. Acta Metallurgica Sinica (English Letters)。 2019, 32(11): 1421-1436.
[6]Mao L, Zhu H, Chen L, et al. Enhancement of corrosion resistance and biocompatibility of Mg-Nd-Zn-Zr alloy achieved with phosphate coating for vascular stent application[J]. Journal of Materials Research and Technology. 2020.
[7]Si C, Duan B, Zhang Q, et al. Microstructure, corrosion-resistance, and wear-resistance properties of subsonic flame sprayed amorphous Fe-Mo-Cr-Co coating with extremely high amorphous rate[J]. Journal of Materials Research and Technology. 2020.
[8]Zhang L, Jia Z, Lyu F, et al. A review of catalytic performance of metallic glasses in wastewater treatment: Recent progress and prospects[J]. Progress in Materials Science. 2019, 105: 100576.
[9]Ding S, Xiang T, Li C, et al. Fabrication of self-cleaning super-hydrophobic nickel/graphene hybrid film with improved corrosion resistance on mild steel[J]. Materials & Design. 2017(117): 280-288.
[10] Zhou Q, Sheikh S, Ou P, et al. Corrosion behavior of Hf0.5Nb0.5Ta0.5Ti1.5Zr refractory high-entropy in aqueous chloride [J]. Electrochemistry Communications. 2019(98): 63-68.
[11] Si C, Duan B, Zhang Q, et al. Self-healing characteristic of praseodymium conversion coating on AZNd Mg alloy studied by scanning electrochemical microscopy[J]. Electrochemistry Communications. 2017(76): 6-9.
[12] Tian W, Du N, Li S, et al. Metastable pitting corrosion of 304 stainless steel in 3.5% NaCl solution[J]. Corrosion Science. 2014, 85:372-379.
[13] Laleh M, Hughes A E, Xu W, et al. On the unusual intergranular corrosion resistance of 316L stainless steel additively manufacturedby selective laser melting[J]. Corrosion Science. 2019(161): 108189.
[14]Coimbr?o D D, Zepon G, Koga G Y, et al. Corrosion properties of amorphous, partially, and fully crystallized Fe68Cr8Mo4Nb4B16 alloy[J]. Journal of Alloys and Compounds. 2020, 826: 154123.
[15]Tan C, Jiang W, Wu X, et al. Effect of crystallization on corrosion resistance of Cu52.5Ti30Zr11.5Ni6 bulk amorphous alloy[J]. Transactions of Nonferrous Metals Society of China. 2007, 4(17): 751-754.
[16]Wu X, Xie C. Influence of crystallization on corrosion resistance of Al86Ni6La6Cu2 amorphous alloy[J]. Journal of Rare Earths.2008, 26(5): 745-748.
[17] Fengqin B I, Bang Z, Yong W. Effect of Alloying on Anti?corrosion Performance of Stainless Steel: a Review[J]. Materials Review. 2019, 33(7): 1206-1214.
毕凤琴,周帮,王勇。 合金化对不锈钢耐蚀性能影响的研究进展[J]. 材料导报。 2019, 33(7): 1206-1214.
[18] Borgioli F, Galvanetto E, Bacci T. Corrosion behaviour of low temperature nitrided nickel-free, AISI 200 and AISI 300 series austenitic stainless steels in NaCl solution[J]. Corrosion Science. 2018(136): 352-365.
[19]Xu J, Niu J, Zhang Z, et al. Effects of B Addition on Glass Formation, Mechanical Properties and Corrosion Resistance of the Zr66.7?x Ni33.3B x (x = 0, 1, 3, and 5 at.%) Metallic Glasses[J]. JOM. 2016, 68(2): 682-691.
[20]Huang L, Qiao D, Green B A, et al. Corrosion behavior of bulk (Zr58Nb3Cu16Ni13Al10)100-xYx (x = 0, 0.5, 2.5 at.%) metallic glasses in sulfuric acid[J]. Intermetallics. 2009, 4(17): 195-199.
[21]Pang S J, Zhang T, Asami K, et al. Synthesis of Fe-Cr-Mo-C-B-P bulk metallic glasses with high corrosion resistance[J]. Acta Materialia. 2002, 50(3): 489-497.
[22]Wang S L, Yi S. The corrosion behaviors of Fe-based bulk metallic glasses in a sulfuric solution at 70°C[J]. Intermetallics. 2010, 18(10): 1950-1953.
[23] Chattoraj I, Baunack S, Stoica M, et al. Electrochemical response of Fe65.5Cr4Mo4Ga4P12 C5B5.5 bulk amorphous alloy in different aqueous media[J]. Materials and Corrosion. 2004, 55(1): 36-42.
[24]Wang J, Wan Y, Ma Z, et al. Glass-forming ability and corrosion performance of Mn-doped Mg-Zn-Ca amorphous alloys for biomedical applications[J]. Rare Metals. 2018, 37(7): 579-586.
[25]Zhou J, Li K, Wang B, et al. Impact of Nd addition on glass formation anility and corrosion resistance of Mg-Zn-Ca alloys[J]. Materials Reports. 2019, 1(33): 73-77.
周杰,李克,王彪,等。 添加 Nb 对 Mg-Zn-Ca 合金非晶形成能力和耐蚀性的影响[J]. 材料导报。 2019, 1(33): 73-77.
[26]Nie X P, Yang X H, Jiang J Z. JAC2009_in press_Ti microalloying effect on corrosion resistance and thermal stability of CuZr-based bulk metallic glasses[J]. Journal of Alloys and Compounds. 2009, 1-2(481): 498-502.
[27]Long Z L, Chang C T, Ding Y H, et al. Corrosion behavior of Fe-based ferromagnetic (Fe, Ni)-B-Si-Nb bulk glassy alloys in aqueous electrolytes[J]. Journal of Non-Crystalline Solids. 2008, 354(40-41): 4609-4613.
[28]Zhou W, Weng W P, Hou J X. Glass-forming Ability and Corrosion Resistance of Zr-Cu-Al-Co Bulk Metallic Glass[J]. Journal of Materials Science & Technology. 2016(4): 349-354.
[29]Zhang C, Li N, Pan J, et al. JAC2010_in press_Enhancement of glass-forming ability and bio-corrosion resistance of Zr-Co-Al bulk metallic glasses by the addition of Ag[J]. Journal of Alloys and Compounds. 2010(504): S163-S167.
[30]Yu L, Tang J, Wang H, et al. Corrosion behavior of bulk (Zr58Nb3Cu16Ni13Al10)100-xYx (x = 0, 0.5, 2.5 at.%) metallic glasses in sulfuric acid[J]. Corrosion Science. 2019, 150: 42-53.
[13]Jin Z S, Yang Y J, Zhang Z P, et al. Effect of Hf substitution Cu on glass-forming ability, mechanical properties and corrosion resistance of Ni-free Zr-Ti-Cu-Al bulk metallic glasses[J]. Journal of Alloys and Compounds. 2019, 806: 668-675.
[14]Xu T, Pang S, Li H, et al. Corrosion resistant Cr-based bulk metallic glasses with high strength and hardness[J]. Journal of Non-Crystalline Solids. 2015, 410: 20-25.
[15]Li H, Pang S, Liu Y, et al. Biodegradable Mg-Zn-Ca-Sr bulk metallic glasses with enhanced corrosion performance for biomedical applications[J]. Materials & Design. 2015, 67: 9-19.
[16]Cao Q P, Peng S, Zhao X N, et al. Effect of Nb substitution for Cu on glass formation and corrosion behavior of Zr Cu Ag Al Be bulk metallic glass[J]. Journal of Alloys and Compounds. 2016, 683: 22-31.
[17]Xu T, Pang S, Zhang T. Glass formation, corrosion behavior, and mechanical properties of novel Cr-rich Cr-Fe-Mo-C-B-Y bulk metallic glasses[J]. Journal of Alloys and Compounds. 2015, 625: 318-322.
[18]Xu D D, Zhou B L, Wang Q Q, et al. Effects of Cr addition on thermal stability, soft magnetic properties and corrosion resistance of FeSiB amorphous alloys[J]. Corrosion Science. 2018(138): 20-27.
[19]Dan Z, Takenaka K, Zhang Y, et al. Effect of Si addition on the corrosion properties of amorphous Fe-based soft magnetic alloys[J]. Journal of Non-Crystalline Solids. 2014, 402: 36-43.
[20]Li X, Zhao X, Liu F, et al. Effect of C addition on the corrosion properties of amorphous Fe-based amorphous alloys[J]. International Journal of Modern Physics B. 2019, 33(01n03): 1940006.
[21]Zhang L M, Zhang S D, Ma A L, et al. Influence of cerium content on the corrosion behavior of Al-Co-Ce amorphous alloys in 0.6?M NaCl solution[J]. Journal of Materials Science & Technology. 2019, 35(7): 1378-1387.
[22]Babilas R, Bajorek A, W?odarczyk P, et al. Effect of Au addition on the corrosion activity of Ca-Mg-Zn bulk metallic glasses in Ringer's solution[J]. Materials Chemistry and Physics. 2019, 226: 51-58.
[23]Zhou M, Hagos K, Huang H, et al. Improved mechanical properties and pitting corrosion resistance of Zr65Cu17.5Fe10Al7.5 bulk metallic glass by isothermal annealing[J]. Journal of Non-Crystalline Solids. 2016, 452: 50-56.
[24]González S, Pellicer E, Suri?ach S, et al. Mechanical and corrosion behaviour of as-cast and annealed Zr60Cu20Al10Fe5Ti5 bulk metallic glass[J]. Intermetallics. 2012, 28: 149-155.
[25]Liu X, Bu W, Liu R. Effects of Heat Treatment Temperature on Corrosion Resistance of Amorphous Alloys[J]. Journal of Netshape Forming Engineering. 2018, 10(6): 34-37.
刘小江,卜文德,刘容光。 热处理温度对非晶合金耐蚀性能的影响[J]. 精密成形工程。 2018, 10(6): 34-37.
[26]Poddar C, Ningshen S, Jayaraj J. Corrosion assessment of Ni60 Nb30Ta10 metallic glass and its partially crystallized alloy in concentrated nitric acid environment[J]. Journal of Alloys and Compounds. 2020, 813: 152172.
[27]Hua N, Liao Z, Wang Q, et al. Effects of crystallization on mechanical behavior and corrosion performance of a ductile Zr68Al8Ni8Cu16 bulk metallic glass[J]. Journal of Non-Crystalline Solids. 2020, 529: 119782.
[28]Lin J G, Xu J, Wang W W, et al. Electrochemical behavior of partially crystallized amorphous Al86Ni9La5 alloys[J]. Materials Science and Engineering: B. 2011, 176(1): 49-52.
[29]Gu Y, Zheng Z, Niu S, et al. The seawater corrosion resistance and mechanical properties of Cu47.5Zr47.5Al5 bulk metallic glass and its composites[J]. Journal of Non-Crystalline Solids. 2013, 380: 135-140.
[30]Debnath M R, Kim D, Fleury E. Dependency of the corrosion properties of in-situ Ti-based BMG matrix composites with the volume fraction of crystalline phase[J]. Intermetallics. 2012, 22: 255-259.
[31]Ríos C T, de Souza J S, Antunes R A. Preparation and characterization of the structure and corrosion behavior of wedge mold cast Fe43.2Co28.8B19.2Si4.8Nb4 bulk amorphous alloy[J]. Journal of Alloys and Compounds. 2016, 682: 412-417.
[32]Fan H B, Fan H B, Zheng W, et al. Corrosion Behavior of Fe41Co7Cr15Mo14C15B6Y2 Bulk Metallic Glass in Sulfuric Acid Solutions[J]. Metallurgical and Materials Transactions A. 2011, 42(6): 1524-1533.
[33]Li G, Huang L, Dong Y, et al. Corrosion behavior of bulk metallic glasses in different aqueous solutions[J]. Science China Physics, Mechanics and Astronomy. 2010, 53(3): 435-439.
[52] Shin S, Kim T, Kang S. The influence of spark plasma sintering temperature on the mechanical properties and corrosion resistance of Zr65Al10Ni10Cu15 metallic glass powder[J]. Intermetallics. 2010, 18(10): 2005-2008.
[53] Ma X, Zhen N, Guo J, et al. Preparation of Ni-based bulk metallic glasses with high corrosion resistance[J]. Journal of Non-Crystalline Solids. 2016, 443: 91-96.
[54] Uhlenhaut D I, Furrer A, Uggowitzer P J, et al. Corrosion properties of glassy Mg70Al15Ga15 in 0.1M NaCl solution[J]. Intermetallics. 2009, 17(10): 811-817.
[55] Liu Y, Wang W, Zhang H, et al. Effect of Compression on the Crystallization Behavior and Corrosion Resistance of Al86Ni9La5 Amorphous Alloy[J]. Journal of Materials Science & Technology. 2012, 28(12): 1102-1108.
[56] Padhy N, Ningshen S, Mudali U K. Electrochemical and surface investigation of zirconium based metallic glass Zr59Ti3Cu20Al10Ni8 alloy in nitric acid and sodium chloride media[J]. Journal of Alloys and Compounds. 2010(503): 50-56.
[57] Ge W, Li B, Axinte E, et al. Crystallization and Corrosion Resistance in Different Aqueous Solutions of Zr50.7Ni28Cu9Al12.3 Amorphous Alloy and Its Crystallization Counterparts[J]. JOM. 2017, 69(4): 776-783.
[58] Liu S, Xia C, Yang T, et al. High strength and superior corrosion resistance of the Ti-Ni-Cu-Zr crystal/glassy alloys with superelasticity[J]. Materials Letters. 2019(260): 126938.
[59] Gu J, Shao Y, Shi L, et al. Novel corrosion behaviours of the annealing and cryogenic thermal cycling treated Ti-based metallic glasses[J]. Intermetallics. 2019, 110: 106467.
[60] Hua N, Huang Y, Zheng Z, et al. Tribological and corrosion behaviors of Mg56.5Cu27Ag5Dy11.5 bulk metallic glass in NaCl solution[J]. Journal of Non-Crystalline Solids. 2017, 459: 36-44.
[61] Wang Y B, Li H F, Zheng Y F, et al. Correlation between corrosion performance and surface wettability in ZrTiCuNiBe bulk metallic glasses[J]. Applied Physics Letters. 2010, 25(96)。
[62] Ma J, Zhang X Y, Wang D P, et al. Superhydrophobic metallic glass surface with superior mechanical stability and corrosion resistance[J]. Applied Physics Letters. 2014, 104(17): 173701.
[63] Gu J, Shao Y, Bu H, et al. An abnormal correlation between electron work function and corrosion resistance in Ti-Zr-Be-(Ni/Fe) metallic glasses[J]. Corrosion Science. 2020, 165: 108392.
[64] Li H, Liu Y, Pang S, et al. Corrosion fatigue behavior of a Mg-based bulk metallic glass in a simulated physiological environment[J]. Intermetallics. 2016, 73(C): 31-39.
[65] Gostin P F, Eigel D, Grell D, et al. Stress corrosion cracking of a Zr-based bulk metallic glass[J]. Materials Science and Engineering: A. 2015, 639: 681-690.
[66] An W K, Cai A H, Xiong X, et al. Effect of tension on corrosive and thermal properties of Cu60Zr30Ti10 metallic glass[J]. Journal of Alloys and Compounds. 2013, 563: 55-62.
[67] Shang S, Kong M, Li Y. Corrsion Behavior of Zr53.5Cu26.5Ni5Al12Ag3 Bulk Metallic Glass in NaOH[J]. Journal of Shenyang University of Chemical Technology. 2012, 26(3): 199-205.
尚世智,孔美玲,李云。 锆基非晶合金在 NaOH 溶液中的腐蚀行为[J]. 沈阳化工大学学报。 2012, 26(3): 199-205.
[68] Bi F, Yang S, Liang Z, et al. Study on High Temperature and High Pressure Corrosion Behavior of Iron-based Amorphous Coatings in CO2/ Cl-Coexisting Medium[J]. Chemical Engineering & Machinery. 2018, 45(2): 157-160.
毕凤琴,杨烁,梁柱,等。 铁基非晶涂层在 CO2/Cl-共存介质中的高温高压腐蚀行为研究[J]. 化工机械。 2018, 45(2): 157-160.
[69] Si J J, Chen X H, Cai Y H, et al. Corrosion behavior of Cr-based bulk metallic glasses in hydrochloric acid solutions[J]. Corrosion Science. 2016, 107: 123-132.
[70] Li G H, Wang W M, Ma H J, et al. Effect of different annealing atmospheres on crystallization and corrosion resistance of Al86Ni9La5 amorphous alloy[J]. Materials Chemistry and Physics. 2011, 125(1-2): 136-142.
[71] Gebert A, Concustell A, Greer A L, et al. Effect of shot-peening on the corrosion resistance of a Zr-based bulk metallic glass[J]. Scripta Materialia. 2010, 9(62): 635-638.
[72] Liu C, Zhou Z, Li K. Improved corrosion resistance of CoCrMo alloy with self-passivation ability facilitated by carbon ion implantation[J]. Electrochimica Acta. 2017(241): 331-340.
[73] Sharma P, Dhawan A, Sharma S K. Influence of nitrogen ion implantation on corrosion behavior of Zr55Cu30Ni5Al10 amorphous alloy[J]. Journal of Non-Crystalline Solids. 2019, 511: 186-193.
[74] Chen S, Tu J, Hu Q, et al. Corrosion resistance and in vitro bioactivity of Si-containing coating prepared on a biodegradable Mg-Zn-Ca bulk metallic glass by micro-arc oxidation[J]. Journal of Non-Crystalline Solids. 2017, 456: 125-131.
[75] Tailleart N R, Huang R, Aburada T, et al. Effect of thermally induced relaxation on passivity and corrosion of an amorphous Al-Co-Ce alloy[J]. Corrosion Science. 2012, 59: 238-248.
[76] Jingtao L, Jixin H, Xiaorong Z, et al. Influence of Remelting Treatment on Corrosion Behavior of Amorphous Alloys[J]. Rare Metal Materials and Engineering. 2017, 2(46): 296-300.
[77] Shi H, Tang C, Zhao X, et al. Effect of isothermal annealing on mechanical performance and corrosion resistance of Ni-free Zr59Ti6Cu17.5Fe10Al7.5 bulk metallic glass[J]. Journal of Non-Crystalline Solids. 2020, 537: 120013.
[78] Yang Y J, Zhang Z P, Jin Z S, et al. A study on the corrosion behavior of the in-situ Ti-based bulk metallic glass matrix composites in acid solutions[J]. Journal of Alloys and Compounds. 2018(782): 927-935.
[79] Li J, Yang L, Ma H, et al. Improved corrosion resistance of novel Fe-based amorphous alloys[J]. Materials & Design. 2016(95):225-230.
[80] Yang Y J, Jin Z S, Ma X Z, et al. Comparison of corrosion behaviors between Ti-based bulk metallic glasses and its composites[J]. Journal of Alloys and Compounds. 2018, 750: 757-764.
[81] Liang S, Jia Z, Liu Y, et al. Compelling Rejuvenated Catalytic Performance in Metallic Glasses[J]. Advanced Materials. 2018, 30(45):1802764.
免责声明:本网站所转载的文字、图片与视频资料版权归原创作者所有,如果涉及侵权,请第一时间联系本网删除。
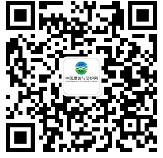
官方微信
《中国腐蚀与防护网电子期刊》征订启事
- 投稿联系:编辑部
- 电话:010-62316606-806
- 邮箱:fsfhzy666@163.com
- 中国腐蚀与防护网官方QQ群:140808414