一、铝合金复合材料
铝合金复合材料的优势所在
在汽车轻量化中强调运用铝合金复合材料,与其自身特点有很大关系。具体而言,铝合金复合材料是一种生命力强大的材料,不仅密度低、尺寸稳定、强度较高,而且耐磨性好、抗断抗疲劳,还具有良好的塑性与模量等诸多优点。其中锻造铝合金材料优势更为突出,即表面光、洁热锻不氧化,加工余量小、无缺陷,强大的刚度可与合金钢相媲美等,经高强度热处理后的铝锻件在汽车轻量化中的运用越来越广泛。
如丰田公司曾在发动机活塞制备中使用铝合金复合材料,较之铸铁活塞不仅质量减轻了5%-10%,还提高了4倍左右的导热性。虽然如此,但在我国汽车轻量化发展中,铝合金复合材料尚未得到有效推广,毕竟铝材成本较高,既需要大量的研发费用和维修成本,在深冲、弹性模量等部分力学性能方面还有待改善,致使其使用效果和应用范围难以达到预期效果。
铝合金复合材料在汽车轻量化中的运用
1、 在车身中的运用
在汽车质量中车身质量约占30% ,而且70%左右的油耗是用于承载车身质量的,可见将铝合金复合材料运用至汽车车身制造中十分必要,或者说势在必行。
如早在90年代初世界第一辆全铝车身框架轿车-奥迪A8第1代便诞生了,奥迪公司通过采用ASF车身结构,其以铝板元件为架构支撑,且基于所承担的任务采用不同形状和横截面积的元件,在保证低质量基础上获得最佳功能,具体可从车身构造中的A、B、C柱内部发现,不仅减轻了40%左右的质量,使得油耗和排放得以大幅降低,而且抗扭转刚度的提高可在一定程度上改变碰撞后的吸能路径,有助于最大限度的保护乘员,故整车的安全性能得到了明显改善。发展至今,奥迪A8整车质量和轻量化结构系数分别达到了250kg和1.5,可以说是汽车轻量化的一大重要成果。
再如Ford·P2000基于冲压焊接制造的铝制车身骨架,结合使用现有钢板加工工艺,使得自车身质量低至135.6kg,整车质量和百公里油耗分别减少了32.8%和22.8%,由此可知,铝合金复合材料在汽车车身轻量化中的合理运用发挥了良好的节能降耗效果,值得进一步研究和推广。
2 、在发动机中的运用
发动机在汽车质量中的比例约为20-30%,显然运用铝合金复合材料意义重大。目前最常见的是缸体缸盖、活塞、曲轴箱、油底壳以及连杆等部位,在此就活塞和缸体缸盖作重点分析。随着汽车制造工艺和性能要求的不断提高,越来越多的发动车活塞采用了铸铝合金材料,这是因为作往复运动的活塞需要借助减重降低惯性,达到降低曲轴配重提高工作效率的目的,且要求具有小的热膨胀系数和良好的导热性,并在350℃环境下能够发挥良好的力学性能,而铸铝合金不仅能够满足上述要求,而且轻质密度低,有助于减少发动机噪音和振以及油耗,故得以应用于活塞及连杆中。再者发动机缸体缸盖在导热性、抗腐蚀性等方面对材料的要求极高,故运用性能优良的铝合金复合材料也是必然的,当下很多国外汽车公司纷纷制备了全铝型缸体缸盖。
如日产VQ、凌志IMZ-FEV6等型号的发动机油底壳采用的便是铸造铝合金复合材料,但从样本机看,与传统材料相比其质量降低了20%左右。
3、 在底盘中的运用
其实在汽车轻量化实践过程中,底板系统不仅容易实现,而且潜力较大。对于悬挂系统来说,铝合金复合材料是替代钢铁的首选材料。
如福特公司经使用铝合金制动盘取代原铸铁盘,虽然成本有所增加,可是降低了2/3的质量,并提高了2倍的使用寿命;Neod Lite 车底盘在运用铝合金零部件后,使得转向机壳、万向节、下控制臂、转向轴以及后制动毂等质量均有所降低,显然符合轻量化要求;此外克尔维特与凯迪拉克等车辆经采用铝合金复合材料制备的零部件也取得了良好的效果。
4、 在车轮中的运用
对于汽车车轮质量而言,轮毂质量占到了70%的比例,试验表明,如果每减轻1kg的轮毂质量,在同样耗费1L汽油的情况下汽车行使距离可增加800m,或者说在节约1L油量的情况下,则有2.5kg的碳无法得到排放,所以轮毂轻量化既便于普及,也有着较高的铝化率和节能环保功效。同时运用铝合金复合材料的轮毂还可发挥良好的减震、抗腐蚀、散热作用,且经久耐用、容易制造,对于改善汽车安全性和舒适性意义重大。预计在日后的发展中,铝合金轮毂在我国的需求量会飞速增长,故有着广阔的发展空间。
二、碳纤维复合材料
碳纤维(carbon fiber,简称CF),是一种含碳量在90%以上的高强度、高模量纤维的新型纤维材料。是由片状石墨微晶等有机纤维沿纤维轴向方向堆砌而成,经碳化及石墨化处理而得到的微晶石墨材料。碳纤维“外柔内刚”,比重只有钢的四分之一,但强度却高于钢铁,并且具有耐腐蚀、高模量的特性。
碳纤维的优点
1.碳纤维复合材料的比强度和比模量高,是最理想的轻质高强车体材料。
2.碳纤维复合材料遇到碰撞时,不是通过塑性形变来吸收能量,而是变成无数细小的碎片,因而能够吸收大量的碰撞的能量,大约是钢结构的4倍,具有和高的安全性。
3.碳纤维复合材料容易成型,即容易成型出符合动力学原理以美观需求、光滑表面的外形,因此可以省去复杂繁琐的车身涂装加工的程序,降低一定成本。
4.碳纤维复合材料成型时,可以将不同的材料一体成型,更加有利于汽车在制造时的模块化和整体化。
5.碳纤维复合材料在酸溶液中、碱溶液中、以及有机溶液中均不溶解,化学性质稳定,因此耐腐蚀性能好、寿命长,几乎不需要维修,维修成本也很低。
6.碳纤维复合材料强度高,模量高,并没有蠕变,可以用于制造传动轴结构。兰博基尼投资打造的LP700-4车身,拥有极高的强度和刚度,安全性也很高。
F1赛车的刹车盘和刹车片也采用了碳纤维复合材料,这使得F1赛车的刹车盘无论是在性能上还是在价格上,都远远高于普通民用车的刹车盘。
但是,碳纤维也存在着自己的局限性
1.操作费时,批量生产少,设计及工艺的开发难度高。
2.材料成本也很高,全碳纤维车身和底盘的LFA售价高于30万英镑,这几乎是一辆法拉利458和一辆路虎揽胜的价格。
3.它是脆性材料,损坏后基本无法修复,而且碳纤维的高强度只限于轴向,它的径向强度是比较脆弱的,(因此往往利用其耐拉质轻的优势而避免去做承受侧面冲击的部分)。
4.碳纤维与其他材料的连接也是个问题,若使用传统的螺栓连接,连接周围很容易产生裂纹。
5.相对于铝合金而言,碳纤维无法做到回收利用。
汽车的防撞梁作为汽车保险杠的主要部件,是低速碰撞中最重要的承载和吸能部件,可以保护乘客和周围的部件。碳纤维复合材料密度小,比强度高,比模量大,碰撞吸能好。根据相关要求建立了碰撞模型后,对钢制防撞梁和碳纤维复合材料防撞梁进行测试,进行碰撞仿真,分析两种材料的吸能情况,结果表明:碳纤维的比吸能是钢制的3.7倍,减重达到了71.4%。吸能特性和轻量化效果提升显著。
如:2020款雪佛兰克尔维特黄貂鱼设计并制造了汽车行业第一款弯曲的多空心拉挤碳纤维防撞梁,它为黄貂鱼的后方及扩展躯干提供了强有力的保护,同时它的轻量化特性也大大提高了黄貂鱼的操控性以及节油性能。
人们对于碳纤维的运用在车身上也很多。相对于之前提到的碳纤维的缺点而言,宝马i系列将它在车身上的运用方法和技术,成功地回避了和解决了一些问题宝马i系列的车身结构大面积采用碳纤维材料,在制造端莱比锡工厂新建的车身制造车间将碳纤维强化塑料复合组件拼合起来,这样就制造出Life模块的基本结构。
由于BMW i3 Life模块的碳纤维强化塑料结构几何融合性高,其车身部件的数量只相当于普通钢制车身的三分之一,整个基本架构由大约150个碳纤维强化塑料组件组成,这也为售后维修提供了便利性。并且,该车身使用最先进的粘合技术并且实现了100%的自动化,避免了传统的螺栓连接而导致的产生裂纹的问题。而且,为了解决维修难的问题,采用这种车身连接工艺,将各个部件在不接触的情况下拼合为相互之间形成精确设定的粘合缝,以便在粘合工艺完成后达到最佳的车身刚性。在维修受损部位时,维修工人只需将其中一块小面积部件进行更换,并采用粘合技术进行再次衔接,这样带来的优势不仅可以恢复到之前的车身强度,成本上也得到了大幅降低。
三、片状模塑料
片状模塑料(SMC)可根据部件需要调整力学及耐腐蚀高温性能,适用于部分车身、承力结构件和耐高温腐蚀零件。SMC质量轻、强度高、易加工成型,可分为通用型、结构型和功能型三类,可替代车身的部分钢铝部件,是汽车轻量化的主流方向之一。该种材料的商业化应用目前主要集中在车体后尾门,其他的应用多为试验阶段。
如雷诺汽车的后尾门相比原钢制后尾门减重10%,且注塑、组装工艺简单,生产成本大为降低。
四、树脂基复合材料
树脂基复合材料不仅可使零部件降低多达 40%的质量,而且还可以使生产成本降低 40%左右。目前,玻璃纤维增强树脂复合材料和碳纤维增强树脂复合材料在汽车上已经获得成功的应用,已大量应用于汽车内饰件和外饰件。
玻璃纤维增强树脂复合材料(GFRP)耐腐蚀、绝缘性好,特别是有良好的可塑性,对模具要求较低,对制造车身大型覆盖件的模具加工工艺较简易,生产周期短,成本较低。在轿车和客车上,采用玻璃纤维增强树脂复合材料制造的轿车车身覆盖件、客车前后围覆盖件和货车驾驶室等零部件。
碳纤维增强树脂基复合材料(CFRP)具有轻质高强、高断裂韧性、耐腐蚀、可设计性强、易成型、减振阻尼性能好等一系列优点,既能够满足部件刚强度、轻量化的设计要求,在车辆安全性上也具有明显优势,因而是很有前途的汽车用轻量化材料,不过,目前存在成本高、成型周期长等缺点。
注:SMC 、GMT 、FRP 和LFT 分别为聚酯片状模塑料、玻璃纤维增强树脂,纤维增强复合材料和长纤维增强热塑性材料。
目前在汽车车身上已普遍应用的有用玻璃纤维增强不饱和聚酯片状模塑料(SMC)制造的车身空气导流板、前翼子板和前挡泥板延伸部件、大灯罩、发动机罩、装饰条、尾板等,用传递模塑工艺技术(RTM)制造的车身板件加强筋等。
五、纤维增强热塑性塑料
按照塑料中纤维的长度,可分为短纤维增强热塑性塑料(纤维长度一般为0.2至0.4 mm),长纤维增强热塑性塑料(纤维长度一般为10 mm以上)和连续纤维增强热塑性塑料。
LFT与其他材料相比
1、LFT与短玻纤增强塑料比较
和传统的短玻纤增强塑料相比,具备特殊的螺杆、模头及切割器设计和浸润剂配方的LFT技术可以得到12mm以上的料粒片材,纤维长度和料粒长度相当,让玻璃纤维在最终制品中拥有更长的玻璃纤维长度。一般的短纤维增强,在经过螺杆、注射口、模腔内流动这三个过程后,纤维的长度下降的非常厉害,最终制品中的纤维平均长度已经不到1mm,因此对制品的力学性能的帮助非常有限,而LFT技术,不论是模压还是注射成型,最终测试制品内的玻璃纤维平均长度仍然不低于4mm,因此大大提高了制品的机械性能。和短纤增强的结构件相比,抗冲击、抗蠕变性更好,抗热性能也更优异。
2、LFT与金属比较
和金属材料相比,LFT材料有非常低的密度和非常高的比强度,制品加工方法较灵活,材料回收率高,相比材料的成本较低,部件的功能性和整体性很高,LFT的部件加工设备如挤出机、注射剂或压机、打孔安装设备、模具,相比昂贵的金属冲击设备和模具来说,其成本是很低的,尤其事在生产批量不大的车型,LFT更体现出优异的经济性。因此,与钢制结构件相比,LFT使产品重量减轻了很多,并拥有部件合并性能,这样可以降低成本。
3、LFT与GMT相比较
LFT片材是继GMT(玻璃纤维毡增强热塑性塑料)片材后的新一代的热塑性复合材料,它是以长玻璃纤维为增强材料,以聚丙烯(PP)、PA、PET等为基体材料复合而成。
LFT片材与CMT片材相比较,其突出的优点是:
1、片材在压制过程中流动性较好。
2、片材价格较低。
3、材料的性能基本上与GMT相同。
若客户对材料的抗冲击性能要求较高时,本公司将会提供高抗冲击性能型号的LFT片材以供需要。
4、LFT与SMC相比较
LFT片材的产品制造工艺与热固性复合材料玻璃钢中的SMC(片状模压料)十分类似。同样是用片材在模具中压制而成。LFT是硬片材加热变软后在模具中冷压,而SMC是在冷态软片材放入模具后热压成型。
LFT片材与SMC片材相比,其技术性能具有如下优点:
1、 无毒、无味,可改善工作环境。
2、 质轻,密度只有1~1.2g/cm3。
3、 边角料及废品可循环使用,最大限度减少浪费。
4、 强度比SMC高,抗冲击韧性尤为突出。
5、 耐腐蚀、电性能更优良。
6、 产品压制速度比SMC快数倍,生产效率大幅提高。
长纤维增强热塑性材料(LFT)一直在汽车工业中用在半结构应用领域。它们的主要优点是诱人的成本/性能比和相对较低的密度。欧洲ELV(end of life vehicle)立法推动了这种材料的发展,该立法促进了再循环,因而也促进了热塑性材料对热固性材料的取代。
在汽车行业中,LFT主要被用于制作结构和半结构部件,如前端模块、保险杠大梁、仪表盘骨架、电池托架、备用轮胎仓、座椅骨架、脚踏板及整体底板等。长纤维增强聚丙烯被用于轿车的发动机罩、仪表板骨架、蓄电池托架、座椅骨架、轿车前端模块、保险杠、行李架、备胎盘、挡泥板、风扇叶片、发动机底盘、车顶棚衬架等;长纤维增强的PA,被进一步扩展到引擎盖内,因为LFT-PA不仅硬度高、重量低,而且高玻纤含量使其热膨胀系数几乎与金属相同,能承受引擎带来的高温。
如:
2003年,Mazda 6安装了全球第一款长纤维聚丙烯的前端模块,整个前端模块重量在3.5公斤,从而开始了长玻纤在前端模块的正式应用。据统计数据推算,预计在未来5年(2019~2024),全球塑料前端模块增长率为6%,现阶段前端模块材料集中在金属(市场占有量 40%),尼龙6+30%GF与金属复合或尼龙6+60%GF(市场占有量 25%),聚丙烯复合材料LGF30、LGF40,含少量D-LFT、GMT(市场占有量 35%),其中长玻纤前端模块经过10多年的发展,已经得到越来越多的OEM 认可,包括中国的汽车制造商如吉利、长城、广汽、上汽等主机厂,都已经开始批量使用长玻纤产品,替代传统的金属和尼龙前端模块。
作为发动机周边的零部件,一般选择具有耐热老化的 30%-40%的长纤维增强聚丙烯材料。
仪表板骨架应用
仪表板骨架上需要安装各种仪表,要求高刚度和尺寸稳定性,同时需要安装副安全气囊,满足安全气囊在低温-35℃和高温80℃的爆破要求,所以也属于安全部件,要求较高的抗冲击韧性和耐高低温性能。随着生活水平的提高,对内饰要求的要求也更加高档,软质仪表板的使用也是越来越多,仪表板骨架材料也从最先的PP-EPDM-TD30、TD20、PC/ABS和SMA+GF材料到现在改用玻璃纤维增强聚丙烯材料。长玻纤材料的一个特点是低温冲击强度比常温冲击强度更高,所以该材料的使用,提高仪表表骨架的气囊安全保护性能,同时,将仪表板骨架从3mm减薄到2.2mm,从而实现了该零部件的轻量化。
为了进一步提高材料性能,降低重量,改善尺寸稳定性和翘曲缺点,宝马公司引入了结构化学发泡(SGI)工艺。该工艺的特点是将长玻纤塑料和化学发泡剂混合后进入料斗,高速注塑进入模腔,然后再利用模芯后退工艺(Core-Back 工艺),给出发泡空间,进而获得较大发泡倍率,得到更高倍率的发泡结构件,根据模芯后退的程度来控制发泡倍率。在2017Mini、 Countryman微型跨界多功能车 (CUV) 的仪表板骨架上,就使用了该工艺,其减重效果达到15%。
除了宝马公司的SGI化学发泡工艺,业界也采用Mucell物理发泡与长玻纤结合的成型工艺,以获得减重与降低翘曲的仪表板骨架,但在早期的开发中,Mucell的发泡剂分散机构,很容易导致玻璃纤维的折断,不能保证最终制品中玻璃纤维长度,所以在使用Mucell工艺时,需要和注塑机企业讨论其工艺的实用性。
长玻纤在仪表板骨架的开发目前在国内的OEM使用还不多,除了结构较为复杂,厚度较薄、翘曲仿真难度较大之外,还因为前面提到副气囊的安全技术、整体产品的翘曲变形等问题,目前国外普遍采用有机纤维作为气囊保护装置,可以采用类似嵌件注塑的工艺一次成型。而国内还是以采用TPO弹性体为主的安全气囊支架技术,该技术需要先成型TPO安全气囊支架,然后利用焊接或者卡扣安装到仪表板骨架上面,再通过表面火焰处理后进行聚氨酯PU发泡等。
后尾门
后尾门目前普遍使用还是以金属结构为主,国外的日产、宝马等主机厂,已经逐步采用长玻纤的全塑后尾门技术,全塑后尾门一般包括外板和内板两部分,外板主要采用可喷涂的滑石粉填充聚丙烯材料,保证零部件的外观,而内板主要起增强作用,多采用玻璃钢 SMC 或者 30%~40% 长玻纤增强聚丙烯材料,两个板之间,采用胶粘等技术,保证后尾门的结构性与外观性要求。
零部件企业方面,日立化成在这块开发比较全面,其产品包括日产Infiniti EX、Infiniti FX、Murano等车型,在国产的日产英菲尼迪、Infiniti、 QX50和奇骏Rogue都已经使用了全塑后尾门产品。同时彼欧、麦格纳、佛吉亚等企业,在全塑后尾门都拥有自己的专利技术,上图是全塑后尾门爆炸示意图,通过长碳纤维、局部单向带材增强等技术,可以获得更大规模的减重效果。
六、玻璃纤维增强树脂
玻璃纤维毡增强热塑性复合材料(Glass Mat Reinforced Thermorplastic,简称GMT)是指以热塑性树脂为基体,以玻璃纤维毡为增强骨架的新颖、节能、轻质的复合材料,是目前国际上极为活跃的复合材料开发品种,被视为世纪新材料之一。
GMT一般可以生产出片材半成品,然后直接加工成所需形状的产品。GMT具备复杂的设计功能,以及出色的抗冲击性,同时易于组装和再加工,并因其强度和轻巧性而倍受赞誉,使其成为替代钢并减少质量的理想结构部件。
图 轻质高强的GMT材料
GMT材料的优点
比强度高:GMT的强度和手糊聚酯玻璃钢制品相似,其密度为1.01-1.19g/cm,比热固性玻璃钢(1.8-2.0g/cm)小,因此,它具有更高的比强度。
轻量化、节能 :用GMT材料做的汽车门自重可从26Kg降到15Kg,并可减少背部厚度,使汽车空间增大,能耗仅为钢制品的60-80%,铝制品的35-50%。
与热固性SMC(片状模塑料)相比,GMT材料具有 成型周期短、冲击性能好,可再生利用和储存周期长等 优点。
冲击性能:GMT吸收冲击的能力比SMC高2.5-3倍,在冲击力作用下,SMC、钢和铝均出现凹痕或裂纹,而GMT却安然无恙。
高刚性:GMT里含有GF织物、即使有10mph的冲击碰撞,仍能保持形状。
GMT材料在汽车领域的应用
GMT片材比强度高、可制得轻质部件,同时设计自由度高、碰撞能量吸收性强、加工性能好,从上个世纪90年代开始在国外被广泛应用于汽车工业中。而随着燃油经济性,可回收性和易加工性的要求不断提高,汽车行业用GMT材料市场也将继续稳步增长。
目前,GMT材料在汽车工业中的应用广泛,主要有座椅骨架、保险杠、仪表板、发动机罩、电池托架、脚踏板、前端、地板、护板、后牵门、车顶棚、行李托架、遮阳板、备用轮胎架等部件。
如:
1. 座椅骨架
福特汽车公司2015 Ford 跑车上的第二排座椅靠背压缩成型设计由一级供应商/加工商Continental Structural Plastics公司采用Hanwha L&C的45%单向玻纤增强的玻璃纤维毡热塑性复合材料(GMT)和Century Tool & Gage的模具,模压成型,成功地满足了极具挑战性的保持行李负载条件下的欧洲安全法规ECE。
该部件需要进行100多次FEA迭代才能完成,从早期的钢结构设计中省去了五个零件,并且在更薄的结构中每辆车可节省3.1千克,也更易于安装。
图 福特汽车公司2015 Ford Mustang跑车的第二排座椅靠背 来源:SPE&福特汽车
2. 车尾防撞梁
现代全新2015款全车尾的防撞梁为GMT采用的就是材料,相比钢材材质产品重量更轻,缓冲性能更好,在减轻车重、降低油耗的同时,保证了安全性能。
图 汽车之家
3. 前端模块
奔驰在其豪华双门轿跑车中选择Quadrant Plastic Composites GMTex?织物增强热塑性复合材料作为前端模块元件。
图 梅赛德斯S级双门跑车前端模块 图源:PressReleaseFinder
4. 车身下护板
由Quadrant Plastic Composites用高性能GMTex?制造的车身下罩保护应用于梅赛德斯越野特别版。
图 车身护板 来源:PressReleaseFinder
5. 尾门骨架
GMT尾门结构除了可以实现功能集成和减轻重量的通常优势外,GMT的可成型性也实现了钢或铝不可能实现的产品形式,应用于日产Murano、Infiniti FX 45等车型。
图 GMT材料的尾门骨架 来源:PressReleaseFinder
6. 仪表板框架
GMT制造仪表板框架的新概念已在福特集团的几种型号上使用:沃尔沃S40和V50,马自达3和福特C-Max。这些复合材料能够实现广泛的功能集成,特别是通过将车辆横梁以薄钢管的形式包含在模制件中,并且与传统方法相比,重量大大减轻,而无需增加成本。
图 GMT制造仪表板框架 来源:PressReleaseFinder
加工工艺
手糊成型工艺和技术
简单地说,手糊成型工艺(Hand Lay-up Molding)是手工作业把玻璃纤维织物和树脂交替地铺层在已被覆好脱模剂和胶衣的模具上,然后用压辊滚压压实脱泡,最后在常温下固化成型为汽车复合材料制品,如图1所示。尽管在现代汽车复合材料成型新工艺不断涌现的情况下,手糊成型工艺显得比较原始,但是,该工艺却具有其独特的不可替代性,仍然为世界各国汽车复合材料行业特别是中国汽车复合材料行业所广泛采用。
图1 手糊成型工艺示意图
图2所示为手糊成型工艺流程。从该工艺流程可以看出,手糊成型工艺具有以下优点:不需要复杂的设备和模具,投资低;生产技术容易掌握,且产品不受尺寸形状的限制,适合小批量和大型制件的生产;可与其他材料如金属、木材及塑料泡沫等同时复合制成一体。这些优点使得手糊成型工艺至今仍然作为汽车复合材料的一种主要成型工艺而被用于小批量地加工各种汽车复合材料制品,如客车和重型卡车的前/后围面板、高顶、导流罩、引擎罩盖、保险杠、挡泥板以及休闲车、农用车的车身等。此外该工艺还被用于新车开发,如制造概念车和新车样件试制。
图2 手糊成型工艺流程
手糊成型工艺的缺点是生产效率低,生产周期长,工作环境差,因此对于大批量车型的产品不太适合。此外,由于这种工艺与操作人员的技能水平和制作环境条件有很大的关系,受此影响,在我国,由手糊成型工艺生产的汽车零部件的质量往往不够稳定,从而影响了汽车复合材料的声誉。
需要说明的是,手糊成型工艺并不是劣质汽车复合材料零部件的代名词。只要严格按照手糊成型工艺的流程和工艺规范,准确掌握手糊工艺的技术要领,同样能够制作出一流水平的汽车复合材料制品。实际上,国外很多昂贵和精致的高档跑车以及在展会上熠熠生辉的很多概念车均出自于手糊成型工艺之手。图3所示的Chevrolet Corvette跑车,其车身即为用手糊成型工艺生产出来的。
图3 用手糊成型工艺生产的跑车车身
喷射成型工艺和技术
图4所示为喷射成型工艺(Spray Up Molding)示意图。该工艺是将混有引发剂和促进剂的两种聚酯分别从喷枪两侧喷出,同时将切断的玻纤无捻粗纱由喷枪中心喷出,使其与树脂在空间均匀混合后沉积到模具上。当沉积到一定厚度时,用压辊滚压使纤维浸透树脂,排除气泡,在经常温固化后成型为汽车复合材料制品。喷射成型工艺是在手糊成型工艺的基础上发展起来的。由于该工艺是借助于机械的手工操作工艺,因此也被称为“半机械手糊成型工艺” 。图5所示为该工艺的工艺流程。
图4 喷射成型工艺示意图
图5 喷射成型工艺流程
与手糊成型工艺相比,喷射成型工艺的效率提高了2~4倍甚至更高。其优点是:由于使用无捻粗纱代替了手糊工艺的玻璃纤维织物,因而材料成本更低;成型过程中无接缝,这使得制品的整体性和层间剪切强度更好;可自由调节产品的壁厚、纤维与树脂的比例以及纤维的长度,因而满足了汽车零部件的不同机械强度要求。由于喷射成型工艺具有效率高、成本低及产品尺寸形状不受限制的优点,因此该工艺在国外汽车复合材料行业中,有逐步取代传统的手糊成型工艺的趋势,例如,客车和重型卡车的很多前/后围面板、侧面护板、高顶及导流罩等都已由喷射成型工艺制作。
喷射成型工艺的缺点是:产品的均匀度在很大程度上取决于操作人员的操作熟练程度;由于喷射成型的树脂含量高且增强玻纤短,因而制品强度较低;阴模成型比阳模成型难度大,小型制品比大型制品生产难度大;生产现场工作环境恶劣,环境污染程度一般均大于其他的工艺方法;初期投资比手糊成型工艺大。尽管如此,近年来,喷射成型工艺的缺点正在得到极大的改善。在国外,已采用机械手编程来替代人工喷射,从而大大提高了产品质量的稳定性,原材料的损耗也被明显降低。同时,通过对生产现场采取全封闭的管理措施以及进行空气排放处理,使得环境污染问题得到明显改善。图6所示为采用喷射成型工艺生产的KENWORTH重卡高顶。
图6 采用喷射成型工艺生产的重卡高顶
缠绕成型工艺和技术
缠绕成型工艺(Filament Winding)是在控制纤维张力和预定线型的条件下,将浸过树脂胶液的连续纤维(或布带、预浸纱)按照一定的规律连续地缠绕到相应于制品内腔尺寸的芯模或内衬上,然后在室温或加热条件下使之固化、脱模,获得一定形状的汽车复合材料制品,如图7所示。根据纤维缠绕成型时树脂基体的物理化学状态不同,分为干法缠绕、湿法缠绕和半干法缠绕三种。其中,湿法缠绕的应用最为普遍。湿法缠绕工艺顾名思义是将连续玻璃纤维粗纱或玻璃布带浸渍树脂胶后,直接缠绕到芯模或内衬上而成型并经固化的成型方法。而干法缠绕一般仅用于高性能、高精度的尖端技术领域中。
图7 纤维缠绕成型工艺示意图
纤维缠绕成型工艺的优点是:能够按产品的受力状况设计缠绕规律,以充分发挥纤维的强度;比强度高。一般来讲,纤维缠绕压力容器与同体积、同压力的钢质容器相比,重量可减轻40%~60%;可靠性高。纤维缠绕制品易实现机械化和自动化生产,工艺条件确定后,缠出来的产品质量稳定、精确;生产效率高。采用机械化或自动化生产,只需少数操作工人,缠绕速度快(240m/min);成本低。在同一产品上,可合理配选若干种材料(包括树脂、纤维和内衬),使其再复合以达到最佳的技术经济效果。现在用纤维缠绕成型工艺生产的CNG/LPG高压气瓶、传动轴和板状弹簧等已广泛应用于大客车、轿车和卡车上。纤维缠绕成型工艺的缺点是:缠绕成型适应性小,不能缠任意结构形式的制品,特别是具有凹形表面的制品。这是因为缠绕时,纤维不能紧贴在芯模表面,而是处于架空状态;缠绕成型需要有缠绕机、芯模、固化加热炉、脱模机及熟练的技术工人,不仅投资大,而且技术要求高,因此只有大批量生产时才能获得较大的经济技术效益。图8所示为采用纤维缠绕成型工艺生产的CNG乘用车用高压气瓶。
图8 采用纤维缠绕成型工艺生产的CNG车用气瓶
树脂传递模塑成型工艺和技术
树脂传递模塑成型工艺(Resin Transfer Moulding)简称RTM。该技术始于1950年代,是从湿法铺层手糊成型工艺和注塑成型工艺中衍生出来的一种新的闭模成型工艺。该工艺一般是在模具的型腔中预先放置玻璃纤维增强材料(包括螺栓、螺帽或聚氨酯泡沫塑料等嵌件),闭模锁紧后,将配好的树脂胶液在一定的温度和压力下,从设置于适当位置的注入孔处注入模腔,浸透玻纤增强材料,然后一起固化,最后启模、脱模,得到两面光滑的汽车复合材料制品。图9所示为RTM工艺示意图。
图9 树脂传递模塑成型工艺示意图
图10所示为RTM的工艺流程。由于是一种闭模成型工艺,因此RTM的优点是:无需胶衣涂层即可使构件获得双面光滑的表面;在成型过程中散发的挥发性物质很少,有利于工人的健康和环境保护;模具制造与材料选择的机动性强,不需要庞大、复杂的成型设备就可以制造出复杂的、有极好制品表面的大型构件;根据设计需求,增强材料可以按任意方向铺放或局部增强,因而容易实现按制品受力状况铺放增强材料的目的。成型效率高、投资少以及易实现自动化生产的特点,使RTM工艺日益为汽车复合材料行业所重视,并逐步成为取代手糊成型、喷射成型的主导成型工艺之一。
图10 RTM工艺流程
目前,RTM工艺在汽车制造业中的应用已非常广泛,如乘用车的车顶、后厢盖、侧门框和备胎仓,以及卡车的整体驾驶室、挡泥板和储物箱门等都有用RTM工艺生产的。图11所示是用RTM工艺生产的ASTON MARTIN跑车的车身侧围板。
图11 用RTM工艺生产的车身侧围板
当然,RTM工艺也存在一些不足,如:双面模具的加工费用较高;预成型坯加工生产设备的投资大;对原材料(树脂和玻纤材料)和模具质量的要求高,以及对模具中的设置与工艺要求严格等。目前,对RTM成型工艺的研究和推广不断取得新的进展,主要研究方向集中在:微机控制注射机组、增强材料预成型技术、低成本模具、快速树脂固化体系及工艺稳定性和适应性等方面,涌现出了一系列改良的RTM成型工艺,如 Lite-RTM、VARTM、VIP和TERTM等。
模压成型工艺和技术
模压成型工艺(Compression Molding)是复合材料生产中最古老而又富有无限活力的一种成型方法。它是将一定量的预混料或预浸料加入金属对模内,经加热、加压固化而成型的一种方法,如图12所示。模压料的品种有很多,可以是预浸物料、预混物料,也可以是坯料。当前常用的模压料品种有:热固性复合材料,包括SMC、BMC和TMC等;热塑性复合材料,包括GMT、D-LFT和G-LFT等。
图12 模压成型工艺示意图
在提到模压成型工艺技术时,我们特别要提到汽车复合材料工业广泛应用的热固性复合材料SMC和热塑性复合材料GMT模压成型工艺。
SMC主要采用金属对模的模压成型工艺,其压制工艺过程相对比较简单,主要包括片状模塑料的制备和成模两部分。由于SMC的组成比较复杂,每种组分的种类、质量、性能及其配比等对SMC的生产工艺、成型工艺及最终制品的性能、价格等都有很大的影响,因此,对组分、用量和配比等进行合理的选择,对于制造优良的汽车SMC零部件具有十分重要的意义。图13所示为SMC模压成型工艺流程。
图13 SMC模压成型工艺流程
GMT片材的成型通常有两种:一是连续玻璃纤维毡或针刺毡与热塑性塑料层合而成,另一种则是随机分布的中长纤维与粉末热塑性树脂制成的片材。前者适合于冲压模压成型,其制品的形状一般比较简单。后者的流动性较好,适合于流动模压成型,适于成型形状较为复杂的汽车零部件。与金属材料相比,GMT的密度约为钢材的1/6~1/7,具有耐腐蚀以及隔热、隔音和绝缘性好的优点,可一次加工成型复杂的制品;与SMC片状模塑料相比,GMT具有极长的贮存期,制品的成型周期是SMC的1/3~1/4,并且冲击韧性好,可回收利用。基于以上特点,GMT在汽车工业中的应用范围不断扩大,应用量不断增加,正越来越多地代替金属和热固性复合材料。
与SMC相似,GMT也是采用金属对模的模压成型工艺,所不同的是SMC的固化成型是化学反应,而GMT的冷却成型是物理变化,成型所要求的工艺参数和对压机、模具的技术要求是不相同的。GMT成型工艺的特点是:片材必须先预热(加热至220~230℃),成型压力高(10~25Mpa),成型温度低(35~50℃),成型周期短(30~60s)。GMT模压成型工艺流程如图14所示。
图14 GMT模压成型工艺流程
总之,模压成型工艺的主要优点是:生产效率高,便于实现专业化和自动化大批量生产;产品尺寸精度高,重复性好;表面光洁,无需二次修饰;能一次成型结构复杂的制品;由于可批量生产,因此价格相对低廉。这些优点使得模压成型工艺特别适合汽车工业要求批量大、精度高及互换性好的生产特点,是目前汽车复合材料工业中最为普遍采用的成型工艺,尤其是乘用车上的复合材料零部件80%均由模压成型工艺制成,如引擎盖、车门、后厢盖、后举门、车顶、前端框架、仪表台骨架、车门中间承载板、座椅骨架和底部护板等。
模压成型工艺的不足之处在于模具制造复杂,投资较大,加上受压机限制,使其更适合于生产中、大批量的汽车复合材料制品(热固性汽车复合材料制品在100000件/年以内,热塑性汽车复合材料制品在1000000件/年以内)。随着金属加工技术、压机制造水平及合成树脂工艺性能的不断改进和提高,压机吨位和台面尺寸不断增大,模压料的成型温度和压力也相对降低,使得模压成型制品的尺寸逐步向大型化发展,目前已能生产的大型汽车部件如模压重卡高顶、MPV车顶、皮卡车厢、重卡驾驶室侧围板等。图15所示即为模压成型工艺生产的2001福特Explorer Sport Trac SMC皮卡车厢。
图15 SMC模压成型工艺生产的皮卡车厢
LFT-D成型工艺技术
LFT-D成型工艺(Long-Fiber Reinforce Thermoplastic Direct)是继GMT和LFT-G之后又一种新的长纤维增强热塑性复合材料工艺技术,是长纤维增强热塑性复合材料在线直接生产制品的一种工艺技术,它区别于GMT和LFT-G的关键因素是半成品步骤被省去了,而在材料的选择上更加灵活,是近年来在汽车复合材料行业中最受关注和市场成长最快的一种崭新的成型工艺技术。在LFT-D技术中,不仅纤维的含量和纤维的长度可以直接调节到最终部件的要求,其基体聚合物也可以直接调节到最终部件的要求。通过使用不同的添加剂可以改变和影响制品的机械和特殊应用特性,如热稳定性、着色性、紫外稳定性和纤维与基体的粘结特性等,这也意味着每一种特殊应用都可以通过LFT-D获得其独特的材料配方。
LFT-D的典型工艺流程是,将聚合物基体颗粒(主要是PP)和添加剂输送到重力混合计量单元中,根据部件的机械性能要求进行材料的混配。经混配好的原料再被送入双螺杆挤出机中进行塑化,熔融的混合物通过一个薄膜模头形成类似瀑布的聚合物薄膜,该聚合物薄膜直接被送入到双螺杆混炼挤塑机的开口处。此时,玻璃纤维粗纱通过特别设计的粗纱架,在经过预热、分散等程序后被引入到聚合物薄膜的顶端与薄膜汇合一同进入到双螺杆挤塑机中,由螺杆切割粗纱,并把它们柔和地混合到预熔的聚合物当中,然后直接送入压制模具中成型或者推压进注射模具成型,如图16所示。
图16 LFT-D成型工艺示意图
LFT-D成型工艺的优点主要有两个:一是成本低。由于是直接一步法生产,因此由LFT-D生产的大型结构部件比两步法生产的GMT或LFT-G压制部件的成本低20%~50%;二是制品的综合性能优异。LFT-D压制成型制品的抗冲击性能比GMT稍低一些,但由于比LFT-G成型后的纤维长很多,因此其抗冲击性能明显比LFT-G高得多。另外,大量的研究表明,LFT-D注塑的生产效率比采用标准LFT-G粒料的生产效率高,因为LFT-D低的塑化要求改善了纤维被剪断的可能性。对于成型周期超过1min的部件,用LFT-D注塑设备在30s内就能完成。LFT-D成型工艺的缺点主要是制品厂需要加大对LFT-D成型工艺以及材料、配方等的研究投入。图17所示为采用 LFT-D生产的2003 大众 Golf V前端框架。
图17 用LFT-D成型工艺生产的前端框架
免责声明:本网站所转载的文字、图片与视频资料版权归原创作者所有,如果涉及侵权,请第一时间联系本网删除。
相关文章
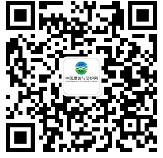
官方微信
《中国腐蚀与防护网电子期刊》征订启事
- 投稿联系:编辑部
- 电话:010-62316606-806
- 邮箱:fsfhzy666@163.com
- 中国腐蚀与防护网官方QQ群:140808414
点击排行
PPT新闻
“海洋金属”——钛合金在舰船的
点击数:7685
腐蚀与“海上丝绸之路”
点击数:6157