取向硅钢是一种通过形变和再结晶退火生产且晶粒择优取向的硅铁合金,通常作为变压器铁芯材料在电力行业广泛应用。随着能源行业快速发展及电力工业节能降耗的迫切需求,不断改善硅钢性能,降低其铁芯损耗(铁损),成为硅钢制造行业的竞争焦点与备受关注的研究课题。目前降低铁损的主要方法是磁畴细化技术,即通过减小取向硅钢磁畴宽度来降低反常涡流损耗(铁损的重要组成)的一类物理方法,包括机械刻痕法、激光刻痕法、等离子束照射法和局部加热法等。当前各大制造厂商主要采用激光刻痕法来降低铁损。 激光刻痕法是用激光束照射有绝缘涂层的取向硅钢表面,使其高温熔解、挥发,冷却后无规则凝聚,形成一定间距的线状或点状刻痕。在激光刻痕瞬间,涂层因高温过热会发生以沸腾和喷溅为形式的相爆炸而形成重熔物、飞溅物乃至孔洞等,刻痕区域涂层厚度均匀性和平整性遭到一定程度破坏,基材出现裸露,这增大了取向硅钢锈蚀的风险。目前,对于取向硅钢的研究主要是针对生产工艺优化和表面涂层性能改良,对于刻痕板的研究也只是对刻痕工艺,关于取向硅钢表面刻痕后的涂层变化和耐蚀性还缺乏系统的研究。随着电子、电气行业的持续发展,取向硅钢产能逐年增加,各大钢厂对取向硅钢刻痕板表面耐蚀性越来越重视,希望建立统一的试验室评价方法和完善的评价体系,优化取向硅钢表面激光刻痕工艺。 本工作以国内某大型钢厂生产的激光刻痕高磁感系列取向硅钢板为研究对象,通过表面微观形貌观察和化学成分检测,对比刻痕区域和非刻痕区域形貌、成分差异,分析激光刻痕技术对取向硅钢表面涂层的厚度、均匀性、平整性及耐蚀性的影响;通过硫酸铜点滴试验,分析激光刻痕取向硅钢板基体裸露情况;通过交变湿热试验和动态接触湿热试验对试片进行加速腐蚀,根据试片表面锈蚀程度分析激光刻痕对取向硅钢耐蚀性能的影响。 试验材料 试验材料为国内某大型钢厂生产的单面激光刻痕高磁感型取向硅钢板,刻痕状态为条状,沿钢板轧制方向延长,横向间距5 mm;试验钢板分为3个生产批次(分别标记为A1,A2,A3);每批次钢板数量为3~5张(A4纸大小,分别标记-1,-2,-3,-4,-5),从卷板不同的位置取样。 试验前用无水乙醇对钢板表面进行清洗,去除表面杂质、灰尘,干燥密封后保存。通过Phenom ProX型扫描电子显微镜观察钢板表面的微观形貌、测量刻痕尺寸,观察重熔物和孔洞分布,生成钢板3D图,观察钢板截面形貌;利用附带能谱仪对钢板表面元素进行分析。 激光刻痕形貌 图1 取向硅钢板激光刻痕区域的形貌 由图1可见,刻痕沿钢板轧制方向延长,刻痕长度为646 μm,宽度为98.3 μm;刻痕区域凸凹不平,凸起和凹坑分布无明显规律,统计结果显示凹坑占比大于85%,最大凹坑直径为19.8 μm。这是由于激光照射取向硅钢板表面使涂层高温熔解、挥发、冷却后无规则凝聚,形成大量的重熔物和孔洞,从而破坏了取向硅钢板表面涂层厚度的均匀性和平整性。 刻痕区域重熔物、孔洞分布 刻痕区域出现白点,且刻痕区域白点明显多于非刻痕区域,这说明钢板表面涂层已出现重熔物和孔洞,激光刻痕已经对涂层平整性造成破坏。刻痕区域重熔物和孔洞的比例反映了钢板表面涂层被破坏的程度。对重熔物和孔洞进行统计,结果如图2所示。 图2 不同试样激光刻痕区域重熔物和孔洞的比例 由图2可见,不同生产批次钢板表面涂层被破坏区域比例最大相差30%,而同一生产批次钢板表面涂层被破坏区域比例最大相差40%,这说明激光刻痕技术工艺稳定性不佳,导致质量一致性存在一定差异。 涂层厚度和孔洞深度 采用扫描电镜观察钢板的3D形貌以及截面微观形貌,结果如图3和图4所示,并测量了刻痕区域孔洞深度及涂层厚度,结果表明,刻痕区域孔洞最大深度为6.10 μm,涂层最大厚度为5.48 μm,取向硅钢板刻痕区域孔洞处有可能出现基材裸露的情况。 (a) 表面 (b) 侧面 图3 试样A3-3的3D图 图4 试样A3-3截面的微观形貌 铁含量 对取向硅钢板表面不同区域的铁元素含量进行分析,非刻痕区域未检测出铁,说明非刻痕区域涂层表面质量良好,基材未出现裸露情况;对比刻痕区域孔洞处和平整处,孔洞处铁质量分数为78.62%,是平整处(0.69%)的113倍,说明刻痕区域孔洞处基材已经裸露;刻痕区域面扫结果显示,该区域铁质量分数为1.95%,进一步证明取向硅钢板刻痕区域已经出现基材裸露的情况。 耐腐蚀性能试验 硫酸铜点滴试验参考GB/T 15519-2002《化学转化膜 钢铁黑色氧化膜 规范和试验方法》,将处理后的试片(75 mm×50 mm)浸泡在25℃、0.1%硫酸铜溶液中10秒,然后匀速提出,用脱脂棉蘸取无水乙醇擦去试片表面残留的硫酸铜溶液,通过试片表面变色情况分析激光刻痕后取向硅钢板刻痕区域和非刻痕区域耐蚀性差异,结果见表1,试样表面的宏观形貌如图5所示。结果表明:未刻痕区域无锈蚀,刻痕区域出现点状和条状红褐色锈蚀,且平均锈蚀比例高达67%,说明刻痕区域基材出现大面积裸露情况,取向硅钢板耐蚀性下降;不同生产批次钢板锈蚀程度存在明显差异,锈蚀比例相差55%;同一批次钢板不同位置的锈蚀比例也相差30%,这进一步说明激光刻痕技术工艺稳定性和质量一致性较差。 表1 各试样硫酸铜点滴试验结果 图5 硫酸铵铜点滴试验后试样A1-3,A2-2,A3-3表面宏观形貌 试验室加速腐蚀试验包括交变湿热试验和动态接触湿热试验。 交变湿热试验参考GB/T 2423.4-2016《电工电子产品环境试验 第2部分:试验方法 试验Db:交变湿热(12 h+12 h循环)》标准,试验温度为25~55℃,相对湿度>90%,试验周期为120小时。 动态接触湿热试验参考QB/T 1319-2010《气相防锈纸》标准,试验温度为(49±1)℃,相对湿度≥95%,试验周期为24小时。 试验室加速腐蚀试验后,对各试样刻痕区域和非刻痕区域的腐蚀情况进行统计,结果见表2。分析试验结果可知,在高温高湿环境中,未刻痕区域耐蚀性明显好于刻痕区域,这说明激光刻痕工艺明显降低了取向硅钢表面耐蚀性能;3个生产批次钢板的平均锈蚀比例分别为4.0%,100.0%,97.5%,最大相差25倍,这也说明取向硅钢激光刻痕工艺稳定性和质量一致性较差。 表2 裸片耐蚀性试验结果
免责声明:本网站所转载的文字、图片与视频资料版权归原创作者所有,如果涉及侵权,请第一时间联系本网删除。
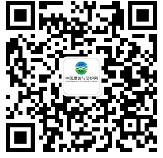
官方微信
《腐蚀与防护网电子期刊》征订启事
- 投稿联系:编辑部
- 电话:010-62316606-806
- 邮箱:fsfhzy666@163.com
- 腐蚀与防护网官方QQ群:140808414