中国兵器工业集团公司成立以来,热处理工艺技术历经了从落后到先进,从以手工操作为主到机械化、半自动化和部分实现自动化的发展过程,工艺参数和产品质量也由不完全可控发展到完全可控,数字化模拟技术的引进也已纳入规划,且指日可待。伴随着行业的发展现状,本公司的热处理工艺技术也发生了翻天覆地的变化,但仍然存在着不足。“十二五”乃至今后更长的期间,本公司热处理工艺技术应不断补充和发展,向国内外先进水平迈进。
1 表面强化技术
1.1表面熔敷技术
表面熔敷技术是利用激光、电磁感应或等离子弧,将自熔合金粉末在工件表面加热到半熔融状态,与工件表面层形成半冶金接合层,从而形成具有抗磨、抗氧化、耐热、耐低应力和耐冲击性好的表面熔敷层。常用的熔敷层有镍基、钴基、铜基及含WC型粉末等,硬度为35~67HRC。在数控机床上熔敷时,可获得厚度均匀的熔敷层,对于非配合尺寸的表面一般无需磨削加工。
1.2激光表面非晶态处理
用激光将金属表面加热到熔融状态后,急速(1×106℃/s)冷却到某一温度以下,使金属成为非晶态结构。非晶态是没有晶粒边界的,结晶时不会出现成分偏析,获得的硬度较高,可达到1000HV以上;同时,耐蚀性和耐磨性也较高。该技术被较多应用在汽车凸轮轴和柴油机铸钢套等的激光表面非晶态处理中。
1.3激光冲击强化技术
激光冲击强化技术也称激光喷丸技术,是由高功率密度(GW/cm2量级)、短脉冲(10~30ns)的激光,通过冲击工件表面的黑漆和铝箔镀层时,形成高压等离子体,并产生高压冲击波,进而在金属表面产生塑变,最终形成残余压应力,使金属表面的抗疲劳性能大幅提高。7075-T6铝合金构件表面经激光冲击后的抗腐蚀疲劳寿命可提高2个数量级,Ti6A14V压气机叶片激光冲击后的强度由206MPa提高到412MPa。
1.4表面机械强化技术
通过在材料或工件表面使用机械滚压和喷丸等手段,使其产生一层残余压应力,常用于轴的表面喷丸和滚压强化、弹簧和齿轮的喷丸强化、螺纹和花键齿的滚压强化、扭力轴的扭转+表面喷丸强化以及奥氏体钢的加工硬化强化。
1.5表面热处理强化数字化技术
随着热处理工艺软件和计算机技术工程化应用的深入,表面热处理强化数字化技术的应用越来越广泛,主要包括电磁感应淬火回火,激光表面淬火回火,电子束表面淬火回火,激光冲击表面强化,渗碳、渗氮和碳氮共渗等表面热处理。该技术不但使热处理工艺参数能通过模拟仿真实现优化,而且也使工艺过程及质量特性实现数字化控制。
2 新工艺技术
2.1低真空变压渗氮技术的应用
通常渗氮都是在炉气和炉压不变的情况下进行的,对于一些细小的盲孔很难渗上氮。采用真空抽气-负压-保压-充气-保压-抽气的变压换气方法,提高了工件表面氮的活性和对氮的吸附能力,使渗层渗速能力加快,再加上稀土催渗剂催渗,渗氮时间将更短。
2.2离子氮化+氧化复合处理新工艺(对软氮化工艺的改进)
该工艺先用离子氮化处理,获得硬化层后,在离子炉内进行1次离子氧化处理,既解决了QPQ处理盐浴氰化物污染环境的问题,又提高了零件的耐磨和耐蚀性。可以尝试用气体氮化+普通化学氧化的工艺方法,提高氮化层的耐磨和耐蚀性。研究表明,绝大多数零件氮化后进行油冷,既不影响变形,又能有效提高氮化层的耐磨和耐蚀性。
2.3液相等离子电解渗碳和渗氮技术
和普通电解技术原理类似,将被渗金属作为阴极,石墨或不锈钢作为阳极,在NaCl电解液中加入含C和N的有机物,如甲醇胺和尿素等,施加的直流电流要足够高,使电解液中正离子在阴极富集,获得具有纳米尺寸的富碳层的晶粒,尺寸为50~70nm,使20#渗碳硬度达到1200HV,H13钢渗氮硬度达到870HV,所需时间仅为25min左右。
2.4等离子体增强电化学表面陶瓷化技术
将Al、Ti、Mg和Zr的有色合金零件接电解液的阳极,并施加较高的电压,就会在零件表面产生微区等离子弧光放电,足以使零件表面形成的氧化膜和界面层的电解质等物质被熔融和烧结,形成1层性能优异且硬度很高的Al2O3陶瓷氧化膜层。纤维硬度达1000~3000HV,相当于硬质合金,其耐磨性、耐蚀性和耐高温性能均比较优良。
2.5回归处理工艺的应用(RRA工艺)
固溶处理的Al-Zn-Mg-Cu系7055-T77铝合金,在时效过程中随着时效温度的升高,GP区和合金相回熔,当达到回归温度的短时内,强度降低,抗蚀性强,可进行快速校正和形变加工;当达到T6的峰值时效时,晶内的GP区密度更高,强度更高。本公司的Al-Mg-Cu系铸铝件的校正也可以采用回归处理的方法进行校正,回归处理已成为进一步提高铝合金热处理强化的推荐技术。
3齿轮热处理变形控制技术
1)齿轮在切削加工过程中存在着内应力,去应力退火虽然能释放应力,使金属组织内歪扭的晶格得到回复;但值得注意的是,回复过程也会引起变形。如渗碳淬火前易变形的齿轮,多次去应力精加工后再淬火,比1次去应力后直接淬火引起的变形小。
2)对于齿轮在淬火过程中的变形,采取的控制措施是保证加热均匀和冷却均匀。加热炉配备有搅拌风扇,加热过程要慢,结构薄厚不均时,应采取厚处先冷或薄处加厚套的措施。冷却过程能采用气淬的方法,就不采用油淬;能采用硝盐淬的方法,就不采用油淬;能采用水基淬火剂淬火的方法,就不采用油冷。
4提高模具寿命的技术
目前,国内外模具热处理技术发展较快的领域是真空热处理、表面强化和材料预硬化技术。真空热处理主要用来解决模具的淬火变形;表面强化是对成型模具进行渗氮、渗硼+淬火、电子束表面淬火、激光表面淬火和表面离子注入(即将模具和要注入的物质C、N、Ti和B等置入真空室,在高压电场的作用下,上述物质被激化成高速离子注入模具表面,形成高度弥散的TiC和TiN等耐磨层)等强化手段;材料预硬化技术是指模具淬火后,再经预先机械滚压和喷丸强化等。
5大型锻件热处理清洁节能技术
5.1加热炉和装炉方式的改进
中国一重大型锻件厂生产的锻件重达十几吨至上百吨,热处理井式炉深>20m,炉温温差均能保证±5℃,大型转子的性能差达到10MPa。为克服厂房高度限制和炉温不均匀,炉子采用开合式井式炉,如图1所示。装炉方式改进如下:
1)炉子侧面开门用折叠式,工件从侧面吊入;
2)工件由吊挂方式改为支承座支承,法兰盘在炉顶上方;
3)吊具不加热,出炉时使用专用冷吊具,吊出炉后淬火,此方法既省去了大型吊具加热,又减小了工件挂头和夹头质量,有效解决了大锻件热处理加热的问题,并且节能效果非常显著。开合式淬火设备如图2所示。
5.2大锻件冷却方式的改变
通常大锻件的冷却介质包括水和油,为解决高合金钢油淬污染和水淬易裂的问题,采用喷雾或喷水淬火,水或雾的喷射速度适时可控,这是大锻件淬火冷速可控的一大特点。
5.3扩氢退火
大锻件退火耗时较长的是扩氢退火,以往非真空方法钢液中的氢含量>2×10-6,临界点以下的扩氢时间一般需要几百至几千小时。真空除气后钢液中的氢含量均控制在1×10-6左右,大部分碳钢大锻件无需扩氢处理,只需普通退火即可解决。
6非晶态材料
高强韧性耐蚀、耐磨、软磁性非晶态合金(俗称金属玻璃)与玻璃的原子结构形态一样,大体上是无序的,为了提高其强度和硬度,以获得高的韧度及软磁性,添加了P、C、B、Zr和Ti等可改善性能的元素,使其相对于金属具有更高的强度、硬度和断裂韧度。当钢液以1×105℃/s急速冷却到凝固点(近于玻璃熔点)时,仍呈现液态。随着温度降低,钢液逐渐凝固,呈现出非晶态结构。可见,只有达到如此高的冷却速度,并且在<-100℃的液氮中,才能得到块状非晶结构。
利用非晶态金属制作原理现已研制出了超高强度纳米非晶态铝合金材料,并在航天航空领域得到了应用,其抗拉强度可达1000~1500MPa,远超出了超硬铝合金材料的强度,与钛合金材料的强度相当,而且回归时间变得更长,从而使构件的成型修复成为可能。
7碳纤维和增强碳基复合材料
碳-碳复合材料是以碳纤维为增强体,碳为基体的复合材料,国内外对其做了大量的应用研究。火炮身管采用以缠绕成型陶瓷为内衬的碳-碳复合材料制成,其质量减轻了30%~50%。在装甲防护上做成轻质复合装甲,破甲厚度可达到700mm,极大地减轻了炮塔的质量。
8结论
采用等离子无氧化热处理的普及程度是衡量一个企业或地区热处理先进程度的主要标准。采用真空、感应、激光、多用炉热处理以及气淬火、压力淬火是减少工件热处理畸变和绿色环保的有效方法。采用数字化热处理技术是发展趋势,能实现对热处理参数和质量的精确控制。利用铸锻件余热等温退火、淬火以及余热的回收利用,进一步减小变形和校正后回火是热处理节能的一个有效途径。高强度或超高强度功能材料的推广应用是实现构件轻量化的重要手段。表面淬火、表面涂层、表面合金化以及表面离子注入、涂镀技术的普及为工件耐磨和耐蚀提供了技术保障。
免责声明:本网站所转载的文字、图片与视频资料版权归原创作者所有,如果涉及侵权,请第一时间联系本网删除。
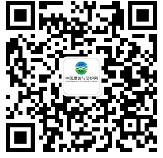
官方微信
《腐蚀与防护网电子期刊》征订启事
- 投稿联系:编辑部
- 电话:010-62316606
- 邮箱:fsfhzy666@163.com
- 腐蚀与防护网官方QQ群:140808414