NH4H2PO4作为一种高效的复合肥料和工业原料,市场前景广阔。目前,NH4H2PO4主要是以热法磷酸或湿法磷酸与氨反应制得,其生产过程中会产生大量的低温余热[1,2]。低温余热资源回收利用的途径主要为用作一般加热热源,被热泵回收利用,低温余热发电[3]。随着我国对低温余热发电的大力支持,再加上其自身具有显著的经济效益和社会效益,低温余热发电受到诸多青睐[4]。
低温余热发电技术的核心原理为有机朗肯循环 (ORC),低温余热发电装置主要由循环泵、蒸发器、汽轮机、冷凝器四部分组成[3]。蒸汽在汽轮机中做完功后,其压力和温度不断降低,并在汽轮机转动部件 (如转子) 表面形成较薄的液膜,由于低温余热发电装置中无除氧、除盐等设施,蒸汽中氧气、腐蚀性杂质盐等又会溶于薄液膜中而形成强电解质溶液,诱发转子材料发生腐蚀破坏,给低温余热发电装置的运行带来安全隐患[4]。
目前,关于转子材料的腐蚀研究,更多集中于核电或火力发电汽轮机低压转子材料的腐蚀行为研究[5-12]。Luo等[5-7]利用U型试样研究了核电汽轮机焊接转子25Cr2Ni2MoV焊接接头在180 ℃、3.5% NaCl溶液中的腐蚀行为,研究表明,焊缝区优先产生大量夹杂物诱发的点蚀坑,此外,焊接接头的母材、焊缝、热影响区存在电势差,并诱发电偶腐蚀。欧阳玉清等[8]研究了温度对核电汽轮机焊接转子25Cr2Ni2MoV焊接接头电偶腐蚀的影响,研究表明,随着温度升高,材料电偶腐蚀效应增强。Maeng等[9]通过恒速率拉伸实验研究了高温水中醋酸对火力发电汽轮机低压转子材料3.5NiCrMoV应力腐蚀行为的影响,研究表明,随着醋酸浓度增大,材料的应力腐蚀敏感性增大,此外,高浓度的醋酸也会造成裂纹尖端钝化。与核电或火力发电汽轮机所用的蒸汽不同,利用NH4H2PO4生产行业产生的低温余热资源发电的装置所用蒸汽温度较低、压力较小,造成转子表面更容易形成一层薄液膜。正常情况下,核电或火力发电汽轮机中蒸汽的含氧量限制在5 10-3 mg/L以下,而启停机时,从冷凝器进入的氧含量增大,最高氧含量可达20 mg/L,而低温余热发电装置中无除氧设施,造成了其蒸汽中的氧含量远高于核电或火力发电汽轮机所用的蒸汽[13]。低温余热发电装置中也无除盐设施,致使其蒸汽中还含有部分残留的NH4H2PO4,NH4H2PO4易溶于水,形成酸性水溶液。然而,汽轮机转子常见材料在含NH4H2PO4酸性溶液条件下NH4H2PO4溶液浓度等变化对材料腐蚀行为的影响规律及其机理鲜有报道,即NH4H2PO4溶液浓度、溶解氧、温度等腐蚀因素影响的基础研究尚未系统开展。
本文以2Cr-1Ni-1.2Mo-0.2V钢作为研究对象,研究结果可为利用NH4H2PO4生产行业产生的低温余热资源发电的装置开发及其防护提供理论依据和数据支持。
1 实验方法
实验用材为2Cr-1Ni-1.2Mo-0.2V钢 (1R钢),主要化学成分 (质量分数,%) 为:C 0.32,Si 0.02,Mn 0.6,S 0.0059,P 0.0015,Cr 2.23,Mo 1.17,Ni 0.95,V 0.22,Al 0.0058,Cu 0.048,As 0.006,Fe余量。1R钢的组织以回火索氏体为主,同时还有少量块状的铁素体组织。
实验用溶液为不同浓度的NH4H2PO4溶液,即纯度为99%的NH4H2PO4药剂与去离子水混合而成的0 (纯去离子水)、1、30、60、90、120 mmol/L NH4H2PO4溶液。
利用线切割的方式将实验用材1R钢加工成所需的试样,失重实验试样规格为50 mm×20 mm×4 mm,XPS试样规格为5 mm×5 mm×2 mm,电化学实验试样规格为10 mm×10 mm×10 mm。试样加工后,认真清洗试样表面的油污和铁锈,电化学实验试样采用环氧树脂对其进行真空冷镶。随后试样表面逐级打磨至2000#水磨砂纸并最终抛光,抛光后,试样在无水乙醇中超声处理5 min,以去除试样表面残留的SiC颗粒,然后用去离子水清洗试样表面,无水乙醇脱除残留水分、冷风吹干,最后放入干燥器中待用,其中失重实验试样在干燥器中静置24 h后称重 (精确至0.1 mg)。去除失重实验试样腐蚀产物的酸洗液由500 mL盐酸 (HCl, =1.19 g/mL)+5 g 1,3-二丁基-2-硫脲+500 mL去离子水配置而成。酸洗液去除腐蚀产物后,用去离子水、无水乙醇清洗试样,冷风快速吹干,在干燥皿中静置24 h后称重 (精确至0.1 mg),并用 公式 (1) 计算材料腐蚀速率[14]。
(1)
其中,R均为腐蚀速率,g·m-2·h-1;M和Mt是实验前和酸洗后的质量,g;S是试样表面积,m2;T是实验时间,h。
电化学实验在PARSTAT4000型电化学工作站上进行,三电极体系,1R钢为工作电极,铂片为辅助电极,饱和甘汞电极 (SCE) 为参比电极,测试温度为(25±2) ℃。开始测试前,试样需在0 (纯去离子水)、1、30、60、90、120 mmol/L NH4H2PO4溶液中浸泡20 h,待试样表面稳定后再进行测试[15]。先测900 s开路电位,开路电位稳定后再进行相应的电化学测试,其中极化扫描在开路电位±0.25 V的范围内进行,扫速为0.1666 mV/s;电化学阻抗谱 (EIS) 测试是在稳定的开路处对工作电极施加一个±5 mV的交流电压扰动下进行的,测试频率范围为105~10-2 Hz,并使用ZSimDemo软件对其数据进行拟合分析。
通过失重法测量1R钢在不同浓度NH4H2PO4溶液中的腐蚀速率,利用LEXT-OLS5000激光共聚焦显微镜 (CLSM) 分析材料表面腐蚀形貌;选取在120 mmol/L NH4H2PO4溶液中浸泡20 h后的试样,通过场发射扫描电镜 (FE-SEM,Thermo Fisher APREO) 及其附带的Quantax400能谱仪 (EDS) 分析内外层腐蚀产物形貌及其合金元素分布;在120 mmol/L NH4H2PO4溶液中浸泡20 h后的试样表面刮取腐蚀产物粉末,使用X射线衍射仪 (XRD,Bruker D8 Advance) 对其进行物相分析,XRD测试采用Co靶,Kα波长0.15406 nm,管电压40 kV,管电流为40 mA,扫描速度为20°/min,衍射角扫描范围为10°~80°,使用MDI Jade6软件处理数据;选取在30、60、90、120 mmol/L NH4H2PO4溶液中浸泡20 h后的试样,用去离子水去除表面疏松的腐蚀产物,通过X射线光电子能谱仪 (XPS,AXIS ULTRADLD) 分析与1R钢基体结合紧固的腐蚀产物组成,XPS测试所用光源为单色Al (=1486.6 eV),测试深度约5 nm,收集Fe 2p、Cr 2p、Mo 3d等能谱图,通过C 1s (284.6 eV) 荷电校正后,采用XPS PEAK41软件处理数据。
2 结果与讨论
2.1 腐蚀速率
图1为1R钢在0 (去离子水)、1、30、60、90、120 mmol/L NH4H2PO4溶液中浸泡20 h的平均腐蚀速率。可见,1R钢在去离子水中的腐蚀速率最小,约为0.017 g·m-2·h-1,在1 mmol/L NH4H2PO4溶液的腐蚀速率约为0.152 g·m-2·h-1,其值比1R钢在去离子水中的腐蚀速率大7.973倍。继续增大NH4H2PO4溶液的浓度,发现1R钢的腐蚀速率也随之增大。1~30、30~60、60~90、90~120 mmol/L NH4H2PO4溶液对应的1R钢的腐蚀速率相对于NH4H2PO4溶液浓度的导数分别约为0.001、0.002、0.003、0.001 L·m-2·h-1 mmol-1,即随着NH4H2PO4溶液浓度的增大,1R钢的腐蚀速率先快速增大后缓慢增大。
图1 1R钢在不同浓度NH4H2PO4溶液中浸泡20 h的平均腐蚀速率
2.2 腐蚀形貌及成分分析
图2为1R钢在0 (去离子水)、1、30、60、90、120 mmol/L NH4H2PO4溶液中浸泡20 h后的腐蚀形貌,图2中所选区域的三维形貌见图3。可见,1R钢在去离子水和1 mmol/L NH4H2PO4溶液中浸泡20 h后,钢基体表面均出现点蚀坑 (图2a2和b2),从在这两种溶液中浸泡后的试样表面随机选取2个点蚀坑,用激光共聚焦显微镜获取其三维形貌 (见图4a和b),可见1R钢在去离子水中浸泡后而生成的点蚀坑孔径和孔深分别为72.9和11.1 μm,而1R钢在1 mmol/L NH4H2PO4溶液中浸泡后生成的点蚀坑孔径和孔深分别73.5和3.1 μm,可见加入少量的NH4H2PO4,可明显抑制点蚀坑向纵向发展。
图2 1R钢在不同浓度NH4H2PO4溶液中浸泡20 h的表面腐蚀形貌
图3 图2中所选区域的三维形貌
图4 在120 mmol/L NH4H2PO4溶液中浸泡20 h后的1R钢试样表面微观形貌
将1R钢放入1 mmol/L NH4H2PO4溶液中浸泡20 h,发现材料表面被部分黄色腐蚀产物覆盖,覆盖度约15% (图2b1)。当NH4H2PO4溶液浓度大于或等于30 mmol/L时,1R钢表面均被黄色的腐蚀产物完全覆盖 (图2c1~f1)。利用激光共聚焦显微镜获取1R钢在30、60、90、120 mmol/L NH4H2PO4溶液中浸泡20 h后的表面三维形貌 (图3c~f),可见材料表面的最大高度差分别为26.9、20.1、17.2和15.8 μm,说明随着NH4H2PO4溶液浓度的增大,材料表面起伏程度逐渐减小。表1为1R钢在30、60、90、120 mmol/L NH4H2PO4溶液中浸泡20 h后的表面粗糙度参数,可见表面粗糙度参数随NH4H2PO4溶液浓度的增大而减小,这与上述表面起伏程度分析结果一致。随着表面粗糙度的减小,表面积比参数也在减小,表明材料与腐蚀介质接触的有效面积减小,此结果会抑制材料腐蚀速率增大[16]。
表1 1R钢在30、60、90和120 mmol/L NH4H2PO4溶液中浸泡20 h后的表面粗糙度参数
1R钢在30~120 mmol/L NH4H2PO4溶液中浸泡20 h后其表面覆盖的黄色的腐蚀产物较为疏松,用镊子轻轻剥落这些黄色的腐蚀产物,便可看到内部黑色的腐蚀产物。利用激光共聚焦显微镜测得剥落区相较于未剥落区的高度,本文将其高度近似等价于材料表面覆盖的腐蚀产物膜厚度,表明1R钢在30、60、90、120 mmol/L NH4H2PO4溶液中浸泡20 h后其表面覆盖的厚度分别为8.7、10.6、14.8和18.6 μm,即随着NH4H2PO4溶液浓度的增大,1R钢表面覆盖的腐蚀产物逐渐增厚。去除腐蚀产物膜后,在30、60、90、120 mmol/L NH4H2PO4溶液中浸泡20 h后的1R钢基体均光滑平整,均未出现局部腐蚀,材料腐蚀特征为均匀腐蚀 (图2c2~f2)。
为验证1R钢在30~120 mmol/L NH4H2PO4溶液中浸泡20 h后其表面形成的腐蚀产物膜为双层结构,本文选取在120 mmol/L NH4H2PO4溶液中浸泡20 h后的1R钢试样,其表面微观形貌见图4。可见1R钢试样表面腐蚀产物膜为双层结构,外层膜较为疏松 (图4a),利用胶布将外层腐蚀产物膜轻轻粘除,可观察到内层腐蚀产物膜 (图4b),内层腐蚀产物膜较薄,可看到膜层下方钢基体晶界,但内层膜致密度高于外层膜[17]。
为了进一步分析在120 mmol/L NH4H2PO4溶液中浸泡20 h后的1R钢试样表面内外层腐蚀产物膜的差异性,分别对内外层腐蚀产物膜进行EDS分析。由表2中EDS结果可知,外层腐蚀产物膜主要由O、P和Fe构成,Fe/P/O原子比为1.03∶1∶5.85,Fe含量为31.37% (质量分数),可推测外层腐蚀产物膜主要为钢基体溶解生成的Fe2+及Fe3+ (溶液中的O将钢基体溶解生成的Fe2+氧化为Fe3+) 与溶液中的阴离子 (如PO43-) 结合而形成的疏松膜层,再结合外层腐蚀产物膜中Fe/P/O原子比为1.03∶1∶5.85,说明该腐蚀产物膜层可能为一个FePO4和Fe3(PO4)2混合的膜层[18]。内层腐蚀产物主要由Fe、Cr、Mo、O和P构成,Fe/Cr/Mo原子比为101.95∶3.24∶1,Fe含量为88.70%,内层腐蚀产物中Fe含量约为外层腐蚀产物膜中Fe含量的2.83倍;P/O原子比为1∶10.37,可推测内层腐蚀产物膜主要为钢基体与溶液中的O反应而生成的氧化物膜层[17]。
表2 在120 mmol/L NH4H2PO4溶液中浸泡20 h后的1R钢试样表面腐蚀产物EDS分析
为证实上述猜想,本文对在120 mmol/L NH4H2PO4溶液中浸泡20 h后的1R钢表面生成的腐蚀产物进行XRD分析 (图5)。由图可知,有明显的Fe3(PO4)2·8H2O衍射峰,该结果表明,腐蚀产物的主要成分有Fe3(PO4)2,反应过程中,钢基体溶解生成的Fe2+与NH4H2PO4分解而成的PO43-结合并沉积在钢基体上[18]。腐蚀产物的XRD图谱也显现出FePO4、Fe3O4衍射峰,结果表明,钢基体溶解生成的Fe2+被溶液中的溶解氧氧化为Fe3+,该Fe3+与NH4H2PO4分解而成的PO43-结合并沉积在钢基体上,另外,钢基体与溶液中的O反应而生成FePO4。结合图4,5和表2可知,1R钢在120 mmol/L NH4H2PO4溶液中浸泡20 h后形成的腐蚀产物膜为双层结构,外层腐蚀产物膜主要由Fe3(PO4)2、FePO4构成,内层腐蚀产物膜主要由Fe3O4构成,这与龙晋明等[19]的研究结果相似。
图5 在120 mmol/L NH4H2PO4溶液中浸泡20 h后的1R钢试样表面腐蚀产物的XRD谱
2.3 XPS测试
通过上述分析,表明1R钢在30~120 mmol/L溶液中浸泡20 h后形成的腐蚀产物膜为双层结构,外层产物膜较疏松,且易脱落,而内层腐蚀产物膜附着力较强,因此本文用去离子水去除表面外层疏松的腐蚀产物,保留与基体结合紧固的内层腐蚀产物,并研究其相组成及其相对含量。
1R钢在30~120 mmol/L NH4H2PO4溶液中浸泡20 h后形成的内层腐蚀产物膜中Fe 2p3/2、Cr 2p3/2、Mo 3d的XPS图谱如图6所示。通过NIST的原子谱数据库和相关文献对图谱进行分峰拟合,主要组成物质的结合能分别为:Fe 2p3/2 Fe3O4/711.4 eV;Fe(OH)3/713.9 eV;Fe3(PO4)2/710.1 eV;FePO4/712.8 eV,Cr2p3/2 CrO3/578.3 eV;Cr(OH)3/577.1 eV,Mo 3d5/2 Mo6+/232.5 eV及Mo 3d3/2 Mo6+/235.8 eV。表3为XPS图谱拟合出的峰面积及各峰的面积比[18-22]。可见内层腐蚀产物膜主要由Fe的氧化物、磷化物、氢氧化物,Cr的氧化物和氢氧化物及Mo6+的相应化合物组成。将NH4H2PO4溶液浓度由30 mmol/L提高到120 mmol/L,虽然溶液浓度增大了3倍,但是Fe3(PO4)2的峰面积比仅由16.8%增至25.7%,FePO4的峰面积比由20.9%减至16.3%,Fe(OH)3的峰面积比由15.6%减至10.1%,Fe3O4的峰面积比基本没变,变化的原因是随着NH4H2PO4溶液浓度的增大,溶液pH变小,从而抑制Fe2+氧化[23]。实验表明30~120 mmol/L NH4H2PO4溶液中pH在4.1至4.9之间,接近FePO4沉淀产生的最佳pH (3~5),随着Fe3+减少,FePO4的含量便会出现减少的趋势,水解而得的Fe(OH)3也会出现减少的趋势[24,25]。将溶液浓度由30 mmol/L提高到120 mmol/L,腐蚀产物膜中CrO3的峰面积比由31.2%增至61.4%,这或许是因为pH增大会促进稳定的Cr的氧化物生成[26]。
图6 1R钢在不同浓度NH4H2PO4溶液中形成的内层腐蚀产物膜中Fe 2p3/2,Cr2p3/2和Mo 3d XPS图谱
表3 内层腐蚀产物膜中Fe 2p3/2、Cr 2p3/2、Mo 3d的XPS图谱拟合出的峰面积及其所占的比重
为了进一步分析1R钢在30~120 mmol/L NH4H2PO4溶液中浸泡20 h后表面形成的内层腐蚀产物膜的差异性,本文利用 公式 (2) 计算不同浓度NH4H2PO4溶液对应的内层腐蚀产物膜中Fe、Cr、Mo之间原子分数 (Cx )[28]。其计算结果见表4。
表4 内层腐蚀产物膜中主要元素含量
(2)
其中,Ix 是各元素的峰强度,可用其对应的峰面积表示,Sx 为各元素的灵敏度因子,Fe 2p、Cr 2p、Mo 3d对应的灵敏度因子分别为2.957、2.427、3.321。从表5中可以看出,Fe对应的化合物为内层腐蚀产物膜中最主要的物质,随着NH4H2PO4溶液浓度的增大,内层腐蚀产物膜中Fe含量呈下降趋势,而Cr、Mo含量却呈递增趋势。这是因为随着NH4H2PO4溶液浓度的增大,溶液pH变小,电导率增大,内层腐蚀产物膜中Fe、Cr、Mo对应的化合物发生选择性溶解,稳定性较差的Fe的氧化物、氢氧化物、磷化物溶解速度较快,而Cr的氧化物和氢氧化物及高价态Mo6+相应的化合物由于耐蚀性较好,溶解缓慢而出现一定的富集,从而造成内层腐蚀产物膜中Fe含量减少,而Cr、Mo含量增多的结果[27-30]。
表5 1R钢在不同浓度NH4H2PO4溶液中的电化学阻抗谱参数
2.4 开路电位
1R钢在不同浓度NH4H2PO4溶液中浸泡20 h后测得的稳定开路电位,pH值和电导率如图7所示。由图7a可知,1R钢的开路电位随NH4H2PO4溶液浓度的增大先负移后基本不变,值得注意的是,1R钢在30~120 mmol/L NH4H2PO4溶液中浸泡20 h后测得的开路电位极为相近 (图7a)。实验发现当溶液由去离子水变成30 mmol/L NH4H2PO4溶液时,溶液pH由6降到4.9,溶液电导率由0.6 μS/cm增到2695 μS/cm,电导率增大了约4491倍 (图7b),随着溶液pH快速下降,电导率快速上升,而此时1R钢表面尚未形成致密的腐蚀产物膜,所以在此浓度范围内,1R钢的腐蚀倾向性随NH4H2PO4溶液浓度的增大而增大,开路电位负移[32];将NH4H2PO4溶液浓度由30 mmol/L增大到120 mmol/L,溶液pH由4.9降到4.1,溶液电导率由2695 μS/cm增到8995 μS/cm电导率仅增大了约2.3倍;随着NH4H2PO4溶液浓度的增大,试样表面腐蚀产物形成也会加快,试样表面覆盖腐蚀产物逐渐增厚;内层腐蚀产物膜中Cr、Mo出现一定程度的富集 (表5),一定程度抑制1R钢腐蚀,促进腐蚀因素与抑制腐蚀因素共同作用,最终造成了1R钢的腐蚀倾向性基本不变的结果,故开路电位极为相近[30-33]。
图7 1R钢在不同浓度NH4H2PO4溶液中的开路电位及不同浓度NH4H2PO4溶液的pH和电导率
2.5 极化曲线
图8为1R钢在不同浓度NH4H2PO4溶液中浸泡20 h后从阴极向阳极方向进行扫描测试的Tafel曲线及其相应的自腐蚀电位和自腐蚀电流密度。由图可见,自腐蚀电位随NH4H2PO4溶液浓度的增大先负移后基本不变,其变化规律与上文开路电位分析结果一致。自腐蚀电位只是反映材料腐蚀的倾向,并不能说明材料腐蚀速率的大小,自腐蚀电流密度却与材料腐蚀速率大小相关,一般材料自腐蚀电流密度越大,材料腐蚀越快[34,35]。从图8b中可获知1R钢的自腐蚀电流密度随NH4H2PO4溶液浓度的增大而增大,所以1R钢的腐蚀速率随NH4H2PO4溶液浓度的增大而增大。
图8 不同浓度NH4H2PO4溶液下1R钢的极化曲线、自腐蚀电位和自腐蚀电流密度
2.6 电化学阻抗谱
图9为1R钢在不同浓度NH4H2PO4溶液中浸泡20 h后测得的电化学阻抗谱。从Nyquist图可知,当NH4H2PO4溶液浓度为0~1 mmol/L时,电化学阻抗谱均有两个容抗弧,相应的,在Bode图 (图9a4) 上有两个时间常数,而高频部分的容抗弧只有在低电导率溶液中才会出现,一旦溶液电导率增大到一定程度,高频部分的容抗弧便消失不见 (图9a2),由高频部分的容抗弧拟合出来的电阻的倒数与溶液电导率呈线性关系[38]。随着NH4H2PO4溶液浓度的增大,1R钢试样表面腐蚀产物增多,电化学阻抗谱表现为高频区和低频区各出现一个容抗弧 (图9a2),其中高频容抗弧与腐蚀产物膜的膜层电容及膜层电阻有关,而低频容抗弧与双电层电容及电荷转移电阻有关,此外,低频区也出现了感抗弧,相应的,在Bode图 (图9a4) 上还有一个低频区的时间常数[17]。
图9 不同浓度NH4H2PO4溶液下1R钢的电化学阻抗谱
结合图2和4,给出了图10所示的等效电路[37,39],拟合结果如表5所示。图10a为1R钢在0~1 mmol/L NH4H2PO4溶液中腐蚀的等效模型,此时1R钢表面的腐蚀产物较少,其中,Rs为溶液电阻,Qdl为双电层电容,Rct为电荷转移电阻;图10b为腐蚀产物完全覆盖在1R钢表面时的等效电路模型,其中,Rs为溶液电阻,Qf为腐蚀产物膜的膜层电容,Rf为膜层电阻,RL和L为感抗元件,感抗一般出现在腐蚀前期和后期,即尚未生成完整的保护膜层及后期部分膜层脱落时,通常,在局部电极表面出现腐蚀中间产物,Qdl为双电层电容,Rct为电荷转移电阻。其中,常相位角元件 的阻抗值可用 公式 (3) 计算[26]。
图10 不同浓度NH4H2PO4溶液下1R钢的等效电路
(3)
其中,ZQ为常相位角Q的阻抗值,Y0为导纳模量,w为角频率,j为虚数单位,n为弥散指数。
从表5中可知,去离子水的溶液电阻最大,其值为7.58 104 Ω·cm2,而上文中测得的去离子水的电导率为0.6 μS/cm,转换为电阻率约为1.67 106 Ω·cm,造成电化学工作站测出来的溶液电阻偏小的原因是盐桥中的KCl,钢基体溶解生成的Fe2+等进入去离子水中,从而提高了溶液的导电性。将1、30、60、90、120 mmol/L NH4H2PO4溶液的导电率转换为电阻率,其值分别为8961.9、371.1、199.5、139.4、111.2 Ω·cm,与电化学工作站测出来的溶液电阻值相近。此外,膜层电阻Rf、电荷转移电阻Rct、感抗电阻RL均随NH4H2PO4溶液浓度的增大而减小,而且电荷转移电阻Rct随NH4H2PO4溶液浓度的变化趋势与上文腐蚀速率分析结果一致。
1R钢试样的电极反应为:
其中,阳极反应为金属基体中铁的溶解,而阴极反应为氧的去极化反应,部分Fe2+也会被溶液中的溶解氧氧化为Fe3+,随着腐蚀过程的进行,H+、Fe2+、Fe3+、NH4+等向阴极区方向移动,而OH-、H2PO4-、HPO42-、PO43-等向阳极区方向移动,并在活化阳极区附近形成较为稳定的Fe(OH)3、FePO4、Fe3(PO4)2腐蚀产物[17,18]。
随着NH4H2PO4溶液浓度的增大,1R钢试样表面形成的腐蚀产物膜覆盖程度及致密程度均有所提高,内层腐蚀产物膜中Cr、Mo出现一定程度的富集,抑制了1R钢腐蚀,但在所研究的浓度范围内,溶液pH下降、电导率增大、材料表面形成的锈层疏松等促进材料腐蚀的因素处于主导地位,所以1R钢的腐蚀速率随NH4H2PO4溶液浓度的增大而增大,不过随着NH4H2PO4溶液浓度的增大,抑制材料腐蚀的因素逐渐增强,从而造成1R钢的腐蚀速率随NH4H2PO4溶液浓度的增大先快速增大后缓慢增大的结果。这与上文腐蚀速率分析、形貌观察结果一致。
3 结论
(1) 2Cr-1Ni-1.2Mo-0.2V钢在去离子水中浸泡20 h后的平均腐蚀速率约为0.017 g·m-2·h-1,在1 mmol/L NH4H2PO4溶液中的腐蚀速率便增大7.973倍。1~30、30~60、60~90、90~120 mmol/L NH4H2PO4溶液对应的2Cr-1Ni-1.2Mo-0.2V钢的腐蚀速率相对于NH4H2PO4溶液浓度的导数分别约为0.001、0.002、0.003、0.001 L·g·m-2·h-1 mmol-1,即随着NH4H2PO4溶液浓度的增大,2Cr-1Ni-1.2Mo-0.2V钢的腐蚀速率先快速增大后缓慢增大
(2) 2Cr-1Ni-1.2Mo-0.2V钢仅在低浓度NH4H2PO4溶液中萌发点蚀,溶液浓度大于或等于30 mmol/L后,材料腐蚀形态表现为均匀腐蚀。2Cr-1Ni-1.2Mo-0.2V钢表面腐蚀产物膜为双层结构,外层腐蚀产物膜疏松,且易脱落,主要由Fe3(PO4)2、FePO4组成,而内层腐蚀产物膜附着力较强,主要由Fe3O4构成。随着NH4H2PO4溶液浓度的增大,外层腐蚀产物膜覆盖程度及致密程度均有所提高,内层腐蚀产物膜中Cr、Mo出现一定程度的富集,抑制了2Cr-1Ni-1.2Mo-0.2V钢的腐蚀。
(3) 在0~120 mmol/L NH4H2PO4溶液中,随着NH4H2PO4溶液浓度的增大,2Cr-1Ni-1.2Mo-0.2V钢的稳定开路电位和自腐蚀电位均先负移后基本不变,而自腐蚀电流密度逐渐增大、电荷转移传递电阻逐渐减小,即2Cr-1Ni-1.2Mo-0.2V钢的腐蚀速率随NH4H2PO4溶液浓度的增大而增大。
参考文献:
略
免责声明:本网站所转载的文字、图片与视频资料版权归原创作者所有,如果涉及侵权,请第一时间联系本网删除。
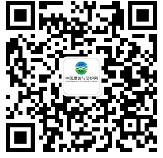
官方微信
《腐蚀与防护网电子期刊》征订启事
- 投稿联系:编辑部
- 电话:010-62316606-806
- 邮箱:fsfhzy666@163.com
- 腐蚀与防护网官方QQ群:140808414