7xxx系铝合金(Al-Zn-Mg-Cu系)因其比强度高、成形性好等优点,作为结构材料广泛应用于航空航天及车辆工程领域[1,2]。但是,该系合金容易发生应力腐蚀开裂(SCC),不仅降低了其服役寿命,也限制了其应用。为了降低该系合金的SCC敏感性,人们进行了大量的研究,发现元素含量和比例[3,4]、再结晶程度[5,6]、热处理制度[7,8]等都对SCC敏感性有重要影响。7xxx系铝合金是可热处理强化合金,淬火是决定其最终性能的一个关键工序。淬火速率对该系合金SCC敏感性影响很大。
Yuan等[9]通过评价裂纹扩展速率发现7xxx系铝合金的SCC敏感性在淬火速率8~150℃/s区间内随着淬火速率的减小而降低。Xie等[7]采用分级淬火的方法发现淬火速率越小,7097铝合金的SCC敏感性越低,认为随着淬火速率减小,晶界附近的无沉淀析出带(PFZ)增宽,晶界析出相(GBP)中Cu含量的增加,均会降低裂纹扩展速率。Jiang等[10]对比了7046铝合金在空气淬火(1.4℃/s)与水淬火(80℃/s)条件下的SCC敏感因子,发现随淬火速率减小SCC敏感性增高,认为这是随淬火速率减小晶界PFZ增宽后更容易被溶解造成的。Chen等[11]通过对比伸长率的损失发现7085铝合金的SCC敏感性在淬火速率1~150℃/s区间内随淬火速率减小先降低再升高,认为淬火速率大于50℃/s时,GBP的尺寸和间距增大降低了SCC敏感性;而淬火速率小于50℃/s后,GBP中Cu含量的降低提高了SCC敏感性。Xiao等[12]通过评价强度的损失发现过时效态7xxx铝合金的SCC敏感性在淬火速率5~130℃/s区间内随淬火速率减小先降低再升高,而峰时效态合金的SCC敏感性随淬火速率的减小而降低,认为GBP的面积分数起了决定性作用,GBP面积分数小于22.3%时SCC敏感性随淬火速率减小而降低,高于22.3%后则随淬火速率减小而升高。
SCC对材料强度、伸长率、服役寿命等都有影响,通过单一的性能损失难以反映SCC对材料整体性能的影响。上述研究均采用不同介质进行淬火,只能获得离散变化的淬火速率。而实际工业生产的淬火过程中,厚截面材料表层到心部的淬火速率是连续减小的。淬火速率不仅改变GBP的化学成分、尺寸、相间距、数量,还会改变PFZ的宽度[9,13],进而对SCC敏感性造成有利或不利的影响。通过微观组织的单一特征变化不能全面地解释淬火速率对SCC敏感性的影响机理。
本工作以7136铝合金为对象,通过浸入式末端淬火的方法获得大范围连续变化的淬火速率,结合慢应变速率拉伸(SSRT)实验中获得的强度、伸长率和断裂时间等数据综合研究淬火速率对该合金SCC敏感性的影响规律,并探讨微观组织特征对SCC的影响机理。这可以深化人们对7xxx系铝合金SCC敏感性的理解,为调控材料性能提供参考。
1 实验方法
实验材料为16 mm厚的7136铝合金挤压板材,实测化学成分(质量分数,%)为Al-9.10Zn-2.18Mg-2.07Cu-0.13Zr,Fe < 0.08,Si < 0.05。为准确表述实验过程及试样位置,建立三维坐标系,定义板材的挤压方向(ED)为x轴,横向(TD)为y轴,法向(ND)为z轴。从板材上沿ED切取长度和宽度分别为360和170 mm的试样置于SX-4-10型箱式电阻炉中进行双级固溶,制度为450℃、1 h + 470℃、0.5 h。固溶后在2 s内将试样转移至室温(约25℃)水槽中进行浸入式末端淬火,TD垂直于水面,试样浸入水中深度为25 mm,其余部分位于空气中。图1为浸入式末端淬火示意图,图中蓝色表示水中的部分,灰色表示空气中的部分。在试样TD-ND面z = 8 mm处沿y轴的不同位置钻出8个直径为1.5 mm、深度为10 mm的小孔预埋热电偶。使用QT-6-K高精度测温仪采集末端淬火过程中的时间-温度曲线,数据采集频率为20 Hz。待试样完全冷却至室温后,立即在SX2-9-12TP箱式电阻炉中进行120℃、24 h的人工时效。
图1 末端淬火示意图及慢应变速率拉伸试样尺寸
按照HB 7235-95标准在YYF-100型慢应变速率应力腐蚀试验机上执行SSRT实验。在板材ND-ED面沿y轴连续切取厚度为3 mm的试样,具体尺寸见图1。取试样中心位置所对应的y轴淬火速率作为名义淬火速率。每组平行样为3个,应变速率为1 × 10-6 s-1,腐蚀介质为3.5%NaCl (质量分数)溶液,惰性介质为硅油。通过试验机自带的加热装置将介质温度控制在(50 ± 2)℃。实验结束后,分析不同试样的应力-应变曲线、断裂时间等数据。
使用EVO MA10扫描电子显微镜(SEM,加速电压20 kV)观察试样的断口形貌,再在断口处取样,观察和分析断裂位置附近(ED-TD面)的腐蚀裂纹特征,并统计腐蚀裂纹数量,测量最大腐蚀深度。在板材不同位置切取试样观察第二相特征,并使用X-MaxN能谱分析仪(EDS)对第二相粒子进行成分分析。电子背散射衍射(EBSD)分析在配有EBSD探头的EVO MA10 SEM上进行。试样经过机械抛光后进行电解抛光,电解电压为15 V,时间约为10 s,抛光液为10%HClO4 + 90%C2H5OH (体积分数)的混合溶液。使用HKL Channel 5软件处理EBSD数据。使用Titan G2 60-300扫描透射电子显微镜(STEM)在高角环形暗场像(HAADF)模式下观察微观组织特征,重点观察晶界(GB)和亚晶界(SGB)上析出相等特征,使用Super-X型EDS检测GBP的化学成分,束斑尺寸为2 nm,加速电压300 kV。STEM样品预磨至80 μm厚后,使用冲孔器冲成直径为3 mm的圆片后进行双喷减薄,双喷液为20%HNO3 + 80%CH3OH (体积分数),使用液氮将温度控制在-20℃以下。
2 实验结果
2.1 时间-温度曲线与淬火速率
图2a为7136铝合金试样不同位置的时间-温度曲线。可见,温度下降率随y值增大而减小,y = 10 mm处温度下降率最大,y = 100、120和150 mm处的冷却曲线形状基本相同。研究[14]发现,7xxx系铝合金的淬火敏感区间约为210~420℃。依据试样的时间-温度曲线计算不同位置在该温度区间的平均淬火速率,如图2b所示。在y = 0~60 mm范围内,淬火速率随y值增大迅速减小,从y = 10 mm时的384.0℃/s减小到y = 60 mm的5.3℃/s。y > 60 mm后淬火速率缓慢减小,并稳定在约1.8℃/s。
图2 7136铝合金试样不同位置的时间-温度曲线与平均淬火速率
2.2 SSRT实验结果
实验结果表明,7136铝合金试样的强度随着淬火速率的减小而降低,伸长率则升高。作为代表给出淬火速率为263.0、5.3和1.8℃/s时7136铝合金试样的应力-应变曲线,如图3所示。淬火速率为263.0℃/s试样的强度最高,硅油和NaCl溶液中的强度分别约为537.0和523.1 MPa,而伸长率最低,分别约为15.1%和13.4%。淬火速率为5.3℃/s试样的强度和伸长率居中,硅油和NaCl溶液中强度分别为478.2和458.3 MPa,伸长率分别为15.7%和14.2%。淬火速率为1.8℃/s试样的强度最低,而伸长率最高,硅油和NaCl溶液中的强度分别为395.0和391.5 MPa,伸长率分别为24.5%和22.3%。
图3 淬火速率为263.0、5.3和1.8℃/s时7136铝合金试样的应力-应变曲线
由此可知,试样在硅油中的拉伸性能均高于NaCl溶液中,为评价各性能的损失情况,引入性能下降率KN,计算公式如下:
式中,NOil为试样在硅油中的性能,NNaCl为试样在NaCl溶液中的性能。分别用KR、KA和Kt表示强度(Rm)、伸长率(A)和断裂时间(t)的下降率,结果如图4,图中还给出了不同淬火速率下7136铝合金试样的强度、伸长率和断裂时间。由图4a可见,淬火速率大于5.3℃/s时,随淬火速率减小强度缓慢降低,淬火速率小于5.3℃/s后强度迅速降低。KR在淬火速率大于20℃/s时随淬火速率减小缓慢升高,淬火速率小于20℃/s之后迅速地升高,在淬火速率约为5.3℃/s时有最高值4.3%,然后迅速降低,淬火速率约为1.8℃/s后基本稳定在1.0%左右。
图4 不同淬火速率下7136铝合金试样的强度、伸长率及断裂时间及相应的下降率(KR、KA、Kt)
由图4b可知,硅油中的试样伸长率在淬火速率大于5.3℃/s时基本不变,淬火速率小于5.3℃/s后迅速增高。NaCl溶液中试样的伸长率在淬火速率大于5.3℃/s时随淬火速率的减小先出现明显降低再逐渐升高,淬火速率小于5.3℃/s后迅速升高。KA随淬火速率减小呈“M”状变化。
由图4c可知,淬火速率大于100℃/s时,硅油中试样的断裂时间变化不大,之后随淬火速率减小逐渐升高,最终稳定在68 h左右;NaCl溶液中试样的断裂时间在淬火速率大于100℃/s时随淬火速率减小缓慢降低,淬火速率在20~100℃/s时断裂时间几乎不变,之后迅速升高并稳定在63 h左右。Kt随淬火速率的减小迅速增加到16.6%,之后缓慢增大,在淬火速率为5.3℃/s时达到峰值(19.5%)后迅速降低。
可见,KR、KA和Kt表现出的规律并不一致,说明采用单一的性能损失很难准确地评价材料的SCC敏感性。为综合评估材料SCC的敏感性,引入SCC敏感指数(ISSRT),计算公式如下[4]:
式中,RmNaCl为NaCl溶液中的断裂强度(MPa),RmOil为硅油中的断裂强度(MPa),ANaCl为NaCl溶液中的伸长率(%),AOil为硅油中的伸长率(%)。ISSRT越大表示SCC敏感性越高。
图5给出不同淬火速率下7136铝合金试样的ISSRT。随着淬火速率的减小,ISSRT呈先升高再降低的趋势,淬火速率为5.3℃/s时的 最高(0.049),淬火速率为263.0和1.8℃/s时的ISSRT分别为0.027和0.024。根据以上实验结果,可以确定试样的SCC敏感性随淬火速率减小先升高后降低,且淬火速率为5.3℃/s时最高。
图5 不同淬火速率下7136铝合金试样的应力腐蚀敏感指数(ISSRT)
2.3 断口SEM像
图6为NaCl溶液中不同淬火速率7136铝合金试样断口形貌的SEM像。淬火速率为263.0℃/s试样的断口表层有较窄的腐蚀裂纹,存在少量的腐蚀产物,断口以穿晶断裂为主,如图6a和a1所示。淬火速率为5.3℃/s试样的断口出现较宽的腐蚀裂纹,裂纹已扩展到试样内部较深的区域,如图6b所示。观察图6b1发现,断口表面存在大量的泥浆状腐蚀产物,以沿晶断裂为主。淬火速率为1.8℃/s的试样表面存在大量腐蚀裂纹,裂纹内塞积有颗粒状腐蚀产物,如图6c所示。观察图6c1发现有较细的裂纹从腐蚀产物附近延伸到试样内部,断口以沿晶断裂为主。
图6 在NaCl溶液中的不同淬火速率下7136铝合金试样断口形貌的SEM像
为更好地分析试样的断裂行为,图7给出NaCl溶液中不同淬火速率下7136铝合金试样断口附近(ED-TD面)的SEM像。淬火速率为263.0℃/s试样的表层存在一些腐蚀裂纹,密度约为12 mm-1;裂纹比较尖锐,最大深度约为71.0 μm,如图7a1所示。将试样用Graff Sargent试剂(1 mL HF + 16 mL HNO3 + 3 g CrO3 + 83 mL H2O)腐蚀后,可以观察到裂纹主要是穿过晶粒向试样内部扩展,如图7a2所示;晶粒内存在一些白色初生相,EDS分析显示其成分(原子分数,下同)为:(76.15~85.68)%Al、(2.87~7.90)%Fe、(5.31~13.26)%Cu和少量Zn元素,应该为Al7Cu2Fe相[15,16]。
图7 在NaCl溶液中不同淬火速率下7136铝合金试样断口附近的SEM像
淬火速率为5.3℃/s试样腐蚀裂纹数量明显增加,约为19 mm-1,最大深度约为78.9 μm,如图7b1所示。从图7b2可以观察到该裂纹很宽,其前部沿晶界扩展到试样内部;晶界和晶内均分布有白色淬火相,EDS分析显示其成分为:(65.90~92.35)%Al、(2.43~6.52)%Mg、(5.31~8.58)%Zn和(1.25~2.71)%Cu,应该为η (Mg(ZnCu)2)相[15]。
淬火速率为1.8℃/s试样表面的腐蚀裂纹数量达到29 mm-1,但是最大深度明显减小,约为43.9 μm,如图7c1所示。仔细观察图7c2发现裂纹主要沿晶界和亚晶界扩展,路径很曲折。晶内和晶界上的淬火相尺寸明显比图7b2更大,数量也更多。
综合以上结果可知,随淬火速率减小,腐蚀裂纹的最大深度先增大后减小,腐蚀裂纹的数量逐渐增多。
2.4 微观组织
2.4.1 EBSD像
实验结果表明淬火速率对晶粒组织基本无影响,作为代表,图8给出淬火速率为263.0和1.8℃/s试样的EBSD像。黑色线代表角度大于15°的晶界,通常称为晶界,白色线代表角度为2°~15°的晶界,一般称为亚晶界[17]。2种试样晶粒组织差异很小,主要为被拉长的未再结晶晶粒,其中有许多亚晶,还有少量细小的再结晶晶粒。淬火速率为263.0℃/s试样的再结晶分数约为(38.3 ± 3.9)%。淬火速率为1.8℃/s试样的再结晶分数约为(37.1 ± 4.5)%,2者非常接近。
图8 不同淬火速率7136铝合金试样纵截面晶粒取向分布图
2.4.2 SEM像
图9a给出淬火速率为263℃/s 7136铝合金试样的SEM像。可以观察到大量尺寸为1.6~9.1 μm的白色第二相沿ED方向呈链状分布,EDS分析其成分为(75.22~86.32)%Al、(3.11~7.70)%Fe、(5.61~15.81)%Cu和少量Zn元素,应该为Al7Cu2Fe相。这些相形成于熔铸过程,在挤压等变形过程中会破碎。固溶时,它们容易引起其周围晶粒发生再结晶[18]。在腐蚀环境中,它们通常充当阴极引起电偶腐蚀[16,19]。淬火速率为1.8℃/s试样的SEM像如图9b所示。除Al7Cu2Fe相以外,晶界和晶内均出现大量η淬火相。晶界上的η相衬托出晶粒形貌。在晶界附近可以观察到明显的PFZ。
图9 不同淬火速率7136铝合金试样的SEM像
2.4.3 STEM-HAADF像
图10为不同淬火速率7136铝合金试样的STEM-HAADF像。淬火速率为263.0℃/s试样晶粒内未发现淬火相,如图10a所示。晶界上分布有η相,长度为(64.0 ± 22.9) nm,相间距为(60.0 ± 8.5) nm。晶界附近可见宽度比较均匀的PFZ,宽度为(55.7 ± 11.2) nm。亚晶界上的析出相(SGBP)分布更连续,尺寸更小,长度为(34.0 ± 12.9) nm,其附近的PFZ也更窄,宽度仅为(45.1 ± 8.0) nm。
图10 不同淬火速率7136铝合金试样的STEM-HAADF像
淬火速率减小至5.3℃/s时,试样的晶内和晶界上都出现了大量的淬火相,如图10b所示。一些淬火相在双喷时脱落,形成黑色的孔洞。淬火速率减小,试样在高温下的时间更长,有利于溶质原子扩散,因而在晶界、亚晶界及Al3Zr粒子等界面能高的地方形成粗大的η相[20]。因此GBP的尺寸差异很大,尺寸大的长度为(453.8 ± 130.3) nm,尺寸小的为(57.4 ± 22.0) nm,与淬火速率为263℃/s试样中的相当。晶界附近的PFZ宽度差别也更大,宽的达(223.0 ± 49.2) nm,窄的仅为(125.9 ± 10.7) nm,平均约174.5 nm。SGBP尺寸增加至(101.5 ± 34.7) nm,分布较连续,亚晶界附近的PFZ宽度为(70.6 ± 12.7) nm。
淬火速率继续减小至1.8℃/s时,晶界和亚晶界上的淬火相进一步长大,附近的PFZ明显更宽,如图10c所示。尺寸大的GBP可达1000 nm,尺寸小的GBP长度增加至80.0 nm左右,晶界附近的PFZ宽度为(303.0 ± 35.0) nm。SGBP的长度为(101.5 ± 34.7) nm,其附近的PFZ宽度为(139.0 ± 7.7) nm,一部分已经超过淬火速率为5.3℃/s试样中部分晶界PFZ的宽度。
综合图7b2和c2、图9以及图10的观察,发现淬火相的尺寸和数量随着淬火速率的减小而增加。这些淬火相几乎没有强化作用,且消耗了大量的溶质原子,减少了时效后η'强化相的数量,降低了试样的强度(图4a)。由于PFZ内没有强化相,因此宽度增加后,也降低了试样的强度[12]。因此,如图4a所示,拉伸强度随淬火速率减小而降低。统计晶界及亚晶界析出相形貌特征参数如图11所示。可见,GBP尺寸、相间距及PFZ宽度均随淬火速率减小而增加,在其他7xxx合金中发现了相似的规律。这是因为淬火速率减小后,更多的溶质原子扩散到晶界和亚晶界上,时效后形成尺寸和相间距更大的GBP,同时导致了PFZ宽度的增加[7,21]。
图11 不同淬火速率7136铝合金试样晶界和亚晶界上析出相的特征参数
此外,还通过STEM-EDS分析了不同淬火速率7136铝合金试样GBP中的化学成分,作为代表给出淬火速率为263.0℃/s试样的STEM-HAADF像和EDS面扫描图,如图12所示。从图12a可见,晶界上有3个明亮的η相,晶界附近有明显的PFZ。由图12b~e可知,η相中Zn、Mg、Cu元素含量高,而PFZ中Zn、Mg和Cu元素含量低。
图12 淬火速率为263.0℃/s时7136铝合金试样晶界处的STEM-HAADF像和EDS面扫描图
在不同淬火速率7136铝合金试样中统计了大量GBP中Zn、Mg、Cu元素含量,如图13所示。随着淬火速率的减小,GBP中Zn、Mg、Cu元素的含量均呈增加的趋势,但是3种元素的增加率不同。淬火速率从263.0℃/s减小至5.3℃/s时,Zn、Mg和Cu元素含量的增加率分别为44.9%、47.8%和28.9%;当淬火速率从5.3℃/s减小至1.8℃/s时,它们的增加率分别为11.0%、9.8%和88.4%。淬火速率大于5.3℃/s时,Zn、Mg元素的增加率明显高于Cu元素,而淬火速率小于5.3℃/s后Cu元素的增加率比Zn、Mg元素的更高。
图13 不同淬火速率7136铝合金试样晶界析出相中Zn、Mg、Cu元素的含量
慢速淬火时,Zn、Mg和Cu原子倾向扩散至晶界,在一些位置上形成了η相,而且使得晶界处这些元素浓度高于基体;淬火速率越小,晶界附近这些元素的浓度越高。Zn、Mg原子的扩散速率比Cu原子更快[22],淬火速率大于5.3℃/s时,GBP中Zn、Mg元素的增加率高于Cu元素。随着淬火速率继续减小,GBP中Zn、Mg原子接近饱和,它们的增加率随之降低。而扩散速率较慢的Cu原子在慢速淬火过程以及后续的时效过程中可以不断进入到GBP里[3]。另外,在淬火或者时效过程中Cu原子可以置换GBP中部分Zn原子[23],从而引起Cu元素含量继续增加。
3 分析讨论
根据SSRT结果可以确定7136铝合金的SCC敏感性随淬火速率减小先升高再降低,这不同于以往的一些研究结果[10~12]。淬火速率对晶界及亚晶界析出相的化学成分和晶界形貌特征的影响很复杂,需要综合考虑其对SCC敏感性的影响。基于实验结果绘制了不同淬火速率时7136铝合金SCC裂纹扩展示意图,如图14所示。
图14 不同淬火速率下7136铝合金应力腐蚀开裂裂纹扩展示意图
淬火速率为263.0℃/s时,试样晶内、晶界和亚晶界没有淬火相出现,晶界和亚晶界附近的PFZ很窄。NaCl溶液中试样的断口处未观察到晶界和亚晶界被明显腐蚀的特征,说明此时没有沿晶界和亚晶界发生阳极溶解。试样表面的Al7Cu2Fe相等引起其周围基体发生腐蚀并形成腐蚀坑[10,16],在外加应力的作用下,腐蚀坑底部形成应力集中,进而引发SCC裂纹的萌生[24~26]。腐蚀过程中产生的H会扩散到基体中,并沿着位错运动到裂纹尖端,降低了晶格结合力,导致SCC裂纹不断扩展[24]。扩展过程中,因为晶界和亚晶界附近狭窄的PFZ抑制了阳极溶解通道的形成[13,27],裂纹选择在晶内不断扩展,如图14a所示。此时SCC以氢脆为主,裂纹主要穿晶扩展,强度、伸长率和断裂时间的损失不大,试样的SCC敏感性并不高。
淬火速率减小至约5.3℃/s时,淬火相的数量明显增多,尺寸增大,GBP的相间距有所增大,晶界附近的PFZ宽度比淬火速率为263.0℃/s时明显增加,亚晶界附近的PFZ宽度增加很小(图11)。淬火相是H不可逆的陷阱,可以捕获试样中的H并使之以气体的形式排放出去,因而减缓了氢脆[28,29]。然而,淬火相的腐蚀电位比基体和Al7Cu2Fe相更负,因而试样表面的淬火相在腐蚀溶液中会充当阳极优先被溶解[27],形成腐蚀裂纹源。GBP中Zn、Mg元素含量比淬火速率为263.0℃/s时大幅增加,引起GBP与基体和Al7Cu2Fe相的电势差增大[15,30],这促进了腐蚀裂纹扩展。晶界附近的PFZ宽度增加有利于裂纹的形成和扩展[10],因而晶界成为快速腐蚀通道,但多数亚晶界对微裂纹的产生和扩展还有较强的抑制作用。此时腐蚀裂纹在氢脆和阳极溶解共同作用下沿晶界迅速扩展到试样内部更深的地方,导致更大的腐蚀深度,如图14b所示。因而试样强度和断裂时间等的损失更大,试样的SCC敏感性很高。
淬火速率减小至约1.8℃/s时,淬火相的数量和尺寸、晶界和亚晶界附近的PFZ宽度都很大,如图11所示。淬火相增多可以捕获更多的H,因而氢脆进一步被削弱。试样表面更多的淬火相被溶解并在外力作用下形成裂纹源,裂纹数量比淬火速率为263.0和5.3℃/s时分别增加了141.7%和52.6%,这大幅缓解了应力集中。GBP中Cu元素大量的增加也可有效抑制SCC裂纹扩展[7,8,24,31,32]。图15是淬火速率为5.3和1.8℃/s时板材的晶界和亚晶界PFZ宽度分布情况。可见,淬火速率为5.3℃/s时,约80%的晶界PFZ宽度在100~200 nm,而淬火速率为1.8℃/s时有约75%的亚晶界PFZ在这个宽度范围内,即淬火速率为1.8℃/s时许多亚晶界PFZ宽度已经超过了淬火速率为5.3℃/s试样中晶界PFZ的宽度。更宽的PFZ导致阳极溶解通道更容易形成,这就增加了沿晶界和亚晶界裂纹的数量(图14c),因而主裂纹被钝化。微裂纹的产生既释放了应力又延缓了裂纹扩展的速率。Tanguy等[25]也发现腐蚀裂纹增多可以降低SCC的扩展速率。因此,淬火速率为1.8℃/s时试样各项性能的损失都很小,试样的SCC敏感性反而降低。
图15 淬火速率为5.3和1.8℃/s时7136铝合金试样中不同无沉淀析出带宽度的晶界和亚晶界的比例
4 结论
(1) 7136铝合金应力腐蚀开裂敏感性随着淬火速率的减小先升高再降低,淬火速率约为5.3℃/s时的应力腐蚀开裂敏感性最高。
(2) 随着淬火速率的减小,晶界析出相增大,相间距增大,PFZ增宽。晶界析出相中Zn、Mg和Cu元素含量随淬火速率减小而增加。淬火速率大于5.3℃/s时,晶界析出相中Zn、Mg元素的含量迅速增加,Cu元素含量缓慢增加;淬火速率小于5.3℃/s后,Zn、Mg元素含量增速降低,而Cu元素含量迅速增加。
(3) 淬火速率减小,晶界和亚晶界附近的PFZ宽化,能够充当腐蚀裂纹扩展路径,应力腐蚀裂纹扩展方式从以穿晶扩展为主转变为沿晶界和亚晶界扩展。
参考文献
1 Deng Y L, Zhang X M. Development of aluminium and aluminium alloy [J]. Chin. J. Nonferrous Met., 2019, 29: 2115
1 邓运来, 张新明. 铝及铝合金材料进展 [J]. 中国有色金属学报, 2019, 29: 2115
2 Rometsch P A, Zhang Y, Knight S. Heat treatment of 7xxx series aluminium alloys—Some recent developments [J]. Trans. Nonferrous Met. Soc. China, 2014, 24: 2003
doi: 10.1016/S1003-6326(14)63306-9
3 Knight S P, Pohl K, Holroyd N J H, et al. Some effects of alloy composition on stress corrosion cracking in Al-Zn-Mg-Cu alloys [J]. Corros. Sci., 2015, 98: 50
doi: 10.1016/j.corsci.2015.05.016
4 Chen S Y, Li J Y, Hu G Y, et al. Effect of Zn/Mg ratios on SCC, electrochemical corrosion properties and microstructure of Al-Zn-Mg alloy [J]. J. Alloys Compd., 2018, 757: 259
doi: 10.1016/j.jallcom.2018.05.063
5 Liu L, Jia Y Y, Jiang J T, et al. The effect of Cu and Sc on the localized corrosion resistance of Al-Zn-Mg-X alloys [J]. J. Alloys Compd., 2019, 799: 1
doi: 10.1016/j.jallcom.2019.05.189
6 Yu M Y, Zhang Y A, Li X W, et al. Effect of recrystallization on plasticity, fracture toughness and stress corrosion cracking of a high-alloying Al-Zn-Mg-Cu alloy [J]. Mater. Lett., 2020, 275: 128074
doi: 10.1016/j.matlet.2020.128074
7 Xie P, Chen S Y, Chen K H, et al. Enhancing the stress corrosion cracking resistance of a low-Cu containing Al-Zn-Mg-Cu aluminum alloy by step-quench and aging heat treatment [J]. Corros. Sci., 2019, 161: 108184
doi: 10.1016/j.corsci.2019.108184
8 Chen J F, Zhang X F, Zou L C, et al. Effect of precipitate state on the stress corrosion behavior of 7050 aluminum alloy [J]. Mater. Charact., 2016, 114: 1
doi: 10.1016/j.matchar.2016.01.022
9 Yuan D L, Chen K H, Chen S Y, et al. Enhancing stress corrosion cracking resistance of low Cu-containing Al-Zn-Mg-Cu alloys by slow quench rate [J]. Mater. Des., 2019, 164: 107558
doi: 10.1016/j.matdes.2018.107558
10 Jiang F Q, Huang J W, Jiang Y G, et al. Effects of quenching rate and over-aging on microstructures, mechanical properties and corrosion resistance of an Al-Zn-Mg (7046A) alloy [J]. J. Alloys Compd., 2021, 854: 157272
doi: 10.1016/j.jallcom.2020.157272
11 Chen S Y, Chen K H, Peng G S, et al. Effect of quenching rate on microstructure and stress corrosion cracking of 7085 aluminum alloy [J]. Trans. Nonferrous Met. Soc. China, 2012, 22: 47
doi: 10.1016/S1003-6326(11)61138-2
12 Xiao Q F, Xu Y M, Huang J W, et al. Effects of quenching agents, two-step aging and microalloying on tensile properties and stress corrosion cracking of Al-Zn-Mg-Cu alloys [J]. J. Mater. Res. Technol., 2020, 9: 10198
doi: 10.1016/j.jmrt.2020.07.014
13 Liu S D, Chen B, Li C B, et al. Mechanism of low exfoliation corrosion resistance due to slow quenching in high strength aluminium alloy [J]. Corros. Sci., 2015, 91: 203
doi: 10.1016/j.corsci.2014.11.024
14 Liu S D, Zhong Q M, Zhang Y, et al. Investigation of quench sensitivity of high strength Al-Zn-Mg-Cu alloys by time-temperature-properties diagrams [J]. Mater. Des., 2010, 31: 3116
doi: 10.1016/j.matdes.2009.12.038
15 Ma Z M, Liu J, Yang Z S, et al. Effect of cooling rate and grain structure on the exfoliation corrosion susceptibility of AA 7136 alloy [J]. Mater. Charact., 2020, 168: 110533
doi: 10.1016/j.matchar.2020.110533
16 Sun Y W, Pan Q L, Sun Y Q, et al. Localized corrosion behavior associated with Al7Cu2Fe intermetallic in Al-Zn-Mg-Cu-Zr alloy [J]. J. Alloys Compd., 2019, 783: 329
doi: 10.1016/j.jallcom.2018.12.151
17 Fang H C, Chao H, Chen K H. Effect of recrystallization on intergranular fracture and corrosion of Al-Zn-Mg-Cu-Zr alloy [J]. J. Alloys Compd., 2015, 622: 166
doi: 10.1016/j.jallcom.2014.10.044
18 Liao Y G, Han X Q, Zeng M X, et al. Influence of Cu on microstructure and tensile properties of 7xxx series aluminum alloy [J]. Mater. Des., 2015, 66: 581
doi: 10.1016/j.matdes.2014.05.003
19 Chemin A, Marques D, Bisanha L, et al. Influence of Al7Cu2Fe intermetallic particles on the localized corrosion of high strength aluminum alloys [J]. Mater. Des., 2014, 53: 118
doi: 10.1016/j.matdes.2013.07.003
20 Godard D, Archambault P, Aeby-Gautier E, et al. Precipitation sequences during quenching of the AA 7010 alloy [J]. Acta Mater., 2002, 50: 2319
doi: 10.1016/S1359-6454(02)00063-0
21 Chen J S, Li X W, Xiong B Q, et al. Quench sensitivity of novel Al-Zn-Mg-Cu alloys containing different Cu contents [J]. Rare Met., 2020, 39: 1395
doi: 10.1007/s12598-017-0981-y
22 Du Y, Chang Y A, Huang B Y, et al. Diffusion coefficients of some solutes in fcc and liquid Al: Critical evaluation and correlation [J]. Mater. Sci. Eng., 2003, A363: 140
23 Garner A, Euesden R, Yao Y C, et al. Multiscale analysis of grain boundary microstructure in high strength 7xxx Al alloys [J]. Acta Mater., 2021, 202: 190
doi: 10.1016/j.actamat.2020.10.021
24 Song R G, Dietzel W, Zhang B J, et al. Stress corrosion cracking and hydrogen embrittlement of an Al-Zn-Mg-Cu alloy [J]. Acta Mater., 2004, 52: 4727
doi: 10.1016/j.actamat.2004.06.023
25 Tanguy D, Bayle B, Dif R, et al. Hydrogen effects during IGSCC of pure Al-5Mg alloy in NaCl media [J]. Corros. Sci., 2002, 44: 1163
doi: 10.1016/S0010-938X(01)00140-8
26 Magnin T, Chambreuil A, Bayle B. The corrosion-enhanced plasticity model for stress corrosion cracking in ductile fcc alloys [J]. Acta Mater., 1996, 44: 1457
doi: 10.1016/1359-6454(95)00301-0
27 Song F X, Zhang X M, Liu S D, et al. The effect of quench rate and overageing temper on the corrosion behaviour of AA7050 [J]. Corros. Sci., 2014, 78: 276
doi: 10.1016/j.corsci.2013.10.010
28 Christodoulou L, Flower H M. Hydrogen embrittlement and trapping in Al-6%-Zn-3%-Mg [J]. Acta Metall., 1980, 28: 481
doi: 10.1016/0001-6160(80)90138-8
29 Tsai T C, Chuang T H. Role of grain size on the stress corrosion cracking of 7475 aluminum alloys [J]. Mater. Sci. Eng., 1997, A225: 135
30 Wang L, Dong C F, Zhang D W, et al. Effect of alloying elements on initial corrosion behavior of aluminum alloy in Bangkok, Thailand [J]. Acta Metall. Sin., 2020, 56: 119
30 王 力, 董超芳, 张达威 等. 合金元素对铝合金在泰国曼谷地区初期腐蚀行为的影响 [J]. 金属学报, 2020, 56: 119
31 Sarkar B, Marek M, Starke E A. The effect of copper content and heat treatment on the stress corrosion characteristics of Al-6Zn-2Mg-XCu alloys [J]. Metall. Trans., 1981, 12A: 1939
32 Rao A C U, Vasu V, Govindaraju M, et al. Stress corrosion cracking behaviour of 7xxx aluminum alloys: A literature review [J]. Trans. Nonferrous Met. Soc. China, 2016, 26: 1447
doi: 10.1016/S1003-6326(16)64220-6
免责声明:本网站所转载的文字、图片与视频资料版权归原创作者所有,如果涉及侵权,请第一时间联系本网删除。
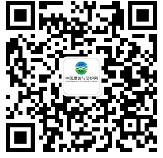
官方微信
《腐蚀与防护网电子期刊》征订启事
- 投稿联系:编辑部
- 电话:010-62316606-806
- 邮箱:fsfhzy666@163.com
- 腐蚀与防护网官方QQ群:140808414