1.1 疲劳的定义
疲劳(fatigue)这个词起源于拉丁文的 fatigäre一词,意思是“疲倦”。人疲劳——身心劳累;材料疲劳——在循环载荷下的损伤和破坏。
定义:材料在应力或应变的反复作用下所发生的性能变化。
1.2 疲劳研究发展过程
材料疲劳的研究可追溯到19世纪上半叶。W.A.J.Albert——德国矿业工程师,金属疲劳的最初研究者,1829年前后完成。
研究内容:用铁制的矿山升降机链条作反复加载试验,验证其可靠性。第一个金属疲劳研究——1842年法国玩尔赛铁路事故分析,机车前轴的断裂是导致这次事故的原因。
1.3 疲劳载荷
规则的交变应力
不规则的交变应力
一点应力随时间变化曲线
应力循环
应力比
平均应力
应力幅值
对称循环:r=-1 脉冲循环:r=0
静应力:r=1
1.4 疲劳极限与应力-寿命曲线
S-N曲线
一般的应力-寿命曲线
对称循环下两种类型S-N曲线
平均应力对S-N曲线的影响
1.5 影响疲劳寿命的因数
应力集中的影响——有效应力集中因数
理论应力集中因数
Sn为名义应力
表面加工质量的影响——表面质量因数
磨削加工(试样)
其他加工
2.1 疲劳失效分析经典案例
疲劳失效典型案例——20世纪50年代世界第一架民用喷气式客机“彗星号”系列事故。
原因:客舱结构疲劳开裂。
2.2 疲劳断裂失效的特点
疲劳断裂属于脆性断裂的一种,几乎没有肉眼可见的塑性变形。疲劳断裂往往具有突发性,危害性大。在机电装备的失效事件中,疲劳断裂失效约占所有断裂事故的60%~80%。
2.3 疲劳断裂失效分析的目的
诊断出疲劳失效的模式;
找出引起疲劳断裂的确切原因;
采取预防措施,避免同类疲劳断裂失效再次发生。
2.4 疲劳断裂失效分析的内容
分析判断零件的断裂失效是否属于疲劳断裂;
疲劳断裂的二级或三级失效模式;
疲劳断裂的载荷类型与大小,疲劳断裂的起源等;
疲劳断裂的原因;
疲劳断裂的机理;
提出避免疲劳断裂再次发生的预防措施。
2.5 疲劳断裂失效的分类
高周疲劳断裂:又称应力疲劳断裂,是指零件在较低的交变应力作用下产生的疲劳断裂。一般将循环周次在104以上的疲劳断裂,称为高周疲劳断裂。
低周疲劳断裂:又称应变疲劳断裂,是指零件在较高的交变应力作用下产生的疲劳现象。一般将循环周次在104以下的疲劳断裂,称为低周疲劳断裂。
疲劳失效的“二级”失效模式分类
根据频率不同:高频疲劳断裂、低频疲劳断裂。
根据循环周次不同:高周疲劳断裂、低周疲劳断裂。
根据控制参量不同:应力疲劳断裂(控制应力幅)、应变疲劳断裂(控制应变幅)。
根据环境介质不同:腐蚀疲劳断裂、应力腐蚀疲劳断裂。
根据温度不同:低温疲劳断裂、室温疲劳断裂、高温疲劳断裂。
2.6 疲劳断裂失效过程
(1)亚结构和显微结构发生变化,永久损伤形核;
(2)产生微观裂纹;
(3)微观裂纹长大和合并,形成“主导”裂纹;
(4)主导宏观裂纹稳定扩展;(5)结构失去稳定性或完全断裂失效。
2.7 疲劳断裂影响因素
力学因素;
材料组织结构因素;
环境因素;
影响微观裂纹的形核和主导疲劳裂纹的扩展速率和路径。
2.8 疲劳断裂失效的特征
名义应力低于静荷载强度;
构件破坏过程;
疲劳破坏断口。
2.9 疲劳断口的宏观分析
典型的疲劳断口按照断裂过程的先后可分为三个特征区,即疲劳源区、疲劳扩展区和瞬断区 。
疲劳源区的宏观特征
①疲劳源区一般位于零件表面或亚表面的应力集中处,也可能在表面或内部的缺陷、损伤处。当疲劳源区位于零件内部时,源区一定存在有缺陷或较大的内应力、残余应力。
②疲劳源区的形成时期早,暴露于环境中的时间长,一般均有一定的氧化或腐蚀,疲劳源区相对于断口上的其它区域,其氧化或腐蚀较重,颜色较深。
③疲劳源区的断面一般平坦、光滑、细腻,有些断口可见到闪光的小刻面。
④疲劳源区往往有向外辐射的放射状疲劳台阶和放射状条纹。
⑤疲劳源区看不到疲劳弧线,但像向外发射疲劳弧线的中心。
从断口上氧化颜色最深的区域、最平坦、光滑的区域、应力集中的表面或缺陷处找到疲劳源区,它是放射棱线的汇聚点,疲劳弧线的发散中心。
疲劳源区有时只有一个,但有时也可能有多个;有时呈点状,有时还呈线状。
疲劳扩展区的宏观特征
疲劳扩展区断面一般较平坦,与主应力相垂直;颜色介于源区与瞬断区之间;最基本的宏观形貌特征是疲劳弧线。
疲劳瞬断区的宏观特征
宏观特征与静载拉伸断口相近,即由纤维区、放射区和剪切唇区三部分组成。
瞬断区面积的大小取决于载荷的大小、材料的性质、环境介质等因素。通常瞬断区面积越大,表示载荷越大;反之,瞬断区的面积越小,表示所受载荷越小。当疲劳裂纹扩展到应力处于平面应变状态以及由平面应变过渡到平面应力状态时,其断口宏观形貌呈现人字纹或放射条纹,当裂纹扩展到使应力处于平面应力状态时,断口呈现剪切唇状态。
疲劳断口的宏观分析
断口宏观形貌受载荷类型、应力水平和缺口严重程度的影响很大。
对真实零件的疲劳失效断口,根据其宏观形貌特征可定性地推断出导致零件失效的载荷类型与大小、应力集中的程度;对旋转弯曲失效,还可推断出零件失效前的转动方向等与失效相关的信息。
疲劳断口的微观分析
(1)疲劳源区的微观分析
确定疲劳源区的具体位置;判明主源、次源。
分析源区的微观形貌特征,包括萌生处有无材质缺陷、腐蚀损伤及腐蚀产物、外物损伤痕迹、加工刀痕、磨损痕迹等。
(2)疲劳扩展区的微观分析
对第二阶段的微观分析主要是观察有无疲劳条带,疲劳条带的性质,疲劳条带间距变化的规律等。这些特征对于分析疲劳断裂机制、裂纹扩展速率、载荷的性质等具有重要作用。
疲劳条带的主要特征
疲劳条带在形貌上一般具有如下主要特征:
(1)疲劳条带是一系列基本上相互平行的、略带弯曲的波浪形条纹,并与裂纹局部扩展的方向垂直;
(2)疲劳条带间距随应力强度因子幅的变化而变化,一般离源区越远,条带的间距越大;
(3)一般源区附近条带特征不如扩展中后期的明显;
(4)匹配断口两侧的疲劳条带特征基本对应;
(5)局部区域的条带扩展方向与裂纹的宏观扩展方向可以相同,也可以不同,甚至可能出现相反的情况;
(6)疲劳断口通常由许多大小不等、高低不同的小断快所组成,各断块上的条带不连续,且不平行;
(7)每一条带代表一次应力循环;
(8)条带是裂纹尖端的位置。一般韧性材料容易形成疲劳条带,而脆性材料则比较困难;
(9)瞬断区微观分析主要是观察韧窝的形态是等轴韧窝、撕裂韧窝还是剪切韧窝,这有助于判断引起疲劳断裂的载荷类型。同时,从瞬断区的微观特征还可对材料的韧性进行定性的判断,为分析失效的原因提供参考。
疲劳断裂失效分析思路
首先应该在对失效件的工作情况(工况)、宏观和微观断口特征分析的基础上,初步确定其属于疲劳断裂。
然后进一步分析判断其属于哪种类型的疲劳失效,即进行疲劳失效的二级模式、三级模式诊断。
最后根据具体的疲劳失效类型,从设计、制造、材质和使用、维护等方面查找失效的原因,分析失效的机理,提出相应的预防措施。
疲劳断裂失效分析思路
(1)参数(工况)判据
力学参数应该具有交替变化的特点,且交变的应力大小应该大于材料的疲劳极限。分析一个零件的失效模式是否为疲劳断裂,首先应确定其工作条件下是否可能承受有交变应力的作用。
(2)宏观变形判据
疲劳断裂属于脆性断裂的一种,在断裂位置的疲劳源区和疲劳扩展区附近没有明显宏观塑性变形。
(3)断口宏观形貌特征判据
断口齐平,存在疲劳弧线。一般的疲劳断口均与主应力轴垂直,断面齐平、细腻,附近没有明显的塑性变形;断口上有疲劳弧线和从疲劳源区向外发散的放射状棱线,有的源区还有疲劳台阶。
(4)断口微观形貌特征判据
疲劳条痕:疲劳条带、二次裂纹带、韧窝带、轮胎花样等。
疲劳条带
轮胎花样
韧窝带
二次裂纹带
(5)断口颜色判据
疲劳区和扩展区在氧化程度上一般都略有差异。两者的光亮程度也有明显差异。
疲劳断裂模式判据
疲劳二级失效模式诊断
(1)高周疲劳与低周疲劳
宏观特征
a.断口粗糙程度:与高周疲劳断口相比,低周疲劳的整个断口相对粗糙,高低不平;且随着断裂循环次数的降低,断口形貌愈来愈接近静拉伸断裂断口。而高周疲劳断口平整、光滑,宏观即可见明显的疲劳区。
b.疲劳源区:低周疲劳具有多个疲劳源点,有时还呈线状;源区间的放射状棱线(疲劳一次台阶)多而且台阶的高度差大。而高周疲劳一般只有一个疲劳源点,源区结构细腻,没有疲劳台阶。
c.瞬断区面积:低周疲劳的瞬断区面积所占比例大,甚至远大于疲劳裂纹稳定扩展区面积。而高周疲劳的应力相对较低,瞬断区所占面积相对较小。
d.疲劳弧线:低周疲劳的弧线间距逐渐加大,但循环次数低到一定程度时,基本见不到疲劳弧线特征;稳定扩展区的棱线(疲劳二次台阶)粗而短。高周疲劳的弧线特征与具体的工况条件有关,无统一的规律。
微观特征
低周疲劳断裂由于宏观塑性变形较大,在疲劳断裂过程中会出现静载断裂机理,在断口上出现各种静载断裂所产生的断口形态。在一般情况下,当疲劳寿命小于90次时,断口上为细小的韧窝,没有疲劳条带出现;当疲劳寿命大于300次时,出现轮胎花样;当疲劳寿命大于10000次时,才出现疲劳条带,此时的条带间距较宽,可达2~3微米/周。如果使用温度超过等强温度,还会出现沿晶断裂。
高周疲劳断口的微观疲劳特征是细密的疲劳条带,一般间距可达1微米以下。对应力为拉-压模式的疲劳断裂,在疲劳源区及其附近,由于两断裂面之间的反复碰磨,其断裂形貌特征经常被磨损而无法看到疲劳条带特征。
(2)腐蚀疲劳断裂
腐蚀疲劳断裂是在腐蚀环境与交变载荷协同、交互作用下发生的一种失效模式。
在机械装备中,因腐蚀疲劳而导致早期断裂失效的事例屡见不鲜。例如:起落架、机翼大梁、刹车轮毂、涡轮盘、叶片等关键部件,均曾发生过腐蚀疲劳断裂失效,有的还酿成过灾难性事故。
腐蚀疲劳对环境介质没有特定的限制。
影响腐蚀疲劳断裂过程的相关因素主要有:
a.环境因素:包括环境介质的成分、浓度、介质的酸度(pH值)、介质中的含氧量、介质的电极电位以及环境温度等;
b.力学因素:包括加载方式、平均应力、应力比、载荷波形、频率以及应力循环周次;
c.材质冶金因素:包括材料的成分、强度、热处理状态、组织结构、冶金缺陷、夹杂物等。
腐蚀疲劳断口特征:
具有疲劳断裂的一般特征,断口上有源区、扩展区和瞬断区三个特征区。腐蚀疲劳断口独特的特征:
a.断口低倍形貌呈现出明显的疲劳弧线;
b.源区与扩展区一般均有腐蚀产物覆盖,通过微区成分分析,可以测定出腐蚀介质的组分及相对含量。
腐蚀疲劳断口微观形貌
断口上覆盖的腐蚀产物
c.腐蚀疲劳断裂一般均起源于表面腐蚀损伤处(包括点腐蚀、晶间腐蚀、应力腐蚀等),大多数腐蚀疲劳断裂的源区可见到腐蚀损伤特征;
d.腐蚀疲劳断裂扩展区有某些较明显腐蚀特征,如腐蚀坑、泥纹花样等;
e.腐蚀疲劳断裂的重要微观特征是穿晶解理脆性疲劳条带;
f.在腐蚀疲劳断裂过程中,当腐蚀损伤占主导地位时,腐蚀疲劳断口呈现穿晶与沿晶混合型;
g.当Kmax>K1scc,在频率很低的情况下,腐蚀疲劳断口呈现出穿晶解理与韧窝混合特征。
腐蚀疲劳断裂失效的主要判据:
a.工况判据:构件是在交变应力和腐蚀条件下工作,交变应力的频率和应力比一般处在腐蚀疲劳区内,在液态、气态和潮湿空气中有腐蚀性元素;
b.颜色判据:断裂表面颜色灰暗,无金属光泽,通常可见到较明显的疲劳弧线;
c.腐蚀产物判据:断裂表面上或多或少存在有腐蚀产物和腐蚀损伤痕迹;
d.形貌判据:疲劳条带多呈解理脆性特征,断裂路径一般为穿晶,有时出现穿晶与沿晶混合型甚至沿晶型。
腐蚀产物是分析、判断失效零件工作环境和工作时间的重要依据。可以采用能谱仪、电子探针以及其它化学分析方法确定腐蚀产物的化学元素及量的分布规律。
(3)微动疲劳失效
一构件与其它构件接触面间发生微动磨损的条件下受交变载荷作用而发生的疲劳损伤过程称为微动疲劳。它是微动磨损、氧化及腐蚀、交变应力综合作用的结果。微动磨损是微动疲劳产生的根本原因。
微动疲劳也有裂纹的萌生和扩展过程,微动疲劳裂纹一般萌生于微动磨损造成的表面损伤的边界处,如皿状浅坑的边缘或微动磨损深坑的边缘。微动磨损的初期可出现多个疲劳裂纹,在扩展过程中,这些微裂纹可合并为一主裂纹并垂直于外加交变正应力而进一步扩展。
影响微动疲劳寿命的主要因素:
配合表面之间的法向夹紧压应力、相对运动幅度、摩擦力、内应力、周围介质、相匹配面的材料等。
微动疲劳断口特征:
微动疲劳断口特征与纯机械疲劳断口相同,包括疲劳源区、疲劳扩展区和瞬断区;微观上有典型的疲劳条带。
裂纹源区和扩展区的前期,往往可以看到腐蚀产物。
微动疲劳失效的最明显特征是在断口的侧表面,即微动磨损面上有大量的微裂纹、表面金属掉块、不均匀磨损擦伤,色泽发生明显改变且有腐蚀坑。微动产生的微裂纹大多集中于微动区的边缘,大多与表面呈45度角,断口常呈杯锥状。
微动损伤表面还常常可以看到层状及山丘状的塑性变形,同时还可看到由于辗压形成的微裂纹。
疲劳失效原因分析
导致零件疲劳失效的原因主要有四个方面:设计(包括应力集中、循环载荷水平、尺寸,选材等)、制造工艺(包括表面完整性、装配等)、材质(包括化学成分、组织结构、力学性能等)、使用维护(包括超载、外来损伤、腐蚀等)。
在查找疲劳失效的原因时,应围绕这四个方面来寻找证据、进行分析。
(1)设计原因分析
设计原因是失效原因中最难分析的原因,需要通过较精确的分析才能定量,而目前的分析水平还主要停留在定性程度,难以对应力进行定量分析;
其次,疲劳一般都是从最薄弱的部位起始,疲劳源区往往存在一定程度的材质缺陷,对准确分析出失效原因具有干扰作用。
要查找设计方面的问题,首先应确定载荷的类型与大小。
a.反复弯曲载荷引起的疲劳断裂:弯曲疲劳可分为单向弯曲疲劳、双向弯曲疲劳、旋转弯曲疲劳等。构件承受弯曲载荷时,表面承受的应力最大,中心承受的应力最小。所以疲劳核心总是在表面形成,然后沿着最大正应力相垂直的方向扩展。当裂纹达到临界尺寸时,构件迅速断裂,因此,弯曲疲劳断口一般与其轴线成90度。
b.拉-拉(压)载荷引起的疲劳断裂:承受拉-拉(压)交变载荷时,应力沿整个零件的横截面均匀分布,疲劳源位置取决于各种缺陷在零件中的分布状态及环境因素的影响,既可以在零件的外表面,也可以在零件的内部。
c. 扭转载荷引起的疲劳断裂:轴类零件在工作过程中经常会承受交变扭转应力的作用,从而可能产生一种特殊的扭转疲劳断口——锯齿状断口。
其次,要判断载荷的来源是否正常,大小是否超出设计范围。
对转动部件,振动是无法避免的,但工作转速下的共振是设计时必须避免的。如果从断口判断出该零件承受了设计应该避免的振动载荷,说明设计不当是失效的主要原因,需从设计方面进行详细的分析。
对重复性的故障,如排除了制造上的批次问题,一般与设计不当有关。
常见的导致失效的设计原因有:
① 设计载荷不准确。主要表现为载荷考虑不全(应力估算不足),载荷变动分析不够,计算假定中出现误差,致使实际工作载荷超过设计载荷,材料在正常工况下也无法承受工作载荷而失效。
② 设计结构不合理。主要表现为零件几何形状设计不当,出现剖面突变或尖角面,导致这些部位承受较大的应力集中,超过材料的强度极限,从而过早地萌生裂纹而失效。如过渡部位没有圆角R或R角太小,主要受力部位存在缺口效应等,使得零件的应力集中大,局部应力水平高,疲劳裂纹提前萌生。
③设计选材不当。主要表现为选用材料的性能不能满足使用要求。在实际失效分析中,设计选材不当导致断裂失效,经常遇到的是所选材料的主要抗力指标与实际损伤模式不符合,致使材料的性能指标在该强的方面不强,不能满足使用的需求。
(2)材质原因分析
失效的材质原因直接表现为与零件失效模式对应的材料力学性能不符合设计要求,如与疲劳断裂失效对应的材料疲劳强度低,与拉伸过载断裂对应的材料抗拉强度低等。
常见的与疲劳失效有关的材质原因有:材料的化学成分不合格,热处理制度或工艺不当,金相组织不符合要求,存在冶金缺陷。
(3)制造工艺原因分析
常见的影响零件疲劳强度的制造工艺缺陷有:
①铸造工艺过程中产生的气孔、梳松和缩孔、裂纹、夹渣、飞边、流痕、比重偏析、共晶偏析等。
②锻造工艺过程中产生的裂纹、折叠、结疤、层状断口、非金属夹杂、铝合金氧化膜、白点、粗晶环、过热、过烧、脱碳、增碳、加热不足引起心部开裂、晶粒不均匀、冷硬现象等。
③切削加工过程中产生的尺寸超差、表面粗糙度差、毛刺、划伤、啃刀、表面烧伤、裂纹、刀痕等。
④冷加工工艺过程中产生的划痕、锈蚀、球化退火不足、带状组织、晶粒粗大或粗细不均、性能不合格、冲模错位,裂纹、压痕、端面鼓起或不平、存在挠度、曲度等。
⑤热处理工艺过程中产生的过热、过烧、氧化、脱碳、机械性能不合格、软点、变形与裂纹、硬度过高、过共析钢网状碳化物、石墨化、压共析钢魏氏组织、铁素体晶粒粗大、硬度不足、淬火不完全、表面脱碳、表面腐蚀、回火脆性等。
⑥表面处理工艺过程中产生的镀层结合力差、起泡、发脆、脱落、发暗、麻点表面,渗层硬度不足、表面网状或粗大块状、爪状碳化物、氮化物、渗层过深、不足或不均匀、表面网状屈氏体组织、黑色斑点状组织、心部硬度超差、零件变形与开裂、渗层脆性和剥落等。
⑦焊接装配工艺过程中产生的焊缝尺寸偏差、咬边、焊瘤、弧坑、烧穿、焊漏、气孔夹渣、未焊透、裂纹,焊点及焊缝位置不正、形状不正、压痕过深、过热、烧伤、裂纹、未焊透或核心小、缩孔、内部飞溅、熔透过大、接头变脆、接头不气密,间隙未填满、气孔、钎缝表面粗糙、夹杂物、裂纹、钎料侵蚀金属表面等。
⑧装配:强行装配、装配应力大等。
(4)使用维护原因分析
导致断裂失效的使用维护原因一般表现为超过设计限制使用、维护不当造成损伤和环境侵蚀。
①超设计限制使用原因:按应力-强度干涉模型,失效是零件所受外力超过材料相应强度的结果。使用限制是根据材料的强度、一定的安全储备及零件工况可导致的应力制定的。如果超过设计限制使用,必将使零件所承受的应力升高,就有可能使零件承受的应力超过材料的强度而使零件失效。
②使用维护原因:使用维护的目的是保证零件能够正常工作,防止发生意外损伤。由于维护一般需要对零件进行拆装,就有可能在重新装配时,其状态与制造状态不一致,并带来额外的损伤、附加的应力等,从而导致零件的失效。
由于使用中维护不当导致的疲劳失效,一般在失效件上或失效系统中均可找到一定的证据。如发动机叶片被打伤,疲劳裂纹从打伤处萌生,并最终导致叶片疲劳断裂失效,在疲劳源区就可以找到伤痕。
③环境侵蚀原因:机械失效中的环境原因主要有两方面,一是腐蚀介质作用,二是温度效应。
腐蚀介质可使材料与环境之间发生有害的化学或电化学作用,引起表面腐蚀损伤,疲劳裂纹从腐蚀处萌生,导致疲劳断裂失效;腐蚀也可与应力同时作用,导致腐蚀疲劳失效。
环境温度的作用主要是降低材料的疲劳强度,导致零件的提前疲劳失效。
疲劳断口定量分析
疲劳断口定量分析:主要是指对疲劳断口上的疲劳断裂形态,包括疲劳源点、疲劳弧线、疲劳台阶、疲劳条带等的位置、数量、间距及疲劳源数量、扩展区、瞬断区面积的大小等进行量化、测量与计算,并据此来反推引起疲劳断裂的相关因素及断裂过程的顺序、应力大小、疲劳扩展与萌生寿命等。
理论依据
宏观上的每一条疲劳弧线相当于裂纹扩展过程中载荷或应变发生一次大的改变;微观上的每一疲劳条带则相当于载荷或应变的一次循环;准确地确定何种疲劳条带与何种载荷之间具有对应关系是断口定量分析的关键所在;疲劳断口的形貌特征及扩展区、瞬断区的大小与疲劳应力幅之间具有定量关系。
Paris公式,适用于高循环低应力的高周疲劳,是目前高周疲劳断口寿命反推估算的基础。目前,研究中用得最多的仍是Paris公式。目前最重要和最有价值的是利用疲劳断口参数估算寿命。利用疲劳断口弧线、条带间距反推疲劳寿命已成功地应用于以下几个方面: ① 低周疲劳寿命估算;② 恒载与谱载下的疲劳寿命估算;③ 起源于先天性“裂纹”或缺陷的高周疲劳寿命估算。
疲劳断口特征与载荷历程对应关系的确定:疲劳断裂是一个过程,构件在疲劳交变载荷作用下,将萌生疲劳裂纹,并扩展。一般交变载荷循环一次,裂纹将向前扩展相应的量,并停顿;如此往复,裂纹将反复扩展、停顿,在断口上留下相应的一系列痕迹。我们最常见的疲劳弧线、条带就是这种特征痕迹。它们的一些量的东西,如数量、间距、方向等就反应了应力水平、循环数量、寿命、裂纹的扩展速率等。
工作载荷与断口特征的对应关系:
1)颜色、成分与工作历程、时间的对应关系断口暴露的时间越长,颜色上的差异越大。
在化学处理过程的前后,断口上颜色出现突变。裂纹不同长度部位暴露的时间不同,其表面的化学成分也会表现出明显的差异。从断口颜色、成分的差异来判断裂纹萌生的时间应该与使用历程、使用条件联系起来。
2)宏观上的对应关系
扩展区与瞬断区交界线对应构件瞬时断裂时的寿命点。每一条宏观疲劳弧线对应裂纹扩展中载荷或应变的一次大的改变(如载荷谱的加载、环境条件等的改变)。对载荷谱试验,分析对比载荷谱特点及断口特征,也可确定相应的对应关系。测量疲劳弧线的数量、间距就可以确定载荷的变化次数和大小。
3)微观上的对应关系
疲劳断口的微观特征主要是疲劳条带。
理论依据:每一疲劳条带相当于载荷或应变的一次循环。
从微观上反推疲劳裂纹扩展寿命可利用的主要数据是疲劳条带间距。
疲劳弧线或疲劳条带间距的测定方法:
一般采用实体光学显微镜、扫描电子显微镜或透射电子显微镜,沿着主裂纹扩展的方向,在一定放大倍数下测量。
疲劳条带间距存在一定的分散性,测量时应取一定范围内的平均值作为某一点的间距。
用扫描电镜测量条带间距时,应进行相应的角度修正和投影修正。透射电子显微镜测出的条带间距一般与真实疲劳条带的平均间距较为接近,一般不需修正。
断口反推疲劳裂纹扩展速率的基本方法:若令每一载荷循环下的疲劳裂纹扩展量为u,则u=da/dN或dN=da/u;式中:a-裂纹长度;N-循环次数。
在断口上测得若干离源区不同距离的裂纹ai处的疲劳弧线、条带间距间距,作出每一载荷循环下的裂纹扩展量与裂纹长度相互关系的曲线,就可求得疲劳裂纹扩展寿命Np。
利用断口反推计算疲劳裂纹扩展寿命的关键是得出疲劳裂纹扩展速率da/dN的数学表达式。当构件承受一稳定的交变载荷时:
da/dN=c(△K)m
da/dN=0 ( △K < △Kth )
对于随机载荷目前尚未有描述裂纹扩展速率的数学表达式,应该根据实际情况分析随机载荷的一般规律,进而建立相应的裂纹扩展速率的数学模型。
断口反推疲劳寿命中,应按如下步骤进行。① 断口分析② 载荷、历程分析③ 确定载荷与断口特征的关系④ 数据获取⑤ 对数据的拟合、估算
小结:利用疲劳断口形貌反推失效件裂纹扩展寿命,首先应通过对失效件断口和履历、载荷分析,确定断口形貌与载荷谱间的对应关系,并从断口上实测出不同裂纹长度处对应的裂纹扩展速率da/dN;然后根据测得的一组数据绘制裂纹长度与谱循环数(或与循环次数)的关系曲线,即疲劳裂纹扩展曲线;最后,对实测曲线拟合,将其反推至整个裂纹扩展区,并以此求得整个断口的裂纹扩展速率、扩展寿命。
在反推过程中应以分析确定的特征寿命点来验证计算结果,以提高反推的准确性。
断口反推疲劳原始质量
按照损伤容限理论,结构件在服役前均带有初始裂纹或缺陷,由该裂纹或缺陷扩展达到临界裂纹的寿命即为结构的总寿命;这些存在于零件中的初始缺陷对疲劳寿命的影响可等效为一当量裂纹长度,称为当量初始裂纹a0,可作为表征零件质量的参量(当量初始质量),对疲劳断裂失效,则称为原始疲劳质量a0i。
利用断口形貌反推零件当量初始质量的原理、方法和步骤:
① 断口分析,确定断口形貌与载荷谱之间的对应关系,从断口上实测出对应于每次载荷循环数的裂纹长度。
② 根据测得的数据绘制疲劳裂纹扩展曲线。
③ 拟合实测曲线,并将与其相吻合的裂纹扩展规律反推至时间为零,即N=0,此时对应的裂纹长度即为该零件的a0i。
④ 对同类零件的a0i进行统计分析,根据a0i的分布密度确定规定概率下同类零件的a0i。
需要说明的是,a0i仅是损伤容限设计中使用的一个参考值,是零件在服役前的内部各种缺陷、表面加工缺陷及表面非完整性因素等对疲劳寿命影响的一个综合反映参考量。
疲劳断口反推失效构件的应力
(1)从裂纹长度及瞬断区大小反推构件疲劳应力水平
构件疲劳裂纹临界长度ac与最大交变应力σmax关系:KⅠ=σmax Y(πa)1/2
当发生快速断裂时,KⅠ=KⅠc,a=a c,σ=σc,则有KⅠc=σc Y(πa)1/2
由试验测得一系列ac-σc数据,拟合求得关系式,将失效件的值代入即可估算出失效件所承受的疲劳应力水平。
疲劳瞬断区是疲劳裂纹达到临界尺寸后发生的快速破断区,其面积大小一般认为受材料的断裂韧性 KⅠc控制。因为ac与瞬断区面积是相关的,因此通过试验测得一系列的A-σc数据,拟合求得关系式,将失效件的值代入也可估算出失效件所承受的疲劳应力水平。
必须注意的是,以上方法只能求得疲劳载荷的最大应力水平,但不能推算疲劳载荷的范围。
(2)利用疲劳条带间距反推失效件的疲劳应力
疲劳裂纹扩展的第二阶段的速率可用Paris公式表达:da/dN = c( Y△σπ0.5 )m×am/2;由断口反推求得疲劳裂纹扩展速率(da/dN)sx~a ,用试样模拟同材料疲劳裂纹扩展速率(da/dN)sy ~△K ,求得材料常数c、m,在裂纹稳定扩展阶段,则有:
若已知Ysx的表达式或数值解,则可求得△σsx。
对一些形状及受力均复杂的大型构件, Ysx难以用表达式来表达,则可用与失效件等同的模拟试验件进行疲劳试验,求得(da/dN)sy ~ a,则有:
若知道实际构件所承受的应力比R=σmin/σmax,则可求得:σmax=△σmax / (1-R) 。
广义地讲,失效是零件(材料)不能抵抗外来载荷作用的结果,即抗力小于外力的结果。疲劳断裂失效是零件(材料)的疲劳强度小于交变载荷的结果。
预防疲劳断裂失效只能从两方面入手,一方面要提高零件(材料)的疲劳强度,另一方面要降低交变载荷。具体来说,应从设计、材质、制造工艺和使用等四个环节来采取措施。
疲劳设计
从设计上预防疲劳断裂失效的主要方法就是要尽量降低设计载荷,避免产生异常应力。从零件的各种结构因素来看,结构布局引起的应力集中对局部疲劳载荷的影响最大。
危险截面的应力集中往往可导致零件的提前疲劳失效。通过合理的布局来降低或改善上述部位的应力集中。
通过合理的结构设计,可以使零件上某些部位的应力集中得到缓和,零件的疲劳抗力得以提高。
零件选材
机械零件的功能都是靠材料来保证的,零件的失效归根到底都是材料的失效。
设计中,应根据零件承受的循环载荷方式、载荷水平、工作环境以及服役寿命等来选择适宜的材料。
选择的材料应在服役条件下具有较好的性能。
制造工艺
制造工艺是决定零件是否发生疲劳失效的关键环节。制造工艺改变是预防疲劳失效最易实现、最经济、途径最多的一个环节。任何改善表面完整性的工艺,一般都可以提高零件的疲劳强度。
(1)提高表面光洁度
(2)表面淬火
(3)表面化学热处理
(4)表面形变强化
使用维护
尽量降低作用于零件上的载荷;尽量保持零件表面的完整性,不降低零件本身的疲劳抗力。
(1)控制使用载荷,降低零件承受的应力水平和应力循环数
(2)保持表面的完整性,防止意外损伤
(3)改善使用环境,尽量减少环境的侵蚀
免责声明:本网站所转载的文字、图片与视频资料版权归原创作者所有,如果涉及侵权,请第一时间联系本网删除。
相关文章
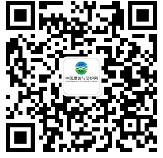
官方微信
《腐蚀与防护网电子期刊》征订启事
- 投稿联系:编辑部
- 电话:010-62316606-806
- 邮箱:fsfhzy666@163.com
- 腐蚀与防护网官方QQ群:140808414
点击排行
PPT新闻
“海洋金属”——钛合金在舰船的
点击数:8148
腐蚀与“海上丝绸之路”
点击数:6486