防腐涂料是人类挑战锈蚀的重要工具,然而,涂层会因受到外力的冲击而发生损伤和脱落,使金属表面不能得到有效防护。模仿生物体自修复( Self - Healing) 功能的基本原理,使材料对内部或者外部损伤能够进行自修复,可以消除隐患,延长涂层使用寿命,实现对底材的长效防腐保护。20 世纪90 年代初期,Dry首先将自修复功能付诸聚合基体材料的损伤修补。21 世纪初,自修复涂料作为新材料和新技术被开发成功,并引起美国军方的高度重视。国外一些科研人员提出了利用微胶囊包覆修复剂技术实现材料的自修复,并对微胶囊的大小、基材性能、催化剂和外部裂痕等条件对修复效率的影响进行了多方面的探索研究。但是,生物体具有新陈代谢能力,可源源不断地产生自修复成分,而聚合物材料中的自修复组分在一次修复后将局部耗尽。如何模仿生物体的自修复原理,制备一种智能防腐涂层,它可以反复进行自我修补,并可以作为一种很薄的涂层长期稳定地使用,成为近期国际上仿生智能涂层研究的目标。本文对实现自修复功能技术方法、选择修复剂体系的原则、微胶囊技术在自修复材料中的最新研究成果进行了总结。
1 实现修复功能的技术方法
自修复技术是模仿生物结构的特性,实现材料在没有外界参与的条件下进行自我愈合,其核心是能量补给和物质补给。具有自修复功能复合材料的提出使得复合材料对内部或者外部损伤能够进行自我修复,可以阻止复合材料尤其是脆性材料内部微裂纹的进一步扩展,从而显着增加材料的机械强度,明显延长材料的使用寿命。目前,材料实现修复功能主要有2 种途径: 被动修复和自动修复。
1. 1 被动修复技术
被动修复主要是指必须依赖于外加辅助条件方可实现的修复,常借助于外界能量的供给。一种是利用热压焊接的技术,通过对聚合物材料进行加热使其升温到玻璃化温度以上,然后在加压的条件下修复损伤。该方法受材料的玻璃化温度影响很大,不适合玻璃化温度太高的材料。而且该方法通常只适用于热塑性材料。另一种是利用高交联聚合物进行共聚,如以呋喃多聚体和马来酰亚胺多聚体为原料,利用Diels -Alder( DA) 环加成反应形成具有可逆共价键的大分子交联网络,当材料局部出现裂纹时,通过加热到一定的温度就可以实现可逆反应,从而实现材料的修复。该方法直接通过加热就可以实现材料自身的修复,而且由于该反应可逆,可以进行多次重复修复,修复效率较高。但该方法只适用于特定的树脂。
由于防腐涂层所用成膜物质大多是热固性树脂,无法利用温度的改变实现修复功能,因此该技术不适用于防腐涂层的修复。
1. 2 自动修复技术
自动修复技术是指无需能量供给,借助于基体材料中预先封装或包埋的修复剂体系实现自修复功能。White 等模仿生物体组织自愈合性能,开发出一种基于微胶囊技术的完全自主修复方法。将内包有修复液的微胶囊和催化剂分散于聚合物中,当聚合物涂层产生裂纹时,伸展裂纹将导致微胶囊的破裂,其中的修复液被释放并由于毛细管作用流入裂缝中,阻止裂纹的进一步扩展,并实现裂纹修复功能,其修复原理如图1 所示。
图1( a) 表示复合材料内微裂纹的产生; 图1( b) 表示裂纹扩展导致微胶囊破裂,释放修复剂; 图1( c) 表示修复剂遇到催化剂后发生聚合反应,形成交联网状结构,修复裂纹,最终达到修复的目的。
常用封装修复剂的容器有中空玻璃纤维和微胶囊。微胶囊技术是利用成膜材料包覆具有分散性的固体物质、液滴或气体而形成微粒的一种技术。微胶囊的制备方法有化学法、相分离法和物理法。化学法是常用的制备方法,其中,应用最多的是原位聚合法和界面聚合法。White 等首先通过原位聚合法制备了以脲醛树脂为壳、环戊二烯二聚体( DCPD) 为核的微胶囊,将微胶囊与Grubbs 催化剂一起分散在环氧树脂基体中,当材料产生裂纹时,裂纹前端应力集中引发微胶囊破裂,包覆在其中的DCPD 在毛细管的虹吸作用下渗入裂纹处,与此处包埋的Grubbs 催化剂相遇,在催化剂的作用下发生聚合反应,实现环氧树脂的自修复。虽然利用聚脲甲醛包覆DCPD 微胶囊可以制备自修复效果较好的自修复复合材料,但是DCPD 的凝固点为19. 5 ~ 33. 0 ℃,不适用于室温或较低温度下成膜的涂料体系。Cosco 等在油水界面处通过原位乳液聚合制备了以脲醛树脂为壳、环氧树脂为芯的微胶囊,对影响参数进行了考查,并进行了结构的表征与性能研究。研究结果表明随着反应温度和搅拌转速的提高,聚合反应由水相聚合更趋向于界面聚合,从而使微胶囊包覆效率提高。Yang等采用界面乳液聚合的方法制备了以聚氨酯为囊材,以异佛尔酮二异氰酸酯/氯苯为芯材的微胶囊,利用异佛尔酮二异氰酸酯在潮湿环境中的自聚合实现修复功能。方征平等结合硅氮化反应及其催化剂的特点,提出了一种新的自修复体系,修复剂选用兼有多个硅氮键和硅乙烯键的低聚有机硅氧烷。该体系由分散于基体中的包覆有修复单体的微胶囊和能在常温常压下快速高效催化硅氮化反应的负载型铂基催化剂的增强粒子或纤维填料构成。
利用微胶囊技术实现自修复是一个真正的自愈合的过程,是现在自修复技术研究的重点。虽然微胶囊技术对聚合物基复合材料的自修复很有潜力,但目前所制备的可用于聚合物基复合材料的微胶囊种类仍有限,且在裂纹修复动力学和催化剂的稳定性及材料多次自修复能力上仍存在很大限制。如何实现在材料破裂处的多次修复是该技术今后发展的重要方向。
2 微胶囊技术自修复效果的影响因素及体系选择条件
2. 1 微胶囊技术自修复效果的影响因素
自修复效果的影响因素有很多,如微胶囊的浓度与大小、微胶囊的包覆率、微胶囊的力学性能、微胶囊在基体材料中的分布、修复剂的种类、修复剂的流动性能、修复剂的聚合速率和聚合度、愈合裂纹的时间及愈合温度、被愈合树脂基体的种类等。此外,各种因素之间又相互牵制,使得复合材料自修复效果的影响情况变得更加复杂,所有这些因素的影响均可以体现在裂纹界面修复效果的好坏上。若修复后复合材料的整体力学性能相对提高,则自修复效果相对较好。
Brown 等对微胶囊的自修复进行了大量的研究,对影响复合材料修复效率的几个因素进行了探讨,通过对材料的疲劳性能及修复效率研究,表明微胶囊的加入能明显改善环氧基体的韧性,通过优化微胶囊和固化剂的浓度,体系的修复效率超过90%。Kessler 等利用聚脲甲醛包覆DCPD 制备了微胶囊,初步研究了E - 玻纤/环氧树脂复合材料的自修复情况,裂纹修复效率可达67%。研究表明微胶囊的直径对断裂强度有着至关重要的影响,在失效之前,越小的胶囊就能够支持越大的载荷。White 小组通过对各种影响参数的深入探讨,得出具有参考价值的结果: ①在使用催化剂的自修复体系中,将催化剂采用微胶囊包覆后,在同样修复效率下,催化剂用量可降低90%; ②通过调控反应搅拌转速和采用超声分散,可得到直径范围为0. 3 ~ 300 μm 的微胶囊; ③对于微胶囊含量在0 ~ 20%的体系,当微胶囊含量相同时,微胶囊传递到裂痕处的修复剂量与微胶囊的直径成正比,并且随着微胶囊含量的增加,自修复效率增加; ④当裂痕较小时,对于平均直径约为30 μm 的微胶囊,要得到较好的修复效率,其含量 不能低于1. 5%。该小组通过一系列研究,使自修复材料的修复率有了很大提高。
2. 2 微胶囊体系的选择条件
利用微胶囊技术制备自修复材料时,微胶囊和修复剂体系的选择起着至关重要的作用,为了保证较好的修复效果,将微胶囊应用于聚合物基复合材料中必须满足如下要求: ①体系中微胶囊数量和大小要适中,既要保证有足够的修复剂修复损伤处,又不能影响基材的性能,这就要求微胶囊有较高的包覆率,即使在粒径很小时,仍具有较高的芯含量; ②微胶囊的囊壁厚度和强度必须适当,且囊壁材料和基体材料的力学性能相匹配,既要能承受加工过程中带来的压力,又要在产生裂纹的应力作用下能够适时破裂并释放出修复剂; ③囊壁具有良好的密闭性,保证芯材长期不能渗漏; ④囊壁材料和基体材料两相界面要有良好的相容性,保证裂纹修复后的强度;⑤芯材需具有良好的化学性能和物理性能,不能溶解壁材,在微胶囊破裂之前稳定地保存,⑥芯材要黏度低、易流动,保证从微胶囊释放出来后能够较快渗入裂纹中,同时要蒸汽压比较低,不易从胶囊内向外渗透和挥发,而在释放后和聚合反应之前不会挥发; ⑦芯材具有适当的反应活性,应在环境温度下迅速发生聚合反应修复裂纹面,修复剂聚合反应必须在其挥发或被环氧树脂基体吸收或是发生其他次级反应之前进行,但反应也不能太快,否则修复剂会在微裂纹未被完全填充前便交联固化,导致修复剂不能扩散至损伤面,使裂纹面不能有效愈合; ⑧芯材在聚合后体积收缩小,避免产生新的应力裂纹,并且修复剂聚合后的材料性能应优于或接近基体材料性能,对复合材料的整体性能应尽可能最大限度恢复,不应给复合材料基体带来不利的影响; ⑨微胶囊的制备方法简单,能够批量生产。
由此可见,制备自修复复合材料体系其组成要求是较为严格的,而将微胶囊自修复技术应用到防腐涂层中,则需要更苛刻的条件。将微胶囊应用到涂料中,除了以上条件外,还要求壁材的稳定性,不能被涂料中的溶剂所溶解,要考虑微胶囊在基材中的分布,不能造成微胶囊直接与底材接触,影响涂层的附着力,也不能因分布不均对涂层本身的性能造成影响。同时受涂层厚度的限制,对微胶囊的大小还有更严格的要求。
3 自修复防腐涂层的研究进展及存在问题
3. 1 腐蚀抑制剂体系研究及存在问题
涂料防腐蚀主要依靠涂层屏蔽、金属表面钝化( 如红丹、铬酸盐及磷酸盐等防腐颜料与金属表面作用产生钝化层) 、富锌涂料的阴极保护以及缓蚀剂等基本原理。直接将腐蚀抑制剂添加到涂层中会导致聚合物材料性能的下降,并容易由于腐蚀抑制剂的挥发渗漏而失效。自修复防腐涂料可通过将腐蚀抑制剂埋于体系中,通过对环境条件变化的刺激响应释放抑制剂或修复剂,实现防腐目的。
由于化学腐蚀过程大都伴随着pH 的变化,Zheludekevich等和Shchukin 等采用层层组装( layer - by - layer assembly)方法,制备了以纳米SiO2粒子为核心,外层沉积包含防腐 剂苯并三唑( benzotriazole) 的多层聚合电解质的纳米活性单元( SiO2 /PEI /PSS /benzotriazole /PSS /benzotriazole) 。当腐蚀发生时,由于pH 的变化,引起活性单元聚电解质层的结构和渗透性改变,释放出苯并三唑,在金属表面形成吸附层,使金属表面钝化,有效地阻止金属腐蚀。他们还用类似的方法分别制备了以高岭土和多孔纳米TiO2粒子为核心的吸附抑制剂,以及表层沉积聚电解质层的活性单元。Abdullayev采用真空吸附的方法,将腐蚀抑制剂苯并三唑吸附到高岭土中空纳米管内,应用于防腐涂层,并对抑制剂的释放速率进行了研究。Kumar采用原位乳液聚合和超声技术,制备了以聚脲- 甲醛( PMU) 为囊壁材料,包含不同类型腐蚀抑制剂的微胶囊,并应用到不同的涂料体系,探讨了不同粒径的微胶囊在几种涂料体系中的稳定性以及当微胶囊受到机械损伤破裂时腐蚀抑制剂的释放能力。另外,试验还表明微胶囊较好的添加方式是先在底材上涂一层底漆,10 ~ 20 min 后添加一层微胶囊,再喷涂一层底漆和面漆,形成“三明治”式结构,这样不但有利于修复效率的提高,而且可以增强粘接涂层的附着力。Sauvant - Moynot采用反相乳液中界面聚合的方法制备了包含MgSO4的微胶囊,通过阴极保护原理实现防腐作用。
Mehta 等通过实验对自修复防腐粘接涂层进行了评价,将包覆有防腐剂的微胶囊加入到EP 底漆中,涂于钢制品表面,再涂一层PU 面漆制得样板; 将样板暴露于天然热带海岸环境中,并对其防腐蚀效果进行测定。结果表明: 当含胶囊的粘接涂层被破坏( 如划伤) 时,微胶囊破裂并释放出活性成分于损坏区域,阻碍了电化学电池的形成,有效减小了金属氧化速率。但这些自修复涂料是依靠金属表面钝化、阴极保护和缓蚀剂作用防止腐蚀蔓延,并达到临时性的保护,而涂层裂痕本身不能被修复,因此难以实现长期保护的目标。所以,严格意义上讲还不是真正的自修复涂料。
3. 2 反应型修复剂体系研究及存在问题
防腐涂层自修复的核心是成膜物在涂层裂缝时能自动流出、填充并固化后形成相对平整并有良好屏蔽性的修复涂层。
至今将微胶囊技术应用在防腐自修复涂层中的研究工作主要是体现在不同的修复剂体系,在近期的报道中,Cho 等利用原位乳液聚合方法制备了以聚氨酯( PU) 为囊壁,以溶解于氯苯的有机锡催化剂( DMDNT) 为囊芯的微胶囊,植入环氧乙烯基酯基体中,同时,利用相分离作用,将修复剂端羟基聚二甲基硅氧烷( HOPDMS) 和聚二乙氧基硅氧烷( PDES) 以液滴的形式分散在基体材料中,当微胶囊破裂时,释放出的催化剂及体系中的胺固化剂会引发聚硅氧烷的缩聚,实现涂层自修复。但该体系存在明显的不足,分散在基体中的硅氧烷极易与基材发生反应,自修复效率较低。尽管将硅氧烷用聚脲-甲醛( PMU) 包覆,但由于室温下催化剂的活性大大降低,修复效率并不理想。其后又合成了一种催化剂Si[OSn ( n -C4H9)2OOCCH3]4( TKAS) 代替DMDNT,使修复效率有了一定改善。Suryanarayana 等采用同样的技术方法制备了包含亚麻子油的PMU 微胶囊,并应用于无溶剂环氧防腐涂料,微胶囊破裂后释放到体系中的亚麻子油被空气中的氧气氧化,在 裂纹处形成连续的膜,实现自修复防腐功能。Yuan 等研究了以三聚氰胺- 甲醛为壁材包覆环氧树脂和硫醇固化剂体系,通过原位乳液聚合制备了平均粒径为93 μm 左右的微胶囊,得到了较高的修复强度。邢瑞英等设计了一种以高沸点反应性有机硅系列物质作为囊芯、聚脲甲醛树脂为囊壁的微胶囊,平均粒径在123 μm 左右。利用高沸点有机硅分子链上的乙烯基的反应活性,添加一些光敏剂,使其在受到外力破坏时囊芯材料溢出并在紫外环境下固化,实现有机硅涂层的自修复。但是,这些体系中都存在着共同的问题: 一是微胶囊的粒径比较大( 50 ~ 400 μm) ,只能应用在较厚的涂层中,而且释放修复剂和催化剂以后的微胶囊会塌陷,导致新的问题产生; 二是较大粒径的微胶囊限制了其在涂层中的加入量,使得微胶囊在涂层中的分布难以形成连续排列,而由于裂痕通常只发生在涂层表面,含有修复剂的活性单元不能在裂痕处破裂,无法提供修复剂。
随着微胶囊技术的进展,微胶囊粒径逐渐由几百微米缩小至几十微米,包覆率也逐步提高。Yuan 等以原位乳液聚合方法制备了聚脲- 甲醛分别包覆环氧树脂和固化剂的微胶囊,粒径在10 ~ 60 μm,并探讨了不同型号的环氧树脂和固化剂对修复效率和速率的影响。为了提高自修复效率,Xiao等探讨采用新的固化体系,利用紫外光诱导乳液界面聚合方法制备了以聚脲甲醛分别包覆环氧树脂和固化剂( C2H5)2O·BF3的微胶囊,粒径在5 ~ 45 μm,虽然该体系室温固化速率较快,但由于修复剂环氧树脂的流动性差,无法保证提供足够量的修复剂。
4 自修复涂层的研究方向
尽管对自修复聚合物材料和聚合物涂层制备方法的研究已取得较大进展,但由于自修复组分在长期或多次使用后终将枯竭,其使用寿命是有限的,其与生物的自愈合功能存在本质的区别,因为生物具有新陈代谢能力,可源源不断地产生自修复成分。到目前为止,人们还没有制备出这样一种材料体系,使修复剂能够长期稳定贮存在涂层中,一旦需要便能够及时送达并能反复实现自修复,避免腐蚀的发生; 另一方面对聚合物涂层自修复机理以及微导管传输机理的研究还很少。目前国内外研究人员在这方面已开始了一系列探索,然而尚不能实现真正意义上的自愈合。目前的主要技术途径是尽可能地在自修复涂层中增大自修复组分的容量,并尽可能地将它们形成类似微血管循环通路,达到及时补充和充分利用的目标。近期国外研究的主要技术途径有2 种: 一是采用内部封存修复剂的中空纤维管层压排列在涂层中,形成修复剂供应的连续通道。Trask 等采用层压法将分别封存环氧树脂和固化剂的中空玻璃管及碳纤维管排列在基体材料中,研究了不同的排列方式对修复效果的影响。Bleay 等采用外径15 μm、内径5 μm 的中空玻璃纤维,内部封存修复剂异氰酸酯或环氧树脂,但是由于异氰酸酯的固化速率比扩散速率快,无法提供裂痕充分修复所需的供给量,对于环氧树脂则需要大量溶剂稀释保证其流动性,而大量溶剂的存在会导致固化时形成气泡,影响涂层强度。同时,由于中空纤维的空心率和修复剂的充填率不是很高,自修复效率无法保证,修复剂的充填和封存以及破裂后的再封存等许多问题还有待探讨; 二是采用印刷电路版( direct - write assembly) 技术,将自修复成分在涂层中生成互通三维结构,尽可能地将它们形成类似微导管循环通路。不过这种技术还存在许多问题,自修复效率只有38%,低于微胶囊技术,而且加工方法非常复杂,其可行性和实用性尚待商榷。
自修复涂料可用于导电涂层、耐擦伤涂层以及在需要长寿命、难以维修保养且处于严酷腐蚀环境的防腐涂层,如风能发电机的塔身、叶片,海洋钻井平台,船舶、铁路、桥梁、航天航空器件等。开发自修复涂料具有巨大的经济效益和发展空间,作为21 世纪初开发的新材料和新技术,自修复涂料在重防腐、建筑塑料复合材料等领域才刚刚起步,其研究涉及高分子化学、高分子物理、材料学、胶体科学和仿生学等领域,是一个典型的跨学科难题,尚存在许多问题,需要开展大量的基础研究,如微胶囊壳的断裂机理、微胶囊的机械性能、微胶囊在基体中的分布特性、微胶囊与基体材料性能的匹配、修复剂的扩散方式、流动性和愈合强度、材料多次愈合的可行性等,特别是关于材料如何自动感知损伤的萌芽和形成,然后触发相应的愈合机制的课题。上述难题的解决,将极大推动相关学科的发展,并将催生崭新的智能材料,使得高分子材料及智能涂料的研究和应用进入一个全新的阶段。
更多关于材料方面、材料腐蚀控制、材料科普等方面的国内外最新动态,我们网站会不断更新。希望大家一直关注中国腐蚀与防护网http://www.ecorr.org
责任编辑:王元
《中国腐蚀与防护网电子期刊》征订启事
投稿联系:编辑部
电话:010-62313558-806
邮箱:fsfhzy666@163.com
中国腐蚀与防护网官方 QQ群:140808414
免责声明:本网站所转载的文字、图片与视频资料版权归原创作者所有,如果涉及侵权,请第一时间联系本网删除。
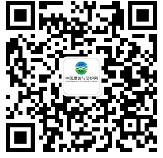
官方微信
《中国腐蚀与防护网电子期刊》征订启事
- 投稿联系:编辑部
- 电话:010-62313558-806
- 邮箱:fsfhzy666@163.com
- 中国腐蚀与防护网官方QQ群:140808414