海底管线(海管)作为海底原油输送的动脉,其运行状态直接关系到油田的正常生产,海管一旦发生泄漏,不仅会引起设备更换、平台停产等巨大的经济损失,还会造成严重的环境污染。据统计,1986-2016年间中海油有37%管道故障是腐蚀导致的,尤其是多相流混输管道,其腐蚀问题更为突出。
由于海管在海底服役,其监测、检测以及维修的难度要远高于陆地管道,一旦发生腐蚀泄漏将会造成无法估量的损失,因此,掌握海管真实的腐蚀状态和详实的腐蚀特征信息变得尤为重要。内腐蚀直接评价是海管完整性管理的重要工作内容之一,它通过分析海管的生产数据、检测数据、运维数据等多源数据,综合评判海管内腐蚀状况以及腐蚀剩余寿命,充分评判现有防腐措施的有效性,为后续海管的腐蚀管理提供有效的管控措施,减少安全事故的发生。内腐蚀直接评价的基本流程包括:预评价、间接评价、详细检查和后评价。
某海底多相流混输管线已投产二十余年,因管线结构问题无法进行内检测,为了解其内腐蚀状况,参考国际通行的管道内腐蚀直接评价方法,对该海管的内腐蚀风险进行评价。由于该海管为双层结构海管,暂无法实现对内管的详细壁厚检查,中海石油(中国)有限公司深圳分公司和安科工程技术研究院(北京)有限公司的技术人员利用室内腐蚀模拟试验代替详细检查,以验证评价方法的可靠性。
预评价
预评价的主要目的是对目标管线进行数据收集与校核,该部分工作一方面为内腐蚀直接评价提供数据支持,另一方面可对管线设计、建造、施工和运维期间的数据进行梳理,发现日常运维管理中的问题并及时纠正。预评价的具体流程如图1所示。
图1 预评价流程
该海管投产于1994年,设计寿命为25年。管线材质为API 5L X70钢,输送介质为油气水混输物。管线为双层保温管:外管的外径355.6 mm,壁厚9.5 mm;内管的外径273.1 mm,壁厚12.7 mm。管线入口温度89~97 ℃,出口温度56~78 ℃,入口压力0.59~0.91 MPa,出口压力0.35~0.46 MPa。管线日输量1798~3853 m3/d,含水率14%~45%。管内腐蚀性气体CO2和H2S的含量分别为24%(质量分数,下同)和0.0005%?基于上述信息初步识别该海管的内腐蚀风险,为间接评价阶段提供数据基础?
间接评价
间接评价是基于目标管线的数据情况,使用内腐蚀直接评价模型或软件对管线的内腐蚀风险进行预测。按照NACE SP0116-2016标准,评价管线的内腐蚀风险位置应考虑两个因素:首先从壁厚损失角度分析,根据管线的流态变化对目标管线进行评价分区,并将每一个评价分区进一步划分子区,重点关注子区内壁厚损失大于其平均值的位置;另一方面,由于多相流海管输送介质中含固体物质,需重点关注流速较低、固态颗粒易积聚、易发生结垢的潜在风险位置。通过建立模型对管线内输送介质的固体积聚风险进行判断。间接评价的具体流程如图2所示。
图2 间接评价流程
(1)壁厚损失预测
根据该海管的实际情况,选择De Waard腐蚀预测模型和Petalas-Aziz多相流模型分别预测管线沿里程的腐蚀速率变化和流态变化。首先根据流态变化划分子区,然后选择子区内腐蚀速率大于平均值的位置作为重点关注位置。
海管流态及腐蚀速率变化趋势图如图3所示,海管的腐蚀速率沿里程呈现先升高后降低的趋势,全线流态以分层流为主,出口附近出现几处段塞流,根据流态变化将全线划分为6个子区,计算每个子区腐蚀速率的平均值,将每个子区内腐蚀速率大于平均值的位置作为重点关注位置,从壁厚损失角度筛选出的重点关注位置如图4所示。
图3 海管的腐蚀速率-流态沿里程的变化
图4 从壁厚损失角度筛选出的重点关注位置
(2)固体积聚预测
对于多相流管道的内腐蚀进行直接评价,判断管道是否存在固体积聚的风险是标准中明确规定的必不可少的一个环节。而一旦管道内出现固体积聚,往往会诱发管道内部产生垢下腐蚀,同时也为细菌提供适宜的生长环境从而加重管道的细菌腐蚀。因此,借助适宜的多相流模型对管道内介质的固体积聚情况进行模拟,对于多相流混输介质管道内腐蚀直接评价至关重要。但混输介质管道的内腐蚀直接评价起步较晚,现有标准中并没有明确给出混输介质固体积聚预测的推荐方法和模型,因此下文参考几种常用的公式分析目标管道的固体积聚风险。
目标多相流海管输送介质中含有少量砂,该海管内砂粒径范围在0.09~2.00mm,砂密度为2700kg/m3(花岗岩材质),砂在海管流动介质中的体积分数约为0.003%。
预测砂沉积的临界流速是判断海管中是否会发生砂沉积的关键。若实际运行中海管内水相流速大于砂沉积的临界流速,则水可以把砂携带走而不会发生砂沉积;反之,若海管内实际水相流速小于砂沉积临界流速则会发生砂沉积。
因海管中砂粒径是不均匀的,因此可认为海管输送的是非均匀的混合粒径浆体,对于这种非均质流体,其临界流速目前有多种计算公式,其适用范围有所不同,目前还没有统一的公式。技术人员选用了比较常见的几种公式对海管中砂沉积临界流速进行了预测:
砂沉积临界流速:
卡察斯基公式:0.49m/s
舒克公式:0.62m/s
王可欣公式:0.47m/s
海管水相流速:0.35~0.54m/s
根据NACE SP0208-2008标准推荐模型计算得到管线沿里程的水相流速为0.35~0.54m/s,将水相流速与砂沉积临界流速(为突出砂沉积高风险位置,取3种模型中计算结果最小的值)对比,见图5。
图5 水相流速与砂沉积临界流速对比
小于砂沉积临界流速的位置有发生砂沉积风险,根据该原则筛选出砂沉积位置如图6所示。
图6 砂沉积高风险位置分布
(3)高风险位置
参考NACE SP0116-2016标准,综合考虑管线沿里程的腐蚀速率/壁厚损失、流态、固体积聚、温度、压力、流速等参数确定最终的内腐蚀高风险位置。针对目标海管,考虑上述因素共筛选出13处内腐蚀高风险位置,其沿里程分布如图7所示。建议后续对这13处位置进行重点关注,条件允许的情况下开展水下检测,由被动维修变主动防御,保障海管的安全运行。
图7 海管内腐蚀高风险位置的分布
腐蚀模拟试验
内腐蚀直接评价的第三步为详细检查,即开挖管道利用超声波测厚等手段实际检查管线的剩余壁厚,与预测结果进行对比验证。但因目标海管为双层保温管,无法直接对内管进行常规的详细检查。本工作通过腐蚀模拟试验的方法获取海管的内腐蚀速率,同时结合海管的运行年限推测海管的壁厚减薄量,并与软件预测结果进行对比分析,进而验证预测结果的准确性。
参照ASTM G170-2006标准在高温高压反应釜中模拟实际工况环境进行腐蚀模拟试验,研究X70管线钢的腐蚀行为,试验周期为7天,具体参数及结果如下:
材质:X70
温度:90.2℃
压力:0.86MPa
CO2质量分数:24%
H2S质量分数:50×10-4%
流速:0.75m/s
溶液:下海管水样
腐蚀速率:0.452mm/a
预测腐蚀速率:0.51mm/a
材质:X70
温度:71.0℃
压力:0.47MPa
CO2质量分数:18%
H2S质量分数:35×10-4%
流速:0.75m/s
溶液:上海管水样
腐蚀速率:0.136mm/a
预测腐蚀速率: 0.22mm/a
结果表明,试验所得腐蚀速率与软件预测结果基本吻合,验证了评估模型的准确性。
图8和图9分别为X70管线钢表面宏微观腐蚀形貌。结果表明,此试验条件下,X70管线钢发生的是均匀腐蚀,无点蚀现象。
(a)入口水样 (b)出口水样
图8在不同水样中腐蚀后X70管线钢表面宏观形貌
(a) 入口水样
(b) 出口水样
图9 在不同水样中腐蚀后X70管线钢表面微观形貌
后评价
通过对比分析腐蚀模拟试验结果和腐蚀预测结果发现,预测结果与试验结果基本吻合,表明本次选用的评价模型适用于目标海管。基于预测得到的壁厚损失,参照DNV-RP-F101-2017标准计算目标海管的剩余强度,当前工况下,该海管失效压力为47MPa,远高于设计压力,即目标海管的剩余强度未受到影响。假设海管按照当前最高腐蚀速率继续发展,其剩余寿命为9年。根据ASME B31.8S-2016和NACE SP0110-2010标准规定,最大再评价周期为剩余寿命的一半,即该海管再评估周期为4.5年。
结 论
采用多相流管线内腐蚀直接评估方法对某海管进行了评价。参考NACE SP0116-2016标准,从壁厚损失预测和固体积聚预测两个角度综合判断海管的内腐蚀高风险位置。通过腐蚀模拟试验验证了预测结果的准确性。预测结果显示目前该海管存在内腐蚀,但其剩余强度暂未受到影响,剩余寿命为9年,再评估周期为4.5年。
免责声明:本网站所转载的文字、图片与视频资料版权归原创作者所有,如果涉及侵权,请第一时间联系本网删除。
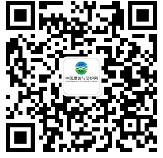
官方微信
《中国腐蚀与防护网电子期刊》征订启事
- 投稿联系:编辑部
- 电话:010-62316606-806
- 邮箱:fsfhzy666@163.com
- 中国腐蚀与防护网官方QQ群:140808414