随着油气行业的不断发展,采用高钢级、大口径、高压力输送管道是重要的生产趋势,但管线钢强度越高,氢脆敏感性就越高。
目前,针对输氢管道,国际上制定了相应的技术规范,但目前我国拟采用或正在运行的煤制气管道大部分为X70和X80高级管线钢,高于国内外有文献记载的输氢管道规范要求,同时,现有规范只针对H2及H2/CO混合气体的输配系统给出了一些需要考虑的安全问题,针对低含氢环境(氢气的体积分数为2%~6%)中管道的设计,目前还没有相应的标准。
近年来,煤制气管道氢脆敏感性问题得到了越来越多学者的关注和研究,但尚未形成统一的测试评价体系,同时对评价指标的选择也存在差异,不同评价指标对现场管线实际运行、控制的指导意义也有待进一步明确。因此,本工作通过对现有输氢管道及储氢容器标准进行梳理。
含氢管道脆化与环境损伤类型
01 氢致应力开裂
氢致应力开裂(HSC)具有滞后性,材料需要在氢和应力的持续作用下发生脆性断裂,且多数情况下,导致断裂的应力低于材料的屈服强度,这给管道的安全运行带来风险。
HSC最容易在室温条件下发生,在含氢环境中,敏感材料的断裂韧性参数较在惰性气氛中的降低,性能损失幅度与材料和环境因素有关。
根据管道缺陷处产生的应力和缺陷尺寸能够对管道的开裂风险进行判断:钝状缺口,如腐蚀是不会产生较大应力集中的;锋利的缺陷,如裂纹是会产生较大应力集中的,需要重点关注。
HSC测试的结果可以用来评估工程结构中可接受的临界缺陷尺寸,为管道完整性管理和裂纹检测提供依据。
02 塑性和强度降低
高钢级管线钢在氢的作用下,塑性和强度会降低,特别是存在缺陷的情况下,降低幅度更为明显。根据ASME B31.12-2014《Hydrogen Piping and Pipelines》标准,紧固试样的过早爆破,也是强度损伤的一种表现。因此,管线钢材料的拉伸指标及爆破压力变化测试,对于评价管线钢的氢脆敏感性,确定管线设计的应力及应变系数,具有重要的指导意义。
03 氢致疲劳裂纹扩展
高钢级管线钢在氢和疲劳载荷的作用下通常会表现出疲劳裂纹扩展速率的增加和疲劳裂纹扩展门槛值ΔKth的降低,进而对材料抵抗疲劳载荷的能力及服役寿命产生影响。虽然管线运行中的温度、压力波动不大,但疲劳载荷在特殊工况及穿跨越等特殊环境中,也可能造成管线失效。因此,管线钢在含氢环境中的疲劳性能测试,对于管线运行载荷波动控制及管线受力设计具有重要的指导意义。
煤制合成天然气管道的适用性评价方法
01 断裂韧性测试
● 断裂韧性测试方法的选择受管线壁厚的影响,当管线壁厚满足式(1)的要求时,材料满足平面应变状态,可以采用GB/T 4161-2007《金属材料平面应变断裂韧度KIC试验方法》中的方法对断裂韧性进行测试。
B≥2.5(KIC/RP0.2)2(1)
式中:B为试样厚度;KIC为材料的断裂韧性;RP0.2为屈服强度。
● 当试样尺寸不能满足平面应变状态时,可以参考GB/T 2038-1991《金属材料延性断裂韧度JIC试验方法》中规定的金属材料的延性断裂韧度JIC的测试方法,并根据JIC的测试结果转换成KIC,标准规定测试时试样尺寸需要满足式(2)要求。
B>25JIC/RP0.2(2)
● 当试样的尺寸不能满足式(1)和(2)的要求时,可以参考GB/T 2358-1994《金属材料裂纹尖端张开位移试验方法》中规定的金属材料裂纹尖端张开位移的测试方法,并根据特征裂纹尖端张开位移(CTOD)值采用式(3)进行计算。
(3)
式中:mCTOD为转换常数,取1.4;σf为流变应力,σf=1/2(σy+σμ),MPa;σy为材料屈服强度,MPa;σμ为材料抗拉强度,MPa;δcrit为极限裂纹尖端张开位移值,m;Ey为弹性模量,取206×105MPa;v为泊松比,取0.3。
无论采用上述哪种方法,KIH的测试均需要在含氢环境中进行,同时需要保证测试前X80钢试样在含氢环境中暴露足够的时间以满足平衡状态,并采用合适的载荷/应变速率。该测试能够获得试样在含氢气环境中的临界应力强度因子,可用来评估工程结构中可接受的临界缺陷尺寸,为管道完整性管理和裂纹检测提供依据。
除此之外,ASME B31.12-2014中规定了基于材料断裂韧性的使用资格评价方法,该方法旨在判断规定壁厚材料在规定气氛环境中的适用性。测试采用紧凑拉伸(CT)试样,沿管道TL方向(试样断面法向平行于管道环向)取样,试样的有效厚度应不小于管道壁厚的85%。将预制有疲劳裂纹的试样放入含氢环境中进行恒载荷加载,应力强度因子选择KIAPP和中的最大值,其中KIAPP为设计压力下管道表面椭圆裂纹的应力强度因子,椭圆裂纹的深度为1/4t,长度为1.5t,t为管道壁厚。试验1000h后,将试样沿裂纹打开,观察25%,50%和75%壁厚位置处的裂纹扩展情况:若平均裂纹扩展长度超过0.25mm,则材料不能在试验环境中使用;若平均裂纹扩展长度低于0.25mm,则材料可以在试验环境中使用。
02 缺口试样拉伸试验和慢应变速率试验
缺口拉伸试验和慢应变速率试验测试方法参考标准ASTM G 142-98《Standard Test Method for Determination of Susceptibility of Metals to Embrittlement in Hydrogen Containing Environments at High Pressure,High Temperature,or Both》进行,将轴对称缺口拉伸试样或光滑试样置于常温常压和典型煤制气含氢环境中施加单轴拉伸应力。缺口拉伸试验测试环境中氢气组分对材料在三向应力集中区域的氢脆行为的影响,而慢应变速率试验包括了裂纹孕育、裂纹亚稳扩展及失稳扩展三个阶段,这两种方法都能够有效评价X80钢对氢的敏感性。
通过标准及文献调研,缺口拉伸试验和慢应变速率试验的测试结果可以从两方面进行分析:
(1)力学性能变化
可比较暴露在含氢环境和非含氢(常温常压)环境中的同种试样的力学性能,进而评定材料的氢脆敏感性,见式(4)。
比值=试样在试验环境中得到的结果/试样在惰性介质环境中得到的结果(4)
(2)断口形貌观察
GB/T 9711-2011《石油天然气工业管线输送用钢管》指出,可以在试样完全被破坏后,采用低倍显微镜检查二次裂纹,或通过观察断口微观形貌检查断裂模式的变化,来确定试样是否发生氢脆断裂。
对于X80钢,空气中拉断的断口为韧性断口,会有明显的颈缩区域,因此,若断口出现脆性区域,表明材料受到氢的影响,发生氢脆开裂。
03 紧固圆盘压力试验(碟形爆破)
碟形爆破试样参照ASTM F 1459-06《Standard Test Method for Determination of the Suscepitibility of Metallic Materials to Hydrogen Gas Embrittlement》进行,测试装置如图1所示。
图1 蝶形爆破测试装置示意图
综合标准和实际管道运行环境,分别采用纯氦气(纯度为99.995%)、以及含氢煤制气进行试验。增压速率在标准规定的范围内进行选择。根据标准规定,PHe/P煤制气的最大比率可以评价材料的氢脆敏感性:比率为1,材料对环境不敏感;比率高于2,材料对环境敏感,应避免在此种环境中使用;比率介于1~2,材料长时间暴露在这种环境中,可能会导致氢脆。
04 疲劳裂纹扩展试验
疲劳裂纹扩展试验参照ASME B31.12-2014和ASTM E647-2005《测量疲劳裂纹增长率的标准试验方法》进行,试样壁厚应不低于管道壁厚的85%,TL方向取样。标准规定,评价气态氢气影响时,测试频率不应超过0.1Hz,测试应力Kmin/Kmax不应低于0.1。
试验使暴露在常温常压和典型含氢煤制气环境中的试样承受疲劳载荷,比较氢对于材料疲劳裂纹扩展速率和疲劳裂纹扩展门槛值的影响,从而有效评价材料对氢的敏感性。
结论
(1)含氢煤制气环境中的管道需要考虑的脆化和损伤类型主要有氢致应力开裂,塑性与强度降低以及氢致疲劳裂纹扩展。
(2)含氢煤制气环境中管道材料的适用性评价方法包括氢致断裂韧性KIH测试,缺口试样拉伸试验和慢应变速率试验,含氢环境中的碟形爆破压力测试以及含氢环境中的疲劳扩展速率及门槛值测试。
(3)根据含氢煤制气环境中管道材料的适用性评价结果,可以从管段临界缺陷尺寸,管道设计应力及应变系数,管道波动载荷控制几个角度,对管道的建造和维护提供数据支持。
更多关于材料方面、材料腐蚀控制、材料科普等方面的国内外最新动态,我们网站会不断更新。希望大家一直关注中国腐蚀与防护网http://www.ecorr.org
责任编辑:殷鹏飞
《中国腐蚀与防护网电子期刊》征订启事
投稿联系:编辑部
电话:010-62313558-806
邮箱:fsfhzy666@163.com
中国腐蚀与防护网官方 QQ群:140808414
免责声明:本网站所转载的文字、图片与视频资料版权归原创作者所有,如果涉及侵权,请第一时间联系本网删除。
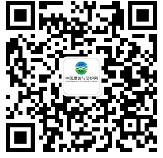
官方微信
《中国腐蚀与防护网电子期刊》征订启事
- 投稿联系:编辑部
- 电话:010-62313558-806
- 邮箱:fsfhzy666@163.com
- 中国腐蚀与防护网官方QQ群:140808414