随着工程机械、汽车等行业的快速发展,为降低成本、增“强”减重,以实现节能降耗的目标,国内外广泛探索工程机械及汽车的轻量化方法。要最大限度地减轻设备质量,一个有效的途径就是提高钢的强度级别。
近年来,工程机械用钢从500~600MPa级快速上升至800MPa、1000MPa,甚至1500MPa。然而,随着强度提高,钢的延迟断裂敏感性也随之增大,氢致延迟断裂敏感性高已经成为制约高强度级别钢种推广应用的一个重要因素。
高强钢的氢致延迟断裂现象
延迟断裂是材料在静止应力的作用下,经过一定时间后突然发生脆性破坏的一种现象,它是材料—环境—应力之间相互作用的结果,是氢致材质恶化的一种形态。
延迟断裂现象的产生是由于材料内部的氢向应力集中的部位扩散聚集,这些应力集中的部位往往缺陷较多(原子点阵错位、空穴等),氢扩散到这些缺陷处,氢离子合成氢原子,氢原子进一步合成氢分子,将产生巨大的压力。
这个压力与材料内部的残余应力以及材料服役状态下所承受的外加应力,形成一个合力,当这个合力超过材料的屈服强度时,就会导致断裂的发生。
由于延迟断裂常常在材料所承受的外加应力水平显著低于其屈服强度时突然发生,具有其不可预知性,因此,往往导致较为严重的破坏和后果。随着超高强度级别钢的发展及其应用领域的不断拓展,延迟断裂现象受到更大程度的关注。
以汽车零部件为例,其产品形状复杂,变形量大,车厂、零部件制造商及材料供应商对延迟断裂性能更加重视,已经成为材料性能认证项目之一。
延迟断裂行为的影响因素
金属材料的延迟断裂行为是在材料、环境和应力三者共同作用下发生的,与材料的特性以及受力状态、服役环境密切相关。
材料强度的影响。一般来讲材料的强度越高,其延迟断裂敏感性越大。一般认为1000MPa是一个危险的水平,即抗拉强度低于1000MPa时钢材耐延迟开裂的性能相对较好,而当材料强度大于1000MPa时,其延迟断裂敏感性较高。
合金成分的影响。不同的合金元素会对材料的延迟断裂行为产生不同的影响。研究发现,随着钢中(Mn+0.5Si+S+P)含量的升高,4340系列钢材发生氢致延迟断裂的临界应力强度因子随之下降,说明其断裂敏感性逐渐升高。
这是由于钢中C、S、P、Si、Mn等元素的偏析会促进腐蚀环境下氢的吸收,从而增大材料的氢致延迟断裂敏感性,使得材料在较低的应力水平下即发生断裂。
而Ti、V、Mo、Ni、Nb等元素可细化晶粒,提高材料的韧性,减少偏析,而且所形成的细小析出物有利于形成氢的捕获陷阱,从而降低材料的延迟断裂敏感性。此外,也有研究指出,Al元素的添加可以显着改善含锰TWIP钢的氢致开裂敏感性。
微观组织的影响。由于氢在不同组织中的扩散速度和储存能力不同,因此,材料的微观组织对延迟断裂敏感性的影响很大。从金相组织上讲,相比于奥氏体和全珠光体组织,铁素体—马氏体和单一马氏体组织钢材具有更高的氢致延迟断裂敏感性。
此外,相同的应力水平下,加工诱发马氏体的含量越高,延迟断裂敏感性越大;在相同的强度水平下,含Mo的高温回火马氏体组织,比普通回火马氏体钢的极限扩散氢含量高,延迟断裂敏感性降低。
同时,材料微观组织上的不均匀性,如晶界、相界等,由于原子错排和局部应力场的存在,会成为氢的捕获陷阱或氢快速传输的通道,从而影响材料的氢致延迟开裂行为。此外,降低晶粒尺寸,晶界处吸附的氢含量减少,也有利于改善材料沿晶界开裂的敏感性。
加工缺陷的影响。高强钢的加工会经历弯曲、拉拔、冷轧等工艺,不同的加工方式会在材料上留下微孔、微裂纹和位错等缺陷,这些缺陷位置会成为氢的捕获陷阱或者提供氢原子快速传输的通道,在外力作用下还会在缺陷位置形成应力集中,它们会对材料的氢致延迟开裂行为产生较大的影响。
受力状态的影响。一方面,金属构件在服役过程中会受到各种外力的作用;另一方面,材料本身也会因为不同的加工成型过程而产生不同的残余应变状态。高强钢的主要成型工艺有折弯、扩孔和翻边、浅拉伸等,这些加工残余应变的存在会促进延迟断裂的发生。
最新研究认为,加工过程中产生的残余应变是外加应力和材料中的可扩散氢含量之外的第三大导致高强钢延迟断裂失效行为发生的重要因素,氢致延迟断裂行为发生的敏感区处于高外加应力、高应变和高浓度扩散氢含量的重合区。
环境的影响。环境主要是会影响氢向金属材料内部的渗透。金属在各种致氢环境中,如氢气、H2S气体和水溶液、水介质、丙酮等有机溶液中,氢致延迟断裂敏感性会大大增加。
根据环境中氢来源的不同,高强钢的氢致延迟断裂行为主要分为以下两类:一类是服役环境渗入的氢(外氢)引起的延迟断裂,如桥梁用高强钢,在潮湿大气、雨水等环境中长期暴露发生腐蚀,由腐蚀反应生成的氢侵入钢中而发生延迟断裂。另一类是酸洗、电镀、焊接等制造过程中侵入钢中的氢(内氢)引起延迟断裂。
以焊接为例,它是一个局部冶炼过程,局部高温可使焊条及药皮中所含的水分分解成氢原子进入金属。这些过程引入的氢含量较高,因此,钢材常常在施加应力后的几小时或几天内即发生延迟断裂失效。
氢致延迟断裂机理
关于氢致延迟断裂的机理,近年来已经进行了广泛的研究,但问题还远远没有解决。已经提出的经典理论主要有:氢压理论、氢降低表面能理论、氢降低原子键合力理论,以及氢促进局部塑性变形理论等。
氢压理论、氢降低表面能理论和氢降低原子键合力(即弱键)理论均认为,氢致裂纹的产生和扩展是原子面在正应力作用下的整体解理过程,即氢致脆性的过程。
与此相反,氢致局部塑性变形理论则认为任何断裂过程都是局部塑性变形的结果。该理论认为,在存在应力梯度的条件下,如裂纹尖端附近,由于应力诱导扩散,原子氢能富集在裂纹尖端局部区域。
当有效氢浓度达到临界值时,可以使局部区域的表观屈服应力明显下降,于是在较低的应力作用下就能产生氢致滞后塑性并导致滞后断裂,而且局部区域表观屈服应力的下降量明显依赖于钢的强度和初始氢含量。
总体来讲,上述4种经典理论都有其局限性,将氢促进局部塑性变形理论和弱键理论、氢压理论联合起来,是今后研究的一个方向,有可能发展新的氢致开裂理论以解释氢致韧断和氢致韧脆转变机理。
延迟断裂性能实验室评价方法
材料的延迟断裂性能受到许多因素影响,但目前尚未形成通用的评价标准,在实验室评价材料的延迟断裂性能往往采用加速型方法来进行相对评价。目前,常见的延迟断裂试验方法有如下几种:
1. 恒载荷延迟断裂试验。这种试验通常采用光滑或带缺口的圆棒或平板试样在恒载荷下拉伸,或者采用带缺口的悬臂弯曲试样、四点弯曲试样等。对于此类实验,一般用临界应力、断裂时间或者临界氢浓度来评价材料的延迟断裂敏感性。
2. 恒应变延迟断裂试验。恒应变延迟断裂试验是使试样处于恒定应变的受力状态下,其主要特点是简单、经济、试样紧凑,不需要特殊的装置,仅利用夹具或螺栓紧固即可获得应力。试样的实际应力随工作截面的减少而降低。一般通过测定延迟断裂试样占总试样数目的百分比或试样断裂的时间,来比较材料延迟断裂的敏感性。
3. 慢应变速率拉伸试验。目前,国内外已广泛采用慢应变速率拉伸试验(SSRT)方法,以促进试样在很短的时间内发生延迟断裂并能敏感地反映材料的延迟断裂性能。通常用塑性(断面收缩率、伸长率)损失、最大断裂应力、断裂时间和吸收能量等指标评价给定材料-介质体系对延迟断裂的敏感性。
4. 断裂力学试验。这类方法采用预制裂纹试样,其优点主要是:缩短了裂纹产生的时间;真实反映了实际构件中难免存在宏观缺陷的情况;可直接使用线弹性断裂力学公式;评价判据KISCC或KIH不随试样而变,可以应用于设计。但是这种方法只是评价氢致裂纹的扩展,对于裂纹的产生不能提供任何信息。
5. 冲杯试验。作为一种标准化的氢致开裂评价方法,冲杯试验在欧洲应用得较为广泛。相比于U弯试验,冲杯试验中发生氢致开裂的临界应变与临界氢含量更高,也即冲杯试验中材料在更高的应变和可扩散氢含量条件下才会发生氢致开裂。
更多关于材料方面、材料腐蚀控制、材料科普等方面的国内外最新动态,我们网站会不断更新。希望大家一直关注中国腐蚀与防护网http://www.ecorr.org
责任编辑:王元
《中国腐蚀与防护网电子期刊》征订启事
投稿联系:编辑部
电话:010-62313558-806
邮箱:fsfhzy666@163.com
中国腐蚀与防护网官方 QQ群:140808414
免责声明:本网站所转载的文字、图片与视频资料版权归原创作者所有,如果涉及侵权,请第一时间联系本网删除。
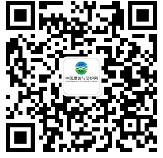
官方微信
《中国腐蚀与防护网电子期刊》征订启事
- 投稿联系:编辑部
- 电话:010-62313558-806
- 邮箱:fsfhzy666@163.com
- 中国腐蚀与防护网官方QQ群:140808414