高参数垃圾电站锅炉温度对腐蚀的影响及其防护技术 原创
2025-07-17 15:00:35
作者:曲作鹏,田欣利,谢广校 来源:《腐蚀与防护》2025年6期
分享至:
垃圾焚烧发电是目前国际上公认最有发展前景的垃圾处理方式,我国垃圾发电产业后来居上,目前规模全球领先。随着国内越来越多的垃圾焚 烧电站的建成运行,以及国家对垃圾处理补贴的逐年降低,原本垃圾电站处理垃圾的功能已相对弱化,提高垃圾焚烧锅炉的主蒸汽参数是提升垃圾电站的经济效益的必然选择。然而,高参数垃圾电站锅炉每年因腐蚀引发的事故远高于中参数垃圾电站锅炉。锅炉四管(水冷壁、过热器、再热器、省煤器) 属于压力部件,一旦发生管壁腐蚀减薄就容易出现爆管事故,从而造成锅炉非规性停机,这不仅对垃圾电站的发电效率及经济效益产生巨大影响,还严重影响了人员与设备安全。因此高参数锅炉管道的腐蚀问题成为影响垃圾电站行业持续发展的瓶颈。
锅炉四管受热面的腐蚀过程是一个包括腐蚀气体、固体积灰、熔融态液体间的多相耦合复杂腐蚀反应过程,炉膛烟气温度、管道壁温等是主要影响因素。为了对腐蚀规律和机制有一个全面和深入的认识,笔者总结和探讨了壁温和烟温对管壁腐蚀速率的影响与机理,并在此基础上,对于高参数锅炉四管的涂层防护技术进行了综合评价。
垃圾焚烧锅炉高参数化后,金属腐蚀的热力学倾向显著增加,锅炉管道对水汽运行工况的敏感度也相应提高,管内壁腐蚀速率加快。而且,随着主蒸汽压 力的提高,工作介质的饱和度也升高,管道壁温随之 升高,致使管外壁腐蚀速率加快。表1给出了水冷壁和高温过热器在高参数和中参数条件下的介质温度与壁温。可知,中、高参数条件下水冷壁的壁温均在300~400℃,中参数过热器的壁温为450℃ ,高参数下高温过热器壁温均超过500℃。介质温度与最大壁温相差约50℃且数值基本恒定,中参数与高参数条件下水冷壁最大壁温相差19~80℃,中参数与高参数条件下高温过热器壁温相差50~85 ℃ 。综上可见,中、高参数条件下壁温相差很大,这也是造成高参数条件下管壁发生较严重腐蚀的主要原因。
表1 水冷壁和高温过热器在高参数和中参数条件下的介质温度与壁温
管壁温度是影响管壁腐蚀的最直接也是最重要的原因。图1为垃圾炉锅炉四管受热面腐蚀速率随壁温的变化规律。
根据图1所示的管道腐蚀速率随壁温的变化规律,曲线可分为低温电化学腐蚀区、中温弱腐蚀区以及高温强腐蚀区等三个区域。同时,又可根据管壁腐蚀介质的变化将曲线分为气液腐蚀区、气相腐蚀区、飞灰软化腐蚀区、飞灰熔融区、积灰完全包覆区以及腐蚀减弱平缓区等六个区域。此外,还可根据锅炉内设备的工况将曲线分为水冷壁壁温区与过热器壁温区,并在这两个温区内又具体划分出中参数锅炉与高参数锅炉的工作温区。根据腐蚀特征将图1中的曲线划分成上述各区域,得到图2。
图2 圾锅炉管道的腐蚀速率随壁温的变化曲线区域划分
当壁温在20~150℃区间内时,管壁金属的腐蚀类型为电化学腐蚀,虽然居于中、低温区,但在120~150℃区间内管壁的腐蚀速率几乎不低于高温区,这种情况大多发生于垃圾锅炉尾部烟道的管道表面,省煤器就在该温度区间工作。电化学腐蚀的特点是腐蚀材料表面较少出现点蚀坑,腐蚀面积大且厚度比较均匀,管壁减薄最终导致管道破裂,这对尾部烟道管 道的危害性很大。垃圾焚烧过程烟气中不仅HCl含量高而且湿度较大,极易形成酸雾,这导致各种酸的露点温度升高,因此垃圾锅炉中产生高温烟气的酸露点温度高于火电燃煤锅炉。
垃圾焚烧烟气中的氯化物和硫化物等气体和H2O蒸汽产生的酸性化合物,在温度降至其饱和凝结温度时称为酸露点(温度),在该温度之下即低于150℃时,开始发生电化学腐蚀也称电解腐蚀及露点腐蚀。电解腐蚀主要指的是硫酸和盐酸这两种强酸的腐蚀。一般情况下,氯化氢的露点在27~60℃,而硫酸露点在110~150℃,在露点温度以下20~50℃时管壁会发生较严重的腐蚀。如当烟气中含有SO2时,经氧化反应会部分转化为SO3。SO3与烟气中的水蒸气结合生成硫酸蒸气,从而提高烟气的酸露点温度。当烟气温度降至酸露点以下时,硫酸蒸气会冷凝成液态硫酸溶液,并在管壁表面结露。这种酸性液膜与金属管壁接触后,会形成电化学腐蚀环境,导致金属发生阳极溶解。
当壁温在150~300℃时(图2所示的气相腐蚀区),腐蚀速率处于曲线低位。这是因为壁温高于硫酸露点温度时,烟气中的硫酸以气态形式存在,无法在管壁冷凝形成液态电解质,因而无法构成电化学腐蚀所需的电极条件,腐蚀速率显著降低。
壁温>300℃对应于高温腐蚀区,垃圾锅炉四管中的水冷壁、过热器、再热器等管道的工作位于此温度区间内。而300~480℃对应于相对偏弱腐蚀区,此区域内FeCl3、碱式硫酸盐开始逐渐生成。熔融态或液态和固态的碱式氯酸盐和硫酸盐更具有腐蚀性,它们本身熔点较低,混合后形成熔点更低的共晶盐积灰。在积灰和管壁表面的接触界面处产生液相层,使得管壁表面发生较严重的腐蚀。
当壁温为480~700℃时,高温腐蚀反应最剧烈,一方面随着温度的升高,烟气中的氯化氢含量也在不断增高;另一方面在此温度区间内,FeCl3及碱式硫酸盐发生分解和熔融,产生Cl2,以“活化氧化” 机理进行腐蚀。一些试验研究结果指出:当垃圾中的Cl体积分数≥0.35%时,腐蚀速率大幅度提高;当氯化氢体积分数达到0.8%时,金属表面氧化层的完整性被破坏,在其体积分数>2.0%时,氧化层的连续性也被破坏。
垃圾焚烧飞灰中Si、Ca、Al、Na、Cl等元素含量较高,其主要由大量含钠钙长石、钠长石、石英成分的混合熔融盐构成,在加热过程中易随机组合形成各种低熔点共融化合物,飞灰熔融温度低易导致受热面积灰、结渣。
在壁温为320~700℃范围内进一步将曲线划分为4个区域,分别论述其腐蚀机理。
(1) 飞灰软化区:在320~480℃壁温范围内 (图2中所示的飞灰软化区和飞灰熔融区),烟气温度高于飞灰中低熔点共晶化合物的软化温度(通常为300~500℃) 。此时,管壁表面会吸附粘聚性灰渣,其吸附量随温度升高而增加,并逐渐形成半熔融态熔渣。但由于熔渣颗粒需吸收管壁热量才能完全熔化,而烟气流动的剪切力会不断剥离未牢固附着的熔渣,因此该区域腐蚀以气固两相流的冲刷腐蚀为主,腐蚀速率相对较低(图2中曲线平缓段),随着温度接近480℃,熔渣粘附性增强,腐蚀速率呈抛物线上升趋势。
(2) 飞灰熔融区:在 480~600℃壁温范围内(图2中所示的飞灰熔融体积灰包覆区) ,高温下,飞灰中的低熔点盐完全熔融,在积灰-金属界面形成局部液相,构成电化学腐蚀环境,导致基体金属溶解。这种液相腐蚀反应使熔融盐腐蚀进一步加快,且外层的熔融态飞灰的黏附性很强,在管壁形成致密积灰层,厚度随温度升高而增加,阻碍热传导并加剧腐蚀。此外,积灰层因热膨胀系数差异产生热应力,在温度波动下导致管壁应力开裂,进一步加速腐蚀。
(3) 腐蚀稳定期 : 在600~700℃壁温范围内(图2所示的腐蚀减弱至平缓区),腐蚀速率达到峰值后趋于稳定,这是因为管壁金属与积灰中的低熔点盐在高温下发生共晶反应,生成复合化合物,当反应产物在界面层积累至一定厚度时,会阻碍腐蚀介质的进一步扩散,导致腐蚀速率由峰值转为稳定。较厚的积灰层可降低管壁表面实际温度,减缓熔融盐的流动性及反应活性,防止管壁进一步腐蚀,但影响传热。
(4) 腐蚀缓慢期:在700~720℃壁温范围内 (图2所示的腐蚀减弱至平缓区末端),腐蚀反应基本完成,也就是说氯化铁和碱性硫酸铁在320~600℃内生成,而当温度超过700℃时又会重新分解,腐蚀速率迅速下降,当下降到一个平衡点后又重新进入新的低反应稳定期。
除了壁温外,烟温、管内壁氧化皮、温度波动等因素也影响腐蚀速率,其中烟温的影响最显著。对于垃圾电站锅炉烟温对腐蚀的影响,学者们的观点并不统一。首先,有人认为烟温升高会加剧烟气中腐蚀性介质的活性,促进熔融盐形成及气相腐蚀反应。然而,实际检测表明,管壁温度主要由工作介质的温度和压力决定,在稳定工况下基本恒定,烟温波动对其影响有限,因此腐蚀速率的核心驱动因素更可能是壁温而非烟温本身。还有人认为,在垃圾焚烧环境中,烟温对腐蚀过程起到重要作用,关键原因是烟温对腐蚀介质的形成顺序和稳定性起到助力作用。作者认为,烟温主要通过改变腐蚀介质行为间接影响腐蚀,当烟温超过飞灰的熔点后碱金属化合物为熔融态,而呈液态的熔融盐黏附在管壁上形成液相腐蚀,使腐蚀加剧,这是烟温影响腐蚀速率的真正原因。
图3为高温腐蚀与烟温、受热面壁温的关系。 根据受热面管壁腐蚀程度将曲线划分出三个区域,包括低腐蚀风险区、中等腐蚀区和重腐蚀区。
在图3的基础上,结合表1得到关于水冷壁和过热器在不同烟道内的腐蚀工况,如图4所示。
通过分析表1和图4数据可以得出以下结论:在垃圾焚烧锅炉运行过程中,当水冷壁管壁温维持在 309~389℃范围内时,在常规烟温条件下处于弱腐蚀区域,但在高参数工况(13.7MPa/485℃) 下,实际腐蚀情况加剧至中等和严重腐蚀区域,为保证 服役寿命,对管壁必须要采取涂层防护措施。对于 过热器系统,中参数(4MPa/400℃) 工况下壁温450℃处于安全服役温度范围,而高参数(5.3MPa/450℃)工况下壁温达到500℃时即进入中等腐蚀区域,更高参数工况(6.4/13.7MPa) 下壁温超过535℃,腐蚀情况预计更为严重,因此,高参数过热器也必须进行严格的涂层防护。
由此可知,高参数下锅炉水冷壁和过热器的腐蚀工况比中参数下要严重得多。实际上,这种情况早有先例,如我国最早的高参数锅炉即广州李坑垃圾电厂在刚投运时,在无防护的条件下,因水冷壁管泄漏而频繁发生故障停炉的情况,尤其以第一烟道前墙、两侧墙、顶棚、第二烟道两侧墙最为严重,运行6个月左右就需局部切割更换水冷壁管,这严重影响了锅炉的正常运行。
综上所述,处于高温区域的高参数水冷壁和过热器均需重点防护。但对其他区域及中参数下大多数水冷壁与过热器来说,虽然处于低腐蚀区域,但不代表不需要进行表面防护。如要保证所有金属管道均达到设定的服役寿命,也需要进行表面防护,不同的是防护级别有差别。也就是说重点防护采用高性能涂层长效防护,普通防护采用中等性能涂层的高效防护,从而引出防护策略的问题。
在温度影响腐蚀速率的规律和机理的基础上,针对锅炉四管高温腐蚀最严重也是爆管率最高的水冷壁与过热器的防护方法,根据国内高参数锅炉的应用 情况,选择两组较典型的高参数5.3MPa/450 ℃(6.4MPa/450℃)与6.4MPa/485℃(9.7MPa/485℃),与中参数4MPa/400℃水冷壁的防护成本进行比较。以此为典型案例,对于优选防腐蚀材料和防护方法进行探讨。
4. 1 防护原则
一般锅炉运行寿命为28a,管道在锅炉服役期内更换次数在3次以内比较合算。这是因为若水冷壁和过热器的运行寿命低于8a,管道更换将超过3次,经济性偏低;若水冷壁和过热器的运行寿命高于10a,虽然管道更换次数降低,但以目前的防护技术来说,需耗费很高的防护成本。综合衡量,水冷壁和过热器的服役寿命在8~10a,经济性较好。表2为两种中、高参数锅炉水冷壁维修成本对比。由表2可知,中参数锅炉若采用20G钢水冷壁不加涂层的方案,则在28a的运行期内需更换管道5次,年均维修费仅2.68万元;而采用堆焊防护后,虽然服役寿命可延长至10a(运行期内更换管道 2次) ,但年均维修费显著增加至 31.6万元。对比显示,高参数锅炉 的年均维修成本比中参数锅炉高出28.92万元和39.82万元,这说明堆焊防护虽减少更换次数,但综合经济性仍需进一步优化。
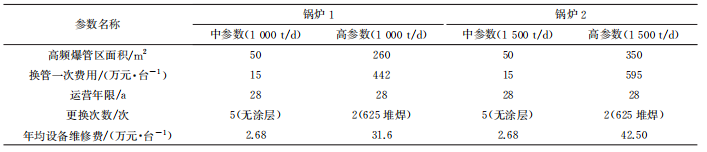
4.2 涂层防护技术
多年来,对垃圾锅炉高温防护来说,真正能够应用于水冷壁和过热器表面防护涂层生产的技术比较有限。如热喷涂技术尽管发源较早,但对于垃圾锅炉管的表面防护,由于结合强度偏低和孔隙率偏高,大多防护效果难尽如人意。相对来说,超音速火焰喷涂(HVOF)涂层的防护效果更好,且已应用到部分企业。但由于该方法粉末沉积率低,造成成本偏高,而其制备的涂层服役寿命又无法与堆焊技术相比,致使其发展空间受限。预先在基体表面涂敷涂层再进行激光熔覆的方法,由于投资大、工艺复杂等问题,一直未能进入规模化生产。此外,近年来各种高温陶瓷涂料技术发展很快,由于其具有现场施工方便和成本低的优势,受到一些中、小型企业的青睐。但采用该技术制备的涂层较薄,一般使用一年多就开始出现斑驳型脱落,需重新涂刷,而非规停炉又使运行成本升高。在国外,高温涂料技术多被作为辅助防护方法。
目前,在垃圾焚烧发电锅炉高温防腐蚀行业使用的主流技术为Inconel625合金堆焊和低温熔焊,采用该技术进行防护的设备服役寿命是目前公认最高的,能达到10a以上,技术也相当成熟,因此应用最为广泛,但存在稀释率和成本偏高、生产效率偏低等缺点。低温熔焊一般指火焰熔焊和感应熔焊,由于火焰熔焊存在成品质量不易控制、运行成本偏高等问题,因此感应熔焊更胜一筹。国内自2017年开发成功的垃圾电站锅炉管道感应熔焊技术,大有后来居上之势。其优势在于:首先,感应熔焊涂层厚度只有约0.5mm,与厚度约2.5mm的堆焊涂层相比薄很多,但由于堆焊技术存在稀释率高的短板,在实际高温服役条件下,采用这两种技术防护的设备服役寿命比较接近;其次,与堆焊涂层相比,感应熔焊涂层的制备成本降低近一半,而生产效率又是堆焊的5倍以上。因此感应熔焊技术一进入市场,很快受到业界特别是众多中、小型企业的青睐,发展前景广阔。
2019年国内在感应熔焊技术的基础上又进一 步开发成功了感应熔焊+超音速等离子喷涂金属陶瓷复合涂层技术(以下简称复合感应熔焊技术),即在水冷壁受热面镍基自熔合金感应重熔后,管排刚从线圈出来仍处于红热状态时,采用超音速等离子 喷涂技术在重熔层表面立即喷涂一层NiCrCr2C3/YSZ/Al2O3+TiO2金属陶瓷面层,由于底层仍处于红热状态,高速喷涂的陶瓷粒子极有可能有一部分进入软底层表面,形成钉扎效应,使面层和底层间的结合强度达到微冶金结合。如前所述,无论是20G钢还是低合金钢,即使在无涂层的保护下使用,正常情况下整体服役寿命也能达到4~5a,加上感应熔焊层的保护,服役寿命可增加3~4a;如果再增加一层金属陶瓷面层,虽然厚度仅约0.2mm,但也足以再增加1~2a服役寿命。总之,采用复合感应熔焊涂层防护的设备服役寿命在中参数下可达到10a,高参数下也超过8a。
(1) 涂层与基体的结合强度
涂层与基体的结合界面是其理化特性发生突变的二维空间,腐蚀气体极易通过孔隙渗入结合界面,使管壁腐蚀减薄;或因热膨胀系数相差较大,疲劳裂纹扩展使涂层剥离失效。因此,需要对高温防腐蚀涂层的结合强度进行严格的评价。堆焊涂层、复合感应熔焊涂层、感应熔焊涂层、HVOF涂层、热固化反应纳米陶瓷涂层与基体的结合强度分别为200~250MPa、0~110MPa、100~150MPa和 50~70MPa、60~80MPa。
(2) 涂层的孔隙率
垃圾锅炉中的高温腐蚀气体会通过孔隙渗透到管壁表面,涂层的隔离效果取决于其孔隙率,而喷涂工艺和材料是影响孔隙率的决定因素。涂层多少都有孔隙,有害的是其中部分贯穿孔隙,我们应尽量降低孔隙率。堆焊涂层的孔隙率<0.5%,复合感应熔焊涂层的孔隙率为0.8%~1.5%,感应熔焊涂层的孔隙率为0.5%~1%,HVOF涂层的孔隙率<1%,热固化反应纳米陶瓷涂层的孔隙率<1%。
(3) 涂层的稀释率
涂层的稀释率决定堆焊层的质量,稀释率越低表明涂层合金成分被基体材料稀释的程度越小。以堆焊工艺为例,在满足使用性能要求的前提下,降低稀释率可实现两大优势:一是减少为达到目标成分所需的堆焊层数,从而节省堆焊材料;二是提高熔敷效率(熔敷速率与稀释率通常呈负相关关系)。能否优化熔敷速率与稀释率之间的平衡,直接决定了堆焊工艺在效率和质量方面的综合表现。堆焊涂层的稀释率为8%~15%,复合感应熔焊与感应熔焊涂层的稀释率<3%,激光熔覆涂层的稀释率为3%~ 7%,HVOF涂层与高温陶瓷涂层的稀释率很小,可忽略不计。
(4) 涂层的防护寿命
堆焊涂层的服役寿命>10a,复合感应熔焊涂层的服役寿命为9~10a,感应熔焊涂层的服役寿命为7~8a,超音速火焰喷涂涂层的服役寿命<5a,热固化反应纳米陶瓷涂层的服役寿命<2a。
(5) 经济性
关于经济性,首先考虑的是涂层的制备成本,5种常用涂层的制备成本从高到低的排序为堆焊、 复合感应熔焊、感应熔焊、超音速火焰喷涂、高温陶瓷涂料。其次,考虑涂层的维护成本。此外,还要结合局部管道更换的难易程度、非计划停机时间等因素综合评判运行费用。高参数锅炉相比中参数锅炉腐蚀加剧,因此在设备运营和维护方面的费用肯定会有所增加。
(6) 生产效率
相对来说,堆焊技术的生产效率最低。这是因为除堆焊速率慢之外,还存在涂层稀释率高的问题,所以必须要堆焊两层以上;感应熔焊技术是在火焰喷涂的基础上,又增加了一道重熔的工序,所以比喷涂技术的生产效率低;复合感应熔焊在感应熔焊基础上又增加一道超音速等离子喷涂的工序。因此,5种常用涂层制备技术的生产效率从低到高的排序为堆焊、复合感应熔焊、感应熔焊、超音速火焰喷涂、高温陶瓷涂料。
表3对比了垃圾锅炉中五种主流高温防护涂层的性能,包括堆焊(Inconel625镍基合金) 、感应熔 焊(镍基自熔合金) 、复合感应熔焊(镍基自熔合金+金属陶瓷) 、HVOF(镍基合金) 和高温陶瓷涂料 (ZST/RSI) 。除常规性能指标(结合强度、孔隙率、 稀释率等)外,实际工程中还需重点关注涂层厚度、 导热系数和制备场地等三个参数。涂层厚度直接影响工艺成本和防护能力,导热系数影响锅炉传热效率,制备场地则与涂层制备工艺的可操作性密切相关。
从工程应用的角度出发,根据应用环境、条件的不同,对防护方案进行选择。较为典型的方案有两种,即高性价比方案和经济型方案。高性价比方案比较注重涂层防护的综合性能,强调防护的性价比,既注重涂层质量,又兼顾经济效益。该方案内容如下:在第一、第二烟道水冷壁及高温过热器等高温腐蚀严重区域,推荐采用Inconel625镍基合金堆焊工艺,其他设备均采用感应熔焊工艺,该方案适用于大、中型企业,其以控制成本为首要目标,在满足基本防护要求的前提下实现经济效益最大化。经济型方案内容如下:在第一、第二烟道水冷壁及高温过热器区域,采用复合感应熔焊工艺,其它设备均采用感应熔焊或高温陶瓷涂料,该方案适用于大多数中、小型企业。
(1) 腐蚀可分为低温电化学腐蚀区、中温弱腐蚀区以及高温强腐蚀区等三个区域。同时又可根据 管壁腐蚀介质的变化规律将曲线划分为处于低温区的气液腐蚀区、气相腐蚀区和处于高温区的飞灰软化腐蚀区、飞灰熔融区、积灰完全包覆区以及腐蚀减弱平缓区。其中处于480~600℃区间的气固液三相区腐蚀最为剧烈。
(2) 对于高温腐蚀与烟温、受热面壁温的关系曲线,根据受热面管壁的腐蚀程度,将其划分出三个区域,即低腐蚀区、重腐蚀区和中等腐蚀区。对于处于高温区域的高参数水冷壁和过热器,需重点防护,对于其它区域及大多数中参数水冷壁与过热器,为保证设定的服役寿命,也需一定的表面防护,其中重点防护采用高性能涂层的长效防护,普通防护采用中等性能涂层的有效防护。
(3) 目前垃圾锅炉应用较普遍的防护方法为堆焊、感应熔焊、复合感应熔焊、超音速火焰喷涂以及高温陶瓷涂料,建立了高温防护涂层的性能评价指标体系,主要包括涂层材料、涂层厚度、导热系数、结合强度、孔隙率、稀释率、防护寿命、成本、生产效率、制备场地等。从工程应用的角度出发,对于防护方案的选择,用户需求不尽相同,较为典型的方案有高性价比方案和经济型方案。
免责声明:本网站所转载的文字、图片与视频资料版权归原创作者所有,如果涉及侵权,请第一时间联系本网删除。