C919成功首飞说明大飞机国产化不是梦,飞机复合材料和关键零部件100%国产化也是迟早的事情,但是目前仍然存在一些技术难题,今天让我们一起来探讨一下飞机结构件的工艺特点与加工难点,以及实际加工中遇到的问题与解决办法。
飞机整体结构件
飞机整体结构件是构成飞机机体骨架和气动外形的重要组成部分,它们品种繁多、形状复杂、材料各异。为了减轻重量,进行的强度设计,往往在结构件上形成各种复杂型腔。
与一般机械零件相比具有的特点:加工难度大,制造水平高,行位精度要求高,严格的重量控制、严格的寿命使用要求。
飞机整体结构件的主要类型:
(1)整体壁板。
(2)整体梁类零件。
(3)整体框、肋类零件。
(4)整体骨架类、接头类零件。
(5)挤压型材和变截面桁条类零件。
过去飞机机体主要部分都由钣金零件装配而成,而后来随着飞机性能的不断提高,整体结构日益增多。由于整体框、梁、肋的出现及整体壁板结构的广泛应用,机械加工零件的类型和品种日益增加,在某些类型飞机的生产中,机械加工零件所占劳动量比重已超过钣金成形零件件,而且飞机工厂设备和厂房布局也由此相应有所改变。例如如有些客机的整体结构件占机身重量的65%,因此整体结构件在航空航天领域发挥越来越重要的作用。
整体结构件与旧式铆接结构相比有如下优点:
(1)气动性能方面:外形准确,对称性好;
(2)强度方面:刚性好,比强度高,可减轻重量(约15%~20%),气密性好;
(3)工艺和经济效益方面:大大减少零件和连接件数量,装配后变形小,可使部件成本降低50%左右。
飞机整体结构件主要工艺
Harvi Ultra 8X 铣刀的金属移除率达
1003 cm3/min
创下
钛合金金属移除率的世界纪录
1.飞机整体结构件的外形多数与飞机外形有关,有复杂的装配协调关系,精度要求较高。
当骨架和蒙皮均为大厚度的整体结构时:若蒙皮和贴合的骨架有较大的装配间隙,就会发生很大的装配应力,会导致飞机强度和寿命的降低。如在组装时加相应尺寸的调整垫片作为补偿,装配工时增多,周期延长,加垫过多也会影响结构强度和飞机寿命。
2.多数整体结构件尺寸大,形状复杂,加工技术难度大。
尺寸大:大型的整体壁板有的长达30m左右,毛坯重3~4t,大型机身整体框约6×3m,毛坯重约2t,小型机身框约2×2m,毛坯重1t,必须配置大型机加机床和相应的装卸、搬运等设备。
形状复杂:整体结构件多数为板块状,其轮廊外形部位一般均与飞机机体复杂的外形有关,如梁、框、肋等平面零件周边外形角度变化较大,因此,加工的开敞性差,工作量大,加工技术难度大。
一个中等复杂的整体结构件的加工工序约需要100道以上按40架一批,每批的制造工时达10万小时,制造周期需10~12个月。
3.整体结构件的材料大部分采用航空用的铝合金,高强度合金钢、钛合金和复合材料。
铝合金整体结构件的毛坯有模锻和预拉伸厚板材两种。平面类整体壁板、框、肋、梁的铝合金零件大部分采用拉伸的厚板材,在板材厚度允许的情况下,尽量不采用模锻毛坯。
其主要原因是:
(1)模锻毛坯需要较高的模具费用。
(2)模锻毛坯成形过程中残留的内应力大,工序和工时都增多,周期也延长。
(3)模锻毛坯,经切削加工后与预拉伸板材切削加工后的强度性能相比提高并不显著。
实际加工中遇到的问题与解答
问: 我们在加工航空铝板,大约400*1500*8mm,平面0.05很难达到,有什么好的刀具或解决方案?
答:这种零件保证平面度的关键在于夹紧方式,不能用钳口夹紧方式,在外力去除后,零件在内应力作用下肯定会发生变形。国外流行一种真空吸附的夹 具进行夹持,留0.2-0.3mm余量精加工,可控制变形,面铣刀进给放慢,减小切削力。
问:加工槽型件,车1.29的R,厚度最小值为0.8。如何能保证4.4加减0.02的槽宽,在切断后槽宽不变 ?
答:厚度R0.8的属于超薄的壁厚,正常切削产生变形的风险很高,在航空发动机零件加工当中,需要采取一些辅助手段提高刚性,例如人工加厚,加垫板,或者灌低温合金。
问:在加工高温合金方面有没有独特的设计?还是断续加工,AP1.5,车削加工,现在给客户用的是加工不锈钢的材质与槽型有解决方案么?
答:高温合金断续切削关键在于刀片的槽型,Ap1.5的话可以选用负角刀片,使用肯纳的MS槽型或者UP槽型(详见肯纳刀具样本)。
问:老师什么方法可以更好的解决切削热,降低刀具负荷,获得更好的表面质量?
答:如果你说的解决钛合金的加工的切削热的话,首先冷却是必不可少的,冷却压力尽量高于 30bar,另外刀片的材质选用抗热冲击性能好的材质,如果表面质量要求比较高的话,可以采用肯纳的KCSM40材质,PVD涂层TiALN/TIN。
问:薄壁加工怎样更好的保证尺寸的精确性?
答:薄壁件加工主要注意的因素很多,对于铣削来说,刀具选择,夹持方式,走刀路径都需要注意。
问:老师讲的这种刀柄刚性很好!不过适合什么类型的机床主轴?
答:KM4X的原理与HSK主轴类似,都是通过过盈量和端面接触提高主轴连接刚性,而KM4x的过盈量更大,抗弯性能更好替换HSK主轴的设备的情况比较多。
问:老设备能用吗?
答:老设备指的是怎样的设备,需要数据与信息定义。
问:在加工的过程中采用哪种夹具更有优势?
答:不同的夹具有不同的适用场合,不能一概而论。
问:最大转速能达到多少?
答:最大转速取决于机床,而不是刀具,KM4x动平衡等级是G2.5/15000RPM。
问:这种柄的动态刚性怎样?
答:KM4X柄的动平衡等级是G2.5/15000rpm,本身抗弯能力很强,强于HSK刀柄,所谓动态刚性指的是切削时机床抵抗振动的能力,除了与刀具相关外还与机床各部件的机械性能有关。
问:有碳纤维加工刀具介绍吗?
答:肯纳拥有加工碳纤维材料的刀具产品,请联系肯纳当地工程师或授权经销商。根据您的具体需求介绍相应的刀具。
问:刀片的实际工作前角是多大?
答:不同种刀片的工作前角不同,取决于选择何种刀片。
问:铣钛合金的寿命怎样?
答:铣削钛合金的具体寿命在视频当中有,切宽切深不同,寿命也不同。
问:冷却压力及流量多少?
答:冷却压力至少30bar以上,越大越好。
问:如果玉米铣有一片破损是不是要全部更换刀片?
答:刀片磨损有先后是正常的,因为公差的原因,径向直径会有高有低,不会影响正常切削,但是磨损与崩裂是不一样的。
问:怎么没有中喷呢?
答:玉米铣刀主要用于铣槽或者侧铣,冷却液都针对每个刀片的刃口,中心不需要喷。
问:刀片什么材质呢?
答:刀片材质是肯纳的KCSM40,PVD TiALN/TiN 涂层,具有良好的抗热冲击性。
问:Harvi Ultra 8X这刀有几个刃?
答:刀片有8个刃,刀体的刃数由直径决定。
问:加工钛合金材料是涂层需要有什么注意吗?
答:加工钛合金的涂层需要有良好的抗热冲击性。
问:锯片铣刀的锁紧螺母,在换掉的情况下,怎么取下?
答:无法确定你说的是哪种锯片铣刀,肯纳的锯片铣刀是通过刀体的弹性变形装卸刀片,不需要锁紧螺母,只需要一个扳手。
问:这种刀具精加工时用cam软件分析受力与变形情况怎样?
答:精加工的效果可以通过检验工件来印证,HavillII 5倍径刃长的铣刀精铣钛合金侧面的直线度是0.03mm。
问:壁面加工精度度怎样? 粗糙度怎样?Harvi Ultra 8X玉米铣刀?
答:玉米铣刀加工粗糙度Ra6.3,玉米铣刀加工后的表面粗糙度往往不是最关键的。
问:铝合金材料加工完后零件表面的平面度及壁厚尺寸一致性怎样?
答:精加工铝合金的平面度一般在0.05mm,平面度是形状公差,面积越大越难保证刀片式的铣刀一般用来挖铝合金型腔,属于粗加工与半精加工。
问:转速这么高,对铝合金来说不会糊刀么?
答:刀片与刃口都经过抛光处理过,加上高压冷却,高速加工铝合金排屑效果很好。
问:加工中的不确定性问题通过什么控制技术与算法来解决呢?
答:加工中出现的问题有些体现在刀具上,有些体现在工件上,都会有相对应的方式解决所有问题都会有一个体现方式,需要具体分析。
更多关于材料方面、材料腐蚀控制、材料科普等方面的国内外最新动态,我们网站会不断更新。希望大家一直关注中国腐蚀与防护网http://www.ecorr.org
责任编辑:殷鹏飞
《中国腐蚀与防护网电子期刊》征订启事
投稿联系:编辑部
电话:010-62313558-806
邮箱:fsfhzy666@163.com
中国腐蚀与防护网官方 QQ群:140808414
免责声明:本网站所转载的文字、图片与视频资料版权归原创作者所有,如果涉及侵权,请第一时间联系本网删除。
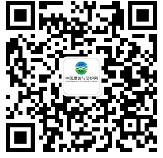
官方微信
《中国腐蚀与防护网电子期刊》征订启事
- 投稿联系:编辑部
- 电话:010-62313558-806
- 邮箱:fsfhzy666@163.com
- 中国腐蚀与防护网官方QQ群:140808414