1 前言
冲刷腐蚀 (Erosion-corrosion) , 是金属表面与腐蚀性流体之间由于相对运动而引起的金属损坏现象 , 是材料受冲刷和腐蚀交互作用的结果 , 在石油、化工等生产领域中广泛存在 , 是一种危害性较大的局部腐蚀。在石油天然气工业中 , 各种装置、设备内的液相介质流速普遍较高且大多具有腐蚀性 , 固相的摄入使得其零部件遭受严重的破坏。据Kermani 等报道 , 石油天然气工业中 9%的腐蚀失效都是由冲刷腐蚀造成的。长期以来 , 冲刷腐蚀不仅造成了巨大的经济损失 , 还在一定程度上限制了新技术与工程应用的发展。
冲刷腐蚀是一个广义名词 , 按介质不同 , 冲刷腐蚀可分为单相流、双相流、多相流冲刷腐蚀等 , 其中液 / 固两相流冲刷腐蚀在工业中最为普遍 , 相应的研究工作也最多。根据占主导机制的不同 , 冲刷腐蚀包括从以溶解占主导机制的活化腐蚀到以纯冲刷占主导机制的机械破坏之间一系列的范畴。冲刷腐蚀是一个冲刷和腐蚀在溶液中同时存在 , 并伴随复杂交互作用的过程。其中 , 冲刷是固相颗粒冲击材料表面导致材料去除或变形的力学过程 , 腐蚀是在材料表面发生化学或电化学反应导致材料去除的过程 , 这两个过程的交互作用为协同作用。在不同的研究体系下 , 协同作用可表现为正协同作用或负协同作用 ( 或称抑制效应 )。相对于负协同作用 , 正协同作用更为普遍 , 且常在材料的总冲刷腐蚀失重中占较大比重。此外 , 正协同作用又可细分为冲刷对腐蚀的促进作用和腐蚀对冲刷的促进作用因而冲刷腐蚀过程可表示为 :
式中,T 为冲刷腐蚀导致的总质量损失,E 为纯冲刷导致的质量损失,C 为纯腐蚀导致的质量损失,ΔE 为腐蚀对冲刷的促进作用导致的质量损失,ΔC 为冲刷对腐蚀的促进作用导致的质量损失。将冲刷对腐蚀的促进作用机制和腐蚀对冲刷的促进作用机制进一步细化,可分别由下面两式表示:
式中 ,ΔE p 为金相间腐蚀促进冲刷 ,ΔE m 为 腐 蚀 对 材 料 力 学 性 能 的影响 ,ΔE s 为氧化膜形成导致冲刷增加 ,ΔC f 为冲蚀颗粒破坏钝化膜或腐蚀产物膜导致下层金属表面腐蚀 ,ΔC e 为颗粒使材料表面变形进而促进腐蚀。
为了有效解决冲刷腐蚀问题 , 从而为材料的选用及防护措施的采取提供依据 , 需要确定冲刷腐蚀中占主导地位的破坏机制。国内外研究人员先后开展了大量的研究工作 , 通过实验研究和数值仿真等手段探讨了冲刷腐蚀的作用机制和控制因素。本文旨在针对冲刷腐蚀当前主要采用的研究方法和存在的问题进行综合评述。
2 冲刷腐蚀实验研究2.1 冲刷腐蚀实验装置在实验室内开展模拟工艺条件下的实验研究是当前获得材料的冲刷腐蚀性能参数行之有效的方法 , 这其中 , 实验装置起着至关重要的作用。目前 , 应用较多的实验装置包括旋转电极式试验机、射流式冲刷腐蚀试验机、管流式冲刷腐蚀试验机和 Coriolis 冲蚀试验机等。
2.1.1 旋转电极式试验机旋转电极式试验机是最早用于评价金属腐蚀性能的实验装置 , 其原理是电极浸没在浆体中随转轴高速旋转而发生冲刷腐蚀。它具有设备简单、价格低廉、测试用溶液量小、实验周期短的特点 , 是目前国内外使用最多的一种实验装置。
根据电极形状及电极装夹结构的不同 ,这种试验机主要分为料浆罐式、旋转圆柱电极式 (RCE)及旋转圆盘电极式 (RDE)等 3 种。图 1 所示为 Zhou 等开展实验研究用的旋转圆柱电极试验机的示意图。
料浆罐式试验机可以模拟水轮机叶片和水泵叶轮等工况 , 直观地反映出材料在腐蚀介质中的流失情况 , 可用于指导类似设备的选材和设计。但使用这种试验机进行实验时会因旋转而在溶液中形成涡流 , 溶液随旋转试件一起运动会降低其相对速度 ; 尽管可采用加挡板的方法消除这方面的影响 , 但这又会使流态变得复杂。除非预先开展预实验测试,否则无法确切获知浆体的流动特点和颗粒冲击条件,进而实验结果仅能对应“名义”设定的测试条件。此外 , 由于浆体流动及颗粒冲击条件非常复杂 , 颗粒粒径可能产生的影响往往难以测定。
而旋转圆柱电极和旋转圆盘电极在结构上有一定相似之处,比较适合用于流体力学因素对冲刷腐蚀影响的研究。其中,旋转圆柱电极可较好地模拟湍流流动 , 而旋转盘电极则更适合模拟层流流动。但这两种试验机在控制电极与液体的冲击角方面都比较困难 , 且冲击角通常都较小。Tian 等借助旋转圆盘电极开展实验时发现 , 电极旋转仅能将一部分砂粒带入到溶液中 , 很大一部分的砂粒都沉积在实验池的底部 , 单纯提高转速并不能显着改善砂粒在溶液中的浓度和分布。综合考虑电机转速、旋转圆盘浸入溶液的深度、旋转圆盘与容器的相对尺寸、沙含量、沙粒大小以及是否加有搅拌装置等因素 ,并只有将这些因素控制得当 , 才能获得容器中沙粒的均匀分布。由此可见 ,RCE 在钢材冲刷腐蚀研究中不容易实现量化固体砂粒作用的研究。
2.1.2 射流式冲刷腐蚀试验机射流冲刷腐蚀试验机是另外一种应用较多的实验装置 , 比较适合于研究流体流经复杂形状部件时的冲刷腐蚀作用 , 并可用于开展较高流速下的实验研究。Zu 等于 1990 年建成了一台射流式料浆冲刷实验设备 , 该设备可很好地控制冲击速度、固体颗粒浓度和冲角等重要参数 , 通过吸射式喷头结构较好地解决了料浆流动造成的泵体、管路、阀门等过流部件磨损而给实验带来的不稳定问题。
早期的射流冲刷腐蚀实验数据多采用失重法获得 , 为了能够实时获得电极表面的腐蚀电化学信息并开展冲刷腐蚀作用机制的研究 ,Barika 等在原射流式试验机设计的基础上增设了电化学测试系统 , 改进后的装置如图 2 所示。
Barika 等的设计采用 Venturi tube 原理将颗粒吸入到液体中 , 但这种方法通常要求射流速度较高 , 且从喷头流出的含砂量不能保持稳定 , 三电极测试体系结构通常也较为复杂。
从驱动泵及射流型式方面改进 ,Neville 等提出了图 3 所示的射流试验机 , 该试验机结构相对简单 , 便于开展测试 , 但存在试验机的管路及驱动泵等容易出现磨损的问题。
将射流实验同射流数值模拟相结合 , 利用数值模拟获得的流场内流速、实验颗粒轨迹等数据同实验结果进行比较 ,将有助于探讨冲刷腐蚀机理。射流实验的不足之处在于 , 除非颗粒含量很低 , 颗粒间会不可避免地产生交互影响 ; 高速射流必须穿过侧向移过表面的低速流体 , 颗粒的冲击速度将因此降低 , 冲击角也会发生变化 ; 当冲击角小于 90°时 , 流道内流型不再具有对称性 , 使流动分析变得更为复杂。此外 ,实验中颗粒的实际冲角并不等同于名义射流角度。
2.1.3 管流式冲刷腐蚀实验装置管流式实验装置由于其实验参数容易控制 , 能较好地模拟管道冲刷的实际工况 , 而且还可模拟多种流态形式 , 并有良好的流体力学模型支持 , 有利于深入开展理论分析 , 因而得到了研究者的重视。该方法的主要优点是符合管道冲刷的实际工况条件 , 实验结果有很强的实用价值 , 易于控制流速、流态 , 有良好的流体力学模型 , 实验结果可以同流体力学参数 ( 如传质系数、Reynolds 数等 ) 相关联 , 易于解释说明。
但管流装置的缺点也很突出 , 整套系统占据空间大 , 实验所需溶液量大 , 泵需要持续运转 , 实验周期长 , 对阀门、管件以及密封的可靠性要求高 , 整套装置的费用和实验费用均较高 , 所模拟的壁面剪切力相对较小等。
图 4 所示为 Postlethwaite 等于 1978 年建成的管流式实验装置 , 该装置的测试段主要包括一根仅供简单暴露性实验的样品段及一个用于三电极体系电化学测量的电化学测量池。
电化学测量池的设计如图 5 所示 , 其中 , 工作电极为一个与管内壁有相同曲率的碳钢电极片 , 将其安装在管的内壁且与管内壁保持一致 , 该电化学测量池有助于研究碳钢在较长时间内腐蚀速率的变化。这套装置的缺点在于只能用于研究水平流动式管线材料的冲刷腐蚀 , 且无法开展含有固体粒子的腐蚀性流体的冲刷腐蚀研究。
为了研究在管路突然收缩、扩张及有突起物等工况下的冲刷腐蚀作用机制 ,Malka 等开发了一种新型大规格的管流循环实验装置 , 如图 6 所示。其实验段包括一个直径比为 1.61、由粗管到细管突变的区段 , 同时在收缩管段安装有一个高出约 3mm 的突起环。测试单元为被分割成数段较薄的电极环 ,这样可方便地对扰动流流经区域开展局部电化学测试和失重测量。不过 , 该测试方法仅能获得整个电极环内表面冲刷腐蚀的统计平均数据 , 而无法对某一截面不同角度位置处进行测试。
此外 ,El-Gammala 等在设计的管路中对 90°弯头内的流致腐蚀进行了研究 , 并借助数值模拟获得了弯头内的流场数据。
2.1.4 Coriolis 冲蚀试验机Coriolis 冲蚀试验机的工作原理是通过 Coriolis 效应来加强流体与靶材表面的接触 , 其结构如图 7 所示。该试验机包含一个带有 4 个样品架的圆筒 , 圆筒绕一个竖直轴旋转 , 样品架上邻近流道处有 T 型模槽用于安装样品。测试时 , 浆体通过管路从料浆罐中泵送到旋转圆筒并经样品架流出 , 从而对样品架上的电极进行冲刷腐蚀。可通过调节圆筒转速实现对冲刷速度的调节。
Coriolis 测试方法可有效地模拟离心渣浆泵、旋风分离器及其它应用系统并开展相应材料的冲蚀磨损测试。Coriolis冲蚀试验机当前主要用于测定材料的滑移磨损系数 ( 去除单位体积材料需要的能量 )。Tian 等将其用于材料在液 / 固两相浆体冲刷腐蚀性能的研究由于不同的试验机都有各自的优缺点 , 仅适合于开展特定工况条件下的实验,但最大的问题还在于,从理论上讲,冲刷腐蚀是一种危害性较大的局部腐蚀 , 现有研究工作中采用的研究手段及方法多是基于宏观条件下的实验研究 ,仅能获得整体电极的统计平均的冲刷腐蚀信息。如何对局部腐蚀问题进行研究、表征 , 还需要展开更多的尝试及研究工作。此外 , 为了让不同测试条件下的测试结果之间具有可比性 , 迫切需要对冲刷腐蚀测试进行标准化。这些实验装置更适用于材料性能的排序 , 而将这种排序用于提供冲刷腐蚀机制信息 , 预测在役设备真实的磨蚀速率仍是一个很大的挑战。这主要是由于实验条件同工厂装置工作条件有很大不同 , 以及现场工作条件的不确定性等因素所导致。为提高实验的经济性及可行性 , 通常实验室内的测试都属于小尺寸结构内的加速冲刷腐蚀测试。此时 , 用获得的实验结果来对工厂设备进行标定将非常复杂 , 这主要是由于随着设备尺寸的不同 , 导致颗粒冲击的水动力条件也将会不同 , 从而导致冲刷腐蚀机制的差异。
2.2 冲刷和腐蚀单因素控制方法为了量化纯腐蚀、纯冲刷、腐蚀促进冲刷和冲刷促进腐蚀等几部分失重在总冲刷腐蚀失重中所占的比重 , 进而确定占主导的破坏机制 , 需要分别测定纯腐蚀、纯冲刷及总冲刷腐蚀的失重数据。
为了表征冲刷和腐蚀单独的作用 , 进行纯腐蚀实验时需要有效抑制冲刷的发生 , 同样地纯冲刷实验中则需要抑制腐蚀的发生。
2.2.1 抑制冲刷方法鉴于对纯腐蚀认识的不同 , 研究人员获得纯腐蚀的方法亦有不同。郑玉贵等曾采用静态实验的方法抑制冲刷作用 , 即将静止介质中开展的腐蚀测试结果作为纯腐蚀失重。
考虑到介质流动常常会影响到传质过程及腐蚀产物在电极表面的分布进而影响到腐蚀过程 , 当前已开展的研究中更多将在不含固相颗粒的动态介质中开展的实验测试结果作为纯腐蚀失重。
2.2.2 抑制腐蚀方法为了将腐蚀控制在可以忽略的水平 , 当前已开展的实验研究中常用的方法包括 :
(1) 阴极保护方法 : 通过施加阴极电位或阴极电流来抑制腐蚀电化学反应的发生。林玉珍等指出 , 即使在高流速条件下 , 对处于流体中的试样施加阴极电流 , 控制其电位比自腐蚀电位负 250mV 以上时 , 其阴极保护度可达98% 以上。Neville 等在研究钴基钨铬钴合金 X40 及铸铁 BS 3468 S2W 在料浆的冲刷腐蚀交互作用时 , 恒电位控制在 -0.8V(vsSCE) 作为冲击条件下对工作电极的阴极保护以抑制腐蚀作用。而实验中遇到的一些问题表明阴极保护的方法仍有一些需要解决的问题 , 包括 :
施加阴极保护电位过低将不足以提供全部保护 , 仍会有残余腐蚀存在 ; 施加的外加电流会加大 H 还原电流 , 导致产生过多 H 渗入到金属基体内。同时 , 阴极保护会改变界面化学组成 , 且样品成为阴极 , 需将阴极反应加以考虑。
(2) 控制溶液溶氧量 : 由于在一些盐溶液中的阴极反应主要是吸氧腐蚀 ,通过控制介质中溶氧量可以抑制阴极反应的发生 , 进而控制材料的腐蚀。Malka等在 NaCl 溶液中采取充 N 2 至饱和去除溶液中溶氧及控制中性 pH 值方法来研究纯冲刷作用。但该方法仅适合于近中性或偏碱性的盐溶液中 , 使用范围很有限。
(3) 添加缓蚀剂 : 选用适宜的缓蚀剂 , 亦可以有效地控制腐蚀的发生 , 缓蚀剂包覆在金属和砂粒表面 , 形成一种很薄的有机膜 , 从而起到保护作用。但是 , 在加速实验中缓蚀剂可能部分或完全地被冲走却无法控制。
(4) 采用非腐蚀性的替代液 : 如采用自来水或钝化性溶液替代海水等腐蚀性溶液 ,Harvey 等在研究碳钢 (En3B) 材料在含砂溶液中的纯冲刷性能时 , 即用0.1mol/L NaOH 替代原 3.5%NaCl( 质量分数 ) 溶液。该方法可以抑制腐蚀的发生 , 但溶液的改变会改变界面的化学组成 , 生成一种在原腐蚀性溶液中所观察不到的氧化膜 , 进而对冲刷也产生一定的影响。
2.2.3 电化学划痕法电化学划痕法是指人为地在电极表面制造一段划痕 , 从而使新鲜的金属暴露在介质环境中的方法。该方法由于测试方便、操作简便的特点 , 在研究冲刷腐蚀的作用机制时有一定的优越性 , 常用于钝化金属及合金的再钝化机制研究 , 同时也用于腐蚀环境下的材料磨蚀研究。由于冲刷腐蚀的研究体系中常包括固 / 液两相 , 而电化学划痕法的研究体系仅为液相 , 所以电化学划痕法主要是应用于磨损腐蚀而非冲刷腐蚀的研究。但是 , 利用电化学划痕法研究磨损腐蚀的思路与冲刷腐蚀的研究有类似之处 ,Wang 等采用该方法结合其它测试手段 , 获得了 3 种材料在 3.5%NaCl 溶液及自来水中腐蚀、磨损和协同作用在总失重中的比重。此外 ,Guo 等则采用电极划痕法模拟固体颗粒冲击样品表面 ,去除腐蚀产物或产物膜 , 从而导致新鲜的金属表面暴露在腐蚀环境中 , 材料遭受严重腐蚀破坏的过程。
2.3 冲刷腐蚀实验的测试方法2.3.1 重量损失测试方法在冲刷腐蚀的实验研究中 , 传统的测试方法是通过测量材料的重量损失( 简称失重法 ) 来计算冲刷腐蚀速率。
失重法的特点是操作简单 , 主要是对试样实验前后的重量进行测试和比较 , 容易实现。为了获得准确数据 , 在称量天平精度确定的情况下 , 要求失重数据尽可能大 , 因而也就需要比较长的实验周期。由于失重法只能获得材料总体的损失速率 , 给出的统计平均数据不能满足深入研究的需要 , 但该方法在当前冲刷腐蚀作用机制的研究中又是不可缺少的 , 它常被用来获得纯腐蚀、纯冲刷和总冲刷腐蚀的失重。
2.3.2 电化学测试方法相比之下 , 电化学测试方法的优势则比较突出 , 原因在于该方法可以定量地测定冲刷腐蚀速率 , 或定性地提供工作表面上的腐蚀信息 , 可实时记录工作表面的腐蚀反应状态。电化学测试可通过电化学仪器对试样的状态进行在线监测 , 选用不同的分析方法可得到冲刷腐蚀进程中不同时刻的实时腐蚀数据 , 实验周期短 , 精确度高 , 与失重法配合使用 , 有助于深入研究冲刷腐蚀的作用机制。其缺点是电化学测试是以三电极体系为前提的 , 进行测试前需要设计出巧妙的结构来满足三电极的安装和测试要求。另外 , 电化学仪器测试中容易受到干扰 , 需要做好屏蔽措施。
当前常用的电化学测试技术包括极化曲线和电化学阻抗谱等。此外 , 电化学噪声测量方法也被愈来愈多地应用到冲刷腐蚀研究中。Rajahram 等就曾利用电化学噪声方法研究不锈钢UNS S31603在颗粒冲击下的去钝化和再钝化过程。
Wood 等的研究表明 , 电化学噪声方法可以实时清晰地对冲刷腐蚀条件下涂层破裂 , 如电解质渗透、涂层剥落等行为做出实时响应 , 并指出电化学噪声方法的主要优点是 :1) 利用它开展研究不会对体系带来人为的干扰 ;2) 与仅可获得少量信息的传统测试方法相比 , 电化学噪声方法对局部腐蚀过程更为敏感。
2.3.3 其它测试方法激光 Doppler 测速仪 (LDA) 因适合于紊流条件下局部干扰流场的测量 , 在冲刷腐蚀研究中也有一定的应用。早期Blatt 等运用 LDA 对管流实验装置中流型突变部位单相流和液 / 固双相流的流速、流态进行测试。国内郑玉贵等首先在一套管流式实验装置上配置了二维激光 Doppler 测试系统 , 开展了扰流条件下的冲刷腐蚀实验并定量测量了扰流场的流速、流态。
因声发射技术 (AE) 可对材料的受力变形、断裂等产生响应 , 人们认为可利用该技术来监测颗粒对材料的冲击行为,并获得颗粒的冲击频率及能量分布。
基于此 ,Burstein 等创新性地将声发射技术应用到冲刷腐蚀的研究 , 测试了不同冲角下颗粒对电极表面的冲击作用。
3 冲刷腐蚀的数值模拟计算随着计算机技术的快速发展 , 数值模拟方法在冲刷腐蚀的研究中有愈发广泛地应用。与单纯理论计算相比 , 数值模拟在研究流体力学问题时可以得到数值解 , 更能适应研究复杂工程问题的需要。和实验相比 , 数值模拟不会受到实验条件的种种限制 , 能够很好地指导实验 , 更能大幅度节省实验费用和时间 ,特别是对实验难以完成的某些测量 , 则可以用计算机作数值模拟。数值模拟的优点还在于 , 在研究流道结构对冲刷腐蚀的影响时 , 能够清晰地观察到易腐蚀部位的流场情况 , 方便提取流动参数 ,如压力、剪切应力和紊流度等 , 可结合流动情况和参数变化规律深入分析侵蚀原因 , 同时还能较为直观地给出颗粒相运动信息 , 如颗粒对过流部件壁面的碰撞作用等 , 进而对冲刷腐蚀速率进行计算和预测 , 这有利于进一步揭示多相流中冲刷腐蚀的规律及机理。为此 , 许多学者认为 , 冲刷腐蚀的数值模拟研究是很有必要的。
3.1 数值模拟技术的应用现状借助商用计算流体动力学 (CFD) 软件或自行开发模拟仿真软件是当前开展冲刷腐蚀数值模拟研究的主要方式 , 其中 CFD 软件如 Fluent 软件包的应用较为广泛 , 因其对研究人员的要求相对较低 , 可直接利用现有的程序开展研究 ,但有时也需要通过用户自定义编程引入所需的模型。与 CFD 相比 , 自行开发软件也有一定的优势 , 开展研究不受软件自身的限制 , 可自行引入数值模拟所需的模块 , 具有很大的灵活性。两种模式的思路则是相同的 , 均需要借助流体流动模型以及冲刷模型、腐蚀模型等进行计算和求解。
Ferng 等借助 CFD 方法计算获得管线内的流动参数 , 并将其与实测的局部壁面减薄数据相对应 , 通过对两者之间的关系进行研究和拓展 , 从而为管壁检测方案设计提供指导。Davis 等利用 CFD可以计算 O 在流体中的扩散及向反应面转移的特点 , 研究了收缩 - 扩张几何模型内的冲蚀磨损情况 , 获得的磨蚀图与实验结果有较好的一致性。Telfer 等用 CFD 软件研究了颗粒浓度、粒度等对Fe 等纯金属在水 / 砂两相流中的冲刷腐蚀机制的影响。由于射流实验中浆体冲击试样的名义角度和颗粒实际冲角是不同的 , 为此 Gnanavelu 等利用 CFD 软件给出局部的颗粒冲击速度、冲角与距测试面中心半径位置的函数关系。Bozzini等运用 CFD 软件模拟了两种互不相溶液体、气体、固体颗粒等四相流对管道弯头的冲刷腐蚀 , 分别研究了气相体积分数、流体流速、固相含量等因素对腐蚀的影响。Hu 等借助 CFD 模拟得到弯曲及焊点部位的流动行为 , 从而辅助分析管道的失效原因。此外 , 张政等利用 CFD研究了突扩圆管中液 / 固两相流冲刷腐蚀过程。
北京化工大学的研究人员利用自行编制的程序分别开展了层流、紊流条件下 , 单相或两相流中 , 碳钢、不锈钢等材料的流动腐蚀数值研究 , 探讨了表面剪切力与腐蚀速率的关系 , 得到的结果与实测值有较好的一致性。
3.2 冲刷腐蚀的计算模型开发计算模型最初的目的在于 , 用数学方程的方法量化在某种工况下冲刷腐蚀所造成的材料损失 , 初步判定腐蚀过程的类型及程度 , 从而为操作的优化和材质的选用提供依据。如 Stack 等先后通过模型计算及实验获得相关数据 , 根据表 1 中对机制的分类 , 构建了不同研究体系下的冲刷腐蚀机制图,分别表征了外加电位、颗粒含量、颗粒速度、溶液 pH 值、氧浓度、流速和冲击角等因素下的冲刷腐蚀机制 , 可用于识别不同条件下材料的损失机制和水平 , 该图可以成为选择材料和优化过程参数潜在的有力工具。同时 , 冲刷腐蚀计算模型的建立也为数值模拟的开展提供了可能。
3.2.1 冲刷计算模型目前的冲刷模型可包括由 Finnie 于1958 年首次提出的基于微切削的模型 ,由 Bitter 对 Finnie 的切削模型修正后提出的变形磨损理论模型 , 由 Mamoun 首先提出并经 Hutchings 扩充的基于低循环疲劳的疲劳模型 , 由 Sundararajan 等提出的局部化模型 , 针对充分硬化的钢由Hien等和Shewmon等提出的“绝热剪切-导致剥落”模型 , 由 Levy 提出的挤压锻造“成片”模型 , 由 Jahanmir 提出的脱层理论模型等。
由于研究人员对冲刷机制认识的不同 , 侧重点各异 , 而且冲刷受到环境、材料、几何结构等众多因素的影响 , 至今仍未提出一个得到广泛认可并应用于生产实践的理论模型。因此 , 目前研究人员往往根据研究体系及研究因素的需要 , 选用不同的理论计算模型 , 如Wood 等在开展基于冲刷模型的 CFD 模拟运算 , 进而预测阀门、管路的冲蚀情况时 , 采用了 Bitter-Hashish 冲蚀模型 ;Stack 等所开展的研究中 , 曾先后用 到 Finnie,Bitter,Hutching,Sundararajan,Sundararajan 和 Shewmon 等 模 型 , 还 曾为研究温度的影响 , 对 Sundararajan 和Shewmon 模型进行了改进。
目前 , 比较常用的冲刷计算模型是经 Bergevin 改进后的 Finnie 模型 :
对于撞击角度 α ≤ 18.5°时 , 有 :
对于撞击角度 α ≥ 18.5°时 , 有 :
式中 ,P 为材料屈服强度 ,Ucr 为流体的临界速度 ,ρ m 为失重金属的密度 ,c m 为颗粒质量浓度 ,U p 为颗粒的撞击速度。
3.2.2 腐蚀计算模型对处于活化溶解区的金属腐蚀计算模型为:
式中 ,Z 和 M 分别为转移的电子数和物质的摩尔质量 ,m 为溶解物质的种类 ( 如 Fe),Cb,O 2 为溶液主体中的氧浓度 ,fd 为引起腐蚀电流密度的分数 , 视溶解的物质在主体溶液或在质量传递边界层中氧化而定 , 即溶解氧贡献的大小 ,fd 取 1 ( 氧化在溶液主体 ) 或 2/3( 氧化在质量传递边界层 ),fe 为冲刷对腐蚀过程的增强因子 ,D 为扩散系数 ,Uf为流体流速 ,drce 为旋转圆盘电极直径 ,ν 为动力粘度。
而对于钝化控制的条件 , 钝化过程会阻止纯腐蚀的进一步发生 , 总腐蚀速率可以简化为钝化膜的去除量 , 进而钝化模型为 :
式中 ,h 为氧化层厚度 ,Df 为钝化膜密度 ,c 为颗粒含量 ,υ 为颗粒速度 ,r为颗粒半径 ,D p 为颗粒的密度 ,H s 为材料静态硬度。
3.3 数值模拟存在的问题数值模拟计算在应用于冲刷腐蚀研究过程中存在的主要问题为 :
(1) 边界条件的设定需要基于一定的假设。例如 , 颗粒的形状是球形 , 直径一致 ; 忽略颗粒 - 颗粒间的相互作用 , 因而要求介质中颗粒的含量较低 ;认为在颗粒含量较低时 , 固相对平板的冲击不会影响到主流场 ; 流体中各相是均匀混合的等。而这些假设往往与实际情况不符 , 得到的结果会有偏差。
(2) 数值模拟中腐蚀与冲刷的计算均要基于一定的计算模型。例如 , 双相流中腐蚀动力学模型 , 固体颗粒对金属表面冲击的冲刷模型。而随研究体系与研究条件的不同 , 模型外推能力和适用性有限 , 因此目前还没有一套通用的模型用于计算。
此外 , 由于协同机制的认识有限且因材料而异 , 因此目前尚未提出一个考虑了冲刷和腐蚀协同作用的计算模型 , 也就无法开展协同作用的数值模拟计算。
Note: Ke is total mass loss oferosion, Ke=E+ΔE, Kc is totalmass lossof corrosion, Kc=C+ΔC(3) 由于实际体系中随着冲刷腐蚀时间的延长 , 材料表面腐蚀产物的堆积或蚀坑的形成会导致壁面粗糙度加大 ,进而影响到流场内流速、流态分布 , 呈现出一个非稳定的动态过程 , 这就需要考虑液 / 固的耦合作用 , 以保证流体流动和冲刷腐蚀数值计算结果的准确性。
4 结束语一直以来 , 冲刷腐蚀不仅造成了巨大的经济损失 , 还给装备安全及人身安全埋下了隐患 , 为了有效解决冲刷腐蚀问题 , 人们紧密结合现场条件采用实验研究和数值模拟计算等手段开展了大量的研究工作。当前存在的主要问题为 :
(1) 实验研究已较好地做到了流动条件相似 , 而如何做到冲刷腐蚀行为相似以及如何用短时间的实验结果去指导现场长周期运行出现的问题仍有待于进一步解决。其次 , 冲刷腐蚀是一种危害性较大的局部腐蚀 , 现有研究工作中采用的研究手段及方法多是基于宏观条件下的实验研究 , 仅能获得整体电极的统计平均的冲刷腐蚀信息。如何对局部腐蚀问题进行研究、表征 , 还需要开发相应的局部冲刷腐蚀测试装置和方法 , 展开更多的尝试及研究工作。
(2) 数值模拟计算有助于从流动参数角度解释冲刷腐蚀问题 , 该方法的良好运用对冲刷腐蚀的预测工作具有重要意义。而数值模拟计算由于受到基于假设的合理性、计算模型的适应性、对动态过程的考虑等方面的影响 , 其结果的准确性还需要经过实验的验证。
(3) 实验研究与数值模拟计算相结合的方法是开展冲刷腐蚀研究较为有效的方法。但由于两种研究手段在结果的表现形式方面存在一定的差异 , 如何对获得的结果进行有效的对比分析 , 从而进一步指导实验设计或数值模拟 , 同样也是需要考虑的问题。
免责声明:本网站所转载的文字、图片与视频资料版权归原创作者所有,如果涉及侵权,请第一时间联系本网删除。
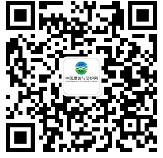
官方微信
《腐蚀与防护网电子期刊》征订启事
- 投稿联系:编辑部
- 电话:010-62316606-806
- 邮箱:fsfhzy666@163.com
- 腐蚀与防护网官方QQ群:140808414