加氢裂化空冷器管束多相流冲刷腐蚀数值模拟
空气冷却器 (空冷器) 是渣油加氢过程中的重要设备,会承受流体劣质化、工况苛刻化、长周期甚至超负荷运行的考验。空冷器及相关管道的腐蚀损伤显着地影响加氢过程的安全稳定运行。空冷器管束的失效形式较多,其中管子是最常见的失效部件,通常与流体的流动状态、流体的腐蚀性有关,特别是在空冷器管束的进口端腐蚀最严重,主要的腐蚀形式为冲刷腐蚀。
冲刷腐蚀是金属表面与腐蚀性流体之间由于高速相对运动而产生的金属损坏现象,是冲刷磨损和电化学腐蚀交互作用的结果[2]。冲刷腐蚀过程影响因素众多,主要有固体颗粒的含量、直径、冲击速度、冲击角度、与基材的相对硬度、冲击频度以及流体介质的性质、流速[8,9,10]、流态等。按冲刷腐蚀所涉及的介质种类的不同,可以把冲刷腐蚀分为3类:单相流、两相流、多相流冲刷腐蚀[3,11,12,13]。单相流冲刷腐蚀是由高速流动的单相腐蚀流体造成的,涉及的工业设备主要是输送高纯度的腐蚀性液体的过流部件;两相流冲刷腐蚀是最常遇到的,工业背景十分普遍,它还可以进一步细分为气/液、气/固、液/固等几种类型;多相流冲刷腐蚀是由气/液/固等组成的多相流引起的,其过程较复杂,工业背景较普遍。
偶国富等[14,采用数值模拟研究了空冷器内气/液两相流动及换热情况,表明第一排管束发生冲刷腐蚀的可能性最大,上排冲刷腐蚀的位置主要集中在正对法兰出口及管箱两侧的管束,下排冲刷腐蚀的位置主要集中在正对法兰出口的管束。Sun等[16]利用数值模拟与实验相结合的方法研究了空冷器处理含铵盐物系的冲刷腐蚀现象,表明空冷器第一排管束发生了严重的冲刷腐蚀,且腐蚀位置主要在距离管束进口5.8 m处,该处水相比率最高且NH4HS的浓度最高。Valeh-E-Sheyda等[17]采用化学分析法、失重法、电化学法和涡流法测定腐蚀产物和腐蚀速率,并数值模拟了空冷器内部管束冲刷腐蚀状况,表明冲刷腐蚀是由于快速旋转流动而引起管束进口处湍动能变大而导致的。上述研究仅对空冷器内冲刷腐蚀的位置进行了模拟,但并未对空冷器内部冲刷腐蚀的数量以及冲刷-腐蚀的交互作用进行分析,故而难以全面理解空冷器内部管束冲刷腐蚀的现象。
本文以某石化厂渣油加氢装置分馏塔顶空冷器为研究对象,基于现场生产过程实际腐蚀状况,采用数值模拟对空冷器内部气/液两相流动与传热进行模拟,通过空冷器管束内部流动状况确定冲刷腐蚀位置及其腐蚀程度,并与实际腐蚀情形作对比。进而考察空冷器结构变化对空冷器管束内流体动力学参数分布规律的影响,目的在于优化空冷器结构,提高空冷器长期运行的可靠性。
1 冲刷腐蚀模型
冲刷腐蚀模型可分为电化学腐蚀模型和机械冲刷模型,由机械磨损和电化学腐蚀的交互作用引起的金属材料的腐蚀速率大于两者单独作用时的腐蚀速率之和。文献研究表明,冲刷腐蚀速率KEC可表示为:

其中,KEC为总的冲刷-腐蚀速率,kg·m-2·s-1;KC是在冲刷情况下的腐蚀速率,kg·m-2·s-1;KCO是纯腐蚀速率,kg·m-2·s-1;KE是在腐蚀情况下的冲刷速率,kg·m-2·s-1;KEO是纯冲刷速率,kg·m-2·s-1;ΔKC?KC是冲刷协同效应影响的腐蚀速率,kg·m-2·s-1;ΔKE?KE是腐蚀协同效应影响的冲刷速率,kg·m-2·s-1。
针对冲刷腐蚀过程,可区分为如下4个腐蚀过程[19],即:KCKE<0.1KCKE<0.1时,冲刷占主导;0.1≤KCKE<10.1≤KCKE<1时,冲刷-腐蚀占主导;1≤KCKE<101≤KCKE<10时,腐蚀-冲刷占主导;KCKE≥10KCKE≥10时,腐蚀占主导。
1.1 电化学腐蚀模型
首先,H2S溶解在水中,电离出H+,HS-和S2-,然后溶解有H2S的液滴撞击金属壁面,在金属壁面表面形成一层水膜,金属壁面为阳极,阳极金属表面失去电子生成的Fe2+与水膜中的HS-和S2-结合生成FeS和FeS2,FeS和FeS2在金属壁面形成一层腐蚀产物膜,该腐蚀产物膜可保护金属进一步被氧化腐蚀。
H2S的电化学腐蚀速率可表示为:

其中,fd=2/3;fe=1.3;ZH2SZH2S和ZW分别为H2S和金属壁面转移的电子数;DH2SDH2S为H2S的扩散系数,m2·s-1;Cb,H2SCb,H2S为H2S的质量浓度,kg·m-3;Ug为气相速度,m·s-1;νgνg为气相运动粘度,m2·s-1;MH2SMH2S为H2S的摩尔质量;MW为碳钢的摩尔质量;dW为管径,m。
1.2 机械冲刷模型
液滴冲刷过程如图1所示。当球形粒子冲击材料基体时,粒子中心将沿一条曲线运动,这条曲线可以分为3个部分:(1) oa段代表基体的弹性变形,如果形变只在这段范围内发生,那么在冲击之后基体将会重新恢复到原来的形状;(2) ab段代表基体的塑性变形,在b点处粒子的垂直速度分量将达到零;(3) bc段代表冲击粒子的反弹过程,这是由于弹性斥力和粒子的水平速度分量造成的,在这一过程中基体将进一步产生形变,同时粒子动能将进一步减小。在液滴与金属壁面撞击的过程中考虑了液滴变形,液滴与气相间的曳力。

液滴与管壁碰撞所导致的冲刷速率可表示为:

其中,ER为冲刷速率,mm·a-1;C=3.15×1010,转换因子,由m·s-1到mm·a-1;un为液滴的速度,m/s;mdrop为撞到壁面的颗粒质量流率,kg·s-1;A为颗粒撞击壁面的面积,m2;ρw为壁面金属材料的密度,kg·m-3;K为与钢的结构有关的常数,碳钢取2×10-9。根据文献,n=5;F(α)为与碰撞角度有关的函数,对韧性金属和脆性金属,F(α) 如图2所示。

2 空冷器工艺条件
空冷器结构上设有6排管束,双管程布置,每个管程有3排管束,每排管束38根管,呈三角形排列。空冷器管束规格为Φ25 mm×2.5 mm×9000 mm,空冷器每排管束之间的距离为60 mm,相邻管束间的距离为58 mm。
空冷器内部流体为石脑油和水的混合物,其中水占18.3% (质量分数),石脑油占81.7%。石脑油组成为:C3 0.08% (质量分数),C4 0.37%,C5 1.52%,C6 8.35%,C7 18.36%,C8 30.95%,C9 29.55%,C10 10.04%,C11 0.78%,N6 mg·kg-1,S 0.0289%。可以看出,N含量较少,可忽略不计;S含量为0.0289%,且主要以H2S形式存在,会产生严重的电化学腐蚀。流体流动状态为气/液两相流,气/液两相的工艺参数如表1所示。

空冷器实际腐蚀情况如图3所示,运行8个月左右空冷器管束因腐蚀穿孔损坏停止运行。图中红色标记代表腐蚀穿孔的管束。可以看出,第一排管束腐蚀最为严重且集中在空冷器进口的两侧,第二排管束有三根管因腐蚀穿孔发生泄漏,而其它管束未出现。

3 CFD模型
由于空冷器腐蚀位置主要集中在前三排管束,为此本文研究亦集中在前三排管束,采用混合网格对其进行网格划分。
本文采用Mixture模型和k-ε模型描述多相湍流流动过程,连续相为气相,离散相为水相。进口边界条件为质量流速进口,出口边界条件为压力出口;空冷器进口温度为126.6 ℃,第一管程出口温度为104 ℃,其中涉及到流体的相变过程。因此,将气相的凝结过程通过用户自定义函数 (UDF) 编译到Fluent中。壁面采用标准壁面函数处理。首先进行网格无关性检验,当网格数为321万与网格数为431万时的液滴速度分布是一致的,所以选定的网格数为321万,如图4所示。

4 结果与讨论
4.1 管束流速分析
图5是各排管束中流体法向速度分布图。当流体为气/液两相流时,作用在冲刷面上的力可分为法向力和切向力,法向力产生撞击作用,切向力产生切削作用。法向速度和切向速度分布可反映法向力和切向力分布。可以看出,各排管束中流体的法向速度分布均匀,且数值较小,对管束产生的法向撞击作用较小。
图6是各排管束中流体的切向速度分布图。可知,各排管束中切向速度分布极不均衡,变化较大,所以流体对壁面产生的切削作用较大。

4.2 管束流动偏流情形分析
在此,引入偏流比,定义为每排管束某根管子中流体流速与该排管束中流体平均流速之比。每根管子偏流比可反映管束流体分布状况。
当偏流比接近于1时,管束流体分布最为均衡。由图7可知,各排管束流体分布极不均衡,偏流比在0.6~1.85之间变动。偏流比变化越大,湍动能在管束内分布就越不均衡。

4.3 湍动能分析
由图8a可知,在管束进口位置处,流体的湍动能变化较大,特别是5,6,7,12,13,14,17,18,19,20,21,25,26,27,33,34,35根管进口处湍动能变化最大。所以,这些管束最先被流体冲刷使其失效。由图8b可知,在管束进口位置处,流体的湍动能变化较大,在3,4,5,13,14,15,16,23,24,25,26,33,34,35,36根管束的进口位置湍动能变化最大,所以在这些管束的进口位置是冲刷最严重的。从图8c可以看出,第三排管束湍动能较小且变化不大,基本不被流体冲刷而破坏。
4.4 冲刷腐蚀分析
图9和10分别是第一排管束第5根管的XY平面冲刷速率分布和电化学腐蚀速率分布。从图9可以看出,左壁面 (XY平面左侧) 冲刷速率要远大于右壁面 (XY平面右侧) 冲刷速率,最大值为4.76 mm·a-1。从图10可以看出,左壁面的电化学腐蚀速率大于右壁面的,最大值仅为6.5×10-4 mm·a-1。与冲刷速率相比,电化学腐蚀速率可以忽略。与空冷器实际腐蚀速率相比,模拟结果与实际结果基本一致。
5 空冷器结构优化
空冷器冲刷腐蚀的主要原因是气/液流动不均匀,进而导致空冷器管束湍动能分布不均匀。为此,本文提出为了使空冷器气/液分布均匀,使空冷器进口管增加到4个,改进的空冷器结构见图11。

5.1 结构优化后管束中流速分析
图12是优化后各排管束中流体的法向速度分布图。可以看出,各排管束中法向速度分布均匀,且管束内法向速度较小,对管束产生的法向撞击作用较小。



图13是空冷器结构优化后各排管束中流体的切向速度分布图。可以看出,各排管束中切向速度分布极不均衡,变化较大,且第一排管束切向速度比优化之前的小约10 m·s-1,第二排管束切向速度比优化之前的小约11 m·s-1,第三排管束切向速度比优化之前的小约17 m·s-1,所以结构优化之后的空冷器能大大降低冲刷对管束的损伤。

5.2 结构优化后管束中流体流动偏流情形分析
图14为空冷器结构优化后各排管束中偏流比分布图。可知,各排管束中流体分布比较均衡,且偏流比在0.7~1.3变化,变化幅度较小,所以湍动能在管束内分布均衡性大为提高。

5.3 结构优化后湍动能分析
图15为空冷器结构优化后各排管束中湍动能分布图。可知,湍动能分布基本比较均匀,在管束进口位置处,流体的湍动能变化比较大,但是相对进口为2个的时候,湍动能比较小,在管束进口位置之后,流体的湍动能基本不变化,特别是5,6,9,10,11,18,19,29,30,33,34根管进口处湍动能变化最明显,所以,这些管束无疑是冲刷最严重的,最先被流体冲刷使其失效。由图15b可知,空冷器管箱内的湍动能和空冷器管束进口端湍动能变化较大,在第1,2,3,4,5,12,13,25,26,35,36,37根管束的进口位置湍动能变化很大,其它管束的湍动能基本不变化,所以在这些管束的进口位置是冲刷最严重的,即这些管束最先被流体冲刷破坏而失效。由图15c可知,第三排管束湍动能较小且变化不大,基本不被流体冲刷而破坏。
5.4 结构优化后冲刷腐蚀分析
图16和17分别是第一排管束第5根管的冲刷速率分布和电化学腐蚀速率分布。从图16可以看出,左壁面的冲刷速率要远大于右壁面的,最大值为0.18 mm·a-1。从图17可以看出,左壁面的电化学腐蚀速率大于右壁面的,最大值仅为3×10-4 mm·a-1。与冲刷速率相比,电化学腐蚀速率可以忽略。


改进后的空冷器与之前相比,冲刷速率和电化学腐蚀速率都大大降低,大幅度提高了空冷器的寿命,增加空冷器运行稳定性。
6 结论
(1) 针对一种空冷器的散热管束,建立了反映不同结构特征的冲刷腐蚀流体分析模型,考虑了柔性液滴相与管壁的碰撞行为。
(2) 空冷器管束中气/液双相流体的切向力是产生冲刷作用的主要因素,法向力是产生冲刷作用的次要因素。
(3) 与腐蚀速率相比,冲刷居于主导作用。左壁面 (XY平面左侧) 冲刷速率要远大于右壁面 (XY平面右侧) 冲刷速率,最大值为4.76 mm/a。左壁面的电化学腐蚀速率大于右壁面的,最大值仅为6.5×10-4 mm/a。与冲刷速率相比,电化学腐蚀速率可以忽略。
(4) 将空冷器的进口管由2根增加到4根,改进后的空冷器管束内部流体的流动相对稳定。与改进前相比,改进后空冷器内部流体流动更加均匀,消除了偏流,冲刷腐蚀位置基本未变,但冲刷腐蚀速率大大降低,最大冲刷速率降低为0.18 mm/a,电化学腐蚀速率降为3×10-4 mm/a,改进效果明显。
注:文章、作品、图片版权归作者享有,如有作者来源标记有误或涉及侵权,请原创作者联系小编删除。
免责声明:本网站所转载的文字、图片与视频资料版权归原创作者所有,如果涉及侵权,请第一时间联系本网删除。
相关文章
无相关信息
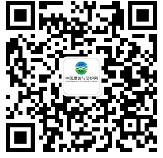
官方微信
《中国腐蚀与防护网电子期刊》征订启事
- 投稿联系:编辑部
- 电话:010-62313558-806
- 邮箱:fsfhzy666@163.com
- 中国腐蚀与防护网官方QQ群:140808414
点击排行
PPT新闻
“海洋金属”——钛合金在舰船的
点击数:5768
腐蚀与“海上丝绸之路”
点击数:4763