12.1 发展该产业的重要性和紧迫性
进入 21 世纪以来,我国高速铁路蓬勃发展,已建成“四横四纵”的高速铁路网,现在正在建设覆盖中西部地区“八横八纵”高速铁路网。截至 2019 年,我国高速铁路总里程达 3.5 万千米,居世界第一位。“复兴号”动车组已经达到 350km/h 的运行速度,居于世界首位。
在高速铁路快速发展的同时,我国自主研发了大量的核心技术,目前已经系统掌握了各种复杂地质及气候条件下高铁建造的成套技术,全面掌握了时速 200 ~ 250km、300~ 350km 动车组制造技术。高速铁路不仅是我国经济发展的一大支柱,也带来了巨大的社会效益,对我国区域融合、经济转型都产生了深远的影响。同时,高铁技术是对传统铁路基础的重大突破, 也带动了相关领域综合科学技术能力的发展,反映了一个国家的科技实力和工业水平。
然而,值得注意的是,尽管高速列车国产化在我国基本实现,但其核心的走行系统中高速运转体系的部分关键零部件,例如车轮、车轴和转向架轴承,仍然大量甚至完全依赖进口,在采购、 技术、供货周期与价格上受制于人,成为我国高速列车快速发展的瓶颈。
根据《中国国家铁路集团有限公司 2019 年统计公报》,截至 2019 年底,全国铁路机车拥有量为 2.2 万台,其中,内燃机车 0.80 万台,占 36.9% ;电力机车 1.37 万台,占 63.0%。全国铁路客车拥有量为 7.6 万辆,其中,动车组 3665 标准组、29319 辆。全国铁路货车拥有 量为 87.8 万辆。按照每辆动车组装备 2 个转向架计算,仅动车组就有近 24 万片车轮、12 万 根车轴、几十万套轴承在使用。随着“八横八纵”高铁网的进一步建设,每年新增以及更换车轮、车轴以及转向架轴承的数量将会进一步增加,形成了极大的市场容量。同时,除高铁之外,现在国内 160km/h 以上列车、地铁列车中高速运转体系使用的轴承、车轮和车轴等也大量依赖进口,随着国内各城市地铁建设的加速推进,未来相关市场将会迎来更大的需求。
轨道交通高速运转体系关键零部件主要包括车轮、车轴和轴承等。涉及的关键材料分别 为中碳低合金钢(ER8 等)、低碳合金钢(EA4T 等)和高品质轴承钢(GCr15、20CrNi2Mo 等)。目前除了少量低转速的车轮钢可以实现部分国产化外,高速列车的车轴和运转体系的轴承全部依赖进口。
除市场因素外,车辆高速运转体系使用的关键材料也是高端金属材料的典型代表,其中的轴承钢被称为特钢之王,轴承产业也是国家基础性、战略性产业。我国中长期发展规划战略的实现、制造业强国战略的实施,均需要突破上述关键部件的自主可控制造。同时,高铁 作为中国高端制造的靓丽名片,在对外出口时也不应长期依赖从国外进口关键零部件。
此外,在当前逆全球化趋势和贸易保护主义抬头的国际形势下,在某些极端情况下,上述关键零部件的进口稳定性可能会受到影响,甚至阻碍、限制高铁全行业发展。而这些车辆高速运转体系中的关键零部件的短缺将直接影响高铁的运行,从而给已经习惯于依赖高铁出 行的国人带来出行上的不便,以及极大的心理冲击甚至恐慌,造成不可估量的负面影响。
因此,解决以车轮、车轴和转向架轴承为代表的车辆高速运转体系中关键零部件的国产 化自主可控制造问题,是当前面临的迫切的科技和产业任务。
12.2 产业发展现状及发展态势
12.2.1 车轮用钢
车轮是高速列车运行过程中承受载荷最大的部件,尽管高速列车国产化在我国基本实现, 但高速车轮依然大量依赖进口,这已经成为我国高速列车快速发展的瓶颈。我国铁路网建成之后,高速车轮需求量巨大,达 2.8 万片每年,用钢量约 1 万吨 / 年。而高速车轮服役 2 ~ 3 年就要全部更换一次,预计 2025 年之后,全球每年高速车轮需求量超过 8 万片。我国仅有马钢股份有限公司和太原重工能够批量生产高速车轮,目前能生产适用于中低时速的高速车轮。日本住友、法国 Valdunes、德国 BVV 和意大利 Lucchini 是世界上少数可以批量生产高速车 轮的厂家,几乎垄断了我国高铁的车轮市场。
12.2.1.1 国外车轮钢发展态势
目前只有日本和欧洲少数厂商能够生产高速车轮钢,它们依据的标准分别是日本的 JIS E5402《铁道车辆整体车轮质量要求》和欧洲的 EN13262《铁路规范—轮对和转向架—车轮— 产品要求》。日本的 JIS E5402 标准列出的七大类车轮用钢化学成分见表 12-1。
在车轮制造与性能要求方面,JIS E5402 标准对成型工艺要求比较宽松,除了 SSW 钢车轮仅适用于碾压车轮,其他钢种可同时适用于碾压车轮和铸造车轮。对于车轮的热处理, SSW 钢采用不热处理和轮辋淬回火处理两种工艺,C44GW-C74GW 钢采用正火和轮辋回火处理两种工艺。正火后车轮性能要求:①轮缘位置抗拉强度为 800 ~ 940MPa ;②轮缘边缘冲 击功 AkV 不低于 10J;③轮缘表面硬度为 233 ~ 285HB。淬火后车轮性能指标要求较高,但检 测内容与正火后车轮一致:①轮缘位置抗拉强度为 940 ~ 1140MPa ;②轮缘边缘冲击功 AkV 不低于 10J;③轮缘表面硬度为 277 ~ 341HB。
欧洲 EN13262 标准包含了碳含量不超过 0.60% 的 4 种中碳低合金钢,其化学成分见表 12-2。
在车轮制造与性能要求方面,EN13262 标准只针对碾压并经淬回火热处理的车轮,相比 于日本 JIS E5402 标准,EN13262 对每一种钢提出了不同的性能要求,并增加了冲击韧性和 断裂韧性的要求。由此可见,欧洲标准更加强调车轮的韧性。除了力学指标之外,欧洲标准 对非金属夹杂物、超声波探伤、外形尺寸公差均有严格的要求。总体上看,日本和欧洲车轮 标准在钢的质量水平、尺寸精度要求方面具有共性,而在车轮材料及性能要求上存在较大的 差异。
相比于普通车轮,高速列车动力学条件显著变化,接触应力更加复杂,其安全性主要受 踏面剥离和轮辋裂纹两种失效机制的影响。踏面剥离是车轮在运行过程中由于轮 / 轨滚动接 触疲劳的作用和热机械作用而在踏面局部产生裂纹萌生和金属剥落的现象。国外研究者们通 常把轮轨接触疲劳产生的这种损伤定义为剥落。将由于热损伤产生的这种现象称为剥离。局部接触疲劳导致踏面剥离的原因是车轮轮辋的各种缺陷,包括非金属夹杂物,加工缺陷在轮 轨接触应力作用下萌生裂纹并扩展导致轮辋表面金属剥离。产生踏面剥离的另外一个原因是 热机械交互作用,在车轮制动过程中,由于蠕滑等原因使车轮表面温度急剧升高到奥氏体温度以上,局部产生的奥氏体组织在随后滚动过程中急剧冷却,产生高硬度马氏体“白层”组织;在反复应力作用下马氏体 / 基体界面产生裂纹并导致剥离发生,踏面剥离已成为我国动 车组车轮失效的主要形式,占所有失效原因的 90% 以上。轮辋裂纹的产生是由于车轮表面附近的缺陷,一般是材料中的非金属夹杂物,如 Al2O3、SiO2 等,在周期应力作用下产生疲劳 裂纹,疲劳裂纹扩展基体形成裂纹,由于裂纹起源于车轮内部,很容易形成贯通于整个轮缘 的裂纹,严重威胁了高速列车的行车安全。
国际上通常把运行速度超过 200km/h 的列车称为高速列车,国内外学者的研究结果表明, 运行速度超过 120km/h 后,车轮与钢轨之间的摩擦加剧,并在制动过程中产生大量摩擦热, 加剧了车轮与钢轨因疲劳、剥离等引发的失效问题,给高速列车的安全运行带来极大的隐患。欧洲早期普遍采用 UIC812-3 标准中 R7 钢,R7 钢含碳量在 0.52% 左右,采用 Si、Mn 作为 强化元素,属于中碳系铁素体 - 珠光体钢。1998 年,德国下萨克森州 Eschede 高速列车脱轨, 列车一个车轮轮箍断裂,引起车头车身分离,造成 101 人死亡、81 人受伤。此后,欧洲加大 了对新型高速列车用车轮钢的研究,重点研究在保证材料的强度和硬度降低不大的情况下, 提高车轮钢的韧性。同时研究者提出了改进车轮钢的冶炼工艺,提高材料的洁净度。并提出 了高速车轮钢降碳、微合金化和低碳贝氏体车轮研究新思路。例如,法国 Valdunes 公司对 R7 钢进行了改进,碳含量降低至 0.50% 以下,并严格控制硫和磷的含量,增加微合金化元素 Cr 的含量,同时加入少量的 Al、Cu 合金元素进行强化。另外 20 世纪 80 年代末,英国剑桥大 学 Bhadeshia 教授与英国钢铁公司合作,研制 Fe-0.5C-1.5Si-2.0Mn 贝氏体钢,Bhadeshia 教授 称之为无碳化物贝氏体钢,并对其成分和组织优化;研究中还采用了含碳量 0.04%、0.10%、 0.52% 及 0.77% 四种钢对比,研究结果表明,贝氏体钢有着比珠光体更优良的抗磨损性能。可见,有必要深入对贝氏体钢作为高速车轮材料的研究。
日本早期高速车轮和欧洲车轮在选材上存在较大的差异,日本采用的是高碳碳素钢,代 号 SSW,SSW 钢在强度上远高于欧洲的 R7 钢,但在断裂韧性和抗断裂能力方面明显低于 R7 钢,由此可见日本早期采用的是高强度路线。后来,日本研究者为了提高车轮高速行驶时 抗裂损能力,开发了 V2 钢,将碳含量由 0.65% 降低至 0.55%,并加入 0.18% ~ 0.21% 的 V, 从而使钢的冲击韧性、断裂韧性显著提高,抗裂损性能也得到改善。从日本和欧洲的研究方 向上不难看出,高速车轮钢发展趋势是在保证钢的强度和硬度没有明显降低的情况下减少 C 含量,同时采用微合金化的方法提高韧性,最终提高材料的抗裂损能力。随着冶炼工艺和技 术的改进,材料的洁净度也得到了提高,非金属夹杂物的数量、尺寸和形态得到了优化,对 改善车轮的抗裂损性能有利。
12.2.1.2 国内车轮钢发展态势
国内很早就对高速车轮材料进行研究,1990 年,马钢股份有限公司参考苏联标准研制了 一种含钒微合金化车轮钢。该钢种的各项性能都优于原来的 CL60 钢,铁道部的实验也证明 含 V 钢的实际应用性能优于普通碳素钢。2000 年,马钢股份有限公司技术中心与西安交通大学联合研制了微合金化车轮用钢,用于速度 200km/h 的列车,该钢降低了含碳量,增加了合 金元素的含量,并用 V 进行微合金化。研究表明,新钢种强度、硬度较高,其他各项性能均 比原来钢种优异。2001 年起,钢铁研究总院与马钢股份有限公司合作,系统开展了碳含量对车轮综合性能的影响的研究,在含量 0.7% ~ 0.4% 的范围内研究了不同成分材料的力学性能、 抗滑动摩擦、抗疲劳以及抗接触疲劳性能。试验结果表明,随着碳含量的降低,材料的耐滑 动摩擦性能、耐滚动摩擦性能以及材料的耐接触疲劳性能降低,材料的耐热疲劳性能显著上 升。综合所有结果表明,碳含量在 0.5% 左右可以获得最好的综合性能。根据以上试验结果 并结合欧洲标准 EN13262,马钢股份有限公司设计开发出 CL50A 材质高速车轮钢,并建成 了国内第一条车轮连铸圆坯生产线,该车轮成功运用到秦沈客运专线,试验运行最高速度超 300km/h。2014 年,中国铁路总公司设立重大课题“动车组关键技术自主创新深化研究— 时速 350km 中国标准动车组轮轴设计研究”,马钢股份有限公司开发出一种中碳 Si-V 微合金 化 D2 材质车轮,该钢种抗疲劳性能、抗磨损性能优于进口车轮 30% 以上,该材质车轮现已 在复兴号标准动车组上装配 48 件,完成考核并投入使用,累计里程已超过 120 万千米。
12.2.2 车轴用钢
车轴是列车运行过程中的另一个重要承重零件,它通过过盈连接与车轮组成一个轮对, 列车的整体重量几乎都加载在车轴上,其在运行过程中受力十分复杂。列车车轴基本是按照 无限使用寿命来设计的。但是,即使如此也无法保证车轴在整个使用期间的绝对安全性,高 速行进中的列车,车轴一旦出现问题,将会给人民生命和财产安全造成不可估量的损失。
对于提高车轴的可靠性,世界各国都十分重视。车轴质量的影响因素主要包括车轴钢的 种类、热处理工艺及装配工艺等。对于车轴选材而言,最主要的指标是保证其良好的强度, 特别是疲劳强度和韧性。目前,对于高速列车用车轴,国内主要采用欧洲进口合金钢 EA4T, 在制造工艺方面与国外存在较大差距,缺乏相关领域核心技术及知识产权。
12.2.2.1 国外车轴钢发展态势
国际上因为不同国家的技术水平存在较大差异且各国国情不同,所以各国使用的车轴钢 也有较大差异。列车使用的车轴钢一般可以两大类:碳素钢及合金钢。日本、韩国和美国多 采用中碳碳素钢,欧洲国家多采用合金钢。从碳含量来说这两种车轴用钢都属于中碳钢,合 金化的目的是提高钢材淬透性、改善强韧性等综合性能,特别对于大截面的车轴用钢更是如 此。铬、镍、钼、锰等合金元素是车轴钢合金化的主要元素。通常还会控制钢中铝元素含量 和添加钒等,以获得细小组织,改善韧性特别是低温韧性。此外经济性也是选材和钢种成分 设计时必须要考虑的因素之一。从含碳量来看,日本采用的车轴用钢 SFA55 及 SFA60 的含碳 量为 0.35% ~ 0.45%。苏联在 1967 年前车轴用钢的含碳量为 0.43%,到 1971 年降为 0.41%, 由于含碳量的降低,使钢的强度下降 25MPa,但韧性有所提高。为了保证强度,又于 1974 年将车轴用钢的含碳量恢复到 0.43%。法国为 0.34% ~ 0.38%,美国为 0.45% ~ 0.59%,德 国采用含碳较低的 EA4T 钢,在调质状态下使用。
日本高速列车用车轴选用的材料是普通碳素钢(SFAQA/S38C),采用感应淬火热处理对 其表面进一步强化。在表面淬硬层内获得细小的马氏体组织,使材料的表面强度得到显著提 高,并使材料表面产生残余压应力,这种热处理工艺可以显著提高材料的疲劳性能。其热加工制造的具体工艺路线为:锻造成形—调质热处理—表层感应快速加热—喷水淬火—低温回 火处理。该材料的特点为:原材料价格较低,但其热处理工艺比较复杂,参数控制精度高。我国引进的 CRH2 型号动车组使用的车轴材料就是该型钢。
欧洲各国多采用合金钢 EA4T,主要用于制造高速、重载铁路车轴,其热加工制造工艺 为锻造成型 - 调质处理,为了进一步提高车轴材料的使用寿命,最终会采用表面热处理及喷 丸处理使车轴表面产生一定的残余压应力。合金钢 EA4T 原材料成本比较高,但是其生产工 艺相对简单,更加适合中国国情。表 12-3 为国外主要车轴钢牌号及标准。
尽管各国使用的车轴钢材料及制造工艺存在较大差异,但有如下趋势:
① 发展精炼工艺,净化钢水,以提高材料的纯净度,从而减少车轴的裂纹源。
② 锻造方面主要采用径向锻造机和大吨位高速精锻机进行锻造,空气锤和水压机锻造只 适用于小批量的生产。
③ 随着高速重载车轴的发展,选用淬透性好的中碳低合金钢,在进行调质处理后还开展 表面淬火、滚压及喷丸等处理。实践证明,车轴经表面淬火处理可以提高疲劳强度极限 30% 以上,而表面经喷丸强化处理可以使疲劳极限提高 25% 以上。
12.2.2.2 国内车轴钢发展态势
国内铁路是世界铁路运输总量最大的国家之一,中国也是铁路车辆轮轴生产和需求量最 大的国家之一。鉴于铁路发展历程的特殊性,政府始终把铁路放在优先发展的地位,但铁路 车辆轮轴的使用工况仍旧相对恶劣。主要呈现出的特点有:
① 运输负荷重;
② 线路条件复杂;
③ 铁路覆盖面积大,大气环境差异大,气温在 -40 ~ 40℃之间,既有高温、湿热地区, 又有高寒、干燥地区,且桥梁、涵洞多。
上述这些外部因素,无疑都对国内铁路车辆轮轴的设计、制造和维修保养提出了较为苛刻的条件。近年来,重载技术和提速战略都给国内铁路车辆轮轴技术提出了新的要求。
我国列车车轴主要以 LZ40 钢和 JZ45 钢为主,前者含碳稍低,为 0.37% ~ 0.45%,含锰 也稍低,为0.45%~0.8%;后者含碳及含锰均稍高,分别为0.4%~0.48%及0.55%~0.85%。显然这是为了保证车辆用车轴钢具有较好的韧性及较低的冷脆转折温度,但其强度低、耐磨 性差和疲劳寿命短的缺点无法满足近些年铁路提速的要求。根据四方车辆研究所对轨道列车 车轴普查的结果显示,由于强度低、耐磨性差导致报废的车轴每年平均将近一万根。为此, 我国参照 AAR 标准研制了力学性能优于 LZ40 车轴钢,并且寿命比 LZ40 延长一倍以上的 LZ50 车轴钢,经历了十年的装车考核后现已在轨道列车上推广使用。虽然 LZ50 车轴钢解决 了行业部分难题,但现今我国动车组所用空心车轴主要还是依赖于进口,并且在相关车轴制 造的核心技术方面缺少自主知识产权。值得一提的是,目前我国在钢铁冶炼方面技术较为成 熟,车轴钢坯质量稳定性及氧含量和夹杂物控制水平处于世界先进水平。
目前国内高速铁路车轴用钢主要采用进口的合金钢 EA4T,其化学成分与国产 25CrMoA 钢相近,经过适当的热处理后可获得优良的强韧性,是目前最合适的高速、重载车轴材料, 主要应用于地铁车轴和准高速机车车轴。国内对于 EA4T 钢所采用的热处理工艺大多是调质 处理工艺,得到的组织为回火索氏体组织,该组织具有良好的综合力学性能。但由于原始材 料的成分不均匀以及材料本身淬透性不足等问题,在热处理过程中往往会产生“遗传现象”, 导致最终产物中含有大量的块状铁素体,这些铁素体严重影响材料的力学性能。
解决热处理过程中“遗传现象”的关键是改善材料的组织均匀性。郑业方等设计了针 对 EA4T 钢的热处理方案,通过研究发现:如果在调质处理前进行适当的预处理可以显著改 善材料的组织均匀性,减少块状铁素体的含量,并能有效提高材料的综合性能。张昌裕等在 EA4T 钢调质处理之前,首先对原始组织进行了高温回火处理,他们认为高温回火可以使原 始组织的成分更加均匀,并能够减少元素分布不均产生的成分偏析,进而能够减少块状铁素 体的生成。刘曙蓉等针对原始组织成分不均匀现象,运用二次正火工艺和高温长时间奥氏体 化处理,使材料中的合金元素和碳元素在热处理过程中得到更充分的扩散,并最终得到了较 细的晶粒尺寸,确定了最佳的热处理工艺。
国内学者在成分分析、锻造与热处理工艺、金相组织与力学性能等方面进行探索,在材 料特性、工艺参数等方面取得一些成果。同时也发现,进口的合金钢 EA4T 仍有存在非金属 夹杂物以及组织不均匀等缺陷,性能及疲劳寿命潜力有待进一步发掘。但目前的研究工作主 要集中在了传统工艺改善等方面,对新工艺的探索仍相对较少。虽然近年来开展了大量对 EA4T 钢的研究,国内钢坯质量也较高,但由于在车轴制造相关领域缺少核心技术的自主知 识产权,且无完善的考核评价标准,目前合金钢 EA4T 车轴主要依赖于欧洲进口。对于 EA4T 钢,在材料特性、生产工艺、疲劳寿命预测等方面的研究,在实现国产化,发掘材料潜力等 方面,仍然具有重要价值。
12.2.3 转向架轴承用钢
轴承是列车走行系统的核心转向架中的关键部件,其性能和安全性直接影响高铁的运行 安全。高速列车转向架轴承主要包括电机轴承、齿轮箱轴承和轴箱轴承等,电机轴承尺寸小 于齿轮箱轴承和轴箱轴承。从轴承类型上看,转向架轴承均为滚动轴承,由内外套圈、滚动 体、保持架和润滑油脂组成。
当前,在普通机车车辆用轴承研究与制造领域,我国的总体技术水平基本与世界先进水 平相当,国内中信特钢、西宁特钢等钢铁企业能够生产满足中国铁路总公司技术标准要求的 轴承钢钢材,瓦轴、洛轴和天马等轴承企业能够生产出满足使用要求的相关轴承,并已稳定 供货。转向架轴承作为典型的高端轴承代表,受轴承行业整体技术水平的影响,目前我国生 产的轴承仅能适用于运行速度 140km/h 以下的车辆。因此,在高速铁路领域,由于受设计开 发能力和制造水平等诸多因素的限制,现阶段我国的高速铁路列车均采用进口配套轴承,主 要从瑞典 SKF、德国 FAG、日本 NSK/NTN 和美国 Timken 等国际著名轴承公司采购轴承, 急需实现国产化。
12.2.3.1 国外轴承钢发展态势
如前所述,高速列车转向架轴承主要包括电机轴承、齿轮箱轴承和轴箱轴承等,虽然均 为滚动轴承,但因服役条件不同,不同部位使用的轴承类型、大小均不相同,而且不同轴承 厂家根据各自的技术特色在内外套圈和滚动体上使用的轴承钢材质也不尽相同。随着列车运 行速度的提高和载重的增加,各国广泛使用渗碳钢制造的圆锥滚子轴承。瑞典 SKF 公司、美 国 Timken 公司、日本 NSK 公司和 NTN 公司等采用表面渗碳钢制作圆锥滚子轴承,有效地 提高了轴承免维护运行里程及其安全可靠性。
尽管世界各国标准对轴承钢的具体合金成分要求有所差别,同时各轴承厂也根据自身技 术特点在国标范围内进一步优化设计了内控材料成分范围和 / 或特殊制造工艺,但整体上仍 然可以把现用的国外进口高铁转向架轴承用钢归属到全淬透性的高碳铬轴承钢和渗碳轴承钢 两大类轴承钢。从检测数据来看,目前进口高铁转向架轴承使用的轴承钢可以对应到我国轴 承钢牌号 GCr15、GCr18Mo、GCr15SiMn 等高碳铬轴承钢和 G20CrNi2Mo 渗碳轴承钢。这 说明国外轴承公司针对高铁转向架轴承的应用特点,并没有超出传统材料的范围而另行开发 新的材料,而是在这些传统材料的基础上,通过提高材料纯净度、均质性并结合后续差异化 热处理工艺提升性能,满足使用需求。我国国标对上述牌号的轴承钢成分要求如表 12-4 所示 (以特优级钢为例)。
虽然进口高铁转向架轴承均采用现有牌号轴承钢制造,但其普遍具有较高的洁净度,多 数高碳铬轴承钢和渗碳轴承钢的氧含量控制在 6ppm 以下, Ti 含量控制到 15ppm 以下,达到 了我国国标中规定的特优级轴承钢的要求,但部分轴承也存在氧含量超过 6ppm、Ti 含量达 到 20ppm(渗碳轴承钢)的现象。在严格控制杂质元素含量的同时,国外进口高铁轴承中的 夹杂物控制也体现出了较高的水平,尤其是对于对疲劳性能影响较大的 DS 类夹杂物控制较为 严格,一般在 0.5 级,很少有达到 1.0 级的情况。使用 ASPEX 夹杂物自动检测分析技术对进口高铁轴承进行大面积的夹杂物统计发现,其中夹杂物最大尺寸一般小于 20μm,且最大尺寸 夹杂物一般为硫化物。
值得注意的是,从目前公开的数据分析,国外进口高铁轴承并未使用瑞典 Ovako 的 IQ 钢(主要指标为氧含量 4~6ppm,钛含量 8~12ppm,最大夹杂物 DS<15μm,同时具有各向同 性特征)等轴承领域口碑较好、公认品质较高的顶级轴承钢。由于钢中夹杂物含量、形状和 尺寸对钢材疲劳极限强度的高低有着很大的影响,世界各国都在努力提高钢材纯净度。Ovako 在冶炼时不但能控制钢中夹杂物的含量,还能控制钢中夹杂物的形状和尺寸,目前 Ovako 生 产的 BQ 和 IQ 等级钢材在 10MHz 水浸超声探伤已经很难发现 0.2mm 平底孔当量的宏观夹杂物,微观夹杂物更是比 ASTM A295 和 ASTM E45 标准低了一个数量级。
除纯净度之外,轴承钢中和钢材冶金质量相关的指标还有液析碳化物、网状碳化物和带 状碳化物,以及成分均匀性。相关数据表明,国外进口高铁轴承中液析碳化物控制水平很好, 基本上在 0.5 级以下,很少能够观察到轴承中存在液析碳化物;网状碳化物通常控制在 1.0 级 以下,带状碳化物一般控制在 1.5 级以下,同时整个轴承的硬度均匀性也控制得很好,硬度差都在 ±1HRC 之内,体现出较好的组织均匀性。
轴承是较为特殊的一类零部件,钢材的冶金质量仅仅是一个基础的性能指标,轴承最终 的服役性能还直接受最终热处理以及机加工过程表层和近表层显微组织变化的影响。由于高 铁转向架中电机轴承、齿轮箱轴承和轴箱轴承三大类轴承的服役载荷特征不同,因此国外轴 承企业也针对不同的服役载荷特征选用不同轴承材料,并对其实施不同的热处理工艺,以获 得最适合服役载荷特征的显微组织和性能。以轴箱轴承为例,某企业虽然使用高碳铬轴承钢 制备轴箱轴承的内外套圈和滚动体,但依然在根据轴承内外圈和滚动体的尺寸,合理选用了 不同牌号的高碳铬轴承钢制备内外套圈和滚动体;在热处理和显微组织控制方面,考虑到轴 箱轴承需要承受较强的冲击载荷,内外套圈的显微组织为马氏体 + 贝氏体复合组织,在保证 较高的硬度情况下仍然维持了良好的韧性。而另外一家轴承企业,则根据自己的轴承设计和 技术特长,选用渗碳轴承钢制造轴箱轴承的内外套圈,选用高碳铬轴承钢制备滚动体。
从对高铁转向架轴承的解剖分析结果来看,国外著名轴承公司已经掌握了大量高铁轴承 台架以及实际运行的经验和数据,从而可以综合考虑轴承设计、轴承制造和轴承材料之间的 相互配合,以达到稳定服役为目标,虽然没有使用行业内最著名的轴承钢,但其轴承钢洁净度也达到了非常高的水平。
12.2.3.2 国内轴承钢发展趋势
高铁转向架轴承是高端轴承的典型代表,其研究和使用状况也直接受我国轴承的整体发 展状况的影响和制约。在轴承钢方面,国内轴承钢方面近些年也做了很多工作,建立了合理 的轴承钢生产流程,在氧含量、夹杂物、碳化物控制方面都有很好的进展,尤其是以兴澄特钢、大冶特钢等为代表的一些国内特殊钢厂近些年在高端轴承钢的研发与生产方面取得了巨 大的进步。从杂质元素含量指标来看,兴澄特钢等钢厂的钢材质量控制水平已经达到国外进 口高铁轴承用钢的水平。在夹杂物控制方面,国内钢厂的控制水平经过十余年的不断改善, 也已经达到很高的水平,在严格控制的情况下钢材的纯净度可以达到进口高铁轴承用钢的纯 净度水平。
此外,中国科学院金属研究所通过多年研发,发明了钢液和稀土金属中的“双纯净技 术”,与西王、天马等多家企业合作,解决了钢中添加稀土导致钢的性能不稳定、时好时坏 的问题,取得了稀土钢工业化应用的飞跃。在其他常规冶金手段无法提高轴承钢的品质的情 况下,每吨钢只需加入 200g 微量镧、铈稀土金属,5μm 以上较大尺寸的夹杂物可减少 30% 以上,将硬脆的氧化铝变质为与基体匹配良好的稀土氧硫化物,这些稀土氧硫化物在疲劳加 载过程中可以发生塑性变形,从而降低了夹杂物与基体界面处的应变集中,延缓了疲劳裂纹 的萌生。同时也显著降低了轴承钢中 MnS 的含量,将长条形 MnS 变质为球状的稀土氧硫化 物。夹杂物数量、尺寸的大幅降低,以及夹杂物属性的改变,显著提升了轴承钢的疲劳寿命。这些进展都为高铁转向架轴承的国产化奠定了基础。
为解决铁路系统用轴承的国产化问题,我国已经开展过多次攻关研究,取得了一定的成绩。如前所述,在普通机车车辆用轴承研究与制造领域,我国的总体技术水平基本与世界 先进水平相当,中国铁路总公司已经制定了 Q/CR 592《铁路货车轴承用渗碳轴承钢》和 Q/ CR593《铁路货车轴承用高碳铬轴承钢》两个专用的材料标准,这两个标准在材料纯净度和 冶金质量方面的要求已经非常严格,依据上述标准国内大冶特钢、西宁特钢等钢铁企业已经 获得生产资质,稳定提供相关钢材,实现了国产轴承在铁路货车上的成功应用。
如前所述,轴承是一类极为特殊的零部件,轴承制造企业从特钢厂购买轴承钢之后,还 要经过后续重新的加热锻造、球化处理、淬火 + 回火处理、机加工等工艺流程才能最终制造 出成品轴承,最终决定成品轴承服役性能的关键通常是轴承滚道的表面和近表面材料性能, 而这些区域材料的性能虽然受特钢厂出厂时轴承钢的成分、洁净度和显微组织的影响,但更受后续工艺流程的影响,因此对轴承钢品质的控制不应仅仅局限在特钢厂关注的冶金质量上, 而是应该延伸到轴承制造过程,乃至轴承服役过程。
正是因为如此,我国围绕高铁转向架轴承国产化也曾经安排过协同攻关研究。国家科技 部在 2011 年支持了由轴研科技牵头申报的国家科技支撑计划项目“高速铁路和城市轨道交通 车辆轴承关键技术研究与应用”,针对高铁轴承开展了科技攻关,同时在国家 863 项目支持 下,由洛阳 LYC 轴承有限公司、青岛四方车辆研究所、中国铁道科学研究院、浙江大学及河 南科技大学共同承担了 863 计划先进制造技术领域“大型专用轴承试验台研制”重点项目中“大型高速铁路轴承实验台”课题,针对高铁轴承实验台架开展了研究。目前洛轴制造出了速 度 250km/h 和 350km/h 的高铁轴承,并在上述试验台上进行了测试实验。
12.3 目前制约该产业发展的主要问题与面临的挑战
12.3.1 高速车轮材料
降低碳含量并结合微合金化是国内高速车轮用钢发展的主要趋势,在碳含量基本确定的 情况下,研究 Cr、V、Mo、Nb 等微合金元素的固溶强化机理,从碳当量的角度综合考虑 Si、 Mn、Ni 对车轮材料强韧性指标的影响,确定 C 及微合金元素的最佳成分匹配。
冶炼工艺的改善有利于钢的洁净度的提高。我国必须大力开展不同钢种二次精炼工艺研 究,进一步实现二次精炼工艺的高效化、高速化及智能化控制。
车轮与轨道在服役过程中的相互作用关系十分复杂,目前对高速车轮钢在服役过程中组 织变化和裂纹萌生、扩展过程不够清楚,必须深入对高速运行状态下车轮的疲劳与断裂行为 研究。
无碳化物贝氏体钢具有良好的热稳定性、耐磨性、抗热裂能力和强韧性配合,是极具潜 力的新型高强韧车轮钢。在冶炼工艺、成分控制方面需与现有车轮工艺衔接。在合金元素上 需选择我国丰富的合金元素,如 Si、Mn 等。研究表明,在 Si、Mn 适当提高的基础上,降低 C 含量,并调节热处理参数获得无碳化物贝氏体组织是可行的。
我国在评价高速车轮钢服役寿命和状态上尚无统一标准,必须深入分析各类材料的服役 寿命和受损情况,从而建立新型车轮服役寿命和服役状态的评价体系。
12.3.2 高速车轴材料
合金钢 EA4T 是目前最合适的高速、重载车轴材料,也是目前国内高速铁路主要采用的 车轴材料。国内在合金钢冶炼、成型、热处理方面已经较为成熟,该材料的制造不存在无法 克服的技术难题。但由于在车轴制造相关领域缺少核心技术的自主知识产权,且无完善的考核评价标准,目前合金钢 EA4T 车轴主要依赖于欧洲进口。进口的合金钢 EA4T 仍存在非金 属夹杂物以及组织不均匀等缺陷,性能及疲劳寿命潜力有待进一步发掘。
在国内具备车轴制造能力的情况下,对车轴的制造标准、考核与评价标准等方面急需完 善,需建立一套独立的制造标准与考核评价流程,才能实现车轴制造国产化。
12.3.3 转向架轴承材料
轴承钢是轴承结构材料的主体,因此轴承钢的研究始终是轴承发展中的重要主题。从目 前进口高铁转向架轴承用轴承钢来看,高铁转向架轴承使用的材料均是成熟牌号的传统轴承钢。以应用最为广泛的高碳铬轴承钢 GCr15 钢为例,发明 100 余年以来虽然其主合金成分变 化不大,但围绕其洁净度、热处理与显微组织控制、精细机加工等方面却在持续优化改进。值得注意的是,将轴承钢制造成轴承,涉及众多热、冷加工环节,由于国产高铁转向架轴承 缺乏大量的台架试验结果和实际应用经验,虽然国内企业已经试制出高铁转向架轴承,但还未能实际装车应用。
轴承是汇集了冶金、材料和机械等多个学科的一个极为特殊的零部件,由于其加工制造 流程长,且服役过程影响因素众多,因此,虽然经过不同学科的大量研究,在各自学科领域 内的研究取得了诸多进展,但跨领域涵盖整个加工制造流程和服役工况的研究较少,“轴承钢 组织和性能”与“轴承服役寿命”之间的关系尚不清晰,这也直接限制了国产轴承在高铁转 向架上的应用。
虽然“轴承钢组织和性能”与“轴承服役寿命”之间的关系尚不十分清晰,但轴承钢的 接触疲劳性能与轴承服役寿命密切相关,且洁净度影响轴承钢的接触疲劳性能的观点受到了 国内外学者的广泛认可。仅从纯净度方面来看,基于国内特钢厂现有基础,通过精细化控制, 应该可以满足高铁转向架轴承的应用需求。但需要指出的是,钢材的纯净度提升是没有止境 的,中科院金属所研发的稀土轴承钢技术,以及国外采用的 Ca 处理技术等都可以进一步提 升轴承钢的纯净度,为高品质轴承的制造提供基础。
在解决钢材纯净度的基础上,还应该树立“全寿命周期轴承钢材料研究”的理念,即不 仅仅关注轴承钢的冶金质量,还要根据轴承的服役特征,有机地将轴承钢的冶金质量和后续 轴承钢的热处理、机加工乃至服役工况结合起来,针对不同轴承形成有针对性的调控策略, 而这需要打破以往特殊钢厂、轴承厂和轴承用户之间的隔阂。
除上述研究思路的改变之外,现阶段制约高铁轴承国产化的问题还在于国产轴承缺乏令 各方信服的、科学可靠的测试数据。这方面需要从研发高铁转向架轴承测试台架着手,需要研发大量能够模拟真实服役状况的台架,对国产高铁轴承进行批量的性能评估和测试,并根据测试结果不断优化改进轴承设计与制造流程。
12.4 促进该产业发展的对策与措施建议
从上述对制约该产业发展的主要问题与面临的挑战分析可以看出,无论是车轮、车轴, 还是转向架轴承,都面临着相似的困境,即:国内相关材料研究和生产已经有一定的基础, 相关企业对于国产化有极高的热情,但由于缺少足够的、令人信服的接近实际服役状况的数 据,终端用户从保障绝对安全的角度考虑,无法采购国产产品,从而形成一种“无应用业绩, 不能应用”“不能应用,无应用业绩”的死循环,导致国产化难以取得实质性突破。
为解决上述问题,我们需要从基础科研和应用推广两个方面加强协调。在基础科研方面, 需要集合行业内的优势力量,从材料端牵引,建立“全寿命周期”材料研究理念,融合下游 部件制造与服役评价,开展系统的研究工作,在材料纯净度提升等毫无争议的领域研发具有 我国特色的杀手锏技术,在材料显微组织控制方面需要和转动核心部件设计、加工以及服役研究密切配合,针对不同基础部件研发不同的显微组织控制技术方案。
在应用推广方面,建议由国内相关单位牵头,组织国内各科研机构和制造厂的优势力量, 进行冶炼—铸造—锻造—热处理—机加工全流程的制造与研发工作,建立相关的技术标准, 获得自主知识产权。在此基础上,建立车辆高速运转体系材料的考核评价体系,通过台架试 验建立材料力学性能与服役寿命的映射关系,为国产车轮、车轴和转向架轴承的应用建立技 术、制造、考核的全方位保障,打通国产车轮、车轴和转向架轴承应用的技术渠道,最终实 现全面的国产化,替代进口,并最终形成出口。
免责声明:本网站所转载的文字、图片与视频资料版权归原创作者所有,如果涉及侵权,请第一时间联系本网删除。
相关文章
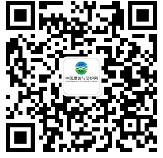
官方微信
《腐蚀与防护网电子期刊》征订启事
- 投稿联系:编辑部
- 电话:010-62316606-806
- 邮箱:fsfhzy666@163.com
- 腐蚀与防护网官方QQ群:140808414
点击排行
PPT新闻
“海洋金属”——钛合金在舰船的
点击数:8156
腐蚀与“海上丝绸之路”
点击数:6487