案例概况
某公司炼油厂安全技术人员对中间产品罐区储罐进行罐内可燃气体浓度和H2S气体浓度检测时发现其4个罐罐顶可燃气体浓度和H2S气体浓度超标,可燃气浓度在30ppm左右,H2S气体浓度在100ppm左右,在发现这一情况后车间分析认为罐内的内浮船在密封方面存在问题,导致罐内储存介质中含有的气体外泄,检测时浓度超标,因此车间对这些罐安排停用检修。检修过程中发现铂料罐的浮盘蒙皮、浮筒及其它附件腐蚀严重,严重影响了浮船的使用效果。
腐蚀检测
宏观观察
对罐铝浮船浮盘蒙皮和浮筒腐蚀表面进行检查,发现浮盘蒙皮上表面(接触气相部位)出现黑褐色的锈蚀,且锈蚀部位产生许多大小不等的蚀孔,浮盘蒙皮已穿孔。而浮盘蒙皮下表面气相与液相交界处则覆盖着大面积的黑褐色锈蚀,出现多处蚀孔,如下图所示,说明浮盘蒙皮下表面气相与液相交界处腐蚀是由含硫化氢油气所造成。腐蚀穿孔是由浮盘蒙皮下表面产生,并向接触油气部位的浮盘蒙皮上表面发展;浮筒焊缝处锈蚀严重,黑褐色锈层集中分布在焊缝处,然而焊缝处以外腐蚀轻微,浮筒上部仍保持金属光泽,说明浮筒外壁发生孔蚀后,油气进入浮筒,浮筒内壁焊接处出现许多蚀坑,而且蚀孔边缘处有明显减薄,孔蚀边缘锈层呈絮状花纹,出现许多微减薄,说明浮筒腐蚀最初是由浮筒外壁向内壁扩展。

图1.罐密封胶带腐蚀破损

图2.罐浮船蒙皮腐蚀破损

图3. 罐浮船浮筒腐蚀破损
腐蚀原因分析
通过现场检查和综合分析认为中间产品罐铝浮船浮盘蒙皮和浮筒是由于中间产品中含硫化物而导致局部腐蚀;同时,由于介质含水和稀释引起氯化物对浮盘蒙皮和浮筒的局部腐蚀。对铂料罐区储罐内的介质进行了分析,分析结果见下表:

分析认为,铂料中含有硫化物等腐蚀性介质,这些腐蚀性介质从铂料中逸出,溶解在油气中,从而加速浮盘蒙皮和浮筒的腐蚀。
当储罐付油时,含氧空气可通过人罐顶和罐壁的透气孔进人罐中,造成气相空间存在大量含氧空气;当储罐收油时,由于内浮盘密封圈和罐壁之间有一定间隙,在正压力作用下,少部分油气就从间隙处进入罐顶和内浮盘之间,使浮盘上表面、罐壁和罐顶遭受含硫气体的腐蚀,而且含硫气体与空气中的水和氧相互促进而加速腐蚀。值得指出的是,浮筒的二分之一均处于气液交替处,腐蚀比气相部位要严重得多;浮盘蒙皮盖板下表面和浮筒外表面的腐蚀穿孔均验证了这一点,由于空气中的氧透过油气比透过完全浸没的液层要容易的多。
铝浮船蒙皮、浮筒腐蚀穿孔,储存介质中含有硫、水,对油罐、铝浮船具有一定的腐蚀性。在浮船与储罐的空间内介质里含有的酸离子与水反应生成了SO32-离子、SO42-离子,所含有的H2S与水反应生成氢离子,这些离子存在于液体和浮船间的气相空间里,金属与硫化物产生酸性物质直接于浮船接触,与浮船表面接触腐蚀直至穿孔。浮筒暴露在气相空间的部分与酸性物质接触,也导致了浮筒的局部腐蚀穿孔。
另一方面,浮船在长期频繁运行过程中,受到油品的腐蚀,油品的温度的变化、气候变化、罐体的变形、浮船附件不完好的影响、浮船几何形状和尺寸变化、罐内的油品大量进入到腐蚀穿孔及焊口拉裂的浮筒内,浮筒内油品的重力大于浮船的浮力,以致浮船靠建北侧浮力下降,局部严重倾斜。
该厂使用的铝浮船舌型密封胶带选用的是丁氰橡胶材料,这种橡胶在耐油气腐蚀方面性能较差,和氟橡胶材料的密封胶带相比,氟橡胶材料的密封胶带的耐腐蚀性和柔韧性都更好,但相对价格也更高,是丁氰材料的10倍左右,所以车间普遍使用的都是丁氰橡胶的密封胶带,503号罐浮船密封胶带使用时间较长,油品的腐蚀浸泡已影响破坏胶带的密封性。
内浮顶罐浮船与罐体用铜编织带作为导静电设施,用于释放浮船起浮及油品进出产生的静电,中间产品罐的浮船变形后部分油气泄漏至浮船上,使铜导电带受到罐内油气的腐蚀发生断裂掉在浮船上,掉在浮船上的导电带和浮船接触,对浮船形成了一定的腐蚀,造成了在导电带与浮船接触的地方铝浮船发生腐蚀穿孔见图4。

图4.浮船导电带腐蚀情况
结 论
中间产品储罐浮船盖板蒙皮和浮筒是由于物料中有硫化物而导致局部腐蚀穿孔,腐蚀穿孔是由浮盘蒙皮下表面发生,并向接触气相部位的浮盘蒙皮上表面发展。同时,由于储存介质含水和稀释引起氯化对浮盘蒙皮和浮筒的局部腐蚀。
浮船浮筒暴露在气相空间的部分与酸性物质接触,也导致了浮筒的局部腐蚀穿孔。
铝浮密封胶带选用的丁氰橡胶材料在耐油气腐蚀方面性能较差,由于浮船盖板腐蚀泄漏和油品的腐蚀浸泡严重影响了胶带的密封性,导致密封胶带损坏。
中间产品储罐的浮船变形后部分含硫油气泄漏至浮船上,使铜导电带受到罐内油气的腐蚀发生断裂。
预防措施
定期对浮船上部空间气体进行采样分析,发现有毒有害气体含量超标,应该进行停用检修,并且每2年对含硫量较高的储罐进行开罐检查和维护,及时了解浮盘导向柱、浮盘自动呼吸阀、浮盘表面、浮盘安全附件、油罐内表面防腐状况,对油罐及其附件应作全面、细致的检查,尤其对罐内储存腐蚀性强的介质,更要加强监控,确保及时发现和消除事故隐患。
改善工艺条件,严格按规程操作。上游装置要切实抓好平稳生产,避免波动,控制好来油不串气和来油温度,对上游装置的含硫物质进行脱硫处理,严格控制进油速度,严格按规程操作,杜绝违章作业。
加强日常巡检工作,提高巡检的质量和发现问题的能力,使隐患能得到及时发现和处理;修订油罐安全附件检查要求及细则,完善设备管理制度,强化各项设备管理制度的执行。
利用公司有毒有害气体治理、改善环境质量的机会进行浮船升级改造,届时采用新型扇形结构浮船及新型的氟橡胶密封材料,对浮船导向柱采用不锈钢材质。提高浮船的使用安全性、可靠性。
为了防止浮盘蒙皮上表面(接触气相部位)腐蚀,选择软泡沫塑料外包不漏液的环向橡胶包袋的密封形式,限制和降低硫化物和硫化氢的挥发或逸出;定期进行清洗去除浮盘上表面的腐蚀产物,确保浮盘的正常起浮。
免责声明:本网站所转载的文字、图片与视频资料版权归原创作者所有,如果涉及侵权,请第一时间联系本网删除。
相关文章
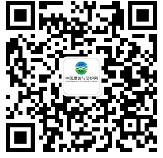
官方微信
《中国腐蚀与防护网电子期刊》征订启事
- 投稿联系:编辑部
- 电话:010-62313558-806
- 邮箱:fsfhzy666@163.com
- 中国腐蚀与防护网官方QQ群:140808414
点击排行
PPT新闻
“海洋金属”——钛合金在舰船的
点击数:5768
腐蚀与“海上丝绸之路”
点击数:4763