C/C 复合材料有着优异的耐热性和高温性能,可经受住2 000 ℃以上的高温,是目前在惰性气氛中高温力学性能最好的材料。此外,它具有良好的抗热冲击、抗烧蚀、耐含固态微粒燃气冲刷、热膨胀系数低及良好的热导性能等一系列的特性,能应用于高于3 000 ℃高温短时的烧蚀环境中,如航天飞机、洲际导弹的鼻锥帽、固体火箭发动机喷管与喉衬等。但是,高温易氧化问题导致C/C 复合材料优异的高温性能只有在无氧环境中才能得到充分发挥。然而,C/C 热结构部件的服役环境大多是极为恶劣的高温强氧化环境,如飞机发动机内的燃气环境、大气环境、高温腐蚀或烧蚀环境等,氧化对材料的力学性能的影响较大。同时,C/C 复合材料作为烧蚀材料主要应用于固体火箭喷管,火箭喷管内夹带固相或液相粒子的高速燃气流不断冲刷喉衬,使得喉衬不断氧化与烧蚀。
目前,国内外解决C/C 复合材料防氧化与抗烧蚀的办法综合起来主要有2 种:1)以材料本身对氧化反应进行催化为前提的内部改性技术,即在C/C 复合材料制备过程中就对碳纤维和碳基体进行改性处理,使C/C 复合材料基体本身具有较强的抗氧化与抗烧蚀能力。该技术主要应用于短时烧蚀环境下的C/C 复合材料氧化性能的提高,对于C/C 复合材料的长寿命抗氧化主要局限于1 000 ℃以下的环境。2)在防止含氧气体接触扩散为前提的材料外部表面涂层技术,即在C/C 复合材料表面涂覆耐氧化、抗烧蚀的高熔点化合物,如Ta、Hf、Zr、Nb、Si、Mo 等的碳化物、硼化物、硅化物涂层,以提高C/C 复合材料的抗氧化与抗烧蚀性能。
金属间化合物MoSi2 高温时其表面会形成一层致密的SiO2 保护膜,具有特别优异的高温抗氧化性能,常作为难熔金属、石墨和 C/C 复合材料的高温抗氧化涂层。目前主要的涂层方法包括包埋法、原位反应法、料浆-涂刷法、水热-电泳沉积法、化学气相沉积法等。然而,虽然相关报道较多,但也只停留在试验阶段,在实际工程应用过程中,涂层C/C 复合材料不仅要承受高温氧化,而且要克服高速粒子的冲刷。因此,对涂层结构致密度、厚度均匀性以及涂层的结合强度要求较高。
这除了由于MoSi2 本身的固有性质外,更大程度上是因为现有涂层方法MoSi2 涂层制备技术尚存在一定的缺陷,很难制备出满足上述要求的涂层。因此,开发新的涂层技术迫在眉睫,等离子喷涂制备的涂层结构致密度、厚度均匀性以及涂层的结合强度较高,且工艺稳定、可重复性好,是一种很有前途的MoSi2 涂层制备工艺。
本文将采用超音速等离子喷涂法在SiC 涂层C/C 表面制备MoSi2 涂层,研究喷涂功率、主气(Ar)流量对粉料表面温度、飞行速度、沉积率以及对涂层表面微观结构和结合强度的影响。
1 实 验
1.1 实验原料
具有SiC 涂层的C/C 复合材料,自制;聚乙烯醇(Polyvinyl alcohol(PVA)), 中聚合度,醇解度99.8%~100%,天津市科密欧化学试剂有限公司;二硅化钼粉(MoSi2),纯度≥99.5%,粒度300 目,郑州嵩山电热元件有限公司; 氩气(Ar),纯度≥99.99%,四川梅塞尔气体产品有限公司;氢气(H2),纯度≥99.99%,四川梅塞尔气体产品有限公司。
1.2 MoSi2 涂层的制备过程
利用超音速等离子喷涂系统,按设定的喷涂工艺喷涂MoSi2 涂层到带SiC 涂层的C/C 复合材料表面,主要研究了不同喷涂功率、主气(Ar)流量对涂层制备过程的影响,涂层制备工艺如下:
1)按比例称取聚乙烯醇与水,而后利用恒温磁力搅拌器加热至100 ℃,搅拌5 h 左右,静置12h,得到PVA 质量分数为7%的粘结剂;2)称取一定量的二硅化钼粉,加入质量分数10%的粘结剂,充分搅拌后置入干燥箱中,在100 ℃下干燥3 h,利用球磨机球磨5 h 后,分别过325 目与200 目分子筛,取200~325 目的粉料作为喷涂粉;3)利用超音速等离子喷涂系统按设定的喷涂工艺,将准备好的喷涂粉料喷涂到带SiC 涂层的C/C 复合材料表面,得到致密的MoSi2 外涂层。
喷涂工艺参数如表1 和2 所示。结合强度测试装置如图1 所示。
按照GB/T 8642-88《热喷涂结合强度的测定》要求,采用粘接拉伸法测试涂层与基体间界面结合力,测试原理如图1 所示,在2 个对偶件端面分别均匀地涂上改性丙烯酸脂粘结剂,而后将试样粘接在两端面间,室温下5~10 min 定位,固化24 h 后,待粘结好后,在电子万能试验机(CMT5304-30kN)上均匀的、连续加载,直到试样断开,记录最大断裂载荷,有效试样不少于5 个,取记录载荷的平均值,涂层与基体的结合强度(σ)计算公式如下:
式中:F 为涂层脱离时最大拉力,N;S 为涂层试样的粘结面积,m2;σ 为界面结合强度,MPa。
1.3 MoSi2 涂层的微观结构分析
超音速等离子喷涂系统:HEPJ 型高效能超音速等离子喷涂设备(功率≥80 kW);喷涂粉料的测温测速设备:SprayWatch 2i 热喷涂监测系统;ZGS-350 型真空高温烧结炉(最高使用温度:3000 ℃);M-4L 型行星式球磨机(转速≤600 r/min);JSM-6460 型和VEGA TS5136XM 型扫描电镜扫描电镜和SUPRA55 型场发射扫描电镜用于分析涂层的微观结构;X'Pert PRO 型X 射线衍射分析仪。
2 结果与分析
2.1 喷涂功率对MoSi2 涂层制备的影响
2.1.1 喷涂功率对粒子温度和飞行速度的影响
图2 为不同功率对MoSi2 粒子温度、速度的影响规律。由图2 可以看出:随着功率的增大,粒子温度在47.5 kW 之前快速上升,在47.5~55 kW 增速减缓,55 kW 之后其温度不再增加,基本保持不变;粒子飞行速度在47.5 kW 之前亦快速上升,在47.5~52.5 kW 增速较为缓慢,而52.5 kW 以后出现缓慢降低。
MoSi2 粒子温度与速度随功率增加主要是射流加热能量增加的缘故,而在47.5 kW 后粒子可能是因为物理变化或化学反应消耗一定的热量,使得粒子温度增加缓慢甚至不再增加;粒子的速度先增大后略微减小,主要是因为功率过大而导致少量粉末过熔甚至团聚,从而阻碍了粒子速度进一步提高。因此,功率选为47.5~55 kW,既能使粒子有较高的速度和温度,还能保证粉末不过熔。
从图3 可以看出,随着喷涂功率的增加,喷涂粉末的沉积率先增加后降低,在喷涂功率为50 kW时达到最高值38%。在较低功率下,喷涂粉末的热焓和熔化程度不高,粒子中将存在较多熔化不完全或者未熔化的喷涂粒子,这些粒子的存在将降低喷涂粉料整体塑性,变形不充分,在高速射流作用下撞击到基体表面,可能出现粒子破碎,产生大量的粉末飞溅;而随着功率的升高,喷涂粉末热焓和熔化程度提高,同时其飞行速度也有所提高,撞击到基体表面能够很好地附着与铺展,不会发生粉末的飞溅,沉积效率较高;而当喷涂功率达到一定程度时,喷涂粉末将会产生少量粉末过熔甚至团聚的现象,降低了粉末的飞行速度,增加粉末在飞行过程中的氧化消耗,从而导致粉末的沉积率降低。
2.1.2 喷涂功率对涂层微观结构的影响
图4 为不同喷涂功率条件下,制备的MoSi2 涂层表面X-射线衍射谱图,可以发现:4 种功率条件下制备出的涂层主要由MoSi2、Mo5Si3 两相组成;随着喷涂功率的增加,涂层中Mo5Si3 峰的相对强度逐渐减弱,特别是当功率达到55 kW 时,涂层中的Mo5Si3 峰的相对强度值几乎减半,同时涂层中出现了MoO3 峰。在超音速等离子喷涂过程中,熔融的MoSi2 粉料在飞行过程不可避免地与空气中的氧发生反应,可能的反应式为:
由以上反应可推测出涂层中Mo5Si3 来源于MoSi2 的氧化,涂层中可能存在非晶的SiO2。并且随着喷涂功率的增加,喷涂粉料的温度升高;MoSi2粉料氧化反应生成Mo5Si3 与SiO2 的速率加快,当功率升高到一定程度,MoSi2 将会同时发生式(1)和(2)的氧化反应。反应产物Mo5Si3 也会进一步氧化生成MoO3 和SiO2 如反应式(3),这就解释了随着喷涂功率升高涂层Mo5Si3 峰相对强度值降低。
另外,因为温度的升高,反应(2)与(3)同时进行生成的MoO3 量增多,使得少量MoO3 不能及时挥发,被熔融的喷涂粉料粘附带入涂层内,当温度喷涂功率达到55 kW 时,涂层XRD 谱图中出现MoO3相的峰。涂层中Mo5Si3 相以及可能存在的非晶SiO2都是有利于提高涂层的抗氧化性能;然而,MoO3相高温下容易挥发,在涂层中留下孔洞,破坏涂层的致密性与完整性,不利于涂层的高温防氧化。
图5 为不同喷涂功率下制备的MoSi2 涂层的表面形貌照片,可以看出:随着喷涂功率的增加,涂层中的孔隙缺陷先减少后增加;在喷涂功率为45kW 时,涂层表面气孔含量较多;在功率为50 kW时,获得的涂层表面致密,几乎没有气孔和裂纹的存在;而当喷涂功率达到55 kW 时,涂层致密度降低,开始出现裂纹。
在较低功率下,等离子射流温度过低,未熔融的MoSi2 粉末较多,到达基体表面铺展程度较低,未熔融的粉料颗粒保持原始颗粒特征,半熔融的和熔融的粉料凝聚堆积,颗粒间有明显的界面,因此涂层表面的气孔含量较高;随着功率的增加,MoSi2粉的温度和飞行速度逐渐增加,尤其是喷涂功率50kW 时,粉料能充分熔融,且有较大的冲量撞击基体表面而变形、润湿、铺展,最后凝固冷却形成涂层,使得涂层表面光滑且致密性较好;而当喷涂功率过高时,MoSi2 喷涂粉料温度较高,容易出现过熔和团聚,使得粉料氧化严重,可能携带大量的氧化副产物进到达基体表面铺展、凝固,这些副产物在MoSi2 粉料的凝固过程中,一部分以气体的形式排出在涂层中留下小孔隙,另一部分来不及排出的气体随涂层一起冷却凝固留在涂层内部,从而影响涂层的致密度。另外,粉料温度过高,形成的涂层热应力较大,容易在涂层中产生裂纹,破坏涂层的完整性。
图6 为不同喷涂功率下制备MoSi2 涂层的截面形貌照片,可以看出,在较低功率下,涂层局部出现大量的孔隙,涂层与基体之间存在裂纹。因为低功率下MoSi2 熔融不充分,可能有部分的生粉被带入涂层,生粉颗粒碰撞到基体表面不会发生塑性变形,直接镶嵌在涂层中,在其周围产生很多较大的间隙,从而在涂层中留下许多孔隙,当生粉出现在涂层与基体界面处时,将会在涂层与基体之间产生缺陷,大大地弱化涂层与基体间的界面结合强度。
由图6 还可以看出:随着功率的增加,MoSi2的熔化程度与飞行速度都有所提高,涂层中的生粉减少,涂层中的气孔缺陷降低,界面结合状态较好,特别是当喷涂功率达到50 kW 时,获得的涂层致密,无孔隙和裂纹存在,与基体结合紧密;而随着喷涂功率的继续增加,涂层致密性变差,开始出现少量的气孔,当喷涂功率过大,喷涂粉料容易产生过烧,氧化严重,产生较多的气态的MoO3,可能有少量的MoO3 被带入涂层,在熔融凝固过程中,部分的MoO3 及时排出将在涂层中留下气孔,而部分的MoO3 液化凝固残留在涂层内部,弱化涂层自身的强度,当这些MoO3 存在于涂层与基体间的界面时,将弱化界面结合强度。另外,因为粉料过熔,使得粉料的飞行速度降低,碰撞到基体表面的冲量变小,可能导致涂层与基体间的界面结合强度变差。
2.1.3 喷涂功率对涂层结合强度的影响
喷涂功率对涂层与基体的结合强度有很大的影响。在涂层C/C 复合材料的在实际应用过程中,若涂层结合强度太低,涂层试样在热震过程中产生的涂层应力将使得涂层脱落而失效。因此,研究喷涂功率对涂层的结合强度的影响有着非常重要的意义。由图7 可以发现:随着喷涂功率的提高,外涂层与SiC 涂层C/C 复合材料之间的结合强度先增加后降低;在喷涂功率达到50 kW 时,涂层结合强度达到最大值15.6 MPa;功率继续增加,涂层结合强度有所下降。喷涂法制备的涂层与基体的结合主要是以机械结合为主。熔化的粒子在凝固时与基体上的凹凸点勾结形成结合点,如果涂层缺陷增多,接触点会减少,结合强度就会降低。
在较低的喷涂功率下,一方面喷涂粉料温度较低,不能充分熔化,可能出现“生粉”现象,到达基体表面不能充分铺展填充基体表面的裂纹或孔洞,使得涂层与基体界面处存在缺陷,减少了内外层间的接触点,降低了涂层的结合强度;另一方面,由于喷涂功率较低,工作气体受到等离子射流加热膨胀的能力小,喷涂粉料的速度会降低,使得粉料到达基体表面与基体撞击力减小,从而降低涂层的结合强度。而当喷涂功率增加到55 kW 时,由于喷涂功率过高导致喷涂粉料过熔,涂层中可能出现MoO3 弱化了涂层与基体间的结合力。
2.2 主气(Ar)流量对MoSi2 涂层制备的影响
2.2.1 主气(Ar)流量对粒子温度和飞行速度的影响
图8 是MoSi2 粉料温度和飞行速度随Ar 流量的变化曲线,可以看出,随着Ar 流量的增加,粒子温度先缓慢减小而后快速下降,速度先快速增加而后趋于平缓。当Ar 流量较低时,等离子弧射流太小,射流的携带能力降低,喷涂粉末速度较低,增加了粉末在火焰中的滞留时间,可能导致少量粉末过熔甚至团聚,反而进一步降低了粒子速度;而当Ar 流量进一步增大时,等离子弧射流增强,射流的携带能力提高,粒子飞行速度增加,减小了粉末在火焰中的滞留时间,从而避免了粉末的过熔和团聚;当Ar 流量过大时,过量的气体会冷却等离子的射流,使其热焓和温度下降,不利于粉末的加热,同时粒子的射流速度过高,也降低了粒子在射流中的滞留时间,导致粒子温度进一步降低。因此,为获得合适的粒子温度和粒子飞行速度,需要均衡考虑粒子的温度与速度,本文将Ar 流量选择为65L/min。
2.2.2 主气(Ar)流量对粉料沉积率的影响
图9 为MoSi2 涂层的沉积率随Ar 流量的变化曲线,可以看出,随着Ar 流量的增加,涂层的沉积率快速增加,在Ar 流量为65 L/min 时达到最大沉积率38%,而后沉积率开始随Ar 流量的增加而降低。在Ar 较低时,MoSi2 粉料表面温度高,飞行速度低,使得其在等离子射流中滞留时间长,粉料出现过熔或团聚,加剧MoSi2 氧化损失。同时,过熔的粒子可能包裹少量生粉形成球状体,撞击到基体表面圆球破裂生粉飞溅出去,不能形成涂层,导致沉积率降低。而当Ar 较高时,过量的Ar 冷却了等离子射流,使得射流的热焓和温度降低,粉料不能很好地被熔化加速,撞击到基体表面不能很好铺展和镶嵌到基体的裂纹与孔隙之中,而出现大量粒子被反弹或飞溅出去,无法形成涂层,降低沉积率。因此,为提高MoSi2 涂层的沉积率,获得质量较高的涂层,本文选择主气流量为65 L/min。
2.2.3 主气(Ar)流量对涂层微观结构的影响
图10 为不同Ar 流量下MoSi2涂层的表面形貌,可以发现:Ar 流量不同时,涂层的形貌有很大的差别;Ar 流量为60 L/min 时,涂层表面疏松,孔隙率较高,有大量微裂纹存在,这主要是因为MoSi2粉料的表面温度高且飞行速度低,容易出现过熔与团聚,氧化较为严重,撞击到基体表面只有少量熔融粒子能够铺展。同时,因为粒子的温度过高,在凝固过程,体积收缩较大,在涂层中留下许多微裂纹;当Ar 流量达到65 L/min 时,MoSi2 粉料表面温度与飞行速度都保持在较高数值,粉料熔融充分且获得的动能较大,撞击到基体表面很好的铺展、凝固形成结构致密的涂层;随着Ar 流量继续增加到70 L/min 时,Ar 涂层中气孔明显增加,并伴随着大的气孔缺陷产生,由于过量的气体冷却了等离子射流,MoSi2 粉末熔融不充分,整体刚性加大,粒子撞击大基体表面,粒子与粒子之间不能很好地堆叠,从而在涂层中形成大量的孔隙;进一步增加Ar 流量,等离子射流温度降低而飞行速度加快,无法将MoSi2 喷涂粉末熔化,携带着大量的生粉颗粒,这些粉料撞击到基体表面,一部分直接反弹飞溅,另一部分以机械铆合的形式与基体结合形成涂层,因此,Ar 流量为75 L/min 时,涂层表面疏松,存在大量的空隙与裂纹。
图11 为不同主气(Ar)流量下制备MoSi2 涂层的截面形貌照片,可以看出:Ar 流量为60 L/min时,涂层表面疏松,有较多微裂纹存在;当Ar 流量达到65 L/min 时,MoSi2 粉料表面温度与飞行速度都保持在较高数值,粉料熔融充分且获得的动能较大,撞击到基体表面很好地铺展、凝固,形成结构致密的涂层;随着Ar 流量继续增加到70 L/min时,涂层中气孔明显增加;Ar 流量为75 L/min 时,涂层表面疏松,存在大量的空隙与裂纹。
随着Ar 气流量的增加,等离子射流温度降低,造成MoSi2 粉末熔融不充分,同时由于粒子飞行速度快,在撞击到基体表面时,粒子与粒子之间不能很好地堆叠,从而在涂层中形成大量的孔隙与裂纹。
3 结 论
1)喷涂功率在47.5~52.5 kW 时,既能使粒子有较高的速度和温度,还能保证粉末不过熔。喷涂功率为50 kW 时,粉料的沉积率最高,涂层氧化程度不高,微观结构分析显示涂层表面致密性好,截面结合紧密,涂层结合强度达到最大值15.6 MPa。
2)在不同喷涂功率下涂层主要由MoSi2、Mo5Si3 两相组成。涂层中Mo5Si3 相以及可能存在的非晶SiO2 都是有利于提高涂层的抗氧化性能。
3)在Ar 流量为65 L/min 时,能够保证MoSi2粉末有较高的表面温度与较快飞行速度,沉积率最高,氧化不高,涂层表面致密,几乎没有孔隙与裂纹。
更多关于材料方面、材料腐蚀控制、材料科普等方面的国内外最新动态,我们网站会不断更新。希望大家一直关注中国腐蚀与防护网http://www.ecorr.org
责任编辑:王元
《中国腐蚀与防护网电子期刊》征订启事
投稿联系:编辑部
电话:010-62313558-806
邮箱:fsfhzy666@163.com
中国腐蚀与防护网官方 QQ群:140808414
免责声明:本网站所转载的文字、图片与视频资料版权归原创作者所有,如果涉及侵权,请第一时间联系本网删除。
-
标签: 碳/碳复合材料;超音速等离子喷涂, 二硅化钼涂层, 喷涂功率, 主气(Ar)流量
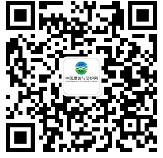
官方微信
《中国腐蚀与防护网电子期刊》征订启事
- 投稿联系:编辑部
- 电话:010-62313558-806
- 邮箱:fsfhzy666@163.com
- 中国腐蚀与防护网官方QQ群:140808414