在这个技术革新飞速的时代,构想的发生很少不可能,汽车的更新换代与我们的生活息息相关,汽车轻量化也在逐步实现。汽车轻量化是指保证汽车强度和安全性能不受影响的情况下,通过先进的设计方法、外观和结构改进、零部件替换或使用新材料最大限度的减轻整车重量,从而尽可能的提高汽车的动力性能,减少燃料消耗,降低排放污染。
何以轻
节能减排政策推动汽车轻量化
根据世界气象组织(WMO)发布公报,2015年全球二氧化碳平均浓度首次达400ppm,而工业革命前该数值仅为280ppm。二氧化碳作为主要的温室效应气体,其主要来源是人类活动,而在各项人类活动中,交通工具二氧化碳排放量占据了五分之一。
图1 各项人类活动二氧化碳排放量占比
另外从重要的大气污染物PM2.5来源来看,上海市PM2.5来源中本地污染排放贡献占64%-84%,平均约为74%左右;本地排放源中,流动源占29.2%,工业生产占28.9%,燃煤占13.5%,扬尘占13.4%,另有农业生产、生物质燃烧、民用生活面源及自然源等其他源类占15.0%。流动源指的是车辆排放,扬尘的来源之一则是汽车路面行驶。
从1992年制定的欧一,到2014年颁布的欧六,排放标准愈加严厉。中国排放标准是基于欧洲标准制定的,由于国内汽车工业起步较晚,开始阶段较为宽松,近几年开始逐步向欧洲标准跟进。达不到排放标准的产品将不得出售。
图2 各国历年排放标准
再来看各国的油耗计划,这张图是每公里二氧化碳排放量,以汽车内燃机平均燃烧效率计算,和百公里油耗换算比为22.5:1,即到2020年我国汽车百公里平均油耗将降至5.3L以下。
图3 各国历年油耗计划
在不影响汽车性能的情况下降低油耗的方法主要有以下三种:(1)提升内燃机热效率;(2)降低汽车行驶过程中的风阻;(3)车身轻量化。
涡轮增压技术大幅提高了内燃机效率,但越接近卡诺定律所规定热效率极限,寻求技术上的突破也就越困难,短期难有能够大幅提升内燃机燃烧效率的技术革新。一辆汽车以80km/h的速度行驶时,约有60%的阻力源于风阻,所以每个车型面世前都要经过工程师数百次修改设计和上千小时的风洞试验,空气动力学性能几乎被压榨到了极限。而进入到21世纪以来,新材料不断面世和材料加工成型工艺的发展使得汽车轻量化成为了可能。
据有关研究,一般情况下车重每减轻1kg,则1L的汽油可以使汽车多行驶0.011km。于此同时,汽车减重不仅减少了油耗,也减少了二氧化碳排放量,车重如能减少一半,二氧化碳排放量就能减少13%。同时也减少了如氮化物、硫化物等其他有害物质的排放量。
图4 油耗与汽车质量 图5 排放量与汽车质量
以何轻
量产车轻量化的前提是建立在汽车的整体品质、性能和造价不变甚至优化的基础之上的,所以即使减配可以有效减轻车重并提高车辆性能,也不能作为汽车轻量化的有效手段,而是要通过材料、工艺和结构的重新设计,来实现整车减重的目标。
设计能力提升和制造工艺进步
汽车不同部位在行驶过程中的受力和安全要求不同,工程师针对不同部位进行钢材差异化的选择,在力学性能要求高的部位选用高强度钢,而非加厚板材,在其他部位选用成本较低的钢材起到基本的结构和覆盖功能。这样即有效控制了成本,又减轻了车重。现在汽车生产用钢通常被分为5-6个等级,不同等级的搭配使用能使白车身减重25%,而白车身又占据了整车质量的1/4,仅仅该部分的优化潜力就可达上百公斤。
金属成型方式主要分为锻造和铸造两种,铸造件容易产生沙眼、气孔等缺陷,而锻造件可使材料晶格排列整齐,晶粒细化,组织更致密,所以一般情况下锻造件力学性能要优于铸造件。但汽车零部件种类繁多,有些零部件形状复杂,受限于当时的技术水平,难以采用锻造工艺。随着金属加工成型工艺水平提高,复杂形状零部件也开始应用锻造工艺。更好地力学性能也就意味着更薄的结构和更轻的重量。以铝合金轮毂为例,要达到相同的力学性能,一组铸造轮毂要比锻造轮毂多出20%的重量。
图6 锻造件与铸造件对比图
焊接是车身装配过程中的一道主要工序,车身底板、车架、车顶、车门等部分都会采用焊接工艺。传统电阻焊是通过电流形成的电阻热融化焊件接触面,通过压力使焊件连接的方法,其技术特点决定了电阻焊在用于板材连接时需留有翻边。而新的激光焊工艺可以通过激光束直接融化需焊接部位,省去了翻边,减轻了重量的同时也使外形更美观,使车体密封性更好。
图7 激光焊与电阻焊对比图
另外借助CAD、CAE等软件和有限元模拟,汽车工程师可以方便的在计算机中对汽车进行设计和模拟,不必反复造样车拿去撞,然后回炉重新设计,大幅提高了设计效率,也便于设计师发现更多可以采取蜂窝、镂空等轻量化设计的部位。
新材料的渗透
汽车轻量化的升级过程中,车体材料经历了钢材到镁、铝合金再到碳纤维的演变过程,越好的材料越轻质高强。但车身轻量化并不是新材料对原有材料的简单替代过程,简而言之,汽车生产厂商是要盈利的,成本和性能的权衡也就成了量产车设计的主旋律。
一种材料如果能大规模的应用在量产车上,必然有生产规模化、品质稳定、成本可控,加工性能优越的特点。铝合金和镁合金具有密度低、抗冲击性能好、加工性能优良等特点,开始逐步替代汽车用钢材。以车身底盘零部件为例,铝合金应用在前后转向节中可使重量减轻40%,而镁合金用于车轮毂则可减重30%。
图8 单车用铝量图9单车用镁量
当前汽车用材中钢铁比重较大,其中绝大多数钢制零部件都可用铝、镁合金代替,包括发动机、轮毂、热交换器、车身、转向轴、变速器支架、悬架等。目前铝合金在变速箱、轮毂、热交换器领域渗透率较高,部分整车厂如捷豹等已经开始尝试大批量生产全铝车身,减重效果明显。而镁合金性能上虽然更优于铝合金,但由于其成本和表面处理工艺的复杂性,在汽车中应用仍受到极大限制。但随着各界在镁合金应用推广上不断的努力,未来汽车用镁量年均增长率将超过20%。
以碳纤维和玻璃纤维作为增强体的复合材料凭借其高强度、高弹性模量和远低于钢材和铝材的重量成为未来最理想的汽车轻量化材料。其比重不足钢材的1/4,仅有铝合金的1/2,而抗拉强度却能达到钢材的7-9倍。目前推广车用碳纤维最积极的厂商莫过于宝马,保守估计它的车用碳纤维产能占全球总产能50%以上,在宝马7系、i3等车型上均能看到其身影。但由于其生产工艺尚不成熟,成本过高,目前在量产车中的应用还处于初步阶段,但相信不久后,这项应用一定会迈向成熟,普及推广。
— END —
更多关于材料方面、材料腐蚀控制、材料科普等方面的国内外最新动态,我们网站会不断更新。希望大家一直关注中国腐蚀与防护网http://www.ecorr.org
责任编辑:殷鹏飞
《中国腐蚀与防护网电子期刊》征订启事
投稿联系:编辑部
电话:010-62313558-806
邮箱:fsfhzy666@163.com
中国腐蚀与防护网官方 QQ群:140808414
免责声明:本网站所转载的文字、图片与视频资料版权归原创作者所有,如果涉及侵权,请第一时间联系本网删除。
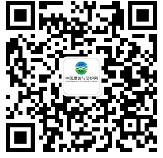
官方微信
《中国腐蚀与防护网电子期刊》征订启事
- 投稿联系:编辑部
- 电话:010-62313558-806
- 邮箱:fsfhzy666@163.com
- 中国腐蚀与防护网官方QQ群:140808414