不锈钢材料的碱致应力腐蚀开裂,简称“碱脆”或“碱裂”,许多文献已对其展开了报道,但多数研究集中在高温条件下,而中低温条件下不锈钢碱脆的相关研究较少。不锈钢碱脆失效的案例也多发生在高温环境中,在中低温时发生的失效案例较为少见。国内某核电站制氢机储罐材料为316L奥氏体不锈钢,罐内介质为KOH溶液,工作压力为700kPa~800kPa。该储罐在服役8a后,其下封头发生开裂。对储罐进行了理化检验及不同区域的应力状态分析,研究了该储罐开裂的原因并提出了改进建议。
1 理化检验
1.1 宏观观察和渗透检测
泄漏储罐由筒体和椭圆封头焊接而成,封头可分为直边段与弯曲段,如图1a)所示。外壁贯穿裂纹位于封头直边段,裂纹上尖端距熔合线约8mm,下尖端距熔合线约13mm,裂纹总长度约为5mm。
对储罐进行液体渗透检测,结果表明:除贯穿裂纹外,储罐外壁未发现其他裂纹;内壁靠近焊缝两侧发现较多裂纹,既有垂直于焊缝的轴向裂纹,也有平行于焊缝的环向裂纹,如图1b)所示。轴向裂纹仅位于距焊缝熔合线约13mm以内的封头直边段区域,周向均匀分布,长短不一。较长裂纹上尖端距熔合线1~2mm,下尖端距熔合线约13mm;较短裂纹上尖端距熔合线约4mm,下尖端熔合线约10mm,将此裂纹记为A类裂纹,贯穿裂纹即为A类裂纹。环向裂纹位于焊缝两侧距熔合线1~3mm,筒体侧裂纹记为B1类裂纹,封头侧裂纹记为B2类裂纹。泄漏储罐裂纹分布宏观示意如图2所示。
1.2 化学成分分析
采用电火花直读光谱仪对筒体、封头母材进行化学成分分析,两者化学成分均满足ASTM A473—2017标准的要求。
1.3 金相检验
在筒体和封头母材处取样,利用光学显微镜进行金相检验。储罐母材的显微组织形貌如图3所示。筒体母材显微组织为奥氏体+少量退火孪晶,晶粒度为6级;封头母材显微组织为奥氏体+大量形变孪晶和滑移带,晶粒度为3.5级。
1.4 硬度测试
利用数显维氏硬度计对储罐各部位进行硬度测试。筒体及封头母材硬度分别为165 HV,248 HV。焊缝、筒体侧热影响区、封头侧热影响区硬度分别为171 HV,188 HV,165 HV,筒体侧、封头侧平均厚度分别为3.71,4.24mm。筒体为正常固溶退火态316L 钢。ASTM A473—2017标准中对316L钢的硬度未作明确要求,但参考GB/T 3280—2015 《不锈钢冷轧钢板和钢带》标准可知,316L钢硬度要求不大于220 HV,可见封头硬度较高,这与其组织中含有大量形变孪晶和滑移带有关,为冷作硬化态316L钢。
1.5 裂纹形貌分析
1.5.1 裂纹表面分析
在储罐内壁,对A类和B类裂纹表面进行取样分析,取样位置如图4所示。试样经弧面削平、抛光及侵蚀后,用光学显微镜进行观察,微观形貌如图5所示,可见两类裂纹在表面均沿晶扩展。
A类裂纹中心位置较宽,两端较细,封头侧热影响区出现明显粗晶区和细晶区,总长约为4mm;筒体侧热影响区只出现粗晶区,长约0.8mm,未发现细晶区。封头侧母材含有大量形变孪晶和滑移带,形变、畸变程度高,焊接受热时发生静态再结晶。靠近焊缝部位由于温度较高,再结晶后发生晶粒长大,形成粗晶区,离焊缝稍远的区域只发生了静态再结晶,晶粒未长大形成细晶区。筒体侧母材为固溶退火态,其形变、畸变程度差,再结晶驱动力不够,由于靠近焊缝部位温度较高,故直接发生晶粒长大,形成粗晶区;由于距离焊缝稍远的区域温度低于晶粒长大温度,故只发生了回复而未发生结晶,未出现类似封头侧的细晶区,无法直接判断热影响区范围。筒体与封头母体材料均为316L不锈钢,导热系数一致,焊缝两边热影响区范围基本相同,由封头侧热影响区范围推断,筒体热影响区宽度约为4mm。由此可知,一部分A类裂纹的一侧尖端位于热影响区,另一侧尖端位于封头直边段,中心位置位于封头直边段;另一部分A类裂纹均位于封头直边段;所有B类裂纹均位于焊缝两侧的热影响区内。
1.5.2 裂纹截面分析
图6,7分别为两类裂纹壁厚方向的显微组织形貌。A类裂纹由储罐内壁沿晶向外壁扩展,扩展深度不一,严重处几乎已贯穿储罐全壁厚,裂纹尖端分叉,晶界未敏化,具有典型沿晶应力腐蚀裂纹特征。B1和B2类裂纹主要位于焊缝两侧的热影响区,裂纹沿晶扩展,尖端分叉,晶界未敏化,具有典型沿晶应力腐蚀裂纹特征。A,B1,B2类裂纹处的显微硬度分别为242 HV,171 HV,157 HV。B2类裂纹区硬度大幅下降的原因是原始形变的奥氏体晶粒焊接后发生了静态再结晶。
为了进一步分析A类裂纹在储罐内壁的起源位置,沿同一条裂纹长度方向,在中心位置及两侧解剖并测其深度,结果如图8所示。裂纹中间部位沿壁厚方向扩展深度最深,这表明A类裂纹的起源位置为裂纹长度方向的中部,由内壁表面向两侧扩展。
1.6 残余应力分析
采用残余应力分析仪,以焊缝为分界,分别对筒体、封头进行残余应力测试,每个位置均测试0°(平行于焊缝方向)和90°(垂直于焊缝方向)两个方向,测试结果如图9所示。筒体侧0°方向和90°方向残余拉应力区分别在距焊缝中心线约20,12mm处;封头侧0°方向和90°方向的残余拉应力区分别在距焊缝中心线约17,15mm处。A 类裂纹、B类裂纹均位于残余拉应力区。
2 合分析
A类裂纹和B类裂纹均位于储罐的残余拉应力区,均沿壁厚方向由内壁向外壁沿晶扩展。A类裂纹起源于封头母材区,在表面垂直于焊缝向两侧扩展;B类裂纹位于焊缝两侧的热影响区,在表面平行于焊缝扩展。封头的制造工艺为冷冲压成型,封头直边段是由原板料边缘向内“翻边”而成,会产生较大的塑性变形和残余拉应力。在原始冷加工残余应力,温度为65~70℃,及KOH碱液服役条件的长期作用下,产生了垂直于焊缝的沿晶应力腐蚀开裂。由于热影响区焊接后奥氏体晶粒的回复及再结晶,原始残余应力基本消失。由于奥氏体晶粒的冷却收缩,热影响区产生了焊接残余拉应力,该残余应力以垂直于焊缝为主,在温度为65~70℃,KOH碱液服役条件的长期作用下产生了平行于焊缝的沿晶应力腐蚀开裂。
该储罐开裂机理可用碱致应力腐蚀开裂的膜破裂理论进行解释。在KOH碱液环境中,储罐内壁表面形成一层钝化膜,该钝化膜在较高残余拉应力的作用下发生破裂。钝化膜破裂后,破裂区金属表面未及时形成钝化膜,裸露金属与KOH碱液接触,OH-在表面破裂区域发生浓缩,进而与裸露金属发生反应,裸露金属与浓缩碱液反应生成金属氧化膜,此氧化膜在应力作用下又发生破裂,继而再钝化-破裂-钝化-破裂循环反复进行,裂纹不断扩展延伸,最终导致储罐发生开裂并泄漏。
3 论与建议
(1) 储罐内壁的环向裂纹和轴向裂纹均为碱致应力腐蚀开裂,环向裂纹主要受焊接残余拉应力作用,而轴向裂纹主要受封头直边段冷加工残余拉应力作用。
(2) 控制焊接热输入,降低焊接残余应力,以避免环向裂纹;封头冷成型后增加去应力处理工艺,降低冷加工残余应力,以避免轴向裂纹。
(3) 为保障设备的安全运行,应加强运行过程中的渗透检测等无损检测措施。
免责声明:本网站所转载的文字、图片与视频资料版权归原创作者所有,如果涉及侵权,请第一时间联系本网删除。
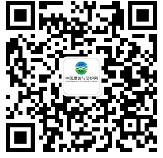
官方微信
《腐蚀与防护网电子期刊》征订启事
- 投稿联系:编辑部
- 电话:010-62316606-806
- 邮箱:fsfhzy666@163.com
- 腐蚀与防护网官方QQ群:140808414