应力腐蚀开裂(SCC)是轻水堆核电站结构材料常见的环境损伤模式之一。研究发现[1,2,3],SCC是由敏感的材料结构、腐蚀性介质和应力共同加速作用下造成的一个裂纹由局部缺陷萌生到缓慢稳态扩展的过程,材料、水化学和应力是影响高温高压水环境中材料SCC的三个主要因素,而腐蚀是SCC发生的基本过程[4]。腐蚀产物膜(氧化膜)的结构和成分与SCC的萌生和扩展过程密切相关,研究氧化膜的结构与成分能够揭示腐蚀的动力学过程和机制,从而为阐明SCC的机理提供基础。在所有影响材料腐蚀行为的因素中,材料表面状态是一个重要因素。目前关于表面状态对奥氏体不锈钢和镍基合金在高温高压水环境中腐蚀行为的影响已进行了大量研究[5,6,7,8],发现了材料的机加工表面、打磨表面、机械抛光表面和电解抛光表面等具有不同的腐蚀行为。S.Cissé等报道了模拟压水堆(PWR)一回路水环境(340℃,500h)和蒸汽环境(400℃,500h)中,打磨态304L不锈钢表面形成的氧化膜比机械抛光态的薄[9]。关于电解抛光的研究,学者[6,7]主要从去除表面残余应变层的角度解释了电解抛光对不锈钢和镍基合金在高温高压水中腐蚀行为的影响。Ziemniak[6]认为高温高压水的温度小于临界温度(374.15℃,22.1MPa)时,304不锈钢电解抛光表面的腐蚀速率比机械抛光表面的低。尽管很多学者已经对电解抛光态镍基合金在高温高压水中的氧化行为进行了研究,但是关于电解抛光工艺引起的表面成分改变对高温高压水环境中材料腐蚀行为的影响还鲜见报道。近期研究发现,电解抛光会提高600合金表面的铬含量[8],在高温高压水中形成保护性较好的氧化膜,从而抑制腐蚀。由于电解抛光工艺可能造成材料表面的成分改变,进而影响材料的腐蚀行为,因而抛光工艺可能是影响材料腐蚀行为的重要因素。本工作在前期工作基础上[8],针对不同电解抛光态600合金在压水堆一回路水中的腐蚀行为进行研究,探讨不同电解抛光工艺对材料腐蚀行为的影响及其机理。
1 试验
1.1 试样
试验用材料为轧制退火态600合金。其化学成分(质量分数)为:wCr15.57%, wFe9.50%, wTi0.28%, wMn0.22%,wSi0.12%, wNb<0.05%,wC0.065%, wP0.007%, wS0.002 1%,余量为镍。试样尺寸为10mm×10mm×1mm,用SiC水砂纸将试样表面逐级打磨至2000号,再用金刚石研磨膏抛光到0.5μm,最后采用两种工艺对试样进行电解抛光:(1)电解液成分(体积分数,下同)为15%硫酸+64%磷酸+21%水,电解温度为70℃,电流密度为0.2A/cm2,抛光时间为30s(经此种工艺抛光的表面以下简称EPS-1);(2)电解液成分为30%硝酸+70%甲醇,电解温度为0℃,电压为3V,抛光时间为10s(经此工艺抛光的表面以下简称EPS-2)。电解抛光后,试样依次在酒精-丙酮混合液和纯水中超声清洗,吹干后放入干燥皿中保存。
1.2 高温高压水腐蚀试验
高温高压水腐蚀试验在配有动态循环水回路、容积3L的316不锈钢高压釜中进行,试验温度为320℃,压力为13MPa。试验溶液模拟PWR一回路水溶液,含1000 mg/L B(以H3BO3加入)和2mg/L Li(以LiOH加入),室温下溶液pH为6.398,325℃高温下溶液pH约为7.25[10]。试验前,向回路水罐中通高纯氮气去除水中的溶解氧,使水中溶解氧质量浓度<5mg/L。将试片置于高压釜中,进行浸泡试验,试验时间分别为1,5,25,120,500h。
1.3 样品分析
腐蚀试验前,采用配有2keV氩离子溅射功能的ESCALAB 250型X射线光电子能谱(XPS)分析两种电解抛光初始表面产物膜的成分和结构。腐蚀试验后,采用XPS分析试样表面腐蚀产物膜厚度方向的成分和结构,采用配有能谱分析系统(EDS)的FEI XL30型环境扫描电子显微镜(ESEM)观察样品表面的腐蚀产物形貌。XPS分析过程中采用Ar+对氧化膜进行溅射,据文献[11]介绍,不同氧化物之间,比如尖晶石结构的Fe3O4和FeCr2O4溅射速率差异很小,参考标准Ta2O5样品,溅射速率约为0.1nm/s。为保证XPS分析准确性,Ar+溅射区域直径约2mm,而XPS分析区域直径约0.5mm。铬、镍、铁等元素的含量由元素峰面积乘以各元素的敏感性因子得出。采用XPSpeak4.1软件进行分峰处理,以得到各元素价态及其所占百分比。采用C1s峰值285eV作为标准校正峰偏移。
2 结果与讨论
2.1 产物膜的XPS
经不同电解工艺抛光后获得的600合金初始表面元素随溅射深度变化的XPS分析结果见图1。由图1可见,两种电解抛光工艺都促使表层富铬,EPS-1的Cr/(Ni+Fe)原子比大于EPS-2的,说明EPS-1富铬程度高。从图1(b)和图1(c)可知,两种工艺抛光后表面都形成了双层结构的超薄产物膜,表层主要为氢氧化物,次表层主要为氧化物,这与文献[12,13]一致。但两种表面的产物膜成分与厚度存在差异。其中两种产物膜表层的Cr(OH)3含量相近,EPS-1为32.1%(原子分数,下同),EPS-2为33.2%,但EPS-1中Ni(OH)2的含量大于EPS-2中的,分别为51.7%和36.5%。次表层氧化物的组成和成分也不同,其中EPS-1中的氧化物含量略高于EPS-2中的,由32.6%Cr2O3、7.5%NiO、3.8%Fe3O4或Fe2O3等组成,而EPS-2由24.5%Cr2O3、6.8%NiO组成。由氧化物含量的半峰高可以判断,EPS-1的产物膜比EPS-2的厚,EPS-1约为5.6nm,而EPS-2约为2.1nm,如图1(b)和(c)所示。需要注意,图1所示产物膜中单质态金属的存在可能是由于Ar+溅射的不均匀性以及XPS分析厚度超过产物膜厚度所致[14]。
图1不同电解工艺抛光后600合金初始表面产物膜的XPS结果
Fig.1 XPS results of the films on the surface of alloy 600after different electropolishing processes:(a)depth profile of the atomic ratio of Cr/(Ni+Fe)for EPS-1and EPS-2;(b)and(c)composition depth profiles of Cr,Ni and Fe for EPS-1and EPS-2
2.2 腐蚀试验
2.2.1 氧化膜形貌
两种抛光工艺均能在试样表面形成双层结构的氧化膜,即连续致密的内层和由分散的颗粒状或针状氧化物组成的外层。试样在晶界处存在凸起或沟壑,这是由于电解抛光工艺所致,并非腐蚀后形成的。由图2(a)可见,试样经过25h腐蚀试验后,样品表面形貌与原始形貌几乎相同,只有极少的小颗粒形成;经120h腐蚀试验后,EPS-1形成稀疏分布的小颗粒和针状氧化物;经500h腐蚀试验后,氧化膜外层的氧化物尺寸和密度都明显增加,其中颗粒状氧化物大小不均,小颗粒约几百纳米,大颗粒约5μm,针状氧化物长度约3μm。由图3可见,EPS-2具有相似的腐蚀行为,经500h腐蚀试验后,EPS-2形成的颗粒状氧化物分布密集,尺寸小,仅有几百纳米,针状氧化物尺寸比EPS-1的小。
2.2.2 氧化膜厚度与成分
图4中y轴代表铁、铬、镍、氧四种元素的相对含量,其中,氧元素含量是氧元素占三种金属元素和氧元素总和的原子比。由图4和图5可见,经不同抛光工艺抛光后,表面氧化膜具有不同的厚度(从氧的半峰高估计出氧化膜厚度)和化学成分。随着腐蚀时间的延长,两种氧化膜的厚度都增加,且EPS-1氧化膜的厚度比EPS-2的厚。腐蚀时间从1h延长到500h,EPS-1表面氧化膜的最高铬含量分别为4 3.4%,34%,33.2%,35.7%,34.3%,而EPS-2表面氧化膜的最高铬含量分别为47.5%,37.3%,42.7%,39.6%,31.2%。两种表面中的铬含量都在1h腐蚀试验后达到最大,EPS-1中的最高铬含量随腐蚀时间的延长基本不变,而EPS-2则逐渐降低。氧化膜外层富含镍和铁,而内层富铬,说明氧化膜外层可能是Ni-Fe氧化物,而内层可能是Ni-Cr-Fe氧化物。
图2 EPS-1经不同时间腐蚀试验后的表面形貌
Fig.2 Surface morphology of EPS-1after corrosion for different times
图3 EPS-2经不同时间腐蚀试验后的表面形貌
Fig.3 Surface morphology of EPS-2after corrosion for different times
图4两种电解抛光后600合金经不同时间腐蚀后形成产物膜厚度方向的XPS成分分析结果
Fig.4 XPS composition profiles of the oxide scale formed in EPS-1and EPS-2for different corrosion times
由图6(a)和图6(b)可见,在腐蚀前期,两种氧化膜的表面主要会形成铬的氧化物,这与文献一致[15]。两种表面膜的区别在于各组分的含量不同。对未溅射表面进行价态分析发现,EPS-1中的氢氧化物含量高于EPS-2的,尤其是Ni(OH)2的含量,EPS-1中的Ni(OH)2含量为23.4%,EPS-2中的为13.9%。而氧化物中的Cr3+含量基本相同,EPS-1中为14.1%,EPS-2中为13.7%。溅射15s后得到两种表面膜的次表面,其氢氧化物含量明显比未溅射表面的低,都小于10%。但EPS-1中的氢氧化物含量仍比EPS-2中的高,而氧化物中的Cr3+含量都明显增加,但EPS-1中的低于EPS-2中的,分别为31.9%和40.1%,而Ni2+含量相差不大,分别为9.7%和6.1%。对于EPS-1,其氢氧化物中的Cr含量占25%,而EPS-2中约为13%。随溅射时间增加,氢氧化物消失,剩下富铬的氧化物。
图5 EPS-1和EPS-2两种氧化膜厚度随腐蚀时间的变化曲线
Fig.5 Thickness of the oxide scales in EPS-1and EPS-2as a function of corrosion time
腐蚀500h后,两种抛光表面形成的氧化膜价态分布不同,如图6(c)和(d)所示,但都为两层结构,即富铬内层和由氢氧化物和氧化物组成的几乎不含铬的外层。EPS-1的内层氧化物中Cr3+的原子分数为47.7%,而EPS-2是58.1%,比EPS-1的高,这与图4(i)和(j)中铬元素占比较低相反。需要说明的是,在氧化膜中起保护作用的是Cr3+而不是Cr,因此Cr3+占比更能反映出氧化膜保护性的差异。另外,由于Ar+溅射过程是一个宏观均匀过程,因此XPS数据同时包含内层氧化膜和外层颗粒的信息。在腐蚀初期,氧化物颗粒的尺寸和密度都很小,可以认为得到的都是内层氧化膜的信息。在腐蚀后期,外层氧化物的尺寸和密度都不可忽略,因此图6是一个综合了氧化膜内层和外层的分析结果。
2.3 讨论
2.3.1 电解抛光初始产物膜
经不同电解抛光工艺形成的表面产物膜具有不同的成分和结构。研究表明[16,17],电解抛光形成产物膜的成分和结构不仅跟基体材料的性质有关,还跟电解抛光工艺有关。电解抛光可能会造成铁、镍的优先溶解,从而形成富铬产物膜[8]。M.Datta[18]研究纯铁在磷酸-硫酸溶液中电解抛光时,发现向溶液中增加Fe3+会明显改变表面产物膜结构,这是由于电解抛光过程中会在样品表面形成一层盐膜,改变电解抛光液成分会改变盐膜的性质,从而改变表面氧化膜结构。因此,本工作中所采用的两种抛光溶液在电解抛光过程中会形成两种性质的盐膜,影响电解抛光过程,从而形成两种性质的表面,即EPS-1和EPS-2。电解抛光形成产物膜的具体结构,不同研究者有不同的表述[13,17,18]。Maurice[12]发现316不锈钢电解抛光表面产物膜的组成复杂,这与电解抛光条件有关,并与本工作结果一致,即都是由氢氧化物和氧化物组成。如前文论述,EPS-1形成的产物膜比较厚,且氢氧化物尤是Ni(OH)2的含量高于EPS-2中的。
图6两种电解抛光后600合金经不同腐蚀时间后形成产物膜厚度方向的元素价态分布
Fig.6 Composition depth profiles of Ni,Cr and Fe ions in the oxide films in EPS-1(a,c)and EPS-2(b,d)after 1h(a,b)and 500h(c,d)exposure
2.3.2 高温高压水中的腐蚀行为
在高温高压水中,两种电解抛光工艺产生的表面成分和结构不同的初始表面膜会转变为成分和结构有差异的产物膜。首先,在高温高压水中,氢氧化物的存在,会使表面膜不够致密,保护性差。氧化物在高温高压水中会发生溶解,其过程可能是先与水反应生成氢氧化物,然后通过氢氧化物溶于水中[19]。由于镍的溶解速率比铬的快[20],因此Ni(OH)2可能会在高温高压水中优先溶解,形成不致密的氧化膜。文献[21]报道,由于Ni(OH)2的存在,600合金在一回路水环境中形成的氧化膜的保护性较差。另外,由于氧化膜中铬的氧化物占主要部分,因此Cr(OH)3的溶解速率较慢。具体反应[19]如下:
也有文献认为,在内表层氧化物晶界处形成的氢氧化铬可能成为元素快速扩散的通道[7,19],增加了腐蚀速率。其次,氧化膜内层的铬含量是影响高温高压水腐蚀的重要因素。Machet[15]研究了600合金在325℃时的短期腐蚀行为,认为原始表面存在的氢氧化物会发生脱羟基反应生成晶态氧化物,其化学反应如下:
文献[20]认为,在高温高压水中,由于镍、铁等元素在氧化膜中的扩散速率比铬的快,因此镍、铁等元素也有可能以离子形式溶解在水中,在氧化膜中留下空位,氧填补这些空位向内扩散,在界面处优先与铬发生反应生成Cr2O3[21,22],形成富铬氧化膜。也有文献认为,基体氧化过程中,铬优先于镍、铁与氧发生反应,在初始表面形成一层具有保护性的Cr2O3膜[19,20]。文献[19]指出,在低溶解氧条件下,Cr2O3会稳定存在,并对基体起保护作用,而在高溶解氧条件下,Cr2O3不稳定,铬会快速溶解,腐蚀速率加快。因此在DO<5mg/L条件下,Cr2O3的存在会对基体起到保护作用。
综上可知,两种电解抛光表面的初始膜中铬含量和氢氧化物含量不同,尤其是Ni(OH)2含量不同,会导致在高温高压水中形成的氧化膜中铬含量和氢氧化物含量不同,进而产生不同的高温高压水腐蚀行为。如图1(b)和(c)、图6(a)和(b)所示,EPS-1初始表面膜中铬含量与EPS-2相近,但氢氧化物多,不够致密。而EPS-2中氢氧化物尤其是Ni(OH)2含量少,在高温高压水中生成的氧化膜比EPS-1的致密,各元素在氧化膜中扩散速率较慢,可形成含铬量高的氧化膜。经1h腐蚀试验后EPS-1氧化膜中的最高铬含量虽然从初始状态的约35%增加到45%,但其中氧化物中的Cr3+含量基本不变(从32.6%到31.9%)。另一方面,EPS-2初始表面膜中铬含量略低,氢氧化物少,经1h腐蚀试验后最高铬含量从约35%增加到约50%,其中氧化物中Cr3+含量从24.5%增加到40.1%,高于EPS-1,在随后的高温高压水腐蚀中,表现出更好的保护性。
在高温高压水中,两种电解抛光表面腐蚀行为类似,但腐蚀动力学有差异,EPS-1的腐蚀程度大于EPS-2的。腐蚀试验后观察到两种电解抛光表面形成的氧化膜都呈双层结构,这与文献报道一致[5,6,7,8,9,23]。外层为富铁、镍大颗粒氧化物,内层为富铬氧化物,并且尖晶石结构氧化物的化学组成具有非化学计量比的特点[11]。疏松的外层对基体没有保护作用,内层可以阻止基体进一步被氧化,控制着基体的腐蚀速率。外层大颗粒氧化物的生长主要通过溶解/沉积机制而形成,氧化膜内层是由氧通过氧化膜向基体侧扩散与基体金属反应形成[7,11,15]。EPS-1与EPS-2形成的氧化膜主要差别在于内层。EPS-1氧化膜内层由于Cr3+含量低,保护性较差,具有较快扩散速率的镍、铁离子更容易通过氧化膜扩散到溶液中,再以沉积机制在氧化膜表面形成分散的颗粒状、针状氧化物,氧也更容易通过氧化膜扩散到氧化膜/基体界面,与金属原子反应,使氧化膜内层向基体侧生长。而EPS-2形成富铬程度高的氧化膜,保护性好,各种离子在氧化膜中扩散速率相对较慢,形成较薄的氧化膜。从图5中铬价态分布上可以推断,EPS-1形成的内层氧化膜可能是由氧化物和少量氢氧化物混合组成的,而EPS-2可能是由氧化物组成的。文献[7,21]指出,氧化膜中的氢氧化物可能会提供离子快速扩散的通道从而导致腐蚀速率增加,因此EPS-2形成的氧化物致密性可能更好。
3 结论
(1)电解抛光工艺对镍基600合金表面成分与结构有明显影响,与EPS-2相比,EPS-1所采用的电解抛光工艺形成氢氧化物含量高且厚度大的产物膜。
(2)EPS-1与EPS-2初始表面成分与结构的不同会对高温高压水环境的腐蚀产生影响。氢氧化物含量高的EPS-1表面膜在高温高压水中转变为致密性差、富铬程度低的氧化膜,各离子在该氧化膜中扩散速率快,增加了氧化反应速率,形成较厚的氧化膜。
免责声明:本网站所转载的文字、图片与视频资料版权归原创作者所有,如果涉及侵权,请第一时间联系本网删除。
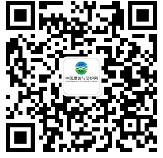
官方微信
《腐蚀与防护网电子期刊》征订启事
- 投稿联系:编辑部
- 电话:010-62316606-806
- 邮箱:fsfhzy666@163.com
- 腐蚀与防护网官方QQ群:140808414