0 引 言
装备是由各种材料制造的。从广义角度讲,是材料就有腐蚀问题,亦即是装备就有腐蚀问题。腐蚀现象的存在严重影响着装备性能和装备管理工作,腐蚀的发生会直接或间接导致装备安全性、可靠性的降低,对腐蚀故障的维护、维修会增加相应的费用,腐蚀造成的泄漏会恶化装备使用人员的工作、生活环境。因此美、俄等海军强国长期致力于舰船装备的腐蚀控制工作,我国同样会长期面临装备的腐蚀问题,需要展开艰苦、持之以恒的腐蚀预防与控制工作。
1 关于舰船腐蚀问题的基本认识
腐蚀是一种客观存在的自然现象,遵循电化学理论、金属氧化理论和材料老化理论 。随着现代工业发展和大量金属材料应用于工业、民用基础设施、国防乃至于日常生活,腐蚀问题逐步突显出来,腐蚀预防与控制工作逐渐受到人们重视。开展腐蚀预防与控制系统研究则是近 100 年左右的事情。大量腐蚀事故的不断出现使我们认识到,环境对材料的侵蚀是严重的,忽略腐蚀控制将会受到大自然的惩罚,将会造成重大的社会、军事和经济损失。
1.1 腐蚀问题的客观性
由于腐蚀引起的各种事故层出不穷。1956 年建设的湛江码头,由于腐蚀问题 1988 年决定拆除,使用时间仅为 32 年; 我国在开发某油田时,由于硫化氢应力腐蚀破坏产生井喷,大量天然气放空,在持续 6 天后又遇雷击引起火灾,一次造成经济损失达 6 亿元; 1974 年,日本沿海地区的石油化工厂贮罐因腐蚀破裂,大量重油流出,造成严重污染; 20 世纪 70 年代的重庆嘉陵江大桥大修时发现腐蚀深度达 2 ~ 3 mm; 2002 年的宜宾市南门大桥吊杆腐蚀失效后引起的突然倒塌,使用仅 11 年 ; 早期英国彗星式民用客机、美国 F111战斗机由于应力腐蚀发生空中坠毁; 1981 年我国某架直升机由于腐蚀疲劳导致飞机空中解体 ;1987 年美国航天飞机因橡胶密封圈老化失效造成燃料泄漏,航天飞机空中爆炸,机毁人亡 ; 美、英等国潜艇通海管路发生腐蚀穿孔,出现过海水淹舱、舱室设备报废的事故; 化工厂、油田由于管道腐蚀穿孔更是随处可见。
事实上,由于腐蚀引发的事故不计其数,腐蚀问题的发生不仅仅是在海军装备,也不仅仅是在中国,腐蚀问题是在装备上客观存在的事实,需要认真对待和处理。
1.2 舰船腐蚀问题的普遍性
在舰船上,无论是与海水直接接触的船体、附体、海水管路和相关设备,还是在海洋大气环境中使用的各类结构、系统、设备,无论这些构件、系统、设备是由金属材料制造还是非金属材料制造,都存在腐蚀和老化问题,也就是说都有一个寿命问题。以前大家关注比较多的是金属材料制造的如船体结构、海水管路等的腐蚀问题,随着装备和科学技术的发展,大量的新装备、新材料上舰 (艇),近年来经常听到 “某某电子设备从东海海域到南海海域以后经常出现故障”的谈论,这就是南海海域比东海海域腐蚀环境恶劣的缘故,出现了新的腐蚀问题。可以说,无论是传统的船体结构、机电设备/系统,还是发展迅猛的兵器、电子设备/系统,都存在腐蚀问题,都需要加强腐蚀控制。
1.3 舰船腐蚀问题危害的严重性
纵观世界舰艇装备发展史,腐蚀是引发重大恶性事故主要因素之一,由于腐蚀破损引发的舰船恶性事故并不鲜见。1956 年 2 月,苏联 C 型某艇,高压空气瓶发生爆炸,直接原因是腐蚀造成瓶体减薄、强度不足而引起; 1951 年 4 月 17 日,英国 “艾菲莱”常规潜艇,在韦特岛南方巡逻训练,发生沉没,艇员 75 人全部死亡,据分析最大可能是因材料选择不当造成腐蚀和焊接问题,使通气管在底座处折断,海水从裂口进入而沉没; 1965 年 9 月 22 日,英国 “无畏”核潜艇在法斯拉海军基地码头附近,尾舱因舷外附件损坏而下沉,海水罐进舱内,将推进电机泡坏,只得进厂拆开耐压壳体,更换电机;1973 年,美国 “黑线鳕”号核潜艇在向最大深度下潜时,一海水管路破损,海水进入舱内,后迅速将进水排掉才没有导致舱室淹没; 1958 年 4 月 25 日,美国 “鹦鹉螺”号核潜艇主冷凝器管子腐蚀漏水,通过不大的孔道海水进入主冷凝器用的补水回路中,主冷凝器无法继续工作; 1959 年,该艇在大西洋沿海进行反潜战斗演习时,在 20 m 深度潜航,机舱冷凝器的 4 英寸冷却水管损坏,海水进入机舱,几乎灌满了整个舱室,后经堵住通海阀,并紧急上浮,才幸免于难。由于船体板腐蚀穿孔而使得海水进入油舱引发动力设备故障,海水管路破损造成舱室进水而不得不停机停航,这些事故在水面舰船上则多有发生。
腐蚀会造成重大的经济损失。腐蚀经济损失可分为直接损失和间接损失。对于舰船来说,直接损失是指更换被腐蚀的船体、构件、设备、管路等,并包括这种更换工作所需劳动力在内合计花费的费用; 另一类直接损失的例子是对这些构件、设备进行以防锈为目的的重新涂装的费用和外加电流、牺牲阳极阴极保护时的基本投资及维持费用。间接损失包括停航损失、效率损失、过度设计、污染损失等。间接损失难以估算,若腐蚀引起爆炸、舱室进水、潜艇沉没就不是用经济性来衡量的了。美国2004 财年全军因腐蚀造成的综合预算为 200 亿美元,其中海军腐蚀预算为 22. 5 亿美元。我国在海军舰艇方面的腐蚀损失没有详细统计,有的资料表明腐蚀损失要超过修理费的 1/3,腐蚀问题占装备故障比例超过 2/3,已严重影响装备使用、在航率,使维修经费大量增加。如果说,能将腐蚀损失减少一定比例,经济价值将十分可观。
2 舰船腐蚀预防与控制系统工程基本思想
2. 1 要将腐蚀预防与控制工程置于装备技术发展的重要位置
腐蚀会引发舰船恶性安全事故,腐蚀会降低设备和系统的可靠性,修理腐蚀故障会造成停机停航,引起在航率下降。所以,舰船腐蚀预防和控制是一个与舰船装备安全性、可靠性、战斗力密切相关的工程,是一项非常重要的工作。无容置疑,应该将舰船腐蚀预防与控制作为一项大事来抓,将腐蚀预防与控制相关材料、工艺、技术的发展作为海军装备技术发展的一个重要组成部分。
2. 2 要积极推进 “腐蚀经济学”,算好全寿命、全行业的经济账
腐蚀控制强调的是技术上的先进性、可靠性与经济上的合理性、节约性的辩证统一。与一般的经济问题不同,它既要满足一定的技术要求,又要满足经济上最节约的原则,设计建造部门要根据军方提出的要求和提供的经费情况,提出型号的具体设计建造目标设想和设计建造对策,进行认真的经济分析,以求获得军方要求的设计并达到经济效果的最优化; 设计部门还要在设计之初根据型号的维修间隔进行维修性设计,统筹优化研制阶段为腐蚀控制而进行的材料、工艺、技术的直接费用和使用过程中的维护保养、换件、修理等后续过程的间接费用,要达到全寿命费用的最优,而不仅仅是研制阶段费用的最优。设计人员还要了解掌握国家相关矿产、材料资源储备和技术基础,尽量选择符合国家发展战略大趋势的材料、技术,为国家节省资源和避免造成不必要的浪费。
2. 3 腐蚀预防与控制必须进行顶层设计、系统控制
要控制腐蚀,需要论证、设计、制造、使用、维护、修理有关工程技术人员的共同配合,从图纸设计开始,进行全员、全方位、全过程、全寿命的控制。要真正控制腐蚀,需要研究和发展一系列相应的腐蚀控制技术。也就是说,腐蚀要进行系统控制,才有可能获得成功。
2. 4 腐蚀预防与控制必须从设计开始
舰船总体、系统或设备的设计师如果不能把握自己所设计的对象可能遭受的环境侵蚀性,让具有侵蚀性的介质随意肆虐其设计对象; 所设计的结构不足以抵御腐蚀和外力的协同作用; 设计选用材料在所在的环境中不具有良好的耐蚀性; 甚至设计师对所同意的制造工艺可能带来的腐蚀危害心中无数的话,装备的腐蚀就会不可避免地发生,甚至造成灾难。腐蚀的预防只有从设计源头抓起,才是最根本的保障。型号总师要从全舰/艇的高度和全寿命周期角度对军方提出的腐蚀控制技术指标进行合理分配,要对各系统之间、系统与总体之间的用材、腐蚀控制技术进行协调,要预留足够的重量和空间裕量用于腐蚀控制; 设计师要进行合理的预防腐蚀的结构设计,预防应力腐蚀、磨蚀或疲劳腐蚀的设计,预防不同金属接触的电偶腐蚀设计,耐蚀材料与加工工艺合理选用的设计; 各系统的设计师要提出外购件、外购设备在制造过程中的腐蚀控制要求; 设计师为了满足上述需求,要不断学习腐蚀科学知识,掌握腐蚀控制技术的最新进展,要具备预防腐蚀和控制腐蚀的设计能力。
2. 5 腐蚀预防与控制要贯穿建造的全过程
有了良好的设计,腐蚀控制才刚刚开始。设备和构件的制造应该完全按照设计的要求,制造出完全符合设计要求和设计内容的新产品; 制造工艺不能损伤材料固有的耐蚀性; 要严格制造过程,相关的制造工人了解相关工艺规程,不能有所疏忽而损伤了材料的耐蚀性; 要有制造过程进行全员、全方位预防腐蚀控制的质量保证体系及其成套的技术和管理文件。
2. 6 使用过程中要始终注意延缓腐蚀发生
当部队接受产品、投入使用的整个过程中,要按照舰船、各系统、各设备的使用要求进行维护、保养,要定期检查阴极保护装置是否处于良好的运行状态,要及时地更换用于保护的牺牲阳极元器件,要及时排除舱室积水使舱室保持干燥状态,要定期检查液舱、潜艇上层建筑区域、海水管路等易腐蚀部位的腐蚀情况,并记录在案,确保舰船装备使用可靠性、安全性和耐久性。
2. 7 修理过程中要注意继承性、相容性
一艘舰船在寿命周期内要经过多次坞修、小修,至少要经过 1 次中修。在这些修理过程中,要根据装备的腐蚀情况和腐蚀控制技术发展情况进行修理或修复设计。在这些修理或修复设计时,要密切关注采用的修理或修复材料、工艺是否与原有的材料、腐蚀控制工艺相矛盾,是否会对相邻的区域构件、系统和设备产生影响,应特别强调修理、修复过程中的材料、工艺的继承性和相容性。
2. 8 要建立腐蚀控制系统工程的管理程序
总体设计部门、总装厂和大型设备的制造单位要研究建立腐蚀控制系统工程的管理程序和要求,要对设计、制造的每个过程进行监督检查,要明确设计师、制造人员在腐蚀控制过程中的职责、任务和具体原则,要有外购材料、外购零部件、外购装配件的腐蚀控制措施和要求,要有装备交付部队时成套的腐蚀控制培训机制和相关文件,才有可能实现舰船从设计、研制、生产、使用、维护、修理直至退役的全过程进行全方位腐蚀控制。
3 舰船腐蚀控制系统工程
当前几项紧迫工作经过几十年的发展,腐蚀预防与控制技术有了长足的发展,舰船腐蚀问题得到了有效控制,但是随着舰船航行的更远、下潜的更深、寿命要求更长以及发展了更多型号,新的舰船腐蚀问题又在不断涌现,除在设计、建造、使用、修理等过程中进行腐蚀控制以外,还有一些共性问题需要集智攻关,破解难题,使得设计、建造、修理等技术人员能做 “有米之炊”。
3. 1 腐蚀预防与控制技术发展规划、计划和逐步实施
舰船腐蚀预防与控制技术涉及面广、要求高、基础薄弱,先进的防腐蚀方法、措施、工艺匮乏是造成舰船腐蚀预防与控制技术水平不高的一个主要原因,防腐蚀整体技术不能满足新时期舰船高质量要求和高强度的训练使用要求。腐蚀预防与控制技术应该有一个长远的发展规划和能够逐步实施的年度计划,改变当前的 “零打碎敲”和 “头痛医头、脚痛医脚”的局面。由于腐蚀问题引起的巨大开销,美国海军通过每年对国防腐蚀花费的构成、比例、规律等的系统分析,剖析出存在的腐蚀共性问题和难题,然后有针对性地对经费投入进行调整,在此基础上确定下一财年的国防腐蚀经费预算。2005 年 5 月,美国国防部向国会递交了 《最新的关于减小腐蚀及其对军用装备和设施影响的努力和成果》的报告,其中明确提出了为实现这一目标的近期和长期研究项目资助计划。即使美国海军腐蚀防护技术非常发达的国家,每年仍投入大量经费用于研究和技术攻关,以求不断发展和进步。而对于向我国舰船腐蚀预防与控制技术研究基础较为薄弱的国家,更应该在这方面加大投入,力求跨越式发展,以尽快提高我国舰船腐蚀预防与控制技术水平,避免腐蚀问题成为舰船装备发展的瓶颈。
3. 2 相关标准、规范、要求的编制
腐蚀问题涉及到舰船装备的方方面面,涉及到的标准规范数量也是非常庞大。要提高舰船腐蚀预防与控制技术水平,相关标准规范的编制、修订已迫在眉睫。近年来,相关部门为改变局面围绕着型号研制以文件形式提出了一定数量的技术要求,并已着手安排相关标准的编制,这些要求对于推动舰船装备腐蚀预防与控制技术发展起到了积极的作用。
但是相关标准缺少、内容落后、相互矛盾的现象依然存在,其发展速度远远不能满足装备发展需要。
3. 3 材料耐蚀性能提高和材料环境考核
舰船腐蚀问题与基体材料的耐蚀性密切相关,说到底材料是否耐蚀是腐蚀控制的 “本”。我们在今后相当长的一段时间内,一方面要积极开发耐蚀性良好的先进材料,要积极研究如何提高现有的材料耐蚀性能,另一方面要加强上舰材料的环境考核工作,要将材料的耐蚀性、耐久性作为材料的一项重要指标。
3. 4 腐蚀数据库的建设
装备的腐蚀故障减少与腐蚀控制技术水平的提高相辅相成,要以海军为主导逐步建立材料环境考核的腐蚀数据库和装备的腐蚀数据库,只有设计、研制、修理等相关技术人员全面掌握材料腐蚀和装备腐蚀的真实情况,才有可能进行设计改进,有可能相互吸收经验教训,真正提高装备的腐蚀控制技术水平。
3. 5 腐蚀监检测与评估工作
在明确设计、建造、使用、修理人员在装备腐蚀预防与控制职责基础上,应加大研制、使用、修理等各阶段的装备腐蚀监检测和评估工作,要形成问责制,否则责、权、利不明确,很难真正提高装备的腐蚀预防与控制水平。
更多关于材料方面、材料腐蚀控制、材料科普等方面的国内外最新动态,我们网站会不断更新。希望大家一直关注中国腐蚀与防护网http://www.ecorr.org
责任编辑:殷鹏飞
免责声明:本网站所转载的文字、图片与视频资料版权归原创作者所有,如果涉及侵权,请第一时间联系本网删除。
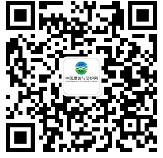
官方微信
《中国腐蚀与防护网电子期刊》征订启事
- 投稿联系:编辑部
- 电话:010-62313558-806
- 邮箱:fsfhzy666@163.com
- 中国腐蚀与防护网官方QQ群:140808414