核电厂二回路为封闭的汽水循环回路,其主要功能为将高温高压蒸汽导入汽轮机做功后冷凝,再将冷凝水逐级加热送至蒸汽发生器二次侧产生蒸汽,并维持这一汽水循环不断运行。二回路由蒸汽发生器、汽轮机、凝汽器、多级给水加热器、除氧器、主给水泵等设备和相应的汽水分离再热、抽气疏水、蒸汽发生器排污及其他辅助系统组成。图1为某核电厂二回路热平衡简图[1] 。
核电厂二回路管道主要选用低碳钢管件焊接连接。由于蒸汽发生器是压水堆核电厂一回路和二回路的主要压力边界,为关键的核安全1级设备,其结构复杂、检修更换成本高,因此从蒸汽发生器运行的安全性和经济性角度考虑,二回路水化学控制主要是创造一个低腐蚀的还原性条件以保证蒸汽发生器的使用寿命。一般通过在除盐水中加入联氨等除氧剂除氧,加入吗啉、氨等碱化剂调节pH,将二回路溶解氧质量浓度控制在10μg·L-1以下,pH控制在9.6~9.8(25℃),其他有害离子如Cl-质量浓度约为1μg·L-1。在此水化学环境中,二回路设备管道的腐蚀速率总体缓慢,给水总铁含量约为1μg·L-1[1,2] 。
但溶解氧含量低的环境不利于低碳钢管线内壁形成稳定而致密的氧化膜,管线局部位置由流动加速腐蚀(FAC)造成的减薄会比较显著。此外,由于结构或压力突变,一些节流孔板、压力控制阀、疏水减压阀等设备下游会产生高流速并发生介质的相态、流态变化,不仅会加剧FAC,也可能造成冲蚀(EC)。与FAC相比,EC造成的管壁减薄速率更快,甚至会形成常规超声测厚难以准确探查的冲蚀沟槽,管线短时间内即可发生泄漏。运行经验表明,FAC和EC是核电厂二回路管道的主要腐蚀降级形式。
图1 某核电厂二回路热平衡简图
(1)蒸汽发生器;(2)高压缸;(3)汽水分离再热器;(4)低压缸;(5)发电机;(6)凝汽器;(7)1号低压加热器;(8)2号低压加热器;(9)3号低压加热器;(10)除氧器;11 5号高压加热器;12 6号高压加热器
1986年12月9日,美国Surry核电站二回路管线破口,造成4人死亡,4人重伤;2004年8月9日,日本Mihama核电站二回路管线破口,造成4人死亡,7人受伤。据统计,由于对核电厂二回路管道的腐蚀降级缺乏认识,世界范围内核电厂二回路腐蚀降级造成的管道破口事件已有上百起,严重影响了核电厂人员安全和机组安全、可靠、经济运行。因此,对核电厂二回路管道的腐蚀降级进行有效的监督和控制至关重要。
本工作根据二回路管道的设计、运行特点,讨论了FAC、EC的机理及影响因素,对气液两相环境中管线不同程度的腐蚀损伤特征进行了分析,研究了相应的敏感点识别方法。
1 二回路管道的FAC和EC
1.1 二回路管道的FAC
FAC是一种电化学腐蚀。对于低碳钢等合金,溶液中阳极溶解和沉积作用会在金属基体表面形成一定厚度的Fe3O4氧化膜,这一多孔扩散阻碍层能够降低溶解氧和Fe2+的传质速率;同时,Fe3O4氧化膜也会在溶液的还原作用下溶解。当Fe3O4的生成速率与其溶解速率达到平衡时,Fe3O4多孔扩散阻碍层的厚度保持不变,可防止金属进一步腐蚀。但是,随着溶液流速逐渐增大,金属基体及其氧化膜附近的Fe2+浓度梯度随之增大,氧化膜溶解加速,多孔扩散阻碍层减薄,进而加快了Fe2+的扩散和迁移,使金属基体不断腐蚀减薄,见图2。
图2 FAC减薄机理示意图
考虑氧化膜的稳定性和Fe2+的扩散性,FAC的影响因素主要为材料、环境和流体动力学3方面。
合金元素是影响金属氧化膜稳定性和溶解度的内因,适当增加低碳钢中的铬含量可显著提高其抗FAC能力,合金元素铜、钼也能缓解FAC。
影响FAC的环境因素包括温度、pH、溶解氧含量等。液态单相流150℃、汽液两相流180℃时FAC速率最大;pH控制在9.5以上时,FAC速率随pH增大急剧减小;溶解氧质量浓度低于10μg·L-1时FAC敏感性大,当溶解氧质量浓度达到90μg·L-1时FAC可忽略不计。
流体动力学因素主要包含流速、结构、粗糙度等,通过影响Fe2+向主体溶液中扩散、迁移的传质速率来起作用。
1.2 二回路管道的EC
EC指高速液滴或者液流冲击机械力作用下造成管道内壁氧化膜及金属基体损伤的一种腐蚀形式。由于低碳钢Fe3O4氧化膜和不锈钢钝化膜在高温液态单相环境中具有较高的力学稳定性,因此核电厂二回路管道发生的EC主要以气液两相下的液滴冲击侵蚀、空泡腐蚀和闪蒸冲刷等损伤形式为主,运行经验表明二回路管道也存在液态单相流下的喷射切割损伤。
液滴冲击侵蚀是指掺杂在气相中的液相微粒在高速气流带动下持续离散地冲击管道内壁,使氧化膜或金属基体表面接触应力显著升高而发生局部磨损,弯头、三通、孔板、阀门等处的结构或压力变化往往会使二回路管道遭受液滴冲击侵蚀。
空泡腐蚀是指高温高压流体的压力下降至饱和蒸汽压以下后,液相中形成大量微小汽泡,这些汽泡被带到下游高压区后随即发生剧烈爆裂,靠近管壁处的大量汽泡爆裂导致管道内壁发生高频疲劳损伤。
闪蒸冲蚀是指高温高压液态单相流或气液两相流的压力在突然下降至饱和蒸汽压以下后,流体中的液相迅速汽化,流体体积急剧膨胀,流体流速骤然加快使管道内壁氧化膜或金属基体受损的一种破坏形式。流体以气相为主时闪蒸作用实际上是加速了液滴冲击侵蚀,而以液相为主时,闪蒸作用使流体加速在管道内壁形成光滑的磨痕。
液态单相流下的喷射切割损伤是指高温高压的液态单相流在流经高压差小开度阀门后,由于压力骤降产生小股高速流体对管道金属基体的机械切割损伤,高速液流会在管道内壁沿流向切割出锋利的沟槽。同时,由于压力突然下降,也会伴随一定程度的液滴冲击或闪蒸冲蚀。
2 液态单相介质中的FAC损伤特征
以某给水泵暖泵管线节流孔板下游管线为例,采用体式显微镜和扫描电镜等设备研究了管道在液态单相介质中的FAC损伤特征。管道运行温度142℃、运行压力7 MPa。管道尺寸为DN20,材料为ASME SA106B,采用电感耦合等离子光谱发生仪测定管段母材中铬的质量分数为0.10%。
2.1 液态单相条件下的腐蚀损伤
图3为液态单相环境中,未发生腐蚀损伤和发生腐蚀损伤的管道内壁形貌。两者均已累计运行10a。由图3(a)可见,管道内壁被均匀平整的氧化膜覆盖,氧化膜未发生局部溶解损伤。能谱半定量分析表明氧化膜由氧和铁组成,其中铁的原子分数为43%,与Fe3O4中铁的含量基本吻合。由图3(b)可见,管道内壁局部存在结疤状腐蚀产物,个别位置已存在较浅的腐蚀坑,这些腐蚀坑与液态单相环境中特殊工况下氧化膜的局部溶解损伤有关。
图3液态单相条件下管壁有、无局部腐蚀损伤的形貌
2.2 液态单相条件下的FAC
图4为液态单相环境中发生局部轻微FAC的管内壁形貌。该管道已累计运行4a,现场超声波测厚未发现明显减薄。管道内壁局部存在宽度较大但深度很浅的条带状凹坑,凹坑深度沿流向逐渐减小。观察发现这些深度较浅的凹坑已有氧化膜剥落迹象。能谱半定量分析表明凹坑处的铁含量为62.28%(原子分数,下同),明显高于Fe3O4中43%的铁含量,这表明表面氧化膜已存在一定程度的损伤。
图5为液态单相环境中发生轻度FAC的管内壁形貌。该管道已累计运行8a。现场超声波测厚能够发现孔板下游管道存在异常减薄,最大减薄速率为0.19mm/a。从壁厚分布情况来看,减薄区与非减薄区壁厚平缓过渡,管内壁靠近孔板位置存在密集小凹坑,凹坑沿流向逐渐变得大而稀疏。凹坑均呈马蹄形,观察凹坑底部可见,氧化膜在流体作用下发生局部溶解的痕迹。分别对氧化膜的未溶解区和溶解区进行能谱分析,发现溶解区铁含量为74.61%,未溶解区铁含量为41.87%。
图4 液态单相条件下管内壁的局部轻微FAC形貌
图5液态单相条件下管内壁的轻度FAC形貌
图6为液态单相环境中发生中度FAC的管内壁形貌。该管道已累计运行4a,根据超声测厚数据计算最大减薄速率为0.22 mm/a。从壁厚分布情况来看,减薄区与非减薄区壁厚平缓过渡。宏观可见管道内壁靠近孔板位置布满了均匀分布的凹坑,凹坑沿流向逐渐变得大而稀疏,见图6(a)。凹坑呈马蹄形均匀分布,对凹坑以及凹坑底部的能谱分析表明,表面主要由铁和氧组成,其中铁含量为62.28%,明显高于Fe3O4中铁的含量。观察凹坑底部可见氧化膜在流体作用下发生局部溶解的痕迹。
图7为液态单相环境中发生严重FAC的管内壁形貌。该管道已累计运行10a,现场超声测厚发现孔板下游管道异常减薄,最大减薄速率达0.3mm/a。从壁厚分布情况来看,减薄区与非减薄区壁厚平缓过渡。靠近孔板位置有密集的小凹坑,小凹坑呈蜂窝状,沿着流体方向凹坑逐渐变得大而稀疏。凹坑底部的氧化膜在流体作用下也呈现出明显溶解的痕迹。能谱分析表明,凹坑底部氧化膜表面主要由铁和氧组成,其中铁含量已达到66.2%。
图6液态单相条件下管内壁的中度FAC形貌
图7 液态单相条件下的管内壁严重FAC形貌
由以上分析可以发现,液态单相下管道内壁氧化膜状态受FAC速率影响,FAC速率越大,氧化膜损伤越严重,同时,氧化膜的损伤进一步加剧了FAC。对发生不同程度FAC损伤的管道内壁形貌观察可以发现,液态单相下FAC减薄区与非减薄区壁厚平缓过渡,管线靠近孔板位置即FAC敏感位置存在密集小凹坑,凹坑沿流向逐渐变得大而稀疏,微观下凹坑呈马蹄形均匀分布。这种形貌与液态单相下管道局部流态和流场相对较为稳定有关。
3 气液两相介质中的FAC损伤特征
核电厂二回路管道气液两相流流速较大,流态复杂,对氧化膜的影响强烈,对气液两相流下发生不同程度腐蚀损伤的低碳钢管线内表面宏微观特征进行了观察和分析。
管道为主气门疏水管线节流孔板下游管段,管道运行温度257.6℃,运行压力4.51MPa。管道尺寸为DN25,材料为ASME A106B,管段母材中铬的质量分数均为0.10%。
3.1 气液两相条件下局部腐蚀
图8为气液两相环境中发生局部FAC的管内壁形貌。该管道已累计运行10a。宏观可见内壁有较多结疤状腐蚀产物,有明显的沉积痕迹,能谱显示结疤处与基体处成分相近,均为铁和氧的化合物。可见在气液两相流作用下,氧化膜发生了局部溶解,溶解的氧化膜没有及时被主体流体充分带走,而是逐渐沉积在凹坑表面,形成沿流向分布的结疤。气液两相环境中,流体的流态较纯液相环境中的更复杂,流体中离子的传质速率也更高,氧化膜溶解速率较快,与2.1节所述的液态单相下的局部腐蚀损伤相比,形成的结疤和蚀坑更多,腐蚀损伤也更严重。
图8气液两相条件下局部FAC形貌
3.2 气水两相条件下FAC
图9为气液两相环境中发生中度FAC的管内壁形貌。该管道已累计运行10a,现场超声波测厚能够发现孔板下游管道存在异常减薄,最大减薄速率为0.2mm/a。
图9气液两相条件下中度FAC形貌
宏观上孔板附近区域减薄严重,减薄位置呈虎皮斑纹花样,存在强烈的流体湍流影响痕迹;沿流向虎皮斑纹花样逐渐消失,壁厚减薄量也逐渐减小。这表明流体经过孔板后由于压降发生了部分气化,形成气相为主的气液两相,气液两相流下FAC剧烈,随后温度逐渐下降,流体以液相为主。能谱分析表明,无论气液两相区还是液相区,凹坑底部氧化膜均不完整。
图10为气液两相环境中发生严重FAC的管内壁形貌。该管道已累计运行8a,最大减薄速率为0.3mm/a。可见靠近孔板处减薄严重,减薄区与非减薄区过渡较突然,减薄区壁厚出现整体损失。
宏观可见管内壁布满了小凹坑,减薄区呈现出强烈的流体湍流痕迹。微观可见减薄区凹坑呈马蹄坑状均匀分布。能谱分析表明,减薄区表面主要为铁和氧的氧化膜,氧含量很低。说明此位置形成的Fe3O4氧化膜在气液两相环境中的溶解速率较快,相应的FAC减薄速率很高。
由以上分析可以发现,气液两相下管道内壁氧化膜较液态单相下损伤更为严重,FAC速率也更大。由于气液两相条件下流体的强烈作用,减薄区与非减薄区过渡较突然,减薄区出现整体的壁厚损失,虽然最大减薄速率与液态单相下相近,但实际腐蚀失重却大很多。
图10气液两相条件下严重的FAC形貌
4 二回路管道EC损伤特征
图11为高压缸疏水管线节流孔板下游的ASME SA106B、DN25管道内壁在汽液两相条件下发生EC的形貌。孔板上游运行温度216℃,运行压力1.95 MPa;孔板下游运行温度167℃,运行压力0.64 MPa。
该管线已累计运行12a,最大减薄速率约0.5mm/a。宏观上可见孔板下游位置已经发生了腐蚀穿孔,腐蚀减薄形貌呈河流状和平滑沟槽状,微观下呈波纹状或海滩状,几乎未见稳定的氧化膜存在,为典型冲刷腐蚀形貌;在腐蚀穿孔位置下游的管道内壁也发现了马蹄坑状FAC形貌。
图12为高压加热器疏水阀下游管道内壁冲蚀形貌。管线运行10a后,现场超声测厚发现管道整体减薄并存在局部严重减薄,严重减薄处壁厚已由5mm减至1.5mm。该疏水阀上游为液态单相流,运行温度170℃,运行压力1.2 MPa;阀后连接凝汽器,考虑管阻压降等因素后阀后运行压力约为0.01 MPa。阀门小开度动作或小流量内漏时产生高压喷射流,流速可达177m/s,直接对管壁金属进行喷射切割,形成明显沟槽,高倍下沟槽底部沿流体方向存在线状冲刷凹坑。同时高温高压水经过阀门后发生闪蒸,加剧流体对管壁的冲刷,导致管道整体减薄。除喷射切割处形成的沟槽外,其他减薄位置较为光滑,为闪蒸冲刷形貌。
图11气液两相下严重的EC形貌
图12液态单相条件下的严重EC形貌
可见,EC的减薄速率明显大于FAC的,冲刷形貌也与相应腐蚀机理有关,其中高速液流可能会冲刷出窄而深的沟槽,常规超声测厚手段难以发现并准确测量剩余壁厚,需根据实际运行工况对检查结果进行判断并保守决策。
5 腐蚀降级敏感点的识别
液态单相中FAC对壁厚的影响较为温和,壁厚减薄区与未减薄区平缓过渡,管道内壁均布蚀坑,蚀坑沿流向逐渐变得大而稀疏,微观上呈马蹄坑形貌。汽液两相中FAC对壁厚影响较大,减薄区集中于局部位置或管段,减薄区壁厚发生了整体减薄,减薄区与未减薄区壁厚过渡较突然。减薄处宏观呈虎皮斑纹,微观上呈马蹄坑形貌。气液两相下发生EC时,壁厚存在较大程度的局部突变,具体形貌与相应的冲蚀机理有关。高速液流的切割冲蚀则形成锋利的冲刷沟槽,壁厚局部突变严重。
由于管道定期监督的常用方法为均匀布点实施超声波壁厚测量,因此对FAC造成的壁厚减薄较易识别,但对于减薄速率快,而泄漏危害大的EC所造成的局部减薄则容易被漏检,尤其难以准确发现沟槽状减薄区。因此,应在充分了解腐蚀降级机理的前提下,通过材料、工况、壁厚分布、内表面宏微观形貌等特征的分析,明确区分FAC和EC部件,识别出二回路的腐蚀降级敏感点,再实施针对性的定期检查和预防性维修。
对核电厂工程实际而言,二回路水化学调控趋于稳定后,影响FAC的主要因素仅限于材料、温度和流场3方面。可根据管道的材质和运行温度筛选出FAC敏感管线,进而再根据流场特征识别出管线上的FAC敏感点。而EC敏感点的识别则主要考虑流场特征。具体的敏感点识别方法可参考表1。为提高后续的定期检查和预防性维修效率,将EC和FAC敏感点按相应的影响因素分为敏感和次敏感2个级别。针对不同级别规划相应的检查计划,各相邻级别的敏感点可根据实际的跟踪检查情况进行适当的分级调整以对应不同的检查策略。
表1 二回路管道腐蚀降级敏感点识别
除实施二回路管道的定期监督外,如果通过实际运行验证能够确定为管线因FAC发生降级,可将液态单相常开管线和预期寿命小于10a的气液两相管线更换为铬含量高于1%(质量分数)的合金钢或不锈钢管道[7],如常见的P11、P22或304L等,从而彻底消除FAC失效敏感点;对于确定因EC降级的管线,可考虑引入高表面硬度的材料或表面喷涂高强度合金的方式缓解EC;对于严重的EC,必要时需要优化系统设计,降低压差从而降低局部流速,以缓解EC。但应注意,提高表面强度和改善系统设计并不能够彻底消除EC失效敏感点。
6 总结
FAC和EC是核电厂二回路管道的主要腐蚀降级形式。其中,二回路管道的FAC主要受材料、温度和流场等因素影响,而EC主要受流场和流态的影响;在液态单相流、气液两相流介质条件下FAC和EC减薄区的壁厚分布、宏微观形貌、氧化膜状态等都各不相同,可根据本文讨论确定的腐蚀降级特征明确区分各类失效形式,并对核电厂二回路管道的腐蚀降级敏感点进行有效识别和分级管理。在此基础上,通过开展针对性的监督评价、材质变更及系统设计优化,能够对FAC和EC进行有效监控,从而保障二回路管道在寿期内完整可靠。
参考文献:
[1] 赵亮,胡建群,吴志刚,等.核电站二回路管道流动加速腐蚀管理探讨[M].北京:化学工业出版社,2009.
[2] 赵亮,胡建群,吴志刚,等.秦山第三核电厂二回路管道流动加速腐蚀管理[M].北京:化学工业出版社,2010.
免责声明:本网站所转载的文字、图片与视频资料版权归原创作者所有,如果涉及侵权,请第一时间联系本网删除。
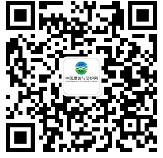
官方微信
《腐蚀与防护网电子期刊》征订启事
- 投稿联系:编辑部
- 电话:010-62316606-806
- 邮箱:fsfhzy666@163.com
- 腐蚀与防护网官方QQ群:140808414