在飞行过程中,飞机遭受雷击的事件在国内外时有发生。飞机遭雷击后,闪电产生强大的电流,形成电磁场、光辐射、冲击波和电弧,严重影响飞行安全。随着先进复合材料在飞机上的广泛运用,以及电子电气系统集成度及重要性的不断提高,航空界对闪电防护的重视程度逐渐加深,相关科学研究的范围和复杂程度也不断加大,特别是全复合材料飞机的闪电防护。因此,确保通用飞机具备良好有效的闪电防护设计,已成为保证飞机可靠性和安全性的一项必不可少的工作。
国内外研究现状与发展趋势
国外研究趋势和现状
早期的飞机采用木制外壳和金属操纵线缆,机体结构无法作为闪电电流的通路,飞机被闪电击中时,其结构和操纵线缆通常会发生起火或解体,飞行员可能被流经金属脚蹬或操纵杆的电流击伤。有时,燃油油箱被击中后,甚至有可能起火爆炸,造成灾难性的事故。二战以后,金属飞机成为主流,因为金属机体具有良好的导电性,使得因闪电而导致的灾难性事故大幅减少。但近年来,低导通性复合材料结构的使用,又对闪电防护提出了新的要求。2000 年前后,SAE 先后发布了一系列飞机HIRF 和闪电防护的指导性文件,规范了航空业内电磁兼容/ 闪电防护设计,通用飞机的相关设计工作变得有规可循。图1 为飞机雷电防护金属丝网。
对国外成熟的飞机设计团队而言,金属飞机的闪电防护设计理论和方法已经不具备太大的挑战性。随着技术的进步和材料的发展,国外各通用飞机制造商推出了多款成功适航取证的全复合材料或大部分采用复合材料结构的飞机机型。这些飞机主要采用在机体外层设置金属防护层,在机体内部构建金属搭接网络的方式,来实现电磁环境效应和闪电防护。
同时,国外还有一些专门从事飞机闪电防护的公司和机构(见表1),参与了较多型号全复合材料通用飞机的闪电防护工作,在复合材料通用飞机防雷击方面的试验数据和技术积累已较为丰富,能提供飞机闪电防护知识培训、信息咨询、设计分析、仿真试验等较为完备的闪电防护技术服务项目,并可协助完成飞机闪电防护相关的适航取证工作。
国内研究现状
我国陆续制定了一些闪电防护设计的指导文件和军用标准,如GJB1389 等,但主要以提出要求为主,缺乏具体的设计指南。直到最近15 年,国内航空产业吸收了国外诸多先进的设计规范和流程,制定了一些飞机闪电防护标准。但因为标准制定的主要来源是对国外标准的直接引用或汇总引用,自身缺乏试验数据基础,因此,仍与国外有着较大的差距。
闪电防护的研究与试验紧密相关,而试验正是我国通用飞机产业的弱项。一方面,国外对我国长期实行的软件、硬件设备封锁,导致国内在试验数据和经验积累比国外先进发达国家更少,试验手段和设施也比较简陋。另一方面,由于经费的限制,为规避漫长的试验周期和高昂的试验费用,国内航空业的设计人员更倾向于使用电脑软件仿真的方法来开展分析验证。同时,国内涉及的飞机设计人员大多数不是专业的闪电防护/ 电磁环境效应研究人员,往往仅从自己专业的角度来考虑,导致忽视或低估了闪电防护的重要性。
此外,国内自行研发的绝大多数飞机型号采用传统金属结构。复合材料在国内主要作为功能性材料,制造形状复杂的零组件,如雷达罩、天线口盖、翼尖、整流包皮、背鳍等,很少用于主结构。这些非主结构零部件的重要性相对较低,即使被闪电破坏,也不致于造成灾难性的后果。因此,在我国通用航空领域,复合材料的闪电防护长期处于“不急迫”的边缘化状态。与国外先进水平相比,我国对全复合材料通用飞机闪电防护设计和验证技术的基础比较薄弱,研究数据极为欠缺,极大地制约了我国新型先进复合材料通用飞机的研制。
适航法规要求
目前,全复合材料设计制造主要运用于小型通用飞机,在CCAR23、FAR23 中,对电磁环境效应和闪电防护的适航要求如表2。
从表2 中不难看出,闪电防护和高强辐射场的要求已明确提出。包括飞机机体结构、燃油系统油箱、航电系统、电子电气系统以及设备系统的安装等,在进行闪电防护设计时,均需进行考虑。
设计方法和验证思路
传统金属飞机天然具备良好的导电性,有利于释放闪电电流;而复合材料飞机主要使用碳纤维复合材料(CFRP)和玻璃纤维复合材料(GFRP)。它们独特的导电性、电化学腐蚀性和材料多样性,必须额外进行闪电防护设计和验证。此外,复合材料飞机往往根据设计要求需要混用多种材料。例如,翼梁等主承载结构采用碳纤维,雷达罩、天线罩等结构采用透波性好的玻璃纤维,机身内部根据强度需要增设金属框架结构等。正因为这些特殊性,复合材料飞机的闪电防护设计和验证,是现代航空研究人员面临的一项挑战。
闪电防护设计流程
全复合材料飞机闪电防护设计和验证流程与金属飞机大致相同,如图2 所示。从图中可以看出,闪电防护设计步骤一般分为:前期规划、雷电分区、确定防护要求、防护设计以及后期符合性验证。也可以看出,在闪电防护设计中,涉及专业众多,适航部门、研发单位和专业闪电设计公司紧密联系,贯穿于飞机设计制造和试验的全过程。
闪电分区方法
闪电分区是闪电直接效应防护设计的重要依据。
按照SAE ARP 5414,根据闪电附着的可能性,可将飞机表面划分为3 个区域。每个区域具有不同的闪电附着特性和传导特性。
区域1:初始电击附着其上面(进口或出口)可能性很大的飞机表面。
区域2 :电击放电被气流从区域1 的初始附着点吹过来、在其上面扫掠的可能性很大的飞机表面。
区域3 :除了区域1 和区域2 以外的所有飞机表面为区域3。在区域3,放电电弧直接附着的可能性很小,但它可能在某对初始闪电附着点或扫掠冲击附着之间传导很大的雷电流。
按照放电长时间悬停在飞机表面的可能性大小,区域1 又进一步分为A 区、B 区和C 区,区域2 划分为A区和B 区。A 区、C 区是电弧在它上面长时间悬停可能性较小的区域(C 区电流幅值小于A 区)。B 区是电弧在它上面长时间悬停可能性较大的区域。
典型的CCAR23/FAR23 部,单发螺旋桨飞机雷电分区如图3。
设计方法
机体结构
传统金属结构飞机电磁环境效应和闪电防护主要的设计方法在于对机体结构进行良好的电搭接(包括闪电防护电搭接、确保设备良好电磁兼容性的电搭接,以及静电释放电搭接),使所有零部件成为等势体。飞机在遭受闪电和高强辐射场干扰时,可以将干扰源(例如闪电电流)快速导离,或起到良好的屏蔽作用。一般来说,金属飞机电磁环境效应和闪电防护设计方法大同小异,只需要进行少量的设计更改,即可满足设计要求。复合材料机体进行模拟雷击试验发现,在没有雷击防护层的情况下,在经受一定的电流后就产生严重损伤,因此,全复合材料的飞机必须进行雷击防护。由于不同类型的复合材料导电性能和介电性能的变化范围较大,闪电防护方法也有很大的差异,主要表现为:
(1)金属箔。铝箔胶结到复合材料部件的外表面上,形成用于雷击防护的铝箔层,使其经受雷击试验而复合材料无损伤。同时,在铝箔和复合材料之间放上高绝缘层能增加防雷击作用并能防止复合材料基体被烧焦或蒸发。使用这种防护层时,对飞机结构表面要经常检查和及时修复。
箔条垂直于气流方向配置在复合材料制件表面上,雷击试验表明,它具有铝箔全覆盖复合材料表面的防雷击效果。但在雷击接触的箔条与其相邻箔条之间发生电弧,在箔条边缘处可见到基体被烧焦的痕迹,雷击接触点也有蒸发现象。使用中也要经常检查和维护。
(2)喷涂铝。喷涂铝的方法有两种:火焰喷涂和等离子喷涂。两种方法喷涂的涂层防雷击效能相近。为提高喷涂铝层的防雷击效果,可在复合材料制件表面上喷涂铝的区域先铺上一层玻璃布(在制造复合材料制件时,表层玻璃布与碳纤维层一起铺叠、一次固化成形),保护制件不接触电荷并保护喷涂铝层不被电化腐蚀。
(3)金属丝网。使用标准纺织工艺将金属丝织成布或针织品,主要是铝丝网和铜丝网。铝丝网在模拟雷击放电试验中损伤最小,具有经受多次雷击的能力,同时能传输很高的电荷量,而且易制成形状复杂的曲面,并可简单地利用复合材料基体作为胶粘剂与零件一次固化成形。铜网单位面积重量比铝网重,但铜网构成的闪电通路优于铝网,防雷击能力、抗雷击损伤能力等均强于铝网。由于碳纤维复合材料结构与铝合金会发生电化学腐蚀,国内外目前多数复合材料飞机均采用铜网。
(4)防雷击导电涂层。在构件外表面涂导电涂层,降低构件表面电阻。总之,全复合材料飞机电磁环境效应和闪电防护,应当根据复合材料本身特性的不同,针对不同的材料和闪电分区,采用不同的防护措施。
燃油系统
燃油系统闪电防护设计的目标在于防止任何由闪电直接或间接效应引发的燃油油箱起火。一般来说,CCAR23/FAR23 部飞机主要采用“消除点火源”的办法来进行燃油系统的闪电防护(AC20-53B 推荐方法)。在型号设计中,一是根据闪电分区合理布置通气孔等零部件的位置,降低其被闪电击中的概率。二是在机翼油箱外蒙皮分别敷设不同厚度的金属铜网,可避免碳纤维复合材料被闪电击穿,点燃燃油蒸汽。三是在油箱内部敷设玻璃纤维绝缘层,或其他材料的绝缘隔断层,防止油箱内部碳纤维结构之间因电势差引发跳火花。四是油箱口盖外蒙皮敷设金属铜网,使其在被闪电击中后,具备传导释放电流的能力。五是在油箱口盖的金属紧固件(如托板螺母)涂抹密封胶(如图4),避免闪电击中紧固件后,通过紧固件传入油箱内部,同时避免紧固件相互间跳火花。
电子电气系统
飞机的电子电气设备主要安装在机体内部,防护重点是考虑闪电间接效应的影响(如图5、6)。
(1)所有天线,通过紧固件,使天线底部与飞机外蒙皮的金属铜网良好接触。
(2)机体内部构建电搭接网络,使用薄铜带敷设搭接路线,各设备外壳搭接到薄铜带上,使整个电子电气系统的设备实现外壳等电势。
(3)对于重要的电子电气设备,或位于易受雷击的闪电分区的电子电气设备,采用闪电抑制器,避免闪电间接效应引起的浪涌电压/ 电流对设备造成伤害。
闪电防护验证
闪电直接效应防护验证
由于飞机外形的不规则性及机械结构与电气电子系统的多样性与复杂性,电场与磁场的精确解非常困难,闪电防护试验方法是最有效的闪电防护能力的验证方法,主要包括:
(1)碳纤维复合材料试片试验。试验方法为:制造多件不同厚度的碳纤维复合材料试验板(500mm×500mm),敷设不同厚度的金属铜网,利用不同强度的模拟闪电对其进行轰击。试验完成后,通过超声波探伤,评估闪电对试片的影响。通过对试验数据的评估分析,得出各闪电分区所需的最低碳纤维敷设厚度,以及最低的金属铜网敷设厚度。
(2)按机翼现有油箱设计做出1:1 试验件。按照SAE 5416 中所规定的步骤和方法,对其进行模拟闪电轰击。试验后检查分析试验件受损情况,以评估燃油系统设计的安全性。
闪电间接效应防护验证
通用飞机闪电间接效应试验的基本思路为:使用经过缩比的模拟闪电电流注入飞机,通过安装在飞机内部或附近的仪器测量和记录所选线缆中感生的电压和电流的瞬态电平,然后按缩比比例线性放大,以此获得所测线缆中的实际瞬态电平(ATL)。试验得到ATL 后,与设备的瞬态设计电平(ETDL)相比较。一般来说,ATL 应小于ETDL,并留有一定的裕度,以补偿试验中的不确定性。否则,需要视情况采取措施,优化完善防护设计。
结论
复合材料飞机闪电防护设计,是保证飞机可靠性和安全性的重要组成部分。在进行设计时,前期应当仔细做好规划,根据飞机闪电分区特点以及材料特性确定防护要求和符合性验证要求,并与适航部门交流,以试验为基础,使飞机闪电防护设计满足规范要求。
更多关于材料方面、材料腐蚀控制、材料科普等方面的国内外最新动态,我们网站会不断更新。希望大家一直关注中国腐蚀与防护网http://www.ecorr.org
责任编辑:庞雪洁
投稿联系:编辑部
电话:010-62313558-806
中国腐蚀与防护网官方 QQ群:140808414
免责声明:本网站所转载的文字、图片与视频资料版权归原创作者所有,如果涉及侵权,请第一时间联系本网删除。
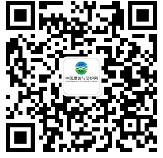
官方微信
《中国腐蚀与防护网电子期刊》征订启事
- 投稿联系:编辑部
- 电话:010-62316606-806
- 邮箱:fsfhzy666@163.com
- 中国腐蚀与防护网官方QQ群:140808414