随着现代经济社会的迅猛发展,人们对汽车的使用越来越多,因此对汽车的安全性、舒适性和环保性提出了更高要求。这就使得更多的附加设备加入到汽车上,相应的,汽车的总质量也就增加了很多。而研究数据表明,汽车总质量每减轻l0%,油耗可降低6%~7%。对空载而言,约70%的油耗是用在车身质量上的,因此车身的轻量化不仅减轻了汽车质量,而且提高了整车的燃油经济性,减少了污染。除此之外,汽车的轻量化还可使得车辆操纵稳定性和冲撞安全性得到提升,使其更加稳定。因此,在当前经济环境下,轻量化技术在汽车工业的发展中起着重要作用。
汽车的轻量化是指应用优化设计的方法,在确保汽车的强度和安全性能的前提下,提高材料的利用率,减少冗余材料,以达到减轻车身质量的目的,从而提高汽车的动力性,减少燃料消耗,降低排气污染。目前,汽车轻量化的主要途径有两个:一是采用轻量化材料,如铝合金、镁合金、塑料、复合材料等重量更轻、强度更高的新材料;二是采用先进的计算机结构设计技术,如有限元分析,局部加强设计,来优化设计汽车的结构,使零部件薄壁化、中空化、小型化、复合化,以及对零部件进行结构和工艺改进等,从而最大限度减轻零部件的质量。鉴于此,本文采用镁合金这种轻质材料来替代钢结构,达到汽车轻量化的目的。
1镁合金材料及其在汽车车身上的应用
镁合金材料是现在机械工业上发展前景较好的金属材料,因为镁合金材料密度小、质量轻、比强度高,并且具有良好的加工和铸造性能,加工后的尺寸可保持良好的稳定性,具有良好的导热性能。此外,镁合金对振动,冲击的吸收性能好。将镁合金、铝合金、塑料以及钢结构的力学性能作对比,如表1。
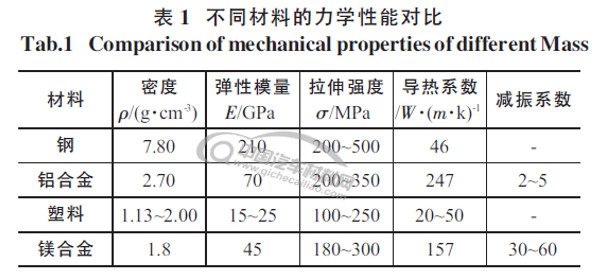
由表1可知,镁合金材料与其他几种材料相比,它是属于最轻的材料,并且其弹性模量较低,因此,在受到相同力的作用时,相对于其他的材料,镁合金可吸收更多的振动冲击,起到减振、降噪的作用。
由于镁合金比钢结构的质量轻,并且具有良好的力学性能,所以镁合金适合在车身上使用,从而达到轻量化的目的。从车身的整个结构来考虑,采用钢结构的前车身结构最为复杂,因为汽车的前车身是发动机的机仓,为了匹配发动机的相关性能要求,它必须有合理的空间布置。而且由于发动机的特殊工作环境,前车身的刚度、强度和疲劳性能等都要满足一定的要求。因此,使得采用钢结构的前车身结构更加复杂化,而这种复杂化必然会导致车身的工艺变得复杂,最终加重了前车身的质量。所以,本文采用镁合金替代前车身的钢结构,从而达到整个车身轻量化的目的,如图1所示。
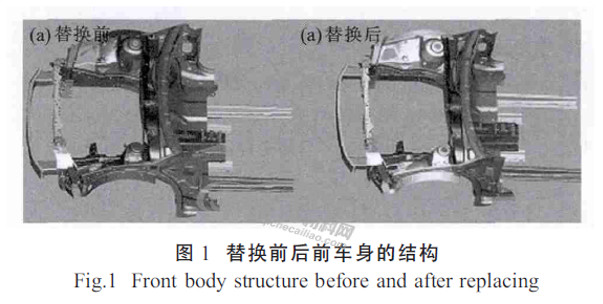
替代之后,所替代部分钢结构的原始质量为85.6kg,替代为镁合金结构后,其质量降为35.4kg,质量降低了50.2kg,因此其替代部分质量降低百分比为58.6%。
车身轻量化贡献率计算如式(1)。

式中:η为车身轻量化贡献率;m1为替代部分的原始质量;m2为替代后质量;m总为替代后白车身的总质量。
因此车身轻量化贡献率为14.7%,具体如表2所示。
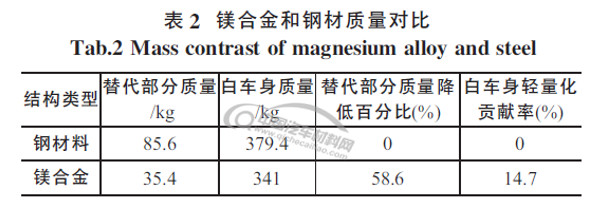
2镁合金制造技术与制造工艺优势
2.1镁合金的制造加工技术
目前,镁合金可采用压铸、挤压铸造、固态成型、半固态铸造、注射成型等多种铸造技术来生产镁合金制件,这些制造工艺给镁合金应用于车身提供了技术支持。
镁合金的压铸技术主要包括真空压铸和充氧压铸两种方式。真空压铸是指在压铸过程中,利用铸造金属消除型内空气,以消除或减少压铸件内的气孔或孔隙,来提高压铸件力学性能和表面质量。充氧压铸是指充型前将活性气体冲入型腔来交换型腔内的空气,充型时利用活性气体与金属液反应来消除铸件内气体和气孔。镁合金的挤压铸造是指采用较低的充型速度以及最小的扰动使金属液在高压下凝固,从而获得可进行热处理的高致密度铸件的铸造工艺。镁合金的半固态铸造,对冷却凝固过程中的金属熔体进行强烈搅动,待熔体达到一定固相分数时对其进行压铸或挤压成形,包括流变成型、触变成型和注射成型。
2.2镁合金材料在工艺上的优势
由于镁合金具有良好的压铸成型性能,铸件及加工尺寸精度高,可以压铸薄壁件以及比钢铁件更复杂的零件。因此,当使用镁合金材料代替钢结构前车身时,替代部分的零件数量就由原来的89个降为50个,因为多个零件可由一个压铸零件来替代,如图2所示,这样零件数量就会减少,从而优化了加工工艺,简化了车身加工的加工工序。
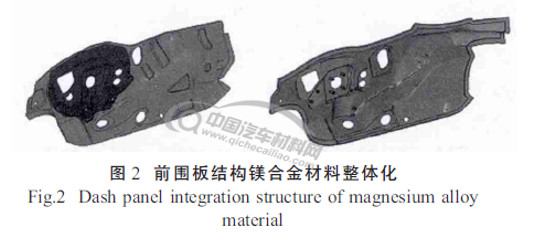
在镁合金的生产加工成本上,以前是处于较高的位置,因为镁合金在使用压铸技术进行生产时会产生大量废料,而废料中含有固液两种形态,所以必须使用熔剂才能清理干净,并且这个清理工艺也很复杂,这样就大大加重了生产成本。然而,现在,利用无熔剂物理精炼方法,就消除了异地生产的困扰,从而使得镁合金在性价比上也占有了较大的优势。
3镁合金车身在疲劳耐久性上的优势
3.1试验方法
对于车身的疲劳耐久性试验,采用影响最大的扭转工况,利用台架进行虚拟耐久性试验,然后进行扭转疲劳强度分析。基本试验方法是:在车身台架试验的试验台上设置4个附着点,共4个通道,然后通过MSC/NASTRAN软件在4个通道上施加扭转力,再在分析软件FEMFAT中进行虚拟车身扭转,循环次数为50000次,通过疲劳损伤累积法则计算车身疲劳损伤。
3.2分析结果对比
3.2.1镁合金替代区域以外疲劳损伤值对比
由于试验过程中,有些区域的疲劳损伤值较小,省略对比,只进行损伤值大于0.1区域的对比,其结果如表3所示。
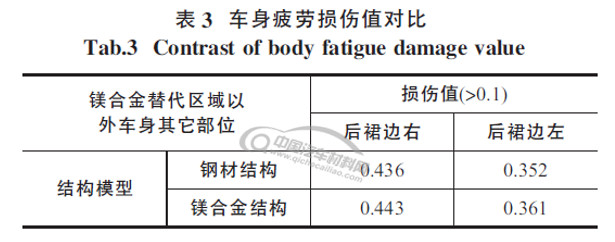
从以上结果可知,当使用了镁合金之后,疲劳损伤最严重的位置是一致的,并且损伤值比之前大了0.008左右。因此,使用镁合金并不会对汽车车身其他部位在疲劳耐久性上造成影响。
3.2.2镁合金替代区域的疲劳损伤值对比
同样选取损伤值大的区域进行对比,对比结果如表4所示。
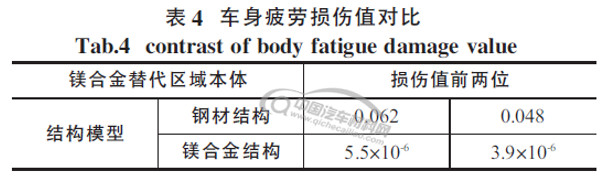
从以上结果可知,在使用了镁合金之后,替代之后的结构的疲劳损伤值小了很多,并且最大的损伤区域也是一致的。
因此,镁合金的使用不仅达到了轻量化目的,而且,在使用后的车身疲劳耐久性上具有很大的优势,这就给镁合金在汽车车身上应用提供了很大支持,使得镁合金在车身轻量化的道路上具有更好的发展前景。
结语
经过从材料、工艺方面的对比,可知,镁合金给汽车车身带来了轻量化,并且简化了车身制造工艺,减小了生产制造成本。在性能方面,镁合金的使用给车身的疲劳耐久性带来了很大优势。因此,经过本文的探索研究,从各个方面体现了镁合金材料的优势和前景,这是汽车车身轻量化发展的一个很好选择。
更多关于材料方面、材料腐蚀控制、材料科普等方面的国内外最新动态,我们网站会不断更新。希望大家一直关注中国腐蚀与防护网http://www.ecorr.org
责任编辑:韩鑫
《中国腐蚀与防护网电子期刊》征订启事
投稿联系:编辑部
电话:010-62313558-806
邮箱:fsfhzy666@163.com
中国腐蚀与防护网官方 QQ群:140808414
免责声明:本网站所转载的文字、图片与视频资料版权归原创作者所有,如果涉及侵权,请第一时间联系本网删除。
相关文章
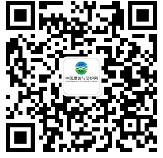
官方微信
《中国腐蚀与防护网电子期刊》征订启事
- 投稿联系:编辑部
- 电话:010-62313558-806
- 邮箱:fsfhzy666@163.com
- 中国腐蚀与防护网官方QQ群:140808414
点击排行
PPT新闻
“海洋金属”——钛合金在舰船的
点击数:5768
腐蚀与“海上丝绸之路”
点击数:4763