目前商用核电站主要采用轻水核反应堆,约占世界核反应堆总数的85%,分为沸水堆和压水堆2种.此外,重水堆占8%.因此,90%以上的核反应堆的冷却剂为高温高压水.我国核电站目前主要采用压水堆,在未来20年内,我国核电站的发展仍将以压水堆为主.
1 高温高压水中材料的腐蚀电化学行为
2 高温高压水中材料的表面膜特征
图1 Fe-H20 25℃[10],Fe-H2O,Cr-H2O,Ni-H2O,Fe-Cr-Ni-H2O 80℃[11]的电位-pH图
Fig.1 Potential-pH diagrams of Fe-H2O system at 25℃[10](a),Fe-H2O (b),Cr—H2O (c),Ni—H2O (d) and Fe-Cr-Ni-H2O (e) system at 80℃[11](the oxygen and hydrogen equilibria at 1.01×105 Pa are represented by dash lines a and b,respectively,and the vertical dash dot lines reveal the passive regions in different pH solutions)
图2 304不锈钢在25—300℃和14 MPa的0.1 mol/L H3BO3+0.0003 mol/L LiOH水溶液中的极化曲线[12]
Fig.2 Polarization curves of 304SS in 14 MPa and pH(300℃)=6.93 aqueous solution consisted of 0.1 mol/L H3BO3+0.0003 mol/L in the temperature range of25—300℃with a scan rate of 1 mV/s[12]
图3 304不锈钢在25—300℃和14 MPa的0.1 mol/L H3BO3+0.0003 mol/L LiOH水溶液中阳极电流密度与温度的关系[12]
Fig.3 Arrhenius plot of the anodic current density of 304SS in 14 MPa and pH(300℃)=6.93 aqueous solution in the temperature range of 25—300℃[12]
图4 镍基合金625在25—300℃和14 MPa的0.1 mol/L H3BO3+0.0003 mol/L LiOH水溶液中的极化曲线[13]
Fig.4 Polarization curves of alloy 625 in 14 MPa and pH(300℃)=6.93 aqueous solution in the temper-ature range of 25—300℃with a scan rate of1 mV/s[13]
图5 镍基合金625在25—300℃和14 MPa的0.1 mol/L H3BO3+0.0003 mol/L LiOH水溶液中的阳极电流密度与温度的关系[13]
Fig.5 Arrhenius plot of the anodic current density of alloy625 in 14 MPa and pH(300℃)=6.93 aqueous solu-tion in the temperature range of 25—300℃[13]
图6 304不锈钢在25—300℃和14 MPa的0.1 mol/L H3BO3+0.0003 mol/L LiOH水溶液中生成氧化膜的Mott-Schottky曲线[12]
Fig.6 Mott-Schottky plots of the oxide film on 304SS in14 MPa and pH(300℃)=6.93 aqueous solution in the temperature range of 25—300℃[12]
表1 304不锈钢在25—300℃和14 MPa以及pH (300℃)=6.93的0.1 mol/L H3BO3+0.0003 mol/L LiOH水溶液中生成氧化膜的载流子密度[12]
Table 1 Doping density of the oxide film on 304 stainless steel in 0.1 mol/L H3BO3+0.0003 mol/L LiOH aqueous solution in 14 MPa and pH(300℃)=6.93 in the temperature range of 25—300℃[12]
图7 304不锈钢在25—300℃和14 MPa的0.1 mol/L H3BO3+0.0003 mol/L LiOH水溶液中生成氧化膜的Cr2p3/2的XPS[12]
Fig.7 Detailed XPS of Cr2p3/2 in the oxide film on 304SS in 14 MPa and pH(300℃)=6.93 aqueous solution in the temperature range of 25-300℃and for different sputtering times[12]
图8 304不锈钢在25—300℃和14 MPa的0.1 mol/L H3BO3+0.0003 mol/L LiOH水溶液中生成氧化膜的Fe2p3/2的XPS[12]
Fig.8 Detailed XPS of Fe2p3/2 in the oxide film on 304SS in 14 MPa and pH(300℃)=6.93 aqueous solution in the temperature range of 25—300℃and for different sputtering times[12]
图9 304不锈钢在25—300℃和14 MPa的0.1 mol/L H3BO3+0.0003 mol/L LiOH水溶液中表面及内层生成氧化膜的Ni2p3/2的XPS[12]
Fig.9 Detailed XPS of Ni2p3/2 in the surface (a) and inner layer (b) of oxide film on 304SS in 14 MPa and pH(300℃)=6.93 aqueous solution in the temperature range of 25-300℃and for different sputtering times[12]
图10 304不锈钢在25—300℃和14 MPa的0.1 mol/L H3BO3+0.0003 mol/L LiOH水溶液中生成氧化膜表面的Ols的XPS[12]
Fig.10 Detailed XPS of Ols on the surface of oxide film on304SS in 14 MPa and pH(300℃)=6.93 aqueous so-lution in the temperature range of 25—300℃[12]
表2 304不锈钢在25—300℃和14 MPa的0.1 mol/L H3BO3+0.0003 mol/L LiOH水溶液中生成氧化膜表面和内层O2-和OH-在O1s谱中所占比例[12]
Table 2 Contents of O2-and OH-in O1s spectra of the surface and inner layer of the oxide film on 304SS in 14 MPa and pH(300℃)=6.93 aqueous solution and the temperature range of 25—300℃[12]
3 影响材料腐蚀的若干主要因素
图11 304不锈钢在25—300℃和14 MPa的0.1 mol/L H3BO3+0.0003 mol/L LiOH水溶液中生成氧化膜内合金元素的深度分布曲线[12]
Fig.11 Depth profiles of the alloy elements in the oxide film on 304SS in 14 MPa and pH(300℃)=6.93 aqueous solution at 25℃(a),100℃(b),200℃(c) and 300℃(d)[12]
图12 304不锈钢在290℃和3×10-6氧的水中实验290 h后产生的表面氧化膜截面的TEM像和选区电子衍射图[15]
Fig.12 TEM micrograph (a) and SAED patterns of oxide film corresponding to A (b),B (c),C (d),D (e) and E(f) marked in Fig.12a formed on type 304 SS exposed for 290 h in 290℃water containing 3×10-6 O2[15]
图13 304不锈钢在290℃和3×10-6氧的水中产生的表面氧化膜内层的TEM像[15]
Fig.13 TEM morphologies (a,b) and corresponding SAED pattern (c) of the inner layer of oxide film formed on type 304 SS in 290℃water containing 3×10-6 O2[15]
图14 690合金管材中以MgO为核心的TiN夹杂以及腐蚀后的截面照片,表明在核电一回路水中325℃的恒载荷下暴露在外表面的MgO核心优先腐蚀产生的点蚀[23]
Fig.14 Morphology of TiN inclusion with the MgO nucleus in alloy 690TT (a) and SCC initiating at TiN inclusion located at the near surface of the alloy after constant loading test in 325℃water containing 1500×10-6 B,2.3x10-6 Li,and dissolved 2×10-6 oxygen (b)[23]
图15 690合金管中条带状TiN夹杂的形貌及恒载荷暴露在一回路水中在条带夹杂处优先发生应力腐蚀[23]
Fig.15 TiN-inclusion striitger at the surface of alloy 690TT (a) and SCC initiation at TiN-inclusion stringer after constant loading test in 325℃water with the addition of 1500×10-6 B,2.3×10-6 Li,and dissolved 2×10-6oxygen (b)[23]
图16 690合金低能的低∑重位点阵晶界数量随一维拉伸应变增加而减少,并且在9%拉伸变形后位错呈塞积结构[24]
Fig.16 The nearly linear relationships between strain amplitude and GB fraction (a) and the TEM observation of dislocation near twin boundaries after X9%tension strain (b)[24]
图17 690合金低能的低∑重位点阵晶界数量随二维拉伸应变加入出现先减少后恢复,在9%的二维交替拉伸变形后呈位错缠结结构[24]
Fig.17 GB number distribution of deviation degree from ideal∑3 misorientation with different range of strains (a)and the TEM observation of dislocation near twin boundaries after 2D tension (consecutively X3%,X5%Y3%,X7%,Y7%,X9%and Y9%)(b)[24]
图18 690合金划伤的变形和划伤底部在高温高压含Pb碱溶液中的应力腐蚀裂纹萌生[25]
Fig.18 Surface morphologies of the scratch with the size about 50μm in depth and 300μm in width at scratching speed of 9 mm/s[25]
(a) top-view of the scratch (b) the scratch-bank with deformed twin and slip bands (c) the scratch-bed with local “micro-cracks” due to tearing shown as arrows (d) crack initiation at scratch-bank and scratch-bed for alloy 690TT after 30 d immersion in 10%NaOH+10 g/L PbO at 330℃
图19 690合金划伤截面形貌、划伤底部晶粒细化与划伤的边缘机械孪晶[26]
Fig.19 Cross-section of the scratch[26]
(a) SEM observation (b) TEM observation of the nanograins at the bottom of the scratch (c) TEM observation of the mechanical twins at the bank of the scratch
图20 690合金在溶解氧浓度为2×10-6的模拟一回路高温高压水中浸泡60 d后,腐蚀产物膜截面的胞状内氧化膜[27]
Fig.20 Cellular inner oxide film of alloy 690TT after 60 d immersion in simulated primary water with dissolved oxygen content of 2×10-6[27]
4 结论
参考文献
[1] Macdonald D D,Scott A C,Wentrcek P.J Electrochem Soc,1979;126:1618
[2] Macdonald D D,Liu C,Michael M P.In:Kearns J R, Scully J R,eds.,Electrochemical Noise Measurements on Carbon and Stainless Steel in High Subcritical and Supercritical Aqueous Environments.ASTM STP 1277,1996: 247
[3] Lvov S N,Zhou X Y,Macdonald D D.J Electroanal Chem, 1999;463:146
[4] Zhou X Y,Lvov S N,Wei X J,Benning L G,Macdonald D D.Corros Sci,2002;44:841
[5] Zhang L,Han E H,Ke W,Guan H.Chin Pat,ZL 02132544.8,2005 (张丽,韩恩厚,柯伟,关辉.中国专利,ZL 02132544.8, 2005)
[6] Zhang L,Han E H,Ke W,Guan H.Chin Pat,ZL 02274025.2,2003 (张丽,韩恩厚,柯伟,关辉.中国实用新型专利,ZL 02274025.2,2003)
[7] Guan H,Zhang L,Han E H,Ke W.Chin Pat,ZL 02274026.0,2003 (关辉,张丽,韩恩厚,柯伟.中国实用新型专利,ZL 02274026.0,2003)
[8] Sun H,Wu X Q,Han E H.Chin Pat,CN101470093,2009 (孙华,吴欣强,韩恩厚.中国专利,CN101470093,2009)
[9] Sun H,Wu X Q,Han E H.Chin Pat,CN10147009A.2009 (孙华,吴欣强,韩恩厚.中国专利,CN101470094,2009)
[10] Pourbaix M.Atlas of Electrochemical Equilibria in Aqueous Solutions.Houston:NACE International,1974:121
[11] Huang J B,Wu X Q,Han E H.Corros Sci,2009;51:2976
[12] Sun H,Wu X Q,Han E H.Corros Sci,2009;51:2840
[13] Sun H,Wu X Q,Han E H.Corros Sci,2009;51:2565
[14] Sun M C,Wu X Q,Zhang Z E,Han E H.Corros Sci,2009; 51:1069
[15] Kuang W J,Han E H,Wu X Q,Rao J C.Corros Sci, 2010;52:3654
[16] Sun M C,Wu X Q,Han E H,Rao J C.Scr Mater,2009; 61:996
[17] Sun M C,Wu X Q,Zhang Z E,Han E H.J Supercrit Fluids,2008;47:309
[18] Gao X,Wu X Q,Guan H,Han E H.J Supercrit Fluids, 2007;42:157
[19] Morrison S R.Electrochemistry at Semiconductors and Oxidized Metal Electrodes.New York:Plenum Press, 1980:113
[20] Macdonald D D.J Electrochem Soc,1992;139:3434
[21] Hakiki N E,Montemor M F,Ferreira M G S,Belo M D. Corros Sci,2000;42:687
[22] Staehle R W,Gorman J A.Corrosion,2003;59:931
[23] Meng F J,Wang J Q,Han E H,Ke W.Corros Sci,2010; 52:927
[24] Hou J,Wang J Q,Han E H,Ke W.Mater Sci Eng,2009; A518:19
[25] Meng F J,Wang J Q,Han E H,Ke W.Corros Sci,2009; 51:2761
[26] Meng F J,Han E H,Wang J Q,Zhang Z M,Ke W.Electrochem Acta,2010,doi:10.1016/j.electacta.2010.08.028
[27] Wang J Q,Zhang Z M,Han E H,Ke W.6th SG Conference, Toronto,2009
[28] Dan T C,Shoji T,Lu Z P,Sakaguchi K,Wang J Q,Han E H,Ke W.Corros Sci,2010;52:1228
[29] Hou J,Peng Q J,Sakaguchi K,Takeda Y,Kuniya J,Shoji T.Corros Sci,2010;52:1098
免责声明:本网站所转载的文字、图片与视频资料版权归原创作者所有,如果涉及侵权,请第一时间联系本网删除。
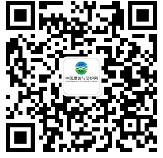
官方微信
《腐蚀与防护网电子期刊》征订启事
- 投稿联系:编辑部
- 电话:010-62316606-806
- 邮箱:fsfhzy666@163.com
- 腐蚀与防护网官方QQ群:140808414