镁合金是目前实际使用的密度最小的一种金属材料,具有比强度高、导电导热性能好、切削加工性好、生物相容性良好等特点,但由于其化学稳定性差且表面氧化膜疏松多孔,耐腐蚀性能差,导致其应用受到严重限制。
01 腐蚀行为
镁的标准电极电位为-2.37V,其高电负性使镁在不存在氧气的情况下也会发生腐蚀,这致使镁合金在应用时的耐腐蚀性较差。根据PB(Pilling-Bedworth)原理,镁合金表面膜层并非是致密状态,无法对镁合金基体提供长期保护作用。通常使用致密系数来衡量氧化膜的致密程度,该参数是金属与氧结合在其表面生成氧化膜的体积与所消耗金属体积之比。MgO膜的致密系数为0.81,而当致密系数小于1时,氧化膜会因受拉应力而难以铺满金属表面,所以MgO膜对基体不具备一定的保护能力。 镁的标准电极电位低,在电化学腐蚀过程中镁作为阳极失去电子而被腐蚀,阴极产生氢气,在碱性或中性环境以及酸性环境下的阴极反应分别为 阴极可能是与镁合金相接触的其他金属部件,也可能是合金元素或杂质,与镁合金基体形成原电池,从而发生腐蚀;该反应与溶解在水中的氧气含量无关。对于暴露在大气环境中的镁合金,还原反应主要是水的还原反应,反应式为 镁合金腐蚀机理和过程十分复杂,表面杂质、镁合金的合金元素、阳极溶解区域等均会对其腐蚀机理产生影响,因此仍需深入研究电化学反应过程中的各种因素对腐蚀的影响。 02 表面处理技术
由于镁合金化学性质活泼,表面氧化膜无法对镁合金基体起到有效的防护,因此为了使镁合金得到高效的利用并获得更长的使用寿命,需要对其表面进行处理。目前比较成熟的表面处理技术有化学氧化、阳极氧化、微弧氧化和有机涂层等。 化学氧化是镁合金常用的表面处理技术之一,具有成本低、易于处理等优点。化学氧化的基本原理是金属浸入转化液中,与转化液发生一系列化学-电化学反应,将一些难溶(化学性质稳定)化合物沉积在金属表面而形成氧化膜,得到的氧化膜具有很好的耐腐蚀性能,并与基体具有较强的结合力,从而起到保护基体的作用。镁合金化学氧化后形成的氧化膜可以分为含铬氧化膜和不含铬氧化膜,其中不含铬氧化膜包括磷酸盐系氧化膜、氟锆酸盐系氧化膜、锡酸盐系氧化膜、高锰酸盐系氧化膜、稀土氧化膜等。 含铬氧化膜是目前应用比较成熟的化学氧化膜。铬化处理可在镁合金基体表面形成金属基体氧化物和铬酸盐组成的混合氧化物膜,Cr6+的含量越高,氧化膜的自愈合能力越强。铬化处理工艺成熟,但由于铬酸盐中的Cr6+具有毒性,对人体和生态环境有较大的危害,因此含铬氧化膜已经被限制使用,不含铬氧化膜成为了研究热点。 ZAI等研究了转化液pH(2.5,3.0,3.5,4.0)和制备温度(40,60,80℃)对AZ31镁合金表面磷酸镁氧化膜耐腐蚀性能的影响,发现制备温度比转化液pH对氧化膜的耐腐蚀性能影响更大,在制备温度80℃、转化液pH为3.0条件下形成的氧化膜具有最好的耐腐蚀性能。 NIU等在镁合金表面制备了钒酸盐氧化膜,发现在含有4g·L-1NaVO3中形成的钒酸盐氧化膜的微观结构精细、无裂纹。 PHUONG等研究发现,在AZ31镁合金表面制备的磷酸锌氧化膜比磷酸镁氧化膜具有更高的自腐蚀电位和更低的自腐蚀电流密度,但由于磷酸锌氧化膜的孔隙率高,因此在盐雾条件下比磷酸镁氧化膜更易发生腐蚀。 稀土化学氧化可分为单一稀土化学氧化、双稀土复合化学氧化和掺杂稀土盐的其他金属盐化学氧化。稀土氧化膜具有较好的耐腐蚀性能,转化液对环境友好,对人体无害,且稀土化学氧化的工艺简单,因此稀土氧化膜具有良好的发展前景。 镁合金的化学氧化膜较薄(厚度0.5~3 μm),且为多孔结构,导致其耐腐蚀性能仍不是很理想,且耐磨性较差,适用于对环境温度和表面质量精度要求不高的构件,如笔记本、手机及其他电子产品的外壳。化学氧化膜只能减缓腐蚀速率,并不能长期防止腐蚀,因而不可作为长期防腐保护层。 阳极氧化是指在特定的电解液中,利用电流在镁合金表面生成耐腐蚀性较好的沉积膜的过程。镁合金阳极氧化技术优势在于所形成的氧化膜与基体结合强度高,且其耐腐蚀性能较好。 电解液的开发是阳极氧化技术的核心之一,电解液必须满足无毒无污染、环境兼容性好等特点。 章钰等对阳极氧化电解液进行优化,在优化的工艺条件下制备的阳极氧化膜表面平整、致密,与基体的结合力强,主要由镁、氧、硅3种元素组成,对镁合金基体有良好的防护性。 张小玲等配制了一种不含铬、磷、氟的镁合金阳极氧化电解液,通过正交试验优化电解液获得一种既满足环境保护又可有效提高镁合金耐腐蚀性能的阳极氧化膜。 ZHANG等研究发现,单宁酸作为一种有机添加剂,可以促进镁合金表面阳极氧化膜的形成,同时单宁酸可通过形成不溶性镁-单宁酸络合物来改善阳极氧化膜表面微孔均匀性,并增加阳极氧化膜的厚度,从而提高其耐腐蚀性能。 伏田田等研究发现,在碱性电解液中加入腺嘌呤后,AZ31镁合金表面阳极氧化过程的电压更为平稳,电火花放电更均匀,所得到的氧化膜更平整,并且膜中孔洞数量减少,氧化膜致密性提高,耐腐蚀性能增强。 毕烩元等研究发现,在电解液中添加纳米碳化钛后,镁合金表面阳极氧化膜均匀致密,其中的微孔孔径减小,自腐蚀电流密度减小,氧化膜的耐腐蚀性能提高。 付广艳等研究发现,六次甲基四胺的添加降低了电解液的导电性,使得AZ91D镁合金表面的阳极氧化电压升高,反应加快,所得到的氧化膜厚度增加,耐腐蚀性能增强。 阳极氧化膜中含有微孔,这会影响其耐腐蚀性能。阳极氧化膜可以作为中间层来提高有机涂层或其他防护涂层与基体之间的结合力,从而达到长期防护的效果。阳极氧化过程需要消耗大量电能,生产成本高,限制了该方法的广泛应用,因此研究出对环境友好、低能耗和膜性能高的镁合金阳极氧化工艺是十分有必要的。 微弧氧化又称微等离子体氧化,微弧氧化膜具有耐腐蚀、耐磨损、硬度高、介电常数低等优点。在微弧氧化工艺中,阳极为镁合金,阴极为用不锈钢制成的圆柱体容器。在微弧氧化过程中镁合金表面先形成一层薄而致密的氧化层,随后在其上沉积一层含有微孔和微裂纹的多孔层;这种双层结构微弧氧化膜的形成可以提高镁合金的耐腐蚀性能。 曹雅心等研究发现:随着硅酸盐体系电解液中KOH质量浓度由2 g·L-1增加到4 g·L-1,LA103Z镁锂合金表面微弧氧化膜中微孔孔径变大,数量减少,当KOH质量浓度继续增大至6 g·L-1时,微弧氧化膜结构疏松,内部缺陷增多;随着KOH质量浓度的增大,微弧氧化膜在质量分数3.5% NaCl溶液中的耐腐蚀性能先变好后变差;当KOH质量浓度为4 g·L-1时,微弧氧化膜的均匀性最好,孔隙率最低,耐腐蚀性能最好。 利用微弧氧化技术,在镁合金表面制备含耐腐蚀性好的其他物质也是提高微弧氧化膜耐腐蚀性能的一种方法。 TANG等采用微弧氧化方法在AZ31镁合金表面制备了一层厚度为5 μm的含CaTiO3的氧化膜,与镁合金基体相比,所制备的微弧氧化膜具有更高的自腐蚀电位、更低的自腐蚀电流密度,更优异的耐腐蚀性能。 SHI等使用一步法和两步法在WE43镁合金表面制备了含硒微弧氧化膜,硒以Se2-和Se0形式存在于微弧氧化膜中,含硒微弧氧化膜有效提高了WE43镁合金的耐腐蚀性能;与采用一步法制备的微弧氧化膜相比,采用两步法制备的微弧氧化膜中微裂纹较少,厚度较大,耐腐蚀性能更好。 微弧氧化膜与基体结合强度高,相比于阳极氧化膜,其厚度可控,可达几百微米,但表面也存在微孔,会降低其耐腐蚀性能的提高程度,因此需对其进行有效的封孔处理。 常见的封孔处理有后处理封孔和自封孔工艺两类,后处理封孔指在生成微弧氧化膜后进行封孔的技术,自封孔工艺指在微弧氧化膜形成的过程中同步进行封孔的技术。其中,自封孔微弧氧化膜具有结合力强、封孔效果好、耐腐蚀性能好等优点,主要通过电解液自封孔、外加电场自封孔两种方法获得。 微弧氧化工艺拓展了镁合金的应用领域,使镁合金的耐腐蚀性能、耐磨性均得到显著的提高,具有良好的应用前景。 可用氟碳涂料、聚氨酯涂料、醇酸树脂涂料以及环氧类涂料等有机涂层对镁合金表面进行防护。有机涂层的保护机理主要是隔绝、屏蔽和电化学保护。有机涂层品类繁多,经济实惠,适应性广泛,施工简单。选用合适的有机涂料,经过适当的预处理涂覆在镁合金表面,可以有效提高镁合金的耐腐蚀性能。但是有机涂层与基体的结合力不好,在严苛环境下可能会出现脱落问题,使镁合金基体暴露在腐蚀介质中。 李浩等研究发现,与镁合金表面直接涂覆的茶多酚层相比,阳极氧化/茶多酚复合涂层的耐腐蚀性能较好,且阳极氧化后表面与茶多酚涂层的结合力更好。作者所在课题组研究发现:在臭氧体积分数为0.0016%的臭氧老化试验箱中放置30天后,涂覆氟碳涂料的镁合金表面无明显变化,具有良好的抗氧化性,这与氟碳涂料中C-F键键能大且分子链中不含不饱和键有关;在中性盐雾环境中放置15天后,涂覆氟碳涂料的镁合金表面无点蚀或其他腐蚀现象出现,具有良好的耐盐雾腐蚀性能。 有机涂层种类繁多,适应性强且操作简单,在提高镁合金表面耐腐蚀性能方面具有很大的优势,但因有机涂层比微弧氧化膜、阳极氧化膜厚,不适用于小构件。为了克服有机涂层与镁合金结合力弱的问题,可以采用底漆加面漆的解决方法。 表面镀镍技术难以在不规则试样表面形成均匀镀层,而且存在着严重的废水处理问题;气相沉积方法可以制备出硬度高、耐腐蚀性能良好和孔隙率低的MgO层,但对制备温度要求较高,工艺复杂;激光表面改性处理技术要求较高,在不规则试样表面难以形成均匀涂层,难以投入使用。 WATAZU等采用射频磁控溅射工艺和平面磁控溅射系统在低铝单相镁合金表面沉积了致密的MgO薄膜,在一定程度上提高了镁合金的力学性能,但是在潮湿的大气环境中镁合金的耐腐蚀性能较差。作者所在课题组使用电镀的方法在ME20M镁合金表面镀镍后,试样表面存在一些微小突起,经过5天盐雾腐蚀试验后,突起部分发生腐蚀并有向外扩散的趋势,试样其他部位无腐蚀现象出现。 03 结束语
近年来,镁合金由于其独特的性能优势而受到国内外研究人员的关注,特别是在绿色经济的背景下,镁合金的受重视程度日益上升。 在无水干燥的天气环境中,镁与氧发生反应生成MgO,而在潮湿大气环境中,镁合金表面腐蚀产物主要为Mg(OH)2和MgO,且环境pH对其腐蚀速率有很大影响;但是多种环境下的腐蚀机理研究较少。阳极氧化、微弧氧化表面处理技术尽管在一定程度上可以增强镁合金的耐腐蚀性能,但阳极氧化膜、微弧氧化膜中有许多微孔隙,目前自封孔技术中所使用的电解液多为含氟电解液,对环境不友好。针对上述问题,未来的研究应主要集中在: (1) 工艺流程以及工艺参数对各种表面处理技术影响方面; (2) 基础研究方面,探索镁合金在含有CO2、SO2、O3等大气环境中的腐蚀机理及腐蚀过程; (3) 环保型自封孔电解液的研究; (4) 稀土氧化膜、磷酸盐系氧化膜等不含铬氧化膜等方面的研究,拓宽镁合金在更多场景下的应用。
免责声明:本网站所转载的文字、图片与视频资料版权归原创作者所有,如果涉及侵权,请第一时间联系本网删除。
-
标签: 镁合金
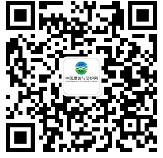
官方微信
《腐蚀与防护网电子期刊》征订启事
- 投稿联系:编辑部
- 电话:010-62316606-806
- 邮箱:fsfhzy666@163.com
- 腐蚀与防护网官方QQ群:140808414