随着全球人口增长和经济飞速发展,能源消耗迅速增加。目前,化石能源是全球主要的能源来源[1]。然而,化石能源的过度利用带来了严重的环境问题,如全球温室效应和空气质量下降等。为应对全球气候变化问题,中国政府在2020年9月提出了“双碳”目标,推动绿色低碳能源的发展。但由于地域和气候的限制,太阳能和风能等可再生能源难以及时消纳,西部地区普遍存在弃风和弃光等问题[2,3]。通过可再生能源电制氢技术将电网无法消纳的弃电转化为氢能可有效解决弃风和弃光等问题,且氢能具有环保、高的能量转化效率、来源广泛和可储能等优点[4],因此,氢能将是我国低碳能源发展的重要途径之一。氢气输送是连接H2制备储存与终端应用的关键环节,其成本占总成本的30%~40%,直接制约着氢能产业的发展[5,6]。当前,管道输氢是长距离、大规模输送中最经济、最有效的方式。但是建立新的输氢管线成本高、工程量大,而利用已有的天然气管线进行大范围输氢则具有成本低和效率高等优点,因此受到越来越广泛的关注[7]。
高压天然气运输管线主要使用X70和X80等高强度管线钢,城镇天然气管网主要使用中低强度管线钢,如X42、X52和X65等。在已有的天然气管线中掺入H2之后,管线钢将会面临氢渗透的问题,而氢在管线钢中的扩散、聚集可能会使管线钢发生氢脆,且随着管线钢强度的增加,其对氢脆的敏感性也随之增大[8,9]。因此,研究掺氢天然气管线钢的氢渗透行为对于输氢管线的安全运行评价具有重要意义。氢渗透行为的研究方法主要包括电化学氢渗透和气相氢渗透等,其中最常用的方法是电化学氢渗透 [10]。通过电化学氢渗透或气相氢渗透实验可以测得管线钢在不同条件下的“氢渗透曲线”,即电流密度与时间的关系曲线,之后根据所得的氢渗透曲线采用不同的计算模型和计算方法就可得到氢渗透参数,如有效扩散系数(Deff)、稳态时阴极侧氢浓度(C0)和氢陷阱密度等,再结合相应的表征技术,可进一步分析氢渗透机理。本文主要介绍了电化学氢渗透和气相氢渗透的氢渗透过程及影响因素,并总结了计算氢渗透参数的一些常用模型及方法。需要指出的是,本团队已经对管线钢氢渗透行为的研究进展进行了较为系统的介绍[10],本文是对其的有效补充,以期对管线钢氢渗透行为有更广泛、更深入的认识。
1 管线钢氢渗透行为研究方法
氢渗透行为的研究方法主要包括电化学氢渗透和气相氢渗透,其主要区别在于氢从外部环境进入管线钢内部的过程,而其他过程则基本一致。影响氢渗透过程的因素可分为外部环境和材料本身,外部环境因素主要包括温度和充氢介质等,材料本身的因素主要包括管线钢的组织、变形程度和样品厚度等。
1.1 电化学氢渗透
图1
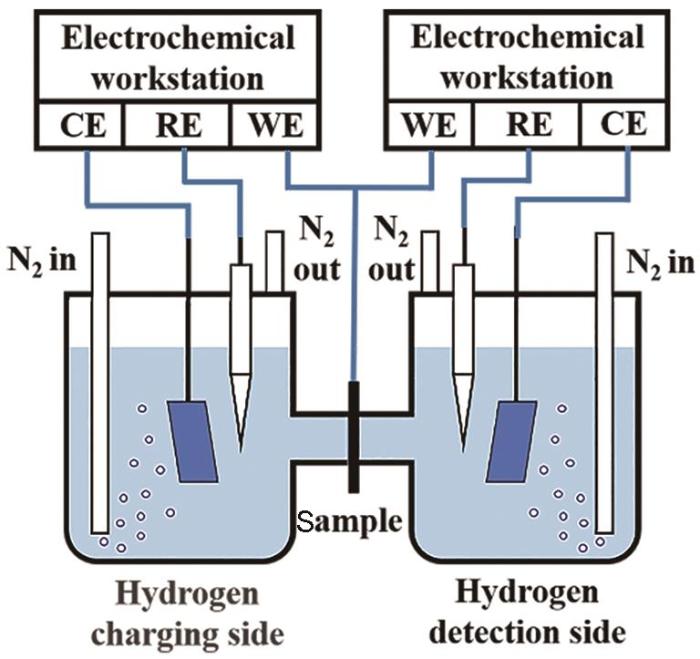
图1 电化学氢渗透装置示意图
Fig.1 Schematic diagram of electrochemical hydrogen permeation device (WE-working electrode, RE-reference electrode, CE-counter electrode)
充氢侧所用溶液的种类较多,酸性、中性和碱性溶液在文献中均有报道,并且大部分充氢侧溶液都会添加毒化剂,如(NH2)2C=S和NH4SCN等。毒化剂的主要目的是抑制样品表面的吸附氢复合成氢分子逸出,使更多吸附氢能进入管线钢,但关于毒化作用的机理目前仍不十分清楚。充氢侧一般采用三电极体系(参比电极、对电极和工作电极)或者两电极体系(对电极和工作电极),在样品表面施加恒电位或恒电流,促进氢原子的产生。恒电位充氢和恒电流充氢的区别很小,采用恒电流充氢时,要监测充氢电位,使其变化尽可能小,当充氢电位发生较大变化时,说明表面状态可能发生了变化或边界条件不稳定。当采用恒电位充氢时,条件是充氢电流没有明显的变化。此外,施加的恒电位要低于样品表面的开路电位,因此要提前测样品表面的开路电位。实验中,要根据所使用的材料、实验目的和实验结果等来选取合适的充氢方法。
测氢侧主要使用的是氢氧化钠溶液,且大部分实验都采用三电极体系。接触测氢侧溶液的样品一侧一般会镀镍或镀钯,这样可以使氢原子在样品表面更好地被氧化而提高测试精度 [9]。
1.1.1 氢渗透过程
图2
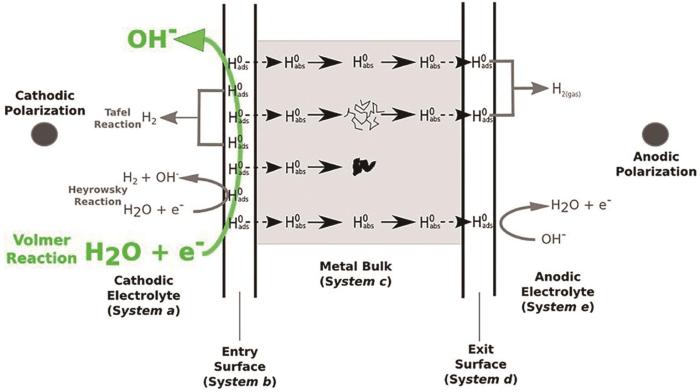
(1) 氢原子的产生与吸附(不考虑样品表面存在腐蚀产物膜的情况)
在酸性溶液中,氢离子直接在管线钢样品表面被还原成氢原子,并吸附在样品表面,如
(1)
(2)
(3)
(4)
(5)
式中,M代表管线钢表面,MHads代表一个氢原子吸附在管线钢表面。
(2)氢原子的吸收
吸附在管线钢表面的氢原子一部分去吸附并再次复合成H2分子逸出(
(6)
(7)
(8)
式中,MHabs代表一个氢原子吸收在管线钢内表面。
(3) 氢原子在管线钢内部的扩散或聚集
扩散的驱动力是化学势差,若管线钢中存在氢的化学势差,氢原子就会从化学势高的地方向化学势低的地方扩散。在电化学氢渗透过程中,氢原子在接触充氢侧溶液的样品表面大量产生,而测氢侧氢原子浓度很低,因此,氢总体上会由充氢侧向测氢侧扩散。
图3
(4) 氢原子被氧化
在测氢侧样品表面施加恒电位,确保到达测氢侧的氢原子都立即被氧化,从而实现氢扩散电流的测量,如
(9)
1.1.2 影响因素
管线钢的电化学氢渗透行为受众多因素的影响,且不同因素对氢渗透过程的影响方式不同。充氢电流密度或充氢电位和充氢侧溶液主要通过改变充氢侧氢原子浓度和影响管线钢的表面状态来影响氢渗透过程,温度对氢渗透各个过程都有很大影响,而管线钢本身主要通过影响氢在钢内部的扩散与聚集来影响氢渗透过程。
(1) 充氢电流密度或充氢电位和充氢侧溶液的影响
一般来说,充氢电流密度绝对值越大或充氢电位越负,充氢侧会产生更多的氢原子,可扩散氢浓度增大,有更多的氢原子渗透通过管线钢。因此,稳态电流密度、有效扩散系数以及稳态时阴极侧氢浓度都会随之增加。Zhang等[8]研究了X70、X80和X100三种管线钢在不同外加电位下的氢渗透行为。结果表明,随着外加电位的负移,3种管线钢的氢渗透电流密度和次表面氢浓度均增加。此外,在模拟海水中的电化学氢渗透测试中几乎没有观察到稳定的渗透电流,认为这主要是因为样品在氢渗透过程中表面状态发生了变化。Koren等[18]测试了X65管线钢在不同充氢电流密度下的氢渗透曲线。结果表明,随着充氢电流密度绝对值的增加,氢渗透电流密度增大,且采用时间滞后法与突破时间法 [11]测得的有效扩散系数也会增加。除此之外,在-1和-50 mA/cm2的充氢电流密度下,X65管线钢第2次和第3次的氢渗透曲线不重合,这表明在电化学氢渗透过程中样品充氢侧的表面状态也发生了变化。
此外,氢的扩散受浓度梯度的影响,与碱性溶液和中性溶液相比,酸性溶液中样品充氢侧会产生更多氢原子。Hu和Cheng[19]测试了X80管线钢在不同充氢溶液(0.5 mol/L H2SO4、NS4和0.1 mol/L NaOH)下的电化学氢渗透曲线,在0.5 mol/L H2SO4中所测得的稳态氢渗透电流密度、有效扩散系数以及稳态时阴极侧氢浓度比在NS4和0.1 mol/L NaOH中测得的数值大很多。
(2) 温度的影响
(3) 管线钢本身的影响
氢在具有不同微观结构的管线钢中的溶解度和扩散性不同,因此,管线钢本身对氢扩散行为也具有显著的影响。不同的管线钢的微观组织不同,氢在其中的扩散过程也会有显著不同。目前,按管线钢的微观组织结构可将其分为铁素体-珠光体管线钢、贝氏体-马氏体管线钢、针状铁素体管线钢和回火索氏体管线钢等[23]。彭先华等 [24]测得了X80和X120管线钢的氢渗透曲线,根据氢渗透曲线获得的氢渗透参数表明,X80管线钢的阴极侧氢浓度比X120管线钢的低,但氢渗透通量和有效扩散系数却均比X120管线钢的高,这说明以针状铁素体为主的X80管线钢的氢原子捕获效率低于具有板条贝氏体组织的X120管线钢。仇文杰等[25]对20#钢、16Mn钢和X52管线钢进行了氢渗透实验,结果表明X52管线钢的氢扩散系数最小,20#钢的氢扩散系数最大。
此外,同一种管线钢经过不同的热处理或者冷变形等加工过程后的微观组织和位错等会有较大差异,会进一步影响管线钢中的氢渗透行为。Yazdipour等[26]对晶粒尺寸不同的X70管线钢样品进行氢渗透实验,并通过二维扩散模型定量研究氢在晶体中的扩散。结果表明,X70管线钢的平均晶粒尺寸与单位体积中晶界面积对氢扩散过程的影响较大,在中等尺寸(约46 μm)的晶粒中,氢扩散速率最高,且单位体积中晶界面积在细晶组织中对氢扩散的影响比在粗晶组织中更明显。Yao等[27]研究了冷变形对X65管线钢氢渗透行为的影响,研究表明随着冷变形程度的增加(0.00%~7.25%),管线钢中的位错密度显著增加,有效扩散系数降低,稳态时阴极侧氢浓度增加,这表明管线钢经历冷变形后,氢渗透过程会被阻碍。
1.2 气相氢渗透
虽然电化学氢渗透方法对管线钢的氢渗透行为研究做出了很多贡献,但也存在一定的局限性。首先,电化学氢渗透过程与实际管道中的氢渗透过程相去甚远,实际管道中的氢为气态氢,而电化学氢渗透充氢侧的氢原子主要通过溶液中的氢离子被还原得到。其次,电化学氢渗透过程对管线钢表面状态的影响较大,难以反映管线钢真实的氢渗透过程。相比之下,气相氢渗透可以更真实的模拟管道的实际服役情况,可进一步研究氢压、掺氢比和杂质气体等对管线钢氢渗透行为的影响,并且气相氢渗透过程对管线钢的表面损伤较小。然而,气相氢渗透方法也有缺点,比如结果重复性不高和实验装置较复杂等,并且在实验过程中会使用到H2,H2属于易燃易爆气体,因此存在一定的安全隐患。
实验室中常用的气相氢渗透装置如图4所示,测氢侧与电化学氢渗透装置测氢侧相同,充氢侧为气态氢。
图4
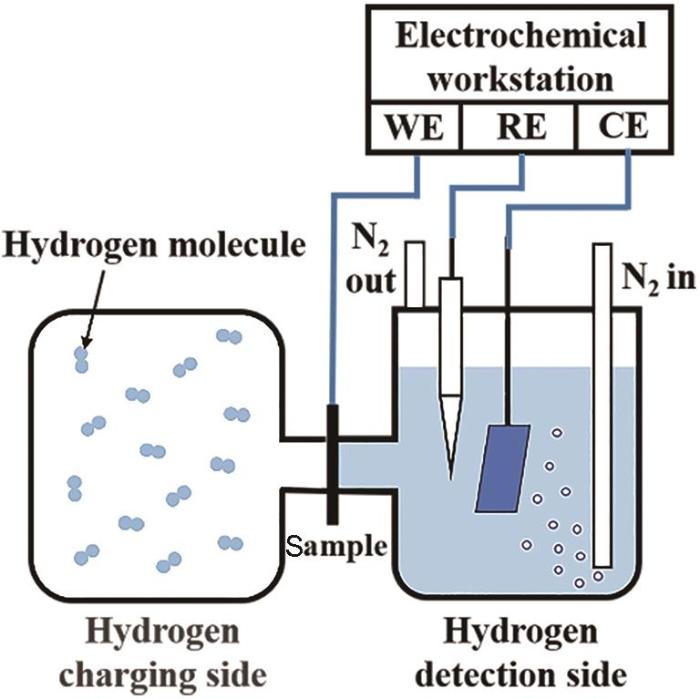
图4 气相氢渗透装置示意图
Fig.4 Schematic diagram of gaseous hydrogen permeation device (WE-working electrode, RE-reference electrode, CE-counter electrode)
1.2.1 氢渗透过程
由于管线钢表面原子和内部原子所处环境不同,因此具有不同的能量。表面原子的配位数要比内部小,原子互作用力不平衡,因此管线钢具有表面能。这种不平衡的相互作用力可将异类原子吸附到管线钢表面,从而使管线钢的表面能下降,所以管线钢表面具有吸附异类原子的倾向[15]。气相氢渗透过程同电化学氢渗透一样,也主要分为5个步骤。气相氢渗透中,氢原子的产生和氢原子的吸附过程与电化学氢渗透中的这两个过程有本质差异,而其他3个过程与电化学氢渗透中的基本一致,所以在本节中只介绍氢原子在气相氢渗透中的产生和吸附过程。
(10)
(11)
式中,MH2代表一个氢分子吸附在管线钢表面。
氢在钢表面的吸附主要研究氢原子和氢分子等微观粒子与表面的相互作用,而目前的实验手段很难真正达到原子尺度的观察,因此研究表面吸附的主要方法是理论计算[31]。
管线钢中常见的微观组织主要有铁素体、珠光体、贝氏体和马氏体等,主要的相结构为体心立方α-Fe[32],氢在体心立方α-Fe不同晶面的原子排列及吸附位点如图5所示。氢在低指数体心立方α-Fe表面吸附的研究已经超过40年,研究表明氢分子可在Fe(100)、Fe(110)和Fe(111)等表面发生解离吸附,且这一过程是放热过程 [33]。其中,Fe(110)是体心立方α-Fe的密排面,表面能最低,在晶体结构中最容易暴露出来,对氢在管线钢表面吸附的研究具有实际意义,因此氢在Fe(110)面的研究最多 [34]。氢在Fe(110)面的高对称吸附位点如图5a所示,LB、SB、OT与TF分别对应长桥位、短桥位、顶位和三重空位。王春璐等 [34]研究了H2在Fe(110)面的解离,结果表明H2能自发吸附于Fe(110)面,H2在Fe(110)面穴位上方呈直立吸附。Jiang和Carter[33]的研究表明当覆盖度在1/4到1 ML (ML为覆盖度的单位,表示吸附原子占基底原子的比例)之间时,准三重空位是唯一稳定的位点。
图5

1.2.2 影响因素
气相氢渗透中氢分子的解离吸附与管线钢表面的吸附位点息息相关,因此气相氢渗透过程受管线钢表面状态的影响较大。但是在其它条件都相同的情况下,两个样品的气相氢渗透结果也会有很大差异,所以研究管线钢表面状态对气相氢渗透过程的影响是非常困难的。由于气相氢渗透过程对管线钢样品充氢侧表面的影响较小,因此可以用同一样品来研究杂质气体、氢压和温度等对气相氢渗透过程的影响。不同的气体在管线钢表面吸附的难易程度不同,杂质气体与H2之间存在“竞争吸附”,因此杂质气体的种类与含量均会影响气相氢渗透过程。
(1) 杂质气体的影响
掺氢天然气管线中除了含有CH4和H2之外,还可能存在CO、CO2、H2S、O2、N2和水蒸气等杂质气体[39],各种杂质气体对氢渗透过程的影响不一样。Wang等 [40]研究了CO对X52管线钢气相氢渗透过程的影响,在氢分压相同的情况下,CO分压逐渐增加时,稳态电流密度和稳态时阴极侧氢浓度明显降低,说明CO会抑制氢的解离吸附,降低氢原子在钢中的渗透通量。Zhang等[41]采用热脱附谱法(TDS)和气相氢渗透研究了CO2和CO对X52管线钢氢渗透过程的影响,TDS结果表明CO2和CO的存在会降低X52管线钢中的氢含量,且CO比CO2的抑制作用更明显。此外,气相氢渗透结果也表明X52管线钢的稳态电流密度和稳态时阴极侧氢浓度都随着CO2或CO分压的增加而降低,说明CO2和CO会降低氢的表面覆盖率,阻碍氢渗透过程,且二次气相氢渗透结果表明,CO在X52管线钢表面的吸附更强、更稳定,对氢渗透过程的抑制作用更强。
当CO2和H2S等酸性气体与水蒸气同时存在时,会使管线钢表面形成腐蚀产物膜,从而对氢渗透过程产生影响。Zhou等[42]研究了低碳管线钢中H2S分压对氢渗透行为的影响。结果表明,X52管线钢的氢渗透速率受氢分压和腐蚀产物膜共同影响。当腐蚀产物膜疏松且易发生剥离时,氢渗透过程受表面的化学反应控制;当腐蚀产物膜变得致密时,腐蚀产物膜对氢渗透过程的影响更大。此外,周成双等[43]研究了CO2对X80管线钢氢渗透行为的影响。结果表明,CO2对氢渗透具有促进作用,中性环境中CO2的氢促进作用为H2S的1/20,且酸性环境中CO2氢促进作用为中性环境下的2倍,酸性环境下产生的腐蚀产物对氢渗透有先促进后阻碍的作用。
采用实验手段研究杂质气体对管线钢氢渗透行为的研究只能做到定性研究,无法深入地研究气体分子在管线钢表面的吸附位点等,而理论计算可以进一步研究杂质气体对氢在表面解离吸附影响的机理。Staykov等[44]采用模拟的方法研究了氢气杂质对Fe表面氢解离的影响。结果表明,由于O2的吸引力比H2大,少量的O2可以成功地与H2竞争表面吸附位点,在Fe表面预解离的氧会阻碍H2的解离,且CO对H2解离的抑制机制与O2的作用机制相似,但H2气体中微量的CH4对H2的解离没有影响。而Sun等[45]研究表明CH4分压的升高会降低H2吸附的热力学倾向,但并不妨碍H2解离吸附的发生。李守英等[46]研究了CO和H2在应变Fe(110)面的竞争吸附。结果表明,CO在Fe(110)面的吸附能比H2的吸附能更负,与Fe(110)面的结合能更强,如表1所示,预先吸附的CO会使H2与Fe(110)面的作用减小,且CO对氢吸附的阻碍作用随着拉应变的增大而减弱。此外,从表1中可以看出,CO在Fe(110)面的最稳定吸附位置为顶位,而H2在Fe(110)面的最稳定吸附位置为三重空位。
表1 CO和H2在Fe(110)面不同位点的吸附能(eV)[46]
Table 1
Adsorbed gas | Top | Short bridge | Long bridge | Three-fold |
---|---|---|---|---|
CO | -1.89 | -1.64 | -1.82 | -1.83 |
H2 | -0.47 | -0.82 | -1.04 | -1.33 |
(2) 氢压和掺氢比的影响
表2 不同管线钢的气相氢渗透参数在氢压或掺氢比增加时的变化趋势
Table 2
Material | Hydrogen pressure or hydrogen blending ratio | i∞ | Deff | C0 |
---|---|---|---|---|
X52[49] | 2.5%, 12.5%, 25%, 50% (total pressure: 4 MPa) | Increase | Almost constant | Increase |
X65[18] | 1 MPa, 5 MPa, 10 MPa | Increase | Increase | Increase |
X80[48] | 3%, 5%, 10%, 15%, 20% (total pressure: 10 MPa) | Increase | Almost constant | Increase |
X80[47] | 2 MPa, 5 MPa, 8 MPa (total pressure: 12 MPa) | Increase | Increase | Increase |
当氢压或掺氢比增加时,金属表面氢分子的数量增多,有更多的氢分子解离成氢原子吸附在金属表面,因此稳态时次表面氢浓度会增加。当稳态时次表面氢浓度增加时,氢原子的浓度梯度增大,扩散驱动力也随之增大,所以渗透通过管线钢样品的氢原子数量增多,稳态电流密度增大。但有效扩散系数的变化规律不一样,目前氢压或掺氢比对有效扩散系数影响的机理并不明确。
(3) 管线钢本身的影响
已有的天然气管线大多采用焊接的方法连接,焊接接头部位各区域的组织和性能存在较大差异,所以各区域组织的氢脆敏感性区别也较大[50]。因此,在研究管线钢的氢渗透行为时,除了研究管线钢基体的氢渗透行为外,管线钢焊接部位的氢渗透行为也需要重点研究。Zhao等[51]研究了高压煤制气环境下X80管线钢基体以及焊接接头不同区域的氢渗透行为。结果表明,在其他条件相同的情况下,各区域的扩散系数按如下顺序增大:基体、焊缝和粗晶热影响区,这是因为X80管线钢基体的微观组织包含许多细长的铁素体板条束,位错密度最高,更多的氢原子被捕获,所以氢扩散系数较低。而X80管线钢粗晶热影响区的微观组织主要是由粗贝氏体铁素体和粒状贝氏体组成,与其他位置相比,粗晶热影响区的位错密度较低,因此氢扩散系数最高。张体明等[52]研究了X80管线钢基体和焊接接头热影响区不同亚区在高压煤制气环境下的氢渗透行为,结果表明X80管线钢的原始组织为细小的针状铁素体,氢陷阱密度与氢溶解度最高,氢扩散系数最低,焊接接头热影响区不同亚区的有效扩散系数从大到小依次为粗晶区、细晶区和部分相变区。X80管线钢焊接接头热影响区不同亚区中,粗晶区的贝氏体铁素体组织粗大,位错密度与大角度晶界数量显著降低,对氢的捕获作用较小,有效扩散系数较大,而部分相变区的晶粒最为细小,大角度晶界含量较高,因此氢扩散系数较小。
目前,焊缝接头的电化学氢渗透行为的相关研究较多,而焊接接头气相氢渗透的研究较少,所以亟需进行更多的焊接区域的气相氢渗透行为研究,以明晰实际工况下氢对管线钢焊接区域的影响。此外,长时间服役的管道会不可避免地存在各种表面缺陷,如腐蚀和凹痕等,这些缺陷会对管线钢的氢渗透行为产生很大影响,影响管道的安全运行。但目前相关的实验研究却非常少,因此也需要设计并开展相关实验,以保证管道的安全运行。
2 氢渗透参数的计算模型及方法
氢渗透参数是评价管线钢氢渗透行为的重要依据,根据电化学氢渗透和气相氢渗透测得的氢渗透曲线可以得到的氢渗透参数主要包括稳态电流密度i∞、稳态氢扩散通量J∞、有效氢扩散系数Deff、稳态时阴极侧氢浓度C0和氢陷阱密度NT等。根据GB/T 30074-2013[53],在分析氢渗透曲线之前,要从检测的氧化电流中减去背底电流(充氢侧溶液添加之前,接触测氢侧溶液的样品表面的钝化电流)。稳态电流密度可以从测得的氢渗透曲线中读取,稳态氢扩散通量可以用稳态电流密度通过简单换算得到,如
(12)
式中,F代表Faraday常数,其值为96485 C/mol。
2.1 氢渗透参数的计算模型
由于氢渗透实验使用的样品基本都是薄片样品,所以文献中一般将氢在薄片样品中的扩散过程认为是一维扩散。电化学氢渗透和气相氢渗透方法测得的氢渗透曲线示意图如图6所示,氢渗透过程可分为非稳态阶段和稳态阶段,氢渗透过程在非稳态阶段满足Fick第二定律,如
(13)
图6
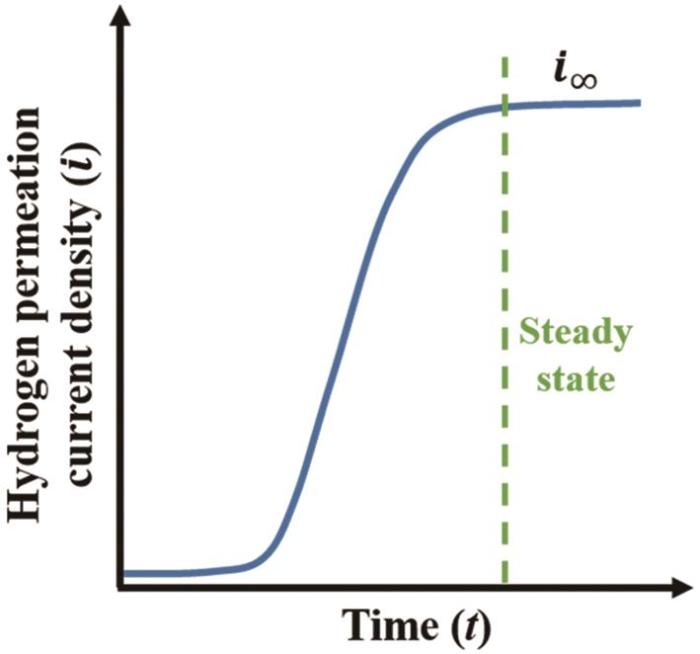
图6 氢渗透曲线示意图
Fig.6 Diagram of hydrogen permeation curve
式中,D为扩散系数,当金属中不存在氢陷阱时,氢只可通过晶格的间隙位置扩散,所测得的扩散系数为点阵扩散系数DL (或晶格扩散常数)。但是,实际使用的管线钢材料中存在各种氢陷阱,对氢有捕获作用,影响氢的扩散过程,因此测得的扩散系数为有效扩散系数Deff (或表观扩散系数)[15]。
2.1.1 CC模型
CC模型假设氢的平衡浓度在渗透实验开始时立即达到,然后在渗透过程中保持不变,其初始条件与边界条件的数学表达式如下:
(14)
(15)
式中,t为时间,L为试样厚度,充氢侧x = 0,测氢侧x = L。
根据上述条件求解Fick第二定律公式可得[57]:
(16)
式中,τ = Dt/L2,it 为t时刻的电流密度,i∞是稳态电流密度,D为扩散系数。
2.1.2 CF模型
CF模型假设充氢侧的氢通量在渗透过程中保持不变,其初始条件与边界条件的数学表达式如下:
(17)
(18)
式中,t为时间,L为试样厚度,充氢侧x = 0,测氢侧x = L。
根据上述条件求解Fick第二定律公式可得 [58]
(19)
2.2 氢渗透参数的计算方法
计算有效氢扩散系数常用的方法如时间滞后法、突破时间法、Laplace法和Fourier法都是基于CC模型得到的[59],大部分文献都采用这几种方法来计算氢扩散系数。
时间滞后法中[11],tL 为氢渗透曲线上it = 0.63 i∞的点所对应的时间,计算公式如下:
(20)
突破时间法中[11],tb是通过外推氢渗透曲线初始的线性部分到it = 0时所对应的时间,计算公式如下:
(21)
Fourier法中[59],有效氢扩散系数由ln (1-it/i∞)与时间t的关系曲线的斜率推导而来,公式如下:
(22)
Laplace法中[60],取
(23)
上述4种方法中,时间滞后法和突破时间法的计算过程简单,但需要准确记录氢渗透开始的时刻,而在电化学氢渗透或者气相氢渗透实验中,很难精准地确定氢渗透开始的时刻,总会存在误差。此外,突破时间法中的tb需要通过外推氢渗透曲线初始的线性部分得到,而在确定线性部分时,会受到人为主观因素的影响,线性部分的选取可能会对Deff的数值产生较大影响。Fourier法和Laplace法与氢渗透开始的时刻无关,当无法确定氢渗透开始的时刻时,选用Fourier法或Laplace法,但这两种计算方法较为复杂,并且在拟合时,需要选取氢渗透曲线的上升阶段进行拟合,选取过程也会对结果产生一定的影响。管线钢材料、充氢侧溶液和温度等都会对氢渗透过程产生很大的影响,氢渗透曲线也会有较大差异,因此需要根据实际测得的氢渗透曲线确定具体的计算方法。
得到Deff之后,对于给定的稳态氢扩散通量J∞,充氢侧稳态时阴极侧氢浓度C0可通过
(24)
氢陷阱密度的计算公式为 [62]
(25)
式中,DL 是晶格扩散常数。
部分文献认为第一次氢渗透反映的是可逆氢陷阱和不可逆氢陷阱对氢的共同捕获作用,第二次氢渗透反映的是可逆氢陷阱对氢的捕获作用,通过两次氢渗透实验就可以计算得到可逆氢陷阱密度和不可逆氢陷阱密度[27]。
3 结语
利用现有的天然气管线钢输氢是最经济、最有效的输氢方式,但氢会对管道的安全运行产生影响,制约着氢能经济的发展。目前,已经有很多关于管线钢氢渗透行为的研究,主要采用电化学氢渗透或气相氢渗透法进行研究。电化学氢渗透实验技术更成熟,并且已经拟定了电化学氢渗透实验的相关标准。此外,用于计算电化学氢渗透参数的模型及方法也有很多。然而,电化学氢渗透始终无法反映真实工况下管线钢的氢渗透行为,因此气相氢渗透实验的开展至关重要。但是气相氢渗透实验较为复杂,且结果重复性不高,因此相关研究较少。基于此,提出了以下几点展望:
(1) 目前已经有一些文献通过气相氢渗透实验研究了氢压和掺氢比等对管线钢氢渗透行为的影响规律,但是并没有相关研究指出不影响服役管线钢安全运行的合适的氢压和掺氢比,且杂质气体促进或抑制管线钢氢渗透过程的内在机理研究基本还停留在模拟阶段。因此,需要开展更多的研究确定合适的氢压和掺氢比,且需要进一步研究杂质气体对管线钢氢渗透过程产生影响的内在机理。
(2) 实际管线钢中存在焊接区域,焊缝及焊缝周围的微观组织与管线钢的基体微观组织存在较大差异,也有文献研究了管线钢焊缝处的电化学氢渗透行为,但是管线钢焊缝处的气相氢渗透行为研究却很少,所以亟需开展管线钢焊缝处的气相氢渗透行为研究。
(3) 除了管线钢本身的组织结构较为复杂外,管线钢的服役工况也很复杂,外在环境和内部输送的介质都会对管线钢的氢渗透行为产生很大影响,单一因素的研究无法反映实际工况下管线钢的氢渗透行为,因此需要进行多因素耦合作用下的氢渗透行为研究,以揭示复杂环境下管线钢的氢渗透机理。此外,管线钢在制造及安装过程中会不可避免的出现一些加工缺陷,会对管线钢的氢渗透行为产生较大影响,但目前相关的研究并不充分。
(4) 目前掺氢天然气的相关标准和规范还不成熟,研究掺氢管线钢在真实工况条件下的氢渗透行为及内在机理可以为掺氢天然气管线钢相关标准和规范的制定提供基础数据,从而为掺氢管道的运行提供安全保障。
免责声明:本网站所转载的文字、图片与视频资料版权归原创作者所有,如果涉及侵权,请第一时间联系本网删除。
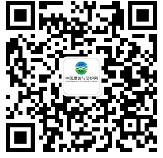
官方微信
《腐蚀与防护网电子期刊》征订启事
- 投稿联系:编辑部
- 电话:010-62316606
- 邮箱:fsfhzy666@163.com
- 腐蚀与防护网官方QQ群:140808414