【摘要】对电站汽轮机叶片的工况与选材进行了简要介绍, 论述了叶片各种疲劳失效方式及原因,从叶片设计与材质、加工与安装、运行与维护等角度, 给出了预防疲劳失效的措施。
关键词:汽轮机叶片 疲劳失效 预防措施
0 前言
由于汽轮机叶片疲劳断裂而引起的电站事故比较常见,约占整个火力电厂运行事故的三分之一。每台汽轮机都拥有许多叶片, 只要一只叶片断裂就可能导致整个机组的严重事故,造成重大经济损失,甚至是人员伤亡。因此, 分析叶片的疲劳断裂原因,制订防止疲劳断裂的措施,从而延长叶片使用寿命,对确保整个电站机组安全性运行具有重要的意义。
1 叶片工况与选材
叶片工况与其选材是密切相关的, 通常是根据叶片的实际工况条件及环境状态, 来选择合适的叶片材料。
1.1 叶片工况条件
电站汽轮机叶片,特别是大型汽轮机动叶片, 所处的工况条件及环境极为恶劣, 主要表现在应力状态、工作温度、环境介质等方而。
汽轮机在工作过程中, 动叶片承受着最大的静应力及交变应力, 静应力主要是转子旋转时作用在叶片上的离心力所引起的拉应力, 叶片愈长、转子的直径及转速愈大,其拉应力愈大。此外, 由于蒸汽流的压力作用还产生弯曲应力和扭力, 叶片受激振力的作用会产生强迫振动; 当强迫振动的频率与叶片自振频率相同时即引起共振,振幅进一步加大, 交变应力急剧增加,最终导至疲劳断裂。汽轮机的每一级叶片工作温度都不相同, 第一级叶片所处的温度最高, 大约在535 ℃ 左右; 随后由于蒸汽逐级作功,温度逐级降低,直到末级叶片将降到100℃ 以下。
叶片在水蒸汽介质中工作, 其中多数是在过热蒸汽中工作的,末级叶片是在潮湿蒸汽中工作;过热蒸汽中含有氧,会造成高温氧化腐蚀,生成腐蚀性盐而影响叶片的疲劳强度;湿蒸汽区, 可溶性盐垢(如钠盐)吸收水珠成为电解液, 造成电化学腐蚀。此外,湿区的游离水分子由于过冷凝结成水滴, 冲击动叶进汽侧背弧面, 造成水冲蚀。
1.2 叶片选材
为确保汽轮机长期安全运行, 叶片材料必须具有良好的抗疲劳和减振性能、足够的室温和高温机械性能、高的组织稳定性、良好的耐蚀性及抗冲蚀稳定性等; 常用汽轮机叶片材料有铬不锈钢、强化型铬不锈钢、铝合金及钦合金等。
由于大功率汽轮机发展, 后几级叶片的尺寸愈来愈大,所产生的离心力很大,按目前不锈钢的强度特性,对于转速为3000r/min的叶片, 最大长度不能超过1100mm~1300mm, 比这更长的叶片需采用高强度、低比重的材料。铝合金及钦合金比重小、耐蚀性高,有一定的强度,在国外已经用于制造大功率汽轮机长叶片。钦合金是以钦为基础, 加人适量铝、错、锡、钒、钥等, 它的比重仅是钢的40% , 可有效降低叶片根部的应力。铁合金的室温机械性能很高,且具有良好的抗蚀性能, 但是铁合金的工艺性能较差,对应力集中比较敏感, 减振性比马氏体钢低且成本较高。目前, 国外还在研究采用碳化物或玻璃纤维增强复合材料制造汽轮机末级叶片, 由于此类材料的比重仅为钢的25% , 而其抗拉强度则可与钢相近, 因而是未来大功率汽轮机末级叶片材料开发的方向之一。
2 叶片疲劳失效
汽轮机叶片的断裂事故, 按其断裂性质可分为高周疲劳、低周疲劳、接触疲劳、高温疲劳、腐蚀疲劳等多种失效方式。
2.1 高周疲劳
高周疲劳失效是指叶片在运行过程中, 承受较低应力且应力循环次数大于10 000次情况下,所发生的一种疲劳方式;这种疲劳失效在火电厂的叶片断裂事故中最为常见。金属材料的疲劳断裂过程通常分为I个阶段, 即裂纹萌生阶段工、裂纹扩展阶段II、失稳态断裂阶段III。
高周疲劳裂纹萌生是一个相对缓慢的过程, 存在一定孕育期。大量光学和电子显微镜的观察表明,疲劳裂纹的萌生与滑移及滑移受阻有关,是局部应力集中及塑性变形的结果; 疲劳裂纹常出现在材料表面附近,萌生于滑移带、孪晶界、晶界及亚晶界、第二相粒子、夹杂物等处。疲劳裂纹萌生机制包括、位错偶极子塞积模型等。影响疲劳裂纹萌生的因素有材料组织结构、表面状况、载荷情况、环境与介质: 如不良材质状况、粗糙表面、高温及腐蚀介质等加速了裂纹的萌生,而材料的表面残余压应力可减缓裂纹的萌生。汽轮机叶片出现疲劳裂纹源的典型实例是,由于叶片或叶片组存在某种异常振动而迭加在叶片上一定的循环应力, 经过一段时间后在叶片表面缺陷(如夹杂,点蚀坑,划痕等}及局部应力集中处萌生出疲劳裂纹源。
萌后的疲劳裂纹源,是否能进一步扩展以及扩展的速度均与裂纹尖端的应力强度因子有关, 当应力强度因子超过门槛值时,裂纹源将进一步扩展, 即进人第II阶段的稳定扩展过程, 裂纹的扩展速率与应力强度
之关系附合
公式或其修正形式。当疲劳裂纹扩展到一定长度后, 即刻转人失稳态快速扩展(第III阶段) , 尤其是叶片在低周波或超负荷等不良状态下运行时, 将加速其最终断裂的过程。
高周疲劳断口的宏观特征: 断口表面平整, 呈细瓷状特征,贝壳纹线十分清楚, 疲劳扩展区的面积一般大于失稳瞬断区的面积。高周疲劳断口的微观特征;第I阶段疲劳断口的微观特征有解理特征、河流花样、平坦区、第二相粒子与基体之间的晶间断裂等;第II阶段疲劳断口的微观特征为疲劳辉纹、轮胎花样、二次裂纹、韧窝及准解理等;第III阶段失稳断裂的微观特征主要是韧窝断口。高周疲劳断口的微观形貌, 与应力状态及应力强度因子有关, 这种关系可参见相应的疲劳断裂机制图。
2.2 低周疲劳
低周疲劳失效是指叶片在运行过成中, 受到外界较大应力,或是较大的激振力,导致叶片经受较低振动次数即发生断裂的一种疲劳损坏方式。高低周疲劳的区别还在于塑性应变量的不同,高周疲劳时弹性应变占主导地位,称应力疲劳;低周疲劳时塑性应变占主导地位,称应变疲劳。
由于汽轮机运行不正常,疏水系统发生故障,使水进人汽缸内,叶片遭到水击而承受大的冲击力并产生较大塑性变形; 或是由于设计不良、安装不好、存在较大的低频激振力; 如转子不平衡而引起振动,隔板结构或安装不良,使叶片受到周期力; 或喷嘴损坏使叶片受力不均等 , 当它同叶片的自振频率相同时即引起共振,产生较大的循环应力和塑性应变,并导至叶片疲劳裂纹的产生、扩展、以及最终的失稳断裂。
叶片低周疲劳断口的宏观特征; 断口表面粗糙,疲劳贝壳纹(又称前沿线)不明显,在断面上疲劳区面积往往小于最终断裂的静撕断区, 断口的四周可能伴有宏观塑性变形, 经受水击的叶片断口还呈现“ 人” 字形纹络特征。叶片低周疲劳断口的微观特征为韧窝、准解理、晶间等花样, 但通常不存在明显的疲劳辉纹花样。
2.3 其它疲劳方式
除叶片高周疲劳和低周疲劳损坏方式外, 还有接触疲劳、高温疲劳、腐蚀疲劳等失效方式。叶片接触疲劳是由于存在某种振型的振动, 使毗邻叶片之间或者叶片与叶轮之间产生往复的微量位移,相互接触摩擦而产生的一种疲劳损坏方式, 接触应力往往是由根齿设计不合理, 或是安装不良产生的, 叶根的接触面因振动而进行循环往复磨擦,造成根部表面层材料晶体滑移和硬化,摩擦一定次数后,硬化区便会产生许多显微裂纹且不断地扩展,最终发生疲劳断裂。叶片的接触疲劳宏观断口, 通常具有贝壳状特征, 并往往伴有因摩擦氧化而产生的斑痕, 它们的显微裂纹呈簇状, 大体上互相平行, 并与摩擦应力方向垂直; 摩擦裂纹和摩擦硬化的现象并存,是接触疲劳的最基本特征,摩擦硬化和摩擦裂纹仅存在于接触部位的表层附近。除此之外, 接触疲劳还具有多裂纹源的特点。
狭义高温疲劳是指在材料再结晶温度以上所产生的疲劳,广义高温疲劳是指高于常温所产生的疲劳现象。叶片的工作温度低于再结晶温度, 如果叶片的损坏特征具有以下现象, 即称为高温疲劳损坏: ①蠕变和疲劳的共同作用造成叶片损坏, ② 高温氧化促进叶片疲劳裂纹的产生和发展。蠕变和疲劳共同作用所形成的高温疲劳是介于由静应力产生的蠕变和动应力产生的疲劳之间的一种损坏形式; 在裂纹源部位,蠕变现象明显; 在裂纹扩展过程中, 尤其是在快速扩展区,裂纹的性质是持久断裂和疲劳断裂的组合, 这种高温疲劳往往伴随着组织的变化。高温氧化使裂纹尖端的应力增大, 促进疲劳裂纹的产生和发展,高温疲劳断口的宏观形貌具有贝壳花样,而断口的微观形貌由于表面有较厚的氧化皮,在电子显微镜下很难进行观察。
腐蚀疲劳是叶片在腐蚀介质中受交变应力作用而产生的疲劳损坏,介于机械疲劳和应力腐蚀之间,当裂纹扩展速度较快时以机械疲劳为主, 裂纹为穿晶类型,断口的宏观形貌为贝壳花样,微观断口形貌具有条纹花样; 当裂纹发展速度慢时, 以应力腐蚀为主,裂纹主要为沿晶型, 断口的宏观特征为粒状断口,看不到疲劳贝纹花样, 断口的微观特征为冰糖块花样。
3 预防措施
汽轮机叶片疲劳失效, 受其设计、材质、加工与安装、运行与维护等因素的影响, 因而可从这几个方面来制订预防叶片疲劳失效的措施。
3.1 设计
金属零部件疲劳失效的前提, 是必须存在一定幅度的循环应力。在零件局部区域静应力与循环应力之迭加超过其强度门槛值的情况下, 必然要出现疲劳裂纹的萌生, 如果应力强度因子保持较高的水平,将造成疲劳裂纹的扩展直至最终断裂。在静应力与循环应力之迭加不超过其强度门槛值的情况下,通常不会发生疲劳损伤,该零件在使用中是安全的。
汽轮机叶片的设计准则是, 确保叶片各部位的工作应力处在安全水平; 要设法增大叶根的接触面积,改善叶轮与叶根接触面的接触状况,使叶根齿部在工作状态下尽量保持均匀的接触, 尽量减少叶片局部区域的应力集中。此外,在叶片的设计过程中,还应充分考虑到可能出现的振动型式, 避免不同振型的相互重迭,消除叶片共振的可能性,对预防叶片的高周疲劳、低周疲劳、接触疲劳等是十分有益的。
3.2 材质
材质状况直接影响到叶片材料的疲劳强度, 不良的叶片材质, 会降低叶片的疲劳抗力。例如材料中的夹杂物、不均匀的块状铁素体、链状碳化物、粗大奥氏体晶粒、回火脆性、内应力等材料缺陷, 对材料的疲劳寿命及耐腐蚀能力是极为不利的, 须加以控制。
在汽轮机叶片原材料投产之前, 应进行一系列的材质复验工作, 检查材料的化学成份、金相组织、力学性能等材质指标是否符合规定的要求, 还要对原材料有关的热加工艺进行审核。总之, 为确保叶片的质量,必须严格把住材料质量这一关。
3.3 加工与安装
汽轮机叶片的制造,是复杂而精密的加工过程: 如果叶片的尺寸及形线未达到要求, 可能引起叶片运行中的反常振动,增加叶片的附加循环应力,导致叶片的疲劳失效断裂; 如果叶片的表面太粗糙,或叶片表面存在明显的加工刀痕, 也可降低叶片的疲劳强度。采用新型的数控机床,优化加工工艺,并加强每道工序的检查工作, 确保叶片尺寸、形线、表面光洁度等指标附合要求,提高叶片加工精度。另外,建议增设一道喷丸处理工序, 以增加叶片表面局部区域的压应力,提高叶片的表面疲劳抗力。
叶片的安装质量是非常重要的, 安装太紧会增加叶片的附加应力; 安装太松、安装错位等不良的安装质量,均可能引起叶片的反常振动, 甚至会引起叶片的共振,导致汽轮机叶片的高周疲劳、低周疲劳、以及接触疲劳等断裂失效方式。为了提高汽轮机叶片的安装质量,除采用先进的安装工艺、严格进行质量检查外, 提高操作工人的责任心是必不可少的。此外, 叶片在装配后, 必须进行测频试验、动平衡试验等检测项目,尽可能降低叶片运行中反常振动的可能性。
3.4 运行与维护
在众多的叶片事故中, 由于运行与维护不当所造成的疲劳断裂占有相当大的比例, 应引起高度重视。通过改善运行条件、消除运行低周波、消除运行超负荷、消除运行低负荷、消除颤振、消除共振、消除低压缸水击、消除叶片之间及叶片同叶轮之间的磨擦等,是减小叶片的疲劳损伤延长叶片寿命的重要途径; 降低蒸汽的含氧量、避免蒸汽超温, 对限制汽轮机高压叶片的高温疲劳损伤是有效的; 改善蒸汽品质,是消除低压叶片腐蚀疲劳的主要方法。按照贯例, 电厂每年都要进行大修; 在汽轮机开缸检修期间,必须详细检查每级叶片的使用情况,如发现叶片上有微裂纹、明显的腐蚀或高温氧化痕迹, 应对其进行维修处理,必要时还可更换新的叶片; 否则叶片的带伤运行是非常危险的。
4 结束语
叶片是汽轮机的心脏部件, 处在高应力、高温、腐蚀环境下工作。汽轮机叶片的疲劳断裂失效, 一直是国内有关学者关心和研究的问题, 研究领域涉及到疲劳断裂理论的方方面面, 投人了大量的研究资金。到目前为止, 我国在常用叶片材料各类疲劳失效方面的研究已取得满意的结果,研究内容主要包括: ①新材料开发与疲劳性能测试,②疲劳起源与机理,③断口金相学与失效分析,④优化设计、材质控制、制造安装工艺的改进,⑤表面处理(如喷丸)以提高疲劳抗力,⑥ 运行与维护情况的调查。在此基础上,我国电站汽轮机叶片运行可靠性将不断提高,从而带来更大的经济效益。
免责声明:本网站所转载的文字、图片与视频资料版权归原创作者所有,如果涉及侵权,请第一时间联系本网删除。
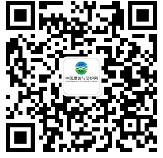
官方微信
《腐蚀与防护网电子期刊》征订启事
- 投稿联系:编辑部
- 电话:010-62316606-806
- 邮箱:fsfhzy666@163.com
- 腐蚀与防护网官方QQ群:140808414