简单说,高温合金是一种专门为高温环境“量身定做”的金属材料,它能在高温(通常600℃以上)、高压、高应力的恶劣环境下长期工作而不变形、不生锈、不“累趴”。 它常由镍、铁或钴做“底子”,再加入一些“助攻元素”如铬、钼、钨、铝、钛等,就像调制超强合金饮料。这种材料特别适合用在发动机、燃气轮机、核电装置、火箭喷嘴等“高热”场合。 它们有三大“超能力”: ✅ 耐高温:不怕热,能在1000℃以上“工作”。 ✅ 抗氧化腐蚀:即使高温下有空气或化学物质,也不容易生锈。 ✅ 耐疲劳 & 抗蠕变:经得起反复拉扯、不容易慢慢变形。 可以说,凡是高温的地方,就有它的身影: 航空航天:发动机涡轮叶片、涡轮盘 能源设备:燃气轮机、核电站燃料壳 汽车工业:涡轮增压器、排气阀座 冶金与化工:高温炉衬、反应釜部件 它是现代工业“顶流选手”之一。 高温合金制备工艺 在生产和选用高温合金时,需参考权威标准。常见的标准如下: GB/T 14992-2005《高温合金分类》 GB/T 14993-2011《高温合金热处理工艺规范》 GB/T 14994-2011《高温合金力学性能试验方法》 HB/Z 140《高温合金材料性能评价方法》 HB 5123《航空用高温合金铸件技术要求》 ASTM B637(镍基合金锻材) AMS 5662/5663(航空用镍基合金Inconel 718标准) 这些标准就像高温合金的“体检表”,确保它们符合严苛的工业应用要求。 近年来,高温合金领域取得了多方面的突破,主要体现在以下几个方面:1)合金体系持续升级:新一代镍基、钴基及高熵合金不断涌现,性能指标全面提升,满足更高温、更苛刻工况需求。2)材料设计智能化:借助机器学习、高通量实验和热力学计算,实现合金成分和组织结构的高效优化。3)先进制备技术成熟化:粉末冶金、定向凝固、单晶工艺及增材制造(3D 打印)等关键技术快速发展,提升材料成形能力与组织控制精度。4)工程应用加速落地:多种新型高温合金已实现工程化应用,特别是在航空发动机核心部件中的国产替代进展显著。5)多性能协同提升:强度、蠕变、抗氧化性、加工性等关键性能实现协同优化,推动高温合金向更高可靠性与更长服役寿命发展。 1)第四代镍基单晶高温合金 利用机器学习和多目标优化算法,四川大学研究团队通过高通量实验、热力学计算和多目标优化策略,实现了镍基高温合金的成分优化。例如,通过调整固溶温度和时间,优化合金的微观组织,使其γ′相体积分数、固溶温度等参数达到设计目标,显著提高了材料的综合性能。 2)粉末冶金高温合金FGH4095与FGH4096 3)增材制造专用无裂纹镍基合金 1)Co-Al-W基高温合金 2)轻质高熵钴基合金 美国橡树岭国家实验室(ORNL)通过七种元素掺杂的铌基复杂成分合金(含Co、Ni、Cr等),结合电子束熔融工艺(EBM),实现1316℃下无裂纹成型,密度较传统镍基合金降低15%,应用于燃气轮机涡轮叶片的快速制造。 2)定向凝固与单晶技术迭代 第四代单晶合金(如DD22)含Re(5%-6%)和Ru(3%-4%),承温能力较第三代提升25℃,在1100℃下的持久强度达到国际领先水平,已装备于某型军用发动机高压涡轮叶片。 高温合金设计长期以来面临“试错周期长、成本高、变量多”的难题。传统方法往往依赖经验+反复实验。AI技术尤其是机器学习(ML)、深度学习(DL)、强化学习(RL)等,能够: 精准预测性能(如屈服强度、抗氧化性、蠕变寿命) 自动筛选成分组合 优化热处理和制造路径 降低研发成本,加快研发周期 AI通过机器学习和遗传算法,实现成分空间的高效探索。例如: 多目标遗传算法:北京科技大学研究团队将镍基高温合金的γ′相体积分数、固溶温度、TCP相含量等参数作为目标,结合热力学数据和机器学习模型,筛选出综合性能优异的候选成分(如C1和C2合金,其蠕变寿命潜力优于传统K438合金)。 逐层筛选策略:东北大学研究团队在钴基高温合金设计中,AI先通过分类模型排除有害相,再利用回归模型优化γ′相溶解温度、密度等参数,最终从36万种候选成分中锁定6种高性能合金。 逆向设计:中国航发团队结合热力学计算与机器学习,逆向设计出满足Vγ′≥60%、Tγ′≥1300℃等要求的8种镍基合金,实验验证其γ′相体积分数达80%以上。 AI通过深度学习解析微观组织与性能关系: γ′相特征预测:北京航空航天大学基于神经网络模型,可高精度预测晶格错配度、γ′相尺寸分布等参数,误差较传统方法降低30%以上。 力学性能关联模型:中国航发研究团队针对K4169合金,多层感知器(MLP)模型通过70组微观结构数据,预测室温与高温拉伸强度的均方误差仅为0.17和0.14,显著优于传统算法。 AI替代部分实验环节,缩短研发周期: 抗氧化性能预测:梯度提升决策树(GBDT)模型通过合成数据集预测难熔高熵合金的氧化质量增加量,显著减少了广泛的实验测试需求。 热处理参数优化:日本国立材料科学研究所和名古屋大学研究团队利用蒙特卡洛树搜索(MCTS)设计非等温时效处理方案,从35亿种组合中筛选出110种最优方案,可产生比传统等温时效过程更好的结果。 高通量计算融合:美国橡树岭国家实验室结合CALPHAD热力学数据库与机器学习,生成1100万数据点支撑的合金设计流程,加速蠕变性能预测。 当前,AI在高温合金设计中的工业化应用正加速推进,多个项目已取得切实成果,显著提升了研发效率和材料性能水平。例如,创材深造公司构建了高通量实验平台与AI算法系统,将原本需要5年完成的材料研发周期压缩至半年内成功推出3到5款新材料,大幅降低成本。北京科技大学团队融合机器学习、遗传算法与聚类分析,在2024年实现了高温合金的高效智能设计。中国航发北京航空材料研究院通过热力学计算与机器学习相结合,开展镍基高温合金的逆向设计,实现精确成分优化以满足极端高温工况。国际方面,宾夕法尼亚州立大学利用生成对抗网络(GAN)设计出在2000℃以上仍具高强度的高熵合金,已应用于涡轮叶片和火箭推进系统;昭和电工与东京大学合作开发的神经网络模型大幅提升了铝合金在高温下的性能预测效率;日本国立材料科学研究所则运用AI优化热处理工艺,显著提高了镍铝合金的高温强度。这些案例共同展示了AI在材料成分筛选、性能预测、热处理优化和实验替代等方面的全面能力,标志着高温合金设计正从传统经验驱动向数据驱动、模型驱动的智能时代迈进。 总结:高温合金,强者之材,智造未来 高温合金,作为航空航天、燃气轮机、核能装置等高端装备中的“关键材料”,其本质是一类能在极端高温、高应力、强腐蚀环境下长期稳定工作的金属合金。它不但要“扛得住热”,还要“撑得住压”“顶得住疲劳”,因此被誉为“材料皇冠上的明珠”。 过去几十年里,高温合金从第一代镍基铸造合金发展到第四代单晶合金,性能不断跃升;同时,钴基、高熵、粉末冶金合金、3D打印专用合金等新体系也快速崛起,正在突破更多极限。尤其是近年来,随着新一代发动机、极端能源系统和高超声速技术的兴起,对材料的性能提出了前所未有的挑战,也推动了新材料的集中爆发。更值得关注的是,人工智能(AI)技术正为高温合金设计插上“加速器”的翅膀。从材料成分的智能筛选、组织结构的精准预测,到性能模拟、热处理优化,再到3D打印的过程控制,AI已经渗透到研发的每一个环节。 无论是研究机构,还是产业一线,AI都显著提升了高温合金的设计效率与创新速度: 材料研发周期从“数年”压缩到“几个月”; 高熵、轻质、无裂纹等多性能合金不断问世; 实验数据与模型预测形成智能闭环,极大降低试错成本。 这一切都说明:高温合金正从“经验时代”进入“智能时代”。 未来,随着AI、数字孪生、多尺度建模与自动化实验平台的进一步融合,我们将迎来更高强度、更轻量化、更可持续的新一代高温合金材料。它们不仅将服务于更快的飞机、更耐烧的发动机和更持久的能源系统,也将成为引领材料科学与制造技术革命的“硬核力量”。
✅ 国内标准(GB/“国标”):
✅ 航空工业标准(HB):
✅ 国际标准:
一、镍基高温合金的创新
浙江大学张泽院士团队研发的第四代镍基单晶合金,通过添加Ru(钌)元素优化γ/γ'相结构,在1100℃/137MPa条件下的持久寿命超过500小时,显著提升涡轮叶片承温能力。该合金已应用于某型航空发动机双冷涡轮叶片,解决了高温下组织稳定性问题,成为国产高推重比发动机的核心材料。
作为第二代粉末高温合金,FGH4096在750℃下的抗裂纹扩展能力较FGH4095提高一倍,尽管强度降低10%,但其损伤容限特性使其成为先进发动机涡轮盘的首选材料。两者在WS-9、WZ-8等发动机中实现规模化应用,支撑了我国航空发动机涡轮盘的国产化进程。
华中科技大学开发的GH3536改进型合金(成分:Ni-Mo-Cr-W-Co-Fe),通过优化Mo(10.5%-11%)和Cr(24.5%-25.3%)比例,显著减少激光选区熔化成型过程中的微裂纹,抗拉强度提升20%以上,已用于复杂结构燃烧室部件的3D打印。二、钴基高温合金的突破
西北工业大学开发的Co-9Al-10W-0.1B合金,在900℃时效后γ'相体积分数超过70%,时效硬度高于传统钴基合金DZ40M和镍基合金Waspaloy,其固/液相线温度较镍基合金高100-150℃,适用于导向器叶片。但该合金仍面临γ'相高温稳定性不足(易分解为D019相)和密度偏高(~9.2 g/cm³)的挑战。
俄罗斯开发的铌-钛-铬三元合金(如Nb-Ti-Cr系),在1000℃下无需冷却即可稳定工作,抗氧化性能较传统铌钛合金提升18倍,已试用于航空发动机燃烧室衬套。三、前沿制备技术与新型材料体系
1)3D打印轻质无裂纹高温合金
AI在高温合金设计中的核心应用方向主要集中在以下几个方面:
1. 成分优化与多目标设计
2. 微观结构预测与组织分析
3. 性能模拟与实验加速
免责声明:本网站所转载的文字、图片与视频资料版权归原创作者所有,如果涉及侵权,请第一时间联系本网删除。
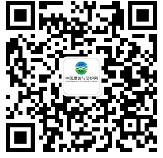
官方微信
《腐蚀与防护网电子期刊》征订启事
- 投稿联系:编辑部
- 电话:010-62316606
- 邮箱:fsfhzy666@163.com
- 腐蚀与防护网官方QQ群:140808414