0 引言
聚脲/聚氨酯涂层以其自身优异的耐腐蚀、耐冲击、耐磨损及耐老化等性能,在防护过程中,充分展现出零 VOC排放,符合国家环保型材料的要求,这种新型绿色环保型材料已在混凝土涂层防护领域中得到了非常广泛的应用,已被应用在各大型防护工程中。
喷涂聚脲弹性体技术于20世纪90年代在美国初首先研发成功,我国对聚脲/聚氨酯涂层的研究起步较晚,1995年,黄微波等开始了对聚脲技术的研究和开发,历经十余年的不断发展,聚脲材料在其应用领域范围内取得了很大突破。作为一种有机涂层,聚脲/聚氨酯涂层在其服役环境中也面临着各种腐蚀老化问题。因此,对聚脲/聚氨酯涂层的老化行为、抗氯离子渗透性能及介质腐蚀等性能进行研究,可以更好的对聚脲涂层的使用寿命进行预测。目前,聚脲/聚氨酯涂层已成功应用在京沪高铁、港珠澳大桥、青岛杭州湾和胶州湾大桥等大型建筑工程。
1 耐久性研究
1.1 抗氯离子渗透性研究
黄微波等通过自然浸泡和干湿循环法对聚脲和聚氨酯涂层混凝土抗氯离子渗透性能进行了研究,自然浸泡120 d的试验结果表明:与无涂层混凝土相比,涂覆聚脲涂层的混凝土Da降低67.9%,涂覆聚氨酯的混凝土Da降低67.8%;干湿循环120次试验结果表明:与无涂层混凝土相比,涂覆聚脲的混凝土Da降低76.7%,涂覆聚氨酯的混凝土Da降低76.6%。可见,聚脲和聚氨酯均能对混凝土起到良好的抗氯离子渗透性能。孙丛涛等对复合型涂层、成膜型环氧涂层、渗透型硅烷及成膜型聚脲涂层进行抗氯离子渗透性、透气性及透水性试验,研究结果表明:在抗氯离子渗透性方面,不同类涂层表现出的效果不同,其中,成膜型涂层和复合涂层的效果明显比渗透型涂层好,聚脲涂层的效果最为优异,氯离子扩散系数降低95.8% ~ 97.2%。伯忠维采用浸泡法对比研究了聚脲、环氧和氯化橡胶涂层砂浆在3.5%氯化钠溶液中的抗氯离子渗透性能,结果表明:浸泡90 d后,与空白试样相比,聚脲、环氧和氯化橡胶三种涂层砂浆在6 mm深度处的Cl-1含量分别为3.41%、4.64%和5.72%,由此可见,聚脲涂层的抗氯离子渗透性能比其他两种涂层显着。杨林等采用自然浸泡和RCM法对喷涂聚脲的混凝土抗氯离子渗透性能进行了研究,结果表明:涂刷80 μm的脂肪族聚脲混凝土和芳香族聚脲混凝土在自然浸泡100 d后,Da分别降低49.39%和44.14%;涂刷由80 μm增加到240 μm的上述两种聚脲涂层混凝土在快速氯离子渗透试验时,脂肪族聚脲涂层混凝土Da降低25.19%,芳香族聚脲涂层混凝土Da降低53.80%;可见,脂肪族聚脲涂层的抗氯离子渗透性能优于芳香族聚脲涂层。
1.2 介质腐蚀研究
吕平等采用海水浸泡、硫酸浸泡和氢氧化钠浸泡等方法对聚脲涂层的耐离子腐蚀性能进行了研究,并通过SEM进一步对聚脲涂层老化后表面的形貌特征进行了观察,结果表明:海水浸泡180 d后,聚脲涂层的拉伸强度仅下降了4%,硫酸浸泡60 d后,涂层的拉伸强度降低30%,但仍保持在15 MPa以上涂层面出现微小孔洞,氢氧化钠浸泡60 d后,拉伸强度降低25%,仍保持在17 MPa以上,可见,海水对脲涂层的性能影响不大,而在硫酸和氢氧化钠浸泡下,聚脲涂层的耐腐蚀性能有所降低。李海扬等对环氧云铁、聚氨酯和聚脲涂层在5%NaCl溶液浸泡作用下的耐腐蚀性能进行了研究分析,结果表明:浸泡90 d后,聚氨酯、环氧云铁和聚脲涂层的失光率分别是4.2%、19.1%和16.7%,附着力分别下降17.65%、52.94%和55.11%;SEM图中发现聚氨酯涂层出现泛白现象,环氧云铁涂层出现轻微裂纹,而聚脲涂层仍保持良好的附着性,涂层结构保持紧密,金属基材出现轻微的腐蚀现象,表现出良好的防护性能。吕平等通过介质浸泡试验对桥梁支座防护材料的耐腐蚀的性能进行了研究,结果表明:经过90 d的5%硫酸、5%氢氧化钠和3.5%氯化钠浸泡后,聚脲涂层的拉伸强度分别下降13.73%、8.13%和12.44%,涂层硬度变化较小;FT-IR测试结果表明聚脲涂层老化后仅表面小部分化学键出现断裂,但涂层内部结构变化不大,涂层仍有较强的耐腐蚀性能。刘培礼等对芳香族聚脲的耐介质性能进行了研究,结果表明:碱对聚脲的强度影响不大,高浓度的酸对聚脲涂层的拉伸强度有很大的影响,聚脲涂层在50%的硝酸中浸泡2 d后就完全失去性能。Ping Lu等对单一NaCl溶液浸泡、荷载和NaCl溶液浸泡共同作用下聚天门冬氨酸酯聚脲涂层混凝土的性能进行了研究,结果表明在荷载和NaCl溶液浸泡共同作用下涂层混凝土中氯离子的含量明显高于单一NaCl溶液浸泡中氯离子的含量。
1.3 老化性能研究
黄微波等采用FT-IR、DSC等试验方法,对纯聚脲重防腐涂层在海洋大气环境中的耐久性进行了研究,试验结果表明:在户外自然曝晒600 d后,纯聚脲重防腐涂层的光泽度发生较大的变化,下降94.53%,涂层力学性能基本保持不变;人工加速老化15 000 h后,涂层已无光泽度可言,涂层内有机染料出现变黑现象,力学性能变化幅度较小;FT-IR、DSC测试结果表明纯聚脲重防腐涂层在自然曝晒和人工加速老化两种环境中,仅涂层表面染料分子的化学键出现断裂、褪色或变黑现象,涂层内部分子结构仍保持稳定,涂层保持良好的防护性能。对在露天海水池中自然曝晒6个月的纯聚脲重防腐涂层进行划叉试验,结果表明纯聚脲重防腐涂层比其他重防腐涂层的防护效果更加优异。
何筱姗研究了自然暴晒、紫外线人工加速老化及腐蚀介质浸泡条件下桥梁钢绞线和支座防护涂层的性能,研究结果表明:聚脲涂层的防护性能表现最好。吕平等通过SEM、AFM及FT-IR方法,对聚天门冬氨酸脂聚脲涂层的加速老化行为进行了系统地研究,结果表明:紫外线/盐雾循环加速老化10周时,涂层表面局部已经产生孔洞,加速老化25周后,涂层表面产生裂纹,且裂纹已延伸至涂层内部,涂层已从基材表面脱落,完全失去对基材的保护作用。张寒露等采用FT-IR和SEM等手段对三亚地区自然曝晒和氙灯加速老化的聚氨酯涂层失效行为进行研究,研究结果发现:与未老化涂层相比,室外自然曝晒18个月后的聚氨酯涂层表面产生裂纹,与氙灯加速老化4 600 h的涂层相比,涂层表面裂纹较浅,裂纹内出现白色沉积物。李倩倩等在万宁近海地区对丙烯酸聚氨酯涂层进行为期2年的自然老化试验研究,探讨了涂层的老化历程和机理,研究结果表明:老化初期涂层的光泽变化显着,老化的方式为水解老化,氯离子的侵入是导致涂层中期老化的主要主要原因,老化1 a左右时,涂层的老化速度变慢,这时涂层的老化主要是由于光氧化的作用导致。
1.4 其他耐久性研究
Damith等对聚脲涂层复合铝板在低速冲击作用下的性能进行了研究,结果发现复合铝板的横截面积没有出现拉伸、撕裂、脱层或剪切等破坏现象,表明聚脲涂层具有很好的抗冲击性。Willians等对聚脲涂层的污水处理设施进行了研究,结果表明:聚脲的抗冲击性、耐磨损和耐化学性都很突出,有助于延长污水设施的寿命以及防止废水和地下水的渗入渗出。李宁等在空蚀模拟试验机上对研制的聚天冬氨酸酯聚脲进行了抗加速空蚀性能的研究,试验结果表明研制的天门冬氨酸酯聚脲具有更优异的抗空蚀性能。李建波等对大坝用聚脲涂层的抗渗性能进行了研究,结果表明聚脲涂层的厚度为4 mm时,可满足宽度为5 mm的裂缝在300m水压力作用下的抗渗要求。钟萍等通过GSPS-S型高速含沙水射流冲蚀磨损试验机对聚脲涂层的耐冲蚀磨损性能进行了研究,对不同冲蚀角度和速度下聚脲涂层的冲蚀规律,结果表明:冲蚀角度为30°时,涂层的切削磨损量达到最大,冲蚀角度接近90°时,涂层的变形磨损量是最大的。
2 耐久性相关模型
刘凉冰通过加速老化试验,对共聚醚聚氨酯断裂伸长率随老化时间的变化规律进行了研究,并对此建立了相关模型:log t=3.1097×1/T×103-4.855,对聚氨酯材料进行了寿命预测,预测涂层在25℃下的使用寿命为21 a。余超等研究了聚氨酯涂层拉伸强度与时间的变化规律,并通过试验得老化动力学参数,对聚氨酯涂层建立了基于拉伸强度的数学模型:σ=20.31exp(-1.65×10-3t0.68),预测聚氨酯涂层在25 ℃下的使用寿命为19.7 a。李春涛等采用热重法对PTMG聚氨酯涂层进行分析,将热失重5% 的温度作为材料的失效标准,建立降解动力学模型,并对涂层的使用寿命进行预测,结果得出涂层使用寿命与温度的关系式:ln tf = 15 700 /T -30. 78。
3 结语
目前,国家大力倡导环境友好型防护涂层,聚脲/聚氨酯涂层正在向该方向发展,而涂层的耐久性能已成为关键问题。单因素作用下涂层的耐久性问题已取得了一部分成果,在涂层老化方面已经建立了相应的模型,但在冻融等方面的对量分析及模型的建立还有待研究,多种因素共同作用下的涂层耐久性研究鲜有报道。
聚脲/聚氨酯涂层因自身已具备较好的耐久性能,在各种环境中能起到很好的防护作用。但在聚脲/聚氨酯涂层中添加ZnO、石墨烯等成分,会使涂层的耐久性能更加优异,这也是聚脲/聚氨酯涂层今后研究的新方向。
更多关于材料方面、材料腐蚀控制、材料科普等方面的国内外最新动态,我们网站会不断更新。希望大家一直关注中国腐蚀与防护网http://www.ecorr.org
责任编辑:王元
《中国腐蚀与防护网电子期刊》征订启事
投稿联系:编辑部
电话:010-62313558-806
邮箱:fsfhzy666@163.com
中国腐蚀与防护网官方 QQ群:140808414
免责声明:本网站所转载的文字、图片与视频资料版权归原创作者所有,如果涉及侵权,请第一时间联系本网删除。
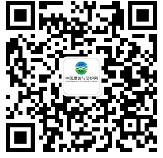
官方微信
《中国腐蚀与防护网电子期刊》征订启事
- 投稿联系:编辑部
- 电话:010-62313558-806
- 邮箱:fsfhzy666@163.com
- 中国腐蚀与防护网官方QQ群:140808414