摘要
碳氮共渗工艺应用广泛,但对碳氮共渗后零部件的滚动接触疲劳失效机理研究较少。采用气体碳氮共渗对马氏体轴承钢进行表面改性处理,对碳氮共渗试样进行滚动接触疲劳试验,研究碳氮共渗对轴承钢滚动接触疲劳性能的影响及其失效机理。研究结果表明:碳氮共渗试样表面硬度、残余应力和残余奥氏体含量显著提高,使得其接触疲劳寿命明显高于常规试样。 疲劳裂纹萌生于表面和亚表面,其中大量表面平行裂纹主要由表面白色蚀刻层硬度梯度变化而导致,表面材料受到严重微观塑性变形产生晶粒细化;亚表面裂纹萌生位置受最大应力的分布和渗层厚度的影响。表面和亚表面疲劳裂纹的扩展和连接最终导致碳氮共渗试样出现浅层剥落和分层剥落的失效形貌。
关键词: 碳氮共渗 ; 马氏体轴承钢 ; 滚动接触疲劳 ; 失效机理 ; 裂纹萌生
0 前言
滚动接触疲劳(RCF)是轴承最常见的失效模式,尤其是在高速、重载等复杂工况下,RCF会导致轴承过早失效而严重影响设备的可靠性及使用寿命[1-3]。在接触疲劳载荷作用下,裂纹会萌生于接触表面或亚表面[4-5],疲劳裂纹的演化最终会导致材料表面形成点蚀、剥落坑和分层而失效。材料表面抗接触疲劳性能对轴承寿命有很大的影响[6-9],因此,获得具有优良耐磨、耐腐蚀和抗氧化性能的改性硬化表面层以提高材料的疲劳性能是很有必要的。
碳氮共渗是提高轴承寿命的主要方式。相比于单独渗氮和渗碳处理,碳氮共渗改性处理能综合渗氮和渗碳的优势,提高表面硬度、耐磨性及耐蚀性,同时表层与基体形成硬度梯度下降缓慢,可提高轴承钢等工程材料的力学性能,特别是摩擦学性能。近几年,已有较多研究人员对表面碳氮改性试样的疲劳失效机理进行研究[10-15]。KARAMIS等[16]研究证明碳氮处理后低碳钢AISI 1020表面硬度提高2倍,基体材料仍保持良好的韧性,试样的摩擦学性能得到显著改善。谷臣清等[17]发现高温碳氮共渗后M50NiL钢疲劳裂纹沿渗层的扩展行为与渗层的塑性和韧性等有关,渗层高温硬度的提高是马氏体回火相析出发生改变的结果。KANCHANOMAI等[18]研究了残余应力对碳氮化AISI 1015钢疲劳性能的影响,发现碳氮改性层内存在较大的残余压应力,其疲劳寿命约为未处理试样的5倍。过渡区内残余应力的变化是诱发疲劳裂纹的主要原因。在现有文献中,对于表面改性材料的疲劳性能研究主要集中于疲劳寿命和渗层宏观摩擦磨损性能,而对滚动接触疲劳载荷下的微观失效特征及其机理以及疲劳过程中微观组织的动态变化对于疲劳性能影响的研究工作很少见。
本文以GCr15马氏体轴承钢为试验对象,应用气体碳氮共渗在试样表面制备硬化改性层。使用MJP-30型滚动接触疲劳试验机进行滚动接触疲劳试验。研究表面碳氮共渗试样滚动接触疲劳行为及失效机理,为碳氮共渗后的零部件在接触疲劳等方面的应用提供理论依据。
1 试验方法
1.1 试验材料及热处理工艺
试验原材料为退火态GCr15钢,其化学成分(质量分数/%)为:0.89~0.92C;0.28~0.32Mn;1.77~1.82Cr;0.28~0.31Si;0.01~0.02S;其余为Fe。表面改性工艺选取为气体碳氮共渗,设备选用多用炉,采用氨气+甲醇+氮气+丙烷的气氛在温度860℃±5℃下保温3h进行共渗处理,淬火冷却至室温,随后在170℃±5℃下回火保温2h。由于碳氮共渗工艺只对试样表面一定深度范围内的基体起到改性强化作用,而内部基体则相当于进行同温条件下的常规热处理,因此将疲劳试样的对照组选为与碳氮共渗工艺相同温度的常规热处理试样。
1.2 接触疲劳试验
根据YB-T5345—2006将试样设计加工为圆环状,外径和内径分别为60mm和30mm,厚度为20mm。为了增加接触应力,主试样的外圆接触面被加工成宽度为5mm、高度为3mm的凸平台,试样示意图如图1所示。试验在MJP-30型滚动接触疲劳试验机上进行。主、陪试样分别由独立轴驱动,试验机配备振动信号传感器,用于监控测试过程,试样在试验过程中会因表面发生点蚀而产生较大震动,当震动信号频率高于300dB时,试验机自动停止。
图1 疲劳试样尺寸示意图
试验全程采用油润滑,在试验过程中,最大赫兹接触应力选取2.0GPa和2.6GPa。下轴转速1 000r/min;上轴转速选取900r/min和850r/min,从而获得10%和15%的滑差比率,分别与上述不同载荷组成对照组,进而研究试样在不同工况下的滚动接触疲劳失效机理。由于滚动接触疲劳寿命存在较大分散性,为了得到统计结果,在每种试验条件下进行了3组滚动接触疲劳试验。
试验结束后利用电火花线切割机切取基体的轴向及径向截面,经过机械研磨抛光后利用4%的硝酸酒精溶液进行腐蚀。使用金相显微镜(OM)和扫描电子显微镜(SEM)观察试验前后试样接触表面及其亚表面显微组织结构的变化。采用显微维氏硬度计测定渗层亚表面沿深度方向的显微硬度分布,每个压痕点间距为25 μm。辉光放电发射光谱仪(GD-OES)用于表征试样亚表面碳、氮元素含量随深度的变化。试样渗层及基体物相使用X射线衍射仪(XRD)进行分析,扫描速度为2(°)/min,扫描范围为20°~100°,用Jade6软件将所得数据与标准峰进行匹配确定物相成分。试验前利用高速残余应力分析仪分别对两组试样接触表面的残余应力进行表征,测试方法为双探测器同倾法, X光管发出的X射线为Cr靶的 Kα辐射,测试电压和电流分别为25kV和5mA,选择的衍射晶面为(BCC,hkl-211)。透射电镜薄片试样由聚焦离子束(FIB)切取制备,利用30kV、50~120pA的电子光束将其进行减薄。待测薄片厚度最终控制在50~70nm,应用透射电镜(TEM)对其微观组织进行观察。
2 试验结果与讨论
2.1 碳氮共渗层的微观形貌和显微硬度
碳氮共渗初始试样腐蚀后的横截面金相形貌如图2a所示,可以看出碳氮扩散层与基体之间存在明显的边界。图2b和2c分别为框选区域A和B内的放大形貌图,渗层与内部基体的宏观组织组成物相类似均以回火马氏体为主。渗层中碳化物数量较多,主要呈球状,平均尺寸为0.95 μm。一定含量的碳化物析出有利于试样接触表面耐磨性能的提升。随深度增加,基体内部碳化物数量明显减少。
图2 碳氮共渗层与基体微观组织形貌
利用辉光放电质谱仪对碳氮共渗试样亚表面元素分布进行分析,含量变化曲线如图3所示。碳、氮元素含量的分布曲线存在三个阶段。在曲线最开始的Ⅰ 阶段存在一个高峰,这表明在气体碳氮共渗处理后近表面碳含量为1.92wt.%,相比基体碳含量提高约2倍。但近表面氮元素含量较少,氮元素含量仅为0.45wt.%。在Ⅱ阶段两元素含量均存在平缓区;最后在Ⅲ阶段碳、氮元素含量随深度增加逐渐减少,在距表面180 μm处的碳含量与基体碳含量基本持平。试样亚表面显微硬度随深度变化的测量结果如图4所示,碳氮共渗处理主要对试样表面起到改性强化作用,渗层硬度提高至795HV0.05,在距离表面200 μm以下的材料硬度趋于基体硬度,为745HV0.05。显微硬度变化趋势和碳、氮元素含量随深度的变化相符合,判断该碳氮共渗工艺下有效硬化层厚度在180~200 μm范围内。
图3 碳、氮元素浓度含量随深度变化曲线
图4 碳氮共渗层和内部基体横截面显微硬度随深度变化曲线
2.2 碳氮共渗层的物相
图5 为碳氮共渗试样试验前后碳氮共渗层与内部基体的XRD图谱。可以看出渗层处组织组成物与基体内部大致相同,主要由马氏体、残余奥氏体和渗碳体组成。由于共渗层中氮含量较低,在XRD图谱中并没有显示出明显的氮化物衍射峰。根据碳氮共渗原理,渗层的组织中应具有少量的氮化物。相比于基体内部,渗层处的奥氏体衍射峰峰强度更强,马氏体的衍射峰强则相对较弱,这表明渗层处含有更多的残余奥氏体。
图5 碳氮共渗试样渗层和基体的XRD图谱
根据XRD图谱分别选取(220)α、(200)γ、 (211)α、(220)γ 以及(311)γ 处的衍射峰,利用式 (1)计算残余奥氏体体积分数[19]:
式中,vγ 为奥氏体相的体积分数(%);n 为衍射峰数目;R 为散射因子;I 为(hkl)晶面衍射峰的积分强度;θ 为衍射角;γ 为单胞体积;F 为结构因子;ρ 为多重性因子;exp(?2M)为温度因子。
经计算,碳氮共渗在疲劳试验前的渗层近表面及其基体内部残余奥氏体含量分别为37.32%和7.07%。渗层处与内部基体中的残余奥氏体含量差别较大,这是由于近表面碳、氮元素含量的提高降低了马氏体转变温度(Ms),同时在一定程度上增加了奥氏体的稳定性,使得奥氏体转化不完全,最终导致渗层处相比基体含有更多的残余奥氏体。
2.3 滚动接触疲劳性能分析
图6 所示为碳氮共渗试样和常规热处理试样在载荷和滑差率分别为2.0GPa-10%,2.0GPa-15%和2.6GPa-15%工况条件下滚动接触疲劳寿命试验结果。比较可见,碳氮共渗试样疲劳性能明显优于常规热处理试样,在三种工况环境下碳氮共渗处理试样疲劳寿命分别提高5、8和3倍。随着载荷和滑差率的增大,两组试样寿命均处于减少趋势。疲劳寿命的改善一方面是由于碳氮共渗层的存在增加了接触表面的硬度,使得试样在接触边缘不容易形成应力集中区域而萌生疲劳裂纹。在一定的硬度范围内,接触疲劳抗性随硬度的增大而升高。试样亚表面硬度分布平缓,表面碳氮改性处理后的M50NiL、AISI 410钢断面渗层显微硬度分布也出现这种趋势[20-21],这能有效降低渗层与基体之间因硬度差异较大而导致组织组成物不兼容萌生裂纹的可能性,有利于试样耐磨性和抗接触疲劳性能的提高[12, 22]。再者,试样经碳氮共渗处理后,碳、氮元素作为间隙元素扩散到铁晶格中,造成严重晶格畸变,并起到弥散强化的作用,在提高渗层硬度的同时也使扩散层内部产生了较高的残余压应力[23-26]。经测得,在本次试验中试验前常规热处理试样以及碳氮共渗试样接触面残余应力大小分别为?34.00MPa和?230.49MPa(沿试样接触表面周向等距离选取5个点,测试结果取平均值),均为残余压应力。 KANCHANOMAI等[18]在对碳氮共渗后的AISI 1015钢研究中发现,共渗层中存在较大的残余压应力且随着深度的增加而减少。较高的残余压应力可以诱使裂纹闭合并在一定程度上延缓其扩展演化,防止试样表面较早出现剥落坑等失效形貌[27-29]。
图6 不同工况下试样的滚动接触疲劳寿命
另一方面,残余奥氏体含量的不同对于试样的疲劳寿命也存在较大影响。已有较多研究表明,一定含量的残余奥氏体能有效提高接触疲劳性能[30-31]。在滚动接触疲劳过程中,发生应变诱发马氏体相变[32-34]。图7为碳氮共渗试样分别在2.0GPa-15%和2.6GPa-15%工况下经过2.8×106 和7.6×105 次循环疲劳失效后接触面的XRD图谱,对比原始物相衍射峰(图5)可以看出马氏体衍射峰强度变化较小,然而奥氏体衍射峰已消失。这表明在疲劳试验后接触表面的残余奥氏体含量几乎为0,近表面处的残余奥氏体基本上已转变为马氏体。同样的结果也出现在滚动接触疲劳试验后的AISI 52100轴承钢表面中[35]。相变后的马氏体体积发生膨胀,考虑到近表面材料硬度较大会对内部基体起到约束作用,这使得内部基体膨胀后的能量会以压应力的形式保存于近表面的基体中。另外,一定量残余奥氏体的存在可以确保样品表面的载荷分布得更加均匀,利用其易变形特点,降低压痕的边缘效应,使起源于压痕边沿的表面疲劳源不易形成和扩展,从而提高试样的接触疲劳寿命。
图7 不同工况碳氮共渗试样失效后近表面XRD图谱
2.4 失效形貌及其机理分析
通过观察失效表面和横截面来识别其损伤机理。接触疲劳裂纹的萌生和扩展是切应力和材料切变强度相互作用的结果,常见的裂纹萌生类型有两种:疲劳裂纹萌生于表面[36];疲劳裂纹萌生于亚表面[37]。在本次碳氮共渗失效试样中,以上两种裂纹类型均有出现且以亚表面裂纹为主。
2.4.1 表面裂纹萌生机理
图8 为碳氮共渗试样在2.6GPa-15%工况条件下循环1.7×105 次后的失效形貌。图8a为接触表面的宏观形貌,经疲劳试验后接触表面呈现“层片状” 结构,接触表面裂纹垂直于滚动方向并向周围扩展,局部区域出现浅层剥落的失效形貌。裂纹附近基体表面出现较多划痕和犁沟,图中圆圈标记位置。图8b为该试样横截面形貌,切取位置由图8a中的虚线A处标出。可以看出在接触表面存在平均厚度为15~20 μm的白色蚀刻层 (WEL)。WEL表现出与基体不同的形貌特征,原始马氏体结构已消失,取而代之的是致密组织形貌并与基体之间存在明显的边界。相比于渗层基体,WEL内球状碳化物的数量大大减少,部分碳化物沿剪切方向被拉长。在WEL内部存在两处裂纹:表面裂纹和层间裂纹。表面裂纹沿与滚动方向呈锐角演化一段距离随即平行于接触表面扩展;层间裂纹贯穿WEL与基体交界处,裂纹与接触表面相平行。这与常规热处理试样中观察到表面裂纹的演化形式存在较大区别[38]。
在疲劳循环载荷作用下,接触表面呈现组织被剪切拉长特征是常见的现象[39-40],较高的摩擦力会导致表面材料发生严重的塑性变形进而影响内部微观组织形貌,这一现象在WEL内尤为明显。TEM明场形貌图以及选区电子衍射花样(SAED)显示了距表面不同深度位置基体的微观结构差异,结果如图8c所示。“A”区域处于WEL内部,可以看出马氏体组织沿剪切方向被大幅拉长,晶界处和晶粒内聚集的位错团簇将其划分为亚晶以及纳米晶,平均晶粒尺寸为50~75nm,“1”处SAED花样为清晰且较为连续的 α-Fe衍射环。“B”区域基体呈层片结构的拉长马氏体晶粒,层片间距集中在150nm,拉长晶粒边界清晰,晶粒长度在200~350nm。从 “2”处SAED可以看出 α-Fe衍射斑点发生了变形,表现为不连续的多晶衍射环。图中两处SAED存在明显区别,这是因为相比于内部基体,WEL内晶粒细化严重,衍射区域中小尺寸晶粒数量增多使得取向更加随机,呈现出更为完整的衍射环。 DAUTZENBERG等[41]通过计算弯曲马氏体板条边界的曲率得出有效剪应变沿深度方向的变化规律,即在一定深度范围内距离表面越近剪切应变越大。根据在WEL与基体交界处的塑性流动线,其等效剪应变最大估计值约为13.8。由于WEL层内塑性流线几乎和磨损表面相平行,无法进行剪应变的估算。然而,有研究表明近表面的有效剪应变可达到62.98[42]。这意味着近表面WEL内剪切应变远大于其以下的基体,导致该位置晶粒细化最为严重,表面基体率先超过材料疲劳极限而萌生表面裂纹。
图8 2.6GPA-15%工况条件下碳氮共渗试样循环1.7×105次后表面以及横截面失效形貌
图8d为近表面显微硬度变化曲线,压痕点间隔10 μm,每个数据点是三个测试结果的平均值。根据结果可知,距表面10 μm处基体硬度为860HV0.05,显微硬度随距表面深度的加大逐渐降低,最后趋于原始渗层硬度值790HV0.05。值得注意的是,距表面20 μm及其附近的基体并未出现形变形貌,但硬度相比于原始渗层硬度仍有提高。近表面WEL处硬度最大,与先前材料经疲劳试验后的表面变形研究结果一致,接触面晶粒细化起到强化材料硬度的作用[32, 43-44]。ZHANG等[45]在研究中指出WEL为表面裂纹萌生的早期阶段,WEL的高硬度可能导致脆性裂纹的形成和随后的疲劳裂纹扩展。WEL与基体之间因硬度以及弹性模量的差异会导致材料的不兼容,在循环载荷作用下两者之间的交界处易萌生层间平行裂纹。表面裂纹会导致接触表面呈现“层片状”结构,润滑油进入裂纹内部形成高压腔,增加了裂纹尖端的应力,加速裂纹向内部扩展[46],当与层间裂纹相连时则会导致表面浅层剥落的失效形貌。疲劳试样表面出现上述WEL形貌而诱发表面裂纹的失效形貌只在2.6GPa-15%的工况条件下出现,其他工况均未观察到该现象,说明高载荷和高滑差是产生WEL的主要原因。
2.4.2 亚表面萌生裂纹
如图9a为碳氮共渗试样在载荷2.0GPa-15%工况条件下,进行2.92×106 次循环后接触面的典型剥落坑失效形貌。接触表面存在较多点蚀坑微孔,这是由润滑油中的颗粒杂质导致。剥落坑的底部较为平坦,与接触表面形成约为30°的坡度。在循环载荷作用下,剥落坑边缘处发生应力集中而诱发横向裂纹。如图9a框选区所示,裂纹处的基体由于塑性变形已出现较多微裂纹,当该部分基体超过屈服极限时发生剥落进而产生更大的失效形貌。根据虚线B处的横截面可知剥落坑深度约为182 μm(图9b),近似于渗层厚度。在剥落坑底端存在两条沿相互垂直方向扩展的裂纹。
图9 2.0GPa-15%工况条件下碳氮共渗试样2.92×106 次循环后接触表面以及横截面失效形貌
剥落坑主要由亚表面裂纹导致。图10a为试样在载荷条件为2.0GPa表面裂纹形貌,裂纹萌生位置距表面约178 μm。主裂纹沿滚动方向呈锐角向接触表面演化,分支裂纹表现出与主裂纹不同的演化方式。分支裂纹的扩展演化不仅受应力作用影响还与材料本身有关,如晶界、夹杂以及碳化物颗粒等。在循环载荷作用下,亚表面裂纹演化至接触表面进而造成如图9a的剥落坑失效形貌。值得注意的是,不同载荷下裂纹分布的位置存在较大区别,如图10b为载荷2.6GPa亚表面裂纹分布位置,可以看出在距表面164 μm和256 μm处均有裂纹出现。
图10 不同载荷条件下亚表面裂纹分布位置
由赫兹接触理论,裂纹起源于距表面0.75b 的最大剪切应力处,其中 b 为接触圆半径。采用有限元软件ABAQUS计算了Mises应力,为简化模型便于计算,建模时将试验装置简化为二维平面模型,云图结果仅显示截取的主滚动接触试样部分。模型的弹性参数与实际试样相同,其中碳氮共渗层为239GPa,基体为208GPa;泊松比分别为0.28和0.3。模型采用四结点双线性平面应变四边形单元 (CPE4R)来划分,并同时采用了减缩积分和沙漏控制。对试样施加分别为2.0GPa和2.6GPa的载荷后,所得接触区域的Mises应力云图分布如图11。当载荷为2.0GPa时,应力集中分布于渗层内部,此时最大应力位于距表面150 μm左右的范围内,此深度与该载荷条件下亚表面裂纹出现的位置不相符。然而当载荷增大为2.6GPa时,最大应力下移至渗层与基体的交界位置,裂纹萌生位置在最大应力的范围内。由此推测,出现上述裂纹分布情况主要还与碳氮改性硬化层的厚度有关。
图11 不同载荷条件下试样亚表面应力分布图
当载荷较小时,最大应力分布于碳氮共渗层内。由于碳氮改性层内部硬度较高,相比之下过渡区处的基体材料会率先因塑性变形局域化而出现疲劳损伤。如图12所示,亚表面微观形貌随距接触表面的距离不同出现较大差异。渗层内部无典型失效特征,随深度增加基体内部开始出现较多因塑性剪切而产生“滑移线”损伤形貌。图12c为基体的放大形貌,可以看出这些“滑移线”平均长度为8 μm,普遍以垂直于接触表面的方向分布。这类微观失效形貌在所有工况条件下的失效样中均能观察到。在循环载荷作用下,“滑移线”会导致附近基体发生应力集中,当塑性变形超过材料的应变极限时易成为疲劳裂纹源。相应的当载荷增大至2.6GPa,最大应力分布位置距接触表面226 μm,最大应力处的基体会因微观缺陷如孔洞、夹杂而导致应力集中萌生微观裂纹。由于此时碳氮共渗层与基体之间的过渡区仍处于最大剪切应力的分布范围内,同样会因“滑移线”而萌生裂纹。因此在大载荷工况条件下,将导致裂纹分布深度更为广泛,在渗层过渡区和最大剪切应力分布范围内均有裂纹出现。
图12 碳氮共渗试样疲劳后横截面“滑移线”形貌图
图13 为碳氮共渗试样的滚动接触疲劳失效机理示意图。首先,在循环载荷以及摩擦力作用下,试样接触表面材料晶粒细化出现白色蚀刻层。与此同时,渗层过渡区因塑性变形局域化而出现“滑移线”的损伤形貌。然后,随着循环次数的增加,接触表面超过疲劳极限而萌生表面裂纹,表面白色蚀刻层与基体交界处出现表面平行裂纹。当表面裂纹与层间裂纹相连时出现浅层剥落坑。浅层剥落坑使试样在滚动接触过程中震动加剧,促使“滑移线” 处基体演化为亚表面裂纹并向接触表面扩展。最后,亚表面裂纹演化至接触表面,导致试样形成剥落坑而失效。
图13 碳氮共渗试样的滚动接触疲劳失效机理示意图
3 结论
(1)碳氮共渗工艺可提高滚动接触疲劳性能。载荷和滑差率越大,疲劳寿命越短。碳氮共渗试样疲劳性能的改善是表面高硬度、残余压应力以及残余奥氏体的综合作用。在滚动接触疲劳过程中,表面材料发生由应变诱导的马氏体相变。渗层内较高含量的残余奥氏体在相变过程中能延缓裂纹扩展,改善表面接触应力分布,这对于提高疲劳性能存在积极作用。
(2)碳氮共渗试样接触表面受高载高滑差作用易形成纳米梯度结构,其中表面晶粒细化程度最为严重。该结构在提高表面硬度的同时也会因与基体组织的不兼容而诱发表面平行裂纹,裂纹演化至表面导致浅层剥落。
(3)亚表面裂纹是导致碳氮共渗试样疲劳失效的主要原因,裂纹萌生位置受最大应力和渗层厚度的共同影响。亚表面裂纹扩展至表面或与表面裂纹连接,产生剥落坑失效形貌。
参考文献: 略
免责声明:本网站所转载的文字、图片与视频资料版权归原创作者所有,如果涉及侵权,请第一时间联系本网删除。
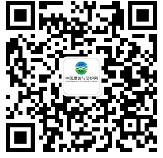
官方微信
《腐蚀与防护网电子期刊》征订启事
- 投稿联系:编辑部
- 电话:010-62316606-806
- 邮箱:fsfhzy666@163.com
- 腐蚀与防护网官方QQ群:140808414