(,南京 211100)
摘要:采用等离子喷涂技术制备了 FeCrMoCBY 铁基非晶涂层,研究了铁基非晶涂层在 3.5wt. %NaCl 溶液中浸泡不同时长后的电化学腐蚀性能和微观组织结构。结果表明,在 720h 的浸泡期间,涂层的耐蚀性经历了先提高后降低的变化,在浸泡 216h 时达到最优,腐蚀电流密度达到最低,为 3.393×10-5 A·cm-2,且此时涂层的表面更加致密,没有明显孔隙。在经过 720h 浸泡后,涂层仍能保持在一个相对较低的腐蚀电流密度, 6.970×10-5 A·cm-2。
关键词:等离子喷涂,铁基非晶,涂层,耐蚀性
非晶合金在物理和力学等性能方面表现极为优越[1],主要归因于两点,首先非晶合金不存在位错、晶格缺陷、晶界等结构缺陷[2、3];另外,就化学成分而言,非晶合金的元素分布均匀,不存在成分偏析等现象[4]。铁基非晶涂层与由相同化学组分构成的晶态涂层相比,其硬度、耐磨性等力学性能和耐腐蚀性能均更为优异[5-8]。因而在海洋、矿山机械等对防腐耐磨性能要求较高的领域有广泛的应用。在铁基非晶涂层的制备方面,等离子喷涂技术以其具有的热源速度快,喷涂温度高(大于 10000K),等离子焰流高度稳定等诸多特点,成为铁基非晶涂层制备技术的焦点之一[9-12]。Liu 等[13]、Kobayashi 等[14]均成功应用等离子喷涂技术制备出了铁基非晶涂层。关于铁基非晶涂层的耐蚀性也有多位学者进行研究,Wang 等[15]的研究表明涂层在 3.5wt.%NaCl 溶液中自腐蚀电流相较钢基体能够降低两个数量级。但有关浸泡对铁基非晶涂层耐蚀性影响的研究还相对较少,本研究通过研究在 3.5wt.%NaCl 溶液中浸泡不同时长的铁基非晶涂层电化学腐蚀性能和微观组织结构,对等离子喷涂铁基非晶涂层的耐蚀性进行了探究。
1 实验方法
本实验以 Fe48Cr15Mo14C15B6Y2(质量分数%)非晶系粉末为喷涂材料,以 Q235 钢为基体,通过美国 PRAXAIR 3710 型等离子设备制备涂层。喷涂以 Ar 为主气和载气,以 He 为辅气。工艺参数如下,电流为 650A,主气压力为 50psi,辅气压力为 75psi,载气压力为 40psi,喷涂距离为 120mm。送粉率为 22.6g/min。
浸泡实验参照 JB/T7901-2001 标准[16]。浸泡过程中,为避免试样非涂层面的影响,使用环氧树脂对涂层进行镶嵌,另制作纯环氧树脂试样块作为对比样,本实验浸泡总时长为 720h,浸泡溶液为 3.5(质量分数)%NaCl 溶液,期间每 72h 更换一次浸泡溶液。
采用 CHI660E 型电化学工作站对浸泡了 1、72、216、432 和 720h 的喷涂态涂层分别进行测试,其中参比电极为甘汞电极,辅助电极为铂电极,工作电极为试样,溶液为 3.5%NaCl溶液。使用 HITACHI-3400N 扫描电子显微镜(SEM)分别对喷涂态涂层截面和浸泡 216h、720h的涂层表面进行观察。使用 HORIBA-7021-H 能谱仪(EDS)分别对喷涂态涂层截面和浸泡 216和 720h 的涂层进行元素分析。使用 D8 型 X 射线衍射仪(XRD)对喷涂态涂层和浸泡试验结束后的涂层分别进行分析,扫描角度为 10°-90°。
2 结果与讨论
图 1 为涂层的 XRD 图谱,由图可明显观察到涂层的 XRD 图谱呈现典型非晶态组织特征,即在 2θ=45°的位置出现明显宽化衍射峰。图 2 为涂层截面形貌,涂层的厚度为 300-350μm,呈明显层状堆叠结构,层与层之间结合较为紧密,存在少量孔隙和微裂纹,通过软件测算可得涂层孔隙率为 3.68%。
图 1 喷涂态涂层的 XRD 图谱
图 2 喷涂态涂层截面显微形貌
图 3 为浸泡不同时间后涂层在 3.5%NaCl 溶液中的 Tafel 极化曲线,从图 3 中可观察到所有的涂层的极化曲线都存在明显钝化区。图 4 为经不同时段浸泡后的涂层在 3.5%NaCl 溶液中的 Nyquist 图,从图中可以观察到涂层的 Nyquist 图均呈单一容抗弧特征,说明腐蚀介质在试验过程中未完全穿透涂层,反应主要在涂层-溶液的接触界面进行。此时涂层的等效电路为 R(Q(R(QR))),如图 5 所示,其中 Rs 为溶液电阻,Qc 和 Rc 分别代表涂层电容和涂层极化电阻,Qdl 和Rt 分别代表双电层电容和电化学反应电荷转移电阻,Rt 是一个与腐蚀速度密切相关的参数,Rt 越大,表明试样的耐蚀性越好。通过对涂层 Tafel 曲线分析可得到涂层的腐蚀电位、腐蚀电流,对 Nyquist 曲线拟合分析可得到涂层的电化学反应电荷转移电阻 Rt,三组数据均如表 1 所列。涂层经浸泡后的电化学腐蚀曲线特征与喷涂态涂层相差不大。经过浸泡后,涂层的腐蚀电流密度先下降后有所上升,并在浸泡 216h 达到最低,3.393×10-5 A·cm-2;自腐蚀电位呈现先提高后降低的变化趋势,表明在浸泡前期涂层的腐蚀倾向有所下降,但浸泡时间较长后,涂层的腐蚀倾向也重新开始回升。涂层的电化学反应电荷转移电阻随浸泡时间的延长也呈现先提高后降低的趋势。综合电化学腐蚀结果分析,在 720h 的浸泡期间,涂层的耐蚀性经历了先提高后降低的变化,但值得注意的是,经过 720h 的浸泡后,涂层依然保持在一个相对较低的腐蚀电流密度,6.970×10-5 A·cm-2,表明涂层经浸泡后在耐蚀方面的表现仍非常优异。
图 3 经过不同浸泡时长后涂层的 Tafel 极化曲线
图 4 经过不同浸泡时长后涂层的 EIS 图谱(Nyquist)
图 5 阻抗谱拟合电路模型
表 1 电化学腐蚀参数
图 6 为经过 720h 浸泡后的涂层的腐蚀产物的 XRD 图谱,可发现浸泡后的喷涂态涂层的腐蚀产物由 FeOOH、Fe2O3、FeCr2O4、Fe3O4 构成,腐蚀产物中含有铬的氧化物,结合前述电化学分析,推测可能是涂层在浸泡腐蚀初期 Fe 和 Cr 会同时参与腐蚀反应,由于 Fe 的腐蚀产物都呈现疏松的形态,难以抑制腐蚀的进行,因此浸泡前期涂层的电化学耐蚀性能较差,而经过较长时间浸泡后涂层中生成了 Fe-Cr 混合腐蚀产物,Cr 具有显著的钝化特性,能生成钝化膜,能够延缓腐蚀的继续进行,但后期,在腐蚀介质的长期作用下,Cr 的钝化膜遭到破坏,因而涂层的耐蚀性有所下降。
图 6 经过 720h 浸泡后涂层的 XRD 图谱
图 7 为未浸泡和经过 216 和 720h 浸泡后的涂层的微观形貌及 Cr 能谱分析的结果。通过图 7a 和 c 的对比,可以发现经 216h 浸泡后,涂层表面被大量腐蚀物质覆盖,涂层表面比较致密,没有明显孔隙。结合能谱分析可以发现,经过 216h 浸泡后的涂层的 Cr 的分布偏聚现象较显著,如图 7d 所示,而且基本集中于腐蚀产物处,Cr 氧化物的生成提高了涂层的自腐蚀电位,降低了涂层的腐蚀倾向,同时,腐蚀产物的堆积填补了涂层的缺陷部位,阻止了腐蚀介质的进一步侵蚀,涂层的耐蚀性有所提升。而通过图 7e 可以发现,经过 720h 浸泡后,涂层表面开始变得疏松,腐蚀产物表现出松散颗粒状态,表明涂层继续浸泡,腐蚀产物会受到腐蚀介质的进一步作用而失去防护的作用,而 Cr 的钝化膜也在这一过程中遭到破坏,其共同导致了涂层耐蚀性的下降。
图 7 未浸泡和经过 216 和 720h 浸泡后的涂层的显微形貌及 Cr 元素分布图
3 结论
(1)铁基非晶涂层经浸泡后,在 216h 耐蚀性达到最优,腐蚀电流密度达到最低,为 3.393×10-5 A·cm-2;经过 720h 浸泡后,涂层的腐蚀电流密度仍能达到 6.970×10-5 A·cm-2,表明经过浸泡后涂层的耐蚀性表现仍然十分优异。
(2)铁基非晶涂层经 216h 浸泡后,涂层表面孔隙、裂纹等缺陷处覆盖有大量腐蚀产物,涂层相比未浸泡涂层更加致密,没有明显缺陷。腐蚀产物中含有多种 Fe、Cr 氧化物,另外浸泡后涂层表面 Cr 的分布主要集中于腐蚀产物处。
参考文献
1)Wang L Q, Zhai S Q, Ding R, et al. Recent development of bulk amorphous alloys[J]. Foundry. Technol., 2017,38(02):274 (王立强,翟慎秋,丁锐,等。大块非晶合金研究进展[J].铸造技术,2017,38(02):274)Inoue A, Takeuchi A. Recent development and application products of bulk glass alloys[J]. Acta. Mate.,2011,59(6):2243-2267.
2)Nie Y S, Li W, Li D K, et al. Microstructure and properties of Fe-based amorphous alloy coating deposited by electro-spark deposition process[J]. Chin. J. Mater. Res., 2013,27(1):75(聂英石,李文,李登科,等。电火花沉积 Fe48Cr16MO15C17B4 非晶合金涂层的微观组织和性能[J].材料研究学报,2013,27(1):75)
3)Liang X B, Cheng J B, Feng Y. Research progress on Fe-based amorphous coatings[J]. J. Mater. Eng., 2017,45(09):1 (梁秀兵,程江波,冯源,等。铁基非晶涂层的研究进展[J].材料工程,2017,45(09):1)Wang M W, Tang C Y, Chen X Y, et al. Research progress of corrosion resistance and friction resistance for Fe-based amorphous
alloy coating[J]. J. Chengdu Technol. Univ., 2016,19(02):56(汪明文,唐翠勇,陈学永,等。铁基非晶合金涂层的耐腐蚀及耐摩擦性能研究进展[J].成都工业学院学报,2016,19(02):56)
[6]Wang Y, Zheng Y G, Wang J Q, et al. Passivation behavior of Fe-based amorphous metallic coting in NaCl and H2SO4 solution[J].Acta. Metall. Sin., 2015,51(01):49(王勇,郑玉贵,王建强,等。铁基非晶涂层在 NaCl 和H2SO4 溶液中的钝化行为[J].金属学报,2015,51(01):49)
[7]Huang Y, Wang S L, Wang S X, et al. Corrosion resistance of Fe-based bulk metallic glass with sulfide inclusions in HCl solution[J]. J. Chin. Soc. Corros. Prot., 2018,38(02):203(黄勇,王善林,王帅星,龚玉兵,柯黎明。含硫化物夹杂铁基块体非晶合金在 HCl 溶液中的腐蚀行为[J].中国腐蚀与防护学报,2018,38(02):203)
[8] Nie G M, Huang C, Li B, et al. Fabrication and application status of Fe-based amorphous alloy coatings[J]. Surf. Technol.,2017,46(11):6(聂贵茂,黄诚,李波,等。铁基非晶合金涂层制备及应用现状[J].表面技术,2017,46(11):6)
[9]Liu X Q, Zheng Y G, Chang X C, et al. Microstructure and properties of Fe-based amorphous metallic coating produced by high velocity axial plasma spraying[J]. J. Alloy. Compd., 2009, 484(1-2), 300
[10]Zhou Z, Wang L, Ye D Y, et al. Microstructure and electrochemical behavior of Fe-based amorphous metallic coatings fabricated by atmospheric plasma spraying[J], J. Therm. Spray. Techn., 2011, 20, 344
[11]Li S B, Xu L K, Shen C J, et al. Performance of erosion resistance ceramic coatings deposited by plasma spraying[J]. J. Chin. Soc.Corros. Prot., 2011,31(03):196(李守彪,许立坤,沈承金,等。等离子喷涂耐冲蚀陶瓷涂层的性能研究[J].,2011,31(03):196)
[12]Li C Y, Ding J Q, Zhu F P, et al. Research progress of Fe-based amorphous coating by thermal spraying technology[J]. J. Func.Mater., 2018,49(12):12056(李春燕,丁娟强,朱福平,等。热喷涂技术制备铁基非晶涂层的研究进展[J].功能材料,2018,49(12):12056)
[13] Liu X Q, Zheng Y G, Chang X C, et al. Microstructure and properties of Fe-based amorphous metallic coating produced by highvelocity axial plasma spraying[J]. J. Alloy. Compd., 2009,484(1):300
[14]Akira Kobayashi, Shoji Yano, Hisaraichi Kimura, et al. Fe-based metallic glass coatings produced by smart plasma spraying process[J]. Mater. Sci. Eng. B-adv., 2008,148(1-3):110
[15]Wang S L, Yi S. The corrosion behaviors of Fe-based bulk metallic glasses in a sulfuric solution at 70℃[J]. Intermetallics.,2010,10(8):1950
[16] JB/T 7901-2001, Metals materials -Uniform corrosion -Methods of laboratory immersion testing[S].JB/T 7901-2001, 金属材料实验室均匀腐蚀全浸试验方法[S].
免责声明:本网站所转载的文字、图片与视频资料版权归原创作者所有,如果涉及侵权,请第一时间联系本网删除。
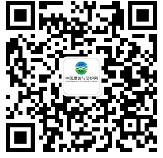
官方微信
《中国腐蚀与防护网电子期刊》征订启事
- 投稿联系:编辑部
- 电话:010-62316606-806
- 邮箱:fsfhzy666@163.com
- 中国腐蚀与防护网官方QQ群:140808414