摘要
分别研究了酸洗时间对316L不锈钢表面形貌、表面光学常数及其在3.5%NaCl溶液中耐蚀性能的影响。结果表明,适当酸洗可提升316L不锈钢耐腐蚀性能,但是过度酸洗则容易出现点蚀,耐腐蚀性能的提高是因为酸洗后316L不锈钢表面形成了富含Cr2O3的钝化膜,点蚀的出现是因为其表面出现的微孔促进了点蚀的形核。酸洗液残留于表面会使316L不锈钢局部表面生成更厚的钝化膜,具有不同的光学常数,从而导致宏观表面白斑的出现。
关键词: 316L不锈钢 ; 酸洗 ; 白斑 ; 电化学 ; 椭偏
在不锈钢的生产过程中,酸洗处理是一种常用且高效的处理方法。它能清除不锈钢表面的油脂、锈斑、焊点和氧化层等,使不锈钢能更好地钝化。在各类酸洗液中,硝酸/氢氟酸混合的酸酸洗工艺的应用较为广泛,相关研究也相对较多[1-4]。Galvez等[5]建立了一种模型测定金属氟复合物在硝酸和氢氟酸废液中的溶解度,以提高酸洗液中金属回收的预测和工艺设计。硫酸和盐酸也是常见的不锈钢酸洗液[6-11]。Yue等[9]在盐酸酸洗液中引入氧化剂 (过氧化氢) 促进基底金属的溶解,保证了良好的除锈效果,同时抑制了热轧430不锈钢的晶间腐蚀,提高了不锈钢的表面完整性。有研究通过304不锈钢在硫酸溶液中的电解酸洗实验揭示了在-0.20和1.25 V (vs Ag/AgCl) 下酸洗的机理和动力学,研究[12]结果表明,被氧化的不锈钢在阳极极化过程中出现了两个与酸洗有关的电流峰,是由于不锈钢在-0.20和1.25 V (vs Ag/AgCl) 的电位下恒电位极化时氧化层中的铁和镍金属相优先溶解。
不锈钢经酸洗后表面出现不均匀的白斑是比较常见的一类问题,一般前期除油不彻底、基底不干净都可能会导致酸洗后样品某些区域的酸洗液在不锈钢表面停留时间过长,造成过度酸洗,使该局部区域与其它表面不同,从而形成白斑[13,14]。
虽然有少数工作分析不锈钢酸洗时间对不锈钢酸洗行为的影响[15],但在这些工作研究的酸洗行为少有涉及酸洗时间对不锈钢钝化 (或腐蚀) 行为的影响。无论是酸洗钝化过程中的腐蚀性还是表面白斑问题,都直接关系到最终产品的使用和可靠性,为了进一步确认过渡酸洗所造成的负面影响,系统探究酸洗过度对不锈钢表面形貌和耐蚀性能的影响,本文研究了不同酸洗时间对不锈钢表面形貌、表面光学常数及其在3.5% (质量分数) NaCl溶液中耐腐蚀性的影响。
1 实验方法
实验材料为商用316L不锈钢,化学成分 (质量分数) 为:S 0.001%,C 0.021%,P 0.028%,N 0.052%,Cu 0.054%,Si 0.500%,Mn 1.167%,Mo 2.11%,Ni 10.132%,Cr 17.343%,余量为Fe。将试样加工成15 mm×15 mm×4 mm的块状,分别用400#、800#、1200#、1500#和2000#SiC水砂纸逐级打磨试样并依次使用W2.5、W1.5和W1的金刚石研磨膏抛光,然后用丙酮和去离子水依次超声清洗。
酸洗液的成分为120~150 g/L 的HNO3和30 g/L 的HF,酸温为室温 (25 ℃)。试样的酸洗时间分别为10、20、30、40和50 min,每个酸洗时间段下准备3个平行试样用于后续实验。实验中还对不锈钢同一表面进行不同酸洗时间的对比实验:将上述商用316L不锈钢试样加工成60 mm×30 mm×4 mm的块状并对试样进行与实验样品相同的打磨、抛光、清洗处理,在预处理完后对试样表面进行8个不同酸洗时间的局部酸洗,这8个区域分别对应酸洗时间10、20、30、40、50、60、70和80 min。
分别使用了光学显微镜、扫描电子显微镜 (SEM, Phenom-World Phenom XL) 以及原子力显微镜 (AFM, Bruker Dimension ICON) 观察不同酸洗时间样品的宏观和微观结构形貌,使用激光共聚焦显微镜 (LSM,Keyence VK-X200K) 以及其配套的VK分析软件分析了不同酸洗时间样品的表面粗糙度。
使用椭圆偏振仪 (SE,M-2000U) 测量表面膜,并使用CompleteEASE软件分析了不同酸洗时间样品表面的钝化膜厚度、反射率以及吸收系数。
电化学实验溶液为3.5%NaCl,室温时,溶液的pH为6.8。采用三电极电解池体系,试样为工作电极,对电极为铂电极,参比电极为饱和氯化钾Ag/AgCl电极,该电极相对于氢标电极的电位为+0.2224 V。
电化学阻抗、Mott-Schottky曲线以及动电位极化的测试均由Gamry E1010型电化学工作站完成。在电化学测试之前,样品先在开路电位 (OCP) 下稳定30 min。电化学阻抗测试的测试频率为105~10-2 Hz,交流激励信号幅值为5 mV,测量均在开路电位下进行,测得的EIS数据使用ZsimpWin软件进行拟合。动电位极化曲线的扫描范围为-0.3 Vvs OCP到1.2 Vvs OCP,扫描速率为0.333 mV·s-1;为了保证实验的可重复性,在动电位极化之前对于未处理的样品 (未酸洗) 进行10 min的恒电位阴极极化以去除样品表面自然形成的氧化物。Mott-Schottky曲线的测试频率为1000 Hz,测试振幅为10 mV,扫面电压范围为-1.0 Vvs OCP到0.1 Vvs OCP,扫描的步阶为20 mV。
钝化膜的成分测试由X射线光电子能谱 (XPS,Thermo Scientific K-Alpha) 完成。X射线的激发源为Al Kα射线 (hv=1486.6 eV),斑束为400 μm,分析室真空度优于5.0×10-7 mBar,工作电压为12 kV,灯丝电流为6 mA,全谱扫描通能为100 eV,步长为1 eV,窄谱扫描通能为50 eV,步长为0.05 eV,窄谱至少进行5次循环信号累加,以C1s=284.80 eV结合能为能量标准进行荷电校正。
2 实验结果
2.1 局部酸洗
同一不锈钢表面上局部酸洗实验结果如图1所示,从图中可以看出随着酸洗时间的增加不锈钢表面变得更白,并且在两个酸洗区域叠加处要白于其周边区域。
2.2 极化曲线和电化学阻抗测试
图2是不同酸洗时间316L不锈钢的动电位极化曲线,表1是其对应的极化曲线的腐蚀参数。从极化曲线以及其腐蚀参数可以看出,未酸洗的316L不锈钢具有较低的腐蚀电位Ecorr以及较高的腐蚀电流Icorr,并且在相对较低的电位就出现了点蚀。酸洗后的样品腐蚀电位正移,腐蚀电流减小一个数量级,但是随着酸洗时间的增加,无论是腐蚀电位还是腐蚀电流,都只是在一个较小的范围波动。值得注意的是,当酸洗时间大于30 min时,样品在实验过程中出现了点蚀。
图1 316L不锈钢表面不同酸洗时间局部区域
图2 不同酸洗时间316L不锈钢的动电位极化曲线
图3是不同酸洗时间316L不锈钢在3.5%NaCl溶液中的电化学阻抗谱Nyquist图。阻抗拟合所使用的简单等效电路图也展示在图3中。阻抗拟合的结果如表2所示,表中Y0是CPE元件拟合得到的值,n是值介于0~1之间的无量纲参数,它被用来表示电容的理想度,Rp直接反应样品的耐腐蚀性能,括号里的百分数是拟合的标准差。酸洗之后的Rp要比酸洗之前高1~2个数量级,随着酸洗时间的增加Rp的值则在一定范围内波动。
表2 样品在3.5%NaCl溶液中EIS结果的拟合参数
图3 不同酸洗时间316L不锈钢的Nyquist图
图4是不同酸洗时间316L不锈钢样品的Bode图。根据图4a中不同酸洗时间样品在低频时 (0.01 Hz) 的相对上下位置可知,酸洗后的316L不锈钢样品具有比未酸洗的样品更高的阻抗模值,而阻抗模值随着酸洗时间的增加在一定范围内波动,并无明显的线性关系,这与从极化曲线以及Nyquist图中得到的结果一致。从图4b中可以看出,酸洗后的样品曲线形状都差不多,而未酸洗样品的曲线形状有一定差别,这可能是由酸洗时形成的钝化膜所导致。
表1 不同酸洗时间316L不锈钢样品的极化曲线腐蚀参数
2.3 表面形貌
图5是不同酸洗时间316L不锈钢的表面形貌。由图可以看出,抛光后的样品表面整体比较平整,表面还是能够看到一些均匀分布的较浅划痕;而随着酸洗时间的增加,样品表面的较浅划痕明显减少;在酸洗时间达到30 min时,样品表面较浅的划痕基本已经被去除;当酸洗时间进一步增加,316L不锈钢表面变得更加不平整。图6是不同酸洗时间316L不锈钢样品的表面粗糙度,从图可以看出,粗糙度随着酸洗时间的变化是呈先减小后增大的趋势的。
图4 不同酸洗时间316L不锈钢样品的Bode图
图5 不同酸洗时间316L不锈钢的表面形貌
为了进一步地分析酸洗时间对316L不锈钢表面的影响,本工作使用SEM对表面进行了微观形貌的观察,图7为316L不锈钢表面的SEM微观形貌。从图可以看出,随着酸洗时间的增加样品表面的划痕逐渐消失,这与在图5中所观察到的结果一致。从这些微观形貌的图中还可发现,样品表面的一些缺陷也在减少,这说明酸洗能够提高316L不锈钢表面的完整性。除此之外,316L不锈钢样品表面还形成了具有片状组织的形貌,并且酸洗时间越长,表面这种片状组织就越多 (图7e和f)。
图8为316L不锈钢表面的AFM微观形貌。图8通过更加微观的视角证实了图5与图7中观察到的表面变化;在酸洗的前20 min,316L不锈钢表面的结构为沿着同一方向的脊状组织,这在较宏观的角度图5和图7表现为较光滑的钝化膜表面;酸洗时间大于20 min时,表面逐渐出现一些边界,这些边界形成对应图7中观察到的片状组织的形成。除此之外,316L不锈钢表面有较多的微小孔洞出现 (图8e和f)。
2.4 表面XPS结果
对不同酸洗时间316L不锈钢样品进行了XPS分析,结果如图9所示,不同酸洗时间316L不锈钢表面钝化膜的部分组成成分如表3所示。根据其他研究中的结合能平均值数据[16,17]可知,Fe2p和Cr2p都表现出了金属和氧化物的峰。Cr2O3占表面氧化物的比值Cr2O3/(Cr2O3+FeO(Fe3O4)) 随着酸洗时间的增加呈增大的趋势,酸洗后形成的钝化膜中Cr2O3的量要普遍高于未酸洗样品表面的钝化膜中Cr2O3的量。显然含Cr量的提高,有利于耐蚀性的提高。
图6 不同酸洗时间316L不锈钢的表面粗糙度
图7 不同酸洗时间316L不锈钢表面钝化膜的SEM微观形貌
图8 不同酸洗时间316L不锈钢表面钝化膜的AFM微观形貌
图9 不同酸洗时间下316L不锈钢表面XPS谱
2.5 表面钝化膜厚度及光学常数
图10为椭圆偏振仪测得的不同酸洗时间316L不锈钢样品表面钝化膜的厚度。由图可知,随着酸洗时间的增加样品表面的钝化膜厚度逐渐增大。表4是椭圆偏振仪测得的不同酸洗时间316L不锈钢样品表面钝化膜在波长为589 nm处的折射率、吸收系数和介电常数,括号内是其对应的百分比标准差。由表中结果可知,无论是钝化膜的折射率还是其吸收系数都是随着酸洗时间的增加先增大然后趋于平稳,并且酸洗后样品表面钝化膜的折射率和吸收系数都要高于未酸洗样品表面钝化膜的折射率和吸收系数。
表3 不同酸洗时间316L不锈钢样品的表面氧化物成分
图10 不同酸洗时间下316L不锈钢表面钝化膜厚度
2.6 表面钝化膜半导体性能
图11是不同酸洗时间316L不锈钢样品的Mott-Schottky曲线图,通过曲线的拟合与表4中的介电常数可以得到平带电位、施主密度和受主密度。表5是不同酸洗时间316L不锈钢样品的平带电位、施主密度和受主密度。从表中可以看出在酸洗之前样品钝化膜的施主密度Nd要大于其受主密度Na,而随着酸洗时间的增加样品钝化膜的施主密度Nd小于了其受主密度Na。
3 讨论
图1局部酸洗结果表明316L不锈钢表面随着酸洗时间的增加变得更白,说明过长的酸洗时间确实会导致被酸洗的不锈钢表面变得更白,也就是说酸洗后不锈钢形成的不均匀白斑确实是由不锈钢表面残留的酸洗液导致的。
表4 不同酸洗时间316L不锈钢样品的光学常数和介电常数 (波长589 nm的结果)
图11 不同酸洗时间316L不锈钢样品的Mott-Schottky图
表5 不同酸洗时间316L不锈钢样品的平带电位、施主密度和受主密度
由极化曲线 (图2和表1) 和电化学阻抗 (图3、4和表2) 的结果可知,酸洗之后样品的耐腐蚀性能要比未酸洗的样品更好,这也是符合常识的,但是从图2极化曲线的结果还可以看出未酸洗的样品出现了点蚀,酸洗40和50 min的316L不锈钢样品同样也出现了点蚀,而酸洗时间更短一点的样品却没有出现点蚀,这说明酸洗时间过长可能会对不锈钢的局部腐蚀性能产生影响。图5结果表明酸洗可以去除样品表明的划痕,但是随着酸洗时间的增加样品的表明会变得更加不平整,图6样品表面粗糙度的结果也证明了图5中表明形貌的变化。从不同酸洗时间样品的SEM图 (图7) 可以看出,随着酸洗时间的增加样品形成了片状组织的表面,这种片状组织表面形貌的形成可能是图5和6中表面变得不平整以及表面粗糙度上升的原因。
综上,酸洗后样品耐腐蚀性能提高是因为酸洗时表面的钝化,而酸洗前30 min没有点蚀发生则可能是因为样品表面的划痕被酸洗去除,提升了样品表面的完整性。虽然图7中片状组织表面的形成可以解释图5和6中表面形貌以及表面粗糙度的变化,但是并不能解释为什么酸洗40和50 min的样品会再次出现点蚀。通过更加微观的AFM观察发现,在酸洗40和50 min样品的表面有一些微孔出现,这些微孔的出现可以作为点蚀的形核位点提高点蚀的发生概率,所以酸洗后点蚀的再次出现应是这些微孔所引起的。
由XPS分析及Mott-Schottky曲线分析可知,酸洗后样品表面的Cr2O3含量基本都要比未酸洗样品表面的Cr2O3含量高 (有个别更低有可能是测试或者其他因素导致),而不锈钢表面钝化膜中富集的Cr2O3能够提高钝化膜的耐蚀性能,这点已经被很多研究证明。另外酸洗之前样品钝化膜的施主密度Nd要大于其受主密度Na,是n型半导体;而随着酸洗时间的增加样品钝化膜的施主密度Nd小于了其受主密度Na,转为p型半导体。Cr2O3属于p型半导体[18],这解释了酸洗前后样品表面钝化膜n型到p型半导体性质的转变,即酸洗后钝化膜中Cr2O3占据主导 (富集),与XPS分析得出的结论一致。综上,可以证明酸洗之后样品耐腐蚀性能提升的更深层原因是酸洗后钝化膜中Cr2O3的富集。
椭偏测得的钝化膜厚度结果 (图10) 说明,随着酸洗时间的增加钝化膜的厚度也增大。更厚钝化膜可能会引起不锈钢表面光学常数的改变,从而在宏观层面形成视觉差异,最终导致白斑的形成。从表4也能看出316L不锈钢表面钝化膜的折射率n和吸收系数k都是随着酸洗时间的增加先增大然后趋于平稳,这证实了上述316L不锈钢表面钝化膜变厚引起其表面光学常数改变的猜测。所以,局部的酸洗液残留会使316L不锈钢局部表面生成更厚的钝化膜,更厚的钝化膜具有不同的光学常数,从而导致宏观层面白斑的出现。
4 结论
(1) 酸洗后316L不锈钢耐腐蚀性能上升,因为酸洗后316L不锈钢表面形成了富含Cr2O3的较厚钝化膜。
(2) 但是当酸洗时间过长时 (本工作中大于30 min) 316L不锈钢出现点蚀,因为酸洗使不锈钢表面出现了微孔,为点蚀提供了形核位点。
(3) 局部的酸洗液残留液滴会使316L不锈钢局部表面生成更厚的、具有不同光学常数的钝化膜,从而宏观上形成白斑现象。
参考文献
1 Heilala B, M?kinen A, Nissinen I, et al. Evaluation of time-gated Raman spectroscopy for the determination of nitric, sulfuric and hydrofluoric acid concentrations in pickle liquor [J]. Microchem. J., 2018, 137: 342
2 Kang G M, Lee K, Park H, et al. Quantitative analysis of mixed hydrofluoric and nitric acids using Raman spectroscopy with partial least squares regression [J]. Talanta, 2010, 81: 1413
3 Ito M, Yoshioka M, Isobe T, et al. Development of automatic analyzer for sulfuric acid, mixed nitric acid, and hydrofluoric acid in stainless pickling process [J]. Kag. Kog. Ronbunshu, 1999, 25: 1
4 Takahari T, Kosaka M, Arigane H. Behavior of ferricfluoride ions in the pickling solution of nitric acid and hydrofluoric acid for stainless steels [J]. Tetsu to Hagane, 1984, 70: 1605
5 Gálvez J L, Dufour J, Negro C, et al. Determination of iron and chromium fluorides solubility for the treatment of wastes from stainless steel mills [J]. Chem. Eng. J., 2008, 136: 116
6 Bystriansky J, Malani'k K, Nova'k P. Stability of minority phases in some corrosion media [J]. Corros. Sci., 1993, 35: 355
7 Li L F, Caenen P, Celis J P. Effect of hydrochloric acid on pickling of hot-rolled 304 stainless steel in iron chloride-based electrolytes [J]. Corros. Sci., 2008, 50: 804
8 Jiang M F, Li X L, Yue Y Y, et al. Effect of hydrochloric acid on electrochemical behaviour of 430 stainless steel [J]. Mater. Res. Innov., 2014, 18: S5-62
9 Yue Y Y, Liu C J, Shi P Y, et al. Corrosion of hot-rolled 430 stainless steel in HCl-based solution [J]. Corros. Eng. Sci. Technol., 2016, 51: 581
10 Erdo?an M, Karakaya E, Aras M S, et al. Removal of trace amounts of copper from concentrated hydrochloric acid solutions [J]. Int. J. Electrochem. Sci., 2018, 13: 10934
11 Li H Y, Zhao A C. Pickling behavior of duplex stainless steel 2205 in hydrochloric acid solution [J]. Adv. Mater. Sci. Eng., 2019, 2019: 1
12 Li L F, Caenen P, Jiang M F. Electrolytic pickling of the oxide layer on hot-rolled 304 stainless steel in sodium sulphate [J]. Corros. Sci., 2008, 50: 2824
13 Yi G H, Zheng D J, Song G L. Surface white spot and pitting corrosion of 316 L stainless steel [J]. Anti-Corros. Methods Mater., 2020, 68: 1
14 Lin J K, Ma G J, Qiao Z, et al. White spot analysis of a nuclear power plant reactor refueling pool stainless steel cladding [J]. Total Corros. Control, 2015, 29(7): 38
14 林建康, 马谷剑, 乔泽等. 某核电厂反应堆换料水池不锈钢覆面钢板白斑分析[J]. 全面腐蚀控制, 2015, 29(7): 38
15 Narvaez L, Miranda J M, Ronquillo A. Stainless steel pickling using ecologies friendly mixtures composed of H2O2-H2SO4-iones F [J]. Rev. Met., 2013, 49: 145
16 Ghods P, Isgor O B, Brown J R, et al. XPS depth profiling study on the passive oxide film of carbon steel in saturated calcium hydroxide solution and the effect of chloride on the film properties [J]. Appl. Surf. Sci., 2011, 257: 4669
17 Liu J, Zhang T, Meng G Z, et al. Effect of pitting nucleation on critical pitting temperature of 316L stainless steel by nitric acid passivation [J]. Corros. Sci., 2015, 91: 232
18 Hakiki N E, Boudin S, Rondot B, et al. The electronic structure of passive films formed on stainless steels [J]. Corros. Sci., 1995, 37: 1809
免责声明:本网站所转载的文字、图片与视频资料版权归原创作者所有,如果涉及侵权,请第一时间联系本网删除。
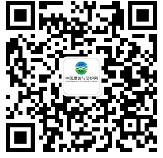
官方微信
《腐蚀与防护网电子期刊》征订启事
- 投稿联系:编辑部
- 电话:010-62316606-806
- 邮箱:fsfhzy666@163.com
- 腐蚀与防护网官方QQ群:140808414