陶瓷颗粒,如SiC颗粒[7]、TiC颗粒[8]、TiB2颗粒[9]等,其强度和刚度高且价格较低,是目前最常用的增强相。Habibnejad[10]等用熔铸法将Al2O3颗粒加入AZ31基体制备复合材料,其抗拉强度和屈服强度分别达到306 MPa和290 MPa。Deng[11,12]等用SiC颗粒和AZ91镁合金制备的复合材料,其晶粒尺寸显著减小,力学性能明显提高。但是,陶瓷颗粒的尺寸较大、与镁基体的界面润湿性也较差,使制备出的复合材料塑性大大降低,限制了它的应用。石墨烯的力学性能优异、增强效率高且与镁基体的化学相容性良好,是最理想的增强体[13]。Yuan[14,15]等用热还原法制备石墨烯增强的镁基复合材料,用原位生成的MgO颗粒调控界面,制备出的复合材料屈服强度和延伸率分别提高了76.2%和24.3%。Wang[16]等用原位反应制备了石墨烯增强镁基复合材料,发现改善石墨烯与镁的界面润湿性可使其力学性能显著提高,其抗拉强度和屈服强度分别达到316 MPa和221 MPa。
目前,制备石墨烯增强镁基复合材料的常用方法有粉末冶金法、搅拌铸造法和机械合成法。这些方法都有一定的不足之处:添加石墨烯容易产生烧损和出现团聚[17]。原位生成法,是通过化学反应直接合成石墨烯增强镁基复合材料。与传统的制备工艺相比,原位生成法能减少石墨烯的烧损,避免石墨烯在镁基体中的分布不均和团聚。鉴于此,本文用原位合成法使葡萄糖与镁发生化学反应制备石墨烯增强的镁基复合材料,研究制备工艺对生成的石墨烯的质量和复合材料性能的影响。
1 实验方法
1.1 实验用材料
实验用基体为AZ31镁合金,其化学成分列于表1,制备增强体使用的葡萄糖粉末其纯度为99.99%。
表1 AZ31镁合金的化学成分
Table 1
Al | Zn | Mn | Si | Cu | Fe | Mg |
---|---|---|---|---|---|---|
2.80 | 1.00 | 0.25 | 0.06 | 0.01 | 0.01 | Bal. |
1.2 复合材料的制备
将AZ31镁锭机加工成碎屑,放入酒精溶液中超声清洗以去除表面的油污;将葡萄糖浓度为4%的葡萄糖粉末与去离子水混合,然后与镁屑料一起放入200℃的高压反应釜中进行水热反应,反应时间为12 h。将得到的反应混合物放入300℃的烘箱中烘干,然后将其装入冷压模具中。在室温和压力为650 MPa条件下保压30 s,制成半径为20 mm、高30 mm的圆柱型坯料。将坯料装入真空热压烧结炉中,分别在700℃、750℃、780℃烧结进行原位自生反应。将原位自生反应后的坯料装入热挤压模具中,在420℃保温15 min。然后在压力为620 MPa、挤压比25∶1、挤压速度为3 mm/s条件下制备出石墨烯增强镁基复合材料。实验流程如图1所示。
图1
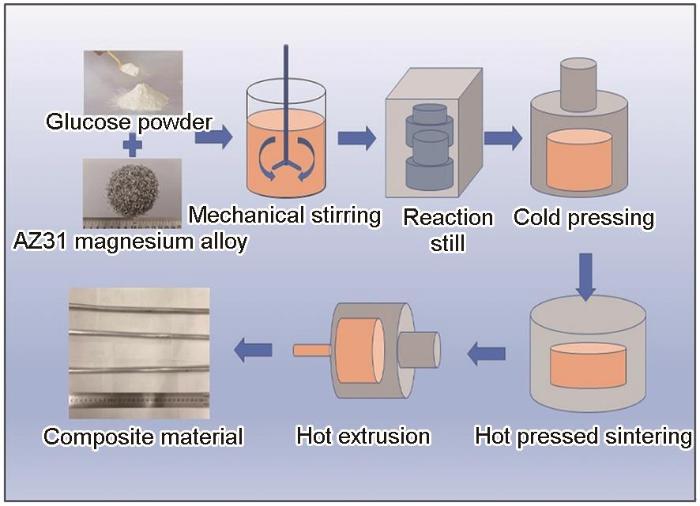
图1 原位反应制备石墨烯/镁复合材料的流程
Fig.1 Flow chart of in-situ reaction graphene/magnesium composite preparation
1.3 性能表征
为了验证原位生成的反应产物是否含有石墨烯材料,将制备出的复合材料放入浓度为40%的硫酸溶液中腐蚀,然后将反应完全后的溶液抽滤,将抽滤后的产物冷冻干燥,将得到的黑色物质用于Raman分析。
用Raman光谱、XPS测试仪、FEI-SIRION扫描电镜、原子力显微镜和型号为TECNAI-F30的透射电镜等仪器表征反应产物的微观组织。用电子万能拉伸试验机测试复合材料的力学性能,每组数据测试3个试样取结果的平均值。
2 实验结果和分析
2.1 石墨烯的微观形貌
图2给出了在不同反应温度下原位自生的石墨烯的Raman分析。在图2a、b和c中都出现了石墨烯的三个特征峰,位于1345 cm-1、1580 cm-1和2680 cm-1,分别对应石墨烯的D峰、G峰和2D峰。结果表明,所得反应产物为石墨烯。G峰为石墨烯的主要特征峰,是sp2杂化的碳原子面内振动引起的,此峰反应石墨烯的层数;D峰为石墨烯的无序振动峰,表征石墨烯所含缺陷的多少;2D峰可表征石墨烯内部碳原子的堆垛方式,通常用ID/IG表征石墨烯的缺陷含量,用I2D/IG表征石墨烯的层数[18]。
图2
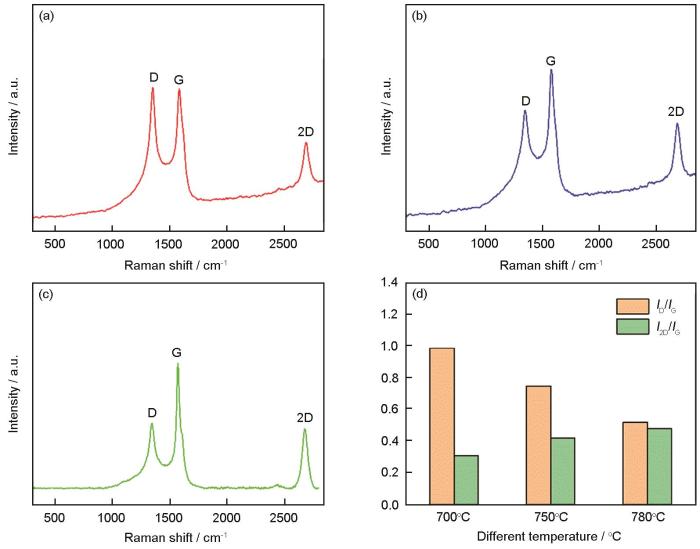
图2 在不同反应温度下原位自生的石墨烯的拉曼光谱和ID/IG和I2D/IG比值
Fig.2 Raman analysis of the in-situ generated graphene at700℃ (a), 750℃ (b), 780℃ (c) and ratio of ID/IG and I2D/IG (d)
从图2a、b和c还可见,随着反应温度的提高原位自生的石墨烯的D峰的强度降低,2D峰的强度提高。这表明,原位生成的石墨烯中缺陷逐渐减少,石墨烯的层厚减小、质量提高。ID/IG和I2D/IG比值的计算结果,如图2d所示。可以看出,随着反应温度的提高ID/IG的值降低,I2D/IG的比值提高。这表明,随着反应温度的提高得到的石墨烯的质量不断提高。其原因是,随着反应温度的提高葡萄糖分解产生的CO2变得活跃,与Mg基体的反应更加充分,使石墨烯的质量提高。碱土金属镁的还原性较高,能与CO2发生氧化还原反应释放大量的热,促使还原的碳在高能量下转变成石墨烯。同时,由于C与金属的润湿性较差,反应生成的C晶体优先相连形成片状结构,最终得到石墨烯薄片。
Raman谱的分析结果表明,反应温度越高得到的石墨烯的质量越高。对在780℃原位生成的石墨烯进行XRD分析,结果如图3所示。可以看出,与标准PDF卡片对比发现,位于2θ=26.3°、44.3°和50.4°的明显特征峰分别对应石墨烯的(002)、(101)和(102)晶面。XRD分析结果进一步证明,高温热压烧结后葡萄糖粉末与镁基体通过原位反应生成了石墨烯。
图3
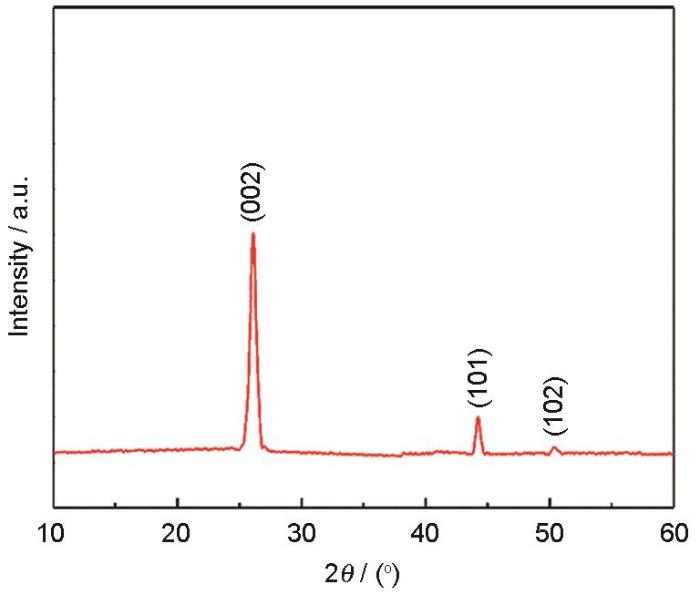
图3 在780℃原位自生的石墨烯的XRD谱
Fig.3 XRD analysis of the in-situ generated graphene at 780℃
对在780℃原位生成的石墨烯进行XPS分析,结果如图4所示。由图4a可见,在780℃热压烧结反应生成的石墨烯氧含量较低,总的碳氧比:为92:5。对原位生成的石墨烯的碳峰进行分峰拟合,发现石墨烯的碳主要以sp2杂化的碳原子为主,且包含了C-O和C-O=C两种官能团,如图4b所示。XPS分析结果表明,原位反应生成的石墨烯氧含量较低,缺陷较少,表明石墨烯的质量较高。
图4
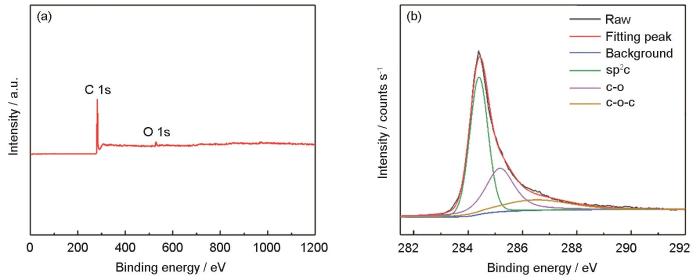
图4 在780℃原位自生石墨烯的XPS分析
Fig.4 XPS analysis of in-situ graphene at 780℃ (a) Carbon-oxygen ratio of in-situ generated graphene; (b) Fitting of carbon peaks of in-situ graphene
图5给出了在780℃原位生成的石墨烯的SEM微观形貌以及在镁基体中的分布。如图5a所示,石墨烯的形状较为完好,没有明显的空洞和缺陷。进一步观察发现,原位生成的石墨烯呈现片状,其尺寸为3~5 μm,如图5b和c所示。观察图5d可见,原位反应生成的石墨烯在镁基体中分散均匀,没有出现明显的团聚。这表明,用原位反应方法合成石墨烯增强的镁基复合材料,能避免增强相在基体中的团聚,且石墨烯呈片状分布,没有明显的缺陷,进一步证明该方法的有效性。
图5
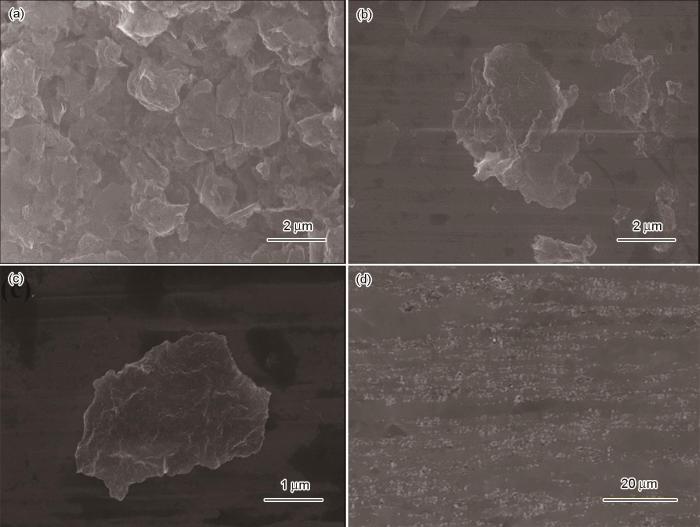
图5 在780℃原位自生石墨烯的SEM形貌和在镁基体中的分布
Fig.5 SEM morphology of in-situ graphene at 780℃ and its distribution in magnesium matrix (a) Micro morphology of in-situ generated graphene; (b) and (c) are enlargements of figure (a); (d) Distribution of in-situ graphene in magnesium matrix
图6给出了在780℃原位生成的石墨烯的TEM微观形貌。如图6a和b所示,石墨烯的形貌完好,没有明显的空洞或缺陷。薄片状石墨烯的曲卷程度较低,质量较高。HRTEM观察发现,石墨烯的层厚为5~15层,厚度约为3~5 nm,如图6c所示。TEM观察发现,石墨烯的质量较高,形貌较为完好;完整的石墨烯形貌在基体中有增强效果,阻碍位错运动和抑制晶粒的长大。如图6d所示,石墨烯与镁基体的界面结合良好,没有明显的微裂纹和微孔。良好的界面结合,有利于复合材料性能的提高。
图6
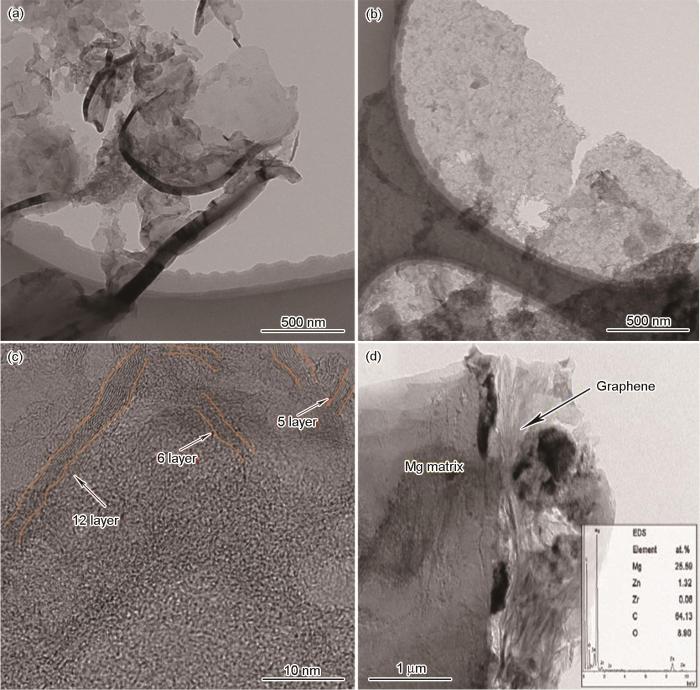
图6 在780℃原位自生石墨烯的TEM形貌
Fig.6 TEM morphology of in-situ graphene at 780℃ (a) and (b) Micro morphology of in-situ generated graphene; (c) HRTEM of in-situ generated graphene; (d) The interface between graphene and magnesium matrix
2.2 石墨烯增强镁基复合材料的力学性能
图7给出了在不同温度原位自生石墨烯增强镁基复合材料的力学性能,其中反应温度为25℃表示纯AZ31镁合金基体。如图7所示,随着原位反应温度的提高镁基复合材料的力学性能随之提高。反应温度为700℃时复合材料的屈服强度、抗拉强度和延伸率分别达到190 MPa、305 MPa和5.3%;反应温度提高到780℃复合材料的屈服强度、抗拉强度和延伸率达到最大值,分别为245 MPa、340 MPa和6.7%,比以纯AZ31基体的力学性能分别提高了40%、21.4%和48.8%。其原因是,对于用原位反应制备的复合材料,石墨烯与镁基体的热膨胀系数很大的差别,导致在热挤压过程中界面结合处出现较大的热应变区。该区域较大的热错配残余应力,使该处产生密度较高的位错。这些位错促进动态再结晶,从而使复合材料的晶粒细化,使其性能提高[19];另一方面,在复合材料的晶粒长大过程中,石墨烯在镁基体中的均匀分布有效阻碍了晶粒生长,从而产生细晶强化[20],同时,在材料加载过程中,力学性能优异的二维石墨烯能分担较多的载荷,使复合材料的综合性能提高。
图7
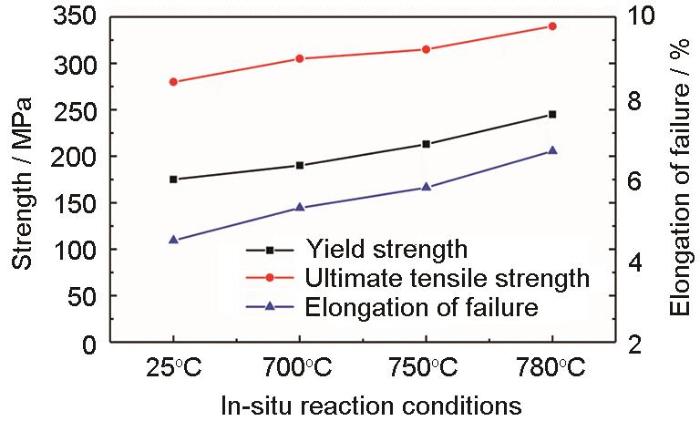
图7 原位自生石墨烯增强镁基复合材料的力学性能
Fig.7 In-situ in-situ graphene reinforced mechanical properties of magnesium matrix composites
图8给出了在780℃原位自生石墨烯增强镁基复合材料的拉伸断口形貌。如图8a所示,在拉伸断口没有明显的微裂纹和微孔存在,表明石墨烯与镁基体界面结合良好,没有出现断裂。对图8a放大后可见,断口处有大量的韧窝,表明复合材料的断裂方式以韧性断裂为主。观察发现,在断口表面有石墨烯碎片,因为石墨烯与镁基体的润湿性不好,复合材料承受较大的拉伸应力时,在石墨烯与镁的界面结合处萌生裂纹。随着应力的加大微裂纹扩展,最终使复合材料断裂。
图8
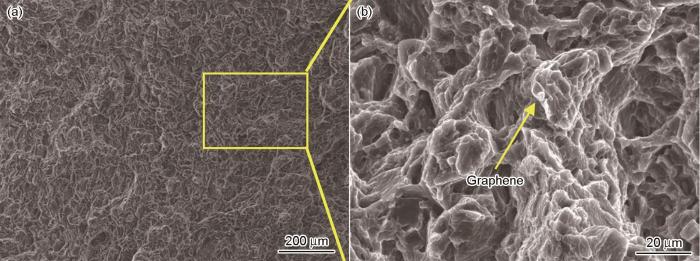
图8 在780℃原位自生石墨烯增强镁基复合材料的断口形貌
Fig.8 Fracture morphology of in-situ graphene reinforced magnesium matrix composite at 780℃ (a) Tensile fracture morphology; (b) is an enlargement of (a)
3 结论
(1) 使葡萄糖粉末与镁发生化学反应和在不同温度进行热压烧结,可制备原位自生石墨烯增强镁基复合材料,原位自生的石墨烯在镁基体中分布均匀。
(2) 改变反应温度,可使原位自生的石墨烯的质量不断提高。反应温度为780℃生成的片状石墨烯缺陷较少、质量最高,其厚度为3~5 nm,尺寸约为4 μm。
(3) 石墨烯增强镁基复合材料的力学性能随着反应温度的提高而提高,反应温度为780℃制备的复合材料其性能最佳,屈服强度、抗拉强度和延伸率分别为245 MPa、340 MPa和6.7%,比AZ31基体的力学性能分别提高了40%、21.4%和48.8%。
免责声明:本网站所转载的文字、图片与视频资料版权归原创作者所有,如果涉及侵权,请第一时间联系本网删除。
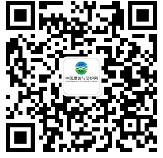
官方微信
《腐蚀与防护网电子期刊》征订启事
- 投稿联系:编辑部
- 电话:010-62316606-806
- 邮箱:fsfhzy666@163.com
- 腐蚀与防护网官方QQ群:140808414